生产线改善报告
生产线改造年度工作总结汇报

生产线改造年度工作总结汇报尊敬的领导和各位同事:
我很荣幸能够在此向大家汇报我们生产线改造的年度工作总结。
在过去的一年里,我们团队经过不懈努力,取得了一系列显著的成就,为公司的发展和生产效率提升做出了重要贡献。
首先,我们在生产线改造方面取得了巨大的进步。
通过引进先进的生产设备和
技术,我们成功地提高了生产线的自动化程度,大大提升了生产效率和产品质量。
同时,我们还对生产流程进行了优化和改进,使得整个生产过程更加顺畅和高效。
其次,我们注重了员工的培训和技能提升。
通过组织各类培训和学习活动,我
们不断提升员工的技术水平和工作能力,使他们能够更好地适应新的生产线设备和流程,为生产线改造提供了有力的保障。
此外,我们还加强了生产线的安全管理工作。
我们制定了一系列严格的安全操
作规程和标准,加强了对生产线设备的维护和保养,有效地提高了生产线的安全性和稳定性,为员工的生命财产安全提供了有力的保障。
最后,我们还注重了与供应商和客户的沟通和合作。
通过与供应商的紧密合作,我们成功地引进了一批高性能的生产设备和原材料,为生产线改造提供了有力的支持。
同时,我们还积极与客户沟通,及时了解他们的需求和反馈,不断改进和优化我们的生产线,以满足客户的需求。
总的来说,我们在生产线改造方面取得了一系列显著的成就,为公司的发展和
生产效率提升做出了重要贡献。
但是,我们也清楚地意识到,生产线改造工作仍然存在一些问题和挑战,需要我们继续努力和改进。
我们将继续秉承“精益求精、追求卓越”的工作态度,不断提升自身的专业水平和团队协作能力,为公司的发展和生产线改造工作再创辉煌!
谢谢大家!。
生产车间改善报告的范文(两篇)2024
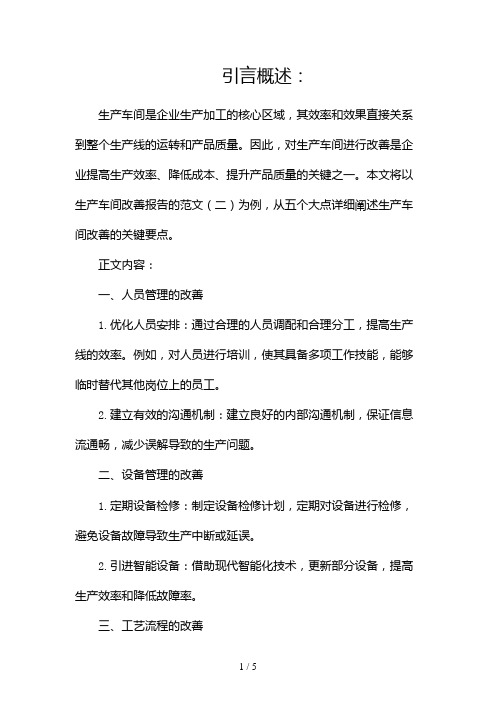
引言概述:生产车间是企业生产加工的核心区域,其效率和效果直接关系到整个生产线的运转和产品质量。
因此,对生产车间进行改善是企业提高生产效率、降低成本、提升产品质量的关键之一。
本文将以生产车间改善报告的范文(二)为例,从五个大点详细阐述生产车间改善的关键要点。
正文内容:一、人员管理的改善1.优化人员安排:通过合理的人员调配和合理分工,提高生产线的效率。
例如,对人员进行培训,使其具备多项工作技能,能够临时替代其他岗位上的员工。
2.建立有效的沟通机制:建立良好的内部沟通机制,保证信息流通畅,减少误解导致的生产问题。
二、设备管理的改善1.定期设备检修:制定设备检修计划,定期对设备进行检修,避免设备故障导致生产中断或延误。
2.引进智能设备:借助现代智能化技术,更新部分设备,提高生产效率和降低故障率。
三、工艺流程的改善1.进行合理的工艺设计:对产品的生产工艺进行细致分析,优化工艺流程,消除工艺瓶颈,提高生产效率。
2.引进新工艺和技术:及时关注新工艺和技术的发展,适时引进使用,提高产品的质量和竞争力。
四、物料管理的改善1.优化物料储存:对生产所需的物料进行分类管理,提供合理的储存空间,保证物料的定位准确、取用方便。
2.加强供应链管理:建立与供应商的长期合作关系,及时分享需求信息,确保及时供应所需物料。
五、质量管理的改善1.建立严格的质量控制体系:制定质量控制标准和流程,并设置质量检测岗位,确保产品符合质量要求。
2.定期开展质量培训:对生产车间的员工进行定期的质量培训,提高员工的质量意识和操作技能。
总结:生产车间的改善是企业提高生产效率和产品质量的关键之一。
通过优化人员管理、设备管理、工艺流程、物料管理和质量管理这五个大点,可以有效提升生产车间的效率和质量。
企业应该不断关注新技术和工艺的发展,及时进行改良和创新,与供应商和员工建立紧密合作关系,共同推动生产车间的改善。
只有保持持续的改进和严格的管理,才能提高企业的竞争力,实现长期发展目标。
生产线改进总结报告

生产线改进总结报告尊敬的领导和同事们:经过我们团队的不懈努力和合作,我很高兴地向大家汇报我们对生产线的改进工作。
在过去的几个月里,我们为了提高生产效率和产品质量,进行了一系列的改进和调整。
现在,我将向大家详细介绍我们的工作成果和总结报告。
首先,我们对生产线的工艺流程进行了全面的分析和评估。
通过对每个环节的细致观察和数据统计,我们找到了一些存在的问题和瓶颈。
比如,在原材料供应环节,我们发现了供应商交货延迟的情况;在生产工艺环节,我们发现了一些不必要的繁琐步骤和低效率操作;在产品检验环节,我们发现了一些漏检和误检的情况。
针对这些问题,我们制定了相应的改进计划和措施。
其次,我们进行了设备更新和技术改进。
我们引进了一批先进的生产设备,并对原有设备进行了调整和优化。
通过技术改进,我们提高了生产线的自动化程度和生产效率,减少了人为操作的环节,降低了生产成本和产品损耗。
同时,我们也对生产工艺进行了改进,优化了生产流程,简化了操作步骤,提高了产品质量和稳定性。
最后,我们加强了团队的协作和沟通。
在改进过程中,我们注重团队的协作和沟通,鼓励员工提出改进建议和意见。
我们组织了一些培训和交流活动,提高了员工的技术水平和生产意识,增强了团队的凝聚力和执行力。
通过团队的共同努力,我们成功地完成了生产线的改进工作,取得了显著的成效。
通过这次生产线改进,我们不仅提高了生产效率和产品质量,也为企业节约了成本和资源。
同时,我们也积累了宝贵的经验和教训,为今后的工作提供了有益的借鉴。
在未来的工作中,我们将继续保持改进的动力和精神,为企业的发展贡献更多的力量。
谢谢大家!。
涂布改善报告模板范文
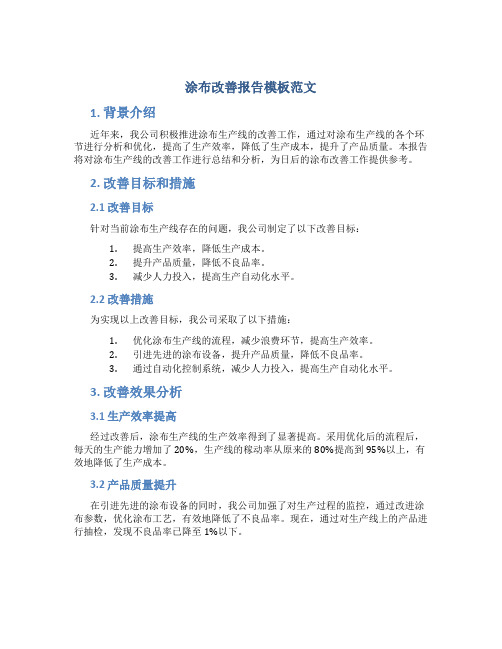
涂布改善报告模板范文1. 背景介绍近年来,我公司积极推进涂布生产线的改善工作,通过对涂布生产线的各个环节进行分析和优化,提高了生产效率,降低了生产成本,提升了产品质量。
本报告将对涂布生产线的改善工作进行总结和分析,为日后的涂布改善工作提供参考。
2. 改善目标和措施2.1 改善目标针对当前涂布生产线存在的问题,我公司制定了以下改善目标:1.提高生产效率,降低生产成本。
2.提升产品质量,降低不良品率。
3.减少人力投入,提高生产自动化水平。
2.2 改善措施为实现以上改善目标,我公司采取了以下措施:1.优化涂布生产线的流程,减少浪费环节,提高生产效率。
2.引进先进的涂布设备,提升产品质量,降低不良品率。
3.通过自动化控制系统,减少人力投入,提高生产自动化水平。
3. 改善效果分析3.1 生产效率提高经过改善后,涂布生产线的生产效率得到了显著提高。
采用优化后的流程后,每天的生产能力增加了20%,生产线的稼动率从原来的80%提高到95%以上,有效地降低了生产成本。
3.2 产品质量提升在引进先进的涂布设备的同时,我公司加强了对生产过程的监控,通过改进涂布参数,优化涂布工艺,有效地降低了不良品率。
现在,通过对生产线上的产品进行抽检,发现不良品率已降至1%以下。
3.3 人力投入减少通过自动化控制系统的引入,我公司减少了人力投入,并提高了生产的自动化水平。
现在,只需2个工人就能完成原来5个工人的工作量,有效地降低了人力成本。
4. 总结和展望通过对涂布生产线的改善工作,我公司实现了生产效率的提升、产品质量的提升和人力投入的减少。
虽然当前的改善工作已经取得了良好的效果,但我们深知改善工作是一个不断迭代的过程。
在未来的工作中,我们将会持续关注涂布生产线的工艺和技术动态,不断引进先进设备和技术,提高生产效率和产品质量,为公司的发展贡献更多力量。
生产线改进与升级报告

报告:生产线改进与升级报告一、引言为了提高生产效率、降低成本,并适应市场需求的变化,本报告将对某公司的生产线进行改进与升级的方案进行详细介绍和分析,以便实现生产线的优化和升级。
二、问题分析在对现有生产线进行调研和分析后,我们发现存在以下问题:1. 低效率:生产线的总体生产效率较低,生产周期长,无法满足市场需求的快速变化。
2. 资源浪费:生产过程中存在资源浪费现象,如物料浪费、能源浪费等,导致成本增加。
3. 工艺陈旧:部分生产工艺落后,无法适应新技术和新产品的生产需求。
4. 人工操作:部分工序仍然采用人工操作,存在劳动强度大、易出错等问题。
三、改进方案基于以上问题,我们提出以下改进方案:1. 自动化设备引入:引入自动化设备,替代部分人工操作,提高生产效率和品质稳定性。
通过自动化生产线,可以减少人工错误和劳动强度,提高生产效率。
2. 生产工艺优化:对生产工艺进行优化,采用更先进的工艺技术和设备,提高生产效率和产品质量。
同时,根据市场需求变化,调整工艺流程,减少生产周期。
3. 物料管理改进:引入物料管理系统,实现物料的准确控制和追踪,避免物料浪费和过度库存问题。
同时,通过供应链管理的优化,确保原材料的及时供应,降低库存成本。
4. 能源节约措施:采取节能措施,如使用高效节能设备、优化能源使用计划等,减少能源浪费,降低生产成本。
5. 数据分析与监控:建立数据分析和监控系统,对生产过程进行实时监测和分析,及时发现问题并进行调整,提高生产效率和品质控制。
6. 培训和人员管理:加强员工培训,提高员工技能水平,提升生产线的运行效率和品质稳定性。
同时,建立激励机制,激励员工积极参与生产线改进和升级。
四、实施计划为了顺利实施生产线改进与升级,我们提出以下实施计划:1. 确定改进目标和指标:明确改进的具体目标和衡量指标,以便评估改进效果。
2. 设计改进方案:根据现有问题和改进方向,设计详细的改进方案,包括引入自动化设备的选型、工艺优化的具体措施、物料管理系统的建立等。
生产效率报告生产线改善与效率提升
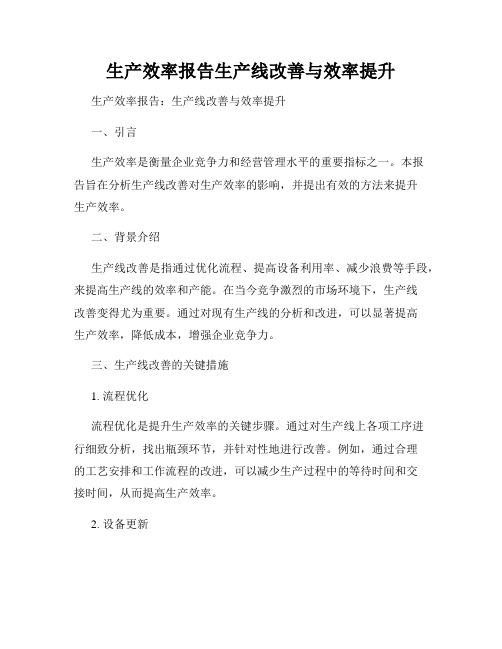
生产效率报告生产线改善与效率提升生产效率报告:生产线改善与效率提升一、引言生产效率是衡量企业竞争力和经营管理水平的重要指标之一。
本报告旨在分析生产线改善对生产效率的影响,并提出有效的方法来提升生产效率。
二、背景介绍生产线改善是指通过优化流程、提高设备利用率、减少浪费等手段,来提高生产线的效率和产能。
在当今竞争激烈的市场环境下,生产线改善变得尤为重要。
通过对现有生产线的分析和改进,可以显著提高生产效率,降低成本,增强企业竞争力。
三、生产线改善的关键措施1. 流程优化流程优化是提升生产效率的关键步骤。
通过对生产线上各项工序进行细致分析,找出瓶颈环节,并针对性地进行改善。
例如,通过合理的工艺安排和工作流程的改进,可以减少生产过程中的等待时间和交接时间,从而提高生产效率。
2. 设备更新现代化的设备可以在很大程度上提高生产线的效率。
企业应关注最新的技术和设备,及时进行设备更新和升级。
在购置新设备时,应考虑其可靠性、自动化程度和生产能力,以确保生产线的高效运行。
3. 培训和激励员工是生产线运行的核心,他们的技能水平和工作动力直接影响生产效率。
为了提高员工的工作效率,企业应定期进行培训和技能提升,使其适应新工艺和设备的要求。
此外,通过激励机制,如奖励制度和晋升机会,可以提高员工的积极性和动力,进一步推动生产效率的提升。
四、效率提升的实践案例以下是一个生产线改善和效率提升的实践案例,以便更具体地说明上述措施的有效性:ABC 公司是一家汽车零部件制造企业,他们拥有一条生产线用于生产发动机缸盖。
他们通过对生产线的分析和改进,成功提升了生产效率。
首先,他们进行了流程优化。
通过对生产线上每一个工序进行详细的时间测算,发现在过程中存在一定的等待和交接时间。
于是,他们重新安排工序,避免了不必要的等待和交接,缩短了生产周期,从而提高了生产效率。
其次,他们进行了设备更新。
ABC 公司购买了最新款的数控设备,取代了老旧的机械设备。
生产线改善报告

生产线改善报告1. 引言生产线是企业的核心部分,直接关系到生产效率和产品质量。
为了提高生产线的效率和改善工作环境,我们进行了一系列的改善措施和调整。
本报告将分析整个改善过程,并总结改善效果。
2. 改善目标在开始改善之前,我们明确了以下改善目标:1.提高生产线的生产效率,减少生产周期;2.降低生产成本,提高产品的竞争力;3.改善工作环境,提高员工的工作满意度。
3. 改善措施3.1 优化生产线布局通过重新规划生产线的布局,我们减少了生产线上的不必要移动和交通,缩短了产品在生产线上的流程时间。
我们还合理安排了设备和工作站的位置,提高了工作效率。
3.2 引入自动化设备为了提高生产效率,我们引入了一些自动化设备。
这些设备能够实现自动化生产、装配和包装,减少了人工操作的时间和难度,大大提高了生产效率。
3.3 建立质量控制机制为了提高产品的质量稳定性,我们建立了严格的质量控制机制。
在每个环节都设立了质量检查点,确保产品在每个环节都符合标准,减少次品率和返工率。
3.4 培训和激励员工为了提高员工的技能水平和工作动力,我们组织了定期的培训和激励活动。
通过培训,我们提高了员工的专业技能,使其更加熟悉生产线的操作流程。
而激励活动则提高了员工的工作积极性和团队合作意识。
4. 改善效果4.1 生产效率提升经过改善措施的实施,我们成功提升了生产线的生产效率。
生产周期缩短了30%,产品的生产量增加了20%。
这使得我们能够更快地响应市场需求,提前向客户交付产品。
4.2 成本降低通过引入自动化设备和建立质量控制机制,我们有效地降低了生产成本。
人工成本减少了20%,次品率和返工率也显著下降。
这使得我们能够降低产品的售价,提高市场竞争力。
4.3 工作环境改善通过改善生产线的布局和工作流程,我们改善了员工的工作环境。
员工的工作负担减轻了,工作效率和工作满意度也得到了提高。
工伤事故率减少了50%,员工流失率也有所降低。
5. 结论通过一系列的改善措施,我们成功地提高了生产线的效率和产品质量,降低了生产成本,改善了员工的工作环境。
生产线改善报告
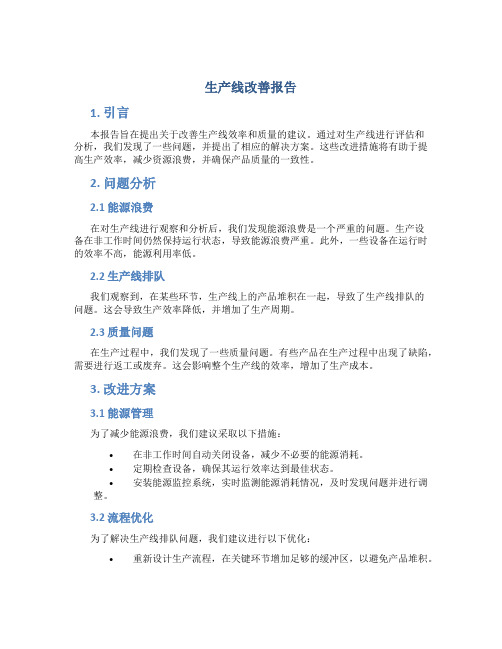
生产线改善报告1. 引言本报告旨在提出关于改善生产线效率和质量的建议。
通过对生产线进行评估和分析,我们发现了一些问题,并提出了相应的解决方案。
这些改进措施将有助于提高生产效率,减少资源浪费,并确保产品质量的一致性。
2. 问题分析2.1 能源浪费在对生产线进行观察和分析后,我们发现能源浪费是一个严重的问题。
生产设备在非工作时间仍然保持运行状态,导致能源浪费严重。
此外,一些设备在运行时的效率不高,能源利用率低。
2.2 生产线排队我们观察到,在某些环节,生产线上的产品堆积在一起,导致了生产线排队的问题。
这会导致生产效率降低,并增加了生产周期。
2.3 质量问题在生产过程中,我们发现了一些质量问题。
有些产品在生产过程中出现了缺陷,需要进行返工或废弃。
这会影响整个生产线的效率,增加了生产成本。
3. 改进方案3.1 能源管理为了减少能源浪费,我们建议采取以下措施:•在非工作时间自动关闭设备,减少不必要的能源消耗。
•定期检查设备,确保其运行效率达到最佳状态。
•安装能源监控系统,实时监测能源消耗情况,及时发现问题并进行调整。
3.2 流程优化为了解决生产线排队问题,我们建议进行以下优化:•重新设计生产流程,在关键环节增加足够的缓冲区,以避免产品堆积。
•提前计划生产任务,合理分配资源和时间,避免生产任务之间的冲突和阻塞。
•优化工作人员的分工和协作,确保生产线的平稳运行。
3.3 质量管理为了解决质量问题,我们建议采取以下措施:•引入质量管理系统,包括质量检查和质量控制措施,在每个生产环节严格把控质量。
•提供员工培训,加强他们对质量标准和要求的理解和意识。
•建立质量反馈机制,及时反馈产品质量问题并追踪处理过程,以避免类似问题再次发生。
4. 改进效果评估为了评估改进效果,我们将引入以下指标进行监测和评估:•生产效率:通过生产量和产能利用率评估生产效率的提升情况。
•资源利用率:通过能源和材料的消耗情况评估资源利用效率的改善情况。
- 1、下载文档前请自行甄别文档内容的完整性,平台不提供额外的编辑、内容补充、找答案等附加服务。
- 2、"仅部分预览"的文档,不可在线预览部分如存在完整性等问题,可反馈申请退款(可完整预览的文档不适用该条件!)。
- 3、如文档侵犯您的权益,请联系客服反馈,我们会尽快为您处理(人工客服工作时间:9:00-18:30)。
观测者 日期 : 单位作业
1. 组装 2. 固定 SCREW固定
第四组 2002.03.03
区
分
NO
作业说明
CABINET BOTTOM 合并,BEZEL组装,DOOR组装
3. 检查
AUDIO,VIDEO 检查 JUNPER 插入 LABEL 粘贴
业
主体作业
4. 连接 5. 粘贴
II. 原因分析
III. 作出改善案
IV. 成果总结
- 目标生产性向上 (最终) - 课后感想 2
1. LINE CAPA
生产Model
GCR-8521B
时间当生产系数
10
1天平均生产量
400
1天出勤时间
150HR
2. 人员现况
区分 班长 直接人员 间接人员
1 4 4 1 5 9 1
合计
组装 检查 修理
问题点
. CABINET的放置过远,作业者要把后 面的资材拉到作业者前. . 二个BOTTOM合并不易分开,容易表 面划伤
. 把合并后的半成品反转.
. 把BOTTOM和半成品SET合并 2. BEZEL装配 . 把BEZEL和半成品SET合并. . 为了固定SET拿取SCREW . 用4个SCREW 把半成品SET固定. . 为了固定SET拿取SCREW . 用4个SCREW 把半成品SET固定. . 把要检查的SET放在JIG上面. . CD-ROM的AUDIO特性检查. . 把DOOR装在TRAY上面. . 把检查完成的SET放在行板上 4.(2) AUDIO检查 . 把要检查的SET放在JIG上面. . CD-ROM的AUDIO特性检查. . 把DOOR装在TRAY上面. . 把检查完成的SET放在行板上
1 4 4
1 2 1 2 2 1 1 3 1 2 2 1 2
1 4
1 2
1 1 2
1 3
2
1 5
1 2
1 2
1 1 2 3
合计
13
13
13
13
13
13
13
13
13
13
13
13
13
13
13
13
13
13
13
13
9
W/S观测表
观测 单位作业 时间
对象Line :CD-ROM 1LINE 观测日: 2002.3.4 2 3 4 5 6 7 8 9 10 11 12 13 14
. BEZEL的包装箱过大,作业者要转 身拿取,造成视线转移,容易掉在地 上,发生不良 . SCREW 供应器故障造成等待,资 材包装不易分离. . 作业者固定SCREW 方向不稳定, 易造成SET表面划伤. . 作业没有按标准作业,造成 BOTTOW 翘起.
3.(1) SCREW 固定 3.(2) SCREW 固定
观测者: 第四组 15 3 2 3 1 1 1 2 1 1 1 2 16 17 3 2 2 1 2 1 1 3 1 18 1 1 3 19 3 2 2 1 1 1 1 2 20 1 2 2
1 2 2 3 1 1
组装 固定 检查 连接 粘贴 包装 材料分离 拿放SET 拿放工具 准备包装 装卸 无作业 余量
交换部品,工具,夹具等. 整理,清扫 部品供应指示 擦汗,上洗手间,喝水 调整呼吸,休息 闲聊,玩耍,等待
非作业
工厂余量
个人余量 疲劳余量 无作业
6
作业者
W/S观测统计表
分 组装 固定 检查 连接 粘贴 单位作业
Line 名
区
主体作业
观测者 日期 : 观测数 58 72 142 6 56 334 33 172 65 120 24
材料 分离 3.2%
件 数 单位 作业
等待
余量
98.7% 1.3%
累计 占有率
12
工序表LOSS分析表
No
1.
工序名
CASE 产出投入
现在作业方法
. 把CABINET 和MD ASSY合并.
要素作业 时间值
0.9 2.35 2.35 4.5 1.28 3.62 2.13 3.57 0.56 4.00 1.10 0.84 0.54 4.22 1.05 0.29
作
主作业
1.材料分离 2.拿SET 放SET 3.拿放工具 4.准备包装 5.包装
从箱子拿部品,去掉塑料 拿放SET 拿放工具为了固定和检查 为了包装打开BOX. SET 包装,PE-BAG包装
附属作业
6.装卸
将部品放在PALLET
准备作业 作业余量
换机型 准备作业 作业指示,记录,会议 生理需求 作业中伸懒腰 作业等待
观测者: 第四组 15 16 17 18 19 20
1
组装 固定 检查 连接 粘贴 包装 材料分离 拿放SET 拿放工具 准备包装 装卸 无作业 余量
1 1 1 1 1 1 1
1 2 3 1 1 1 1
1 1 3 1 1 1 1
2 1 3 1 1 2 1
1 3 1 1 1 2 1 1
1 1 1 1
2 1 2 1 1 1
97.8% 100%
100% 90
组装5.6% 固定6.9%
80
70
等待 23.4% 非驱动 23.7%
包装11.5%
检查 13.7%
60 50 40
附属作业 39.7%
驱动工时 76.3%
主体作业 32.5%
准备作 业4.4%
连接0.6%
30 20 10%
粘贴5.4% 准备包装 4.4%
拿取工具 6.3% 拿取SET 16.5%
5
• 根据BUYER别, 设置JUMPER模式 • • •
6
程序确认 访问时间测试 传输率测试
• 顶壳与底 •BEZEL 装配 盘装配
外观检查
贴 标 签
包 装 袋
放入 SET, 内藏 物
放说明书, 封箱,装 卸
间接人员:班长(1人)
修理(1人) 7
8
9
10
• S/LABEL 粘贴 • 按规定进行包装 • 按指定的卡板摆放
9.
PE-BAG包装
. 确认CD-ROM内部是否有异常物品 . 把CD-ROM装入PE-BAG内部包装
. PE-BAG不易分开,
10. CD-ROM插入PACKING
. 把使用包装的BOX放在台面上
问题说明
平均
最少 最大
使用部品
4
GCR-8521 LINE 作业流程安排如下:
SCREW供应器 cabinet bottom
AUDIO检查工程
BEZEL DOOR DOOR DOOR
修 理 位
JUMP
VIDEO检查工程
1
2
3
•SCREW 固定
4
• DOOR 装配 • AUDIO 波形输出检查 • 高频波输出检查
1 1 1
1 1 1 1 1
1 1 2
1 2
1 1
2
1 1 1
1
2 1
1
1 1
1
1
1
1
1
1
1
1
2
1
1 1
1
1
1 2 1 8 1 4 4 1 4 4 4 6 3 1 3
3
2
3
3
6
2
4
3
1
2
合计
8
W/S观测表
观测 单位作业 时间
对象Line : CD-ROM 1LINE 观测日: 2002.3.4 2 1 1 4 1 2 1 1 1 3 2 1 5 1 2 4 1 4 5 1 2 3 1 1 1 1 2 1 2 6 1 2 3 1 7 1 2 3 1 1 1 2 8 2 1 4 9 4 2 2 1 1 1 1 10 1 2 2 1 11 1 1 1 1 1 1 1 3 2 1 1 2 12 3 2 4 1 13 2 1 3 1 1 1 14 1 2 2 1
1 2 3
2 2 3 1
1 2 3 1 1
1
1 2
1 1 3
2 2 3 1
1 2 1 1 1 1 1
2 2 2 1 1
3 1 1
2 1 3 1
1 1 4 1 1 3
3
4 1
1 1
1
1
1
1 1
1 1
1 2 1 1 1 1
2 1 2 1 1 1 1
2 1 1
1
1
1 1 1 2
1
1
3
1 1
1
1
1
5
3
3
2
2
1 2 1 1 1 1 1
1 2
1 2
1 2
1 2
1 2
1
2
2
2
2 1 2 2 1 2 1 1 2
3
2 1 1 1 1 1 1
1
1 1
1 1 1 5 3
3
4
4
3
3
2
3
1
1
2
3
1
6
2
合计
13
13
13
13
13
13
13
13
13
13
13
13
13
13
13
13
13
13
13
13
11
W/S 观测定理表
非移动要素 LOSS PARETO
比率(%) 5.6 6.9 13.7 0.6 5.4 32.2 3.2 16.5 6.3 11.5 2.3
备
注
主作业