管道全位置自动焊推荐工艺方案
管道全位置自动焊施工工法
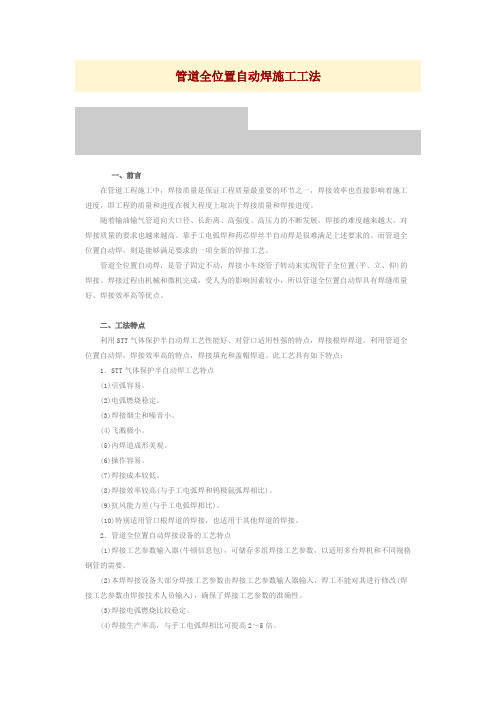
管道全位置自动焊施工工法一、前言在管道工程施工中,焊接质量是保证工程质量最重要的环节之一,焊接效率也直接影响着施工进度,即工程的质量和进度在极大程度上取决于焊接质量和焊接进度。
随着输油输气管道向大口径、长距离、高强度、高压力的不断发展,焊接的难度越来越大,对焊接质量的要求也越来越高。
靠手工电弧焊和药芯焊丝半自动焊是很难满足上述要求的。
而管道全位置自动焊,则是能够满足要求的一项全新的焊接工艺。
管道全位置自动焊,是管子固定不动,焊接小车绕管子转动来实现管子全位置(平、立、仰)的焊接。
焊接过程由机械和微机完成,受人为的影响因素较小,所以管道全位置自动焊具有焊缝质量好、焊接效率高等优点。
二、工法特点利用STT气体保护半自动焊工艺性能好、对管口适用性强的特点,焊接根焊焊道。
利用管道全位置自动焊,焊接效率高的特点,焊接填充和盖帽焊道。
此工艺具有如下特点:1.STT气体保护半自动焊工艺特点(1)引弧容易。
(2)电弧燃烧稳定。
(3)焊接烟尘和噪音小。
(4)飞溅极小。
(5)内焊道成形美观。
(6)操作容易。
(7)焊接成本较低。
(8)焊接效率较高(与手工电弧焊和钨极氩弧焊相比)。
(9)抗风能力差(与手工电弧焊相比)。
(10)特别适用管口根焊道的焊接,也适用于其他焊道的焊接。
2.管道全位置自动焊接设备的工艺特点(1)焊接工艺参数输入器(牛顿信息包),可储存多组焊接工艺参数,以适用多台焊机和不同规格钢管的需要。
(2)本焊焊接设备大部分焊接工艺参数由焊接工艺参数输人器输入,焊工不能对其进行修改(焊接工艺参数由焊接技术人员输入),确保了焊接工艺参数的准确性。
(3)焊接电弧燃烧比较稳定。
(4)焊接生产率高,与手工电弧焊相比可提高2~5倍。
(5)焊缝成形美观,内部质量好。
(6)可采用CO2气体或混合气体(Ar+CO2)作为保护介质。
(7)适用管径φ≥325mm,适用管壁厚度δ≥5mm。
管径越大、壁厚越厚,其经济效益越好。
三、适用范围本工法适用于低碳钢、低合金钢输油、输气和输水等管道的焊接。
中小口径厚壁管全位置自动焊施工工法(2)
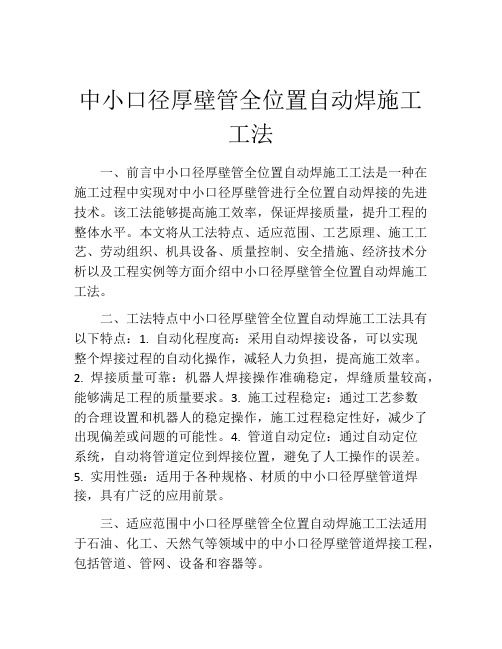
中小口径厚壁管全位置自动焊施工工法一、前言中小口径厚壁管全位置自动焊施工工法是一种在施工过程中实现对中小口径厚壁管进行全位置自动焊接的先进技术。
该工法能够提高施工效率,保证焊接质量,提升工程的整体水平。
本文将从工法特点、适应范围、工艺原理、施工工艺、劳动组织、机具设备、质量控制、安全措施、经济技术分析以及工程实例等方面介绍中小口径厚壁管全位置自动焊施工工法。
二、工法特点中小口径厚壁管全位置自动焊施工工法具有以下特点:1. 自动化程度高:采用自动焊接设备,可以实现整个焊接过程的自动化操作,减轻人力负担,提高施工效率。
2. 焊接质量可靠:机器人焊接操作准确稳定,焊缝质量较高,能够满足工程的质量要求。
3. 施工过程稳定:通过工艺参数的合理设置和机器人的稳定操作,施工过程稳定性好,减少了出现偏差或问题的可能性。
4. 管道自动定位:通过自动定位系统,自动将管道定位到焊接位置,避免了人工操作的误差。
5. 实用性强:适用于各种规格、材质的中小口径厚壁管道焊接,具有广泛的应用前景。
三、适应范围中小口径厚壁管全位置自动焊施工工法适用于石油、化工、天然气等领域中的中小口径厚壁管道焊接工程,包括管道、管网、设备和容器等。
四、工艺原理中小口径厚壁管全位置自动焊施工工法采用机器人焊接设备进行操作,在施工工法与实际工程之间有以下联系和技术措施:1. 工艺参数调整:根据实际工程的要求,对机器人焊接设备的工艺参数进行调整,以实现焊接质量的要求。
2. 焊接材料选择:根据工程的环境和要求,选择合适的焊接材料,确保焊接接头的稳定性和耐腐蚀性。
3. 焊接速度控制:通过调整焊接速度,控制焊接过程中的热输入,使焊缝形成合适的熔池形态,达到预期的焊接质量。
五、施工工艺中小口径厚壁管全位置自动焊施工工法的施工工艺包括以下几个阶段:1. 管道准备:对管道进行表面处理、切割、开槽等工艺,确保管道的质量和准备工作的完成。
2. 自动定位:通过自动定位系统,将管道准确地定位到焊接位置,保证焊接的精度和准确性。
管道自动焊施工方案

管道自动焊施工方案1. 引言管道自动焊是一种高效、准确和可靠的焊接方法,广泛应用于工业领域。
本文将介绍一种管道自动焊施工方案,包括施工准备、设备配置、工艺参数设置、安全措施等方面的内容。
2. 施工准备在进行管道自动焊施工之前,需要进行一系列的准备工作。
具体步骤如下:1.确定焊接的管道材质、规格和长度,并进行必要的测量和标记。
2.准备焊接所需的材料,包括焊条、气体等。
3.确保焊接工作区域干净整洁,清除杂物和可能影响焊接质量的因素。
4.确保施工现场通风良好,以保证焊接过程中排出的有害气体能够及时排除。
5.检查并确认所使用的焊接设备和工具的完好性和可靠性。
3. 设备配置管道自动焊所需的主要设备包括焊接机、焊接工作台、焊接电缆、焊接枪等。
在选择和配置设备时,需要考虑以下因素:•焊接机的类型和参数,需根据管道材质、规格和焊接工艺要求进行选择。
•焊接工作台的高度和稳定性,需根据施工现场实际情况进行调整和固定。
•焊接电缆的长度和容量,需满足焊接距离和电流需求。
•焊接枪的类型和质量,需保证焊接质量和操作方便。
4. 工艺参数设置管道自动焊的工艺参数设置是确保焊接质量的重要步骤。
以下是一些常用的工艺参数及其设置要求:•焊接电流和电压:根据管道材质、壁厚和焊接方法确定合适的电流和电压范围。
•焊接速度:根据管道直径和焊缝要求设置焊接速度,以保证焊缝的完整性和均匀性。
•焊接时间:根据焊接长度和焊接速度计算出合适的焊接时间,并根据实际情况进行调整。
•焊接气体流量:根据焊接材料和管道材质选择适当的焊接气体,并设置合适的流量,以保证焊接质量。
5. 安全措施在进行管道自动焊施工时,需要采取一些安全措施,以保护施工人员和设备的安全。
以下是一些常用的安全措施:•穿戴适当的个人防护装备,如焊接面罩、防火服、防护手套等。
•确保施工现场通风良好,避免有害气体积聚。
•设置明显的警示标志,警告他人注意施工区域。
•安全使用焊接设备,如避免触摸带电部分、正确接地等。
核电厂管道卡钳式全位置自动焊工艺
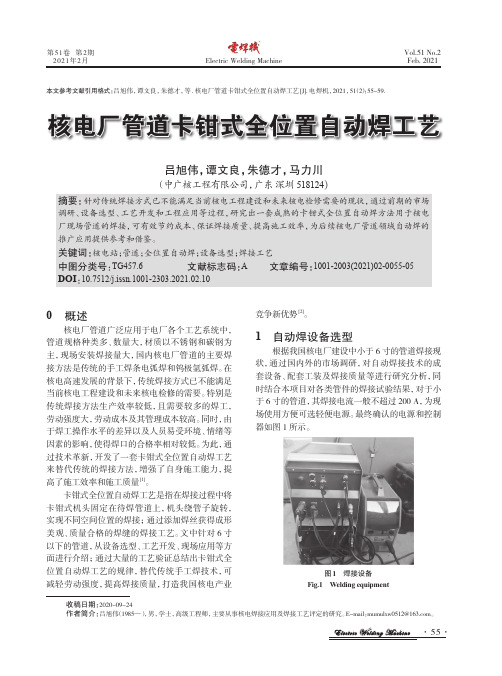
Electric Welding Machine·55·第51卷 第2期2021年2月Electric Welding MachineVol.51 No.2Feb. 2021本文参考文献引用格式:吕旭伟,谭文良,朱德才,等. 核电厂管道卡钳式全位置自动焊工艺[J]. 电焊机,2021,51(2):55-59.核电厂管道卡钳式全位置自动焊工艺0 概述 核电厂管道广泛应用于电厂各个工艺系统中,管道规格种类多、数量大,材质以不锈钢和碳钢为主,现场安装焊接量大,国内核电厂管道的主要焊接方法是传统的手工焊条电弧焊和钨极氩弧焊。
在核电高速发展的背景下,传统焊接方式已不能满足当前核电工程建设和未来核电检修的需要。
特别是传统焊接方法生产效率较低,且需要较多的焊工,劳动强度大,劳动成本及其管理成本较高。
同时,由于焊工操作水平的差异以及人员易受环境、情绪等因素的影响,使得焊口的合格率相对较低。
为此,通过技术革新,开发了一套卡钳式全位置自动焊工艺来替代传统的焊接方法,增强了自身施工能力,提高了施工效率和施工质量[1]。
卡钳式全位置自动焊工艺是指在焊接过程中将卡钳式机头固定在待焊管道上,机头绕管子旋转,实现不同空间位置的焊接;通过添加焊丝获得成形美观、质量合格的焊缝的焊接工艺。
文中针对6寸以下的管道,从设备选型、工艺开发、现场应用等方面进行介绍;通过大量的工艺验证总结出卡钳式全位置自动焊工艺的规律,替代传统手工焊技术,可减轻劳动强度,提高焊接质量,打造我国核电产业收稿日期:2020-09-24作者简介:吕旭伟(1985—),男,学士,高级工程师,主要从事核电焊接应用及焊接工艺评定的研究。
E-mail:*******************。
竞争新优势[2]。
1 自动焊设备选型 根据我国核电厂建设中小于6寸的管道焊接现状,通过国内外的市场调研,对自动焊接技术的成套设备、配套工装及焊接质量等进行研究分析,同时结合本项目对各类管件的焊接试验结果,对于小于6寸的管道,其焊接电流一般不超过200 A,为现场使用方便可选轻便电源。
管道焊接工艺方案

管道焊接工艺方案1. 引言管道焊接是工程建设中常用的连接方法之一。
为了确保管道连接的质量和稳定性,需要制定正确的焊接工艺方案。
本文将介绍一种常用的管道焊接工艺方案,包括焊接设备、焊接方法和操作流程等内容,旨在帮助读者理解管道焊接的基本原理和操作要点。
2. 焊接设备2.1 焊接机对于中小型管道焊接,常用的焊接机有手持式电弧焊接机和气体保护焊接机。
手持式电弧焊接机适用于直流电焊,操作简单,适用于一般焊接工作。
气体保护焊接机适用于气体保护焊接,如惰性气体保护焊接和活性气体保护焊接等,具有较高的焊接质量和稳定性。
2.2 焊接电极常用的焊接电极有碳钢焊丝电极、不锈钢焊丝电极等。
选择合适的焊接电极要根据管道材料和焊接要求进行确定,确保焊接强度和焊缝质量。
3. 焊接方法3.1 电弧焊接电弧焊接是一种常用的管道焊接方法。
具体操作步骤如下:1.准备工作:清理焊接部位,确保表面光洁,无油污和杂质。
2.设置电流:根据焊接电极和焊接材料的要求,设置合适的焊接电流。
3.焊接距离:保持焊枪和焊件的适当距离,一般为1.5倍焊枪咀口径。
4.焊接速度:平稳持续地推动焊枪,保持适当的焊接速度。
5.焊接角度:一般选择倾斜45度的角度进行焊接。
6.焊接顺序:从下至上,从内至外进行焊接。
3.2 气体保护焊接气体保护焊接适用于对焊接质量和焊缝外观要求较高的管道焊接工作。
具体操作步骤如下:1.准备工作:清理焊接部位,确保表面光洁,无油污和杂质。
2.气体选择:根据焊接材料和焊接要求,选择合适的保护气体。
3.预备工作:调整好气体流量和气体稳定器。
4.焊接距离:保持焊枪和焊件的适当距离,一般为10-15mm。
5.焊接速度:平稳持续地推动焊枪,保持适当的焊接速度。
6.焊接顺序:从下至上,从内至外进行焊接。
4. 焊接操作流程在进行管道焊接时,需要按照一定的操作流程进行。
以下是一种常用的管道焊接操作流程:1.准备工作:清理管道焊接部位,确保焊接表面干净无杂质。
长输管道全位置自动焊接工艺分析

长输管道全位置自动焊接工艺分析摘要:在我国各类石油化工长输管道工程建设中,长输管道工程建设朝着“更长距离、更节能、更安全环保”的方向发展。
管道全位置自动焊具有焊接效率高、焊接质量高、劳动强度低等特点,已逐渐成为焊接施工的主要工艺。
文章针对长输管道全位置自动焊施工情况进行总结对比,形成不同管径和材质的性价比最优、操控性最强的管道全位置自动焊工艺选择。
关键词:管道全位置自动焊;根焊;性价比;一次合格率1.概述管道全位置自动焊是一种借助于机械、电气等方法,使整个焊接过程实现自动化、程序化的焊接施工技术,具有效率高、质量稳定、焊缝成形美观、劳动强度低、焊接速度快、焊接过程受人为因素影响小等优点,在欧美发达国家得到了广泛的应用。
而在我国各类石油化工管道工程中,管道全位置自动焊应用的比例相对较低,随着大口径、厚壁钢、高钢级长输管道的大量建设,管道全位置自动焊已逐渐成为我国管道施工的主要焊接方法。
本文针对目前国内施工的长输管道典型管径采用的管道全自动焊工艺及设备进行性价比分析,形成不同管径和材质的管道采用最优的管道全自动焊工艺匹配。
2.管道全位置自动焊工艺使用案例自2016年开始,中俄原油管道二线、陕京四线、中靖联络线和中俄天然气东线的开工建设,除中俄天然气东线(φ1422mm)正在建设中,其余三条长输管道已全部施工完毕。
已建设完毕的三条长输管道自动焊施工及工艺情况可以看出,管道全位置自动焊综合使用比例达到50%以上,根据目前长输管道焊接工程对管道全位置自动焊的使用要求,不仅可在主线路施工中进行应用,同时也可在支线管道进行大面积推广应用。
其一,提升工作效率,自动焊接技术的焊丝熔敷速度更快,进而缩短了焊工换条的时间,有效虽短工作时间达到原先的三到四倍。
其二,焊接质量更为稳定,通常意义上的管道焊接很大程度上受到技工水平的影响。
随着科技的气体的保护,在大口径厚管壁的施工作业上更能够保证工程质量。
其三,缓解施工现场工作强度。
全自动焊接实用工艺
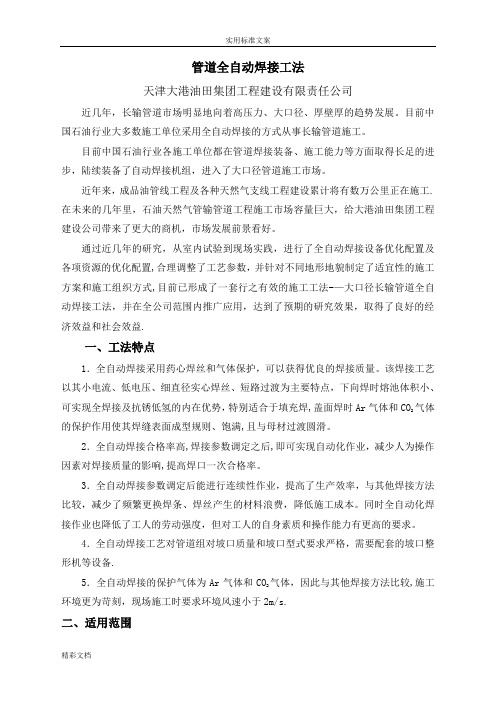
管道全自动焊接工法天津大港油田集团工程建设有限责任公司近几年,长输管道市场明显地向着高压力、大口径、厚壁厚的趋势发展。
目前中国石油行业大多数施工单位采用全自动焊接的方式从事长输管道施工。
目前中国石油行业各施工单位都在管道焊接装备、施工能力等方面取得长足的进步,陆续装备了自动焊接机组,进入了大口径管道施工市场。
近年来,成品油管线工程及各种天然气支线工程建设累计将有数万公里正在施工.在未来的几年里,石油天然气管输管道工程施工市场容量巨大,给大港油田集团工程建设公司带来了更大的商机,市场发展前景看好。
通过近几年的研究,从室内试验到现场实践,进行了全自动焊接设备优化配置及各项资源的优化配置,合理调整了工艺参数,并针对不同地形地貌制定了适宜性的施工方案和施工组织方式,目前已形成了一套行之有效的施工工法-—大口径长输管道全自动焊接工法,并在全公司范围内推广应用,达到了预期的研究效果,取得了良好的经济效益和社会效益.一、工法特点1.全自动焊接采用药心焊丝和气体保护,可以获得优良的焊接质量。
该焊接工艺以其小电流、低电压、细直径实心焊丝、短路过渡为主要特点,下向焊时熔池体积小、可实现全焊接及抗锈低氢的内在优势,特别适合于填充焊,盖面焊时Ar气体和CO气体2的保护作用使其焊缝表面成型规则、饱满,且与母材过渡圆滑。
2.全自动焊接合格率高,焊接参数调定之后,即可实现自动化作业,减少人为操作因素对焊接质量的影响,提高焊口一次合格率。
3.全自动焊接参数调定后能进行连续性作业,提高了生产效率,与其他焊接方法比较,减少了频繁更换焊条、焊丝产生的材料浪费,降低施工成本。
同时全自动化焊接作业也降低了工人的劳动强度,但对工人的自身素质和操作能力有更高的要求。
4.全自动焊接工艺对管道组对坡口质量和坡口型式要求严格,需要配套的坡口整形机等设备.气体,因此与其他焊接方法比较,施工5.全自动焊接的保护气体为Ar气体和CO2环境更为苛刻,现场施工时要求环境风速小于2m/s.二、适用范围1.本工法适用于管径DN700以上、壁厚11mm以上的油气长距离输送管道水平固定对接的全位置下向焊焊接施工。
长输管道全自动焊接单元施工方案

长输管道全自动焊接单元施工方案■刘智,毛静丽,王强,巩向楠摘要:为了真正有效提高长输管道全位置自动焊接施工工效和焊接质量,根据“人、机、料、法、环”五因素对管道全位置自动焊施工质量管理的影响,科学制定管道全自动焊接施工方案。
关键词:人员;设备;焊接施工流程;焊接方法;辅助工器具1.概述长输管道纤维素下向焊和自保护药芯焊丝半自动焊接操作技术,目前已是管道建设成熟的焊接工艺,但随着长输管道钢级的不断提高和国内外对环保问题日趋严格的要求,推广和采用全自动焊接技术进行管道施工,提高全自动焊接技术,制定科学合理的长输管道全自动焊接单元施工方案尤为重要。
传统的焊接机组(纤维素根焊+自保护药芯焊丝填盖)从人员和机械设备的配置,到施工现场的工序流程安排已经不适合全自动焊接机组的正常运转,导致全自动焊接质量和工效低于半自动焊接。
因此,如何用好全自动焊接技术,真正提高焊接质量和施工工效成为亟待解决的问题。
2.长输管道全自动焊接单元施工方案结合长输管道纤维素下向焊和自保护药芯焊丝半自动焊接施工机组的施工经验,对比分析影响施工质量和工效的制约点,针对全自动焊接技术制定科学合理的焊接单元施工方案。
例:某国外项目外输管线工程管线钢级为X52,φ508mm×8.7mm。
采用手工纤维素根焊+气保护药芯焊丝向上全自动填盖的焊接工艺施工。
(1)全自动焊接机组的人员配置分析关键岗位打破传统机组配置,执行能者上、弱者下的用人原则,具体见表1。
(2)全自动焊接机组的设备配置分析设备选型、数量按照施工要求配备,机动性、经济性、稳定性尤其重要,见表2。
(3)全自动焊接机组的材料、工具的配置分析管材、焊接材料必须有加盖红章的材质单和质量证明合格证书,工具类必须为正规类厂家生产,并具有安全生产合格证,见表3。
(4)全自动焊接机组施工方案的制定和工效分析图1为采用纤维焊条根焊,全自动气体保护药芯向上全位置全自动填充、盖面的全自动焊接机组施工的工艺流程和工作站作业内容。
- 1、下载文档前请自行甄别文档内容的完整性,平台不提供额外的编辑、内容补充、找答案等附加服务。
- 2、"仅部分预览"的文档,不可在线预览部分如存在完整性等问题,可反馈申请退款(可完整预览的文档不适用该条件!)。
- 3、如文档侵犯您的权益,请联系客服反馈,我们会尽快为您处理(人工客服工作时间:9:00-18:30)。
管道全位置管道自动焊推荐工艺1、手工焊(氩弧焊)打底+自动焊单枪焊填充盖面
工艺特点介绍
传统工艺打底,设备无需投入;
自动焊填充盖面,完美焊缝成型;
施工环境适应能力强,降低劳动强度;
设备投入少,焊工学习快,填充效率较高。
2、半自动焊打底+自动焊单枪焊填充盖面
工艺特点介绍
半自动工艺打底,适应宽,合格率高;
自动焊填充盖面,完美焊缝成型;
施工环境适应能力强,降低劳动强度;
设备投入少,焊工学习快,填充效率较高。
3、全自动内焊机打底+自动焊单枪焊填充盖面
工艺特点介绍
内焊机打底,效率高,合格率高;
自动焊填充盖面,完美焊缝成型;
遥控操作,全面降低焊工劳动强度;
焊工学习快,填充效率比较高。
4、全自动内焊机打底+自动焊双枪焊填充盖面
工艺特点介绍
内焊机打底,效率高,合格率高;
自动焊双枪填充盖面,完美焊缝成型;
自动电弧跟踪,全面降低劳动强度;
焊工学习快,填充效率最高。
5、内对口器+自动焊(单焊炬)双焊炬打底填充盖面
工艺特点介绍
单焊炬自动焊,适应管径宽;
双焊炬自动焊,焊接效率高;
自动电弧跟踪,降低劳动强度;
设备投入减少,填充效率高。