自动化专业英语课后习题答案
自动化专业英语第三版 王宏文

UNIT 1Electrical NetworksA 电路An electrical circuit or network is composed of elements such as resistors, inductors, and capacito rs connected together in some manner. If the network contains no energy sources, such as batteri es or electrical generators, it is known as a passive network. On the other hand, if one or more en ergy sources are present, the resultant combination is an active network. In studying the behavior of an electrical network, we are interested in determining the voltages and currents that exist wit hin the circuit. Since a network is composed of passive circuit elements, we must first define the electrical characteristics of these elements.电路或电网络由以某种方式连接的电阻器、电感器和电容器等元件组成。
如果网络不包含能源,如电池或发电机,那么就被称作无源网络。
换句话说,如果存在一个或多个能源,那么组合的结果为有源网络。
在研究电网络的特性时,我们感兴趣的是确定电路中的电压和电流。
因为网络由无源电路元件组成,所以必须首先定义这些元件的电特性.In the case of a resistor, the voltage-current relationship is given by Ohm's law, which states that t he voltage across the resistor is equal to the current through the resistor multiplied by the value of the resistance. Mathematically, this is expressed as就电阻来说,电压-电流的关系由欧姆定律给出,欧姆定律指出:电阻两端的电压等于电阻上流过的电流乘以电阻值。
自动控制专业英语 习题参考答案.doc

自动控制专业英语习题参考答案Lesson 1 Introduction to Control Systems1.Translate the following into Chinese.(1)In 1922 Minorsky worked on automatic controllers for steering ships and showed how stability could be determined from the differential equations describing the system.1922年,Minorsky开发了用于轮船驾驶的自动控制器,并指出根据描述系统的差分方程确定系统稳定性的方法。
(2) A home heating system in which a thermostat is the controller is an example of an automatic regulating system.家用供暖系统是自动调节系统的实例,其中的温度调节装置就是控制器。
(3)An engine which rejected no heat and which converted all the heat absorbed to mechanical work would therefore be perfectly consistent with the first law of thermodynamics.一台不散热并且把吸收的所有热量都转换为机械功的机器就与热力学第一定律完全一致。
(4)In short, a robot can do the dirty work —the dull, repetitious, dehumanizing and sometimes dangerous work that humans won"t or shouldn't do.简言之,机器人能干脏活,即那些人们不愿意或不该做的枯燥的、重复性的、呆板且有时有危险的活。
电气工程及其自动化专业英语苏小林课后答案

电气工程及其自动化专业英语苏小林课后答案【篇一:电气工程及其自动化准耶英语】/p> characterize描绘…的特征,塑造人物,具有….的特征property 性质,财产equal in magnitude to 在数量(数量级)上等同于 convert 转换converter 转换器time rate 时间变化率mathematically 从数学上来讲differentiatev 区分,区别in honor of 为纪念某人 name in honor of为纪念某人而以他命名electromotive force ( e m f )电动势voltaic battery 伏打电池,化学电池an element 一个电器元件interpret 口译,解释,说明potential difference/voltage 电势差/电压 expend 花费,消耗instantaneous 瞬时的,促发的passive sign convention 关联参考方向the law of conservation of energy 能量守恒定律 reference polarity 参考极性electron 电子 electronic 电子的 electric 电的,电动的 time-varying 时变的 constant-valued 常量的metallic 金属的be due to 是因为,由于,归功于building block 模块coulomb库伦,ampere安培,joule焦耳,volt伏特,watt瓦特,work 功变量u(t),i(t)是电路中最基本的概念。
他们描述了电路中的各种关系。
电荷量的概念是解释电现象的基本原理,电荷量也是电路中最基本的量。
电荷也是构成物质的原子的电器属性,量纲是库伦。
我们从初等物理可以得知所有物质是由基本组成部分原子组成,而原子又包括电子(electron),质子(proton)和中子(neutron)我们都知道电荷e是带负电的电子,在数量上等于1.60210*1019 c, 而质子携带同等电荷量的正电荷,相同数量的质子,电子使原子呈现电中性(neutrally charged)。
机械设计制造及其自动化专业英语课后题
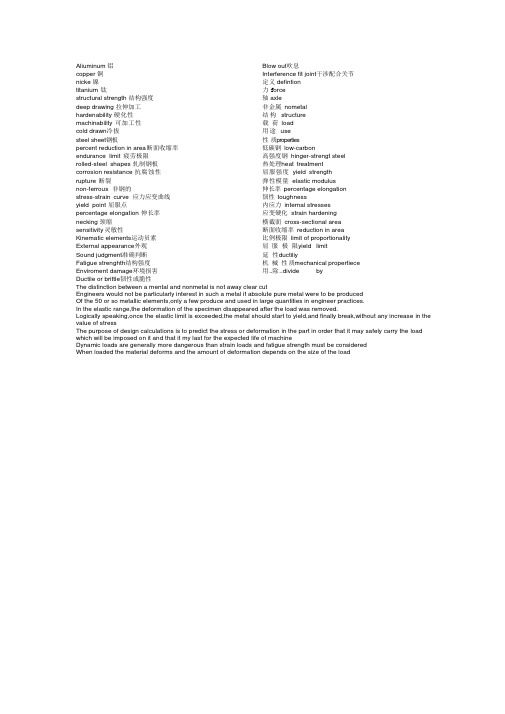
Aliuminum 铝copper 铜nicke 镍titanium 钛structural strength 结构强度deep drawing 拉伸加工hardenability 硬化性machinability 可加工性cold drawn冷拔steel sheet钢板percent reduction in area 断面收缩率endurance limit 疲劳极限rolled-steel shapes 轧制钢板corrosion resistance 抗腐蚀性rupture 断裂non-ferrous 非钢的stress-strain curve 应力应变曲线yield point 屈服点percentage elongation 伸长率necking 颈缩sensitivity 灵敏性Kinematic elements运动员素External appearance外观Sound judgment准确判断Fatigue strenghth结构强度Enviroment damage环境损害Ductile or brittle韧性或脆性Blow out吹息Interference fit joint干涉配合关节定义 defintion力 f orce轴axle非金属nometal结构structure载荷load用途use性质properties低碳钢low-carbon高强度钢hinger-strengt steel热处理heat treatment屈服强度yield strength弹性模量elastic modulus伸长率percentage elongation韧性toughness内应力internal stresses应变硬化strain hardening横截面cross-sectional area断面收缩率reduction in area比例极限limit of proportionality屈服极限yield limit延性ductiliy机械性质mechanical propertiece 用..除..divide byT he distinction between a mental and nonmetal is not away clear cutEngineers would not be particularly interest in such a metal if absolute pure metal were to be producedOf the 50 or so metallic elements,only a few produce and used in large quantities in engineer practices.In the elastic range,the deformation of the specimen disappeared after the load was removed.Logically speaking,once the elastic limit is exceeded,the metal should start to yield,and finally break,without any increase in the value of stressThe purpose of design calculations is to predict the stress or deformation in the part in order that it may safely carry the load which will be imposed on it and that it my last for the expected life of machineDynamic loads are generally more dangerous than strain loads and fatigue strength must be consideredWhen loaded the material deforms and the amount of deformation depends on the size of the load。
2012机械设计制造及其自动化专业外语参考答案
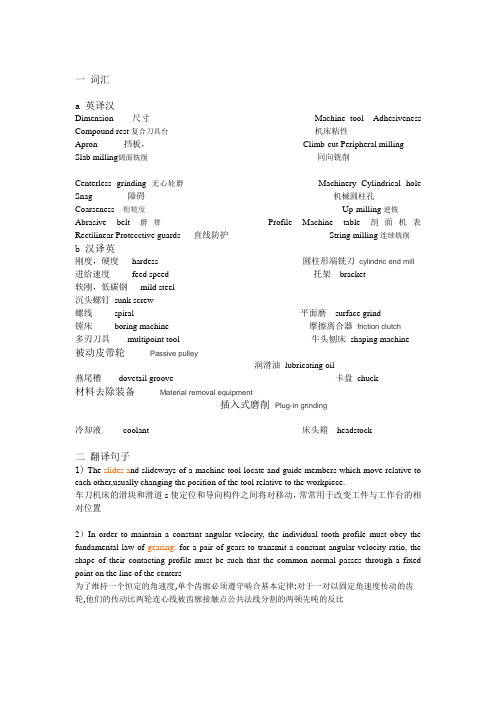
一词汇a 英译汉Dimension 尺寸Machine tool Adhesiveness Compound rest复合刀具台机床粘性Apron 挡板,Climb-cut Peripheral milling Slab milling阔面铣削同向铣削Centerless grinding无心轮磨Machinery Cylindrical hole Snag 障碍机械圆柱孔Coarseness 粗糙度Up-milling逆铣Abrasive belt磨带Profile Machine table剖面机表Rectilinear Protecctive guards 直线防护String milling连续铣削b 汉译英刚度,硬度hardess 圆柱形端铣刀cylindric end mill 进给速度feed speed 托架bracket软刚,低碳钢mild steel沉头螺钉sunk screw螺线spiral 平面磨surface grind镗床boring machine 摩擦离合器friction clutch多刃刀具multipoint tool 牛头刨床shaping machine被动皮带轮Passive pulley润滑油lubricating oil燕尾槽dovetail groove 卡盘chuck材料去除装备Material removal equipment插入式磨削Plug-in grinding冷却液coolant 床头箱headstock二翻译句子1) The slides a nd slideways of a machine tool locate and guide members which move relative to each other,usually changing the position of the tool relative to the workpiece.车刀机床的滑块和滑道s使定位和导向构件之间将对移动,常常用于改变工件与工作台的相对位置2)In order to maintain a constant angular velocity, the individual tooth profile must obey the fundamental law of gearing: for a pair of gears to transmit a constant angular velocity ratio, the shape of their contacting profile must be such that the common normal passes through a fixed point on the line of the centers为了维持一个恒定的角速度,单个齿廓必须遵守啮合基本定律:对于一对以固定角速度传动的齿轮,他们的传动比两轮连心线被齿廓接触点公共法线分割的两顿先吨的反比3)Plain milling cutters are adapted to cut by teeth with cutting edges situatued on the surface of a cylinder which can be circumscribed on cutter. face mills are adapted to cutting by teeth with cutting edges situated on the surface of the mill and partially on its cylindrial surface平铣刀适用于使用位于圆柱面上的齿上的切削刃工作的铣削,平面铣刀适用于使用位于铣刀表面和其部分圆柱面的齿上的切削刃做的铣削4)Pressures angles for spur gear are usually 14.5 or 20 degrees, although other values can be used. Meshing gears must have the same pressure angles.虽然其他值也也可以使用,但齿轮的压力角经常为14.5度或20度,相啮合的齿轮必须有相同的压力角5)The cross section of the milled surface corresponds to the outline or contour of the milling cutter or combination of cutters used.加工表面的界面要与使用的刀具或组合刀具的外轮廓一致6)Lets us now discuss the different concepts associated with the manufacturing accuracy required modern mass-production technologies.让我们来讨论有关现代大规模生产技术所要求的制造精度的不同概念。
机械设计制造及其自动化专业英语课后题

机械设计制造及其自动化专业英语课后题第一单元3. Aliuminum铝copper 铜nicke镍titanium 钛structural strength结构强度deep drawing拉伸加工4. 定义defition 力torce 轴axle(roller) 非金属nometal 结构structure 载荷load 用途use(application)性质properties(nature)(character)第二单元4.hardenability硬化性machinability可加工性cold drawn 冷拔steel sheet钢板percent reduction in area断面收缩率endurance limit疲劳极限rolled-steel shapes 轧制钢板corrosion resistance 抗腐蚀性rupture断裂5.低碳钢low-carbon 高强度钢hinger-strengt steel热处理heat treatment屈服强度yield strength弹性模量elastic modulus伸长率percentage elongation韧性toughness内应力internal stresses第三单元4.non-ferrous 非钢的stress-strain curve应力应变曲线yield point屈服点percentage elongation伸长率necking 颈缩sensitivity 灵敏性5.应变硬化strain hardening横截面cross-sectional area断面收缩率reduction in area比例极限limit of proportionality 屈服极限yield limit 延性ductiliy机械性质mechannicalpropertiece用..除..divide…by…第六单元3.tangential notes肤浅的事情flexible manufacturingsystem 柔性制造系统machine instruction机器指令economy of scale规模经济Hardwireyd logic controller硬固线逻辑控制transfer-line运输线,流水线numerically control(NC)数字控制direct numerical control(DNC)直接数字控制computer numerical control(CNC)计算机数字控制4.计算机辅助制造computer-aided manufacturing数控机床手工、半自动化或全自动化manal semiautomatic or full automation 尽管机械制造业一直在持续发展,但知道20世纪50年代才出现又一个重大发展。
自动化课后答案ch13 intro mfg sys-3e-si

Chapter 13INTRODUCTION TO MANUFACTURING SYSTEMSREVIEW QUESTIONS13.1What is a manufacturing system?Answer: The definition given in the text is the following: A manufacturing system is a collection of integrated equipment and human resources, whose function is to perform one or more processing and/or assemblyoperations on a starting raw material, part, or set of parts.13.2Name the four components of a manufacturing system.Answer: As listed in the text, the four components are (1) production machines plus tools, fixtures, and other related hardware, (2) a material handling system, (3) a computer system to coordinate and/or control thepreceding components, and (4) human workers to operate and manage the system.13.3What are the three classifications of production machines, in terms of worker participation?Answer: In terms of worker participation, the machines can be classified as (1) manually operated, (2) semi-automated or (3) fully automated.13.4What are the five material handling functions that must be provided in a manufacturing system?Answer: The five material handling functions that must be provided in a manufacturing system are (1) loading work units at each station, (2) positioning the work units at the station, (3) unloading the work units from the station, (4) transporting work units between stations in manufacturing systems comprised of multipleworkstations, and (5) temporary storage of work units to prevent starving of workstations.13.5What is the difference between fixed routing and variable routing in manufacturing systems consisting ofmultiple workstations?Answer: In fixed routing, the work units always flow through the same sequence of workstations. This means that the work units are identical or similar enough that the processing sequence is identical. In variable routing, work units are transported through a variety of different station sequences. This means that the manufacturing system processes or assembles different types of work units.13.6What is a pallet fixture in work transport in a manufacturing system?Answer: A pallet fixture is a workholder that is designed to be transported by the material handling system.The part is accurately attached to the fixture on the upper face of the pallet, and the under portion of the pallet is designed to be moved, located, and clamped in position at each workstation in the system.13.7 A computer system is an integral component in a modern manufacturing system. Name four of the eight functionsof the computer system listed in the text.Answer: The eight functions of the computer system identified in the text are (1) communicate instructions to workers, (2) download part programs to computer-controlled machines, (3) control the material handlingsystem, (4) schedule production, (5) failure diagnosis, (6) safety monitoring, (7) quality control, and (8)operations management.13.8What are the five factors that can be used to distinguish manufacturing systems in the classification schemeproposed in the chapter?Answer: The five factors identified in the text are (1) types of operations performed, (2) number ofworkstations, (3) system layout, (4) automation and manning level, and (5) part or product variety.13.9Why is manning level inversely correlated with automation level in a manufacturing system?Answer: Manning level is inversely correlated with automation level in a manufacturing system because thenumber of workers required to operate the system tends to be reduced as the level of automation increases.13.10Name the three cases of part or product variety in manufacturing systems. Briefly define each of the three cases.Answer: The three cases of part or product variety in manufacturing systems are (1) single model, (2) batch model, and (3) mixed model. In the single-model case, all parts or products made by the manufacturingsystem are identical. In the batch-model case, different parts or products are made by the system, but they are made in batches because the physical setup and/or equipment programming must be changed over between models. In the mixed-model case, different parts or products are made by the system, but the differences are not significant, so the system is able to handle them without the need for time-consuming changeovers insetup or program.13.11What is flexibility in a manufacturing system?Answer: Flexibility is the attribute that allows a mixed-model manufacturing system to cope with a certain level of variation in part or product style without interruptions in production for changeovers between models.13.12What are the three capabilities that a manufacturing system must possess in order to be flexible?Answer: As identified in the text, the three capabilities are (1) identification of the different work units, (2)quick changeover of operating instructions, and (3) quick changeover of the physical setup.。
自动化课后答案ch17 automated asby-3e-si
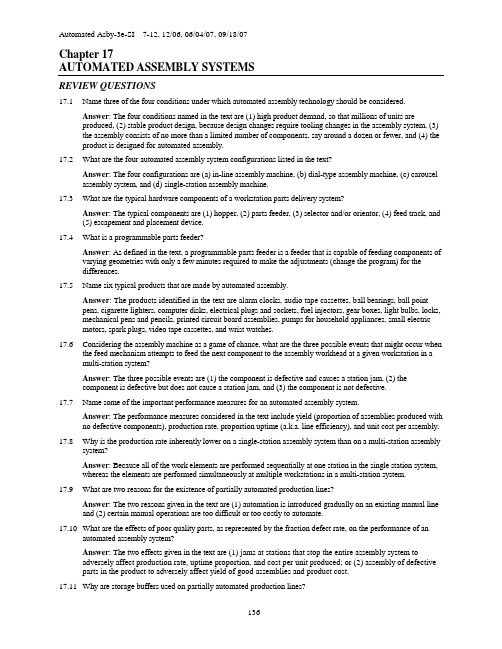
Chapter 17AUTOMATED ASSEMBLY SYSTEMSREVIEW QUESTIONS17.1Name three of the four conditions under which automated assembly technology should be considered.Answer: The four conditions named in the text are (1) high product demand, so that millions of units areproduced, (2) stable product design, because design changes require tooling changes in the assembly system, (3) the assembly consists of no more than a limited number of components, say around a dozen or fewer, and (4) the product is designed for automated assembly.17.2What are the four automated assembly system configurations listed in the text?Answer: The four configurations are (a) in-line assembly machine, (b) dial-type assembly machine, (c) carousel assembly system, and (d) single-station assembly machine.17.3What are the typical hardware components of a workstation parts delivery system?Answer: The typical components are (1) hopper, (2) parts feeder, (3) selector and/or orientor, (4) feed track, and(5) escapement and placement device.17.4What is a programmable parts feeder?Answer: As defined in the text, a programmable parts feeder is a feeder that is capable of feeding components of varying geometries with only a few minutes required to make the adjustments (change the program) for thedifferences.17.5Name six typical products that are made by automated assembly.Answer: The products identified in the text are alarm clocks, audio tape cassettes, ball bearings, ball point pens, cigarette lighters, computer disks, electrical plugs and sockets, fuel injectors, gear boxes, light bulbs, locks, mechanical pens and pencils, printed circuit board assemblies, pumps for household appliances, small electric motors, spark plugs, video tape cassettes, and wrist watches.17.6Considering the assembly machine as a game of chance, what are the three possible events that might occur whenthe feed mechanism attempts to feed the next component to the assembly workhead at a given workstation in a multi-station system?Answer: The three possible events are (1) the component is defective and causes a station jam, (2) thecomponent is defective but does not cause a station jam, and (3) the component is not defective.17.7Name some of the important performance measures for an automated assembly system.Answer: The performance measures considered in the text include yield (proportion of assemblies produced with no defective components), production rate, proportion uptime (a.k.a. line efficiency), and unit cost per assembly.17.8Why is the production rate inherently lower on a single-station assembly system than on a multi-station assemblysystem?Answer: Because all of the work elements are performed sequentially at one station in the single station system, whereas the elements are performed simultaneously at multiple workstations in a multi-station system.17.9What are two reasons for the existence of partially automated production lines?Answer: The two reasons given in the text are (1) automation is introduced gradually on an existing manual line and (2) certain manual operations are too difficult or too costly to automate.17.10What are the effects of poor quality parts, as represented by the fraction defect rate, on the performance of anautomated assembly system?Answer: The two effects given in the text are (1) jams at stations that stop the entire assembly system toadversely affect production rate, uptime proportion, and cost per unit produced; or (2) assembly of defective parts in the product to adversely affect yield of good assemblies and product cost.17.11Why are storage buffers used on partially automated production lines?Answer: Storage buffers are used on partially automated production lines to isolate the manual stations from the breakdowns of the automated stations. Thus, workers do not have to stop working when an automated station breaks down.PROBLEMSParts Feeding17.1 A feeder-selector device at one of the stations of an automated assembly machine has a feed rate of 25 parts perminute and provides a throughput of one part in four. The ideal cycle time of the assembly machine is 10 sec.The low level sensor on the feed track is set at 10 parts, and the high level sensor is set at 20 parts. (a) How long will it take for the supply of parts to be depleted from the high level sensor to the low level sensor once thefeeder-selector device is turned off? (b) How long will it take for the parts to be resupplied from the low level sensor to the high level sensor, on average, after the feeder-selector device is turned on? (c) What proportion of the time that the assembly machine is operating will the feeder-selector device be turned on? Turned off?Solution: (a) Time to deplete from n f2 to n f1Rate of depletion = cycle rate R c = 60/10 = 6 parts/minTime to deplete = (20 - 10)/6 = 10/6 = 1.667 min(b) Time to resupply from n f1 to n f2Rate of resupply = fθ - R c = 25(0.25) - 6 = 0.25 parts/minTime to resupply = (20 - 10)/0.25 = 10/0.25 = 40 min(c) Total cycle of depletion and resupply = 41.667 minProportion of time feeder-selector is on = 40/41.667 = 0.96Proportion of time feeder-selector is off = 1.667/41.667 = 0.0417.2Solve Problem 17.1 but use a feed rate of 32 parts per minute. Note the importance of tuning the feeder-selectorrate to the cycle rate of the assembly machine.Solution: (a) Time to deplete = (20 - 10)/6 = 1.667 min(b) Rate of resupply = 32(.25) - 6 = 8 - 6 = 2 parts/minTime to resupply = (20 - 10)/2 = 10/2 = 5 min(c) Total cycle time = 6.667 minProportion of time feeder-selector turned on = 5/6.667 = 0.75Proportion of time feeder-selector turned off = 1.667/6.667 = 0.2517.3 A synchronous assembly machine has 8 stations and must produce at an average rate of 480 completedassemblies per hour. Average downtime per jam is 2.5 min. When a breakdown occurs, all subsystems (including the feeder) stop. The frequency of breakdowns of the machine is once every 50 parts. One of the eight stations is an automatic assembly operation that uses a feeder-selector. The components fed into the selector can have any of six possible orientations, each with equal probability, but only one of which is correct for passage into the feed track to the assembly workhead. Parts rejected by the selector are fed back into the hopper. What minimum rate must the feeder deliver components to the selector during system uptime in order to keep up with the assembly machine?Solution: T p = 60/480 = 0.125 min/asbyT p = T c + FT d = T c +15025(.)= T c + 0.05T c = 0.125 - 0.05 = 0.075 min/asbyR c = 110.075cT== 13.333 asbys/minMin fθ = 0.1667 f = 13.333 asbys/min Feeder rate f = 1333301667..= 80 parts/minMulti-Station Assembly Systems17.4 A dial indexing machine has six stations that perform assembly operations on a base part. The operations,element times, q and m values for components added are given in the table below (NA means q and m are not applicable to the operation). The indexing time for the dial table is 2 sec. When a jam occurs, it requires 1.5 min to release the jam and put the machine back in operation. Determine (a) production rate for the assemblymachine, (b) yield of good product (final assemblies containing no defective components), and (c) proportion uptime of the system.Station Operation Element time q m1 Add part A 4 sec 0.015 0.62 Fasten part A3 sec NA NA3 Assemble part B 5 sec 0.01 0.84 Add part C 4 sec 0.02 1.05 Fasten part C 3 sec NA NA6 Assemble part D 6 sec 0.01 0.5Solution: (a) (mq) = 0.6(0.015) + 0.8(0.01) + 1(0.02) + .5(0.01) = .042T p = 0.1333 + 0.042(1.5) = 0.19633 min/asbyR p = 60/0.19633 = 305.6 asbys/hr(b) P ap = (1-0.015+0.6x.015)(1-0.01+0.8x.01)(1-0.02+1x0.02)(1-0.01+0.5x0.01)= (0.994)(0.998)(1.0)(0.995) = 0.98705(c) E = 0.1333/0.19633 = 0.679 = 67.9%17.5An eight-station assembly machine has an ideal cycle time of 6 sec. The fraction defect rate at each of the 8stations is q = 0.015 and a defect always jams the affected station. When a breakdown occurs, it takes 1 minute, on average, for the system to be put back into operation. Determine the production rate for the assemblymachine, the yield of good product (final assemblies containing no defective components), and proportionuptime of the system.Solution: T p = 0.1 + 8(1.0)(0.015)(1.0) = 0.22 min/asby.R p = 60/0.22 = 272.7 asbys/hrIf defects always jam the affected station, then m = 1.0P ap = (1 - 0.015 + 1x0.015)8 = 1.0 = yieldE = 0.1/0.22 = 0.4545 = 45.45%17.6Solve Problem 17.5 but assume that defects never jam the workstations. Other data are the same.Solution: T p = 0.1 + 8(0)(0.015)(1.0) = 0.10 min/asby.R p = 60/0.10 = 600 asbys/hrIf defects never jam, then m = 0P ap = (1 - 0.015 + 0x0.015)8 = 0.8861 = yieldE = 0.1/0.1 = 100%17.7Solve Problem 17.5 but assume that m = 0.6 for all stations. Other data are the same.Solution: T p = 0.1 + 8(0.6)(0.015)(1.0) = 0.172 min/asbyR p = 60/0.172 = 348.8 asbys/hrP ap = (1 - 0.015 + 0.6x0.015)8 = 0.953 = yieldE = 0.1/0.172 = 0.5814 = 58.14%17.8 A six-station automatic assembly line has an ideal cycle time of 12 sec. Downtime occurs for two reasons. First,mechanical and electrical failures cause line stops that occur with a frequency of once per 50 cycles. Average downtime for these causes is 3 min. Second, defective components also result in downtime. The fraction defect rate of each of the six components added to the base part at the six stations is 2%. The probability that a defective component will cause a station jam is 0.5 for all stations. Downtime per occurrence for defective parts is 2 min.Determine (a) yield of assemblies that are free of defective components, (b) proportion of assemblies that contain at least one defective component, (c) average production rate of good product, and (d) uptime efficiency.Solution: (a) P ap = (1 - 0.02 + 0.5x0.02)6 = (0.99)6 = 0.9415(b) P qp = 1 - 0.9415 = 0.0585(c) T p = 12/60 + 0.02(3) + 6(0.5)(0.02)(2) = 0.38 minR p = 60/0.38 = 157.6 cycles/hrR ap = (0.9415)(157.9) = 148.66 good asbys/hr(d) E = 0.2/0.38 = 0.526 = 52.6%17.9An eight-station automatic assembly machine has an ideal cycle time of 10 sec. Downtime is caused by defectiveparts jamming at the individual assembly stations. The average downtime per occurrence is 2.0 min. The fraction defect rate is 1.0% and the probability that a defective part will jam at a given station is 0.6 for all stations. The cost to operate the assembly machine is $90.00 per hour and the cost of components being assembled is $.60 per unit assembly. Ignore other costs. Determine (a) yield of good assemblies, (b) average production rate of good assemblies, (c) proportion of assemblies with at least one defective component, and (d) unit cost of the assembled product.Solution: (a) P ap = (1 - 0.01 + 0.6x0.01)8 = (0.996)8 = 0.9684(b) T p = 0.1667 + 8(0.6)(0.01)(2) = 0.2627 min/asbyR p = 60/0.2627 = 228.4 asbys/hrR ap = (0.9684)(228.4) = 221.2 good asbys/hr(c) P qp = 1 - 0.9684 = 0.0316(d) C pc = [0.60+1.50(0.2627)]/0.9684 = $1.0265/asby17.10An automated assembly machine has four workstations. The first station presents the base part, and the otherthree stations add parts to the base. The ideal cycle time for the machine is 3 sec, and the average downtimewhen a jam results from a defective part is 1.5 min. The fraction defective rates (q) and probabilities that adefective part will jam the station (m) are given in the table below. Quantities of 100,000 for each of the bases, brackets, pins, and retainers are used to stock the assembly line for operation. Determine (a) proportion of good product to total product coming off the line, (b) production rate of good product coming off the line, (c) totalnumber of final assemblies produced, given the starting component quantities. Of the total, how many are good product, and how many are products that contain at least one defective component? (d) Of the number ofdefective assemblies determined in above part (c), how many will have defective base parts? How many willhave defective brackets? How many will have defective pins? How many will have defective retainers?Station Part identification q m1 Base 0.01 1.02 Bracket 0.02 1.03 Pin 0.03 1.04 Retainer 0.04 0.5Solution: (a) P ap = (1-0.01+1x0.01)(1-0.02+1x0.02)(1-0.03+1x0.03)(1-0.04+0.5x0.04)= (1.0)(1.0)(1.0)(0.98) = 0.98(b) T p = 3/60 + (0.01+0.02+0.03+0.04x0.5)(1.5) = 0.17 min/cycle.R ap = 0.98(60/0.17) = 345.9 good asbys/hr(c) The diagram below shows quantities of components at the four workstations in the assembly machine:base 100,000 bracket100,000pin100,000retainer100,000→→→→95060 good asbys+ 1940 with defective 1000 def 2000 def 3000 def 1940 def retainers Total number produced = 95,060 + 1,940 = 97,000Number of units of good product = 95,060Number of units containing at least one defect = 1,940 (d) Number of products containing defective base parts = 0 Number of products containing defective brackets = 0 Number of products containing defective pins = 0Number of products containing defective retainers = 1,94017.11 A six-station automatic assembly machine has an ideal cycle time of 6 sec. At stations 2 through 6, parts feedersdeliver components to be assembled to a base part that is added at the first station. Each of stations 2 through 6 is identical and the five components are identical. That is, the completed product consists of the base part plus the five components. The base parts have zero defects, but the other components are defective at a rate q . When an attempt is made to assemble a defective component to the base part, the machine stops (m = 1.0). It takes an average of 2.0 min to make repairs and start the machine up after each stoppage. Since all components areidentical, they are purchased from a supplier who can control the fraction defect rate very closely. However, the supplier charges a premium for better quality. The cost per component is determined by the following equation:Cost per component = 0.1 +0.0012qwhere q = the fraction defect rate. Cost of the base part is 20 cents. Accordingly, the total cost of the base part and the five components is:Product material cost = 0.70 +0.006qThe cost to operate the automatic assembly machine is $150.00 per hour. The problem facing the production manager is this: As the component quality decreases (q increases), the downtime increases which drives production costs up. As the quality improves (q decreases), the material cost increases because of the priceformula used by the supplier. To minimize total cost, the optimum value of q must be determined. Determine by analytical methods (rather than trial-and-error) the value of q that minimizes the total cost per assembly. Also, determine the associated cost per assembly and production rate. (Ignore other costs). Solution : Product material cost C m = 0.20 + 5(0.1 +0.0012q ) = 0.70 + 0.006qT p = 0.1 + 5(1)(q )(2.0) = 0.1 + 10qC pc = C m + C L T p = 0.70 + 0.006q + 2.50(0.1 + 10q ) = 0.70 + 0.006q + 0.25 + 25q = 0.95 + 0.006q + 25qTaking the derivative of the cost equation with respect to q : 20.006250pc dC dqq -=+= 20.006q = 25 q 2 = 0.006/25 = 0.00024q = 0.0155Using this value in the preceding cost equation,C pc = 0.70 + 0.006/0.0155 + 2.50(0.1 + 10x0.0155) = $1.725/asbyT p = 0.1 + 5(10)(0.0155)(2.0) = 0.255 min/asby R p = 60/0.255 = 235.3 asbys/hr17.12 A six-station dial indexing machine is designed to perform four assembly operations at stations 2 through 5 aftera base part has been manually loaded at station 1. Station 6 is the unload station. Each assembly operation involves the attachment of a component to the existing base. At each of the four assembly stations, ahopper-feeder is used to deliver components to a selector device that separates components that are improperly oriented and drops them back into the hopper. The system was designed with the operating parameters for stations 2 through 5 as given in the table below. It takes 2 sec to index the dial from one station position to the next. When a component jam occurs, it takes an average of 2 min to release the jam and restart the system. Line stops due to mechanical and electrical failures of the assembly machine are not significant and can be neglected. The foreman says the system was designed to produce at a certain hourly rate, which takes into account the jams resulting from defective components. However, the actual delivery of finished assemblies is far below thatdesigned production rate. Analyze the problem and determine the following: (a) the designed average production rate that the foreman alluded to, (b) the proportion of assemblies coming off the system that contain one or moredefective components, (c) the problem that limits the assembly system from achieving the expected production rate, and (d) the production rate that the system is actually achieving. State any assumptions that you make in determining your answer.Station Assembly time Feed rate f Selector θq m2 4 sec 32/min 0.25 0.01 1.03 7 sec 20/min 0.50 0.005 0.64 5 sec 20/min 0.25 0.02 1.05 3 sec 15/min 1.0 0.01 0.7Solution: T d = 2 min, T c = 7 + 2 = 9 sec = 0.15 min Cycle rate R c = 1/0.15 = 6.667 cycles/min(a) ∑(mq) = 1(0.01) + 0.6(0.005) + 1(0.02) + 0.7(0.01) = 0.04T p = 0.15 + 0.04(2) = 0.23 minR p = 60/0.23 = 260.9 asbys/hr(b) P ap = (1-0.01+1x0.01)(1-0.005+0.6x0.005)(1-0.02+1x0.02)(1-0.01+0.7x0.01)= (1)(0.998)(1)(0.997) = 0.995P qp= 1 - 0.995 = 0.005R ap = 260.9(0.995) = 259.6 good asbys/hr(c) Station 2: fθ = 32(.25) = 8 components/minStation 3: fθ = 20(.50) = 10 components/minStation 4: fθ = 20(.25) = 5 components/minStation 5: fθ = 15(1.0) = 15 components/minThe problem is that the feeder for station 4 is slower than the machine's cycle rate of 6.667 cycles/min(d) If the machine operates at the cycle rate that is consistent with the feed rate of Station 4, then T c = 12 sec =0.20 minT p = 0.20 + 0.04(2) = 0.28 minR p = 60/0.28 = 214.3 asbys/hrR ap = 214.3(0.995) = 213.2 good asbys/hr17.13For Example 17.4 in the text, dealing with a single-station assembly system, suppose that the sequence ofassembly elements were to be accomplished on a seven-station assembly system with synchronous parts transfer.Each element is performed at a separate station (stations 2 through 6) and the assembly time at each respective station is the same as the element time given in Example 17.4. Assume that the handling time is divided evenly(3.5 sec each) between a load station (station 1) and an unload station (station 7). The transfer time is 2 sec, andthe average downtime per downtime occurrence is 2.0 min. Determine (a) production rate of all completed units,(b) yield, (c) production rate of good quality completed units, and (d) uptime efficiency.Solution: (a) T c = 7 + 2 = 9.0 sec = 0.15 minF = 0.02(1.0) + 0.01(0.6) + 0.015(0.8) + 0.02(1.0) + 0.012 = 0.070T p = 0.15 + 0.070(2.0) = 0.15 + 0.14 = 0.29 minR p = 1/0.29 = 3.45 asbys/min = 206.9 asbys/hr(b) P ap = (1.0)(0.996)(0.997)(1.0) = 0.993(c) R ap = 206.9(0.993) = 205.5 good asbys/hr(d) E = 0.15/0.29 = 0.5172 = 51.7%Comment: Comparing the values with those in Example 17.4, production rate is more than double for the multi-station system, yield is the same, and line efficiency is greatly reduced because of the much faster cycle time. Single Station Assembly Systems17.14 A single-station assembly machine is to be considered as an alternative to the dial-indexing machine in Problem17.4. Use the data given in the table for that problem to determine (a) production rate, (b) yield of good product(final assemblies containing no defective components), and (c) proportion uptime of the system. Handling time to load the base part and unload the finished assembly is 7 sec and the downtime averages 1.5 min every time acomponent jams. Why is the proportion uptime so much higher than in the case of the dial-indexing machine in Problem 17.4?Solution: (a) T c = 7 + (4 + 3 + 5 + 4 + 3 + 6) = 7 + 25 = 32 sec = 0.5333 min∑(mq) = 0.6(0.015) + 0.8(0.01) + 1(0.02) + 0.5(0.01) = 0.042 (same as for Problem 17.4)T p = 0.5333 + 0.042(1.5) = 0.59633 minR p = 60/0.59633 = 100.6 asbys/hr(b) P ap = (1-0.015+0.6x0.015)(1-0.01+0.8x0.01)(1-0.02+1x0.02)(1-0.01+0.5x0.01) = 0.98705 (same as forProblem 17.4)(c) E = .5333/.59633 = 0.8943 = 89.43%Comment: Proportion of uptime E is so much higher than in Problem 17.4 because the cycle time is much longer for the single-station machine than for the six-station dial-indexing machine (32 sec vs 6 sec). The averagedowntime per cycle is the same for both machines, but it is a much lower proportion of the longer cycle time in the single station case.17.15 A single station robotic assembly system performs a series of five assembly elements, each of which adds adifferent component to a base part. Each element takes 4.5 sec. In addition, the handling time needed to move the base part into and out of position is 4 sec. For identification, the components, as well as the elements thatassemble them, are numbered 1, 2, 3, 4, and 5. The fraction defect rate is 0.005 for all components, and theprobability of a jam by a defective component is 0.7. Average downtime per occurrence = 2.0 min. Determine (a) production rate, (b) yield of good product in the output, (c) uptime efficiency, and (d) proportion of the output that contains a defective type 3 component.Solution: (a) T p = T c + nmqT dT c = 4 + 5(4.5) = 26.5 sec = 0.44167 minT p = 0.44167 + 5(0.7)(0.005)(2.0) = 0.47667 minR p = 1/0.47667 = 2.098 asbys/min = 125.9 asbys/hr(b) P ap = (1 - 0.005 + 0.7(0.005))5 = (0.9985)5 = 0.9925(c) E = 0.44167/0.47667 = 0.9266 = 92.66%(d) Type 3 defect = 1 - (1 - 0.005 + 0.7(0.005)) = 0.005 - 0.7(0.005) = 0.3(0.005) = 0.001517.16 A robotic assembly cell uses an industrial robot to perform a series of assembly operations. The base part andparts 2 and 3 are delivered by vibratory bowl feeders that use selectors to insure that only properly oriented parts are delivered to the robot for assembly. The robot cell performs the elements in the table below (also given are feeder rates, selector proportion θ, element times, fraction defect rate q, and probability of jam m, and, for the last element, the frequency of downtime incidents p). In addition to the times given in the table, the time required to unload the completed subassembly takes 4 sec. When a linestop occurs, it takes an average of 1.8 min to make repairs and restart the cell. Determine (a) yield of good product, (b) average production rate of good product, and(c) uptime efficiency for the cell? State any assumptions you must make about the operation of the cell in orderto solve the problem.Element Feed rate f Selector θElement Time T e q m p1 15 pc/min 0.30 Load base part 4 sec 0.01 0.62 12 pc/min 0.25 Add part 23 sec 0.02 0.33 25 pc/min 0.10 Add part 34 sec 0.03 0.84 Fasten 3 sec 0.02Solution: Assumptions: (1) Feeders continue to operate and deliver parts into the feed track even when a jam occurs during assembly. (2) Low level quantity n f1 is sufficient to eliminate possibility of a stockout.T c = T h + ∑T e = 4 + 4 + 3 + 4 + 3 = 18 sec = 0.3 minT p = T c + (∑qm + p)T d = 0.3 + (0.01 x 0.6 + 0.02 x 0.3 + 0.03 x 0.8 + 0.02)(1.8)= 0.3 + 0.056)(1.8) = 0.4008 min/asbyCheck feed rates:f1θ1 = 15(0.3) = 4.5 pc/min or 0.2222 min/pcf2θ2 = 12(0.25) = 3.0 pc/min or 0.3333 min/pcf3 3 = 25(0.1) = 2.5 pc/min or 0.40 min/pcEach of these can be completed within the average cycle time of the robot assembly operation.(a) P ap = (1 - 0.01 + 0.6 x 0.01)(1 - 0.02 + 0.3 x 0.02)(1 - 0.03 + 0.8 x 0.03)= (0.996)(0.986)(0.994) = 0.976(b) R p = 1/0.4008 = 2.495 asbys/min = 149.7 asbys/hrR ap = 149.7(0.9762) = 146.1 good asbys/hr(c) E = 0.3/0.4008 = 0.7485 = 74.85%Alternative assumption: (1) Feeder stops when jam occurs. Hence, cycle time is limited by feeder #3.T c = 0.4 min T p = 0.4 + (0.056)(1.8) = 0.5008 min(a) R p = 1/0.5008 = 1.9968 asbys/min = 119.8 asbys/hr P ap = 0.976 (same as above)(b) R ap = 119.8(0.9762) = 116.9 good asbys/hr(c) E = 0.400/0.5008 = 0.7987 = 79.87%Partial Automation17.17 A partially automated production line has a mixture of three mechanized and three manual workstations. Thereare a total of six stations, and the ideal cycle time of 1.0 min, which includes a transfer time of 6 sec. Data on the six stations are listed in the accompanying table. Cost of the transfer mechanism C at = $0.10/min, cost to run each automated station C as = $0.12/min, and labor cost to operate each manual station C w = $0.17/min. It has been proposed to substitute an automated station in place of station 5. The cost of this station is estimated at C as5 = $0.25/min and its breakdown rate p5 = 0.02, but its process time would be only 30 sec, thus reducing the overall cycle time of the line from 1.0 min to 36 sec. Average downtime per breakdown of the current line, as well as for the proposed configuration, is 3.5 min. Determine the following for the current line and the proposed line: (a) production rate, (b) proportion uptime, and (c) cost per unit. Assume the line operates without storage buffers, so when an automated station stops, the whole line stops, including the manual stations. Also, in computing costs, neglect material and tooling costs.Station Type Process time p i1 Manual 36 sec 02 Automatic 15 sec 0.013 Automatic 20 sec 0.024 Automatic 25 sec 0.015 Manual 54 sec 06 Manual 33 sec 0Solution: For the current line,(a) T c = 1.0 min, F = 0.01 + 0.02 + 0.01 = 0.04T p = 1.0 + 0.04(3.5) = 1.0 + 0.14 = 1.14 min/unit, R p = 1/1.14 = 0.877 units/min = 52.6 units/hr(b) E = 1.0/1.14 = 0.877 = 87.7%(c) C o = 0.10 + 3(0.12) + 3(0.17) = $0.97/min. C pc = (0.97)(1.14) = $1.106/unit.For the proposed line in which station 5 is automated,(a) T c = 36 sec = 0.6 min F = 0.01 + 0.02 + 0.01 + 0.02 = 0.06T p = 0.6 + 0.06(3.5) = 0.6 + 0.21 = 0.81 min/unit, R p = 1/0.81 = 1.235 units/min = 74.1 units/hr(b) E = 0.6/0.81 = 0.7407 = 74.1%(c) C o = 0.10 + 3(0.12) + 0.25 + 2(0.17) = $1.05/min C pc = (1.05)(0.81) = $0.851/unit.17.18Reconsider Problem 17.17 except that both the current line and the proposed line will have storage buffers beforeand after the manual stations. The storage buffers will be of sufficient capacity to allow these manual stations to operate independently of the automated portions of the line. Determine (a) production rate, (b) proportionuptime, and (c) cost per unit for the current line and the proposed line.Solution: For the current line,(a) Automated section of line: T c = 25 + 6 = 31 sec = 0.5167 minF = 0.01 + 0.02 + 0.01 = 0.04 T p = 0.5167 + 0.04(3.5) = 0.6567 min/unit.Manual section of line: T c = 54 + 6 = 60 sec = 1.0 minNo breakdowns, so F = 0. T p = 1.0 + 0(3.5) = 1.0 min/unit.Using the manual section as the limiting section, R p = 1/1.0 = 1.0 units/min = 60.0 units/hr(b) E = 0.5167/1.0 = 0.5167 = 51.7%Comment: The automated sections of the line could operate with an efficiency = 0.5167/0.6567 = 0.787, but production rate is ultimately limited by the manual cycle time of 1.0 min.(c) C o = 0.10 + 3(0.12) + 3(0.17) = $0.97/min C pc = (0.97)(1.0) = $0.97/unit.For the proposed line in which station 5 is automated,(a) Automated section of line: T c = 36 sec = 0.6 minF = 0.01 + 0.02 + 0.01 + 0.02 = 0.06 T p = 0.6 + 0.06(3.5) = 0.6 + 0.21 = 0.81 min/unit.Manual section of line: T c = 36 + 6 = 42 sec = 0.7 minNo breakdowns, so F = 0. T p = 0.7 + 0(3.5) = 0.7 min/unit.Using the automated section as the limiting section, R p = 1/0.81 = 1.235 units/min = 74.1 units/hr(b) E = 0.6/0.81 = 0.7407 = 74.1%(c) C o = 0.10 + 3(0.12) + 0.25 + 2(0.17) = $1.05/min C pc = (1.05)(0.81) = $0.851/unit.17.19 A manual assembly line has six stations. The assembly time at each manual station is 60 sec. Parts are transferredby hand from one station to the next, and the lack of discipline in this method adds 12 sec (T r = 12 sec) to the cycle time. Hence, the current cycle time is 72 sec. The following two proposals have been made: (1) Install a mechanized transfer system to pace the line; and (2) automate one or more of the manual stations using robots that would perform the same tasks as humans only faster. The second proposal requires the mechanized transfer system of the first proposal and would result in a partially or fully automated assembly line. The transfer system would have a transfer time of 6 sec, thus reducing the cycle time on the manual line to 66 sec. Regarding thesecond proposal, all six stations are candidates for automation. Each automated station would have an assembly time of 30 sec. Thus if all six stations were automated the cycle time for the line would be 36 sec. There aredifferences in the quality of parts added at the stations; these data are given in the accompanying table for each station (q = fraction defect rate, m = probability that a defect will jam the station). Average downtime per station jam at the automated stations is 3.0 min. Assume that the manual stations do not experience line stops due todefective components. Cost data: C at = $0.10/min; C w = $0.20/min; and C as = $0.15/min. Determine if either or both of the proposals should be accepted. If the second proposal is accepted, how many stations should beautomated and which ones? Use cost per piece as the criterion of your decision. Assume for all cases considered that the line operates without storage buffers, so when an automated station stops, the whole line stops, including the manual stations.Station q i m i Station q i m i1 0.005 1.0 4 0.020 1.02 0.010 1.0 5 0.025 1.03 0.015 1.0 6 0.030 1.0Solution: Proposal 1: Current operation: T c = 1.2 min C o = 6(0.20) = $1.20/minC pc = 1.20(1.2) = $1.44/unit.Proposal: T c = 1.1 min C o = 0.10 + 6(0.20) = 1.30/minC pc = 1.30(1.1) = $1.43/unit.Conclusion: Accept Proposal 1.Proposal 2: T c = 36 sec = 0.6 min if all six stations are automated.F = 0.005(1.0) + 0.01(1.0) + 0.015(1.0) + 0.02(1.0) + 0.025(1.0) + 0.03(1.0) = 0.105T p = 0.6 + 0.105(3.0) = 0.6 + 0.315 = 0.915 min/unitC o = 0.10 + 6(0.15) = 1.00/minC pc = 1.00(0.915) = $0.915/unitConclusion: Accept Proposal 2.。
- 1、下载文档前请自行甄别文档内容的完整性,平台不提供额外的编辑、内容补充、找答案等附加服务。
- 2、"仅部分预览"的文档,不可在线预览部分如存在完整性等问题,可反馈申请退款(可完整预览的文档不适用该条件!)。
- 3、如文档侵犯您的权益,请联系客服反馈,我们会尽快为您处理(人工客服工作时间:9:00-18:30)。
• 比 例 加 积 分 加 微 分 proportional plus integral plus
derivative (PID)
济南大学控制科学与工程学院
自动化专业英语
5
1.3 Stability of closed-loop control
systems
• 2. Put the following into chinese
• 判据 criteria 拉氏变换 Laplace transform • 零点zero-point 极点 pole-point • 特征方程 characteristic equation • 系数 parameter/coefficient • 偏差变量 deviation variable 比较器 comparator • 伺服问题 servo problem • 给定变化 given changes • 负载变化 load fluctuation/variation in load
• linear quadratic regulator 线性二次调节器
• Linear quadratic 线性二次型 controller 控制器
• Simulation 仿真
temperature 温度
• Flow rate 流速
pressure 压力
• Concentration 浓度 level 液位,液面
• 控制系统设计 control system design • 设计模型 design model • 炼油 oil refinery 化工 chemical (engineering) • 电力 (electric) power 造纸 paper (making) • 水泥 cement 纺织 textile • 塑料 plastic 钢铁 steel (iron and steel) • 航空航天 aerospace (Aeronautics and Astronautics) • 再沸器 reboiler
济南大学控制科学与工程学院
自动化专业英语
9
1.5Controller tunning
• 2. Put the following into chinese
• Setting 设置
tunning 整定,调节
• Trial and error 试差法 guideline 方针,指南
• Averaging control 平均控制 residence time 滞留时间
• observable output 可观测输出
• Measurable disturbance 可测量扰动
济南大学控制科学与工程学院
自动化专业英语
8
1.4 The design process of control system
• 3 Put the following into English
济南大学控制科学与工程学院
自动化专业英语
3
1.2 What is feedback and what are its effects?
• 2. Put the following into chinese
• Stability 稳定性
sensitivity 灵敏度
• Actuator 执行器 sensor 传感器 Transducer 传感器
• Pole-zero cancellation 零极相消
• Self-regulating 自调节
济南大学控制科学与工程学院
自动化专业英语
6
1.3 Stability of closed-loop control systems
• 3 Put the following into English
• Investment 投资
fundamental 基础的
• Evaluating 评价
benifit 利润,益处
• Distillation column 分裂蒸馏塔
• Overhead 在头上的, 高架的 process dynamic 过程动态
• Manipulatable input 可操作输入
• Oscillatory 振动的
damp 衰减
• Unstable 不稳定地 complex number 复数
• Controlled variable 被控变量
• Manipulated variable 操纵变量
• Load variable 负载变量
error 误差
• Process transfer function 过程传递函数
济南大学控制科学与工程学院
自动化专业英语
7
1.4 The design process of control system
• 2. Put the following into chinese
• Design 设计 decision 决定,决策
• Methodology 方法论 productivity 生产率,生产力
济南大学控制科学与工程学院
济南大学控制科学与工程学院
自动化专业英语
14
2.2 Level measurements
• 2. Put the following into English
• 密度 density 浮力式液面计 buoyancy level meter • 浮球 float 标尺 scale • 电位计 potentiometer 导电电极 conductive probe • 电容电极 capacitive probe 超声波 ultrasonic wave • 张力式仪表 tension gauge 应变仪 strain gauge • 荷重传感器 load sensor
自动化专业英语
课后作业答案
1.1 Introduction to Process Control
• 2. Put the following into chinese
• performance 性能 process plant 过程系统 • process control 过程控制 reference 参考 • operating conditions 运行条件 • disturbance 扰动,干扰 • Automatic control 自动控制 • Manual control 手动控制,人工控制 • Perfect control 完美控制 • Feedback control 反馈控制 • Set point 设定值 • Controlled variable 被控变量
济南大学控制科学与工程学院
自动化专业英语
11
2.1 Pressure measurements
• 1. Put the following into chinese
• Atmospheric pressure 大气压 • absolute pressure 绝压 • Gauge pressure 表压 • differential pressure 差压 • Total vacuum 完全真空 diaphragm 膜片 • Capsule 膜盒 bellow 波纹管 • Bourdon tube 波登管 silicon diaphragm 硅膜片
济南大学控制科学与工程学院
自动化专业英语
15
2.3 Flow measurements
• 1. Put the following into chinese
• Flow rate 流速 accounting 统计,计算 • Laminar flow 层流 energy losses 能量损失 • Total flow 总体流量 pressure energy 压能 • Kinetic energy 动能 potential energy 势能 • Restriction 约束,限制 orifice plate 孔板 • Venturi tube 文丘里管 flow nozzle 测流嘴 • Elbow 肘,弯管接头 rotameter 转子流量计 • Mass flow 质量流
济南大学控制科学与工程学院
自动化专业英语
10
1.5Controller tunning
• 3 Put the following into English
• 流量控制 flow control 液面控制 level control • 压力控制 pressure control 温度控制 temperature control • 成分控制 composition control • 临界增益法 ultimate gain method • 临界周期 ultimate cycling 超调 overshoot • 热交换器 heat exchanger 化学反应器 chemical reactor • 汽化器 vaporization (carburettor)
pressure gauges)
济南大学控制科学与工程学院
自动化专业英语
13
2.2 Level measurements
• 1. Put the following into chinese
• Level measurement 液位测量 container 容器 • Interface 界面 buoyancy 浮力 • Immersed 浸没 radium 镭 • Capacitive probe 电容电极 nonconductive 不导电的 • Dielectric constant 介电常数 sight glass 玻璃液面计 • Float 浮体,浮球,浮标 level formula 液位公式
• 可编程逻辑控制器programmable logic controller (PLC)
• 模型 model
黑箱 black-box