1500m3高炉限产封炉及高效开炉达产实践
武钢炼铁厂5号高炉实习报告[1]
![武钢炼铁厂5号高炉实习报告[1]](https://img.taocdn.com/s3/m/04a31bd180eb6294dd886cb6.png)
武钢炼铁厂5号高炉实习目的毕业实习是我们专业重要的教学环节,是专业课教学的一个组成部分。
通过在实习厂主要岗位的生产劳动、现场参观、现场教学和讨论,培养和锻炼我们在生产现场独立工作的能力,分析问题的方法和解决问题的能力,理论联系实际的能力及科学的思维方法。
在牢固掌握专业理论知识的基础上,我们深入到武汉钢铁集团炼铁厂5号高炉,详细了解炼铁工艺流程及其主要设备,收集毕业设计所需的参数等相关资料。
在学习工程技术人员和工人师傅在长期实践中积累的丰富知识和经验的同时,我们还要学习他们勤奋工作的精神和实事求是的工作作风,学习他们的生产实际知识和为“四化”勤奋工作的精神,增强热爱专业,热爱劳动的思想。
为毕业设计的顺利进行以及以后踏上工作岗位奠定坚实的基础。
实习时间共两周,即20xx年x月x日—20xx年x月xx日实习地点武钢炼铁厂5号高炉1 武钢炼铁厂简介武钢股份公司炼铁总厂于2008年6月成立,包括烧结分厂、炼铁分厂,是武钢生产烧结矿和制钢生铁、铸造生铁的首道工序厂,具有精良的生产装备和先进的技术优势,主要经济技术指标在国内外同行业中处于领先地位。
炼铁分厂(原炼铁厂)于1957年破土动工,1958年建成投产。
经过50年的建设、改造和发展,已拥有8座现代化大型高炉,其中3200 m3的有3座,3800m3的有1座(暂未投产),年生产能力超过15 00万吨,是我国生铁的主要生产基地之一。
炼铁分厂坚持走引进、消化与自主开发之路,无料钟炉顶、软水密闭循环、环保型INBA炉渣处理系统、薄炉衬铜冷却壁、高炉专家系统等一大批当代先进的炼铁工艺广泛应用于高炉生产之中,高炉利用系数进入国际一流、国内领先水平。
武钢炼铁厂5号高炉是武钢自行投资建成的一座集国内外十余种先进技术于一身的特大型现代化高炉,于1991年10 月19日点火投产。
高炉有效容积3200 m3,共有32个风口,皮带上料,环形出铁场,设有4个出铁口,对称的两个铁口出铁,另两个检修备用,日产生铁7000t以上。
2000m3高炉开炉方案

2000m3⾼炉开炉⽅案2000m3⾼炉开炉⽅案根据⾼炉⼯程进度和公司安排,定于#年#⽉#⽇点⽕开炉,为实现安全顺利开炉和迅速达产,特制定开炉⽅案如下:⼀、成⽴开炉领导⼩组开炉前的准备⼯作⼆、开炉前的准备⼯作1、对上料系统、炉顶设备、送风系统、煤⽓系统、煤粉喷吹系统和炉前设备等进⾏全⾯、认真的检查,并进⾏12⼩时以上的联动试车,运转正常,确保⽆误后⽅可开炉。
2、蒸汽和通重⼒除尘器氮⽓管路试汽(⽓),炉前⽤压缩空⽓、氧⽓和烘烤⽤途的焦炉煤⽓管道正常要求管路畅通⽆泄漏,汽(⽓)压>0.4MPa。
3、⾼炉各种计算机监控系统、仪表、仪器安装校对完毕,运转正常。
4、上料电⼦秤安装校对完毕,准确可靠。
5、制作临时炭包,铺好并烤⼲所有渣铁沟。
6、准备好备⽤的风⼝⼩套、吹管各⼀套(风⼝∮120mm×450mm 20个,∮110mm×450mm 8个),风⼝⼆套6个。
备件科准备,7#⾼炉领取。
提前烧好热风炉,要求风温⼤于900℃,为⾼炉点⽕做好准备。
7、准备烧铁⼝氧⽓40瓶,氧⽓管1000kg,氧⽓瓶周转使⽤,氧⽓带和卡⼦2套,同时联系管道氧⽓正常供⽓。
8、准备好⽑渣罐(⼤罐)4个和铁罐6个第⼀次铁使⽤。
准备加长钻杆20根。
9、准备好开炉需要的⽆⽔炮泥和有⽔泡泥,⾼炉提供⽤量和规格。
10、准备⽊柴350m3,∮200~300mm,L=500~800mm左右,不能使⽤带油的腐烂⽊柴。
开炉前3天供应科负责送到炉台。
11、准备好开炉料,料仓上料前认真检查每个料仓,把杂物彻底清理⼲净。
(1)烧结矿⽤400m2直过料,保证所有烧结矿仓满仓(装料前24⼩时以内⼊仓,不能提前)(2)使⽤5#、6#焦炉⽣产的焦炭,提前1~2天⼊仓装满。
(3)硅⽯满仓,灰⽯ 100t,萤⽯80t。
(灰⽯不能多上,另上临时通知)开炉料要有分析并报给技术科。
12、风⼝⾯积确定开炉⽤20个∮120×450mm和8个∮110×450mm的风⼝,前期⽤西铁⼝出铁,均匀堵8个风⼝(3#、6#、10#、13#、15#、19#、23#、27#),开20个风⼝送风。
毕业设计 高炉本体设计
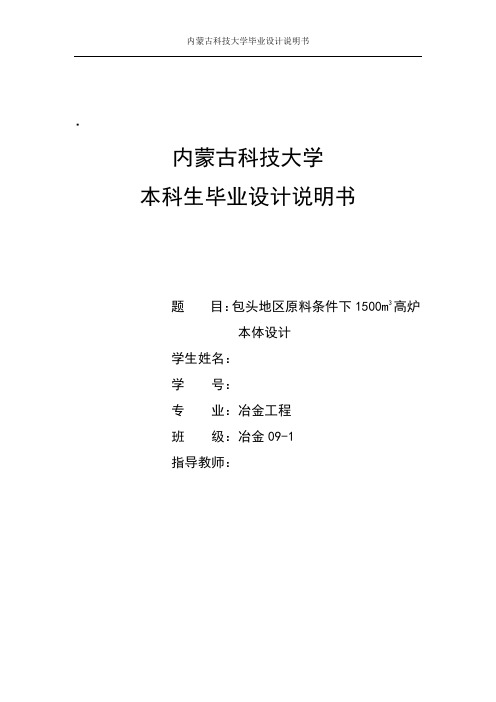
内蒙古科技大学毕业设计说明书.内蒙古科技大学本科生毕业设计说明书题目:包头地区原料条件下1500m3高炉本体设计学生姓名:学号:专业:冶金工程班级:冶金09-1指导教师:摘要高炉炼铁是获得生铁的主要手段,高炉是炼铁的主要设备,高炉本体设计是炼铁厂设计的基础。
本着优质、高产、低耗和对环境污染小的方针,长寿与高效是高炉设计与生产所追求的目标。
本设计说明书进行的详细的设计及计算,同时结合国内外一些大型高炉的先进生产操作经验及相关的数据。
力求设计的高炉做到高度机械化、自动化和大型化。
以期达到最佳的生产效益。
本设计为1500m3高炉本体设计,所设计的炼铁高炉采用的高径比为2.78,高炉的有效利用系数为2.3t/(m3٠d)。
车间采用岛式布置,出铁场采用圆形出铁场。
其炉底和炉缸采用的先进的“陶瓷杯”技术来砌筑,从而达到了隔热保温、减少热损、保护炭砖的目的。
炉腹部位用耐火度较高的铝碳转,炉腰和炉身下部用抗渣和防震较好的碳化硅砖,而炉身上部和炉喉用抗刷和抗侵蚀较好的高铝砖。
高炉冷却方法采用了炉壳喷水冷却,和板壁结合的方式达到冷却效果,其中板壁结合中用到的冷却壁有光面冷却壁、第三代和第四代冷却壁。
合适的钢结构和高炉基础设计保证了高炉的正常冶炼。
关键词高炉;炉衬;冷却系统;钢结构AbstractBlast furnace iron making is the main means for pig iron, the main equipment of iron making is blast furnace, blast furnace design of ontology is the foundation of the iron mill design. In line with high quality, high yield, low consumption and pollution to the environment policy of small, long life and high efficiency is the goal of the design and production of the blast furnace. This design manual for detailed design and calculation, at the same time, combined with some large blast furnace at home and abroad advanced production operation experience and related data. Strive to design blast furnace of high mechanization, automation and large. In order to achieve the best production efficiency.This design for 1500 m3 blast furnace body design, The design of the blast furnace high aspect ratio of 2.78,the effective utilization of blast furnace coefficient of 2.3t/(m3٠d).Workshop uses the island type layout cast house using circular cast house Blast furnace bottom and hearth uses advanced technology to building "ceramic cup", so as to achieve the heat insulation heat preservation, reduce heat loss and protect the carbon brick. Furnace belly with high refractoriness of aluminum carbon, bosh and furnace body with good slag resistance and shock-proof carborundum brick, The furnace body and brush with resistance and erosion resistance furnace throat good high alumina brick.Blast furnace cooling method USES a furnace shell water spray cooling, cooling effect and partition way, combined with the wooden partition used in cooling stave cooling wall has smooth surface, the third and fourth generation of cooling stave.Appropriate steel structure and foundation design guarantees the normal of the blast furnace smelting blast furnace.Key word: blast furnace body;the lining;of blast furnace cooling system;steel structure目录摘要 (I)Abstract (II)目录 (III)第一章文献综述 (1)1.1高炉炉型概述 (1)1.1.1高炉炉型的发展 (1)1.1.2高炉炉龄及其影响因素 (2)1.2高炉炉衬的发展 (2)1.2.1高炉各部分耐火材料的选择 (2)1.2.2我国最新对耐火材料的选择 (4)1.3高炉的冷却设备 (4)1.3.1高炉冷却的必要性 (4)1.3.2高炉冷却的目的 (5)1.3.3高炉冷却的方式 (5)1.3.4高炉各个冷却方式的发展以及优缺点 (6)1.4高炉钢结构以及高炉基础的概述 (10)1.4.1高炉的钢结构以及影响因素 (10)1.4.2我国高炉钢结构设计的基本现状 (11)1.4.3我国在高炉钢结构设计上的差距 (12)1.4.4高炉基础的概述 (13)1.5高炉设计方案 (15)第二章炼铁工艺计算 (17)2.1原料成分及参数选择 (17)2.1.1原料成分 (17)2.1.2参数选择 (18)2.2原料成分的整理计算 (19)2.2.1矿石成分补齐计算 (19)2.2.2矿石成分的平衡计算 (20)2.2.3燃料成分的整理计算 (22)2.3配料计算 (23)2.3.1吨铁矿石用量 (23)2.3.2生铁成分计算 (23)2.3.3熔剂用量计算 (24)2.3.4炉料及炉渣成分计算 (24)2.4物料平衡计算 (25)2.5热平衡计算 (29)2.5.1热收入 (29)2.5.2热支出 (30)2.6高温区热平衡计算 (34)2.6.1高温区热收入 (34)2.6.2高温区热支出 (34)2.7炼铁焦比的计算 (36)第三章高炉炉型设计 (38)3.1炉型的计算 (38)3.1.1铁口 (38)3.1.2渣口 (39)3.1.3风口 (39)3.1.4日产铁量的计算 (40)3.1.5炉缸尺寸计算 (40)3.1.6死铁层厚度 (41)3.1.7炉腰直径、炉腹角、炉腹高度的计算 (41)3.1.8炉喉直径、炉喉高度、炉身高度、炉腰高度 (41)3.2炉容的校核 (42)3.3出铁场布置 (42)第四章高炉炉衬设计 (44)4.1各部位砖衬的选择 (44)4.1.1炉底、炉缸部位的选择 (44)4.1.2炉腹部位的选择 (44)4.1.3炉身中下部及炉腰部位的选择 (44)4.1.4炉身上部及炉喉部位的选择 (45)4.2各部位砖量计算 (45)4.2.1炉底、炉缸的砌筑 (46)4.2.2炉腹的砌筑 (46)4.2.3炉腰的砌筑 (47)4.2.4炉身部位的砌筑 (48)第五章高炉冷却系统设计 (52)5.1高炉冷却设备 (52)5.1.1高炉冷却目的及方法 (52)5.1.2冷却设备 (52)5.2冷却器的工作机制 (53)5.3合理的冷却结构 (54)5.4高炉冷却系统的维护 (57)第六章高炉钢结构及基础 (60)6.1高炉钢结构 (60)6.1.1高炉本体钢结构 (60)6.1.2炉壳 (61)6.1.3炉体平台 (61)6.1.4炉体框架 (61)6.1.5热风围管 (62)6.2高炉基础 (62)参考文献 (63)致谢 (65)第一章文献综述1.1高炉炉型概述1.1.1高炉炉型的发展高炉是一种竖炉型的冶炼炉,它由炉体内耐火材料砌成的工作空间、炉体设备、炉体冷却设备、炉体钢结构等组成。
高炉铁口操作与维护 (1)

第24卷第5期2005年10月髂钦IRONMAKINGV01.24,No.50ctober2005高炉铁口操作与维护孟巍郑文玉刘明祥于君成(北台钢铁集团有限责任公司)(新疆八一钢铁集团有限责任公司)(承德钢铁集团有限公司)(三峡工业设计研究院)摘要对高炉铁口操作和维护中的若干问题进行分析。
认为提高铁口深度合格率是高炉铁口操作与维护的关键,一要控制好铁口的角度、深度、直线度、口径准确度、正点率、出铁均匀率;二要选择合理的开口机、泥炮、钻头和钻杆;三要确保炮泥质量。
关键词高炉铁口铁口深度合格率开口机1概述高炉铁口区域是炉缸内最薄弱环节之一,科学合理地维护好铁口是炉前操作的重要工作。
近年来,随着我国高炉大型化、现代化进程加快,冶炼强度的提高,给炉前操作提出了许多新要求。
笔者认为,高炉铁口的操作与维护,首先,要完成好7项炉前操作指标——即铁口深度,角度,直线度,孔道均匀度,出铁正点率,放净渣、铁,出铁均匀率;其次,要使用结构先进的泥炮和开口机,并能科学合理地操作,匹配合理的钻头钻杆,定期更换修补泥套;第三,确保炮泥质量。
只要满足上述要求,高炉铁口的操作与维护就能提高到一个新水平,这对降低铁口维护量,提高炉前工作效率,降低生产成本以及延长炉底炉缸寿命都是十分有利的。
2提高铁口深度合格率炉前7项操作指标中,最重要的是铁口深度合格率。
铁口深度合格率是铁口深度合格次数与实际出铁次数之比。
影响铁口深度合格率的原因很多,客观分析主要有以下几个方面。
2.1铁口深度合理的铁口深度是出净渣、铁的有效保障。
铁口深度是指铁口至泥包外壳的实际厚度。
要保证有效铁口深度要做好以下几点:①要稳定铁口角度;②有渣口的高炉要放净上渣;③要保证铁口(孔道)直线度;④要稳定打泥时间,保证打泥量,防止漏泥跑泥;⑤提高炮泥质量;⑥选择结构合理的泥炮、开口机;⑦要提高炉前工操作维护水平;⑧科学合理地配置钻头钻杆。
合理的铁口深度一般是炉缸原内衬加炉壳厚度的1.2~1.5倍。
安徽长江钢铁1080 m^3高炉开炉快速达产实践
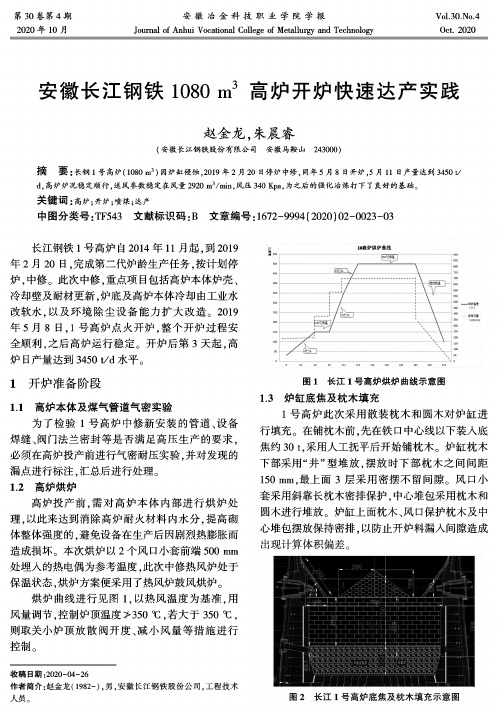
安徽冶金科技职业学院学报Journal of Anhui Vocational College of Metallurgy and Technology第30卷第4期2020年10月Vol.30.No.4Oct. 2020安徽长江钢铁1080 m 3高炉开炉快速达产实践赵金龙,朱晨睿(安徽长江钢铁股份有限公司 安徽马鞍山243000)扌商 要:长钢1号高炉(1080 n?)因炉缸侵蚀,2019年2月20日停炉中修,同年5月8日开炉,5月11日产量达到3450 t/d ,高炉炉况稳定顺行,送风参数稳定在风量2920 m 3/min ,风压340 Kpa ,为之后的强化冶炼打下了良好的基础。
关键词 :高炉;开炉;喷煤;达产中图分类号:TF543 文献标识码:B 文章编号:1672-9994 (2020) 02-0023-03长江钢铁1号高炉自2014年11月起,到2019年2月20日,完成第二代炉龄生产任务,按计划停 炉,中修。
此次中修,重点项目包括高炉本体炉壳、冷却壁及耐材更新,炉底及高炉本体冷却由工业水 改软水,以及环境除尘设备能力扩大改造。
2019 年5月8日,1号高炉点火开炉,整个开炉过程安全顺利,之后高炉运行稳定。
开炉后第3天起,高炉日产量达到3450 t/d 水平。
1开炉准备阶段1.1高炉本体及煤气管道气密实验为了检验1号高炉中修新安装的管道、设备焊缝、阀门法兰密封等是否满足高压生产的要求, 必须在高炉投产前进行气密耐压实验,并对发现的漏点进行标注,汇总后进行处理。
1.2高炉烘炉高炉投产前,需对高炉本体内部进行烘炉处理,以此来达到消除高炉耐火材料内水分,提高砌 体整体强度的,避免设备在生产后因剧烈热膨胀而 造成损坏。
本次烘炉以2个风口小套前端500 mm 处埋入的热电偶为参考温度,此次中修热风炉处于保温状态,烘炉方案便采用了热风炉鼓风烘炉。
烘炉曲线进行见图1,以热风温度为基准,用 风量调节,控制炉顶温度>350 V ,若大于350 °C ,则取关小炉顶放散阀开度、减小风量等措施进行 控制。
包钢8_高炉开炉达产实践_郝志忠

w( Al2 O3 ) ≤14% 。在实际情况中,炉内所用喷涂料 YPZ - 1 以及保护砖全部含有 50% 以上的 Al2 O3[1], 随着开炉料装入及开 炉 送 风 造 成 的 冲 击 以 及“熔
分布合理。全开风口缓解了压量关系,不堵风口可 提前插枪无需休风插枪为迅速达产创造了条件。表 3 为国内部分 4 000 m3 级高炉开炉风口面积选取情
率以及完善的事故应对预案是此次 8# 高炉能够实
现快速达产的关键因素之一。
表 2 7#和 8#高炉在开炉至达产期间
受设备影响减风次数对比
次
高炉 7# BF 8# BF
炉前 5 1
炉顶 10 0
槽下 0 0
喷煤 1 0
送风系统 1 1
3 开炉方案制定
3. 1 全炉 O /C 情况 本次开炉料全炉焦比设定为 3. 49 t / t。炉料结
湛江1高炉开炉及生产实践

3、热风炉烘炉
2015年7月21日9:00热风炉开始烘炉,采用烧嘴烘炉,COG+N2,8月25日12:00,拱 顶温度达到1100℃,更换为热风炉主燃烧器烘炉,至8月28日拱顶温度达到1300℃,热 风炉烘炉结束,共计38天。
4、高炉烘炉
2015年8月29日9:36高炉开始烘炉,9月9日14:15高炉烘炉结束。
炉腰直径
炉腰高度 炉腹高度 炉缸直径
16.2
2.4 4.6 14.5
15.2
2.6 4.0 14.0
炉缸高度
死铁层 高径比 有效高度 炉身角β 炉腹角α 风口数目 铁口数目 有效容积
5.6
3.600 2.02 32.8 81.41 74.21 40 4 5050
5.4
2.985 2.07 31.5 81.71 81.47 38 4 4350
2、炉体冷却系统
采用一串到顶的冷却方式,纯水 I 系水量 5800m3/h,纯水II系为纯水Ⅰ系统的回水增 压系统,水量2570m3/h。
纯水Ⅰ系统冷却炉底水冷管、冷却壁和红
外线摄像仪,冷却水排至脱气罐脱气后返 回泵站循环使用。 纯水Ⅱ系统冷却直吹管、风口中套、热风 炉用阀门,经脱气罐脱气后返回泵站循环 使用。 在炉底、B2和B3之间、S4和S5之间、炉顶 设有环形水管,环管之间有旁通,从而实 现高炉分段分区调整水量和热负荷(纵向 三段,周向八区)。
高炉热风炉首次采用了卡卢金顶燃式热风炉,以全烧高炉煤气(BFG)为主,同 时也能适应掺烧高热值煤气,可适应在不同阶段煤气平衡的变化; 设置热风炉烟气余热回收预热助燃空气及煤气,并配置前置预热炉预热助燃空气, 大幅提高了热风炉的热效率,有效降低热风炉能耗; 采用两烧两送交错并联的送风制度,送风温度能达到 1280℃以上,为高炉高效低 能耗操作提供了良好的条件。
包钢4150m^3高炉提高产量生产实践

表 3 2015—2017年烧结矿化学成分(质量分数)
FeO/%
CaO/%
SiO2/%
F/%
MgO/%
S/%
8.12
9.92
4.96
0.08
2.12
0.022
8.55
10.08
5.04
0.10
1.98
0.031
8.77
9.57
4.83
0.13
1.99
0.025
R 1.99 2.00 1.98
转鼓 /% 78.85 78.74 77.39
从表 2、表 3分析,原燃料质量从开炉后在逐步 下降,从表 1分析,高炉经济指标在逐步向好。
2 主要技术措施
2.1 炉型趋于合理 7#高 炉 设 计 炉 型 高 径 比 为 204,是 矮 胖 型 高
炉;投产 6个月后由于保护砖脱落进入炉型转变期, 出现炉腰处 直 径 扩 大,炉 腹 角 缩 小,高 径 比 降 低 现
2.2 优化装料制度 通过对入炉原燃料质量的日常追踪与严格管
控,积极采取应对措施以消除和应对原燃料成分及 性能对炉况产生的影响,摸索出应对原燃料成分及 性能发生大的变化时的相关应对措施;通过对炉料 的批重、布料方式及料线的探索研究。在日常操作 调整上,跟 踪 炉 墙 温 度 的 变 化,分 段 热 负 荷 曲 线 走 势,十字测温边缘点走势,十字测温形状变化规律, 压量关系,及炉顶摄像判断料面形状,依据铁水[Si] 变化判定中心与边缘下料是否匹配,边缘下料快,还 原的 Si相 对 低,而 中 心 走 料 多,还 原 的 Si相 对 高[1]。边缘走 料 长 时 间 多,中 心 料 面 形 状 滚 起 来, 十字测温形状偏胖,但炉况实际表现为中心气流偏 弱;而中心走料多,料面漏斗会加深,原燃料质量有 波 动 时,中 心 有 塌 料 现 象,致 使 炉 况 出 现 波 动。 对 Z、W值的波动范围进行研究,配合整体热负荷的变 化,确定出合理的 Z、W值运行区间。通过二年多积 累的实际经验,解放思想,大胆创新,逐渐摸索制定 中合理的布料矩阵。
- 1、下载文档前请自行甄别文档内容的完整性,平台不提供额外的编辑、内容补充、找答案等附加服务。
- 2、"仅部分预览"的文档,不可在线预览部分如存在完整性等问题,可反馈申请退款(可完整预览的文档不适用该条件!)。
- 3、如文档侵犯您的权益,请联系客服反馈,我们会尽快为您处理(人工客服工作时间:9:00-18:30)。
1500m3高炉限产封炉及高效开炉达产实践
唐山中厚板材有限公司炼铁部1#高炉(1500m3)自2006年3月份开炉达产以来,已经历了3个年头有余,各项经济技术指标良好,而进入2008年9月以后,受全球金融危机的影响,钢铁行业不景气,尤其是进入2009年2月份,钢铁市场再度进入降价狂潮,市场需求量也急剧萎缩。
为此,中厚板公司1#高炉于2009年3月2日21时开始封炉至4月23日6时16分开炉,历时长达52天9小时16分,而从送风开炉至全风达产仅用47小时,本文针对中厚板公司1#高炉封炉及开炉操作实践总结分析如下。
一、封炉操作
1、封炉料结构
中厚板公司1500m³自开炉以来首次进行封炉操作,经验不足,在借鉴唐钢经验的基础上并结合自己的实际情况制定了如下表的配料方案。
全炉焦比2.5t/tfe,负荷料焦比0.65t/tfe,全部炉料的压缩率为15%
矿批t 焦批t 烧结矿% 球团% 锰矿% 萤石t/ch R2 [Si]% 负荷灰石负数焦比Kg/tFe
23 8.618 65 30 5 0.3 1.02 1.5 2.669 0. 334 650
于2009年3月2日14:40开始下休风料,净焦60批,批重8.817t,同时带硅石10t,锰矿20t,布料采用α:O27(7),C32(5)22(5)全倒装的料制,以利于复风恢复。
2、封炉前准备操作
1)、3月1日将焦比提至400kg,料制采用的是以疏导两道气流为主,保中心气流,放边缘气流的操作方针,锰矿配至2%,萤石0.3t/ch,保证炉况稳定顺行。
2)、针对大高炉的实际情况,采取全焦冶炼封炉,提前计算好所需总煤量,与喷煤车间联系,控制好制粉量,在确保煤粉能够按时喷完的同时,又能保证高炉休风料及时下达炉缸,同时又能准时休风。
3月2日14:30焦比至650kg/tfe,18时左右停煤空喷。
3)、2月28日两铁场开口机角度由11°调至13°,以尽最大限度地出净炉缸残留渣铁,炉前备好堵风口用耐火砖及套泥。
4)、检查好各种设备,对仪表进行校验,尤其是冷却设备即风口、炉缸、炉底等冷却器进行专项检查,对已损坏的冷却设备(4#、9#、22#中套及112#开路水)要在减风时适当控制水量,对有异常情况的及时处理。
3、封炉后操作
高炉封炉期间,主要从两方面尽量减少高炉热损失:一是将风口封好,确保高炉的密封性。
3月2日21时准时休风后,立即组织人员炉顶点火,采用倒流休风点火,炉顶火点燃后,立即组织炉前人员卸吹管、风口小套,堵泥砌砖再堵泥抹平,泥的表面涂上玻璃水,以加强炉体密封,炉内人员定时点检堵泥风口,有漏处及时处理,同时,封炉期间注意观察炉顶温度、火焰;二是Ⅱ系人员加强冷却水的查漏工作,特别是进入炉役中期以后,由于高炉冷却系统存在破损,封炉期间对冷却水的管理尤为重要。
休风后两个小时,软水、高、低压工业水各停泵一台,随后根据软水温度及时控制各泵水流量,逐步降低冷却强度,直至各泵全停,软水全停后,注意观察冷却壁各区的回水温度。
二、开炉操作
1、开炉前的准备工作
1)、炉前备好开炉各种工器具,各设备送风前调试运转正常,做好出铁准备,开口机角度调至10°。
由1#场出铁,主沟沟底铺500-600mm捣打料,两侧沙坝挡好。
各风口抠净堵泥砖,
安装小套及吹管并堵泥,送风风口为1#铁口上方的15#、16#风口,送风风口面积为0.02457m2。
炉前工用氧气烧通15#、16#风口及1#铁口之间的通道,此工作耗时1天有余,消耗吹氧管8吨多。
2)、热风炉于4月19日顺利引煤气烘炉,为复风作好准备。
3)、Ⅱ系人员开炉前先恢复软水,随后安装小套前恢复低压及高压工业水,开炉前恢复九段、气密箱及炉顶打水。
4)、校队各仪表,确认各阀状态,以及确认各种介质到位。
2、复风过程
4月23日6:16送风,风量350m³/min,风压50kpa,送风后不久焦比便降至560kg/tfe。
由于封炉时间长,部分焦碳渣化,加上送风初期风量偏小,铁口喷不开,只好使用圆钢捅铁口,后又用氧气烧,直至9:28开口才从铁口烧出渣铁混合物,视主沟的承载能力以及铁口喷溅程度,堵口清理主沟,如此反复。
由于开始物理热较低,渣铁分离较差,流动性不好,人工引流,11时左右从铁口喷出的渣铁混合物已开始走干渣操作,且铁口流出的渣铁量见多,出渣铁时间已逾10min,于12:25开始逐步向15#、16#风口两侧捅风口加风,至16:45已捅开7个风口,送风风口个数扩大至9个,风量也逐步加至1350 m³/min,料尺边塌边走,送风初期主要以疏导两道气流为主,料制基本采用的是α:O29(4)26(4),C32(4)29(2)26(2)22(4)。
18:05引煤气成功,风量加至1450 m³/min,顶压提至40kpa,由于返热,19:00热悬料,放风至零坐料,右料尺塌至7.31m,左料尺塌至5.43m,逐步加风,赶料线,22:31出铁13843次铁水正式入罐,铁水物理热低,流动性差。
23:00右尺塌至3.18m,左尺塌至4.10m,至24日5:00风量加至1500 m³/min,顶压用至72kpa。
24日6:25-11:08果断休风捅风口,休风前8#风口吹开灌渣,由于炉缸工作状态不好,休风过程中10#风口灌渣,休风后将剩余风口重新捅开堵泥,并更换8#、10#吹管,送风后开10个风口送风,13:40风量加至1700 m³,至21:00风量加至2150 m³/min,顶压用至101kpa,料线赶至正常,此时料制主要采用的是α:O30(3)27(4)24(3),C34(3)31(2)28(2)24(2)15(3),随着向两边逐步捅风口加风,至25日5:21分关冷风放散阀,风量加至2800m³/min,顶压用至150kpa,料尺行走正常,压量关系较平稳,在堵着两个风口的前提下,已是全风状态,但炉温一直居高不下,Si基本维持在2.0%左右,顶温维持在300℃左右,6:00左右将焦比由560 kg/tfe 降至460 kg/tfe,反应后效果明显,炉温恢复正常,气流得到抑制。
20:50捅开最后一个风口4#,风量逐步加至3200 m³/min,顶压逐步加至195kpa,焦比已降至420 kg/tfe,由于两道气流仍然偏盛,拓宽矿石平台,以抑制气流,此阶段料制主要采用的是α:O35.5(3)32.5(4)29.5(4)26(2),C35.5(3)32.5(2)29.5(2)25.5(2)15(4),反应后气流进一步得到规整。
三、结语
1、本次1500m³高炉封炉时间之长、快速达产时间之短、成本消耗之低可谓国内同类型高炉首屈一指的。
2、周密的部署,严密的计划,稳健的操作以及长期稳定顺行的炉况是本次封炉与开炉之所以成功的重要前提保障。
3、封炉应根据高炉顺行状况、封炉时间长短、炉缸状态合理地选择封炉焦比,本次封炉焦比的选择,既保证了后续炉缸充沛的热量,又保证了整个料柱的透气透液性,是本次成功开炉的关键。
4、复风操作时,风口的选择应根据封炉时间长短而定。
封炉时间短,炉缸热量充足,可采取均匀送风,加快恢复时间;封炉时间长,炉缸透液性差,可采用铁口上方的风口送风,更能确保炉况恢复。
另外,捅风口应根据炉缸工作状况及风口明亮程度,以先捅临近铁口的风口为原则,且捅风口速度随风口与铁口距离加大而减慢,本次封炉时间长,开炉以1#铁口上方的15#、16#风口送风,以此为基准向两侧捅风口,捅风口速度快,随之加风,对于尽
快地降低炉温于正常水平,保证路况顺行意义甚大。
5、在休风及复风过程中确保了高炉稳定顺行,操作上调整及时,为炉况顺利恢复打下了良好的基础。
复风过程中没有出现大的操作失误,对炉况的快速恢复至关重要。
6、复风前坚持将两个送风风口与出铁铁口之间的通路打通,对于送风恢复以及保证渣铁尽快顺利地从铁口排出至关重要。
7、炉前出铁钻头使用的是Φ60mm的大钻头以及开口机角度的调整,都为炉内渣铁的及时排放创造了有利条件,尤其是25日12时双场的投入,对于活跃炉缸,炉况进一步恢复起了重要作用。
8、负荷料的调整对于本次开炉起了重要的作用。
由于封炉焦比选择的较高加上后续有插焦,炉温前期一直居高不下,顶温较高,两道气流也较盛,入炉焦比由650kg→560kg→460kg→420kg,降幅较大,实践证明,本次迅速的降焦比降炉温并适当恢复喷煤,使得炉内气流更加容易控制,更大大加快了炉况的恢复进程。
9、复风过程中两道气流的放收比较成功。
送风后为维持炉况顺行,加热炉墙,开始采用小批重倒装的装料制度,强烈开放两道气流。
随开炉进程逐步加重边缘,直至过渡到正常料制。
同时辅以降焦比扩矿批,以稳定气流分布,提高煤气利用率。
10、本次炉况恢复过程中唯一不足之处是由于捅风口速度较快,气流变化快,炉缸的渣铁环流流速和方向变化快,造成2#、5#、11#风口小套漏水,但对于炉况的影响不大,休风机会已更换。