注塑产品_PFMEA案例
pfmea过程潜在失效模式及后果分析案例(从原材料-加工-出货整套案例分析)

1、注射压力大 2、锁模力不够 3.模具分型面有异物
4 调节注射压力 作业准备验证,适当调
整,并进行工艺监控 清理模具分型面
产品不合格
2
C 4.塑料温度太高
调节 56
5
制品质量符合 要求
气泡
1.原料含水分、溶剂或 易挥发物
3
原料检验
2.塑料温度太高或受热 时间长,易降聚或分解
标签贴错 漏检 纸箱受潮变形 数量不准确
产品型号错
误,顾客不满 2
意
不良品混入, 影响客户使用
5
纸箱变形破损 3
顾客不满意
1
C 包装人员粗心 C 检验人员操作失误 C 纸箱堆积太高 C 仓库计数错误
3 检查、更正 3 检验、及时标记 3 检查、更正 3 检查、更正
2 42
1 21
3 18 4 60 3 27 26
3.注射压力太小
调节注射压力
4.注射柱塞退回太早 产品不合格 7 A
5.模具温度太低
调节注射温度
6.注射速度快
调节注射速度
2 42
7.在料筒加料端混入空 气
6
制品质量符合 要求
凹痕、缩水
产品不合格 7
1、流道浇口太小
4
2、塑料件太厚或厚薄 不均
3、浇口位置不当
4、注射保压时间太短 A 5、加料量不夠
过程潜在失效模式及后果分析 (PFMEA)
类型/部件: 车型年:
核心小组:
设计责任: 关键日期:
RPN DETECT
OCCUR CLASS SEV
项目
设计功能/要 求
潜在失效模式
潜在失效后果
1 原材料采购 原材料不合格
汽车大灯配光镜注塑过程PFMEA范例

FMEA编号:项目名称:大灯过程责任编制人:FMEA日期(编车型年/车辆类型:关键日FMEA日期(修页码:核心小开机潜在的失效模式及后果分析(过程FMEA)垃圾/颗粒(PZK002)外观缺陷导致报废41.模具分型面较脏;2.车间清洁度不佳51.定期保养模具;2.车间增加湿度首件点检5100按照注塑开机标准作业书进行开机43448成形不足(PZK003)外观及功能缺陷导致报废51.模温、热流道温度未达到生产要求;2.注塑量不足;3.螺杆内有混有空气41.模具生产前预热;2.按照注塑工艺文件对生产工艺进行点检;3.充分清洗螺杆首件点检360按照注塑开机标准作业书进行开机53345银光丝(PZZ001)外观缺陷导致报废51.注塑速度过快;2.热流道、螺杆温度过高;3.模温过高;4.螺杆、针阀逃料41.按照注塑工艺文件对生产工艺进行点检;2.定期保养清理热流道针阀;3.定期对机床螺杆进行保养;1.按照质量管理点对产品全数检查2.班组长每班定时巡检480无垃圾/颗粒(PZZ002)外观缺陷导致报废41.模具分型面较脏;2.车间清洁度不佳;3.静电风机未开;4.机械手夹具太脏41.定期保养模具;2.车间增加湿度;3.静电风机点检;4.定期更换夹具夹片;1.按照质量管理点对产品全数检查2.班组长每班定时巡检696无成形不足(PZZ003)外观及功能缺陷导致报废51.模温、热流道温度未达到生产要求;2.注塑量不足;3.螺杆内有混有空气31.模具生产前预热;2.按照注塑工艺文件对生产工艺进行点检;3.充分清洗螺杆;4.定期保养模温机,更换老化水道1.按照质量管理点对产品全数检查2.班组长每班定时巡检690无气斑(PZZ004)外观缺陷导致报废51.注塑速度过快;2.热流道温度过低;3.模具排气不良5按照注塑工艺文件对生产工艺进行点检;1.按照质量管理点对产品全数检查2.班组长每班定时巡检41001.模具分型面开排气槽; 2.启用压缩注塑功能534601-d-1开机1-d-2注塑设备故障设备导致产品无法生产51.螺杆加热系统损坏;2.安全保护装置失灵;3.锁模装置损坏;4.人为误操作损坏设备31.按照注塑开机标准作业书进行开机;2.定期对设备维护每天对设备进行设备点检230无1-d-3剪浇口破坏产品有效面外观,浇口修剪不平整外观缺陷造成报废4 1.操作人员手套不洁净;2.操作人员动作不规范;3.工具不良41.定期更换手套及操作工具;2.按照作业指导书进行操作;3.员工培训 1.按照质量管理点对产品全数检查2.班组长每班定时巡检464无污染产品表面外观缺陷造成报废3 1.操作人员手套不洁净;2.料车较脏21.定期更换手套;2.按照标准清洁料车班组长每班定时巡检424无产品有效面碰伤外观缺陷造成报废3 1.操作人员动作不规范;2.产品摆放不合理2 1.按照作业指导书进行操作;2.按照存放工艺卡放置产品;3.员工培训班组长每班定时巡检424无1e移至车间物流产品损坏导致产品报废4物流人员拉取过多2严禁超过最大拉取数量物流人员平稳拖运648无1f堆场存储表面尘点较多和产品混放导致产品报废,造成产品错装21.堆场混乱;2.堆场标识不清;3.堆场环境较差3对堆场进行目视化管理;增加清洁次数物流人员按标识拉取产品636无1g移至装配车间产品散落导致产品报废4物流人员拉取过多2严禁超过最大拉取数量物流人员平稳拖运648无标记处数标记日期1-d-4取放产品更改文件号签字日期处数更改文件号签字。
PFMEA(汽车产品塑胶件分析案例)
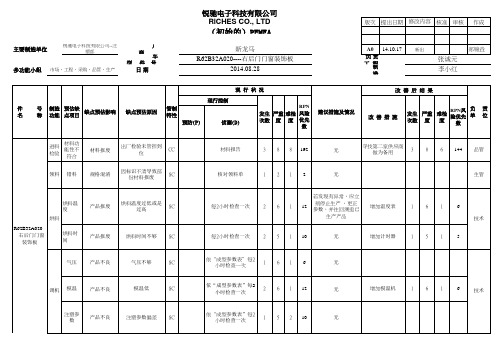
材料报废
出厂检验未管控到 位
CC
领料 错料
规格混淆
因标识不清导致部 份材料报废
SC
材料报告
3 8 8 192
核对领料单
1 21 2
无
寻找第二家供应商 做为备用
3
8
6 144
品管
无
生管
烘料温 度
烘料
R62B32A020---右后门门窗
装饰板
烘料时 间
产品报废
烘料温度过低或是 过高
SC
产品报废
烘料时间不够 SC
主要制造单位
锐驰电子科技有限公司--注 塑部
多功能小组 市场、工程、采购、品管、生产
厂 商车 型 件号 日期
锐驰电子科技有限公司 RiCHES CO., LTD
(初始的)PFMEA
新龙马 R62B32A020----右后门门窗装饰板
2014.08.28
版次 提出日期 修改内容 核准 审核 作成
A0 14.10.17 新出
发生
严重
难检
RPN风 险优先
负 单
责 位
次数 度 度 数
尺寸
报废
1.注塑工艺参数 (模温、压力、射 速)调试不当。
3
8
2
48
由专门人员进行调 试,必要时进行培训 。
由专职技术员调试 并记录到成型参数 表,首未件对比测
量
2
8
1
16
2.读数错误
SC
首未件检 测
依“成型参数表” 每2小时检查一次
2 8 5 80
3 7 4 84 由专门人员负责保养 第一个岗位人员需 2
7
3
42
要对每个产品外观
塑胶件PFMEA 样例
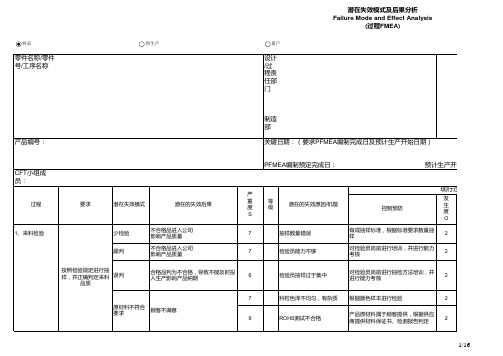
设计/过程责任部门 制造部 关键日期:(要求PFMEA编制完成日及预计生产开始日期) PFMEA编制预定完成日: 预计生产开始日:
严 重 度 S 6
现行过程
等 级 潜在的失效原因/机理 控制预防 发 生 度 O 7
包装箱规格使 造成产品擦伤,导致顾客投诉 用错误
未依据《作业指导书》的包 装要求执行
依据《作业指导书》实施
现行过程
等 级 潜在的失效原因/机理 控制预防 发 生 度 O 2
Байду номын сангаас过程
要求
潜在失效模式
潜在的失效后果
少检验 根据出货检验标准正 漏判 确判定是否可以出货 误判
不合格品进入公司 影响产品质量 不合格品流出公司 顾客投诉 合格品判为不合格, 影响纳期 顾客抱怨
7
抽样数量错误 检验员能力不够
做成抽样标准,根据标准要求数量抽 样 对检验员岗前进行培训,并进行能力 考核 对检验员岗前进行抽检方法培训,并 进行能力考核
现行过程
等 级 潜在的失效原因/机理 控制预防 发 生 度 O 3 模温监控、 成型工艺监控、 3 3 做成生产工艺卡, 根据工艺卡调机 4 3 3 根据生产工艺卡, 模温监控、 成型工艺监控 4 7 3 根据生产工艺卡, 成型工艺监控 根据生产工艺卡, 成型工艺监控 模具定期保养、维护 开机前清洗模具 按照产品《作业指导书》作业 3 3 4 4 3 7
样品 预生产 量产
零件名称/零件号/工序名称 产品编号: CFT小组成员:
严 重 度 S 6 6
设计/过程责任部门 制造部 关键日期:(要求PFMEA编制完成日及预计生产开始日期) PFMEA编制预定完成日: 预计生产开始日:
现行过程
等 级 潜在的失效原因/机理 控制预防 发 生 度 O 7 7
完整实用的过程PFMEA实例(注塑企业)
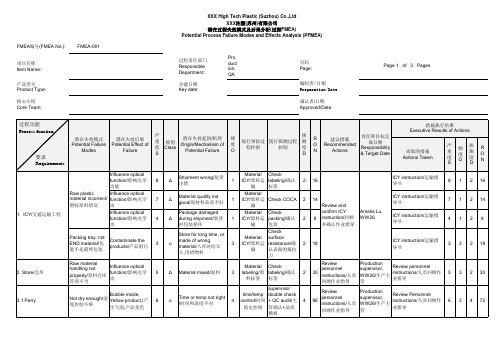
过程责任部门 Responsible Department:
Pro duct ion, QA
关键日期 Key date:
页码 Page:
编制者/日期 Preparation/Date
确认者/日期 Approved/Date
Page 1 of 3 Pages
பைடு நூலகம்
过程功能
Process function 要求
Imaging lens Dia.,
Dim 1: 5.78±0.03 Influence out of spec./镜头 assembly/影响装配
3
直径尺寸超规
Review PM mould
Order start
Production personnel instruction,
o
Wrong insert/嵌入错误
Contaminate the products/产品脏污
3
2. Store/仓库
Raw material handling not properly/原料仓库 管理不当
Influence optical function/影响光学 功
5
3.1 Perry
Not dry enough/湿 度控制不够
1
release
Dim check/尺
plan/订单开 寸确认
2
6
PM mould /点检 磨具
supervisor, incoming inspection WW26/生产主 optical inserts/人员回顾
时包装损坏
输
包装
并确认作业指导
ICY instruction/运输指 导书
ICY instruction/运输指 导书
塑胶产品易开裂物料 PFMEA 模板-(1

清理完成后技术员对清理工 作确认,用无尘布擦拭,无 脏污即可(详见换料作业指
导书进行作业) 技术员开机前对材料进行核 对确认是否按照规范做业。
技术员对加料人员设定的干 燥温度及时间进行确认,选
用设备进行确认.
材料在炮筒停留时间适 当,生产出外观、功能 合格的产品
成型机台与实际零件重量不匹 配,导致材料降解
7 材料在炮筒停留时间过长
成型周期设置不合理,导致生产 7 材料在炮筒停留时间过长 周期过长,导致材料降解
生产设备性能稳定可 靠,产品一致性好,支 持批量生产
螺杆磨损造成储料不稳定或驱动 曲臂磨损造成锁模不稳定,机台 稳定性差,产品一致性不好,可 能出现小概率的不良品
8
注塑机台维护不到位
模温符合理、正确,生 实测多点模温偏低,导致熔接线 8 实测模具温度不够高,致零件内
产出外观、功能合格的 位置强度下降、开裂
应力偏大
产品
注塑压力合理、正确, 注塑压力过大,使产品内应力大 8 注塑压力过大
生产出外观、功能合格
的产品
速度过快会导致材料温度上升而 8 小浇口情况下,注塑速度过快
5
设备维护不到位
生产前5模样品需废弃, 生产前10模内注塑机参数还不稳 5 生产过程控制不完善
10模后注塑趋于稳定, 定,产品一致性不好,不良率高
产品一致性好
8 零件清洗工艺缺失、或不彻底 金属镶件有油污,跟塑胶材料不
兼容
清洗外观、油污的溶剂跟塑胶材 8 清洗剂选择错误 料不兼容
8 模具上模前保养不规范 顶针油、润滑油等模具用油接触
过大,导致材料降解;背压过 小,导致熔胶内气体量过大,材 料易局部降解,产品易产生气 泡,开裂。
印刷注塑PFMEA失效模式分析范例

机种名称: FMEA日期: 制 定:
修 订: 审 核:
严
频
制程功能 潜在失效模式 潜在失效效应
重 度
潜在失效起因
发 度
(S)
(O)
现行控制方式
生产日期:
核 准:
探 测 度
风 险 序 数
(D) RPN
建议改善方案及优先级
编
号:
版
本: A0
第1页 共1页
措施结果
执行单位 责任人
实际改善措施
3
75
车间领班、品管参与监督:要求 干燥时间≥4小时
邹勇
加料员与领班、品管共同 确认:干燥时间应为4H以 5 上
3
3 45
正常生产每3万模次进行保养一
正常生产每3万模次进行
3 72 次;隔数日再生产之前,进行需 邹勇 保养一次;隔数日再生产 4 3 3 36
检修保养
之前,需进行检修保养
注塑
产品缺料/尺 与相关件配合不到 寸偏差/变形 位/不能装配
识 ②印刷面首件确认,每2
6
2
3 36
目
小时核对一次
转序
防护不当
划伤/折伤
4
物料转序防护不到位,作业 员操作不当
5
①用物料车整卷进行周转 ②各管理人员不定时监督稽查
①导入使用吸塑盘转序 4 80 ②对作业员转序作业规范进行培 曾金镇 使用吸塑盘进行周转
训及宣导
4 3 3 36
印刷
印刷颜色差异
与样件不一致,导 致不良报废
4
72
①成型模做方向标识防呆 ②SOP上突出此漏失
梁德刚
①成型模做防呆方向标识 ②SOP已突出此漏失
PFMEA风险分析评估范例

产品型号/Product Model: / 关键日期/ Key Date:2017年8月16日 FMEA日期 FEMA date:2017年8月16日修订revised by:2018年9月25日核心小组:XX,XXX,XXX,XXX,产品型号/Product Model: / 关键日期/ Key Date:2017年8月16日 FMEA日期 FEMA date:2017年8月16日修订revised by:2018年9月25日核心小组:XX,XXX,XXX,XXX,产、设备每日点检;备每日点检;产品型号/Product Model : / 关 键 日 期/ Key Date :2017年8月16 日 FMEA 日期 FEMA date :2017年8月16日 修 订revised by :2018年9月25日核心小组:XX,XXX,XXX,XXX,产、设备每日点检、上线前试产、设备每日点检专检验、上线前试产、设备每日点检产品型号/Product Model: / 关键日期/ Key Date:2017年8月16日 FMEA日期 FEMA date:2017年8月16日修订revised by:2018年9月25日核心小组:XX,XXX,XXX,XXX,产品型号/Product Model: / 关键日期/ Key Date:2017年8月16日 FMEA日期 FEMA date:2017年8月16日修订revised by:2018年9月25日核心小组:XX,XXX,XXX,XXX,产品型号/Product Model: / 关键日期/ Key Date:2017年8月16日 FMEA日期 FEMA date:2017年8月16日修订revised by:2018年9月25日核心小组:XX,XXX,XXX,XXX,产品型号/Product Model: / 关键日期/ Key Date:2017年8月16日 FMEA日期 FEMA date:2017年8月16日修订revised by:2018年9月25日核心小组:XX,XXX,XXX,XXX,产品型号/Product Model: / 关键日期/ Key Date:2017年8月16日 FMEA日期 FEMA date:2017年8月16日修订revised by:2018年9月25日核心小组:XX,XXX,XXX,XXX,产品型号/Product Model: / 关键日期/ Key Date:2017年8月16日 FMEA日期 FEMA date:2017年8月16日修订revised by:2018年9月25日核心小组:XX,XXX,XXX,XXX,功能不良不能达到产品的使用效果,消费者投诉原材料不合格,导致产品品质不合格,达不到预期用途;1严格按照原料标准采购原材料,定期进行产品检测。
- 1、下载文档前请自行甄别文档内容的完整性,平台不提供额外的编辑、内容补充、找答案等附加服务。
- 2、"仅部分预览"的文档,不可在线预览部分如存在完整性等问题,可反馈申请退款(可完整预览的文档不适用该条件!)。
- 3、如文档侵犯您的权益,请联系客服反馈,我们会尽快为您处理(人工客服工作时间:9:00-18:30)。
共 4页 编制
最初编 制日期
FMEA 编号
201
FMEA 版本号
A
电话号码
FMEA 最新 更改日期
过程
要求
潜在失效模式 潜在的失效后果
严
重 等 潜在的失效原因/
度级
机理
S
控制预防
产品表面缩水
产品外观不合格 顾客抱怨
产品尺寸偏大 与相关零件不匹配,
或偏小
使顾客不满意
4、注塑成型
通过注塑机和模 产品表面烧焦 具成型生产出颜 色、外观、尺寸 、性能合格的产
2
《成型条件表》每班 次点检
4
48
2/16
编号: 总成
零件名称/零件号/工 序名称
产品编号:
CFT小组成 员:
分总成
潜在的失效模式及后果分析-PFMEA
零件
设 计/ 过 程 责 任 部 门
制 造 部
关键日期:(要求PFMEA编制完成日及预计生产开始日期)
Hale Waihona Puke PFMEA编制预定完成日:
预计生产开始日:8
9/16
2013-01
A/0
措施结果 R
ODP N
10/16
2013-01
A/0
措施结果 R
ODP N
11/16
2013-01
A/0
措施结果 R
ODP N
12/16
2013-01
A/0
措施结果 R
ODP N
13/16
2013-01
A/0
措施结果 R
ODP N
14/16
2013-01
A/0
不正确
作业
7
PQC巡检、操作员 100%检验
2
6、PQC、FQC检
误判
验/对产品外观 根据检验标准正
将合格品判定为不合 格品,影响纳期
6
检验员未按检查 指导书要求进行 检验
对检查员进行教育,并考 核
2
6
、尺寸等进行验 确判定产品是否
证,使其符合客 户要求
合格
漏检
将不合格品判定为合 格品,造成不良品出 6 货,导致顾客投诉
现行过程
发
探
生 度
控制探测
测 度
O
D
3
4
开机设定确认,
3 首件检查、PQC巡 4
检、自检
3
4
开机设定确认,
4
检验员首检、末
3
3
检,对产品关键装配 尺寸进行检查
3
3
2
4 开机设定确认,
2
首件检查、PQC巡检
7 、自检
2
3
3
3 首件检查、PQC巡检 4 、自检
措施结果
R P N
建议 措施
责任目 标/完成
PFMEA编制预定完成日:
预计生产开始日:8
共 4页 编制
最初编 制日期
FMEA 编号
201
FMEA 版本号
A
电话号码
FMEA 最新 更改日期
过程
要求
潜在失效模式 潜在的失效后果
3、注塑烘料
烘干原材料,生
烘干温度偏差
产品外观不合格 顾客抱怨
产出颜色、外观
、尺寸、性能合
格的产品
烘干时间偏差
产品外观不合格 顾客抱怨
2 投料前确认、记录
2
措施结果
R P N
建议 措施
责任目 标/完成
日期
采取的 措施
S
56 56
48 56 108 32
1/16
编号: 总成
零件名称/零件号/工 序名称
产品编号:
CFT小组成 员:
分总成
潜在的失效模式及后果分析-PFMEA
零件
设 计/ 过 程 责 任 部 门
制 造 部
关键日期:(要求PFMEA编制完成日及预计生产开始日期)
控制探测
测 度
O
D
7
抽样数量错误
做成抽样标准,根据标准 要求数量抽样
2 检验记录表班长确认 4
7
检验员能力不够
对检验员岗前进行培训, 并进行能力考核
2
4
6
检验员能力不够
对检验员岗前进行抽检方 法培训,并进行能力考核
2
4
措施结果
R P N
建议 措施
责任目 标/完成
日期
采取的 措施
S
56 56
48
9、入库成品库
品
产品外观不合格 顾客抱怨
产品缺胶
影响顾客装配 顾客抱怨
注射压力小
6
冷却时间短
模温监控、 成型工艺监控、
模具温度高
注射压力过低或
7
◇
过高 冷却时间过长或
做成生产工艺卡, 根据工艺卡调机
过短
注塑速度快
排气不良
根据生产工艺卡,
6
模具表面温度过 高
模温监控、 成型工艺监控
注射位置设置不
当
8
注射压力小
根据生产工艺卡, 成型工艺监控
8
检验员抽样过于 对检验员岗前进行抽检方
集中
法培训,并进行能力考核
2
4
料粒色泽不均 匀,有杂质
根据颜色样本进行检验
2 投料前确认、记录
4
该产品原材料属于顾客提
ROHS测试不合格 供,根据供应商提供材料
2
6
保证书、检测报告判定
领料员未依据生 产任务通知单进 行实物确认
对领料员、仓库管理员进 行岗前教育
脱模不良
产品变形、拉坏 影响外观
产品表面油污
产品产品碰伤 、划伤
产品外观不合格 顾客抱怨
产品外观不合格 顾客抱怨
潜在的失效模式及后果分析-PFMEA
零件
设 计/ 过 程 责 任 部 门
制 造 部
关键日期:(要求PFMEA编制完成日及预计生产开始日期)
PFMEA编制预定完成日:
预计生产开始日:8
共 4页 编制
产品编号:
CFT小组成 员:
分总成
潜在的失效模式及后果分析-PFMEA
零件
设 计/ 过 程 责 任 部 门
制 造 部
关键日期:(要求PFMEA编制完成日及预计生产开始日期)
PFMEA编制预定完成日:
预计生产开始日:8
共 4页 编制
最初编 制日期
FMEA 编号
201
FMEA 版本号
A
电话号码
FMEA 最新 更改日期
72
72 36 30
7、包装
依据产品《操作 /包装指示》, 对产品进行包装
5/16
编号: 总成
零件名称/零件号/工 序名称
产品编号:
CFT小组成 员:
分总成
潜在的失效模式及后果分析-PFMEA
零件
设 计/ 过 程 责 任 部 门
制 造 部
关键日期:(要求PFMEA编制完成日及预计生产开始日期)
PFMEA编制预定完成日:
日期
采取的 措施
S
72 72 72 84 63 72 48 84 54 96
3/16
编号:
总成 零件名称/零件号/工 序名称
分总成
产品编号:
CFT小组成 员:
4、注塑成型 过程
通过注塑机和模 具成型生产出颜 色、外观、尺寸 、性能要合求格的产 潜在失效模式
品
潜在的失效后果
产品缺胶
影响顾客装配 顾客抱怨
7 入库前包装检验
5
作业员方法不正 确
依据《作业指导书》实施
3 入库前包装检验
未依据《作业指
6
导书》的包装要 依据《作业指导书》实施
7 入库前包装检验
求执行
措施结果
探 测 度
R P N
建议 措施
责任目 标/完成
日期
采取的 措施
S
D
3 45
3 45
3 45
2 98 6 90
2 84
6/16
编号: 总成
FMEA 版本号
A
电话号码
FMEA 最新 更改日期
过程 1、来料检验
2、生产领料
要求
潜在失效模式 潜在的失效后果
严
重 等 潜在的失效原因/
度级
机理
S
现行过程
控制预防
发
探
生 度
控制探测
测 度
O
D
少检验
不合格品进入公司 影响产品质量
7
抽样数量错误
做成抽样标准,根据标准 要求数量抽样
2 检验记录表班长确认 4
顾客抱怨 顾客抱怨
包装箱规格使 造成产品擦伤,导致
用错误
顾客投诉
严
重 等 潜在的失效原因/
度级
机理
S
控制预防
现行过程
发 生 度 O
控制探测
包装材料质量问 题
IQC来料检验
入库前包装检验
5
封箱方式不正确
3
作业员漏封
依据产品《作业指导书》 实施
入库前包装检验
7
作业员一次填写 作业员一次写一种标签, 多种产品标签 依据产品《作业指导书》
检验员能力不够
对检查员进行教育,并考 核
2
6
产品包装数量 不正确
产品标签标识 不符合顾客要 求
顾客抱怨 顾客抱怨
4
作业员工作失误
3
PQC巡检 、FQC、操 作员100%自检
3
5
作业员工作失误
做成《作业指导书》,根 据规程作业