材料力学 论金属的断裂
材料力学性能第四章—金属的断裂韧度
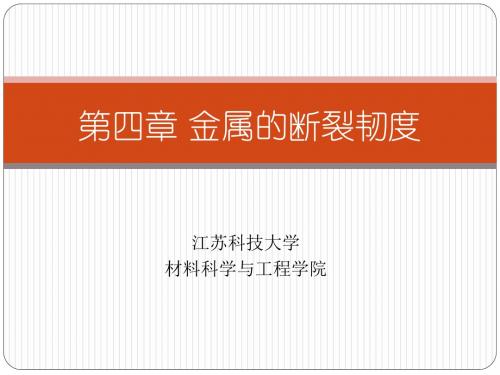
K Ⅰ 、 K Ⅱ 、K Ⅲ
表4-1 几种裂纹的KI表达式
K I Y a
a:1/2裂纹长度 Y——裂纹形状系数(无量纲量)
裂尖应力分量除了决定其 KI 3 x cos (1 sin sin ) 位置外,还与KI有关。 2 2 2 2 r
对于某确定的点,其应力 y K I cos (1 sin sin 3 ) 2 2 2 2 r 分量由KI决定,KI↑,则 z ( x y )(平面应变) 应力场各应力分量也↑。
对应的力学性能指标——断裂韧度
断裂强度 1922,Griffith,首先在强度与裂纹尺度建立关系
格雷菲斯断裂强度(从吸收能量的角度考虑)
弹性能降低足以满足裂纹表面能的增加和塑性变形能从
而导致材料脆性断裂。
断裂韧度(从阻止裂纹扩展的角度考虑) 得到相应的K判据。
用应力应变分析方法,考虑裂纹尖端附近的应力场强度,
超高强度钢, D6AC,1400MPa
断裂力学
低应力脆断与断裂力学
机件设计,σ<σs/n,不考虑裂纹 出现低应力脆断 → 宏观裂纹存在→应力集中 断裂——裂纹扩展引起,研究裂纹体的扩展
主要内容
线弹性条件下的金属断裂韧度☆ 金属断裂韧度的测试 影响断裂韧度的因素
断裂K判据应用案例☆
弹塑性条件下金属断裂韧度的基本概念
2
x y
2
(
x y
2
3 ( 1 2 )
裂纹尖端附近任一点P(r,θ)的主应力:
1 2
大连理工大学精品课程-材料力学性能-第四章-金属的断裂韧度(2)

建立符合塑性变形临界条件(屈服)的函数表达
式r=f(),该式对应的图形即代表塑性区边界形状,
其边界值即为塑性区尺寸。
由材料力学可知,通过一点的主应力1、2、 3和x、y、z方向上各应力分量的关系为:
7
2020年7月30日 星期四
第四章 金属的断裂韧度
1 x y
2
x
2
y
2
2 xy
1 K cos 1 sin
展。我们将x方向(=0)的塑
性区尺寸r0定义为塑性区宽 度。
10
图4-2 裂纹尖端附近塑性区 的形状和尺寸
2020年7月30日 星期四
第四章 金属的断裂韧度
r0
1
2
K
ys
2
KI—应力场强度因子
ys—有效屈服应力
s—单向拉伸时的屈服强度 —泊松比
r0
1
2
K
s
2
(平面应力)
r0
(1 2 2
)2
、有效裂纹及KI的修正 由于裂纹尖端塑性区的存在,会降
低裂纹体的刚度,相当于裂纹长度的增
加,因而会影响应力场及KI的计算,所 以要对KI进行修正。最简单和实用的方 法是在计算KI时采用虚拟等效裂纹代替 实际裂纹。
20
2020年7月30日 星期四
第四章 金属的断裂韧度
如图4-5所示,裂纹a前方
区域未屈服前,y的分布曲线
2020年7月30日 星期四
第四章 金属的断裂韧度
KI≥KI(KIC)是一个很有用的关系式,它将 材料的断裂韧度同机件的工作应力及裂纹尺寸 的关系定量地联系起来了。应用这个关系式可 解决有关裂纹体的断裂问题:如可以估算裂纹
体的最大承载能力、允许裂纹尺寸a及材料断
大连理工大学精品课程-材料力学性能-第一章-金属断裂(2)

解理面(001) 扩展方向[110]
挛晶面(112) 挛晶方向[111]
27
图1-67 解理舌形成示意图
2020年7月26日 第一章 单向静载下材料的力学性能 星期日 准解理
材料中弥散细小的第二
相影响裂纹的形成与扩展,
使裂纹难于严格按一定晶体
学平面扩展,断裂路径不再 与晶粒位向有关,主要与细 小碳化物质点有关。其微观 特征似解理河流但又非真正 28 解理,故称准解理。
24
图1-64 河流通过大角度 晶界时的扇形花样
2020年7月26日 第一章 单向静载下材料的力学性能 星期日
当解理裂纹通过扭转晶界时,因晶界两侧晶
体以边界为公共面转动一个角度,使两侧解理裂
纹存在位向差,故裂纹不能直接越过晶界而必须
重新成核,裂纹将沿若干组
新的相互平行的解理面扩展
而使台阶激增,形成为数众
1
m
E s
a0
2
s——表面能;
a0——原子面间距; E——弹性模量
1
1
形成裂纹的力学条件为: (f
i )
d
2
Es 2
2r a0
可得: f i 2Er s
da0
f——形成裂纹所需
的切应力;
7
2020年7月26日 第一章 单向静载下材料的力学性能 星期日 (二)、解理裂纹的扩展 以上所述主要涉及解理裂纹的形成,并不意味 着由此形成的裂纹将迅速扩展而导致材料断裂。解 理断裂过程包括以下三个阶段:塑性变形形成裂 纹;裂纹在同一晶粒内初期长大;裂纹越过晶界向 相邻晶粒扩展。
多的 “河流”,这与通过大角
度晶界的情况类似。
25
图1-65 河流花样通过扭转晶界
材料力学中的断裂与韧性

材料力学中的断裂与韧性材料力学作为一门关于物质内部结构和力学行为的科学,对于材料的性能与可靠性有着重要的影响。
其中,断裂与韧性是材料力学中一个十分关键的概念。
断裂指的是材料在外界施加力的作用下出现破裂的现象,而韧性则是指材料的抵抗断裂破坏的能力。
本文将从材料的断裂机制、断裂韧性的影响因素以及提高材料韧性的方法等方面加以论述。
一、材料的断裂机制材料断裂机制是指材料在承受外力作用下,因内部结构破坏而发生断裂的过程。
一般来说,材料的断裂机制可以分为韧性断裂和脆性断裂两种情况。
韧性断裂多见于金属等延展性材料,其断裂过程具有典型的韧性特征。
在外力的作用下,材料会先发生塑性变形,从而使得应力集中区域得到缓和。
随着外力的不断增加,应力集中区域逐渐扩大,并伴随着微裂纹的形成和扩展。
当微裂纹沿着材料内部继续扩展,最终导致材料的完全破裂。
需要注意的是,韧性断裂一般伴随着较大的能量吸收过程,因此对于抗震等要求韧性的工程结构,选择具有良好韧性的材料是十分重要的。
脆性断裂则多见于陶瓷、混凝土等脆性材料。
该类材料的断裂过程没有明显的塑性变形区域,而是在外力作用下直接发生破裂。
通常来说,脆性断裂的特点是断裂韧性较低,能量吸收较小。
二、影响材料韧性的因素材料的韧性不仅与材料本身的性质有关,同时也受到外界条件和应力状态的影响。
以下是一些影响材料韧性的常见因素:1.结构层次:材料的内部结构和组织对其韧性有着很大的影响。
晶粒的尺寸、形状以及晶界的性质等都会对材料的韧性产生影响。
一般来说,晶粒尺寸越小、晶界越多越强,材料的韧性也会相对提高。
2.材料纯度:杂质和夹杂物是影响材料韧性的重要因素。
杂质和夹杂物会引起应力集中,从而导致微裂纹的形成和扩展。
因此,材料的纯度对韧性有着直接的影响。
3.应力状态:不同的应力状态对材料的韧性有着直接影响。
例如,拉伸和压缩状态下的材料韧性表现可能不同。
此外,不同应力速率下材料的断裂行为也可能有所不同。
三、提高材料韧性的方法提高材料的韧性是工程实践中的一项重要任务。
金属的断裂应变
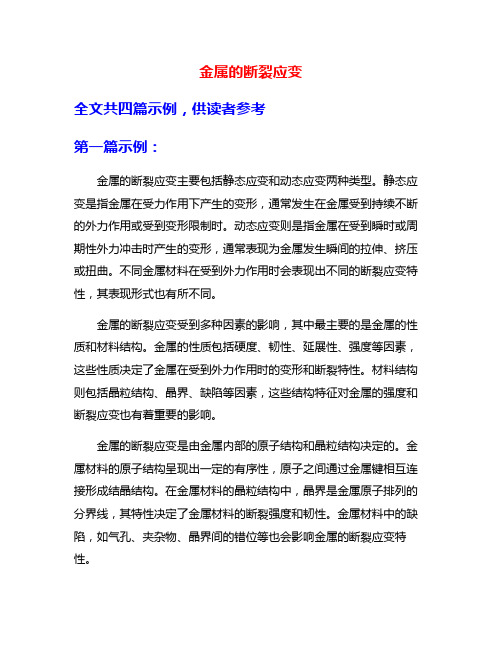
金属的断裂应变全文共四篇示例,供读者参考第一篇示例:金属的断裂应变主要包括静态应变和动态应变两种类型。
静态应变是指金属在受力作用下产生的变形,通常发生在金属受到持续不断的外力作用或受到变形限制时。
动态应变则是指金属在受到瞬时或周期性外力冲击时产生的变形,通常表现为金属发生瞬间的拉伸、挤压或扭曲。
不同金属材料在受到外力作用时会表现出不同的断裂应变特性,其表现形式也有所不同。
金属的断裂应变受到多种因素的影响,其中最主要的是金属的性质和材料结构。
金属的性质包括硬度、韧性、延展性、强度等因素,这些性质决定了金属在受到外力作用时的变形和断裂特性。
材料结构则包括晶粒结构、晶界、缺陷等因素,这些结构特征对金属的强度和断裂应变也有着重要的影响。
金属的断裂应变是由金属内部的原子结构和晶粒结构决定的。
金属材料的原子结构呈现出一定的有序性,原子之间通过金属键相互连接形成结晶结构。
在金属材料的晶粒结构中,晶界是金属原子排列的分界线,其特性决定了金属材料的断裂强度和韧性。
金属材料中的缺陷,如气孔、夹杂物、晶界间的错位等也会影响金属的断裂应变特性。
在金属的断裂应变中,除了金属的性质和结构外,外力的大小、作用方向和加载速度也会对金属的断裂应变产生影响。
外力作用越大,金属的断裂应变越容易发生;外力的作用方向不同,金属的断裂形式也会有所不同;加载速度的快慢则会影响金属的断裂速度和特性。
金属的断裂应变在工程实践中具有重要的意义。
了解金属的断裂应变特性可以帮助设计人员选择合适的金属材料,确保工程结构的安全可靠性。
对金属的断裂应变进行研究可以指导材料的加工和处理工艺,提高金属材料的机械性能和使用寿命。
对金属的断裂应变进行研究还可以为材料科学的发展提供重要的参考和理论基础。
金属的断裂应变是金属材料在受到外力作用时产生的变形和断裂现象。
金属的断裂应变受到多种因素的影响,包括金属的性质、结构、外力大小和加载速度等。
了解金属的断裂应变特性对于材料的设计和选用具有重要意义,可以指导工程实践和科学研究。
材料力学性能-第四章-金属的断裂韧度(4)

公式进行判断:
ac
0.25
KIC
2
2021年10月21日 星期四
第四章 金属的断裂韧度
1、高强度钢的脆断倾向 这类钢的强度很高,0.2≥1400MPa,主要用于航 空航天,工作应力较大,但断裂韧度较低,如18Ni马 氏体时效钢,0.2=1700MPa,KIC=78MPa·m1/2,若工 作应力=1250MPa时,利用上述公式可得ac=1mm,这 样小的裂纹在机件焊接过程中很容易产生,用无损检 测方法也容易漏检,所以此类机件脆断几率很大,因 此在选材时在保证不塑性失稳的前提下,尽量选用0.2 较低而KIC较高的材料。
B工艺:/0.2=1400/2100=0.67<0.7,故不必考虑
塑性区修正问题。由公式 KIC YcB a
可得: cB
1 Y
KIC a
Φ 1.1
KIC
a
1.273
47
1.1 3.14 0.001
971MPa
与其工作应力=1400MPa相比, cB< ,即工
作时会产生破裂,说明B工艺是不合格的,这和
2021年10月21日 星期四
第四章 金属的断裂韧度
其0.2=1800MPa,KIC=62MPa·m1/2,焊接后发现焊缝
中有纵向半椭圆裂纹,尺寸为2c=6mm,a=0.9mm,
试问该容器能否在p=6MPa的压力下正常工作?
t
D
解:根据材料力学理 论可以确定该裂纹受 到的垂直拉应力:
pD 61.5 900MPa
趋于缓和,断裂机理不再发生
变化。
2021年10月21日 星期四
第四章 金属的断裂韧度
7.应变速率:应变速率έ具有 KIC
与温度相似的效应。增加έ相 当于降低温度,使KIC下降,
材料力学性能-第四章-金属的断裂韧度(1)
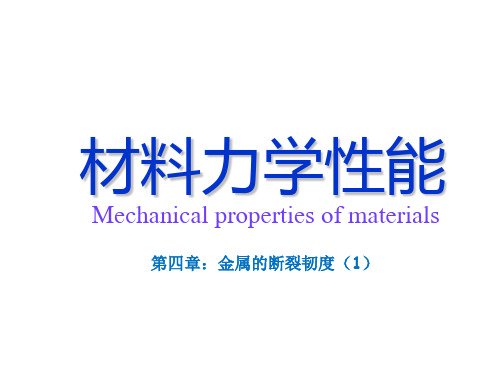
二、应力场强度因子KI和断裂韧度KIC 1、裂纹尖端附近的应力-应变场
由于裂纹扩展是从其尖端开 始进行的,所以首先应该分析裂 纹尖端的应力和应变状态,建立 裂纹扩展的力学条件。如图4-1 所示,假设一有无限大板,其中 有2a长的Ⅰ型裂纹,在无限远处
作用有均匀的拉应力。
图4-1 具有I 型裂纹无限 大板的应力分析
cos
2
1
sin
2
sin
3
2
xy
a
1
2r
cos
2
sin
2
cos3
2
z (x y() 平面应变, 为泊松比)
z 0(平面应力)
2021年12月10日 星期五
第四章 金属的断裂韧度
x方向的位移分量:u
1
E
KI
2r
cos
2
1
2
s in 2
2
y方向的位移分量:
1
E
KI
2r
sin
2
2021年12月10日 星期五
第四章 金属的断裂韧度
应用线弹性力学 y
来分析裂纹尖端附近
的应力、位移场。用
极坐标表示,则各点(r,
裂纹
)的应力、位移分量
可以用下式表示:
y xy x
x
2021年12月10日 星期五
第四章 金属的断裂韧度
x
a
1
2r
cos 2
1
sin
2
sin
3
2
y
a
1
2r
2021年12月10日 星期五
第四章 金属的断裂韧度
断裂力学还证明:上述各式不仅适用于图
材料力学中的断裂与应力分析
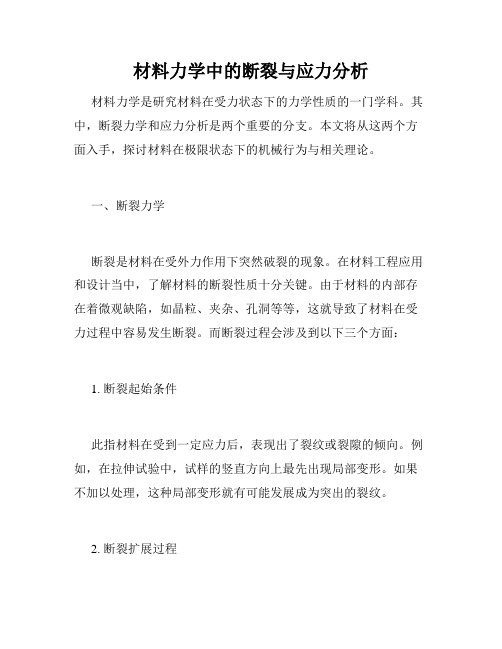
材料力学中的断裂与应力分析材料力学是研究材料在受力状态下的力学性质的一门学科。
其中,断裂力学和应力分析是两个重要的分支。
本文将从这两个方面入手,探讨材料在极限状态下的机械行为与相关理论。
一、断裂力学断裂是材料在受外力作用下突然破裂的现象。
在材料工程应用和设计当中,了解材料的断裂性质十分关键。
由于材料的内部存在着微观缺陷,如晶粒、夹杂、孔洞等等,这就导致了材料在受力过程中容易发生断裂。
而断裂过程会涉及到以下三个方面:1. 断裂起始条件此指材料在受到一定应力后,表现出了裂纹或裂隙的倾向。
例如,在拉伸试验中,试样的竖直方向上最先出现局部变形。
如果不加以处理,这种局部变形就有可能发展成为突出的裂纹。
2. 断裂扩展过程即随着受力的不断加大,裂纹或缺陷会逐渐发展壮大,直到完全破裂。
这个过程叫做断裂扩展。
3. 断裂防止过程这是指在材料的正常工作状态下,为了避免裂纹的产生和扩展,需要采取合理的措施进行防治。
针对这三个方面,在断裂力学中,有若干种理论来描述材料的断裂性质,其中最为常见的有线性弹性断裂力学、弹性塑性断裂力学以及断裂能量理论等等。
需要指出的是,由于材料性质的复杂多变,也并不存在一种全能的理论,针对不同的材料和应变情况,需要结合具体的实验和数据,采用不同的理论进行分析和计算。
二、应力分析应力分析是指采用力学原理和方法,对材料内部所受到的应力状态进行分析和计算。
这个过程中需要解决的问题就是材料内部所受到的力的大小和方向。
根据受力情况的不同,应力的类型也可以分为不同的类别,常见的有以下三种:1. 拉伸应力拉伸应力是在材料受到拉力时对应的应力。
例如,当我们拉伸一个弹簧的时候,就会使其产生拉伸应力。
2. 压缩应力压缩应力则是在材料受到压力时对应的应力。
例如,用重物压在弹簧上,就会使其产生强烈的压缩应力。
3. 剪切应力剪切应力是指当材料受到切向的力时,对应的应力状态。
例如,在修剪纸张或者金属的加工过程中,都会存在这样一种应力状态。
- 1、下载文档前请自行甄别文档内容的完整性,平台不提供额外的编辑、内容补充、找答案等附加服务。
- 2、"仅部分预览"的文档,不可在线预览部分如存在完整性等问题,可反馈申请退款(可完整预览的文档不适用该条件!)。
- 3、如文档侵犯您的权益,请联系客服反馈,我们会尽快为您处理(人工客服工作时间:9:00-18:30)。
工程材料力学期中作业班级成型2班姓名陶帅学号20113650论述金属的断裂一、基本介绍概念:金属材料在外力作用下断裂成两部分的现象。
磨损、腐蚀和断裂是机件的三种主要失效形式,其中以断裂的危害最大。
在应力作用下(有时还兼有热及介的共同作用),金属材料被分成两个或几个部分,称为完全断裂;内部存在裂纹,则为不完全断裂。
实践证明,大多数金属材料的断裂过程都包括裂纹形成与扩展两个阶段。
对于不同的断裂类型,这两个阶段的机理与特征并不相同。
二、断裂的基本类型弹性变形→塑性变形→断裂1,根据材料断裂前产生的宏观塑性变形量的大小来确定断裂类型,可分为韧性断裂和脆性断裂。
2,多晶体金属断裂时,按裂纹扩展路径可以分为穿晶断裂和沿晶断裂。
3,根据应力类型可分为纯剪切断裂和微孔聚集型断裂、解理断裂。
三、具体分析1,韧性断裂韧性断裂是金属材料断裂前产生明显宏观塑性变形的断裂,这种断裂有一个缓慢的撕裂过程,在裂纹扩展过程中不断地消耗能量。
韧性断裂的断裂面一般平行于最大切应力并与主应力成45º角。
用肉眼或放大镜观察时,端口呈纤维状,灰暗色。
纤维状是苏醒变形过程中微裂纹不断扩展和相连造成的,灰暗色则是纤维断口表面对光反射能力很弱所致。
中、低强度钢的光滑圆柱试样在室温下的静拉伸断裂是典型的韧性断裂,其宏观断口呈杯锥形,由纤维区、放射区和剪切唇三个区域组成,即所谓的断口特征三要素。
当光滑圆柱拉伸试样受拉伸力作用,在试验力达到拉伸力-伸长曲线最高点时,便在试样局部区域产生缩颈,同时试样的应力状态也由单向变为三向,且中心轴向应力最大。
在中心三向拉应力作用下,塑性变形难于进行,致使试样中心部分的夹杂物或第二相质点本身碎裂,或使夹杂物质点与基体界面脱离而形成微孔。
微孔不断长大和聚合就形成显微裂纹。
早期形成的显微裂纹,其端部产生较大塑性变形,且集中于极窄的高变形带内。
这些剪切变形带从宏观上看大致与径向呈50º~60º角。
新的微孔就在变形带内成核、长大和聚合,当其与裂纹连接时,裂纹便向前扩展了一段距离。
这样的过程重复进行就形成锯齿形的纤维区。
纤维区所在的平面垂直于拉伸应力方向。
韧性断裂的裂口形成与发展过程均匀拉伸产生细颈在三向拉应力微孔长大合并作用下产生微孔形成小裂口方向断裂裂口沿垂直于拉伸沿max方向扩展接近表面形成杯锥状纤维区中裂纹扩展是很慢的,当其达到临界尺寸后就快速扩展而形成放射区。
放射区是裂纹做快速低能量撕裂形成的。
放射区有放射花样特征。
放射线平行于裂纹扩展方向而垂直于裂纹前端的轮廓线,并逆指向裂纹源。
撕裂时塑性变形量越大,则放射线越粗。
对于几乎不产生塑性变形的极脆材料,放射线消失。
温度降低或再聊强度增加,由于塑性降低,放射线由粗变细乃至消失。
试样拉伸断裂的最后阶段形成杯状或锥状的剪切唇。
剪切唇的表面光滑,与拉伸轴呈45º。
断口三区域的形态、大小和相对位置,因试样形状、尺寸和金属材料的性能以及实验温度、加载速率和受力状态不同而变化。
一般说来,材料强度提高,塑性降低,则放射区比例增大;试样尺寸加大,放射区增大明显,而纤维区变化不大。
综上韧性断裂的特点有:①裂口生成、发展均很慢,断裂前能产生显著的塑性变形。
②断口粗糙,无光泽,呈暗灰色纤维状。
2,脆性断裂脆性断裂是突然发生的断裂,断裂前基本没有任何塑性变形,没有明显征兆,因而危害性极大。
脆性断裂的断裂面一般与正应力垂直,断口平齐而光亮,呈放射状或结晶状。
通常脆性断裂前也产生微量塑性变形。
一般规定光滑拉伸试样的断面收缩率小于5%者为脆性断裂;反之,大于5%者为韧性断裂。
综上:脆性断裂的特点有①裂口生成、发展都很快。
断裂前没有明显的塑性变形。
②断口平整,有金属光泽。
3,穿晶断裂与沿晶断裂穿晶断裂的裂纹穿过晶内--------河流状、舌状花纹沿晶断裂的裂纹沿晶界扩展------------冰糖状、颗粒状穿晶断裂沿晶断裂从宏观上看,穿晶断裂可以是韧性断裂,也可以是脆性断裂;而沿晶断裂则大多数是脆性断裂。
沿晶断裂是由晶界上的一薄层连续或不连续脆性第二相、夹杂物,破坏晶界的连续性所造成,也可能是杂质元素向晶界偏聚引起的。
应力腐蚀、氢脆、回火脆性、淬火裂纹、磨削裂纹等大都是沿晶断裂。
穿晶断裂和沿晶断裂有时可以混合发生。
4,纯剪切断裂与微孔聚集型断裂、解理断裂剪切断裂是金属材料在切应力作用下沿滑移面分离而造成的滑移面分离断裂,其中又分为滑断(纯剪切断裂)和微孔聚集型断裂。
纯金属尤其是单晶体金属常产生纯剪切断裂,其断口呈锋利的契形或刀尖形。
这是纯粹由滑移流变所造成的断裂。
微孔聚集型断裂是通过微孔形核、长大聚合而导致材料分离的。
解理断裂是金属材料在一定条件下,当外加正应力达到一定数值后,以极快速率沿一定晶体学平面产生的穿晶断裂,因与大理石断裂类似,故称此种晶体学平面为解理面。
解理面一般是低指数晶面或表面能最低的晶面。
通常解理断裂总是脆性断裂,但有时在解理断裂前也显示一定的塑性变形。
四、断裂强度1,理论断裂强度概念:将晶体的两个原子面沿垂直于外力方向拉断所需的应力。
假设一完整晶体受拉应力作用后,原子间结合力与原子间位移的关系曲线如图:曲线上的最大值m σ即代表晶体在弹性状态下的最大结合力--------理论断裂强度作为一级近似,该曲线可用正弦曲线表示λπσσx2sin m =式中 λ-------正弦曲线的波长x-------原子间位移如果原子位移很小,则λπλπxx22sin ≈,于是 λπσσx m 2=当原子间位移很小时,根据胡克定律0a Ex E ==εσ式中 ε---------弹性应变0a ---------原子间平衡距离(晶格常数)合并上述二式,消去x 得02a E m πλσ=晶体脆性断裂时消耗的功用来供给形成两个表面所需之表面能。
设裂纹面上单位面积的表面能为s γ。
形成单位裂纹表面外力所作的功,应为σ-x 曲线下所包围的面积,即⎰==2002sin λπλσλπσm m dx x U这个功应等于表面能s γ的两倍(断裂时形成两个新表面),即s m γπλσ2= 或 m s σπγλ2=两式合并,消去λ得 210⎪⎪⎭⎫ ⎝⎛=a E s m γσ这就是理想晶体脆性(解理)断裂的理论断裂强度。
由式可见,晶体弹性模量愈大、表面能愈大、原子间距愈小,即结合愈紧密,则理论断裂强度就愈大。
附:断裂强度的裂纹理论(格雷菲斯裂纹理论)假设:在实际晶体中存在各种缺陷(微裂口),在外力作用下,缺陷端部产生很大的应力集中,在平均应力未达到m σ时,缺陷处的应力集中已超过m σ,使裂口得以逐步发展,结果导致实际断裂强度大为下降。
格雷菲斯公式:212⎪⎭⎫ ⎝⎛=a E s c πγσc σ即为有裂纹物体的断裂强度(实际断裂强度)。
其表明,在脆性材料中,裂纹扩展所需之盈利c σ反比于裂纹半长的平方根。
格雷菲斯认为,对于一定尺寸的裂口存在一个临界应力值c σ当σ<c σ时,裂口不能扩大当σ>c σ时,裂口迅速扩大,导致断裂格雷菲斯理论是根据热力学原理得出断裂发生的必要条件,但这并不意味着事实上一定要断裂。
裂纹自动扩展的充分条件是其尖端应力要等于或大于理论断裂强度m σ。
设材料中自然裂纹尖端曲率半径为ρ,根据弹性应力集中系数计算式,在此条件下裂纹尖端的最大应力为2121max 221⎪⎪⎭⎫ ⎝⎛≈⎥⎥⎥⎦⎤⎢⎢⎢⎣⎡⎪⎪⎭⎫ ⎝⎛+=ρσρσσa a 式中 σ--------名义拉应力。
由式可见,max σ随名义应力增大而增大,当max σ达到m σ时,断裂开始(裂纹扩展)。
此时max σ=m σ,即21021a 2⎪⎪⎭⎫ ⎝⎛=⎪⎪⎭⎫ ⎝⎛a E s γρσ所以,断裂时的名义断裂应力为210c 4⎪⎪⎭⎫ ⎝⎛=aa E s ργσ如果裂纹很尖,其尖端曲率半径小到原子面见距离0a 那样的尺寸,则上式为21c 4⎪⎭⎫ ⎝⎛=a E s γσ必须指出,格雷菲斯对长为2a 的中心穿透裂纹计算所得的断裂应力公式,对长为a 的表面半椭圆裂纹也是适用的,对于后一种裂纹,式中的a 就是裂纹长度。
格雷菲斯只适用于脆性固体,如玻璃、金刚石等,也就是只适用于那些裂纹尖端塑性变形可以忽略的情况。
格雷菲斯理论的前提是,承认时间金属材料中已经存在裂纹,不涉及裂纹的来源问题。
裂纹可能是原材料在冶炼中或工件在铸、焊、热处理等加工过程中产生的;也可能是材料在受载过程中因塑性变形诱发而产生的。
该理论的不完善性:未能反映塑性变形在断裂中的作用Griffith-Orowan 修正公式:2121⎪⎪⎭⎫ ⎝⎛≈⎪⎪⎭⎫ ⎝⎛+=c E c E p p c γγγσ γρ :裂缝扩展时单位面积所需的塑性功γ<<p γ , γ可忽略不计 五、裂口形核机理基本思想:位错理论在外力作用下,刃型位错的合并可构成裂口的胚芽几种具体机理:1.位错塞积机理位错沿某一滑移面移动受阻,在障碍物前塞积,产生极大的应力集中,形成裂口。
2.位错反应机理二位错发生反应生成不易移动的新位错,使位错塞积,产生大的应力集中,形成裂口3.位错消毁机理在两个滑移面间距h<10个原子层的滑移面上,有着不同号的刃型位错,在切应力作用下,它们相遇、相消,产生孔穴,剩余的同号刃型位错进入穴中,造成严重的应力集中,形成裂口。
4.位错墙侧移机理由于位错墙一部分侧移,使滑移面产生弯折,形成裂口。
结论:刃型位错合并、堆积→应力集中→断裂源→达到σc条件→裂口扩展→脆断六、塑性加工中金属的断裂1,镦粗时的侧面开裂产生原因Ⅲ区鼓形处受有环向拉应力作用T℃过高,晶界强度减弱,易沿晶界拉裂裂口⊥σ环,如图(a)T℃较低,穿晶切断,沿τmax 断裂裂口与σ环成45°角,如图(b),2,锻压延伸时的内部裂纹1)平锤头锻压方坯时产生X形内裂产生原因a) 锻压时,对角线方向金属流动发生错动每翻转90°,金属错动方向改变b)铸造组织钢锭中心及对角线是杂质和缺陷聚集的地方,为薄弱环节有柱状晶更易开裂 1c)对角线方向ε最大热效应大,温升高,对角线处易过烧,导致开裂若中心薄弱,裂纹如图c上若角部薄弱,裂纹如图c下2)平锤头锻压圆锭时产生的内裂产生原因锻压圆锭时,相当于压缩厚件。
假若没有外端,则可自由地形成双鼓形,但由于外端的拉齐作用,使工件中心产生附加拉应力。
当翻转90°锻成方坯时,裂纹如图(d),十字形当旋转锻造圆坯时,裂纹如图(e),放射状3)锻压延伸及轧制时产生的内部裂纹产生原因当l/h<0.5时,在断面中心产生纵向拉应力。
4)锻压延伸及轧制时产生的角裂产生原因未及时倒棱,角部温降大,产生拉伸热应力角部变形抗力大,延伸小,产生附加拉应力七、金属材料的脆化现象分两类:(1)在一定温度条件下出现的脆性,温度条件改变后,脆性自行消失,或者在一定温度条件下,经一定时间后出现的脆性。