精益生产培训课程
精益生产培训课程
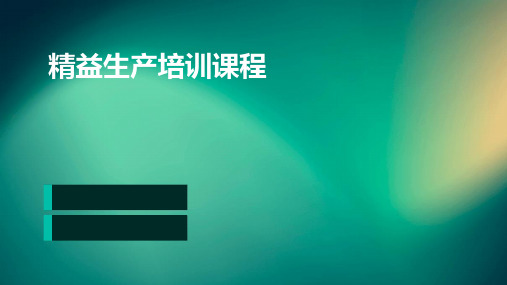
05 精益生产在中国的挑战与 机遇
市场环境与竞争态势
市场竞争激烈
随着中国制造业的快速发展,市 场竞争日趋激烈,企业需要不断 提升生产效率和产品质量以保持 竞争优势。
客户需求多样化
客户需求日益多样化,要求企业 具备快速响应市场变化的能力, 这需要企业引入精益生产理念, 实现个性化定制和柔性生产。
技术创新与人才培养
应用
在产品设计、生产和运营过程中, 绘制价值流图有助于企业了解产品 开发和生产流程中的瓶颈和浪费。
5S管理
定义
5S管理是一种现场管理方法,包 括整理(Sort)、整顿 (Straighten)、清扫
(Sweep)、清洁(Sanitize) 和素养(Sustain)五个方面。
目的
提高工作效率,减少浪费,保证 生产安全。
应用
03
在库存管理中,拉动系统有助于降低库存成本,减少浪费和降
低库存风险。
03 精益生产的实施步骤
明确目标与期望
01
确定企业实施精益生产的目标, 如降低成本、提高效率、优化流 程等。
02
明确企业高层对精益生产的期望 ,确保各部门对目标的理解和认 同。
价值流分析
对企业生产流程进行全面的价值流分 析,包括从原材料采购到产品交付的 整个过程。
质量管理
本田公司注重质量管理,通过严格的质量控制和持续改进,确保产 品的高品质。
创新与研发
本田公司在汽车技术方面不断创新,推出了一系列具有影响力的产 品和技术。
海尔集团
海尔管理模式
海尔集团采用独特的管理模式,注重流程优化、快速响应和持续 改进,实现了高效、低成本的生产和服务。
全球化战略
海尔集团积极推进全球化战略,通过收购、兼并与合作等方式拓 展海外市场,提高国际竞争力。
精益生产培训管理课程

包括物品的定位、定量、定容等方面,使生产现场的物品管理更加规范化和标准化 。
CHAPTER 03
流程改善与效率提升
价值流图分析
价值流图的概念和作用
介绍价值流图的基本定义、绘制方法和应用场景,帮助学 员理解价值流图在精益生产中的重要性。
设备点检制度
01
建立设备点检制度,明确点检的内容、周期和标准,确保设备
正常运行。
设备保养制度
02
制定设备保养计划,包括日常保养、定期保养和特殊保养等,
确保设备性能稳定。
点检与保养记录管理
03
建立点检和保养记录档案,实现设备维护的可追溯性。
故障诊断与预防性维修
故障诊断技术
介绍常见的故障诊断技术 ,如振动分析、油液分析 等,提高员工故障诊断能 力。
安全库存设定
根据历史数据和市场需求预测,设定合理的安全库存水平,避免 库存积压和缺货风险。
库存周转分析
定期对库存周转情况进行分析,识别滞销品和畅销品,优化库存 结构。
采购成本控制策略
集中采购
通过集中采购降低采购成本,提高采购效率。
供应商谈判
与供应商进行价格和质量谈判,争取更优惠的采购条件和更高的产 品质量。
精益生产培训管理课 程
目录
• 精益生产概述 • 现场管理优化 • 流程改善与效率提升 • 设备维护与预防性维修 • 质量管理及持续改进 • 供应链协同与库存管理 • 人力资源管理在精益生产中作用 • 企业实施精益生产挑战与对策
CHAPTER 01
精益生产概述
精益生产起源与发展
起源
精益生产起源于20世纪50年代的日 本丰田汽车公司,其核心思想是通过 消除浪费、提高效率来降低成本、提 升产品质量和客户满意度。
精益生产培训课件(PPT 91页)
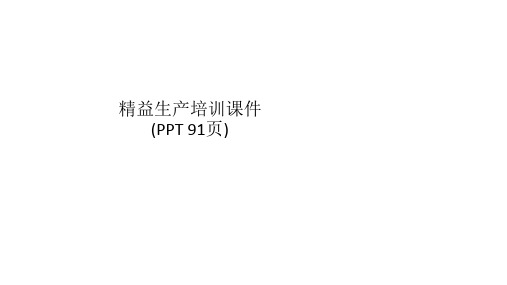
Value Added
Non Value Added
Distance
Time
360 Ft. 12 min.
工作场所布置
物料固定场所
工具,物料放在小臂范围内
工作场所布置
工作场所布置
物料依左右手拿的顺序去摆放
13 4 2
重量堕送
工作场所布置
工作场所布置
保持良好的姿势
工作台的设计:工作 台高度应在肘下一至 三寸
工具设备 设计
一.尽量使用工装或足踏工具,以解除手的“持住”动作。 二.可能时应将两种以上工具合并。 三.对手指的工作负荷应依其本能予以分配。 四.手柄之设计应可能使其与手之接触面积增大。 五.机器设备之操作杆、开关、手柄之位置应在工作者正常作业范围内,以尽量
级别 1 2 3 4 5
运动驱轴
指节 手腕
肘 肩 身躯
人体运动部位
手指 手指及手掌 手指,手掌及前臂 手指,手掌,前臂及上臂 手指,手掌,前臂,上臂及肩
在满足动作需要的情况下,人体的动作应尽量应用最低等级。
2.工作场所 布置
原则:
工具、物料应放置在固定的场所. 工具、物料及装置应放置在小臂的工作范围内. 工具、物料应依工作顺序放置排列以利使用. 零件物料之供给,应利用其重量堕送. 工作台及椅之式样使工作者保持良好的姿势
05
02
过量生产浪费
06
03
搬运浪费
07
04
动作浪费
08
等待浪费 库存浪费 过度加工浪费 管理浪费
良纠正 浪费
定义:由于工厂内出现不良品,需要进行处置的时间、人力、物 力上的浪费,以及由此造成的相关损失。
•额外的时间和人工进行检查, 返工等工作 •由此而引起的无法准时交货 •企业的运作是补救式的,而非 预防式的(救火方式的运作)
精益生产管理培训课程

精益生产管理培训课程本次培训介绍本次培训的目标是帮助参训人员深入了解精益生产管理的基本理念、方法和实践,掌握精益生产的工具和技术,从而提高企业的生产效率和竞争力。
培训介绍了精益生产管理的基本理念,包括价值、价值流、流动、拉动和持续改进等核心概念。
通过案例分析和讨论,参训人员深入理解了精益生产的核心思想,并明确了如何在实际工作中应用这些理念。
接下来,培训深入探讨了精益生产的工具和技术,包括5S、看板、TPM、SMED等。
参训人员通过实操练习和小组讨论,掌握了这些工具的使用方法和技巧,并学会了如何将其应用到实际工作中。
培训还重点介绍了精益生产的实践方法,包括价值流分析、流程改进和持续改进等。
参训人员通过案例分析和模拟练习,掌握了这些实践方法的应用步骤和技巧,并能够将其应用到实际工作中,提高生产效率和质量。
培训还分享了成功实施精益生产的最佳实践和经验教训。
参训人员通过听取成功案例的分享和经验教训的总结,深入了解了精益生产的挑战和机遇,并明确了如何在实际工作中成功实施精益生产。
通过本次培训,参训人员不仅掌握了精益生产管理的基本理念、工具和技术,还学会了如何将其应用到实际工作中,提高企业的生产效率和竞争力。
希望通过本次培训,大家能够将所学知识运用到实际工作中,推动企业的持续改进和发展。
以下是本次培训的主要内容一、培训背景本次培训背景立足于我国制造企业面临的竞争压力和生产效率提升的需求。
随着全球市场的日益激烈,我国企业需要不断提高自身竞争力,以满足市场变化和客户需求的挑战。
而精益生产作为一种有效的生产管理模式,能够帮助企业提高生产效率、降低成本、提升产品质量,从而更好地应对市场竞争。
二、培训目的本次培训的目的在于使参训人员深入理解精益生产管理的基本理念、方法和实践,掌握精益生产的工具和技术,从而提升企业的生产效率和竞争力。
培训还将分享成功实施精益生产的最佳实践和经验教训,帮助参训人员明确如何在实际工作中成功实施精益生产,推动企业的持续改进和发展。
《精益生产基础培训》ppt课件pptx
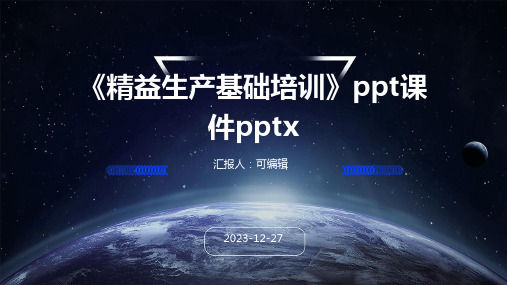
单元化生产
单元化生产是将生产线或设备按照产品族或工艺特点进行模块化设计,以提高生产 效率和灵活性的一种生产方式。
通过单元化生产,可以实现小批量、多品种的生产,满足市场需求的快速变化。同 时还可以提高设备的利用率和员工的技能水平。
单元化生产的实施需要提前进行生产线或设备的规划和设计,并注重员工培训和跨 部门协作。
竞争中获得优势。
促进可持续发展
精益生产注重环保和资源节约 ,有助于企业实现可持续发展
。
精益生产的历史与发展
起源
未来趋势
精益生产起源于日本丰田汽车公司的 生产方式,旨在消除浪费、提高效率 和效益。
随着科技的不断进步和应用,精益生 产将进一步与数字化、智能化相结合 ,实现更高水平的自动化和智能化。
发展历程
Straighten)、清扫(Shine)、清洁 (Standardize)、素养(Sustain)五
个方面。
通过实施5S管理,可以提高生产现场 的整洁度和效率,减少浪费,提高生产 质量、定期 检查和持续改进,确保管理效果的持久
性和有效性。
明确改进措施、时间表、责任人及所需资源。
风险评估与应对
预测潜在风险,制定应对措施,确保改进计划的顺利实施。
实施改进措施
1 2
培训与沟通
对相关人员进行培训,确保他们理解并掌握改进 措施。
资源配置
确保所需的人员、设备、材料和技术得到有效配 置。
3
实施改进措施
按照计划逐步实施改进措施,确保改进过程顺利 进行。
随着丰田生产方式的成功,精益生产 逐渐被全球范围内的企业所采纳和推 广。
02
精益生产的核心原则
价值导向
价值导向
强调从客户需求出发,识别并确 定客户认为有价值的流程和功能 ,消除非增值的环节和活动,实
精益生产知识培训(ppt
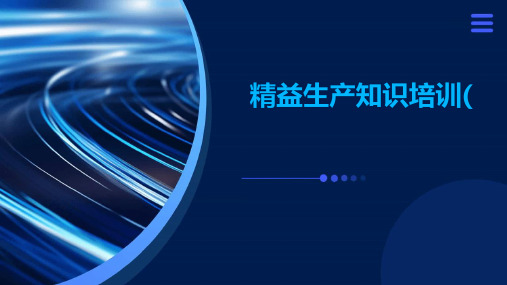
积极引入新技术、新工艺和新设备,提高生产效率和产品质量。
鼓励员工创新
鼓励员工提出改进意见和建议,激发员工的创新精神,促进企业持 续发展。
04
CATALOGUE
精益生产在服务业中的应用
服务流程优化
识别并消除浪费
01
通过对服务流程的全面分析,找出并消除浪费的时间、人力和
资源,提高服务效率。
客户需求导向
精益生产以客户需求为导向,注重满足客户需求和提高客 户满意度,通过快速响应市场需求和灵活调整生产计划, 实现个性化、定制化的生产。
02
CATALOGUE
精益生产的主要工具
5S管理
01
02
03
04
05
整理(Seiri)
整顿(Seiton) 清扫(Seiso)
清洁(Seiketsu 素养(Shitsuke
精益生产的核心思想
消除浪费
精益生产强调消除生产过程中的浪费,包括时间、人力、 物力等方面的浪费,以提高生产效率和降低成本。
持续改进
精益生产强调持续改进和优化生产过程,通过不断改进生 产方法、引入新技术、提高员工技能等方式,不断提高生 产效率和产品质量。
提高效率
精益生产注重提高生产效率,通过优化生产流程、提高设 备利用率、减少停机时间等方式,实现高效、低成本的生 产。
客户反馈机制
建立有效的客户反馈机制,及时了解客户的需求和意见,不断改 进服务,提高客户忠诚度。
持续改进与创新
持续改进
不断寻求改进的机会,通过持续改进提高服务质量和效率。
创新思维
鼓励员工提出创新性的想法和建议,以适应不断变化的市场需求和 客户需求。
跨部门合作
促进不同部门之间的合作,共同寻找改进和创新的机会,推动公司持 续发展。
精益生产管理培训课程
精益生产管理培训课程精益生产管理是一种企业管理方法论,旨在通过减少浪费、提高效率和质量,最大程度地满足客户需求。
为了帮助企业领导者和管理人员更好地理解和应用精益生产管理,开展一门精益生产管理培训课程是非常必要的。
这门精益生产管理培训课程旨在为企业管理者和团队提供精益生产管理理论与实践的基础知识,培养参训人员的分析思维、问题解决和团队合作能力,并引导他们将学到的技能应用到实际的工作场景中。
本课程的主要内容如下:1. 精益生产管理的概念和原则:介绍精益生产管理的核心思想,包括价值、价值流、流动、拉动、追求完美和持续改进等原则。
2. 浪费与价值流分析:讲解不增值活动的种类和如何通过价值流图来分析和改进生产流程,以最大程度地减少浪费。
3. 5S整理与标准化:介绍5S整理方法和标准化工作,包括整理、整顿、清扫、清洁、素养等环节,并讲解如何通过5S来提高工作效率和减少错误。
4. 问题解决与改进:引导参训人员学习常用的问题解决方法,如A3报告、PDCA循环等,并介绍如何将持续改进理念应用到日常工作中。
5. 价值流映射与单品流生产:讲解如何通过价值流映射和单品流生产来提高生产效率和降低库存成本。
6. 人员培训与团队合作:强调人员培养和团队合作对于精益生产管理的重要性,介绍如何培养团队合作和沟通能力。
7. 精益生产管理案例分析:通过实际案例的分析,让参训人员更好地理解和应用精益生产管理的方法。
此外,本课程还将通过实际操作、互动讨论和团队活动等形式,激发参训人员的学习热情和动手实践能力,增强他们的理论知识应用能力。
通过参加这门精益生产管理培训课程,企业管理者和团队成员将能够深入了解精益生产管理的理论和实践,掌握一系列提高效率和质量的工具和技巧,从而能够在实际工作中更好地推动企业的持续改进和发展。
精益生产管理是一种有效的企业管理方法,通过减少浪费、提高效率和质量,可以帮助企业增加竞争力,提升客户满意度,并实现持续改进。
精益生产通用培训课程
加强实践操作和案例分析,增强学员的实践能力
建立完善的培训评估机制,不断改进和优化培训课程
针对不同行业和领域,制定个性化的培训课程
引入先进的精益生产理念和技术,提高培训质量
汇报人:
感谢观看
产品质量提升:通过精益生产通用培训课程,企业员工能够更好地掌握质量控制方法,提高产品质量,减少不良品率。
客户满意度提升:通过精益生产通用培训课程,企业员工能够更好地了解客户需求,提高客户满意度,增加市场份额。
企业形象提升:通过精益生产通用培训课程,企业能够更好地展示自己的实力和形象,提高品牌知名度和美誉度。
精益生产核心理念
客户需求导向:以客户需求为导向,快速响应市场变化
消除浪费:通过消除生产过程中的浪费,提高效率和降低成本
持续改进:不断寻求改进机会,持续优化生产过程
团队合作:强调团队合作,跨部门协作,共同实现目标
03
精益生产通用培训课程目标
提高生产效率
通过精益生产通用培训课程,提高生产效率,减少浪费,降低成本
定义:标准化作业是指将作业人员、机器设备、材料、环境等生产要素进行合理配置,按照规定的程序和方法进行操作,以确保生产过程稳定、高效的一种作业方式。
目的:通过标准化作业,可以提高生产效率、降低成本、提高产品质量,同时也可以提高员工的安全意识和技能水平。
标准化作业的意义:可以促进企业生产管理的规范化、科学化,提高企业的整体竞争力。
07
精益生产通用培训课程总结与展望
总结本次培训课程成果与不足
成果:学员掌握精益生产的基本理念和方法,能够识别浪费并采取相应措施
不足:部分学员对精益生产的理解不够深入,需要加强实践操作和案例分析
精益生产课程培训计划
精益生产课程培训计划一、培训目标本次精益生产课程培训旨在帮助学员全面了解精益生产理念和方法,掌握精益生产工具和技术,提升生产效率和质量,降低成本和浪费,增强企业竞争力和持续改进能力。
二、培训对象适合生产企业管理人员、生产工程师、生产主管、质量管理人员、供应链管理人员等参加。
三、培训内容1. 精益生产理念和价值观- 精益生产的发展历程- 精益生产的核心概念- 精益文化和价值观2. 精益生产原则- 价值流映射- 流程优化- 作业标准化- 拉动生产和短周期生产3. 精益生产工具和方法- 5S整理、整顿、清扫、清洁和安全- 连续流(单片流、小批量生产和快速切换)- 产线平衡和节拍生产- 持续改进和问题解决(PDCA、A3、Kaizen等)- 价值流分析和价值流映射(VSM)4. 精益生产与质量管理- 和谐柔性制造系统- 整合生产和质量控制- 品质圈- 全员参与和错误防范意识五、培训方法本次培训将采用理论讲解、案例分析、现场考察和实际操作相结合的方式进行,让学员在实践中更好地理解和掌握精益生产知识和技术。
六、培训时间和地点时间:根据企业实际情况安排,通常为2-3天地点:企业内部或培训机构七、培训师资本次培训将邀请具有丰富精益生产理论和实践经验的专家学者担任授课讲师,为学员提供专业指导和帮助。
八、培训效果评估在培训结束后,将对学员进行知识点考核和工作实践评估,以评定培训效果,为企业后续改进和发展提供参考。
九、培训投入和收益分析精益生产课程培训需要一定的投入,但通过培训提高生产效率、降低成本和浪费,将带来更多的经济效益和社会效益,值得企业进行投资。
结语精益生产课程培训是企业持续改进和发展的重要手段,通过培训学习,可以帮助企业管理人员和员工更好地理解精益生产理念和方法,主动参与和推动精益生产的实施和持续改进,实现企业生产效率、质量和竞争力的全面提升。
希望通过本次培训,可以为企业和学员带来更多的收益和成长。
精益生产管理理念培训课程
精益生产管理理念培训课程精益生产管理是一种以极简和高效为原则的管理理念,旨在通过减少浪费、提高质量和提升生产效率,从而最大程度地满足客户需求。
为了帮助企业实施精益生产管理,我们定制了一套培训课程,旨在帮助参与者掌握精益生产管理的核心原理和实施方法。
课程一:精益生产管理基础在这门课程中,我们将介绍精益生产管理的基本概念和原则,包括价值流分析、五大浪费、持续改进和流程优化等。
通过实例演练和案例研究,参与者将学习如何发现和减少浪费,提高效率和质量。
课程二:价值流分析这门课程将重点介绍价值流分析方法,它是精益生产管理的核心工具之一。
参与者将学习如何通过价值流分析,识别生产过程中的不必要活动和延迟,从而改进生产流程,提高产品交付时间和顾客满意度。
课程三:持续改进和团队参与这门课程将探讨精益生产管理中的持续改进和团队参与的重要性。
通过案例学习和团队演练,参与者将学习如何建立一个积极参与、持续改进的团队文化,并掌握持续改进工具和技巧,如PDCA循环和KAIZEN活动。
课程四:流程优化和质量管理这门课程将重点介绍如何通过流程优化和质量管理来减少浪费和提高生产效率。
参与者将学习如何使用流程图、价值流图和控制图等工具,来监控和改进生产过程,提升产品质量和顾客满意度。
课程五:精益供应链管理这门课程将探讨精益生产管理在供应链中的应用。
参与者将学习如何通过精益供应链管理来减少库存、提高交付速度和降低成本。
同时,我们还将介绍与供应商的合作和协调的重要性,以及如何建立一个高效、稳定的供应链体系。
通过这套培训课程,参与者将全面了解精益生产管理的核心原理和工具,并具备实施精益生产管理的能力。
我们相信,这将有助于企业改善生产流程,提升效益和竞争力。
课程六:精益文化和领导力这门课程将探讨如何建立和培养一个符合精益文化的工作环境。
参与者将了解领导力在精益生产管理中的关键作用,学习如何激发员工的创造力和主动性,以及如何建立一个高效的沟通和协作机制。
- 1、下载文档前请自行甄别文档内容的完整性,平台不提供额外的编辑、内容补充、找答案等附加服务。
- 2、"仅部分预览"的文档,不可在线预览部分如存在完整性等问题,可反馈申请退款(可完整预览的文档不适用该条件!)。
- 3、如文档侵犯您的权益,请联系客服反馈,我们会尽快为您处理(人工客服工作时间:9:00-18:30)。
rotates between the factory and suppliers
17
Copyright 2006 John Wiley & Sons, Inc.
18
Copyright 2006 John Wiley & Sons, Inc.
19
Copyright 2006 John Wiley & Sons, Inc.
27
Common Techniques for Reducing Setup Time
Copyright 2006 John Wiley & Sons, Inc.
28
Common Techniques for Reducing Setup Time (cont.)
Copyright 2006 John Wiley & Sons, Inc.
Production kanban
authorizes production of goods
Withdrawal kanban
authorizes movement of goods
Kanban square
a marked area designated to hold items
Q-R
Bin 2 R
b) Kanban inventory system Kanban
R
Q = order quantity R = reorder point - demand during lead time
Copyright 2006 John Wiley & Sons, Inc.
16
Types of Kanban
goods
Copyright 2006 John Wiley & Sons, Inc.
14
Sample Kanban
Copyright 2006 John Wiley & Sons, Inc.
15
Origin of Kanban
a) Two-bin inventory system Bin 1
Reorder card
Internal setup
Can be performed only when a process is stopped
External setup
Can be performed in advance
SMED Principles
Separate internal setup from external setup
Copyright 2006 John Wiley & Sons, Inc.
25
Components of Lead Time
Processing time
Reduce number of items or improve efficiency
Move time
Reduce distances, simplify movements, standardize routings
Copyright 2006 John Wiley & Sons, Inc.Biblioteka Signal kanban
a triangular kanban used to signal production at the previous workstation
Material kanban
used to order material in advance of a process
on each other
Copyright 2006 John Wiley & Sons, Inc.
23
▪ Inventory Hides Problems
Copyright 2006 John Wiley & Sons, Inc.
24
▪ Less Inventory Exposes Problems
Copyright 2006 John Wiley & Sons, Inc.
2
Lean Production
Doing more with less inventory, fewer workers, less space
Just-in-time (JIT)
smoothing the flow of material to arrive just as it is needed
3
Waste in Operations
Copyright 2006 John Wiley & Sons, Inc.
4
Waste in Operations (cont.)
Copyright 2006 John Wiley & Sons, Inc.
5
Waste in Operations (cont.)
maintenance Supplier networks
Copyright 2006 John Wiley & Sons, Inc.
7
Flexible Resources
Multifunctional workers
perform more than one job general-purpose machines perform
12
Pull System
Material is pulled through the system when needed
Reversal of traditional push system where material is pushed according to a schedule
22
Small Lots
Require less space and capital investment
Move processes closer together Make quality problems easier to
detect Make processes more dependent
Cli精ck益to生ed产it 培Ma训st课er 程title style
Click to edit Master subtitle style
Copyright 2006 John Wiley & Sons, Inc.
Lecture Outline
Basic Elements of Lean Production Benefits of Lean Production Implementing Lean Production Lean Services
comprised of dissimilar machines brought together to manufacture a family of parts
Cycle time is adjusted to match takt time by changing worker paths
dL + S (150 x 0.5) + 7.5
N= C =
25
75 + 7.5
=
= 3.3 kanbans or containers
25
Round up to 4 (to allow some slack) or down to 3 (to force improvement)
Copyright 2006 John Wiley & Sons, Inc.
20
Determining Number of Kanbans
average demand during lead time + safety stock
No. of Kanbans =
container size
where
dL + S N= C
N = number of kanbans or containers d = average demand over some time period L = lead time to replenish an order S = safety stock C = container size
Copyright 2006 John Wiley & Sons, Inc.
6
Basic Elements
Flexible resources Cellular layouts Pull production system Kanban production control Small lot production Quick setups Uniform production levels Total productive
Copyright 2006 John Wiley & Sons, Inc.
8
Standard Operating Routine for a Worker
Copyright 2006 John Wiley & Sons, Inc.
9
Cellular Layouts
Manufacturing cells
Forces cooperation Prevent over and underproduction While push systems rely on a predetermined
schedule, pull systems rely on customer requests
Copyright 2006 John Wiley & Sons, Inc.
Copyright 2006 John Wiley & Sons, Inc.