转体炉工艺
国内外转底炉的发展趋势及我国发展转底炉技术的建议

一、国内外转底炉技术的发展过程简介
1、转底炉直接还原工艺简介
转底炉炼铁工艺是非高炉炼铁工艺的一种,从1978年加拿大国际镍集团 (Inco,Ltd)建成第一座转底炉以来,已有近30年的历史,它从美国发源ห้องสมุดไป่ตู้先在日 本推广、后在中国得到发展。
转底炉法以其原料适应性强和操作工艺的灵活性等优点,引起冶金界的高度重视。 但由于原料加工方法条件和对产品质量要求的不同,转底炉直接还原炼铁分为 Inmetco法、DRYIRON法, FASTMET法和ITKM3等不同工艺路线。
国内外转底炉的发展趋势及 我国发展转底炉技术的建议
周渝生 齐渊洪 严定鎏 洪益成
钢铁研究总院先进钢铁流程及材料国家重点实验室 钢研晟华工程技术有限公司 20141106
目录
一、国内外转底炉技术的发展过程简介 二、国内外转底炉技术的发展趋势 三、我国发展转底炉技术的背景 四、对我国发展转底炉技术的建议
项目
单位
原料 铁精矿粉 还原煤 皂土 有机粘结剂 小计 能源 电 天然气 氮气 水 小计 其他 消耗品 维修与备件
kg kg kg kg
kwh m3(STP) m3(STP) t
美元 美元
消耗量 单位
1335 410 5 5
65 60 10 0.30
国内外转底炉的发展趋势及我国发展转底炉技术的建议 PPT课件

2020/3Βιβλιοθήκη 317一、国内外转底炉技术的发展过程简介
2、国内外转底炉直接还原工艺简介
2020/3/31
8
一、国内外转底炉技术的发展过程简介
2、国内外转底炉直接还原工艺简介
• Inmetco流程的最突出特点是使用冷固结含碳球团。可使用 矿粉或冶金废料作为含铁原料,焦粉或煤作为内配还原剂。 将原燃料混匀磨细,制作成冷固结球团,然后将冷固结球团 连续加入转体炉,在炉盘上均匀布上一层厚度约为球团矿直 径3倍的炉料。
2020/3/31
2
一、国内外转底炉技术的发展过程简介
1、转底炉直接还原工艺简介
转底炉炼铁工艺是非高炉炼铁工艺的一种,从1978年加拿大国际镍集团 (Inco,Ltd)建成第一座转底炉以来,已有近30年的历史,它从美国发源、先在日 本推广、后在中国得到发展。
转底炉法以其原料适应性强和操作工艺的灵活性等优点,引起冶金界的高度重视。 但由于原料加工方法条件和对产品质量要求的不同,转底炉直接还原炼铁分为 Inmetco法、DRYIRON法, FASTMET法和ITKM3等不同工艺路线。
属化球团经过冷却区后被排出炉外冷却,部分再氧化金属化率降低一些。煤气燃烧
及反应生成的烟气沿着与炉料转动相反的方向流动,最后流入废气净化处理及余热 回收系统。
装料 区
900~1100 ℃
预热区
烟气流动方向 1200~1400℃
还原区
1100~900℃
烧嘴
冷却区
排料区
转底炉炉底转动方向
2020/3/31
2020/3/31
9
一、国内外转底炉技术的发展过程简介
⑵. 干铁法
GLOBA公司(原MR&E公司)在1960年是米德兰-罗斯的快速加热工艺的技 术开发部门,1985年成为独立公司。曾经为美国Ameristeel公司的电炉粉 尘处理系统以及美国Rouge Steel公司综合钢铁厂的粉尘和污泥处理系统提 供DRYIRON法的相关设备,具备丰富的应用实绩。GLOBA公司开发的干铁法 有两项专利技术:用废糖浆作为粘结剂,利用氧化铁粉与碳粉混合物成型 的干压块方式对辊压球机压成球团后直接装入转底炉,取消了球团的烘干 程序;采用特殊的震动传送装置的炉料装入方法。可以得到金属化率大于 90%的DRI。 是一种较理想的煤基直接还原工艺。 该工艺过程中在转底炉 内的高温作用与短暂的停留时间(约10min),其操作具有巨大的灵活性, 而且设备的操作控制非常容易。考虑到上述炼铁厂粉尘和污泥处理以及还 原铁生产的需要,新日铁钢铁事业部于1999年从美国MR&E公司引进转底炉 DRYIRON法,并且争取到代理推销资格。 这是日本FASTMET法发展的基础。
转底炉工艺关键技术分析

转底炉工艺关键技术分析转底炉还原一般包括原料混合、球团制备、直接还原、直接还原铁进一步处理等主要环节,目前转底炉直接还原技术的关键点如下。
1.符合生产的高强度球团的制备转底炉一般以冷固结含碳球团为处理对象,由于处理对象广泛,原料的粒度、强度、亲水性有很大差异,因此在球团的制备过程中对粘结剂的品种与使用量上也有不同的要求。
冶金中常用的球团制备方式有两种,圆盘造球和压球。
圆盘造球在设备成本与生产技术上相对比较成熟,但是生产的球团含水量高,后续工艺烘干要消耗很大的能量,一般使用膨润土做粘结剂,直接还原后膨润土成分大部分留在直接还原球团中,降低产品品质。
冷固结成型的方式设备造价与维护成本高,使用粘结剂量较多,粘结剂消耗占成本很大比例,但制得球团可以直接入炉,使用有机粘结剂燃烧过程中可以供应部分热量,且燃烧产物少,不会影响到直接还原后产品品质。
2.转底炉布料、出料方式以年处理力量20万吨转底炉为例,转底炉中径有21m,炉床内外半径差有5m,转底炉工作时内外环的线速度差值在0.5~1m/min。
将球团匀称散布在这样连续移动且各点位移速度并不相同的料台上是布料技术的难点,假如不能实现匀称布料必定使物料在炉膛内受热程度不一,从而影响物料的还原品质,导致生产率低下。
同时,假如布料装置安装的位置假如过高,布料过程中球团自由落下会产生肯定的冲击力,过大的冲击一方面会使球团的破损率增加,影响产品质量,长期对炉床进行冲击造成炉床的使用寿命降低。
假如安装位置较低位于炉膛口四周,工作环境的温度较高,布料装置在高温下稳定运行对装置有很高的要求。
转底炉的出料装置处理物料的方式与布料类似,要求更高的使用温度环境和连续使用的较强耐磨性能。
3.处理对象的冶金性能不同的处理对象铁氧化物以不同的结合形式存在,品位、杂质成分、还原性等影响因素对直接还原都有很大的影响。
在确定转底炉处理对象后,需要对原料的冶金性能进行具体的讨论,做好充分的技术预备,确定转底炉工艺适合用于处理,能够获得预期直接还原铁、除尘灰与熔炼渣产品后方能进行转底炉的建设。
旋转式燃气烧烤炉设备工艺原理

旋转式燃气烧烤炉设备工艺原理旋转式燃气烧烤炉是一种常用于餐饮行业的设备,它采用燃气作为热源,在旋转的烤盘上将食物进行烤烤,烤制出来的食物口感香味都十分美妙。
本文将详细介绍旋转式燃气烧烤炉的工艺原理,包括设备的构造、加热方式、温控系统等方面。
构造旋转式燃气烧烤炉主要由以下几部分构成:烤盘、转动装置、热源、外壳。
其中,烤盘是烤制食物的主要部件,一般采用不锈钢材质制作,其表面通常有弧形或V形的条纹,以增加食物的接触面积。
转动装置通常采用电机驱动,能够使烤盘沿着水平方向匀速旋转。
热源一般采用燃气,通过管道输送到烤盘下面的燃烧口处完成燃烧过程,产生高温热量用于烤制食物。
外壳是烤炉的保护壳,一般采用不锈钢或者铁皮制作,其外形美观、耐腐蚀、易清洁等特点得到了广泛应用。
加热方式旋转式燃气烧烤炉采用燃气作为热源,燃气在经过调节器的控制后,通过管道输送到烤盘下方的燃烧口处,产生高温火焰,使烤盘上的食物得到各个方向均匀的加热。
由于旋转式燃气烧烤炉的烤盘可以上下调节,因此对不同的食物进行加热时,可以根据需要调整烤盘的高度,以调节不同功率的燃气火焰强度,从而达到最佳的加热效果。
温控系统旋转式燃气烧烤炉采用自动控制技术,配有精确的温控系统,能自动调整火焰大小,控制烤盘上的食物温度,保证烤制出来的食物味道香浓、口感鲜美、营养丰富。
通常温度控制系统会根据烤盘上食物的温度、烤盘的旋转速度、环境温度等因素,进行实时监控,并自动调整燃气火焰大小、烤盘的旋转速度、烤盘高度等参数,以达到最佳的烹饪效果。
工作原理旋转式燃气烧烤炉的工作原理十分简单,燃气在调节阀的调控下,进入烤盘下方的燃烧口处,产生高温火焰,并通过烤盘的旋转,使得食物得到均匀的加热。
同时,烤盘高度可以进行自由的调节,根据不同的食物需要,以达到最佳的烤制效果。
在烤制过程中,温控系统会自动监控烤盘上食物的温度、烤盘的旋转速度、环境温度等因素,自动调整燃气火焰大小、烤盘的旋转速度、烤盘高度等参数,以达到最佳的烹饪效果。
变换炉制造工艺流程控制技术及应用

后的筒体的圆度偏差、 直线度偏差、 棱角度等各项质量指
标符 合要 求 。
— —
钢 板表面 :沿垂 直于钢板 主轴线 的标称 中心距 为 7 5 mm的平行线连续扫查,扫描线应从钢板 中心或某一个
顶 角 开 始 量 起 , 并在 扫 查 面 上 离 钢 板 的所 有 边 缘 不 到 5 0 mm 处补 加一条 扫描 线 。 钢 板边 缘: 在 离钢 板切 口边 缘宽度 为 5 0 m m 的整个 区 域 内进 行 1 0 0 % 扫查 。
根据 封 头的展开 尺寸 下料 ,采用定 长 、 定宽双 定
尺板,减小封头的焊接接头。坯料割圆后 , 应对周边影响
封 头成 形 质量 的 缺陷 进行 修磨 消 除 。
— —
封 头 的成形 采用 热冲压 ,坯料 加热 温度 l 0 0 0 ~
¥ 3 2 1 6 8 锻件的制造、 检验、 验收应符合NB / T 4 7 0 1 0 —
制采用 温卷 , 卷制 前 , 用卷 板机 的计算机 控制 系统计 算 出 每 次最佳 下压 量 ,并在卷 制过程 中用样 板检 测 。 保证 卷制
( 1 ) 逐 张钢 板均 应按 J B / T 4 7 3 0 . 3 2 0 0 5的要求进 行超 声 波检 测 ,验 收标 准为 I 级。 ( 2 ) 钢板 的超 声 波检 测 要求 :
弯 ,并制作 弦长不 小于 5 0 0 mm 的样 板检测 ,压 头预弯 的
钢 板应 采用 电炉冶 炼 工艺 生产 的细 晶粒钢 。
R必须符合样板要求。
— —
( 5 ) 钢板进行冷弯试验 R=l 8 0 。检测次数 : 每炉一次。
— —
为了保证材料的力学性能和使用状态 ,筒体卷
转体炉工艺
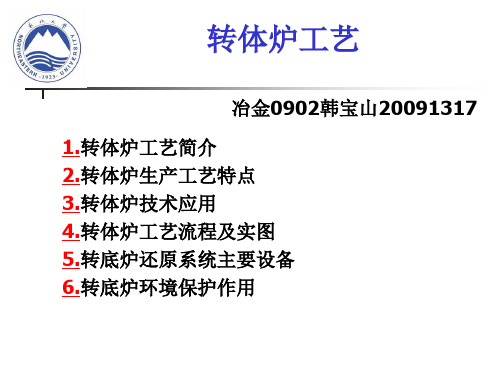
1250下℃加热25分钟,金属化率88%
转底炉应用之三
将V、Ti磁铁矿中的铁精矿、钛精矿制成含炭球团,经转底炉预 还原,再用电炉或矿热炉进行终还原和熔分。
2.转体炉生产工艺特点
1)以煤粉作为还原剂, 仅用少量煤气, 对煤的质量要 求也没有回转窑法那么严格, 故有利于广泛应用。 2)主要设备为环形转底炉,与回转窑相比,该工艺设备 较简单、投资省、能耗较低。 3) 对炉料的强度要求不高。因为料层很薄炉料既不 受压且随炉底一起转动,炉料与炉底之间没有相对运动,可 用含碳生球团.(10~20min) ,操作容易。 4)转底炉工艺可直接使用含铁废粉料(或粉矿)和 粉煤, 在矿石和能源上具有很好的适应性和经济性。金属 化率可达80%以上。
6.转底炉环境保护作用
1、转底炉使用净化的煤气作燃料,并且炉料在炉膛内无相对运动,排出的废 烟气中含尘为20_50 mg/m3,大大低于国家规定的标准:一类100 mg/m3; 二类150 mg/m3。 2、生产过程无污水和固体废弃物排放,工艺工程产生的粉尘可以全部重新利 用。 3、转底炉工艺是含碳球团的直接还原,其中煤中的硫只有极少量的通过烟气 排出,大部分固结在金属化球团内。 4、如果转底炉生产金属化球团加入高炉,代替烧结矿和球团矿,可以大大降 SO2的排放,并以普通煤代替资源紧缺的焦炭,大大降低了传统高炉冶炼对 环境的危害。 5、转底炉直接还原、熔融还原工艺是国家明确鼓励支持的冶金新技术,并且 对于处理钢铁厂尘泥具有较大的优势,是发展循环经济的可行的手段。 6、转底炉工艺需要考虑的环保措施主要是控制粉尘排放,如原料处理、转运、 转底炉出料过程产生的灰尘。
高效节能的燃煤型旋转炉设备工艺原理
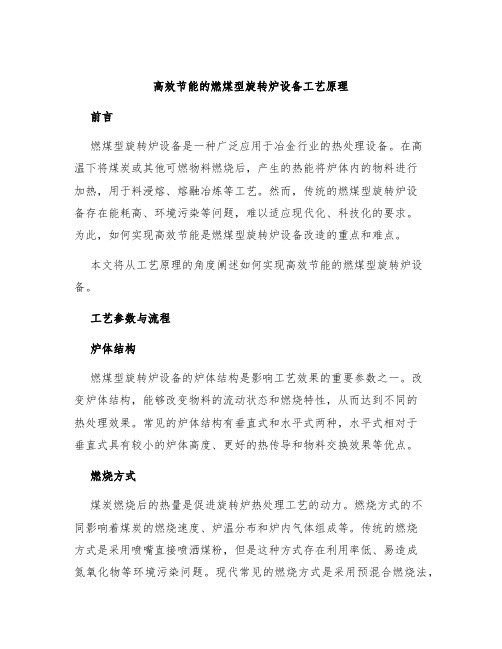
高效节能的燃煤型旋转炉设备工艺原理前言燃煤型旋转炉设备是一种广泛应用于冶金行业的热处理设备。
在高温下将煤炭或其他可燃物料燃烧后,产生的热能将炉体内的物料进行加热,用于料浸熔、熔融冶炼等工艺。
然而,传统的燃煤型旋转炉设备存在能耗高、环境污染等问题,难以适应现代化、科技化的要求。
为此,如何实现高效节能是燃煤型旋转炉设备改造的重点和难点。
本文将从工艺原理的角度阐述如何实现高效节能的燃煤型旋转炉设备。
工艺参数与流程炉体结构燃煤型旋转炉设备的炉体结构是影响工艺效果的重要参数之一。
改变炉体结构,能够改变物料的流动状态和燃烧特性,从而达到不同的热处理效果。
常见的炉体结构有垂直式和水平式两种,水平式相对于垂直式具有较小的炉体高度、更好的热传导和物料交换效果等优点。
燃烧方式煤炭燃烧后的热量是促进旋转炉热处理工艺的动力。
燃烧方式的不同影响着煤炭的燃烧速度、炉温分布和炉内气体组成等。
传统的燃烧方式是采用喷嘴直接喷洒煤粉,但是这种方式存在利用率低、易造成氮氧化物等环境污染问题。
现代常见的燃烧方式是采用预混合燃烧法,即将煤粉、空气、氧气等预先混合后,再通过喷嘴与炉体内的物料接触,充分利用煤炭的热能,提高燃烧效率,减少环境污染。
物料运动轨迹燃煤型旋转炉设备中物料的运动轨迹对热处理效果有着重要影响。
本质上物料是在高温、高氧化环境下加热融化的过程,通过改变物料的运动状态来改变物料的加热速度、热传递、气体分布等参数,从而控制炉体内的温度分布、反应速率等。
现代燃煤型旋转炉设备中一般采用倾斜旋转方式,通过调整物料的滑动、倾斜、旋转等方式,使物料得到更加均匀、充分的加热和混合。
设备改造在上述工艺流程中,实现高效节能的燃煤型旋转炉设备需要特别设计和改造。
以下是一些关键的改造方法:热量回收传统的燃煤型旋转炉设备中,大量的热量会在炉体内部逃逸,造成了极大的能量浪费。
而高效节能的燃煤型旋转炉设备中,则需要通过热量回收的方式,将炉体内部升温的废气中所包含的热量回收起来,用于物料的预热或其他加热工艺。
旋转窑工艺流程

旋转窑工艺流程旋转窑是一种常用的工业设备,广泛应用于水泥、化工、冶金等行业中。
旋转窑工艺流程是指将原料在连续旋转的窑筒中进行加热和烧结,最终产生所需的成品。
首先,原料准备。
在旋转窑工艺中,原料的制备非常重要。
通常使用的原料包括石灰石、黏土、铁矿石等。
这些原料需要经过破碎、磨碎、混合等步骤,以便得到合适的颗粒度和成分。
接下来是燃料准备。
为了使旋转窑内的温度达到所需的烧结温度,需要添加燃料。
常用的燃料是煤粉、天然气、重油等。
燃料要经过破碎、磨碎等处理,以便在燃烧过程中能够充分释放热量。
然后是设备调试和操作。
在开始生产之前,需要对旋转窑进行调试和检查,确保设备正常运行。
调试包括调整的转速、进料量、出料筒的位置等。
操作工人需要熟悉设备的使用方法和安全注意事项,以确保生产的安全和稳定。
进入正式生产阶段后,首先是进料和热风供给。
原料经过称重和检测后,从进料端进入旋转窑。
同时,燃烧设备产生的热风也通过热风管道进入旋转窑,使原料得到加热。
然后是烧结和冷却。
在旋转窑内,原料经过加热和烧结的过程,逐渐形成球状颗粒。
此过程中,原料中的水分和有机物被挥发和分解,形成新的化合物。
烧结后的成品通过旋转窑的出料端排出。
最后是尾气处理。
燃烧产生的尾气含有大量的有害气体和粉尘,需要经过处理后排放。
通常采用的尾气处理方法有干式除尘和湿式除尘等。
干式除尘通过过滤和静电除尘等方法去除尘埃,湿式除尘则是利用喷雾器将尾气中的颗粒捕捉下来。
总结起来,旋转窑工艺流程包括原料准备、燃料准备、设备调试和操作、进料和热风供给、烧结和冷却、尾气处理等步骤。
通过这些步骤,原料经过加热、烧结和冷却,最终形成需要的成品。
旋转窑工艺流程在各个行业中得到广泛应用,为工业生产提供了必要的设备和技术支持。
- 1、下载文档前请自行甄别文档内容的完整性,平台不提供额外的编辑、内容补充、找答案等附加服务。
- 2、"仅部分预览"的文档,不可在线预览部分如存在完整性等问题,可反馈申请退款(可完整预览的文档不适用该条件!)。
- 3、如文档侵犯您的权益,请联系客服反馈,我们会尽快为您处理(人工客服工作时间:9:00-18:30)。
冶金0902韩宝山20091317
1.转体炉工艺简介 2.转体炉生产工艺特点 3.转体炉技术应用 4.转体炉工艺流程及实图 5.转底炉还原系统主要设备 6.转底炉环境保护作用
1.转体炉工艺简介
转底炉熔融还原技术是将配料、混料、制球
和干燥后的含碳球团加入到具有环形炉膛和可转
动的炉底的转底炉中,在1350 ℃ 左右炉膛温度
CaO %
16.80
23.30
转底炉应用之三
将V、Ti磁铁矿中的铁精矿、钛精矿制成含炭球团,经转底炉预 还原,再用电炉或矿热炉进行终还原和熔分。
可将TiO2在炉渣中富余 V进入铁相→再提V 铁用于炼钢
实现Fe、V、Ti综合分离和利用
4.转体炉工艺流程及实图
5.转底炉还原系统主要设备
1.转底炉 作用:转底炉生产工艺核心设备,用于金属化球团的还原生成 主要构成:驱动部、炉床、上下轨道梁、燃烧系统 2.振动布料机 作用:混合生球布料,将生球均匀的布置在转底炉炉床上 主要构成:振源(电机、柔性联轴器、激振器)、箱体、弹簧、导料板 3.螺旋排料机 作用:成品金属化球团矿的热态排料 主要构成:电机减速机、传动链系统、前后轴承座、主轴装配(含螺旋
Hale Waihona Puke 6.转底炉环境保护作用1、转底炉使用净化的煤气作燃料,并且炉料在炉膛内无相对运动,排出的废 烟气中含尘为20_50 mg/m3,大大低于国家规定的标准:一类100 mg/m3; 二类150 mg/m3。
2、生产过程无污水和固体废弃物排放,工艺工程产生的粉尘可以全部重新利 用。
3、转底炉工艺是含碳球团的直接还原,其中煤中的硫只有极少量的通过烟气 排出,大部分固结在金属化球团内。
求也没有回转窑法那么严格, 故有利于广泛应用。
2)主要设备为环形转底炉,与回转窑相比,该工艺设备
较简单、投资省、能耗较低。
3) 对炉料的强度要求不高。因为料层很薄炉料既不
受压且随炉底一起转动,炉料与炉底之间没有相对运动,可
用含碳生球团.(10~20min) ,操作容易。
4)转底炉工艺可直接使用含铁废粉料(或粉矿)和
优质海绵铁
熔融还原的预还原产品
名称
TFe
MFe
金属 化率
SO2
C
%
%
%
%
%
铁矿 69.50
2.0
生球 54.79
2.29 18.20
产品
91.46 83.32
91.1 0
3.83
1.64
名称
铁矿 生球 产品
TFe
MFe
金属 化率
SO2
C
%
%
%
%
%
64.2
6.0
50.07
6.54 16.62
77.90 68.21 87.56 10.18 1.85
粉煤, 在矿石和能源上具有很好的适应性和经济性。金属
化率可达80%以上。
3.转体炉技术应用
第一类:铁精矿的煤基直接还原 第二类:钢铁企业的含锌粉尘的回收利用 第三类:冶炼钒钛磁铁矿
转底炉应用之一
用优质铁矿石和低灰分煤得到含铁品位高、金属化率高的海绵 铁,可供电炉用
用一般铁矿石和煤得到产品需经过终还原、融化,使渣铁分 离,得到生铁。
片)、水冷系统 4.筒式冷却机 作用:热态成品球的冷却 构成:驱动部、筒体、托辊、齿轮
转底炉还原系统主要设备
5.链斗机 作用:热态成品球的大倾角提升 构成:驱动部、链条、链斗 6.还原风机 作用:动力抽风系统 构成:电机、转子联轴器、轴承座、机壳、风门、联轴器 7.带式输送机(拖式皮带秤、大倾角输送机等) 8.螺旋输送机 9.刮板输灰机 10.水封拉链机 11.斗式提升机(斗提机、链斗机)
煤炭灰分4%
煤炭灰分12.5%
转底炉应用之二
钢铁厂粉尘颗粒纤细,容易还原,产品金属化率较高 高效脱除钢铁厂粉尘中的Zn,并且可以将Zn回收
名称
TFe
MFe
Zn
SiO2
%
%
%
%
钢铁厂粉尘 45.80
0.89
3.53
金属化球团 60.10
52.83
0.01
8.00
1250下℃加热25分钟,金属化率88%
4、如果转底炉生产金属化球团加入高炉,代替烧结矿和球团矿,可以大大降 SO2的排放,并以普通煤代替资源紧缺的焦炭,大大降低了传统高炉冶炼对 环境的危害。
5、转底炉直接还原、熔融还原工艺是国家明确鼓励支持的冶金新技术,并且 对于处理钢铁厂尘泥具有较大的优势,是发展循环经济的可行的手段。
6、转底炉工艺需要考虑的环保措施主要是控制粉尘排放,如原料处理、转运、 转底炉出料过程产生的灰尘。
下,在随着炉底旋转一周的过程中,铁矿被碳还
原。当铁矿粉含铁品味在69%以上,采用转底
炉直接还原工艺,产品为金属化球团供电炉使用;
当铁矿粉含铁品味低于62%时,采用转底炉—
—造气炉的熔融还原铁工艺,产品为铁水供炼钢
使用。金属化球团可作为高炉原料。通常金属化
率可达80%以上。
2.转体炉生产工艺特点
1)以煤粉作为还原剂, 仅用少量煤气, 对煤的质量要