模具常规项目检查表
模具验收检查单(模具自检表)

4.水嘴周边是否无干涉、妨碍码模。
其它
1.是否按照模具技术协议开模。
2.模具开合是否畅顺,开合顺序是否正确。
3.导套底部是否有排气槽。
4.电气系统是否能正常运作。
5.液压系统是否能正常运作。
验收人员
意见
验收是否合格□合格□不合格会签:
3.抽芯顺序能否可靠实现。
4.滑动面是否加工油槽或者自润滑。
顶出机构
1.顶出孔是否加工,是否与注塑机相配。
2.顶出是否畅顺,顶出顺序能否可靠实现。
3.顶出行程是否足够,顶针板是否有限位。
4.顶针是否已防转。
5.顶针是否装齐、正确。
冷却系统
1.是否已加工。
2.水嘴是否安装连接好,是否畅通,是否有标识。
5.油污、铁屑、杂物等是否清理干净。
6.各镶件是否固定好。
7.面、轮廓是否清晰、光顺无起级。
8.型芯、滑块、镶件是否有烧焊。
浇注系统
1.唧嘴球面R、小端口径、定位圈是否与啤机相配。
2.唧嘴是否已防转。
3.主流道、分流道的粗糙度是否达到要求。
4.是否有冷料井和排气槽。
抽芯机构
1.滑动是否畅顺、可靠。
2.抽芯前后是否有限位,抽芯行程是否足够。
模具验收检查单
产品名称
供应商
产品图号
版本Biblioteka 模穴数模具代码试模次数
验收日期
项目
检验内容
合格
可接受
不接受
备注
外观
1.是否清洁、无生锈、无凹陷及其它影响外观缺陷。
2.模具配件是否影响模具的吊装和存放。
型腔型芯
1.所有零件是否均已安装。
2.型腔型芯表面粗糙度是否达到要求。
模具检查表

检图100%1√2√3√4√5√6√7√8√9√10√11√12√13√14√15√16√17√18√19√20√21√2223√24√25√2627√28√293031323334上下模U形沟数量L≥1500mm6-8个,L<1500mm4-6个, 是否符合技术协议,分布是否合理;U形沟位置是否与机床吻合;U沟高度是否符合技术协议;U槽是否倒角来增加感应面(感应面150㎜)是否考虑隐藏部件和运动部件有无干涉(螺栓、回程钩、斜楔等)研讨签名三维是否干涉;是否做静态、动态(含非工作状态)检查;前工序板件是否与本工序结构干涉;相关装配尺寸是否衔接技术要求是否填写完整,综合图中技术要求是否和本图纸相符图层管理是否符合要求(见标准)结构是否经过内审人员确认(针对复杂斜楔类结构)起吊的选择是否符合技术协议,是否会与四周干涉;吊钩、螺纹套等埋入件的孔是否做出,孔径与深度是否匹配图纸修改后,是否影响其附近结构,造成悬空、干涉、不匹配等模具连接板、漏水孔、侧视孔、导板窥视孔(导腿处、压芯托芯导滑处、DR凸模处)是否设计机床偏移量是否在75mm以内,中心键槽(28+0.1~0.3)是否与机床吻合,上下模是否要通槽上下模或其与压芯或托芯配合处(导向、各类凸台)及其它需让位处位置尺寸是否一致、形状尺寸是否匹配安全螺栓是否与压边圈干涉压芯侧销伸出部分是否在上模做了避让压边圈接柱垫块是否与凸模干涉研讨记录销钉、螺钉拆卸空间是否足够;是否考虑为螺钉头预留避让空间是否考虑汽缸弯接头的空间避让40mm废料刀和上模刃口的避让是否做出(结构可不做出,由加工数模做出)做压芯过桥设计时是否考虑压芯行程+20mm安全量二.干涉检查冲头固定座与压料芯之间有无干涉装夹U槽四周空间是否符合标准,是否与废料滑板干涉工艺内容是否与工法图一致(核对工艺数模与工法图)压力源(顶杆)行程是否与压芯、托芯、小凸芯、压边圈行程一致;安全行程为ST+15mm(DR为ST+20mm);工作侧销能否用双槽(有CAM、氮气弹簧时不能用)特殊结构处在图纸中是否有提示、指导说明,是否规避了对称制作(如快速定位、左右标记、左右件不完全对称处)是否有模具运动动作线图(弹簧行程图、斜楔行程图);三维行程运动关系是否表达;回程状态是否表达减轻孔设计是否按设计标准,壁厚是否均匀模具检查表制件号: 工序号:检图者:产品名: 客 户:设计者:加工部位(拉延分模线、修边线、冲孔、翻边线、翻孔线、整形区)是否按照工艺数模(工法图仅为参考,核对工艺数模侧工作内容角度等)模具高度、长、宽是否合理,是否设计最省检 查 点检图日期:自检CH孔位置是否与前序(工法图)一致;下模是否符型,上模是否让位“F”向是否标识,与工法图是否一致一.共性内容检查模具是否设计有模具中心线、机床中心线压料芯是否优先设计起吊和翻转螺纹套;是否设计压芯装夹槽行程设定是否合理;行程限制器、存放器、缓冲装置是否设计,是否符合技术协议与设计标准;存放状态下弹性元件是否受力;是否超出装模高度快速定位分布是否合理;强度是否合适;左右两模件是否规避了对称制作NO压芯走框架结构处如果有刀块,刀块螺孔销孔是否悬空冲裁力、成型力、压料力、退料力是否计算。
模具检验记录表
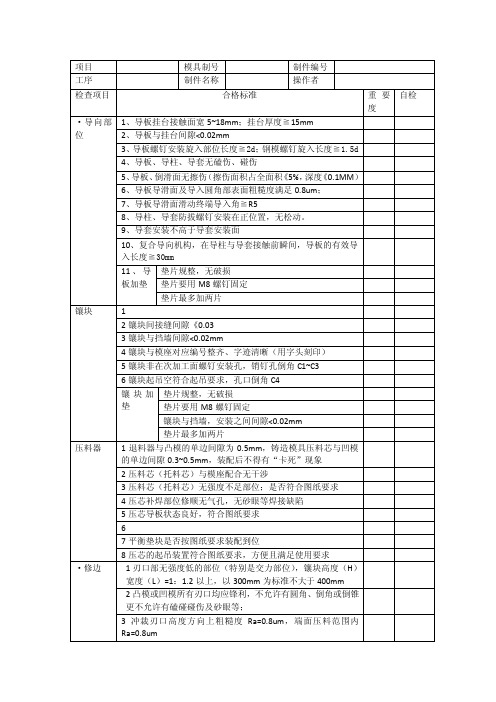
10 异型孔和非平面安装的凹模套及镶套安装孔必须加防转措 · 施 11 凹模套安装到底无悬空;凹模套与型面符型(允许凹模套高 于型面留有微量研量) 12 废料孔通畅无台阶 13 压、托料与冲头安装座无干涉现象 14 使用球锁紧凸模时,冲孔凸模周围的压料芯采用镶块式结 构,以使凸模拆卸方便
翻边、整 1 工作型面光顺无无用螺钉孔、销钉孔或其他孔;无磕伤碰伤;
4 废料滑板的板厚要符合要求,无变形,啊滑料板厚 1.8mm, 啊滑料板厚 2.5mm
5 废料盒要有防脱措施,防止模具起吊过程脱落 6 废料盒与模具型腔壁贴合,并且取放方便
7 折叠式废料滑板要用链条固定 ,不允许将链条固定在上模, 并且折叠固定后废料滑板不允许超出模具顶面
1 料厚(t)《1.5mm,刃口保留高度≧5mm 21.6mm 料厚(t)《3mm,刃口保留高度≧7mm
冲孔
7 修边镶块螺钉、销钉布局合理,螺钉、销孔不允许在一条直 线上 8 刃口镶块的材料牌号、编号需在镶块上打印清楚 1 冲头与固定座安装牢靠,无晃动 2 冲头刃口锋利无损伤 3 冲头弹料销活动自如,无卡滞现象 4 冲头安装销钉是,是否加销堵,起防止脱落保护措施 5 销钉松紧度合理,螺钉安装符合要求(冲头 10 个以下全部 拆检)
格)
3 斜楔压板与导滑面间隙《0.03mm
废料滑 板、废 盒
刃口背空 ·弹簧
键 安全
4 外漏的气缸、裸露的弹簧有安全防护措施 5 斜楔行程背板安装面铸件壁厚应在 60mm 以上,以确保安全
6 导板安装符合图纸要求 7 斜楔各部件刻印正确无误(包括镶块,冲头等与模座安装面 的对应标记刻印)
8 斜楔和挡墙间隙<0.02mm
自检
4、刃口要求锋利,不允许有过烧现象以及与刃口方向平行的 裂纹;垂直裂纹允许 100mm 内《3 个,裂纹宽度<0.05,长度 <5mm 5 上模修边镶块上螺钉、销钉有防脱落措施(螺钉加弹垫,销 钉加丝堵或弹簧销堵),特殊情况加盖板防脱 6 凸凹模刃口过渡出要有圆弧平顺连接,不允许有尖角或应力 集中
模具验收标准检查表

更多免费资料下载请进:
德信诚培训网 41 1 2 M12(含 M12)以上的螺丝是否为进口螺丝(12.9 级) 。 顶出时是否顺畅、无卡滞、无异响。 斜顶是否表面抛光,斜顶面低于型芯面 0.1—0.15mm。 斜顶是否有导滑槽, 材料为锡青铜, 内置在后模模架内, 用螺丝固定, 3 定位销定位。 4 顶出 复位、 抽插 芯、取 件 7 顶针板复位是否到底。 顶出距离是否用限位块进行限位, 限位材料为 45#钢, 不能用螺丝代 8 替,底面须平整。 9 10 复位弹簧是否选用标准件,两端不打磨、割断。 复位弹簧安装孔底面是否为平底,安装孔直径比弹簧大 5mm。 直径超过¢20mm 的弹簧内部是否有导向杆,导向杆比弹簧长 10— 11 15mm。 一般情况下,是否选用短形截面蓝色模具弹簧(轻负荷) ,重负荷用 12 红色,较轻负荷用黄色。 13 弹簧是否有预压缩量,预压缩量为弹簧总长的 10%—15%。 斜顶、滑块的压板材料是否为 638,氮化硬度为 HV700 或 T8A,淬火 14 处理至 HRC50—55。 滑块、抽芯是否有行程限位,小滑块限位用弹簧,在弹簧不便安装的 15 情况下可用波子螺丝,油缸抽芯有行程开关。 6 滑动部件是否有油槽(顶杆除外) ,表面进行氮化处理,硬度 HV700。 5 (大型滑块按客户要求) 。 所有顶杆是否有止转定位,按企业标准的三种定位方式,并有编号。 顶杆端面是否低于型芯面 0-0.1mm。
模具
6
冷却水嘴是否有进出标记,进水为 IN,出水为 OUT,IN、OUT 后加顺 序号,如 IN1、OUT1。 标识英文字符和数字是否大写(5/6″) ,位置在水嘴正下方 10mm 处, 7 字迹清晰、美观、整齐、间距均匀。 进出油嘴、进出气嘴是否同冷却水嘴,并在 IN、OUT 前空一个字符加 8 G(气) 、O(油) 。 模具安装方向上的上下侧开设水嘴,是否内置,并开导流槽或下方有支 9 撑柱加以保护。 10 无法内置的油嘴或水嘴下方是否有支撑柱加以保护。 模架上各模板是否有基准角符号, 大写英文 DATUM,字高 5/16″, 位置 11 在离边 10mm 处,字迹清晰、美观、整齐、间距均匀。
模具自检表格

8.不可以打编号的产品是否在水口上打上编号.
行 位 部 位
冷 却 系 统
顶出 系 统
制模 员:
10.攻牙孔的倒角位是否准确. 11.攻牙孔的孔径、孔距的尺寸是否准确无误. 1.行位起止位置是否正确可靠、装配合理、滑动顺畅.
2.行位润滑系统是否设立可靠.
1.冷却(运水)是否畅通.
2.料咀冷却水是否堵好,并无漏水现象.
有□ 没有 □
是□
否□
有□ 没有 □ 准确 □ 不准确 □ 准确 □ 不准确 □
是□
否□
是□
否□
是□
否□
是□
否□
正确 □ 不正确 □
正确 □ 不正确 □
审核:
注:试模前务必认真检查以上的重点,检查完将此表填好,交由文员存档.
目的:
模具自检表
鉴于模具制造周期较长,遗忘之事时有发生;模具试模前亦经常由于一些小疏忽 而导致重上压铸机、试模多次,浪费资源,为避免此类事情的发生,特针对一 些易遗忘和疏忽之处列于下表以备自检或互查。
型 号:
订 单 号:
开发日期:
项目
内容
资 1.模具与图纸尺寸是否合格(计缩水). 料
复 2.有公差的地方是否都准确无误. 核
1.顶针、司筒针的高度、方向、位置是否正确及无漏装.
2.顶针、斜顶及推板装配是否正确、伸缩顺畅,复位正确可 靠.
检查日
试模日
期:
期:
检查结果
备注
合格 □ 不合格 □
准确 □ 不准确 □
准确 □ 不准确 □
是□
否□
够□ 不够 □
有 □ 没有 □
平□ 不平 □
有□ 没有 □
有□ 没有 □
模具状况及成形状况检查表
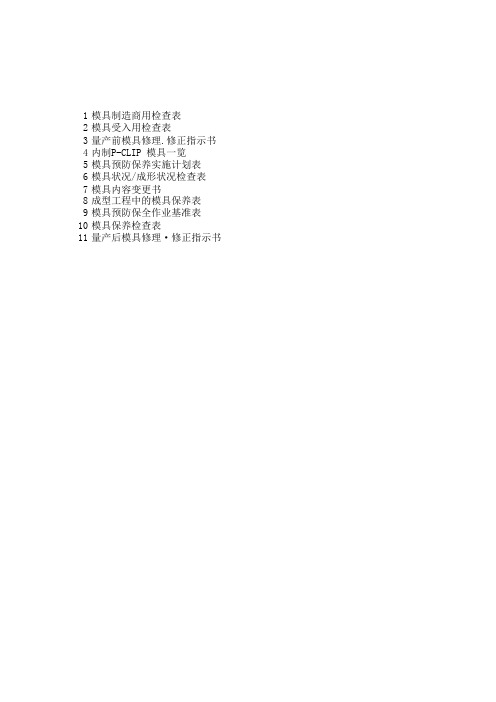
顶出导销的,导销套的清扫
弹簧,支撑块的清扫
一般分型面的清扫
用无尘布擦拭一般分型面 产 流道部的清扫 品 及 镶块部的清扫
滑 定位块的清扫 块 部 侧芯滑块的清扫
滑块导轨的清扫
确认带有球形活塞的模具的运作
确认吊眼螺丝的变形
确认吊眼螺丝的插入状况
其 确认定位环上的是否有严重的划伤等 它 确认模具联结器的变形,损伤
给品保5模以上样品
品担 质当 确
认承 认
流程:成型课—技术课—模具制造商—技术课-成型课-品质保证课(最终承认)-技术课(保管)
量产后模具修理·修正指示书
NO.
不具合内容
对策指示内容
费用明细(模具制造商记录栏)
工程
时间
及
零件
单价
金额
合计
修理内容(模具制造商记录)
模具制造商确认 印
模具接收日 STPS 制造商
1 有否确认模具图纸?
2 顶针孔是否呈三点式?
3 安装板是否是指定厚度?
4 吊环螺栓是否如指示?
5 是否是2点平行悬吊状或在定模上?
6 有否安装铭牌?
7 冷却水的IN、OUT是否在操作侧的反面?
8 是否安装指示?
10 模具是否能简单闭拢?滑块是否能用手轻易拨动?
Ⅳ
制定,改订 制定 改订
0~1万模/月
年月日 2004-8-2
—01 —02 —03 —04
作成
根据模具预防保养作业基 准书实施
确认
承认
备注
模具状况/成形状况检查表
Mold Condition Check List
质量记录编号: 品名:
日期
品号:
/ (星 / (星 / (星 / (星 / (星 / (星 / (星
模具检查表
项目名称.产品名称.OK N/A NG 导柱长于斜导柱吗?斜 滑块下有顶针是否加安OK N/A NG A .计量设定为产品20%-OK N/A NG C.射嘴空射压力bar 经过热流道bar 经过主流道bar 经过进胶口bar 3>>流道及流料井是否合理?10>>热流道温度是否有波动? 验证顶针感应开关感应距离是否在0.3-0.5mm? 热流道感应温度是否正常,热流道铭牌标示是否正确? 型腔内部是否有损伤及锈迹,斑点?1>>短射是否平衡?(热流道温度需设定一致)。
检查导柱.斜导柱.斜导柱孔是否有烧伤?4.正常运行后参数的调整3. 模具设定 检查顶出是否平衡.有无杂音及斜顶能否正常顶出?7>>流道是否弹飞?模具检查表A.确认所选的注塑机锁模力是否足够用于试模。
OK NG B.注塑机螺杆直径选择;实际用料量是注塑机螺杆直径的1到3倍。
OK NG 1.机台选择A>>检查模具各组水流量及水流压力是否符合标准。
(水流量为水管直径的0.472以上) 为预防开模时滑块掉落,天侧滑块是否加保护装置? 顶针是否能顶到底?是否有限位装置?A.调整合模低压保护力及保护时间。
B.模具温度正常后测量模具各区域之间的实际温度,偏差是否ok?6>>模具表面是否有料屑?(生产一段时间后再观察一次)2.上机后模具检查B>>模温正常后检查模具型腔有无漏水(如有热流道须在模温正常升温5分钟后才可开启热流道电源).C>>导柱.斜导柱.精定位.耐磨板加黄油润滑. 滑块是否有定位?限位螺丝位置是否合理?D>>模具正常开模后检查以下项目(试动作时首次选用低压安装模式进行) 检查抽芯动作有无异常,抽芯限位开关是否能正常使用? 开合模导柱是否有碰撞声音,开合模阻力是否偏大?检查压力损失,并做各点的压力记录(射胶速度选用机器中速)9>>射速选用高速后的零件是否存在重大缺陷?4>>浇口大小是否合理和一致,有无圆角?5>>流道及零件能否正常脱落?(在不影响模具安全的情况下尽量选用一次顶出)8>>型芯温度是否过高?(注塑过程中测量)B .注塑填充后模具有无风险(如粘模,顶出困难;变形,卡扣筋位断),如一切正常确认一下项目:2>>型腔填充末端及流道是否有排气? NG描述NG描述日期章能否正常转动,版本号是否做镶针? NG描述mm/sbar SI.在保压确定的情况下降低锁模力tonton ℃#N/A℃冷却时间:S 实际周期时间:S 是否用机械手:Remark:短射平衡重量标准小于等于1g ,相差小于10%。
车间生产模具点检表
柱的角度不超过20 度。
1.0 □是 □否 2.0 □是 □否 1.0 □是 □否
具 3.分型面保持干净、整洁。无手提砂轮打磨避空,封胶部分无凹陷。 F 4.排气槽深度小于塑料的溢边值,PP小于0.03mm,ABS、PS等小于0.05mm,排气 I 槽由机床加工,无手工打磨痕迹。 t 配 5.镶件研配到位安放顺利,定位可靠。 检 6.镶块、镶芯等可靠定位固定。圆形件有止转。镶块下面不垫铜片、铁片,如烧 查 焊垫起,烧焊处形成大面接触并磨平。并处理烧焊痕迹。
。 21.前模插入后模或后模插入前模,四周斜面锁紧或机加工避空。
1.0 □是 □否 1.0 □是 □否 1.0 □是 □否
□是 □否 □是 □否 □是 □否
22.定位销安装不能有间隙。要求拆装顺畅。
1.0 □是 □否
□是 □否
23.笥筒.镶针装配柱子深度胶位是否符合产品要求。
2.0 □是 □否
□是 □否
2.0 □是 □否
5.行位与前模的配合间隙要在-0.02MM;接触面到红丹要在98%以上。行位动作要 顺畅,用手可以推到接触面,用手也可以拉出来的效果。
2.0 □是 □否
6.铲基和行位耐磨块的配合间隙不得大于+0.03MM,或接触面到红丹98%以上。 1.0 □是 □否
□是 □否 □是 □否 □是 □否 □是 □否 □是 □否 □是 □否 □是 □否
1.0 □是 □否
□是 □否
4.外观及包装是否符合走模要求,备损件是否按《模具交付清单》配备。(注: 附图片)。
模具检验表
孔径间隙及顶杆高度尺寸
水管 水管/油管安装是否符合设计要求 油管 漏水测试
按设计图纸安装 水用高压时不能漏水
备件 备件型号及数量
按备件清单核对
备注:
检验员/日期:
批准/日期:
判定
模具检验表
客户单位:
压机型号:
检验结论:
产品名称 :
模具编号 :
一模(
)穴
检验项目
要求
检查结果
模框及各零件各边倒角。 外形
模具外观 模架侧面是否有安装铭牌或刻字。 分流锥是否有刻铭牌号。 标识 冷却水管进水及出水是否有标识。 产品日期标识是否有。ຫໍສະໝຸດ 产品标识、模穴标识是否正确。
尺寸 检查
模具外形尺寸和客户压机是否匹配。 吊环螺纹规 格及位置是 倒拉杆位置及螺纹是否符合压铸机。
浇道、渣包、排气口光洁度符合标准。 光滑不能有加工痕迹
滑块配合间隙检查。
活动灵活
滑出距离是否足够。 滑块 复位弹簧及复位板检查。
保险距离(5-10)mm 是否安装合理
油缸限位开关及安装是否确保正常生产。 油管方向朝压铸机对面
销子 销子配合检查
安装后销子固定处应高出产品面 (0.05-0.1)mm
顶杆 顶杆配合检查
浇口套尺寸和客户压机是否相匹配。
3x45°
不能有敲痕 、锈迹及杂物。
不需要
不需要
目测:(要求字迹清晰)
不需要
5102.3771.302 DUBLER NO72014
AK9M2
480x400x380
25kg以上都要有吊环
无倒拉螺丝
¢101.6x12
动,定模型腔,滑块,抛光是否符合标准。 240#油石打出
模具设计检查表
第2页/共6页
编号 检查项目 48 敲模孔及模芯螺孔是否合适 49 流道上铝料刻字是否符合指令单要求 50 模芯高出模框高度是否合适 51 模芯插穿位是否已避免直角插穿 52 模芯是否有正面吊环及天侧吊环 模框 53 模框外露的部分是否已倒角(分型面除外) 54 动定模框插穿的部分是否已避空 滑块 56 滑块行程是否合适 57 滑块复位机构是否合适 58 锁紧块是否合适 59 滑块冷却是否合适 60 滑块限位是否合适 61 滑块抽出后是否有足够的安全余量 62 滑块是否需要导向机构 63 斜导柱大小是否合适 64 天侧斜导柱是否干涉喷雾头 65 油缸规格是否合适 66 油缸缸径及行程是否合适 67 油缸支架是否合适 68 油缸联接是否合适 69 油缸油嘴是否符合标准 70 油缸油嘴的接出是否方便无干涉 浇注系统 71 浇道截面是否合适 72 是否需加流道板 73 渣包及排气槽是否合适
第3页/共6页
XXX机械制造有限公司
模具设计自检表
K3编号 项目工程师
设计检查
文件编号: 判定
第4页/共6页
设计检查
判定
第5页/共6页
设计检查
判定模具设计自检表
压铸机 冲头大小
第1页/共6页
编号 检查项目 冷却水路
23 水管装拆是否便捷 24 冷却水位置、尺寸及数量是否合适 25 冷却水是否避免同镶针、镶件及顶针穿透 26 运水是否存在死水 27 水管及运水螺孔是否符合标准 28 水管是否与吊环干涉 29 水管是否与码模夹干涉 30 水管是否与哥棱柱干涉 31 水管是否与螺丝等其他结构与孔干涉 顶出系统 32 针板导柱大小 33 顶出行程是否合适 34 垃圾钉位置、数量及尺寸是否合适 35 模脚尺寸及位置是否合适 36 支撑柱尺寸、数量及位置是否合适 37 回针尺寸及位置是否合适 38 顶针尺寸、数量及位置是否合适 39 是否需选用顶针套 40 顶针、顶针套及镶针避空孔是否符合标准 41 异形顶针是否已做防转 42 顶棍顶出时是否有干涉 模芯 43 缩水率选择 44 模芯厚度是否合适 45 分型线是否经客户批准 46 分型是否避免尖角位 47 精定位选择是否合适
- 1、下载文档前请自行甄别文档内容的完整性,平台不提供额外的编辑、内容补充、找答案等附加服务。
- 2、"仅部分预览"的文档,不可在线预览部分如存在完整性等问题,可反馈申请退款(可完整预览的文档不适用该条件!)。
- 3、如文档侵犯您的权益,请联系客服反馈,我们会尽快为您处理(人工客服工作时间:9:00-18:30)。
模具常规项目检查表
客户名称 零件名称 零件图号 零件材料 类别 序号
1 2
年 设计师 钳工组 生管员
Hale Waihona Puke 月日模具名称 模具编号 工序编号
使用设备 闭合高度 模具外形 设备参数
检
验
项
目
判 定 确 认
备
注
模具无锈斑、油污、涂鸦等不洁现象,表面无敲打、撞击、划痕等缺陷; 模板装配整齐、无错位现象,钢印在同一面同一方向,边、角、孔倒角均匀; 按客户或本公司要求涂装油漆,正面钉装铭牌; 模具闭合高度符合设计要求并与所使用的设备匹配; 行程限位柱、存放块、防护板(罩)、废料盒(槽)等所需辅助装置已安装好; 模具上所有螺钉都已锁紧,螺钉、销钉、模柄、吊钩(环)等零配件配置齐全。 内导柱或外导柱已有防反设计; 导柱、导套安装正确,长短、粗细合理,紧固无松动; 导柱与导套、模板之间间隙合理,运动过程顺畅,且已加注润滑油; 导板与导滑面配合顺畅,且受力面接合率大于80%,导板或导滑面适当开油槽。 模板、垫板、压边圈、凸模、镶件、刀口、成型面等按设计要求热处理; 各模板之间间隙合理、无单边,工作面无线割、CNC等明显加工痕迹; 工作面的光洁度必须能保证制件的质量和整个冲压过程的完成; 如有需要,必须开有排气孔(槽); 成形模的工作接触面研配率按客户要求或大于85%,若有必要安装到位标志; 冲头挂台不允许烧焊,冲头不能松动,冲头、镶件合理使用垫片; 定位销长短合适、松紧适宜、形状合理,零件取放方便,有防呆装置; 卸料板(块)活动顺畅,顶出高度、位置合理,受力均衡; 卸料弹簧大小、长短合适,布局合理,适当预压,行程到底时无压死变形现象; 使用氮气弹簧的模具,压力表的位置要易于读数、安全,必要时安装防护板。 凹模刀口厚度、锥度合适,出屑顺畅,垫板、底板、冲床台面等无阻塞; 冲孔不能有跳废料现象; 废料刀长短、位置布置合理,废料能快速、有效清理; 已做到材料利用率最高,废料、搭边合理; 起吊螺丝、安全防护板(罩)已安装到位,模具已退磁,样件已合格。
外 观 部 分
3 4 5 6 1
导 向 部 分
2 3 4 1 2 3 4
工 作 部 分
5 6 7 8 9 10 1
其 他 部 分
2 3 4 5
结 论
结 论
质 检 员 审 核 员
注:各项检查内容合格在判定或确认栏内打“√” 不合格在判定或确认栏内打“×” 无此项在判定或确认栏内打“○”
编号: YK-QP-PG-E-08