机械加工工艺过程概述
机械加工工艺流程
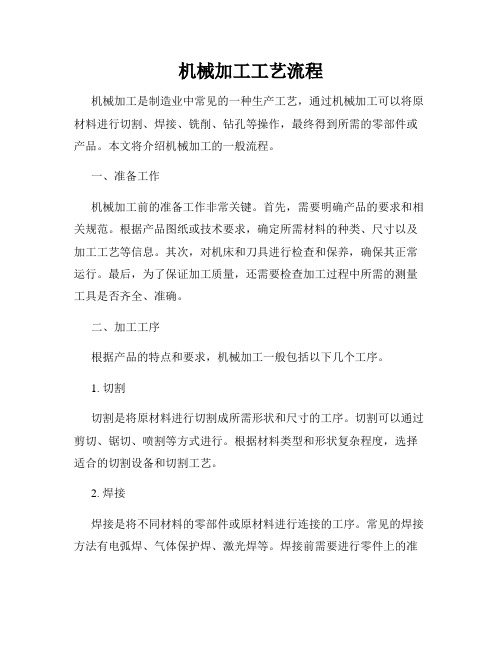
机械加工工艺流程机械加工是制造业中常见的一种生产工艺,通过机械加工可以将原材料进行切割、焊接、铣削、钻孔等操作,最终得到所需的零部件或产品。
本文将介绍机械加工的一般流程。
一、准备工作机械加工前的准备工作非常关键。
首先,需要明确产品的要求和相关规范。
根据产品图纸或技术要求,确定所需材料的种类、尺寸以及加工工艺等信息。
其次,对机床和刀具进行检查和保养,确保其正常运行。
最后,为了保证加工质量,还需要检查加工过程中所需的测量工具是否齐全、准确。
二、加工工序根据产品的特点和要求,机械加工一般包括以下几个工序。
1. 切割切割是将原材料进行切割成所需形状和尺寸的工序。
切割可以通过剪切、锯切、喷割等方式进行。
根据材料类型和形状复杂程度,选择适合的切割设备和切割工艺。
2. 焊接焊接是将不同材料的零部件或原材料进行连接的工序。
常见的焊接方法有电弧焊、气体保护焊、激光焊等。
焊接前需要进行零件上的准备工作,如除锈、清洁等。
根据材料的性质和要求选择合适的焊接设备和焊接工艺。
3. 铣削铣削是将工件固定在机床上,利用铣刀进行切削加工的工序。
铣削广泛应用于零部件的加工中,可以实现平面、曲面、齿轮等形状的加工。
铣削前需要确定切削条件、选择合适的刀具和夹具,保证加工精度和表面质量。
4. 钻孔钻孔是将工件表面钻出孔洞的工序。
钻孔可以采用手动钻床、立式钻床、卧式钻床等设备进行。
在进行钻孔前,需要选择合适的钻头和冷却液,根据钻孔深度和直径进行冷却和润滑。
5. 攻丝攻丝是在孔洞内加工螺纹的工序。
通常使用攻丝机进行,可以实现内螺纹的加工。
在攻丝前,需要根据螺纹类型选择合适的刀具和设定攻丝参数,保证螺纹的质量和尺寸符合要求。
三、加工检验机械加工完成后,需要进行加工成果的检验。
检验的目的是验证加工精度和加工质量是否满足要求。
常用的检验方法包括尺寸测量、功能测试等。
根据产品的要求,可以使用不同的检测设备和手段进行检验。
四、加工后处理机械加工后,还需进行一些后处理工作,以便保证零件的质量和使用效果。
机械加工工艺过程
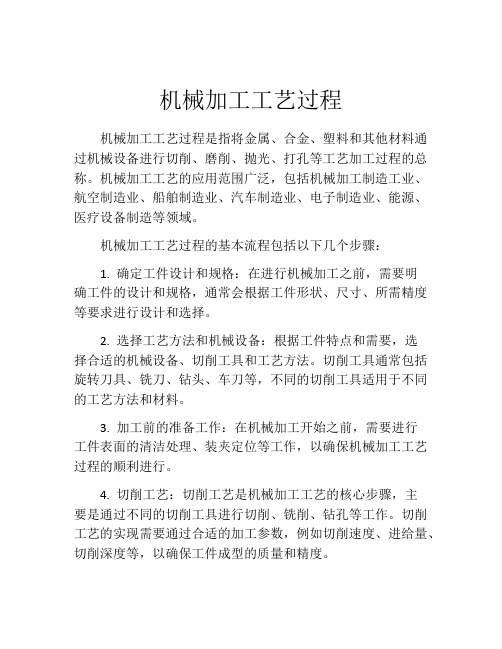
机械加工工艺过程机械加工工艺过程是指将金属、合金、塑料和其他材料通过机械设备进行切削、磨削、抛光、打孔等工艺加工过程的总称。
机械加工工艺的应用范围广泛,包括机械加工制造工业、航空制造业、船舶制造业、汽车制造业、电子制造业、能源、医疗设备制造等领域。
机械加工工艺过程的基本流程包括以下几个步骤:1. 确定工件设计和规格:在进行机械加工之前,需要明确工件的设计和规格,通常会根据工件形状、尺寸、所需精度等要求进行设计和选择。
2. 选择工艺方法和机械设备:根据工件特点和需要,选择合适的机械设备、切削工具和工艺方法。
切削工具通常包括旋转刀具、铣刀、钻头、车刀等,不同的切削工具适用于不同的工艺方法和材料。
3. 加工前的准备工作:在机械加工开始之前,需要进行工件表面的清洁处理、装夹定位等工作,以确保机械加工工艺过程的顺利进行。
4. 切削工艺:切削工艺是机械加工工艺的核心步骤,主要是通过不同的切削工具进行切削、铣削、钻孔等工作。
切削工艺的实现需要通过合适的加工参数,例如切削速度、进给量、切削深度等,以确保工件成型的质量和精度。
5. 精密加工工艺:对于一些需要高精度的工件,还需要进行精密加工工艺,例如磨削、打磨、抛光等工艺。
精密加工工艺可以进一步改善工件的表面质量和尺寸精度。
6. 检验和质量控制:在机械加工工艺过程结束之后,需要进行工件的检验和质量控制,确保工件可以符合设计要求和质量要求。
机械加工工艺过程的优势在于可以对各种材料进行高效、精确和灵活的加工。
通过使用不同的切削工具和工艺方法,可以实现对不同形状和尺寸的工件进行加工。
机械加工工艺过程还可以进行批量加工,提高生产效率和降低成本。
但是,机械加工工艺过程也存在一些缺点,例如机械加工过程通常会产生噪音、粉尘和切屑等废弃物,对环境造成污染。
另外,机械加工过程还需要较高的人员技术水平和设备投资成本。
随着科技不断进步,机械加工工艺过程也在不断演变。
例如,进一步的自动化和数字化技术已经被应用到机械加工工艺过程中,实现了更高效、更精确的加工。
机械加工工艺过程与工艺规程
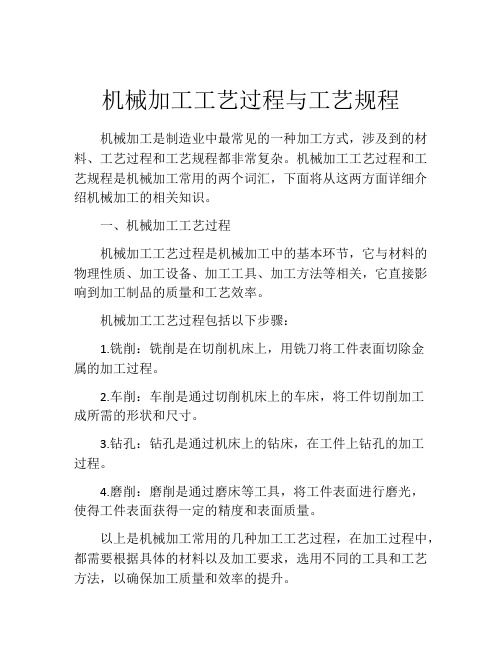
机械加工工艺过程与工艺规程机械加工是制造业中最常见的一种加工方式,涉及到的材料、工艺过程和工艺规程都非常复杂。
机械加工工艺过程和工艺规程是机械加工常用的两个词汇,下面将从这两方面详细介绍机械加工的相关知识。
一、机械加工工艺过程机械加工工艺过程是机械加工中的基本环节,它与材料的物理性质、加工设备、加工工具、加工方法等相关,它直接影响到加工制品的质量和工艺效率。
机械加工工艺过程包括以下步骤:1.铣削:铣削是在切削机床上,用铣刀将工件表面切除金属的加工过程。
2.车削:车削是通过切削机床上的车床,将工件切削加工成所需的形状和尺寸。
3.钻孔:钻孔是通过机床上的钻床,在工件上钻孔的加工过程。
4.磨削:磨削是通过磨床等工具,将工件表面进行磨光,使得工件表面获得一定的精度和表面质量。
以上是机械加工常用的几种加工工艺过程,在加工过程中,都需要根据具体的材料以及加工要求,选用不同的工具和工艺方法,以确保加工质量和效率的提升。
二、机械加工工艺规程机械加工工艺规程是机械加工中的管理工具,是加工生产所必需的制度和规定,为加工生产提供制度上的保障,从而保证了加工质量和制品的合格率。
机械加工工艺规程主要包括以下内容:1.材料的选用:工艺规程应明确加工材料的选用,根据不同的材料特性,来确定不同的加工工艺。
2.加工设备的选择:工艺规程应明确加工设备的选择,根据加工要求和产品规格,来选择合适的加工设备。
3.加工工具的选用:工艺规程应明确加工工具的选用,根据加工要求和产品规格,来选择合适的加工工具。
4.工艺参数的设定:工艺规程应根据不同的加工要求和工艺过程,来设定不同的工艺参数,包括进给速度、转速、切削深度、冷却液等参数。
5.加工顺序的规定:工艺规程应明确加工的顺序,根据不同零件的形状和复杂程度,来确定不同的加工顺序。
机械加工工艺规程的好处是显而易见的,它不仅可以保证加工质量,还可以提高生产效率,降低生产成本,还可以避免一些不必要的安全事故。
机械零件加工工艺过程的基本知识
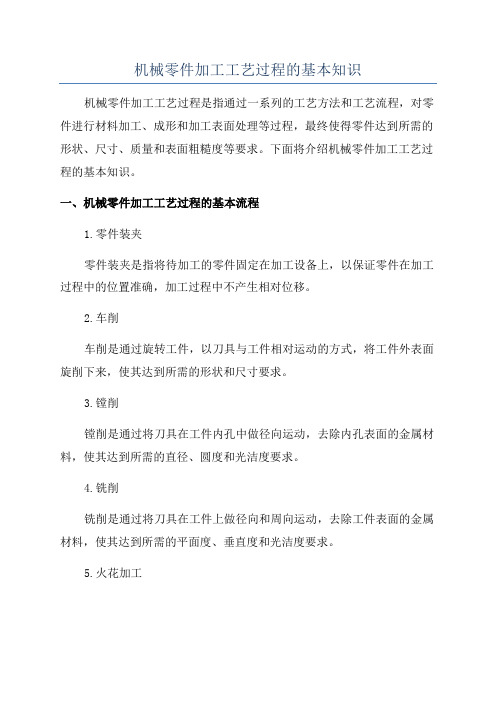
机械零件加工工艺过程的基本知识机械零件加工工艺过程是指通过一系列的工艺方法和工艺流程,对零件进行材料加工、成形和加工表面处理等过程,最终使得零件达到所需的形状、尺寸、质量和表面粗糙度等要求。
下面将介绍机械零件加工工艺过程的基本知识。
一、机械零件加工工艺过程的基本流程1.零件装夹零件装夹是指将待加工的零件固定在加工设备上,以保证零件在加工过程中的位置准确,加工过程中不产生相对位移。
2.车削车削是通过旋转工件,以刀具与工件相对运动的方式,将工件外表面旋削下来,使其达到所需的形状和尺寸要求。
3.镗削镗削是通过将刀具在工件内孔中做径向运动,去除内孔表面的金属材料,使其达到所需的直径、圆度和光洁度要求。
4.铣削铣削是通过将刀具在工件上做径向和周向运动,去除工件表面的金属材料,使其达到所需的平面度、垂直度和光洁度要求。
5.火花加工火花加工是利用电火花放电原理进行零件加工的一种加工方法。
通过电极与工件之间产生电火花放电,将工件上的材料溶解和熔化,并通过水冷剂迅速冷却,使其达到所需的形状和尺寸要求。
6.磨削磨削是通过在工件表面和砂轮之间进行相对运动,将工件表面的金属材料去除,以达到所需的平面度、圆度、光洁度和尺寸要求。
7.锤击锤击是通过将锤击力作用于工件上,去除工件上的金属材料,以达到所需的形状和尺寸要求。
8.切割切割是通过机械力或热能,将工件切割成所需的形状和尺寸。
常用的切割方法有剪切、火焰切割、激光切割等。
二、常见机械零件加工工艺方法1.塑性加工塑性加工是通过在零件上施加外力,使其发生塑性变形,以改变其形状和尺寸。
常见的塑性加工方法有拉伸、压缩、弯曲、冲压等。
2.热处理热处理是通过加热和冷却过程,改变零件内部组织结构,以改变其性能和硬度。
常见的热处理方法有淬火、回火、退火、时效等。
3.表面处理表面处理是对零件表面进行物理或化学处理,以提高其耐磨性、耐腐蚀性及美观度。
常见的表面处理方法有镀铬、镀镍、镀锌、喷涂、抛光等。
机械加工工艺流程
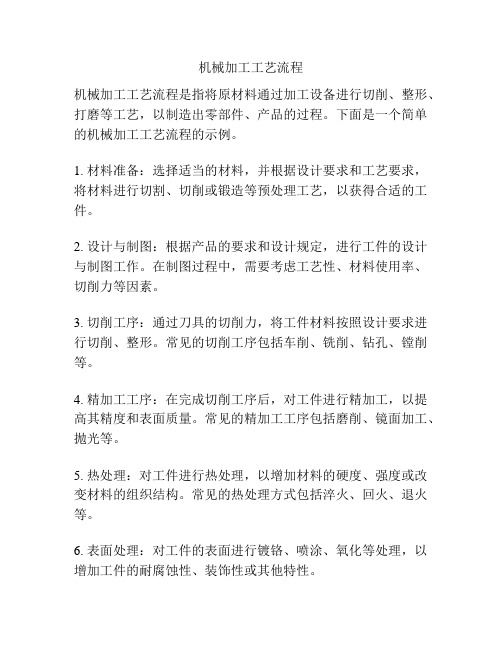
机械加工工艺流程机械加工工艺流程是指将原材料通过加工设备进行切削、整形、打磨等工艺,以制造出零部件、产品的过程。
下面是一个简单的机械加工工艺流程的示例。
1. 材料准备:选择适当的材料,并根据设计要求和工艺要求,将材料进行切割、切削或锻造等预处理工艺,以获得合适的工件。
2. 设计与制图:根据产品的要求和设计规定,进行工件的设计与制图工作。
在制图过程中,需要考虑工艺性、材料使用率、切削力等因素。
3. 切削工序:通过刀具的切削力,将工件材料按照设计要求进行切削、整形。
常见的切削工序包括车削、铣削、钻孔、镗削等。
4. 精加工工序:在完成切削工序后,对工件进行精加工,以提高其精度和表面质量。
常见的精加工工序包括磨削、镜面加工、抛光等。
5. 热处理:对工件进行热处理,以增加材料的硬度、强度或改变材料的组织结构。
常见的热处理方式包括淬火、回火、退火等。
6. 表面处理:对工件的表面进行镀铬、喷涂、氧化等处理,以增加工件的耐腐蚀性、装饰性或其他特性。
7. 装配与调试:根据产品的要求,对加工好的零部件进行组装,进行调试和测试,确保零部件与产品的质量和性能要求。
8. 检验与质量控制:对加工完成的零部件和产品进行检验,确保其质量和性能符合设计要求。
质量控制包括尺寸检验、外观检查、性能测试等。
9. 包装与入库:将加工好的零部件或产品进行包装,以防止损坏和污染。
然后按照规定的要求进行入库,以备后续使用或发货。
10. 运输与售后服务:将产品送往目的地,进行运输、安装和调试。
同时提供售后服务,包括技术支持、维修等。
以上是一个简单的机械加工工艺流程示例,不同的机械加工工艺流程可能会有所区别,具体的工艺流程会根据产品的特点、要求和加工设备的性能而有所不同。
什么是机械加工工艺过程

1.什么是机械加工工艺过程?答:机械加工工艺过程是指用机械加工的方法按规定的顺序把毛坯变成零件的全部过程。
2.工艺过程的基本单元是什么?如何划分?答:工序是组成工艺过程的基本单元。
工序又可分为安装、工位、工步和走刀。
3.什么是工序,安装,工步,工位和走刀?答:工序是指一个(或一组)工人在同一个工作地对一个(或同时对几个)工件连续完成的那一部分工艺过程。
安装是指在一道工序中工件经一次装夹后所完成的那部分工序内容。
工位是指工件在机床上占据每一个位置所完成的加工工步是指在加工表面、刀具和切削速度和进给量均保持不变的情况下完成的部分内容。
走刀是指刀具在加工表面上切削一次所完成的内容。
走刀是构成工艺过程的最小单元。
4.机械加工工艺规程制定的指导思想?答:保证质量,提高效率,降低成本。
尽量减少工人的劳动强度。
在保证质量的前提下,最大限度的提高生产率,满足生产要求,尽可能节约耗费,减少投资,降低制造成本。
6.什么是机械加工的工艺规程?它的作用特点是什么?工艺规程设计的原则和步骤有哪些?答:机械加工的工艺规程是机械制造厂最重要的文件之一。
蒋工艺规程内容填入一定的格式的卡片。
即成生产准备和施工依据的工艺文件。
设计原则:1)以保证零件加工质量,达到设计图纸规定的各项技术要求为前提。
2)工艺过程有较高的生产效率和较低的成本。
3)充分考虑和利用现有生产条件,尽可能作到平衡生产4)尽量减轻工人劳动强度,保证安全生产,创造良好、文明劳动条件。
5)积极采用先进技术和工艺,减少材料和能源消耗,并应符合环保要求。
设计步骤:1).阅读装配图和零件图2).工艺审查审查图纸上的尺寸、视图和技术要求是否完整、正确、统一,分析主要技术要求是否合理、适当,审查零件结构工艺性。
3).熟悉或确定毛坯确定毛坯的依据是零件在产品中的作用、零件本身的结构特征与外形尺寸、零件生产批量等。
7.何为零件的结构工艺性?零件的结构工艺性:零件制造、装配和维修的可行性和经济性。
机械加工工艺过程基本概念
机械加工工艺过程基本概念一、工艺过程的基本概念1.生产过程和工艺过程生产过程:由原材料制成各种零件并装配成机器的全过程。
其中包括原材料的运输、保管、生产准备、制造毛坯、切削加工、装配、检验及试车、油漆和包装等.工艺过程:在生产过程中,直接改变生产对象的形状、尺寸、表面质量、性质及相对位置等,使其成为成品或半成品的过程。
如毛坯的制造(包括铸造工艺、锻压工艺、焊接工艺等)、机械加工、热处理和装配等。
工艺过程是生产过程的核心组成部分。
机械加工工艺过程:采用机械加工的方法按一定顺序直接改变毛坯的形状、尺寸及表面质量,使其成为合格零件的工艺过程.它是生产过程的重要内容。
2。
机械加工工艺过程的组成零件的机械加工工艺过程由许多工序组合而成,每个工序又可分为若干个安装、工位、工步和走刀。
(1)工序工序是机械加工工艺过程的基本单元,是指由一个或一组工人在同一台机床或同一个工作地,对一个或同时对几个工件所连续完成的那一部分工艺过程。
工作地、工人、工件与连续作业构成了工序的四个要素,若其中任一要素发生变更,则构成了另一道工序。
一个工艺过程需要包括哪些工序,是由被加工零件的结构复杂程度、加工精度要求及生产类型所决定的。
如图1—36所示的阶梯轴,因不同的生产批量,就有不同的工艺过程及工序,如表1—4与表1-5所列。
图1—36 阶梯轴表1—4 单件生产阶梯轴的工艺过程表1-5 大批量生产阶梯轴的工艺过程(2)安装工件每经一次装夹后所完成的那部分工序在一道工序中,工件在加工位置上至少要装夹一次,但有的工件也可能会装夹几次。
如表1-5中的第2、3及5工序,须调头经过两次安装才能完成其工序的全部内容。
应尽可能减少装夹次数,多一次装夹就多一次安装误差,又增加了装卸辅助时间.(3)工位工件在机床上占据每一个位置所完成的那部分工序为减少装夹次数,常采用多工位夹具或多轴(多工位)机床,使工件在一次安装中先后经过若干个不同位置顺次进行加工。
机械加工工艺过程概述
在大多数工作地点,经常重复地进行一 种零件某一工序的生产。
生产类型的划分:
生产类型
同一零件的年产量(件)
重型
中型
小型
单件生产
成 小批生产
批 生
中批生产
产 大批生产
<5
5~100 100~300 300~1000
<10
10~200 200~500 500~5000
§1 机械加工工艺过程的基本概念
工艺是指制造产品的技巧、方法和程序。机械制造过程中, 凡是直接改变零件形状、尺寸、相对位置和性能等,使其成 为成品或半成品的过程,称为机械制造工艺过程。它通常包 括零件的制造与机器的装配两部分。
一、生产过程和工艺过程
1. 生产过程
由原材料制成各种零件,并装配成机器的全过程。
包括:原材料的运输、保管,生产准备、毛坯制造、 机械加工、装配、检验、试车、油漆、包装等。
2. 工艺过程
在生产过程中,直接改变原材料的(毛坯)的形状、 尺寸、性能,使之变为成品的过程。
工艺过程具体可分为:
铸造、压力加工、焊接、机械加工、热处理、特种加工、 电镀、涂覆、装配等工艺过程。
3. 机械加工工艺过程的组成
粗车:3~5mm
加工外圆面: 精车:1~1.6mm 粗磨:0.3~0.5mm
磨削 精磨:0.1mm以下
确定加工余量的方法: 1) 估算法
仅适用单件、小批量生产。
2) 查表法
适用一般的加工生产。应用最广泛。
3) 计算法
适用大批量生产和自动机床及数控机床加工。
四、定位基准的选择
1. 基准的概念及分类; 1) 基准
测量基准:测量工件被加工表面尺寸和相 互位置所依据的基准。
机械加工工艺过程概述
机械加工工艺过程概述引言机械加工是指利用机床和相关工具对工件进行形状和尺寸上的加工的过程。
机械加工是制造业中常见的一种加工方式,广泛应用于各个行业。
本文将对机械加工的工艺过程进行概述,包括常见的工艺步骤、加工方法和加工工具等。
工艺步骤机械加工的工艺步骤一般包括以下几个环节:1.设计工艺路线:在进行机械加工之前,需要进行工艺路线的设计。
工艺路线要根据产品的形状和尺寸要求,确定加工的先后顺序、工艺参数和机床设备的选择等。
2.准备工作:准备工作主要包括选择适当的机床和刀具、夹紧装置等,并进行机床的调整和刀具的安装。
3.装夹工件:将待加工的工件安装在机床上,并进行夹紧。
装夹的方式根据工件的材质和加工要求选择合适的夹具。
4.加工工艺:根据工艺路线进行相应的加工操作。
通常包括以下几种工艺:–车削:利用车床对旋转工件进行切削。
–铣削:利用铣床对工件进行切削,主要用于加工平面和曲面。
–镗削:利用镗床进行孔的加工。
–钻削:利用钻床进行孔的加工。
–切割:利用剪切机进行材料的切割。
–磨削:利用磨床进行工件表面的加工,主要用于提高工件的精度和表面质量。
–攻丝:利用螺纹加工机进行螺纹的加工。
–镶嵌:利用镶嵌机进行零件的组合和装配。
–焊接:利用焊接设备进行工件的连接,常见的有气焊、电焊、激光焊等。
–热处理:对工件进行加热和冷却处理,改变材料的组织结构和性能。
5.检验和调整:加工完成后,需要对工件进行检验和调整,以确保达到设计要求。
6.完成工艺:检验合格的工件进行清洗、组装和包装等,最终完成工艺。
加工方法机械加工的方法根据不同的加工要求和设备等,可以分为以下几种:1.切削加工:切削加工是机械加工的主要方法之一。
通过刀具和工件之间的相对运动,利用刀具对工件进行形状和尺寸的切削。
2.成形加工:成形加工是通过塑性变形对工件进行加工。
常见的成形加工方法包括锻造、压力成型、拉伸、胀管等。
3.去除加工:去除加工是通过去除工件表面的材料来达到加工效果。
(完整版)机械加工工艺过程分析
第一节 概述
一、工艺过程组成
生产过程:由原材料到生产出成品的全部劳 动过程的总和。包括原材料运输、保管、生 产准备、制造坯料、机械加工、装配、检验 及试车、油漆和包装等。
工艺过程:生产过程中直接改变原材料(坯料) 的性能、尺寸和形状,使之变成成品的过程。
机械加工工艺过程由一系列工序组成。
(二)、工艺基准 零件在工艺过程中所采用的基准。 1.工序基准
在工序图上,用于确定被加工表面位置使用 的基准称工序基准。 工序基准到被加工表面尺寸称为工序尺寸。
工序基准
2. 定位基准 工件上用于确定工件在夹具中位置的基准称为
定位基准。 C、D、A为定 位基准。
工件加工时的定位基准
3.测量基准 在测量时所采用的基准。
2.成批生产
成批制造相同的工件,每隔一定时间又重复进行的生 产。每批制造相同工件的数量称为批量。
按批量大小,成批生产又分为大批、中批、和小批生产 三种。 实际生产中,成批生产通常指中批生产。 机床制造厂多属成批生产。 3.大量生产
一种产品制造数量很多,多数工作地点经常重复地进 行一种工件某一工序的加工。 如汽车、拖拉机、轴承的制造。
M面为测量基准
工件上已加工表面的测量基准
4.装配基准 在机器装配时,用来确定零件或部件在产
品中的相对位置所采用的基准。
装配基准为M 、 N
四、机械加工精度及其获得方法 (一)、加工精度
加工精度是指零件加工后的实际几何参数(尺 寸、形状、位置)与理想几何参数的符合程度。
加工误差:零件加工后的实际几何参数(尺 寸、形状、位置)与理想几何参数的偏离程度。
零件加工过程中工艺尺寸链
(3)装配尺寸链:由装配精度与构成装配精度的 全部相关零件的设计尺寸所形成的尺寸链。
- 1、下载文档前请自行甄别文档内容的完整性,平台不提供额外的编辑、内容补充、找答案等附加服务。
- 2、"仅部分预览"的文档,不可在线预览部分如存在完整性等问题,可反馈申请退款(可完整预览的文档不适用该条件!)。
- 3、如文档侵犯您的权益,请联系客服反馈,我们会尽快为您处理(人工客服工作时间:9:00-18:30)。
产品数量很大,大多数工作地点经常重复地进行某一个 零件的某一道工序的加工。
生产纲领与生产类型的关系
零件的年生产纲领(件/年)
生产类型 重型零件 中型零件
轻型零件
单件生产 <5
<10
<100
小批生产 5~100
10~200 100~500
中批生产 100 ~300 200 ~500 500 ~5000
第一章 机械加工工艺过程概述
本 章 1.1 机械生产过程、工艺过程 内 1.2 基准的概念及其分类 容 1.3 机械加工精度及其获得方法
教 学 1、掌握生产过程及加工工艺过程基本概念、组成; 目 2、掌握设计基准与工艺基准的概念、分类; 的 3、了解加工精度的基本概念及获得加工精度的方法
§1-1 机械制造生产过程和工艺过程
工艺特征
单件小批
成批生产
大批大量
生产组织
机群式
分工段排列设 备
流水线或自动线
对工人的 技术要求
成本
较高 较高
一定水平 中等
调整工:要求高 操作工:要求低
较低
工艺文件 的要求
发展趋 势
编制简单的工艺 过程卡片
采用成组工艺, 数控机床加工中 心及柔性制造单 元
编制详细的工 艺规程及关键 工序的工序卡 片
一、生产过程
• 生产过程:将原材料或半成品转变为成品的各有关劳动过程 的总和。 包括:1、生产技术准备过程如产品设计、生产准备、原 材料的运输和保管; 2、毛坯制造过程; 3、机械加工和热处理; 4、装配和调试过程; 5、生产服务过程。
生产过程的实质是由原材料(或半成品)变为产品的过程。
二、机械加工工艺过程
它进行多次加工,每加工一次,称一次走刀。
三、生产纲领与生产类型
1.生产纲领 企业在计划期内应当生产的产品数量和进度计划称生产纲领。
N=Qn(1+a%)(1+b%)
• 根据生产纲领确定生产类型,不同的生产类型有不同的 工艺特征。
三、生产纲领与生产类型
• 生产类型对工艺过程的影响
• 当生产类型不同时,生产组织和生产管理、车间的机 床布置、毛坯的制造方法、采用的工艺装备(刀、夹、量 具)、加工方法以及工人的熟练程度等都有很大的不同, 因此在制订工艺路线之前必须明确该产品的生产类型。
1. 机械加工工艺过程:对机械零件采用各种加 工方法直接改变毛坯地形状、尺寸、表面粗 糙度以及力学物理性能使之成为合格零件的 全部劳动过程。
2.
将零件装配成部件或产品的过程,称
为装配工艺过程。
工艺过程按作用和效果分为:
1)毛坯成型工艺:改变零件的形状; 2)切削/ 磨削加工工艺:加工零件至固定尺寸; 3)光整加工工艺:降低表面粗糙度; 4)热处理工艺:改善金属材料的物理机械性能; 5)表面处理工艺:改善材料的外观或对外界环境的防护能力; 6)焊接工艺:连接零件或材料; 7)装配工艺:将合格零件、标准件等装配成产品的。
采用多工位加工,可以提高生产率 和保证被加工表面间的相互位置精度。
(4)工步
• 工步是工序的组成单位。在被加工的表面、切削用量(指 切削速度、背吃刀量和进给量)、切削刀具均保持不变的 情况下所完成的那部分工序,称工步。
• 当同时对一个零件的几个表面进行加工时,则为复合 工步。
(5)走刀
因,在被切加削工用的量某不一(变表的面5条,)件由走下于刀,余用量同较一大把或刀其具它对原
ห้องสมุดไป่ตู้
• 2)安装
•
工件在加工前,在机床或夹具中相对刀具应有一个
正确的位置并给予固定,这个过程称为装夹,一次装夹
所完成的那部分加工过程称为安装。
•
每一个工序可能有一次安装,也可能有几次安装。
3)工位
为减少工序中的装夹次数,常采用 回转工作台或回转夹具,使工件在一次 安装中,可先后在机床上占有不同的位 置进行连续加工,每一个位置所完成的 那部分工序,称一个工位。
模锻,加工 余量中等
通用机床
部分通用机 床和高效机 床
大多采用通用夹具、广泛采用夹 标准附件、通用刀 具,较多采 具、万能量具。靠 用专用刀具 划线和试切法达到 和量具 精度要求
大批大量
具有广泛的互换性
广泛采用金属模机器造 型、模锻或其它高效方 法,加工余量小
广泛采用高效专用机床 及自动机床
广泛采用高效夹具、复 合刀具、专用量具或自 动检验装置
§1-2 基准的概念及其分类
基准是用来确定生产对象上几何要素之间的几何关 系所依据的那些点、线或面。 分为两大类:设计基准和工艺基准 一、设计基准
编制详细的工艺规程、 工序卡片、调整卡片
采用成组工艺, 用计算机控制的自动 用柔性制造系 化制造系统、车间或 统或柔性自动 无人工厂实现自适应
线
控制
• 试切法:是在零件加工过程中不断对已加工表 面的尺寸进行测量,并相应调整刀具相对工件 加工表面的位置进行试切,直至达到尺寸精度 要求的加工方法。
• 调整法:即是按试切好的工件尺寸,标准件或 对刀块调整确定刀具相对工件定位基准的准确 位置,并在保持此准确位置不变的条件下,对 一批工件进行加工的方法。
• 零件生产批量的计算公式
n NA F
2、生产类型
生产类型对工艺过程有着重要影响。
三、生产纲领与生产类型
生产类型是指企业(或车间、工段、班组、工作地) 生产专业化程度的分类,一般分为: (1) 单件生产
三、生产纲领与生产类型
• (2) 成批生产
• 小批生产---其工艺过程的工艺特点和单件小批生产相似; • 大批生产---其工艺过程的特点和大量生产相似; • 中批生产---其工艺过程的特点则介于单件小批生产和大
2、机械加工工艺过程组成:是由一个或若干个顺序排列 的工序组成的,毛坯顺次通过这些工序就变成了成品或半 成品。 1)工序
• 一个或一组工人,在一个工作地对一个或同时对几个工 件所连续完成的那一部分工艺过程,称为工序 。
• 区分工序的主要依据,是设备(或工作地)是否变动和 完成的那一部分工艺内容是否连续。
大批生产 300 ~1000 500 ~5000 5000~50000
大量生产 >1000
>5000
>50000
各种生产类型的工艺特征
工艺特 征
零件的 互换性
毛坯制 造方法 与加工 余量
机床设 备
工艺装 备
单件小批
成批生产
缺乏互换性
大部分具有 互换性
木模手工造型或自 部分采用金 由锻,加工余量大 属模铸造或