普通铣削加工工艺
铣削加工工艺步骤
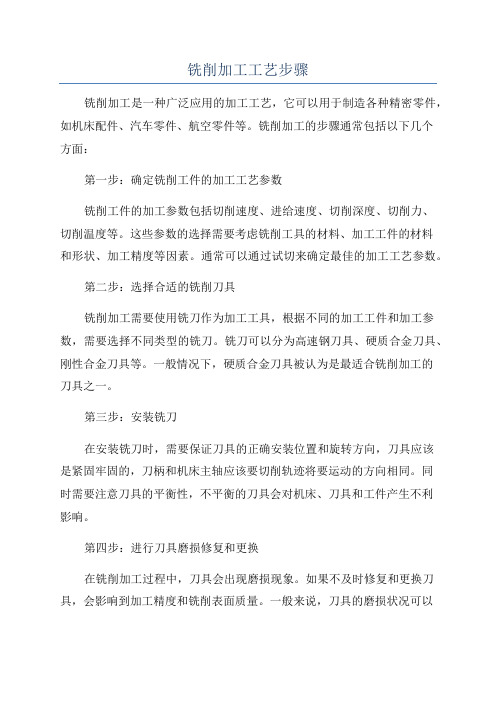
铣削加工工艺步骤铣削加工是一种广泛应用的加工工艺,它可以用于制造各种精密零件,如机床配件、汽车零件、航空零件等。
铣削加工的步骤通常包括以下几个方面:第一步:确定铣削工件的加工工艺参数铣削工件的加工参数包括切削速度、进给速度、切削深度、切削力、切削温度等。
这些参数的选择需要考虑铣削工具的材料、加工工件的材料和形状、加工精度等因素。
通常可以通过试切来确定最佳的加工工艺参数。
第二步:选择合适的铣削刀具铣削加工需要使用铣刀作为加工工具,根据不同的加工工件和加工参数,需要选择不同类型的铣刀。
铣刀可以分为高速钢刀具、硬质合金刀具、刚性合金刀具等。
一般情况下,硬质合金刀具被认为是最适合铣削加工的刀具之一。
第三步:安装铣刀在安装铣刀时,需要保证刀具的正确安装位置和旋转方向,刀具应该是紧固牢固的,刀柄和机床主轴应该要切削轨迹将要运动的方向相同。
同时需要注意刀具的平衡性,不平衡的刀具会对机床、刀具和工件产生不利影响。
第四步:进行刀具磨损修复和更换在铣削加工过程中,刀具会出现磨损现象。
如果不及时修复和更换刀具,会影响到加工精度和铣削表面质量。
一般来说,刀具的磨损状况可以通过刀具的质量控制指标来判断,切削力、加工表面质量的变化等也可以用来判断。
第五步:进行铣削加工操作在进行铣削加工操作时,需要确定加工工件的位置和机床主轴的转速。
同时,需要根据加工要求进行铣削刀具的进给和切削运动,实现加工表面的质量和精度要求。
在加工过程中,需要不断监测刀具的磨损和加工表面质量的变化,及时进行修复和调整。
第六步:完成后处理工作铣削加工完成后,需要进行后处理工作,包括加工表面的清洁和润滑等。
同时还需要对加工工艺参数、加工实际情况和工件质量进行分析和总结,为今后的铣削加工提供参考和借鉴。
铣削铝合金加工工艺
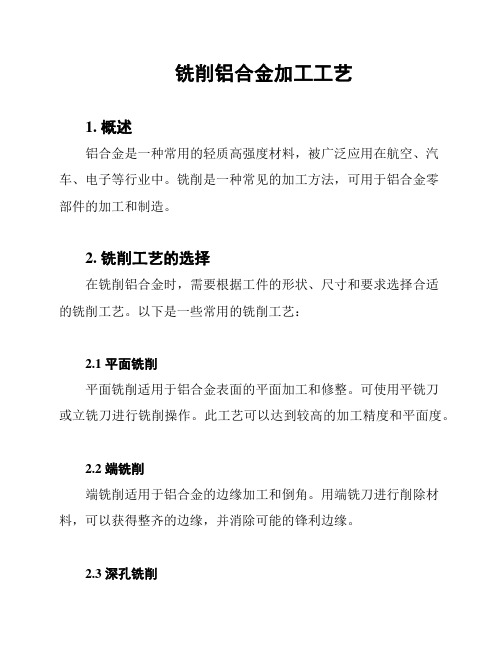
铣削铝合金加工工艺1. 概述铝合金是一种常用的轻质高强度材料,被广泛应用在航空、汽车、电子等行业中。
铣削是一种常见的加工方法,可用于铝合金零部件的加工和制造。
2. 铣削工艺的选择在铣削铝合金时,需要根据工件的形状、尺寸和要求选择合适的铣削工艺。
以下是一些常用的铣削工艺:2.1 平面铣削平面铣削适用于铝合金表面的平面加工和修整。
可使用平铣刀或立铣刀进行铣削操作。
此工艺可以达到较高的加工精度和平面度。
2.2 端铣削端铣削适用于铝合金的边缘加工和倒角。
用端铣刀进行削除材料,可以获得整齐的边缘,并消除可能的锋利边缘。
2.3 深孔铣削深孔铣削适用于铝合金工件的孔内加工。
使用长刀具,沿孔的轴线进行铣削操作。
这种工艺可以获得较深的孔内加工效果。
2.4 铣削槽加工铣削槽加工适用于铝合金工件上的槽加工。
使用槽铣刀进行切割,可以制造出各种形状和尺寸的槽。
此工艺常用于制造槽轨等零部件。
3. 加工参数调整在铣削铝合金时,需要根据具体工件和工艺要求进行加工参数的调整。
以下是一些常见的加工参数:3.1 切削速度切削速度是指刀具切削工件时的线速度。
在铝合金加工中,通常选择较高的切削速度以提高生产效率。
3.2 进给速度进给速度是指刀具在单位时间内移动的距离。
在铝合金加工中,适当的进给速度可以保证加工表面光滑,并减少刀具磨损。
3.3 切削深度切削深度是指每次刀具进入工件的深度。
在铝合金加工中,一般选择较小的切削深度以减少切削力和切削温度。
3.4 刀具选择针对不同的铝合金材料和加工工艺,选择合适的刀具是非常重要的。
常见的铣削刀具包括平铣刀、立铣刀、端铣刀和槽铣刀等。
4. 加工质量控制在铣削铝合金加工过程中,需要进行质量控制以确保加工零部件的质量。
以下是一些常用的质量控制措施:4.1 尺寸测量通过合适的测量工具,对加工零部件的尺寸进行测量和验证。
确保加工尺寸符合设计要求。
4.2 表面质量检查检查加工零部件的表面质量,包括表面粗糙度和平整度。
铣削加工教学课件PPT
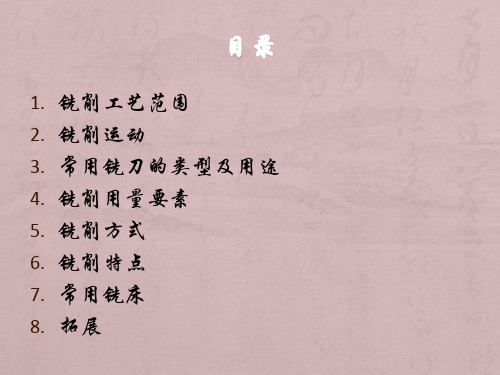
主运动:铣刀绕自身轴线的高速旋转 进给运动:工件的直线运动(加工平面或沟槽)
旋转运动(加工回转面) 直线+旋转运动(加工螺旋面) 切深运动:断续进给 背吃刀量(垂直于工作平面)+侧吃 刀量(切削运动的范围)
(1)加工平面铣刀
圆柱铣刀加工
面铣刀加工
端铣刀的几何角度
注:副偏角一般取2º~3º
γ0
圆柱铣刀切削部分的几何角度
a) 铣削钢件时,取 前角=10°~20°;铣削铸铁件时,取 前角=5°~15° b) 粗加工时取 后角=12°,精加工时取 后角=16° c) 主偏角 =90º,无副偏角(无副切削刃) d) 常用螺旋角=25º~35º,铣削宽平面螺旋角=40º~45º;精铣螺旋角小,粗铣螺旋角大
热钢
(3)端铣法与周铣法特点比较
加工质量:端铣>周铣 生产效率:端铣>周铣 工艺范围:端铣<周铣 生产批量:端铣>周铣
断续切削,力和热冲击大,振动大
a) 多刀多刃切削,刀齿易出现径向和轴向跳动。刀 具寿命降低,工件表面粗糙度加大。提高刀杆刚 性,减小刀杆与刀具的配合间隙。
b) 半封闭容屑形式。足够容屑空间,否则损坏刀齿。
表 1. 圆柱铣刀VS面铣刀
加工平面铣刀 用途
铣床类型 铣削方式 刀齿分布 铣削角度
类型
圆柱铣刀
面铣刀
加工狭长平面
加工宽大平面
卧式
立式
周铣
端铣
圆柱面
圆柱面+1个端面
铣刀轴线//被加工平面 铣刀轴线⊥被加工平面
铣削加工工艺流程分析
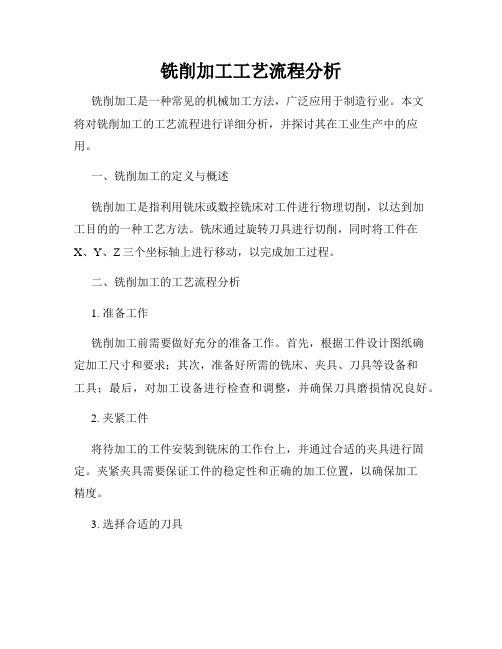
铣削加工工艺流程分析铣削加工是一种常见的机械加工方法,广泛应用于制造行业。
本文将对铣削加工的工艺流程进行详细分析,并探讨其在工业生产中的应用。
一、铣削加工的定义与概述铣削加工是指利用铣床或数控铣床对工件进行物理切削,以达到加工目的的一种工艺方法。
铣床通过旋转刀具进行切削,同时将工件在X、Y、Z三个坐标轴上进行移动,以完成加工过程。
二、铣削加工的工艺流程分析1. 准备工作铣削加工前需要做好充分的准备工作。
首先,根据工件设计图纸确定加工尺寸和要求;其次,准备好所需的铣床、夹具、刀具等设备和工具;最后,对加工设备进行检查和调整,并确保刀具磨损情况良好。
2. 夹紧工件将待加工的工件安装到铣床的工作台上,并通过合适的夹具进行固定。
夹紧夹具需要保证工件的稳定性和正确的加工位置,以确保加工精度。
3. 选择合适的刀具根据工件的材质、形状和加工要求选择合适的刀具。
刀具的选择应综合考虑切削力、切削速度和切削质量等因素,以获得最佳的加工效果。
4. 设定切削参数根据所选刀具和工件的特点,设定合适的切削参数,包括进给速度、转速、切削深度等。
切削参数的设定需要综合考虑加工效率和切削质量之间的平衡。
5. 进行铣削加工根据设定的切削参数,启动铣床,开始进行铣削加工。
在整个加工过程中,操作人员需要密切关注加工状态,确保加工精度和安全。
6. 检验加工质量铣削加工完成后,对加工后的工件进行检验和测量。
通过使用测量工具,比如千分尺、游标卡尺等,对加工尺寸进行检查,以确保加工质量符合要求。
三、铣削加工的应用领域铣削加工广泛应用于各个制造行业,特别是机械制造和零部件加工领域。
以下是铣削加工的一些常见应用领域:1. 汽车制造铣削加工在汽车制造过程中扮演着重要的角色。
通过铣削加工,可以精确地加工汽车发动机零部件、车身结构件等,提高汽车的精度和性能。
2. 航空航天工业铣削加工在航空航天工业中也起到至关重要的作用。
航空发动机的叶片、螺栓等零部件需要通过铣削加工来保证其高精度和可靠性。
典型铣削零件加工的工艺分析及编程

典型铣削零件加工的工艺分析及编程1. 引言铣削是一种常见的机械加工方法,广泛应用于零件加工领域。
在铣削加工中,我们通常需要进行工艺分析和编程,以保证零件加工的准确性和效率。
本文将针对典型铣削零件的加工过程进行工艺分析,并介绍如何进行编程。
2. 零件加工的工艺分析在进行铣削零件加工之前,我们首先需要对零件的形状、尺寸、加工材料进行分析,以确定合适的工艺路线和加工参数。
2.1 零件形状分析零件的形状对于确定铣削工艺有重要影响。
常见的零件形状包括平面零件、曲面零件、孔型零件等。
不同形状的零件需要采用不同的加工策略和工艺路线。
2.2 尺寸分析零件的尺寸要求对于决定加工工艺参数也非常重要。
尺寸分析包括零件的最大尺寸、最小尺寸、公差要求等。
根据不同的尺寸要求,我们可以选择合适的刀具和机床进行加工。
2.3 加工材料分析加工材料的硬度、韧性、热传导性等性质也会对加工工艺产生影响。
选择合适的切削速度、进给量和切削深度可以提高加工质量和效率。
3. 零件加工的编程在确定了合适的工艺路线和加工参数之后,我们需要进行编程,将加工过程转化为机床可以理解和执行的指令。
3.1 编程语言介绍目前,常用的铣削加工编程语言包括G代码和M代码。
G代码用于定义运动轨迹和加工方式,M代码用于定义辅助功能和机床控制。
3.2 编程步骤编程的步骤包括创建编程文件、选择刀具和工艺路线、编写加工指令、设定初始位置等。
在编程过程中,需要考虑刀具半径补偿、切削参数调整和刀具路径优化等问题。
3.3 编程实例以下是一个简单的铣削编程实例:1. G90 G54 G17 G40 ;刀具半径编程方式选择,选择工作坐标系,选择平面2. M3 S1000 ;主轴启动,设置主轴转速3. G0 X0 Y0 Z20 ;快速定位到初始位置4. G1 Z-5 ;快速下刀到指定深度5. G2 X50 Y0 I25 J0 F200 ;顺时针沿圆弧加工6. G1 X100 ;快速移动到指定位置7. G1 Z-10 F100 ;沿Z轴下刀到指定深度8. G1 X50 ;移动到指定位置9. G1 Z-20 ;下刀到指定深度10. G2 X0 Y0 I-25 J0 ;逆时针沿圆弧加工11. G0 Z20 ;快速抬刀12. M5 ;主轴停止13. M30 ;程序结束4. 总结本文针对典型铣削零件的加工过程进行了工艺分析,并介绍了编程的相关知识。
铣削加工工艺
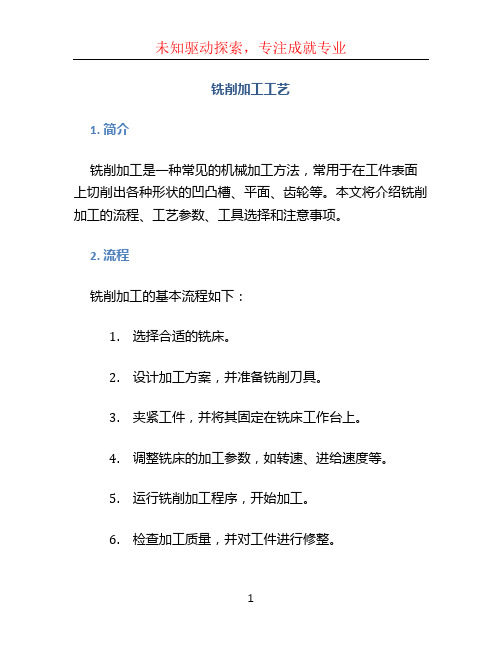
铣削加工工艺1. 简介铣削加工是一种常见的机械加工方法,常用于在工件表面上切削出各种形状的凹凸槽、平面、齿轮等。
本文将介绍铣削加工的流程、工艺参数、工具选择和注意事项。
2. 流程铣削加工的基本流程如下:1.选择合适的铣床。
2.设计加工方案,并准备铣削刀具。
3.夹紧工件,并将其固定在铣床工作台上。
4.调整铣床的加工参数,如转速、进给速度等。
5.运行铣削加工程序,开始加工。
6.检查加工质量,并对工件进行修整。
7.收尾工作和清洁。
3. 工艺参数铣削加工的工艺参数对于加工质量和效率具有重要影响,以下是常见的工艺参数:•切削速度(Cutting Speed):切削刀具在单位时间内通过工件的线速度,一般使用米/分钟(m/min)作为单位。
•进给速度(Feed Rate):每次切割刀具移动的距离。
通常用毫米/转(mm/tooth)表示。
•切削深度(Cutting Depth):切削刀具在每次进给完成后,切入工件的深度。
•切削宽度(Cutting Width):切削刀具在每次进给完成后,切削工件的宽度。
•刀具半径补偿(Tool Radius Compensation):针对切削刀具的尺寸进行补偿,保证加工尺寸的精确度。
4. 工具选择选择合适的铣刀工具对于加工质量和效率至关重要。
以下是常见的铣刀工具类型:•端铣刀:用于切削平面和轮廓。
•刀柄铣刀:用于开槽、切割等操作。
•高铣刀:用于深孔加工。
•槽铣刀:用于加工凹槽和槽口。
具体选择何种铣刀工具需要根据加工要求、工件材料和加工量来进行评估。
5. 注意事项在进行铣削加工时,需要注意以下事项:•安全操作:操作人员应戴上安全帽、眼镜等防护用品。
避免手部接触刀具,确保操作安全。
•刀具使用寿命:定期检查铣刀刃口的磨损情况,及时更换刀具,以确保加工质量。
•清洁工作:加工完成后,注意清理铣床、工作台和周围空间,保持工作环境整洁。
结论铣削加工是一种常见的机械加工方法,本文介绍了铣削加工的流程、工艺参数、工具选择和注意事项。
铣削加工工艺规范
铣削加工工艺规范操作者必须接受有关铣削加工的理论和实践的培训,并且通过考核获得上岗证,才能具备操作铣床的资格。
一、加工前的准备1. 操作者在加工前要检查图纸资料是否齐全,坯件是否符合要求。
2. 认真消化全部图纸资料,掌握工装的使用要求和操作方法。
3. 检查加工所用的机床设备,准备好各种附件,按规定对机床进行润滑和试运转。
二、装夹加工1. 在装夹各种刀具前,一定要把刀柄、刀杆、刀套擦拭干净。
2. 工件在装夹前,一定要把定位面、夹紧面、垫铁和夹具的定位、夹紧面擦干净,并不得有毛刺。
3. 铣刀的齿数应根据工件的材料和加工要求选择,一般铣削塑性或粗加工时,选用粗齿铣刀铣削脆性材料或半精加工、精加工时,选用中、细齿铣刀。
4. 在立式铣床上装夹铣刀时,在不影响铣削的情况下,尽量选用短铣刀。
5. 要保证平口钳在工作台上的正确位置,必要时应用百分表校正固定钳口面,使其与机床工作台运动方向平行或垂直。
6. 机动快速趋进时,靠近工件前应改为正常的进给速度,以防刀具与工件的撞击。
7. 在铣床上镗孔时,在不影响加工的情况下,刀杆尽可能粗、短,以增加刀杆的刚性,镗孔前钻孔余量根据孔的大小放1~4mm。
8. 镗上、下模板时必须配镗,保证孔距一致。
9. 当切断时,铣刀应尽量靠近夹具,增加切断时的稳定性。
10. 在以下情况下用逆铣:A、铣床工作台丝杆与螺母的间隙较大;B、切削深度较大时。
在以下情况下用顺铣:A、精铣时,B、铣胶木、塑料、有机玻璃等材料。
11. 粗、精加工在一台机床上进行时,粗加工后一般应松开工件待其冷却后重新装夹。
12. 铣削面放磨余量,根据面的大小和变形情况,单面放余量0.2~0.5mm。
13. 在批量生产中,必须进行首件检查,合格后方能进行继续加工。
14. 全部上下模板、固定板、垫板、卸料板、垫铁和凸非工作边等,要求在第一道加工铣并倒角后才转序,对图上未注倒角的则按附表要求倒角。
15. 对发泡模、吸塑模零件的工作边同样要求在第一道加工工序铣并倒角后才转序,对图上未注倒角的非工作边,均按1×45°倒角。
《铣削加工工艺》课件
铣削加工适用于各种金属材料的加工,如钢铁、有色金属等,尤其适用于加工平面、沟 槽、齿形等复杂形状。在航空制造业中,铣削加工广泛应用于机翼、机身和发动机部件 的制造;在汽车制造业中,铣削加工用于发动机、变速器和底盘部件的制造;在模具制
造业中,铣削加工用于模具型腔和型芯的加工。
铣削加工的发展趋势
总结词
工件表面质量不佳是铣削加工中常见的问题 之一,它可能影响工件的外观和使用性能。
详细描述
工件表面质量不佳的原因可能包括机床精度 不足、刀具磨损、切削参数选择不当等。为 了提高工件表面质量,可以采取一系列措施 ,如提高机床精度、定期检查和更换刀具、
优化切削参数等。
THANKS
感谢观看
02
切削速度是指铣刀在单位时间内所转过的弧长,通常以米/分钟为单 位。
03
进给速度是指铣刀在进给系统中每分钟所移动的距离,通常以毫米/ 分钟为单位。
04
铣削深度是指铣刀在工件表面上所切削的深度,通常以毫米为单位。
铣削深度与进给速度的确定
铣削深度的确定应根据工件的材料、硬度、铣刀的材质和规格以及加工要求等因素 综合考虑。
02
CATALOGUE
铣削加工的基本原理
铣削力的产生与影响
总结词
了解铣削力的产生原因及其对铣削加工的影响
详细描述
铣削力是铣削加工过程中的主要作用力,其产生与切削层的形成和切屑的排出 有关。铣削力的方向、大小和变化直接影响铣削加工的效率、刀具的磨损和加 工质量。
铣削加工的切屑形成与控制
总结词
掌握切屑的形成机理及切屑控制的方法
齿轮铣削是一种针对齿轮的铣削 工艺,主要用于加工各种齿轮。
齿轮铣削工艺主要采用指状铣刀 进行加工,通过调整刀具的角度 和切削参数,可以获得较好的加
铣削加工_精品文档
铣 削 要 素
a)圆周铣削
b)端面铣削
铣削. 用量要素
14
三、铣削方式
铣削方式是指铣削时铣刀相对于工件的运动和
位置关系。
它对铣刀寿命、工件表面粗糙度、铣削过程平 铣 削 稳性及生产率都有较大的影响。
方
式
铣平面时根据所用铣刀的类型(切削刃在铣刀
上的分布:圆柱面和端平面)不同,可分为圆周
.
48
加垫平行垫铁装夹工件 加垫圆棒装夹工件
压板的结构
.
49
.
上一页50
TSK万能倾斜分度盘
上.一页
51
3.万能分度头
是铣床的重要精密附件。
用途:多边形工件、花键轴、牙嵌式离合器、齿轮等圆周分度和螺旋槽加工。
在成批和大量生产中得到广泛的
应用。
.
38
二、X6132型卧式万能升降台铣床
铣床型号X6132具体含义如下:
.
39
如图所示为X6132型铣床, 它是国产铣床中最典型、应用 最广泛的一种卧式万能升降台 铣床。X6132型铣床的主要特 征是铣床主轴轴线与工作台台 面平行。结构完善,变速范围 大,刚性较好,操作方便,有 纵向进给间隙自动调节装置, 工作台可以回转45°,工艺范 围较广。
本 (1)了解铣床的种类及X6132型铣床的传动系
节 教
统;
学 (2)掌握铣床的主要部件及功用,各类铣床
要 求
的运用特点;
.
30
铣床的运动
主运动:主轴(铣刀)的回转运动 主电动机的回转运动,经主轴变速机构传递主 轴,使主轴回转。主轴转速共18级。 进给运动:工作台(工件)的纵向、横向和垂直 方向的移动。 进给电动机的回转运动经进给变速机构,分别传 递给三个进给方向的进给丝杠,进给速度各18 级。
铣削主要的加工工艺
铣削主要的加工工艺
铣削是一种高效的金属加工工艺,主要包括以下几个步骤:
1. 设计产品图纸:根据产品需求,设计出产品的CAD图纸。
2. 选择切削工具:根据产品的材料和加工要求,选择合适的铣刀头。
3. 设计切削路径:根据产品图纸,确定切削路径和加工顺序。
4. 设定机床参数:根据材料的硬度和产品要求,设定合适的切削速度、进给速度和切削深度。
5. 安装工件:将待加工的工件固定在铣床上,确保稳定性和定位准确度。
6. 开始铣削:根据切削路径和加工顺序,将铣刀头沿着工件表面进行切削。
根据需要,可能需要进行多次切削来达到最终的形状和尺寸。
7. 检查和修磨:在加工过程中,及时检查工件的尺寸和表面质量,如有需要,进行修磨以满足要求。
8. 清洁和保养:在完成铣削后,清理工作区域,对机床进行保养,以确保设备的正常运行。
铣削是一种常见的金属加工工艺,适用于各种形状和尺寸的工件,可以用于加工平面、曲面、凸轮槽等。
铣削广泛应用于机械制造、汽车制造、航空航天等行业,是一项重要的制造工艺。
- 1、下载文档前请自行甄别文档内容的完整性,平台不提供额外的编辑、内容补充、找答案等附加服务。
- 2、"仅部分预览"的文档,不可在线预览部分如存在完整性等问题,可反馈申请退款(可完整预览的文档不适用该条件!)。
- 3、如文档侵犯您的权益,请联系客服反馈,我们会尽快为您处理(人工客服工作时间:9:00-18:30)。
7.确定切削用量
(2)铣削轮廓 3齿Φ16立铣刀,材料为高速钢。铣削凸台轮廓和台阶面时分粗、 精铣削。
粗铣:背吃刀量1.8~4.8,留0.2精铣余量,侧吃刀量的范围为 4.8~11.01,也留0.2精铣余量。 查表取切削速度vc =30m/min,则主轴转速n: n=1000vc/(πD)=1000×30/(3.14×16)r/min≈600 r/min 查表取每齿进给量fz=0.1mm/r,则进给速度vf vf =0.1×3×600mm/min≈180 mm/min 精铣:侧吃刀量0.2,背吃刀量0.2。 查表取切削速度Vc =40m/min,则主轴转速n: n=1000vc/(πD)=1000×40/(3.14×16)r/min≈800 r/min 查表取每齿进给量fz=0.05mm/r,则进给速度vf: vf=0.05×3×800mm/min≈120 mm/min
模具制造技术
2020/10/21
8.填写工艺文件
根据上述分析与计算,填写如 下表的数控加工工艺卡片。
表2-1 加工工艺卡片
单位名称
工序号
程序编号
O1/ O2
工步 号
工步内容
1 铣顶面达Ra3.2,厚17
零件名称 凸模
夹具名称 平口虎钳
刀具 刀具规格 号 /mm T01 Φ100
零件材料 铸铝ZL4 使用设备
根据零件形状及加工精度要
求,一次装夹完成所有加工
内容。上平面要求表面粗糙
度为Ra3.2,铣削一次能达
到加工要求;两凸台轮廓要 求表面粗糙度为Ra3.2,分
6.选择刀具
粗、精加工两次完成;下台 铣削上平面选用标准8齿Φ100可
阶面要求表面粗糙度为
转位端铣刀。
Ra6.3,加工凸台轮廓时分 粗、精加工凸轮廓时,由于加工
主轴转速 进给速度 /r.min-1 /mm.r-1
380
240
零件图号 10-1001
车间
背吃刀量 备注 /mm 3
2
粗铣轮廓,留精加工 余量0.2
3 精铣轮廓达图纸要求
4 清理、入库
编制
审核
T02 Φ16 T02 Φ16
批准
600
180
800
120
年月日
1.8~4.8 0.2
共页
第页
模具制造技术
体ZL4铸铝小零件。
加工内容:零件的上平面,下台阶 2.选用毛坯或明确来料状况
面,90×70×3并4个角均为R10圆 角过度的凸台轮廓和Φ60深度2的 圆形凸台。
采用车间现有100×80×20的 锻铝板料代替ZL4铸铝。
加工精度:均为自由公差,上表面、 90×70×3凸台和Φ60圆形凸台轮 廓表面粗糙度均为Ra3.2,下台阶 面粗糙度为Ra6.3。
模具制造技术
2020/10/21
3.选用机床
由于零件比较简单,加工的过程中不 需要换刀,所以选用车间里现有的三 轴联动TK7640数控立式铣床。
模具制造技术
4.确定装夹方案
定位基准的选择:毛坯下表面 +两个长侧面。 夹具的选择:选用通用夹具— 机用平口虎钳装夹工件。
2020/10/21
5.确定加工方案及加工顺序
2020/10/21
粗、精加工两次完成。
外轮廓,应尽量选用大直径刀,
先用端铣刀加工工件上表面,以提高加工效率。选用Φ16的三
然后用立铣刀加工工件的两 齿平底高速钢立铣刀。
凸台轮廓。
模具制造技术
2020/10/21
7.确定切削用量
(1)铣削顶面 8齿Φ100端铣刀铣削顶面,侧吃刀量 ae=80,背吃刀量ap =3,查表取切削速 度vc =120m/min,则主轴转速n(编程 时主轴转速用S表示) n=1000vc /(πD)
◆ 项目二 板块类零件的加工
例题 凸模零件铣削加工工序卡片编制
模具制造技术
2020/10/21
工作任务
按图纸要求加工零件
模具制造技术
生产纲领:加工5件。 图2-1 凸模零件
2020/10/21
工作化学习内容
(一)编制加工工艺
1.分析零件工艺性能
该零件外形尺寸长宽高100×80×17,是 Nhomakorabea状规整的长方
=1000×120/(3.14×100)r/min ≈380 r/min 式中:vc -表示切削速度;
D-表示刀具直径。 查表取每齿进给量fz=0.08mm/r,则进 给速度vf (编程时用F表示,下同) vf =0.08×8×380mm/min
≈240 mm/min
模具制造技术
2020/10/21