模具静态检查表(最新)
模具动静态检查表

硬度计
打印去清晰无凸起
目视
高于型面0.1-0.2mm,工作面清晰 是否产生压痕 排气通畅 管理面95%准管理面90%凹模>80% 符合图纸,工件表面平整 带料冲压检查轮廓线是否清晰、顺畅 最经济下料尺寸
目视 目视 目视 目视 红丹粉 目视 目视 卷尺
贴合率≥80
目视 红丹粉
不能过紧或过松
目视 目视
目视.8,支撑面1.6
目视
无单边接触、无损伤、无松动现象
红丹粉
大型<0.1,中型<0.08,反侧导板≤0.0塞1 尺
≥85%,着色均匀
红丹粉
间隙<0.03
塞尺
扒钩间隙 侧冲0.5-1 吊冲<0.3
塞尺
粗糙度0.8
目视
按图纸要求
硬度计
≤0.03mm
塞尺
垂直于刃口≤100以内不允许超过3条裂纹目视
沧州瑞恒模具动、静态检查表
项目名称 工序名称 调试设备 630T
类别 序号
1
外 观 检 查
2 3 4 5 6
7
8
1
导
2
向
3
装
4
置
5
6
冲
1
载
2
落
3
料
4
、
5
冲
6
孔
7
、
8
切
9
边
10
部
11
分
12
13
前防撞梁左吸能盒内板
主压力
20
检查项目
静
模具颜色
模具铭牌
模具倒角、出气槽
刀块非工作面倒角、孔倒角
F标记、模具号
≤0.01mm
塞尺
模具点检表
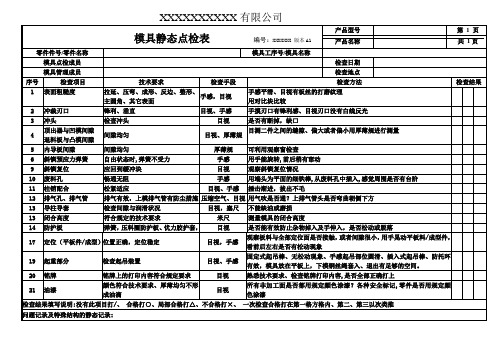
6 斜锲预应力弹簧 自由状态时,弹簧不受力
手感
用手能旋转,前后稍有窜动
9 斜锲复位
应回到缓冲块
目视
观察斜锲复位情况
10 废料孔
Байду номын сангаас
畅通无阻
手感
用端头为平面的细铁棒,从废料孔中插入,感觉周围是否有台阶
11 柱销配合
松紧适应
目视、手感 捶击渐进,拔出不毛
12 排气孔、排气管 排气有效,上模排气管有防尘措施 压缩空气、目视 用气吹是否通?上排气管头是否弯曲朝侧下方
XXXXXXXXXX 有限公司
模具静态点检表
编号:XXXXXXX 版本 A1
产品型号 产品名称
第1页 共 1页
零件件号/零件名称 模具点检成员
模具工序号/模具名称
检查日期
模具管理成员
检查地点
序号
检查项目
技术要求
检查手段
检查方法
检查结果
1 表面粗糙度
拉延、压弯、成形、反边、整形、
主圆角、其它表面
手感,目视
XXXXXXXXXX 有限公司
XXXXXXXXXX 有限公司
XXXXXXXXXX 有限公司
XXXXXXXXXX 有限公司
看前后左右是否有松动现象
19 起重部分
检查起吊装置
固定式起吊棒、无松动现象、手感起吊部位圆滑、插入式起吊棒、防托环 目视、手感
有效,模具放在平板上,下模钢丝绳套入、退出有足够的空间。
20 铭牌
铭牌上的打印内容符合规定要求
目视
熟悉技术要求、检查铭牌打印内容,是否全部正确打上
21 油漆
颜色符合技术要求、厚薄均匀不形 成油滴
13 导柱导套
冲压模具检查记录表范例
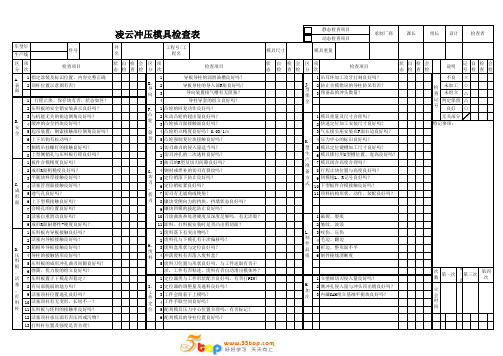
3 预备品的冲头数量?
全
1 模具重量及尺寸合理吗?
2 快速定位加工安装尺寸良好吗?
3 气压接头座安装在F面右边良好吗?
K. 4 压力中心的标识良好吗? 型 5 模具定位键槽加工尺寸良好吗?
生 6 模具锁付用U型槽位置、宽高良好吗?
产 准
7 模具闭合高度合理吗?
备 8 行程止块位置与高度良好吗?
方 9 闭模钮L、R记号良好吗? 式 10 下型板件合模接触良好吗?
12 活塞顶杆承压面有否压凹或污物?
13 打料杆位置及强度是否合理?
1 E. 2 导 向3
4
导板导柱的润滑油槽良好吗? 导板导柱的导入部R角良好吗?
导向装置排气槽有无阻塞? 导柱导套的组立良好吗?
F. 1 凸轮的回复动作良好吗?
凸 2 从动凸轮的超出量良好吗?
轮 、
3 凸轮插刀面接触面良好吗?
斜 4 凸轮组立精度良好吗?0.03/1m
凌云冲压模具检查表
静态检查项目 动态检查项目
承制厂商
课长
组长 设计
检查者
车型年 生产线
件号
件 名
工程号/工 程名
模具尺寸
模具重量
区项 分次
检查项目
状自检会 区项 态检查检 分次
检查项目
状 自 检会 区项 态 检 查检 分次
检查项目
状自检会 态检查检
说明
记自检会 号检查检
A. 1 指定涂装及标识位置、内容完整正确 表 2 顶杆位置示意图有否? 面
11 顶料机构形状、动作、装配良好吗?
1 破裂、裂痕
2 皱纹、波浪
L. 3 咬伤、压伤 制 4 毛边、翻边 件 品 5 折边、整形面不平 质 6 制件棱线清晰度
模具检查表

热流道**检查日检查员式外出荷样观出荷T1T1T1T1T1T1T1T1T1T1T1T1T1T1T1T1T1T1T1T1T1T1T1T1防腐T1T1T1T1T1T1出荷T1T1是否有部品标记(确认部品的位置)是否做了决定必要位置的加工 (锁扣等)必要的部品有无拔出螺纹孔(一个 二个)是否有防腐处理(出荷前)外形尺寸是否符图纸(能否安装在预定成型机上)长喷嘴的式样内径加工间隙尺寸(φ1 3 5 )顶杆孔的尺寸.间距是否符图纸R符图纸 R21定位圈上是否封印尺寸是否符图纸 (φ100 120 150)安装孔的余量是否够安装孔的尺寸.间距是否符图纸平衡是否好(螺丝孔的位置正确否)导柱的长度是否够.弯曲.拉着.油槽.排气导套是否有台肩或横向顶丝固定侧是否有保护锁块(PL面上有突形)吊物是否平衡(各顶板的螺丝孔处理)基准面是否有标记螺丝有无弯曲和龟裂 (确认部品)350t的时候要使其能采取一点吊 (爱丽思的特别式样)吊的平衡是否好挂上钢丝绳时有无干涉物对突出物品的保护是否到位固定板和对各个板上的水嘴的保护热流道模具在换色时型板是否能分离确认为防止各型板丢失是否进行了丝锥处理支脚*4的粗细 平衡性螺丝是否够深根据模具的重量选择的型号是否合适 (是否安全)周围有无干涉物 (装卸有无问题)有/无有/无有/无OK/N检 查 项 目是否有标牌 (模具尺寸.重量...) 喷嘴NO是否按用户的式样表示的是否安装了防开模板 (操作侧和反操作侧)防开模板的螺丝是否够深 (是否全部拧进)防开模板是否容易装卸(是否和成型机的拉杆相冲突)OK/NOK/NOK/N有/无有/无有/无有/无OK/NOK/N有/无OK/NOK/N有/无有/无OK/NOK/NOK/N有/无备有/无OK/N有/无OK/NOK/N固定板成形机的安装安全 性外 观 及 安 全 保 障吊 环分解组装PL面开闭移动作业模具尺寸成形机 TON分 类喷嘴定位环OK/NOK/NOK/NOK/NOK/NOK/NOK/NOK/N模具检查表(新型)考口Array考未/完对应各点检项目 年 月 日 完了如纳品模具无此检项目时,要用斜线划掉每页的营业栏和右上的最终责任者栏要无一遗漏的盖章最后, 此文件做为检查说明的文件, 今后必需填写,并且填写后要全部提交.注意: 如不提交将不与办理验收手续天;实际工时: 天; 改造天数 天日 T5 月 日 完了日 年 月 日年 月 日( ) T2 月 日( ) 设计承设计承辅助说明)未/完。
模具动静态检验标准

镶
材质是否与图纸
17 块 刃口吃入量
积料不超过 3 片。刃口吃入量 3-5mm。
18 与 接刀缝
间隙规测量 0.05mm 以下
19 刀 镶块补焊
补焊光顺,横向裂纹无,纵向裂纹 100 mm 内允许 3 条
20 口 镶块与安装底面
自由状态,贴合间隙小于 0.02mm/与基体或背托贴合率大于 90%
21 冲 标准异形冲头
凹模套在斜面上要有防转措施,小于等于¢8 的冲头采用快换冲头 材质、编号与实物一一对应;字体工整,醒目,内容齐全
15kg 以上或难于取出的镶块应有起吊螺纹孔,并有标示
检查时看导柱、导板间隙;如果是钢板变形量大,涂红丹看导柱间隙。
除压(托)料面,其他地方都要倒角
压(托)料板与刃口配合间隙 0.5-0.8mm 单边至少有两处定位,进料方向有导入角,并且刚性良好。 压料板上要有导正销,导正销突出压料板时要有退料销 活动部分必须有安全护板。 沉孔深度一致,正反面要倒角。螺钉拧入直径 2 倍以上。 工作时不起作用,但位置分布要合理,孔四周用黄漆标注 与沉孔一致,正反面倒角,螺钉紧入量是螺钉直径的 2 倍
8
上、下模型面 R 角光顺,棱线清晰,油石抛光
上
9
压边圈
下
压料面油石抛光;拉延筋(槽)圆顺光滑。
10 模 排气孔
钻孔¢6 应在凹处不影响制件外观
11
防尘管
紧固可靠,通畅
12
材质与硬度 材质依技术协议及图纸,硬度不低于 HRC50
13
拉延成型标记 标记深度 0.3mm,左右件用“L、R”代替, 压印不得留在 A 表上
型 型面及压料面
14 面 空研
上下模空研。平面着色
模具动静态检查表

零件图号 操作者
检查方法
目视
验收 123
9 修边口粗糙度
※ Ra<0.8,240#以上油石推光
粗糙度样块
10 修边口无咬合、擦黑、刮痕等现象
※ 空车4-5次
目视
11 修边口及刃口的状态
※
锋利、无缺口,崩刃,啃刃等现象,刃口垂 直,无倒椎
目视,直角尺
12
焊接刃口不能有气孔、夹渣及平行于刃口的 裂纹
※
允许垂直于刃口的微裂纹应控制在100mm≤3条 (长<2mm,宽<0.02mm,深度≤1mm)
目视
※ 筋内侧100%,外侧85%,均匀 ※ 板厚+0.25mm以上
红丹粉 红丹粉
7 型面、侧壁的间隙 8 拉延面、型面、棱线及圆角,拉延筋粗糙度 9 其它加工面精糙度
※ 板厚±0 Ra≤0.8,320#以上油石推光,圆角、筋细砂
※布 推光
※ Ra≤1.6
10
凸模凹模、压料圈等工作部位,凸圆角淬火 硬度
直角尺 厚薄规
5 上下模导向面中心
※ 应无错位现象
目视
6 导板导柱的导入圆角
※ R8-R10
R规
7 导滑面、导入圆角粗糙度
※ ≤0.8,平整顺滑,240#油石推光
粗糙度样块
导 8 导板、导柱配合使用时
※ 导板应先于导住导向
目视
向 9 导板止退台宽度
10 导板与止退台安装面配合 装
11 导柱与导套配合间隙 置
※
无划伤、裂纹、波纹、磕碰伤、气孔、砂眼、 塌角、凹陷等,缺陷<0.05mm以内
目视
※
必须按基准制作,不准随意打磨,修改,要保 产品图,工艺
证产品尺寸要求
模具检查表(新型)(XLS)

模具检查表(新型)
最终检查日: 检查员: 模具番号: 模具品名: 厂家验收 顾客验收 设计担当
分 类
嵌和有无问题 有无防转销 是否打字码 (考虑保养) 是否有火(HRC58~60确认品质)
检 查 项 目 (径 杆 顶管冷却有无问题 顶管高度有无问题 时间差顶杆动作有无问题 (动作量) 孔内径是否用铰刀加工 是否使用了特殊型号(扁形 极细 阶梯 其他) 有无干涉 (径. 间距) 回 导柱是否使用沾火料 程 杆 回程杆的碰面是否良好 回程杆的头部是否倒角 推板上是否有冷却 厚度是否够. 是否会弯 推 分型面是否设计缓冲块或勒聚胺脂块 板 回位弹簧和导柱的位置设计有无问题(因弯曲而动作不良) 在表面按回位弹簧时要在背面把螺丝 角落的镶块要注意斜度的设定和推杆孔的间隙 顶 环式镶块要却认是否有冷却 出 环式镶块的有配管型. 动作时要确认是否有干涉 镶 块 环式镶块顶出时是否会因重量发生平衡不良(支点确认) 动作部位是否使用了无油导套和轴承 顶板和芯子和顶杆导柱位置有无错位 设定的行程能否顺畅动作 是否使用了中荷重的弹簧 早回位弹簧是否能顺畅回位(0面) 100T以上的自动落下无问题否 150T以上自动取出无问题否 有无顶杆回位确认限位(防止滑块和顶杆相互干涉) 有无强制回位的装置(防止滑块和顶杆相互干涉) 顶出有无白化 是否多肉 有无拉着 (顶杆. 导柱) 顶杆眼加工间距是否良好(有无紧) 离型的行程有无问题 动作时使用油缸的时候.构造和轴承是否无问题 是否使用特殊构造(轴承.2段顶出.斜向凸轮) 固定板上是否安装了顶杆孔用的垫片 出荷前顶杆是否清扫好(润滑油.研磨膏) 是否确认了备品的种类荷数量
排气导套是否有台肩或横向顶丝固定侧是否有保护锁块pl面上有突形吊物是否平衡各顶板的螺丝孔处理基准面是否有标记螺丝有无弯曲和龟裂确认部品350t的时候要使其能采取一点吊爱丽思的特别式样吊的平衡是否好挂上钢丝绳时有无干涉物对突出物品的保护是否到位固定板和对各个板上的水嘴的保护热流道模具在换色时型板是否能分离确认为防止各型板丢失是否进行了丝锥处理支脚4的粗细平衡性螺丝是否够深根据模具的重量选择的型号是否合适是否安全周围有无干涉物装卸有无问题有有有ok是否有标牌模具尺寸
钢板模具动静态检查表
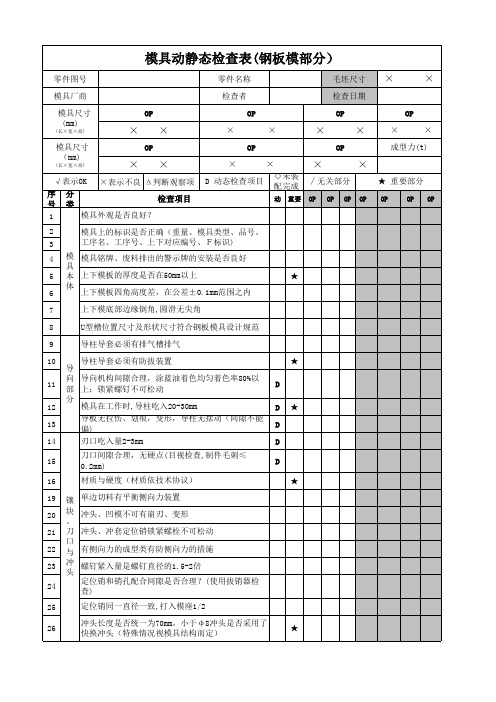
D D
D D
★ ★
64 65 66 67 68
标准件全部按协议要求使用 模柄需采用法兰式模柄 其 到底标记深度0.3mm,不易辨别左右件用L、R代替 它 制件无起皱、压伤、隐裂、棱线清晰,符合数模 制件毛刺≤0.2mm
★
D D
验收结论
ห้องสมุดไป่ตู้
确认人
动 重要 OP OP OP OP
★ 重要部分
OP OP OP
1 2 3 4 5 6 7 8 9 10 11 12 13 14 15 16 19 20 21 22 23 24 25 26 镶 块 、 刀 口 与 冲 头
模具外观是否良好? 模具上的标识是否正确(重量、模具类型、品号、 工序名、工序号、上下对应编号、F标识) 模 模具铭牌、废料排出的警示牌的安装是否良好 具 本 上下模板的厚度是否在50mm以上 体 上下模板四角高度差,在公差±0.1mm范围之内 上下模底部边缘倒角,圆滑无尖角 U型槽位置尺寸及形状尺寸符合钢板模具设计规范 导柱导套必须有排气槽排气 导柱导套必须有防拔装置 导 向 导向机构间隙合理,涂蓝油着色均匀着色率80%以 部 上;锁紧螺钉不可松动 分 模具在工作时,导柱吃入20-30mm 导板无拉伤、划痕,变形,导柱无摆动(间隙不能 偏) 刃口吃入量2-3mm 刀口间隙合理,无硬点(目视检查,制件毛刺≤ 0.2mm) 材质与硬度(材质依技术协议) 单边切料有平衡侧向力装置 冲头、凹模不可有崩刃、变形 冲头、冲套定位销锁紧螺栓不可松动 有侧向力的成型类有防侧向力的措施 螺钉紧入量是螺钉直径的1.5-2倍 定位销和销孔配合间隙是否合理?(使用拔销器检 查) 定位销同一直径一致,打入模座1/2 冲头长度是否统一为70mm,小于φ 8冲头是否采用了 快换冲头(特殊情况视模具结构而定) ★ ★ D D D D D ★ ★
- 1、下载文档前请自行甄别文档内容的完整性,平台不提供额外的编辑、内容补充、找答案等附加服务。
- 2、"仅部分预览"的文档,不可在线预览部分如存在完整性等问题,可反馈申请退款(可完整预览的文档不适用该条件!)。
- 3、如文档侵犯您的权益,请联系客服反馈,我们会尽快为您处理(人工客服工作时间:9:00-18:30)。
卡尺/键 按机床参数、图纸尺寸 目视 按 机 按 机 目视/图纸确认 目视/图纸确认 塞尺检验 目视 目视 目视 目视 目视
1 定位销垂直部位长度 2 定位销要做拔出孔,工作部位热处理
C 3 定位要有可调整量,前后保证5mm
4 单孔的定位挡块与卡槽间隙小于1mm
定 5 上模定位让空最少5mm
6 升降定位动作合理、顺畅,定位高度合理
付 表
客
件
户
名
车
件
型
号
模具静态检查表(一)
模
工
具
序
尺
寸
OP10 OP20 OP30 OP40 OP50 OP60
检验项 符合项 合格率 检验员
说明:
合 格“ O” 不合格“ N” 无此项“\”作 设计者 制造组
检查判定
区分 NO 静 态 检 查 项 目
检查基准
1
移动部件(压料体等)是否有安全及限位装 置
目视/铁片测试
D 4 镶块的接合间隙0.05MM内,并能够方便单个镶块取出 塞尺检测
5 镶块的与挡墙的间隙
无间隙(如有垫片必须固 定)
6 焊接质量(无横向裂纹渣孔,纵向100mm不得超过3条) 目视
镶 7 镶块底面研合率90%以上,平整度手感无明显凹槽
块 的 装
8 超过12KG的部件要有起吊孔,且M值刻印 9 镶块的对号标记全部敲好,字体清晰整齐,成一条线
12 冲头固定座要有销钉、螺塞(逐一检查),且松紧OK 目视
13 冲头与固定座底面平整
目视/平板推研确认
14 异形冲头凹模及有型面的凹模套要有防转
15 凹模孔下方不能有铸件突出
目视
16 凹模套无开裂
17 修边镶块强度薄弱处要做镶件式,要做备件
3 模具上F向及送料方向的标记是否正确
4 压机槽位置和数量
B
5
压机槽尺寸:寛度: mm
mm高度
mm深度
安 装 、 导 向
6 上模自动夹紧槽探测座面加工良好
7 导柱、导套、导板表面无划伤、檫伤
8 9 10 11
导 板导 柱导 套导 板
12 导柱、导套要有拆卸孔和排气孔
13 导向件(导柱导板导套锥形定距块)不允许人为打磨
料厚加3MM 目视/硬度计/锉刀 目视/直尺 目视/塞尺 目视/直尺 定位稳定、方便操作
位
区 分 NO
静态检查项目
1 模块的光洁度0.8以上,模块非工作面倒角5*45
检查判定
检 查 基 准 OP
OP
OP
上下 上 下 上下
目视
模模 模 模 模模
2 镶块底面研合率90%以上
目视/平板推研确认
3 镶块不能有磁性
目视
2 侧销与模座间隙0.03-0.06mm
手感转动
OP
OP
OP
上 模
下模
上 模
下 模
上 模
下 模
3 压板锁付螺钉深度大于直径的两倍 4 工作套筒高度是否一致(1mm内) 5 压板工作部分有效长度至少10MM
钢板尺 取出压料体,统一放入套筒检查工作高 度 目视,钢板尺
A 6 限位柱下方要有支撑筋,不可悬空
目视
7 滑块顶出装置是否有油槽,以防研伤
安 全
8 9 10 11 12
铸 入吊 耳压 料与 机安 全
13 弹性元件
目视
加强筋
敲击确认
目视
检查压料体(重点底面)
目视
目视,倒角美观,不能有弯曲、毛刺
外漏弹性元件增加防护板
14 是否有排油/排水/排气孔
目视
1 模具上键槽寛度 mm,位置是否正确
2 模具上的模具中心、压机中心V型槽铸出
工作部分、凸R角硬度不小于HRC50
1 螺孔,销孔距刀口距离必须最少大于5MM
2 刃口垂直度有效垂直面标准10MM,特殊情况最少5MM
目视/刀口角尺
3 修边刃口不能有啃坏,擦痕,擦黑,拉毛等现象
目视
4 表面淬火刃口端头10MM以内不允许任何缺陷
目视 无气泡、龟裂
5 镶块安装面形状不得突出镶块废料道以外
目视
16 上模镶块型面沿刃口,料边线15MM以外要做让空
1 成焊形接凹处模不口得圆有角气是 孔否 塌光 角顺 不, 平无 沙棱 眼线 ,修整后外观质量良 目视
DR 2 好
目视
3 排气孔位置及数量,直径为外板工作区域4mm,其他6mm
用细铁丝检查是否通透
FO 4 型面及R形状不得有凹坑不平滑伤铸造压痕等缺陷 目视
目视
6 废料刀口刃宽10MM以外要做让空
目视
7 废料刀切刃为
对
TR
8 废料刀布置合理,圆角处过R5MM左右分布
目视
错 目视
目视
9 超过1.2MM料厚,废料刀要有靠山,贴合无间隙
PI
10
焊接质量(无横向裂纹渣孔,纵向100mm不得超过3 条)
11 冲孔冲头、凹模不允许存在中心线偏移(间隙偏)
目视 目视 侧壁无黑色擦痕刮伤,目视
目视 目视
配 10 拆压料体需先拆卸的镶块要有明显标识
目视
及 11 模块的硬度HRC56--60
仪器测量
外 12 检查螺钉旋入深度(铸件大于2.0倍,钢件大于1.5倍 目视
观 13 螺钉沉孔倒角,分布合理,全部拧紧,无露头
目视
14 销钉松紧深度合适,为直径的两倍,上模是否有螺塞 目视
15 镶块上销孔上部要透空处理