热流道的优点
热流道与冷流道

*何为热流道,何为冷流道1.冷流道:是指模具入口与产品浇口之间的部分。
塑料在流道内靠注塑压力和其本身的热量保持流动状态,流道作为成型物料的一部分,但并不属于产品。
(冷流道部分为注塑残留。
)特点:冷流道系统的优点是易于使用,也能很好地满足某些美观需求。
冷流道能够减少注塑道用来透光的丙烯酸酯或是聚碳酸酯等部分,避免注射在某些部分造成可见的带状效果。
冷流道的缺点:(1)原材料的浪费较多;(2)使整个生产过程中增加了步骤;(3)不适合多型腔系统。
2.热流道:作为注塑模具系统的一个常用部件,是通过加热的办法来保证流道和浇口的塑料保持熔融状态。
由于在流道附近或中心设有加热棒和加热圈,从注塑机喷嘴出口到浇口的整个流道都处于高温状态,使流道中的塑料保持熔融,停机后一般不需要打开流道取出凝料,再开机时只需加热流道到所需温度即可。
因此,热流道工艺有时称为热集流管系统,或者称为无流道模塑。
特点:热流道技术与常规的冷流道相比有以下的好处:(1)节约原材料,降低成;(2)缩短成型周期,提高机器效率;(3)改善制品表面质量和力学性能;(4)不必用三板式模具即可以使用点浇口;(5)可经济地以侧浇口成型单个制品;(6)提高自动化程度;(7)可用针阀式浇口控制浇口封冻;(8)多模腔模具的注塑件质量一致;(9)提高注塑制品表面美观度。
热流道技术存在缺点:(1)模具结构复杂,造价高,维护费用高;(2)开机需要一段时间工艺才会稳定,造成开价废品较多;(3)出现熔体泄露、加热元件故障时,对产品质量和生产进度影响较大。
上面第三项缺点,通过采购质量上等的加热元件、热流道板以及喷嘴并且使用时精心维护,可以减少这些不利情况的出现3.热流道系统的优势(1).热流道的直径一般比较大,而熔胶在热流道中一直保持在高温状态,所以塑流流经热流道的剪切应力(shear stress)与压力降远较流经冷流道者低,而能将同质(相对同温同压)的熔胶送到所有的浇口,这对制品(尤其是薄壁制品)的高品质注塑成型以及更多型腔的模具开发是有利的。
热流道侧进胶结构
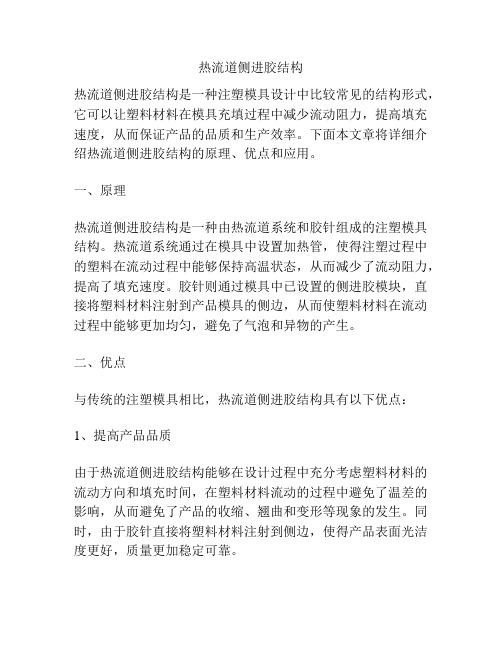
热流道侧进胶结构热流道侧进胶结构是一种注塑模具设计中比较常见的结构形式,它可以让塑料材料在模具充填过程中减少流动阻力,提高填充速度,从而保证产品的品质和生产效率。
下面本文章将详细介绍热流道侧进胶结构的原理、优点和应用。
一、原理热流道侧进胶结构是一种由热流道系统和胶针组成的注塑模具结构。
热流道系统通过在模具中设置加热管,使得注塑过程中的塑料在流动过程中能够保持高温状态,从而减少了流动阻力,提高了填充速度。
胶针则通过模具中已设置的侧进胶模块,直接将塑料材料注射到产品模具的侧边,从而使塑料材料在流动过程中能够更加均匀,避免了气泡和异物的产生。
二、优点与传统的注塑模具相比,热流道侧进胶结构具有以下优点:1、提高产品品质由于热流道侧进胶结构能够在设计过程中充分考虑塑料材料的流动方向和填充时间,在塑料材料流动的过程中避免了温差的影响,从而避免了产品的收缩、翘曲和变形等现象的发生。
同时,由于胶针直接将塑料材料注射到侧边,使得产品表面光洁度更好,质量更加稳定可靠。
2、提高生产效率由于热流道侧进胶结构所需的压力和速度相对较低,可以减少模具的磨损和损伤,同时能够在短的时间内生产出大批量的产品,从而提高了生产效率和降低了生产成本。
3、降低能耗热流道侧进胶结构需要通过加热系统来维持注塑过程中的高温状态,但是由于其采用了先进的加热技术,在加热过程中能够减少能耗和热量损失,并且在工作结束后也能够减少冷却时间和能量消耗。
三、应用热流道侧进胶结构广泛应用于各种高精度和高品质要求的注塑产品的生产中,如手机壳、汽车零部件、电子设备外壳、医疗器械零件等。
其中,由于手机市场的持续增长和消费者对产品品质要求不断提高,热流道侧进胶结构得到了广泛应用。
同时,在汽车零部件、电子设备外壳、医疗器械零件等领域,热流道侧进胶结构也得到了越来越多的应用。
总之,热流道侧进胶结构作为一种先进的注塑模具设计方案,能够提高产品品质和生产效率,降低生产成本和能耗,广泛应用于各种高精度和高要求的注塑产品生产中。
热流道在什么情况下使用?

(6)改换颜色、改换树脂
如果歧管等部件中有死角(树脂不流动的部分)或像内部加热式的热喷嘴那样有固化层,则在改换颜色和改换树脂时将花费更多时间。换言之,对于热喷嘴形式,外部加热型比内部加热型更为有型比内部加热型更为有利。
·1个模腔的尺寸偏差:
:
0.035~0.040%
·1个板块(8个模腔)的尺寸偏差:
什么情况下可以使用热流道
产品热敏性敏感的情况下
产品大或者壁薄的情况下
流道过长的情况下
产品量大的情况下
对产品外观或者精度要求高的情况下等
热流道有下列优点:
(1)由于主流道和分流道没有成型,因此无需回收利用它们。
(2)有时可进行短周期成型。
(3)有时可减少多腔成型时的尺寸偏差。
(5)消除后续工序,有利于生产自动化。
制件经热流道模具成型后即为成品,无需修剪浇口及回收加工冷浇道等工序。有利于生产自动化。国外很多产品生产厂家均将热流道与自动化结合起来以大幅度地提高生产效率。
(6)扩大注塑成型工艺应用笵围
许多先进的塑料成型工艺是在热流道技术基础上发展起来的。如PET预成型制作,在模具中多色共注,多种材料共注工艺,STACK MOLD等。
(4)减少废品,提高产品质量
在热流道模具成型过程中,塑料熔体温度在流道系统里得到准确地控制。塑料可以更为均匀一致的状态流入各模腔,其结果是品质一致的零件。热流道成型的零件浇口质量好,脱模后残余应力低,零件变形小。所以市场上很多高质量的产品均由热流道模具生产。 如人们熟悉的MOTOROLA手机,HP打印机,DELL笔记本电脑里的许多塑料零件均用热流道模具制作。
:
0.10~0.12%
·全部32个模腔的尺寸偏差:
热流道模具与冷流道模具相比
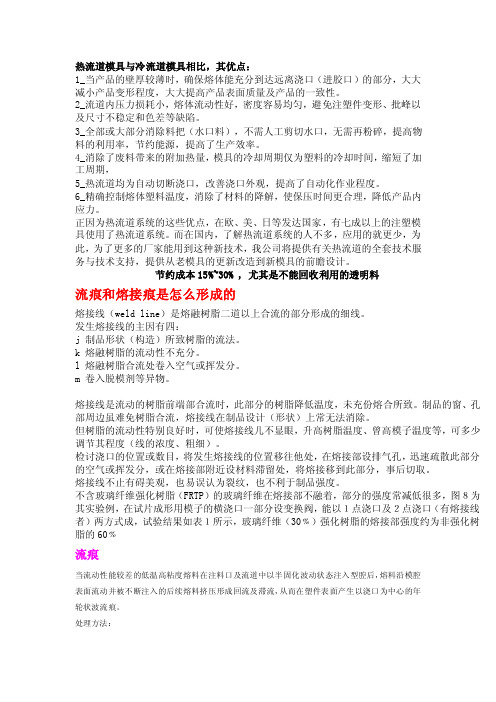
热流道模具与冷流道模具相比,其优点:1_当产品的壁厚较薄时,确保熔体能充分到达远离浇口(进胶口)的部分,大大减小产品变形程度,大大提高产品表面质量及产品的一致性。
2_流道内压力损耗小,熔体流动性好,密度容易均匀,避免注塑件变形、批峰以及尺寸不稳定和色差等缺陷。
3_全部或大部分消除料把(水口料),不需人工剪切水口,无需再粉碎,提高物料的利用率,节约能源,提高了生产效率。
4_消除了废料带来的附加热量,模具的冷却周期仅为塑料的冷却时间,缩短了加工周期,5_热流道均为自动切断浇口,改善浇口外观,提高了自动化作业程度。
6_精确控制熔体塑料温度,消除了材料的降解,使保压时间更合理,降低产品内应力。
正因为热流道系统的这些优点,在欧、美、日等发达国家,有七成以上的注塑模具使用了热流道系统。
而在国内,了解热流道系统的人不多,应用的就更少,为此,为了更多的厂家能用到这种新技术,我公司将提供有关热流道的全套技术服务与技术支持,提供从老模具的更新改造到新模具的前瞻设计。
节约成本15%~30% , 尤其是不能回收利用的透明料流痕和熔接痕是怎么形成的熔接线(weld line)是熔融树脂二道以上合流的部分形成的细线。
发生熔接线的主因有四:j 制品形状(构造)所致树脂的流法。
k 熔融树脂的流动性不充分。
l 熔融树脂合流处卷入空气或挥发分。
m 卷入脱模剂等异物。
熔接线是流动的树脂前端部合流时,此部分的树脂降低温度,未充份熔合所致。
制品的窗、孔部周边虽难免树脂合流,熔接线在制品设计(形状)上常无法消除。
但树脂的流动性特别良好时,可使熔接线几不显眼,升高树脂温度、曾高模子温度等,可多少调节其程度(线的浓度、粗细)。
检讨浇口的位置或数目,将发生熔接线的位置移往他处,在熔接部设排气孔,迅速疏散此部分的空气或挥发分,或在熔接部附近设材料滞留处,将熔接移到此部分,事后切取。
熔接线不止有碍美观,也易误认为裂纹,也不利于制品强度。
不含玻璃纤维强化树脂(FRTP)的玻璃纤维在熔接部不融着,部分的强度常减低很多,图8为其实验例,在试片成形用模子的横浇口一部分设变换阀,能以1点浇口及2点浇口(有熔接线者)两方式成,试验结果如表1所示,玻璃纤维(30﹪)强化树脂的熔接部强度约为非强化树脂的60﹪流痕当流动性能较差的低温高粘度熔料在注料口及流道中以半固化波动状态注入型腔后,熔料沿模腔表面流动并被不断注入的后续熔料挤压形成回流及滞流,从而在塑件表面产生以浇口为中心的年轮状波流痕。
热流道特点及应用
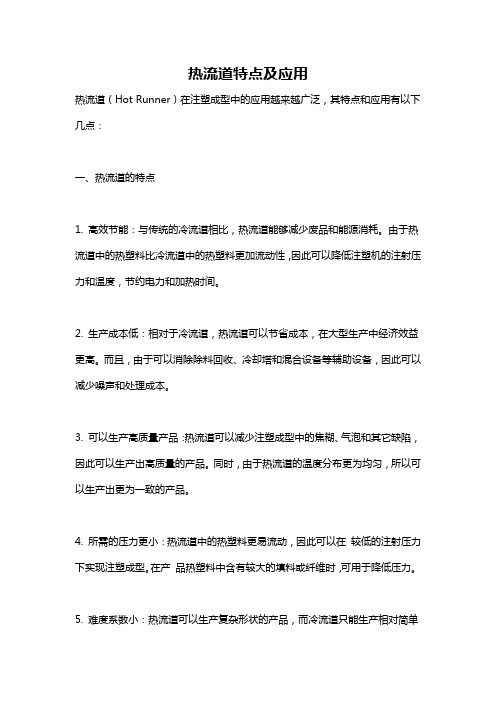
热流道特点及应用热流道(Hot Runner)在注塑成型中的应用越来越广泛,其特点和应用有以下几点:一、热流道的特点1. 高效节能:与传统的冷流道相比,热流道能够减少废品和能源消耗。
由于热流道中的热塑料比冷流道中的热塑料更加流动性,因此可以降低注塑机的注射压力和温度,节约电力和加热时间。
2. 生产成本低:相对于冷流道,热流道可以节省成本,在大型生产中经济效益更高。
而且,由于可以消除除料回收、冷却塔和混合设备等辅助设备,因此可以减少噪声和处理成本。
3. 可以生产高质量产品:热流道可以减少注塑成型中的焦糊、气泡和其它缺陷,因此可以生产出高质量的产品。
同时,由于热流道的温度分布更为均匀,所以可以生产出更为一致的产品。
4. 所需的压力更小:热流道中的热塑料更易流动,因此可以在较低的注射压力下实现注塑成型。
在产品热塑料中含有较大的填料或纤维时,可用于降低压力。
5. 难度系数小:热流道可以生产复杂形状的产品,而冷流道只能生产相对简单的形状。
二、热流道的应用1. 电子产品:电子产品中的外壳、按键、充电器以及电源插座等零部件都可以使用热流道进行生产。
2. 医疗设备和医疗器械:许多耐磨耐腐蚀的医疗器械可以使用热流道生产,如医用针头、注射器、口腔用具以及医疗监视仪器等等。
3. 家居用品:热流道可以生产许多常用的家居用品,如电水壶、吹风机、微波炉等厨房用品,同时也可以生产浴缸、花盆、灯具等家居装饰品。
4. 汽车零部件:热流道可以生产汽车内外装饰零部件,如仪表板、门板、座椅外壳、汽车灯具等。
总之,热流道注塑技术可以应用于各种现代工业,如家居、电子、汽车、医疗器械、航空等领域,可节约时间和成本,同时生产高质量的产品。
流痕和熔接痕等问题

热流道模具与冷流道模具相比,其优点:1_当产品的壁厚较薄时,确保熔体能充分到达远离浇口(进胶口)的部分,大大减小产品变形程度,大大提高产品表面质量及产品的一致性。
2_流道内压力损耗小,熔体流动性好,密度容易均匀,避免注塑件变形、批峰以及尺寸不稳定和色差等缺陷。
3_全部或大部分消除料把(水口料),不需人工剪切水口,无需再粉碎,提高物料的利用率,节约能源,提高了生产效率。
4_消除了废料带来的附加热量,模具的冷却周期仅为塑料的冷却时间,缩短了加工周期,5_热流道均为自动切断浇口,改善浇口外观,提高了自动化作业程度。
6_精确控制熔体塑料温度,消除了材料的降解,使保压时间更合理,降低产品内应力。
正因为热流道系统的这些优点,在欧、美、日等发达国家,有七成以上的注塑模具使用了热流道系统。
而在国内,了解热流道系统的人不多,应用的就更少,为此,为了更多的厂家能用到这种新技术,我公司将提供有关热流道的全套技术服务与技术支持,提供从老模具的更新改造到新模具的前瞻设计。
节约成本15%~30% , 尤其是不能回收利用的透明料流痕和熔接痕是怎么形成的熔接線(weld line)是熔融樹脂二道以上合流的部分形成的細線。
發生熔接線的主因有四:j 製品形狀(構造)所致樹脂的流法。
k 熔融樹脂的流動性不充分。
l 熔融樹脂合流處捲入空氣或揮發分。
m 卷入脫模劑等異物。
熔接線是流動的樹脂前端部合流時,此部分的樹脂降低溫度,未充份熔合所致。
製品的窗、孔部周邊雖難免樹脂合流,熔接線在製品設計(形狀)上常無法消除。
但樹脂的流動性特別良好時,可使熔接線幾不顯眼,升高樹脂溫度、曾高模子溫度等,可多少調節其程度(線的濃度、粗細)。
檢討澆口的位置或數目,將發生熔接線的位置移往他處,在熔接部設排氣孔,迅速疏散此部分的空氣或揮發分,或在熔接部附近設材料滯留處,將熔接移到此部分,事後切取。
熔接線不止有礙美觀,也易誤認為裂紋,也不利於製品強度。
不含玻璃纖維強化樹脂(FRTP)的玻璃纖維在熔接部不融著,部分的強度常減低很多,圖8為其實驗例,在試片成形用模子的橫澆口一部分設變換閥,能以1點澆口及2點澆口(有熔接線者)兩方式成,試驗結果如表1所示,玻璃纖維(30﹪)強化樹脂的熔接部強度約為非強化樹脂的60﹪流痕当流动性能较差的低温高粘度熔料在注料口及流道中以半固化波动状态注入型腔后,熔料沿模腔表面流动并被不断注入的后续熔料挤压形成回流及滞流,从而在塑件表面产生以浇口为中心的年轮状波流痕。
各种热流道系统之优缺点

各种热流道系统之优缺点
来源:热恒热流道理想的射出成形系统可以生产密度均匀的塑件,而且不需要流道,不产生毛边和浇口废料。
使用热流道系统(hot runner systems)可以达成此一目标。
热流道内尚未射进模穴的塑料会维持在熔融状态,等充填下一个塑件时再进入模穴,所以不会变成浇口废料。
热流道系统也称作热歧管系统(hot manifold systems)或无流道成形(runnerless molding)。
常用的热流道系统包括:绝热式和加热式两种。
使用绝热式流道(insulated runners) 的模具,其模板有足够大的通道,于射出成形时,接近流道壁面塑料的绝热效果加上每次射出熔胶之加热量,就足以维持熔胶流路的通畅,如图1(a)所示。
加热式流道(heated runners)系统有内部加热与外部加热两种设计。
内部加热式如图1(b),由内部的热探针或鱼雷管加热,提供了环形的流动通道。
藉由熔胶的隔热作用可以减少热量散失到模具。
外部加热式提供了内部的流动通道,并由隔热组件与模具隔离以降低热损失,如图1(c)。
表2列出三种热流道的优缺点。
采用热流道的优点介绍
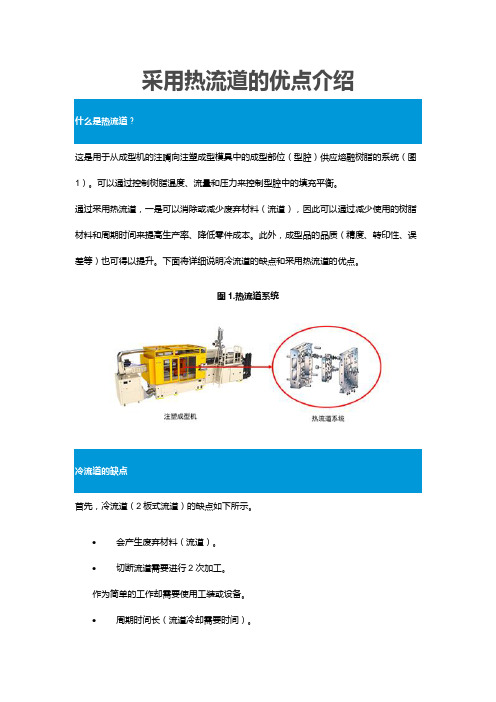
采用热流道的优点介绍这是用于从成型机的注嘴向注塑成型模具中的成型部位(型腔)供应熔融树脂的系统(图1)。
可以通过控制树脂温度、流量和压力来控制型腔中的填充平衡。
通过采用热流道,一是可以消除或减少废弃材料(流道),因此可以通过减少使用的树脂材料和周期时间来提高生产率、降低零件成本。
此外,成型品的品质(精度、转印性、误差等)也可得以提升。
下面将详细说明冷流道的缺点和采用热流道的优点。
图1.热流道系统冷流道的缺点首先,冷流道(2板式流道)的缺点如下所示。
•会产生废弃材料(流道)。
•切断流道需要进行2次加工。
作为简单的工作却需要使用工装或设备。
•周期时间长(流道冷却需要时间)。
•成型品精度(尺寸、误差等)低,转印性差。
例如一模64腔采用冷流道(图2)时,流道使用的树脂(红色部分,占总量的60%)全部报废,需要通过人工作业或自动设备将流道从产品上分离。
另外,由于流道部分的重量甚至比产品本身更重,因此流道的冷却需要更多时间,在此之前无法取出成型品,难以大幅降低运行成本。
此外,64个型腔中取出的产品质量可能会出现偏差。
图2.一模64腔冷流道型时(合计注塑重量320g)采用热流道的优点而采用热流道,可以消除冷流道的上述缺点。
A)通过排除废弃材料•可以减少树脂材料的用量。
•可以减少废弃前所需的堆放场地以及废弃费用。
•可完全消除为了再利用而进行粉碎处理时导致的异物混入以及因异物而导致的浇口堵塞。
B)通过自动切割浇口(通过分模)•无需进行浇口切割加工(二次加工)(浇口部分的质量也可稳定提高)。
•取出成型品后的产品对齐变得更容易。
C)通过消除冷流道•由于缩短了模具开闭时间、缩短了称重和注塑时间,而且流道部分不需要冷却,因此可以缩短成型周期时间(图3)。
图3.周期时间缩短D)通过在成型品部分附近进行树脂温度、流速和压力控制•可以减少型腔之间的差异,提高尺寸精度和转印性。
通过实现上述A)~D),可以降低不良率,提高生产效率和质量。
- 1、下载文档前请自行甄别文档内容的完整性,平台不提供额外的编辑、内容补充、找答案等附加服务。
- 2、"仅部分预览"的文档,不可在线预览部分如存在完整性等问题,可反馈申请退款(可完整预览的文档不适用该条件!)。
- 3、如文档侵犯您的权益,请联系客服反馈,我们会尽快为您处理(人工客服工作时间:9:00-18:30)。
热流道的优点
热流道技术,凭借其节约成本、缩短成型周期等独特的技术优势,成为塑料注塑成型工艺发展的一个重要方向。
在欧美国家,注塑生产大部分都依赖于热流道技术,
热流道技术与常规的冷流道相比的好处:
1、节约原材料,降低成。
2、缩短成型周期,提高机器效率。
3、改善制品表面质量和力学性能。
4、不必用三板式模具即可以使用点浇口。
5、可经济地以侧浇口成型单个制品。
6、提高自动化程度。
7、可用针阀式浇口控制浇口封冻。
8、多模腔模具的注塑件质量一致。
9、提高注塑制品表面美观度。
热流道技术的优点
1 .节省塑料原料
由于热流道无冷凝料。
或很小的冷料柄,基本上无冷流道浇口料不用回收,尤其是价格昂贵,不能用回料加工的塑料产品,可大大的节约成本。
应用热流道如果正常生产一般2-3个月,就可收回热流道成本。
2.提高产品质量
与双分型面的三板模相比,热流道系统内的塑料溶体温度不易下降,保持恒温,不需要像冷流道模具,以提高注射温度来补偿塑料溶体温度的下降,所以热流道内的塑料溶体更
易流动,对于大型,薄壁,难以加工的塑料产品更易成型,脱模后产品残余应力低,产品变形小,热流道系统
使浇口更小,选用针阀式热流道来注塑是理想选择。
3.提高生产率,实现自动化生产
塑料产品经过热流道模具成型后,无需修建浇口,取冷凝料柄工序,有利于浇口与产品的自动分离,便于实现生产过程自动化,缩短塑料产品成形周期。
4.强化注射机功能
热流道系统中塑料溶体有利于压力传递,流道中的压力损失较小,可大幅度降低注塑压力和锁模力,减小了注射和保压时间,在较小的注射机上更容易成型长流程的大尺寸塑性,可选择较小的
注射机和减少注射机的费用,强化了注射机的功能,改善了注塑工艺。
5.提高产品一致性和平衡性
6.热流道系统可按流变学原理人工平衡,
通过温度控制和可控喷嘴实现充模平衡,自然平衡的效果也很好,对浇口的精确控制,保证多腔成型的一致性,提高了塑件的精度。