薄板坯连铸机低碳钢塞棒上涨原因探讨(炼钢生产技术会议))
板坯连铸机粘结漏钢的原因分析及预防 刘雷锋

板坯连铸机粘结漏钢的原因分析及预防刘雷锋摘要:随着连铸技术的发展和广泛应用,连铸坯的质量和品质受到了人们的广泛关注,提高连铸坯的质量成为连铸生产中重点关注的问题之一。
连铸过程开始广泛运用于有色金属行业,尤其是铜和铝。
连铸技术迅速发展起来。
本文对此进行了分析研究。
关键词:坯;连铸;连铸工艺连铸漏钢是个常见现象。
钢水在结晶器内形成坯壳,连铸坯出结晶器后,薄弱的坯壳抵抗不住钢水静压力,出现断裂而漏钢。
对于薄板坯连铸来说更易发生漏钢事故。
漏钢对连铸生产危害很大。
即影响了连铸车间的产量,又影响了连铸坯的质量,更危及操作者的安全。
因此,降低薄板坯连铸漏钢率是提高生产效率,提高产量,提高产品质量,降低成本的重要途径。
现对某厂自2008~2013年薄板坯漏钢率进行统计。
2008年漏钢率达0.56%;2009年漏钢率达0.19%;2010年漏钢率达0.19%;2011年漏钢率达0.19%;2012年漏钢率达0.15%;2013年漏钢率达0.07。
1 工艺流程某厂第一钢轧厂工艺流程为:鱼雷罐供应铁水/混铁炉供应铁水→铁水预处理→转炉炼钢→氩站→精炼→薄板坯连铸2 薄板坯漏钢类型某厂薄板坯连铸漏钢主要有:粘结漏钢、裂纹漏钢、卷渣漏钢、开浇漏钢、鼓肚漏钢五个类型。
3 薄板坯漏钢特征、原因及预防措施3.1 粘结漏钢粘结漏钢是指钢水直接与结晶器铜板接触形成粘结点,粘结点处坯壳与结晶器壁之间发生粘结,此处在结晶器振动和拉坯的双重作用下被撕裂,并向下和两侧扩展,形成倒“V”形破裂线,钢水补充后又形成新的粘结点,这一过程反复进行,粘结点随坯壳运动不断下移,此处坯壳较薄,出结晶器后,坯壳不能承受上部钢水的静压力,便会发生漏钢事故。
据统计,粘结漏钢发生率最高,高达50%以上。
(1)铸坯粘结漏钢后特征。
粘结漏钢后铸坯特征。
坯壳呈“V”字型或“倒三角”状,粘结点明显。
(2)粘结漏钢的原因:1)保护渣性能不好。
保护渣在结晶器铜板与凝固坯壳之间起润滑的效果。
薄板坯连铸连轧设备生产热轧薄板的缺陷分析与改进

薄板坯连铸连轧设备生产热轧薄板的缺陷分析与改进热轧薄板广泛应用于许多行业,包括建筑、汽车制造和航空航天等领域。
然而,在生产过程中,薄板坯连铸连轧设备生产热轧薄板时可能会出现一些缺陷,这些缺陷会对产品质量和性能造成影响。
因此,及时进行缺陷分析和改进是至关重要的。
首先,我们将对薄板坯连铸连轧设备生产热轧薄板的常见缺陷进行分析。
在生产过程中,以下几种常见缺陷可能会出现:1. 表面缺陷:这是最常见的缺陷之一,包括锈蚀、划痕、斑点和凹凸等。
这些缺陷可能是由于设备不良或操作不当导致的。
2. 内部缺陷:内部缺陷主要包括夹杂物、气泡和裂纹等。
夹杂物通常是由原材料中的杂质引起的,如硅、锰、钢水中的氧化物等。
气泡则是由于薄板坯连铸过程中,气体在坯料中的溶解度下降而引起的。
裂纹则主要是由于过高的轧制温度、轧制力过大或轧制参数设置不当等原因引起的。
3. 带杂质缺陷:这种缺陷通常是由于设备设备不良或操作不当导致的。
例如,如果轧机辊子表面不平整或有划痕,则会导致薄板表面出现糙痕。
其次,我们需要进行缺陷改进的工作。
以下是一些建议和方法:1. 优化设备和工艺参数:我们可以通过改进设备和调整工艺参数来减少缺陷的发生。
例如,定期检查和维修设备,确保其正常运行。
在设备运行过程中,根据产品要求和材料特性,适时调整轧制温度、轧制力和轧制速度等参数,以提高产品质量并减少缺陷的发生。
2. 加强原材料质量控制:原材料的质量对产品质量有着重要影响。
因此,我们应该加强原材料的质量控制,确保其符合要求。
例如,定期检测原材料中的杂质含量,采取相应措施减少杂质对产品的不良影响。
3. 强化操作培训和管理:员工的操作技能和工作态度对于产品质量的控制和缺陷改进至关重要。
因此,我们应该加强操作培训,提高员工的技能水平。
同时,加强对生产过程的管理,制定标准作业流程,确保操作规范和一致性。
4. 建立完善的质量管理体系:建立完善的质量管理体系是确保产品质量和缺陷改进的基础。
中国薄板坯连铸连轧技术的现状和发展

中国薄板坯连铸连轧技术的现状和发展中国薄板坯连铸连轧技术是指将熔化的金属经过连铸机连续铸造成坯料,然后通过连续轧制、切割等工艺过程,制成各种规格的薄板材料的生产技术。
目前,中国的薄板坯连铸连轧技术已经取得了较大的进步和发展。
主要体现在以下几个方面:
一、品种规格的增加
随着市场需求的不断增加,中国的薄板坯连铸连轧技术已经实现了从单一规格向多品种、小批量和高品质的发展。
目前,我国已经能够生产厚度为0.8mm以下、宽度在800mm以上的薄板产品,满足了市场对多种产品的需求。
二、技术水平的提高
随着技术的不断发展,中国的薄板坯连铸连轧技术逐步实现了数控化、自动化和智能化。
同时,新的轧制工艺和设备的应用,也使得产品的质量和生产效率得到了大幅提升。
三、环保意识的加强
在当前环保意识不断提高的背景下,中国的薄板坯连铸连轧技术也在不断推进环境保护措施。
例如,在生产过程中采用了新型的净化技术和设备,有效降低了环境污染和能源消耗。
未来,中国薄板坯连铸连轧技术还将继续发展和完善。
我们有理由相信,在技术革新和环保要求的推动下,中国的薄板坯连铸连轧技术将会更加先进、更加高效、更加环保、也更加适应市场需求。
- 1 -。
板坯拉速提高对铸坯质量的影响

表 5 保护渣现场试用结果
保 护 渣
1
拉速为 1 . 8 而I m 时 n
耗 量 / 兹 ・ m 一 2
>0. 3
表 面缺陷
尤
流人均匀性
好
技 术讲座 6v C 提高对结晶器液面起伏的影响 v C 提高时, 液面起伏加剧, 铸坯表面容易裹渣,
如果浸人式水口浸人深度不足, 将使裹渣加剧。薄
板坯连铸从浸人式水 口侧孔出来的向下流股的下倾 角应当大一些, 以便将钢流分散到结晶器深处。电 磁制动可使液面平稳和液面温度高。当液面起伏偏 离最佳值时, 可用电磁制动进行调节。
c 提高后, V 结晶器热面温度升高, 为了防止粘
结, 结晶器铜板厚度应当减薄, 见表 2 。
表Z v C 提高对结晶器铜板厚度的影响
板坯连铸机 伯利恒
<14 >1 . 4
热 流> 2 . S M W / 扩时, 将产生宽面 纵裂。 该厂在v c
提高时, 为了减少宽面纵裂, 使用了C a o / 5 1 仇 高和 含有2 政 的保护渣, 见表3 。 C o/ a 1 5 仇高和含有2 0 1 2 时, 可以提高保护渣的 结晶温度T c, e可以 T 使热流减少。
而 n [ 2 ] 。
高碳钢因 为容易粘结漏钢和容易内 裂, 所以v c
7V C 提高对板坯内部质量的影响 卢肯斯钢铁公司V c 提高后, 板坯内 部质量( 中心
裂纹、 三重点裂纹、 经向裂纹) 有所下降。该公司经过 研究得出: 降低中间罐钢水过热度和增加铸机下部组 件( n x 对 l u )的夹紧力对改进内部质量有好处。 e
表 4 保护渣的性能( 用于低碳铝镇静钢)
化学成分/ %
1 5 仇 月2 场F 伪 场 临( ) 凡O F 固定
[连铸机,板坯,技术]提高板坯连铸机中间包连浇炉数的技术优化与实践
![[连铸机,板坯,技术]提高板坯连铸机中间包连浇炉数的技术优化与实践](https://img.taocdn.com/s3/m/302929ea0912a21615792924.png)
提高板坯连铸机中间包连浇炉数的技术优化与实践摘要:分析认为,影响济钢板坯连铸机中间包连浇炉数的因素很多,除了与耐材质量、铸机设备有关外,还受到生产组织、市场因素、操作水平和生产工艺的影响。
通过对影响因素的系统分析和改进,使单中间包的连浇炉数较之前有所提高,降低了生产成本,取得了良好的效果。
关键词:连铸机;连浇炉数;使用寿命;生产组织目前,随着国内钢铁市场形势的急剧恶化,各大型钢铁企业均面临着急剧亏损的状态,企业转型以及不断降低生产成本的压力不可避免。
因此,优化板坯连铸机中间包使用寿命,成为济钢炼钢厂连铸工序降成本直接有效的关键措施之一。
1 板坯连铸机中间包使用现状2 影响板坯连铸机中间包连浇炉数的主要因素分析2.1 优化功能耐火材料质量中间包的功能耐火材料有塞棒、套管、浸入式水口,这3种耐火材料能否与中间包包衬寿命同步,直接影响中间包包龄的提高,合理的选用耐材对提高中间包连浇炉数起重要作用。
针对这3种耐火材料对中间包包龄的影响进行了针对性的研究与改进。
2.1.1 提高浸入式水口的使用寿命(1)增强浸入式水口渣线部位的侵蚀性,提高浸入式水口的寿命。
采用高纯度铝碳质材料的整体水口,渣线部分复合锆质,提高渣线部位抗热震性和抗侵蚀性。
优化浸入式水口形状,降低水口堵塞的几率。
(2)改善水口烘烤效果,防止开浇时水口炸裂。
原有水口烘烤装置为烘烤小车,后制作水口烘烤装置,具体见下图1,并对水口烘烤时间和煤气用量的控制,烘烤均匀,有效的防止了开浇或者换水口时的水口炸裂。
(3)优化保护渣成分,减少对水口的侵蚀。
积极与保护渣厂家协调优化保护渣的成分,使用含F和碱金属较低的保护渣,减少了水口C质的氧化和釉质的烧损。
4台板坯连铸机均采用中间包整体塞棒,且带有液位控制装置。
但在生产过程中,时常出现浇铸后期棒头不耐侵蚀、棒身渣线部位抗侵蚀效果差、以及棒头易脱落的现象。
针对以上问题,我们采取如下措施:(1)棒头由镁碳材质改为铝碳材质,保证了塞棒吹氩效果的同时减少了棒头的侵蚀;(2)棒身由铝碳质改为复合锆质材料,减少了棒身渣线部位侵蚀;(3)改进棒头与棒身的结合方式,杜绝了棒头脱落现象;(4)优化装塞棒操作,保证在热态情况下对中良好;(5)细化开浇前对塞棒的检查,观察塞棒本体及头部是否有脱落及裂纹。
薄板坯连铸连轧设备生产热轧薄板的轧辊磨损分析与改进
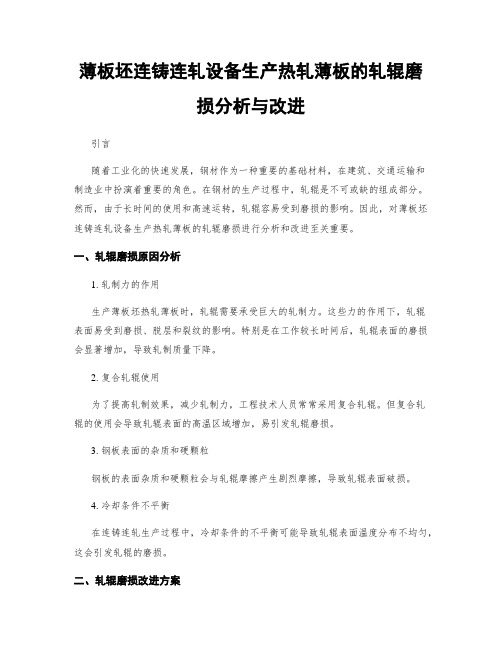
薄板坯连铸连轧设备生产热轧薄板的轧辊磨损分析与改进引言随着工业化的快速发展,钢材作为一种重要的基础材料,在建筑、交通运输和制造业中扮演着重要的角色。
在钢材的生产过程中,轧辊是不可或缺的组成部分。
然而,由于长时间的使用和高速运转,轧辊容易受到磨损的影响。
因此,对薄板坯连铸连轧设备生产热轧薄板的轧辊磨损进行分析和改进至关重要。
一、轧辊磨损原因分析1. 轧制力的作用生产薄板坯热轧薄板时,轧辊需要承受巨大的轧制力。
这些力的作用下,轧辊表面易受到磨损、脱层和裂纹的影响。
特别是在工作较长时间后,轧辊表面的磨损会显著增加,导致轧制质量下降。
2. 复合轧辊使用为了提高轧制效果,减少轧制力,工程技术人员常常采用复合轧辊。
但复合轧辊的使用会导致轧辊表面的高温区域增加,易引发轧辊磨损。
3. 钢板表面的杂质和硬颗粒钢板的表面杂质和硬颗粒会与轧辊摩擦产生剧烈摩擦,导致轧辊表面破损。
4. 冷却条件不平衡在连铸连轧生产过程中,冷却条件的不平衡可能导致轧辊表面温度分布不均匀,这会引发轧辊的磨损。
二、轧辊磨损改进方案1. 提高轧辊材料的性能选择高性能的轧辊材料可以有效提高轧辊的抗磨性能。
例如,采用高硬度、高耐热的合金材料可以减少轧辊表面的磨损。
2. 优化轧辊表面涂层技术采用涂层技术可以有效改善轧辊的抗磨性能。
常用的涂层材料包括液体纳米材料、尖晶石材料等。
这些涂层可以形成坚硬的保护层,降低轧辊与钢坯之间的摩擦和磨损。
3. 控制轧制力合理控制轧制力的大小,可以减少轧辊表面的磨损。
通过优化传动系统和辊系设计,减小轧制力的大小,对轧辊的寿命和性能有着显著的改善作用。
4. 加强轧辊的维护管理定期进行轧辊的维护保养是减少磨损的重要措施。
清洁轧辊表面的杂质和硬颗粒,控制轧辊的温度分布,防止轧辊因过热而受损。
5. 定期更换轧辊根据轧辊使用寿命和磨损情况,定期更换轧辊是降低轧辊磨损的有效方式。
及时更换轧辊可以避免轧辊磨损过度,影响生产质量和效率。
QC-减少中薄板连铸机开浇第一炉生产事故的工艺措施优化.ppt

2008 赵登报 年6月 郭卫国
《减少中包开浇第一炉生产事故的工艺措施优化》
三炼钢连铸车间QC成果
九、实施对策
依据制定的对策,结合实际生产操作要求,2007年5、6月份, 我们对以上四个方面的改进同时进行实施,具体改进过程如下。
★实施一:采用蓄热式烘烤器★
1、为了降低生产成本,中包烘烤由混合煤气置换成转炉煤气后,热值大大降低,中包温 度达不到要求,为了提高烘烤效果,把烘烤器都改为蓄热式烘烤器,提高了烘烤效果。
《减少中包开浇第一炉生产事故的工艺措施优化》
九、实施对策
★实施四:优化引锭封堵方式★
三炼钢连铸车间QC成果
角部抹硅胶
插入连接钢筋
封堵好的引锭
《减少中包开浇第一炉生产事故的工艺措施优化》
三炼钢连铸车间QC成果
十、效果检查
7月10号开始,进行了全面评估,结果统计如下
序号 调查项目
调查方法
调查结果
1 中包温度
《减少中包开浇第一炉生产事故的工艺措施优化》
九、实施对策
★实施四:优化引锭封堵方式★
三炼钢连铸车间QC成果
纸绳
塞纸绳
《减少中包开浇第一炉生产事故的工艺措施优化》
九、实施对策
★实施四:优化引锭封堵方式★
三炼钢连铸车间QC成果
2、多处增加垫板,规范铁粒铺设方式,防止开浇漏钢和粘引锭头:在浸入 式水口的正中央铺设大垫板,在凹入的燕尾槽斜面处各铺设一个中垫板。然 后在引锭的表面铺设铁粒,铁粒的厚度大约为20mm,保持铁粒铺设均匀。
《减少中包开浇第一炉生产事故的工艺措施优化》
三炼钢连铸车间QC成果
四、制定目标
通过分析事故发生的原因,随着职工操作技能水平的提高和工艺 参数的优化,本着“自我加压、争创一流”的精神,我们设定这 次活动的目标为
《改善连铸板坯缺陷的轧制工艺》范文

《改善连铸板坯缺陷的轧制工艺》篇一一、引言随着现代工业的快速发展,钢铁行业作为国民经济的重要支柱,其产品质量和生产效率的提升显得尤为重要。
连铸板坯作为钢铁生产中的重要环节,其质量直接影响到后续轧制工艺的效率和产品质量。
因此,如何有效改善连铸板坯的缺陷,优化轧制工艺,成为了业界关注的焦点。
本文旨在探讨连铸板坯的常见缺陷及原因,并分析轧制工艺的改进措施,以提高钢铁产品的质量和生产效率。
二、连铸板坯常见缺陷及原因分析1. 中心裂纹:中心裂纹是连铸板坯的主要缺陷之一,其形成原因主要是板坯凝固过程中的温度梯度和热应力过大。
此外,铸坯的化学成分、夹杂物、铸机振动等因素也会对中心裂纹的产生造成影响。
2. 表面裂纹:表面裂纹主要出现在板坯的表面,其形成原因包括钢水质量、结晶器振动、二次冷却制度等因素。
此外,钢中合金元素和夹杂物的含量也会对表面裂纹的产生造成影响。
3. 夹渣和夹杂物:夹渣和夹杂物主要来源于钢水的精炼过程和浇注过程中的夹杂物。
此外,铸模的质量、涂料的性能以及连铸机的维护保养也会影响夹渣和夹杂物的产生。
三、轧制工艺的改进措施针对上述连铸板坯的常见缺陷,轧制工艺的改进措施主要包括以下几个方面:1. 优化轧制参数:通过合理设定轧制温度、轧制速度、压下量等参数,使轧制过程更加稳定,减少轧制过程中的变形和裂纹等缺陷的产生。
2. 调整轧辊质量:选用高质量的轧辊,提高轧辊的硬度和耐磨性,减少轧制过程中的磨损和振动,从而降低板坯的表面裂纹和内部缺陷。
3. 强化轧前准备:在轧制前对连铸板坯进行充分的预热和除鳞处理,以去除表面的夹杂物和氧化皮,提高板坯的表面质量。
4. 优化冷却制度:根据板坯的化学成分、尺寸和轧制要求,制定合理的冷却制度,控制板坯的冷却速度和温度分布,以减少中心裂纹和表面裂纹的产生。
5. 引入无损检测技术:在轧制过程中引入无损检测技术,如超声波检测、X射线检测等,对板坯进行实时监测,及时发现并处理缺陷,提高产品的良品率。
- 1、下载文档前请自行甄别文档内容的完整性,平台不提供额外的编辑、内容补充、找答案等附加服务。
- 2、"仅部分预览"的文档,不可在线预览部分如存在完整性等问题,可反馈申请退款(可完整预览的文档不适用该条件!)。
- 3、如文档侵犯您的权益,请联系客服反馈,我们会尽快为您处理(人工客服工作时间:9:00-18:30)。
2010年炼钢-连铸生产技术会议
薄板坯连铸机低碳钢塞棒上涨原因探讨
郑伟栋黄文杰唐志军郝强
(河北钢铁集团邯钢公司河北邯郸 056015)
摘要:结合邯钢生产实践,对CSP连铸机低碳钢塞棒上涨原因进行了分析并提出了预防措施,有效减少了事故停浇次数。
关键词:CSP,低碳钢,塞棒上涨
Discussion and Analysis for Stopping Rising on
Low Carbon Steel of Thin Slab Caster
ZHENG Wei-dong HUANG Wen-jie TANG Zhi-jun HAO Qiang
(Hebei Iron & Steel Group HanGang Company, Handan, Hebei, 056015)
Abstract: Through the causes analysis put forward prevent measures for stopping rising on low carbon steel of Handan CSP caster. The accident can be reduced effectively.
Key Words: CSP,low carbon steel,stopping rising
1 前言
邯钢CSP薄板坯连铸机主要生产低碳钢、SS400、Q345A/B等铝镇静钢种,其中低碳钢占总产量的60%以上,低碳钢主要为冷轧备料。
在CSP连铸机生产低碳钢过程中,多次出现塞棒上涨事故停浇,甚至开浇不成功,对正常生产组织造成了很大影响,给公司造成了巨大的经济损失。
本文结合邯钢生产实践,通过大量实际生产数据,对CSP薄板坯连铸机生产低碳钢塞棒上涨原因进行了分析,并提出了预防措施,目前塞棒上涨事故停浇已得到有效控制,为公司生产稳定顺行创造了良好条件。
2 薄板坯低碳钢塞棒上涨的机理
邯钢CSP薄板坯连铸机通过塞棒机构控制塞棒的开度,实现结晶器液位控制系统稳定地控制钢水从中包到结晶器中,当液位控制系统检测到结晶器中的钢水液位后,将实际值和设定值进行比较,如果实际液位与设定液位有偏差,控制系统将自动进行补偿调节:当结晶器钢水液位高于设定值,塞棒将下压减小开度;当结晶器钢水液位低于设定值,塞棒将上抬增加开度。
造成塞棒上涨即塞棒持续上抬的直接原因是流入结晶器内的钢水逐渐减少,为满足结晶器钢水液位要求,塞棒逐步上涨。
造成流入结晶器内的钢水逐渐减少的根本原因是高熔点夹杂物逐步附着在侵入式水口下部内壁(一侧或两侧)、水口上部碗部区域,部分附着物被钢水冲刷掉进入结晶器,导致结晶器液面控制曲线在相应点剧烈波动,随着夹杂物的越积越多,塞棒逐步上涨。
3 CSP低碳钢塞棒上涨的影响因素
3.1钢水钙含量及钙铝比
作者简介:郑伟栋(1974—),男,钢铁冶金高级工程师,zhtzwd@.
3.1.1 CSP连铸机第一炉钢水Ca含量统计分析
CSP连铸机低碳钢第一炉钢水Ca含量对开浇成功与否有重要影响,通过对CSP薄板坯连铸机开浇成功与开浇不成功(不能起步或起步后塞棒上涨严重)炉次钢水Ca含量情况进行了统计(表1、图1)表明,开浇成功与开浇不成功精炼出站样平均Ca含量分别为65.6ppm、51.2ppm,成品样平均Ca含量分别为27.4ppm、20.6ppm,Ca损失率分别为58.23%、59.77%。
表1 CSP低碳钢开浇第一炉钢水Ca含量统计
类别精炼样Ca含量/ppm 成品样Ca含量/ppm Ca损失率/% 开浇成功65.6 27.4 -58.23 开浇不成功51.2 20.6 -59.77
图1 CSP低碳钢开浇第一炉钢水Ca含量统计(ppm)
由于第一炉开浇,中间包钢水需要一个填充过程。
填充期间,中间包内没有渣层保护,长水口没有浸入熔池,钢水与空气接触,吸N2和O2,发生二次氧化,产生大量夹杂,没有时间上浮。
中间包钢水开浇过程中氧含量和氮含量会明显上升,中间包钢水填充1.5 min,w(N)高达160~170ppm,w(TO)为80ppm左右[1]。
从表1、图2可以看出,开浇成功炉次钢水精炼样及成品样Ca含量均高于开浇不成功炉次,钢水Ca 损失率均在60%左右,故要求CSP低碳钢第一炉钢水精炼出站样Ca含量控制在60ppm左右,确保CSP连铸机开浇成功。
3.1.2 CSP低碳钢连拉炉次钢水Ca含量统计分析
对CSP低碳钢连拉炉次钢水Ca含量进行统计(表2、图2)表明,正常炉次、塞棒上涨炉次精炼出站样平均Ca含量分别为49.4ppm、34.2ppm,成品样平均Ca含量分别为28.0ppm、18.7ppm,Ca损失率分别为43.30%、45.03%。
表2 CSP低碳钢连拉炉次钢水Ca含量统计
类别精炼样Ca含量/ppm 成品样Ca含量/ppm Ca损失率/% 正常炉次49.4 28.0 -43.32 塞棒上涨炉次34.2 18.8 -45.03
图2 CSP低碳钢连拉炉次钢水Ca含量统计(ppm)
从表2、图2可以看出,正常炉次钢水精炼样及成品样Ca含量均高于塞棒上涨炉次,钢水Ca损失率均在45%左右,故要求CSP低碳钢连拉炉次钢水精炼样Ca含量控制在50ppm左右。
3.1.3 CSP低碳钢Ca/Als统计分析
对CSP低碳钢正常炉次、塞棒上涨炉次Ca/Als进行统计(表3)表明,正常炉次精炼出站样Ca/Als、成品样Ca/Als均高于塞棒上涨炉次,为提高钢水可浇性,要求第一炉钢水Ca/Als控制在0.18左右,连浇炉次钢水精炼出站样Ca/Als控制在0.15左右,确保成品样Ca/Als在0.09~0.15。
表3 CSP低碳钢连拉炉次钢水Ca/Als统计
类别精炼样Ca/Als 成品样Ca/Als
正常炉次0.147 0.096
塞棒上涨炉次0.088 0.056
3.2 CSP低碳钢Alin(夹杂铝)含量统计分析
对CSP低碳钢正常炉次、塞棒上涨炉次Alin含量进行统计(表4)表明,正常炉次精炼出站样及成品样平均Alin含量均低于塞棒上涨炉次,成品样比精炼样Alin升高11ppm左右,尤其是第一炉钢水与空气接触机会多,二次氧化严重,Alin含量升高20ppm左右。
故要求加强钢水纯净度控制,保证钢水净吹时间,尽可能保证钢水精炼出站样Alin含量控制在25ppm以下。
表4 CSP低碳钢Alin统计
类别精炼样Alin/ppm 成品样Alin/ppm
正常炉次24 35
塞棒上涨炉次33 45
3.3 CSP低碳钢精炼后期补铝操作
对塞棒上涨炉次精炼过程分析表明,精炼后期补铝操作,极易引起塞棒上涨事故停浇。
精炼后期补铝,产生的Al2O3夹杂尺寸小,不利于夹杂物碰撞长大并且没有充分时间上浮去除[2]。
故要求精炼前期加强钢水过程Als控制,以利于高熔点Al2O3夹杂形成簇状物上浮去除。
如后期必须要进行补铝操作,为了尽可能降低补铝对钢水质量及可浇性造成影响,要保证补铝后到钙处理前的时间至少在10min以上,并保证钢水静吹时间至少在5 min以上,确保夹杂物充分上浮。
3.4 钢水精炼时间
钢液中的夹杂主要靠聚集上浮入渣去除,在有吹氩搅拌的条件下,钢液中全氧的变化与精炼时间呈指数关系,达到一定的精炼时间后,钢液中的全氧达最低,所以,从去除夹杂物的角度,必须保证一定的精炼时间。
但精炼时间过长,钢液在高温下和熔渣、大气以及耐火材料长时间接触,钢水中的Als二次氧化及钢包耐材熔损产生大量小颗粒夹杂,悬浮在钢水中难以去除,极易造成塞棒上涨甚至漏钢事故。
故要求加强生产组织,尽可能避免钢水压站时间过长对钢水质量造成影响。
3.5 钢包烧氧
在生产中多次出现钢包不自开烧氧后塞棒上涨现象,据有关资料介绍,烧氧对中间包钢水w(TO)有显著影响[3],钢包烧氧可以使中间包钢水w(TO)上升15ppm以上。
故要求严格钢包热修操作、选择优质引流砂等措施,提高大包自开率,尤其是连铸第一炉钢水,要求使用包况良好的周转包确保自开,避免诸多不利因素叠加严重影响钢水质量,造成塞棒上涨事故停浇。
4 结论
(1)为减少CSP低碳钢塞棒上涨事故停浇,第一炉钢水精炼出站样Ca含量应控制在60ppm左右,Ca/Als 控制在0.18左右;连浇炉次钢水精炼出站样Ca含量应控制在50ppm左右,Ca/Als控制在0.15左右。
(2)钢水精炼出站样Alin含量尽量控制在25ppm以下。
(3)尽可能避免精炼后期补铝操作,确需补铝则要保证补铝后到钙处理前的时间至少在10min以上。
(4)要保证钢水精炼时间,同时要避免钢水压站时间过长。
(5)钢包烧氧对钢水质量有严重影响,要尽可能避免CSP连铸第一炉钢包烧氧。
参考文献:
[1] 高海潮等. CSP连铸浸入式水口结瘤案例研究.钢铁.2005.11.
[2] 成国光等.《新编钢水精炼暨铁水预处理1500问》.北京:中国科学技术出版社,2007.3.
[3] Hughes P.Improvement in the Internal Quality of Continuously Cast Slabs at Lukens Steel[J].Iron and Steelmaker,1995,22(6):35.。