金属材料-准静态断裂韧性测试的方法
金属断裂韧度测试
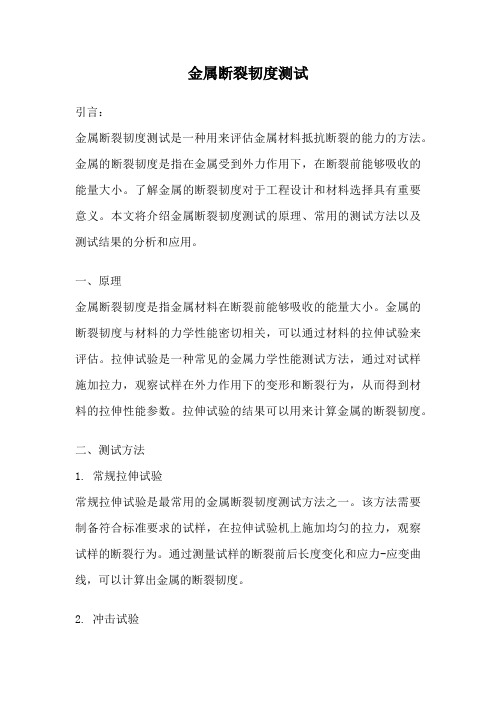
金属断裂韧度测试引言:金属断裂韧度测试是一种用来评估金属材料抵抗断裂的能力的方法。
金属的断裂韧度是指在金属受到外力作用下,在断裂前能够吸收的能量大小。
了解金属的断裂韧度对于工程设计和材料选择具有重要意义。
本文将介绍金属断裂韧度测试的原理、常用的测试方法以及测试结果的分析和应用。
一、原理金属断裂韧度是指金属材料在断裂前能够吸收的能量大小。
金属的断裂韧度与材料的力学性能密切相关,可以通过材料的拉伸试验来评估。
拉伸试验是一种常见的金属力学性能测试方法,通过对试样施加拉力,观察试样在外力作用下的变形和断裂行为,从而得到材料的拉伸性能参数。
拉伸试验的结果可以用来计算金属的断裂韧度。
二、测试方法1. 常规拉伸试验常规拉伸试验是最常用的金属断裂韧度测试方法之一。
该方法需要制备符合标准要求的试样,在拉伸试验机上施加均匀的拉力,观察试样的断裂行为。
通过测量试样的断裂前后长度变化和应力-应变曲线,可以计算出金属的断裂韧度。
2. 冲击试验冲击试验也是一种常用的金属断裂韧度测试方法。
该方法利用冲击试验机对试样施加冲击载荷,观察试样在冲击载荷下的断裂行为。
冲击试验的结果可以通过试样的冲击功吸收能力来评估金属的断裂韧度。
3. 复合试验复合试验是一种结合多种测试方法的金属断裂韧度测试方法。
通过对试样进行拉伸、冲击等多种试验,综合评估金属的断裂韧度。
这种方法可以更全面地了解金属材料的断裂行为,提供更准确的韧度评估。
三、测试结果分析和应用根据金属断裂韧度测试的结果,可以评估金属材料的断裂性能,并为工程设计和材料选择提供依据。
1. 工程设计金属的断裂韧度是衡量金属材料抵抗断裂的能力的重要指标。
对于需要承受大量外力的工程结构,如桥梁、飞机等,需要选择具有较高断裂韧度的金属材料,以确保结构的安全可靠性。
2. 材料选择不同金属材料的断裂韧度不同,根据具体应用需求选择合适的金属材料非常重要。
通过金属断裂韧度测试,可以评估不同材料的断裂韧度,并选择适合的材料。
金属材料表面裂纹拉伸试样断裂韧度试验方法
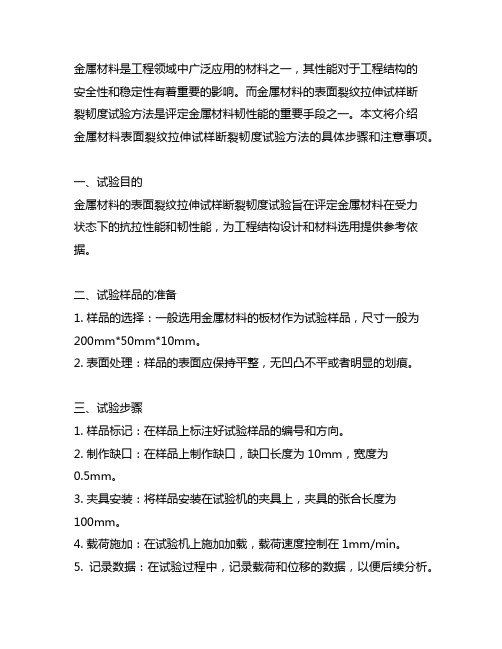
金属材料是工程领域中广泛应用的材料之一,其性能对于工程结构的安全性和稳定性有着重要的影响。
而金属材料的表面裂纹拉伸试样断裂韧度试验方法是评定金属材料韧性能的重要手段之一。
本文将介绍金属材料表面裂纹拉伸试样断裂韧度试验方法的具体步骤和注意事项。
一、试验目的金属材料的表面裂纹拉伸试样断裂韧度试验旨在评定金属材料在受力状态下的抗拉性能和韧性能,为工程结构设计和材料选用提供参考依据。
二、试验样品的准备1. 样品的选择:一般选用金属材料的板材作为试验样品,尺寸一般为200mm*50mm*10mm。
2. 表面处理:样品的表面应保持平整,无凹凸不平或者明显的划痕。
三、试验步骤1. 样品标记:在样品上标注好试验样品的编号和方向。
2. 制作缺口:在样品上制作缺口,缺口长度为10mm,宽度为0.5mm。
3. 夹具安装:将样品安装在试验机的夹具上,夹具的张合长度为100mm。
4. 载荷施加:在试验机上施加加载,载荷速度控制在1mm/min。
5. 记录数据:在试验过程中,记录载荷和位移的数据,以便后续分析。
四、试验注意事项1. 缺口制作:缺口的制作应该尽量避免产生裂纹,可以使用慢速切割或者加工。
2. 夹具安装:夹具的安装要稳固,保证试验过程中的样品不会出现偏移或者松动。
3. 载荷施加:载荷的施加速度要均匀,避免过快或者过慢导致试验结果的偏差。
4. 安全防护:在试验过程中,要保证操作人员的安全,并严格遵守安全操作规程。
五、试验结果分析根据试验数据,可以得到金属材料在受拉状态下的应力-应变曲线,并据此分析金属材料的屈服强度、最大应力、断裂韧性等性能指标。
通过以上试验方法,我们可以准确评定金属材料在受拉状态下的韧性能,并为工程设计和材料选用提供科学依据。
试验过程中需要特别注意安全事项,确保工作人员的安全。
希望本文对金属材料表面裂纹拉伸试样断裂韧度试验方法有所帮助。
六、试验结果分析通过表面裂纹拉伸试样断裂韧度试验得到的金属材料在受拉状态下的应力-应变曲线,可以为工程设计和材料选择提供重要参考信息。
金属材料的断裂韧性测试
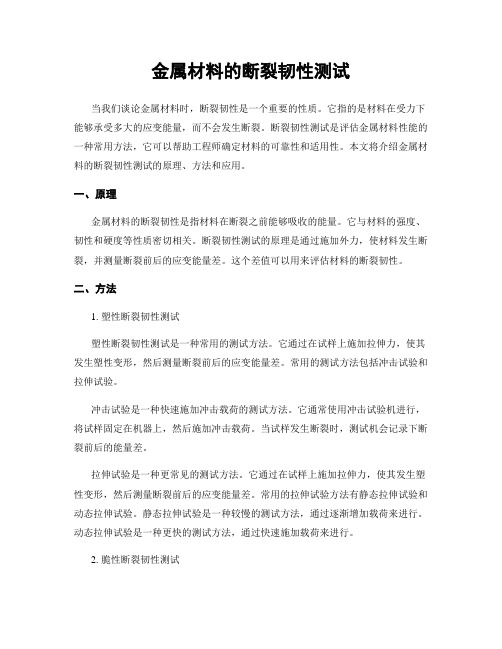
金属材料的断裂韧性测试当我们谈论金属材料时,断裂韧性是一个重要的性质。
它指的是材料在受力下能够承受多大的应变能量,而不会发生断裂。
断裂韧性测试是评估金属材料性能的一种常用方法,它可以帮助工程师确定材料的可靠性和适用性。
本文将介绍金属材料的断裂韧性测试的原理、方法和应用。
一、原理金属材料的断裂韧性是指材料在断裂之前能够吸收的能量。
它与材料的强度、韧性和硬度等性质密切相关。
断裂韧性测试的原理是通过施加外力,使材料发生断裂,并测量断裂前后的应变能量差。
这个差值可以用来评估材料的断裂韧性。
二、方法1. 塑性断裂韧性测试塑性断裂韧性测试是一种常用的测试方法。
它通过在试样上施加拉伸力,使其发生塑性变形,然后测量断裂前后的应变能量差。
常用的测试方法包括冲击试验和拉伸试验。
冲击试验是一种快速施加冲击载荷的测试方法。
它通常使用冲击试验机进行,将试样固定在机器上,然后施加冲击载荷。
当试样发生断裂时,测试机会记录下断裂前后的能量差。
拉伸试验是一种更常见的测试方法。
它通过在试样上施加拉伸力,使其发生塑性变形,然后测量断裂前后的应变能量差。
常用的拉伸试验方法有静态拉伸试验和动态拉伸试验。
静态拉伸试验是一种较慢的测试方法,通过逐渐增加载荷来进行。
动态拉伸试验是一种更快的测试方法,通过快速施加载荷来进行。
2. 脆性断裂韧性测试脆性断裂韧性测试是一种针对脆性材料的测试方法。
脆性材料在受力下容易发生断裂,因此需要特殊的测试方法来评估其断裂韧性。
常用的测试方法包括冲击试验和压缩试验。
冲击试验是一种常用的测试方法,通过在试样上施加冲击载荷来评估脆性材料的断裂韧性。
冲击试验机将试样固定在机器上,然后施加冲击载荷。
当试样发生断裂时,测试机会记录下断裂前后的能量差。
压缩试验是一种较少使用的测试方法,通过在试样上施加压缩载荷来评估脆性材料的断裂韧性。
压缩试验机将试样固定在机器上,然后施加压缩载荷。
当试样发生断裂时,测试机会记录下断裂前后的能量差。
金属行业金属材料强度与韧性的测试方法
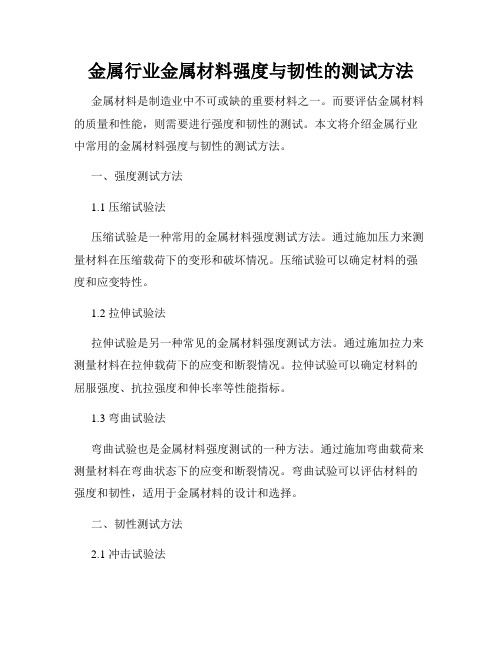
金属行业金属材料强度与韧性的测试方法金属材料是制造业中不可或缺的重要材料之一。
而要评估金属材料的质量和性能,则需要进行强度和韧性的测试。
本文将介绍金属行业中常用的金属材料强度与韧性的测试方法。
一、强度测试方法1.1 压缩试验法压缩试验是一种常用的金属材料强度测试方法。
通过施加压力来测量材料在压缩载荷下的变形和破坏情况。
压缩试验可以确定材料的强度和应变特性。
1.2 拉伸试验法拉伸试验是另一种常见的金属材料强度测试方法。
通过施加拉力来测量材料在拉伸载荷下的应变和断裂情况。
拉伸试验可以确定材料的屈服强度、抗拉强度和伸长率等性能指标。
1.3 弯曲试验法弯曲试验也是金属材料强度测试的一种方法。
通过施加弯曲载荷来测量材料在弯曲状态下的应变和断裂情况。
弯曲试验可以评估材料的强度和韧性,适用于金属材料的设计和选择。
二、韧性测试方法2.1 冲击试验法冲击试验是评估金属材料韧性的重要方法之一。
冲击试验通常使用冲击机或差动式冲击试验机进行,通过使试样在冲击载荷下破裂,测量其吸收能量和断裂机理,进而评估材料的韧性。
2.2 缺口冲击试验法缺口冲击试验是对金属材料韧性评估的一种更具挑战性的方法。
通过在试样上制造不同形状和尺寸的缺口,并在冲击试验中测量材料的断裂韧性。
该方法对材料的抗缺口性能具有较高的要求,能够更准确地评估材料的韧性。
2.3 塑性断裂韧性测试法塑性断裂韧性测试法是用于评估金属材料韧性的一种方法。
通过应用加载模式和观察材料在加载过程中的塑性变形和破裂行为,评估其在低温和高应变速率下的韧性。
该方法可用于评估材料在工业事故中的断裂行为和应对能力。
三、测试流程金属材料强度与韧性的测试一般遵循以下流程:3.1 试样制备根据不同的测试方法和标准,选择合适的试样尺寸和形状,然后使用相应的加工设备对试样进行制备。
3.2 试验设备设置根据测试要求,将相应的试样放置在试验设备上,并进行必要的调校和校准。
3.3 施加载荷按照测试要求,在试样上施加相应的载荷,如压力、拉力或弯曲力等。
金属材料断裂韧性测试与数值模拟

金属材料断裂韧性测试与数值模拟金属材料在工程领域中扮演着重要的角色,其力学性能对结构的可靠性和安全性具有至关重要的影响。
其中,金属材料的断裂韧性是一个重要的性能指标,它衡量了材料在受到外力作用下抵抗破坏的能力。
为了准确评估金属材料的断裂韧性,实验测试与数值模拟成为了研究的重点。
实验测试是评估金属材料断裂韧性最主要的手段之一。
常用的实验方法包括冲击试验、拉伸试验和压缩试验等。
冲击试验通过施加冲击载荷在极短时间内造成材料断裂,从而实现韧性的测定。
拉伸试验则通过施加拉伸载荷,观察金属材料在断裂前的塑性变形行为来评估其韧性。
压缩试验则利用压缩载荷作用在金属材料上,观察材料在破坏前的强度和塑性变形能力来判断其韧性。
通过这些实验,可以获得金属材料的断裂韧性参数,如断裂韧性KIC值和断裂韧性强度σIc等。
然而,实验测试存在一些局限性。
首先,实验测试通常需要大量的时间、资源和材料。
其次,由于金属材料的力学性能受到多种因素的影响,实验测试结果的可靠性和重复性较差。
此外,实验测试也存在一定的安全隐患,特别是在冲击试验中。
为了克服实验测试的局限性,数值模拟成为了评估金属材料断裂韧性的重要工具。
数值模拟可以通过建立材料力学行为的数学模型,模拟实际工况下的应力应变分布和断裂过程。
常用的数值模拟方法包括有限元法、位错动力学模拟和分子动力学模拟等。
有限元法是一种广泛应用的数值模拟方法,它通过将结构分割成有限个小单元,在每个单元内建立与实际结构相对应的数学模型,通过求解节点的位移和应力分布来模拟结构的力学行为。
在金属材料断裂韧性测试中,有限元法可以模拟金属材料在受到外力作用时的应力和应变分布,进而评估其断裂韧性。
位错动力学模拟和分子动力学模拟则更注重于材料的微观行为,可以研究金属材料中位错的运动和相互作用,从而揭示其断裂韧性的微观机制。
数值模拟的优点在于可以对实验难以观测到的细节进行研究,并且可以提供更全面、更详细的信息。
然而,数值模拟的可靠性和准确性也受到多种因素的限制,如模型的准确性、模拟过程中的边界条件的确定等。
(完整版)断裂韧性KIC测试试验
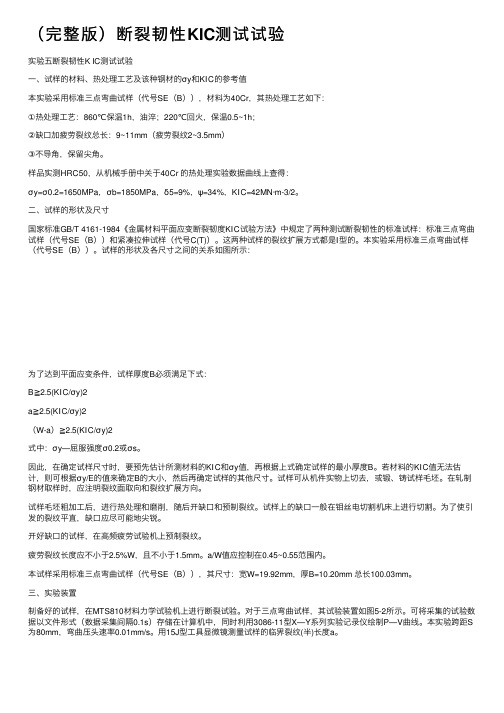
(完整版)断裂韧性KIC测试试验实验五断裂韧性K IC测试试验⼀、试样的材料、热处理⼯艺及该种钢材的σy和KⅠC的参考值本实验采⽤标准三点弯曲试样(代号SE(B)),材料为40Cr,其热处理⼯艺如下:①热处理⼯艺:860℃保温1h,油淬;220℃回⽕,保温0.5~1h;②缺⼝加疲劳裂纹总长:9~11mm(疲劳裂纹2~3.5mm)③不导⾓,保留尖⾓。
样品实测HRC50,从机械⼿册中关于40Cr 的热处理实验数据曲线上查得:σy=σ0.2=1650MPa,σb=1850MPa,δ5=9%,ψ=34%,KⅠC=42MN·m-3/2。
⼆、试样的形状及尺⼨国家标准GB/T 4161-1984《⾦属材料平⾯应变断裂韧度KⅠC试验⽅法》中规定了两种测试断裂韧性的标准试样:标准三点弯曲试样(代号SE(B))和紧凑拉伸试样(代号C(T))。
这两种试样的裂纹扩展⽅式都是Ⅰ型的。
本实验采⽤标准三点弯曲试样(代号SE(B))。
试样的形状及各尺⼨之间的关系如图所⽰:为了达到平⾯应变条件,试样厚度B必须满⾜下式:B≧2.5(KⅠC/σy)2a≧2.5(KⅠC/σy)2(W-a)≧2.5(KⅠC/σy)2式中:σy—屈服强度σ0.2或σs。
因此,在确定试样尺⼨时,要预先估计所测材料的KⅠC和σy值,再根据上式确定试样的最⼩厚度B。
若材料的KⅠC值⽆法估计,则可根据σy/E的值来确定B的⼤⼩,然后再确定试样的其他尺⼨。
试样可从机件实物上切去,或锻、铸试样⽑坯。
在轧制钢材取样时,应注明裂纹⾯取向和裂纹扩展⽅向。
试样⽑坯粗加⼯后,进⾏热处理和磨削,随后开缺⼝和预制裂纹。
试样上的缺⼝⼀般在钼丝电切割机床上进⾏切割。
为了使引发的裂纹平直,缺⼝应尽可能地尖锐。
开好缺⼝的试样,在⾼频疲劳试验机上预制裂纹。
疲劳裂纹长度应不⼩于2.5%W,且不⼩于1.5mm。
a/W值应控制在0.45~0.55范围内。
本试样采⽤标准三点弯曲试样(代号SE(B)),其尺⼨:宽W=19.92mm,厚B=10.20mm 总长100.03mm。
材料力学中的断裂韧性研究
材料力学中的断裂韧性研究材料力学是研究材料在外部作用下的变形和破坏行为的学科。
在材料力学中,断裂韧性是一个非常重要的指标,它描述了材料在应力作用下逐渐破坏的能力。
断裂韧性是材料设计和制造的重要依据之一,因此研究断裂韧性具有重要的科学意义和应用价值。
一、断裂韧性的概念和测量方法断裂韧性是指材料在应力作用下逐渐破坏的能力。
通常情况下,材料受到外部应力作用时会发生塑性变形,逐渐形成裂纹,最终导致断裂。
断裂韧性与材料的断裂强度不同,它反映了材料的抗拉断性能,而断裂强度只是材料拉伸断裂时的强度极限。
断裂韧性的测量方法比较复杂,通常有以下几种常见方法:1. K_IC(裂纹扩展应力强度因子)法:是一种直接测量断裂韧性的方法,通过对裂纹扩展的速率和裂纹尖端周围应力场的分析,可以确定材料的断裂韧性。
2. TCT(脆性破坏温度)法:该方法可以得到材料在低温下的断裂韧性,通常用于评估金属材料或复合材料的热应力断裂韧性。
3. CTOD(裂纹口开度位移)法:CTOD法是一种非常有效的测量断裂韧性的方法,通过测量裂纹口的开度位移来确定材料的断裂韧性。
二、断裂韧性的影响因素材料的断裂韧性是由多种因素综合作用所决定的,包括材料本身的组织结构、晶粒度、温度、应力状态等。
其中,比较重要的因素有以下几个:1.材料微观结构:材料的微观结构决定了材料的强度和塑性性能,因此也会影响断裂韧性。
晶粒尺寸、晶格位错、晶界等因素都会对材料的断裂韧性产生影响。
2.温度:温度对材料的断裂韧性影响很大,一般来说低温下材料的断裂韧性更高。
这是因为低温下材料的塑性变形能力较差,裂纹扩展速率较慢,因此材料的断裂韧性更高。
3.应力状态:不同的应力状态对材料的断裂韧性也有影响。
在拉伸应力状态下,裂纹的扩展方向往往与应力作用方向垂直,这种情况下材料的断裂韧性最高。
三、断裂韧性的研究现状和发展趋势作为材料力学的一个重要分支,断裂力学已经成为一个非常成熟的学科。
对于断裂韧性的研究也已经进行了很多年。
92192-断裂韧度实验-4
疲劳试验
疲劳试验
尺寸测量 厚度:从疲劳裂纹顶端至试样的无缺口边,沿
着预期的裂纹扩展线,在三个等间隔位置处进 行测量,取均值。 宽度:从缺口外边缘到相对的试件侧面,在缺 口附近三个位置上进行测量,然后减去缺口边 至加载孔中心线的距离,取均值。
疲劳试验
疲劳裂纹预制: 裂纹要求:
a= a0+af = 0.45W ~0.55W af≥1.3mm 且 af≥0.025W
Instron8801 电液伺服疲劳试验机
读数精度
为1mm
裂纹测量设备
疲劳试验
JX13C 万能工具显微镜
试验件
0.8
2-0.25W +0.05 0 0.002W A 0.002W A
疲劳试验
0.002W A
0.6W±0.005W 0.275W±0.005W
0.275W±0.005W
A
0.6W±0.005W
(a WW
)(0.886
4.64a
/W
13 .32 a 2 (1 a /W
/W )3/ 2
2
14.72a3
/W
3
5.6a 4
/W
4
)
a/W = 0.450~0.550所对应的f(a/W)值可查表
相关研究
疲劳试验
✓ 试样
疲劳试验
作业:
加工试件
开始撰写实验报告
疲劳试验
同时采用目测法和柔度法进行裂纹 长度的测量。
疲劳试验
疲劳裂纹预制: 载荷给定:采用载荷控制,正弦波加载
预制开始时,最大疲劳载荷应使得 应力强度因子的最大值不超过80%KIc。
应力比R取-1- 0.1之间。 预制循环数在104-106之间。 当裂纹扩到标线位置时,降低最大 载荷,使得应力强度因子 Kfmax<60%Kq, 同时Kfmax/E < 0.01mm1/2
断裂韧性实验指导书
实验一系列冲击实验一、实验目的:1.学习低温温度下金属冲击韧性测定的操作方法;2.测定温度对金属材料冲击韧性的影响,掌握确定金属材料的脆性转化温度T k的方法。
二、实验原理:本实验按冲击试验的最新国家标准GB/T229-1994进行。
用规定高度的摆锤对处于简支粱状态的缺口试样进行一次性打击,可测量试样折断时的冲击吸收功A k。
(A k除以试样缺口处截面积得冲击韧性值a k)。
为了表明材料低温脆性倾向大小,常用方法就是测定材料的“韧脆转化温度”。
一般使用标准夏比V型缺口冲击试样测定。
根据不同温度下的冲击试验结果,以冲击吸收功或脆性断面率为纵坐标,以试验温度为横坐标绘制曲线见图1。
韧脆转变温度确定方法:a. 冲击吸收功-温度曲线上平台与下平台区间规定百分数(n)所对应的温度,用ETT n表示。
如冲击吸收功上平台与下平台区间50%所对应的温度记为ETT50(℃)。
b. 脆性断面率-温度曲线中规定脆性断面率(n)所对应的温度,用FTT n 表示。
如脆性断面率为50%所对应的温度记为FTT50(℃)。
用不同方法测定的韧脆转变温度不能相互比较。
三、在不同温度下作冲击试验,可以得出典型的A k-T曲线和脆性断面率曲线(见图1)。
冲击吸收功曲线可近似的分为三部分:(1)温度较低,冲击值变化不大,平行横坐标的低A k值部分,称下平台,对应断口为脆性的结晶状;(2)温度较高,高冲击值部分,称为上平台,对应断口为韧性的纤维状;(3)中间部分A k值在上下平台的范围内,变化较大,且分散,对应断口为混合状(结晶状+纤维状断口)。
脆性断面率曲线与上述曲线相反,(1)温度较低,断面率高的部分,断口为脆性的结晶状;(2)温度较高,断面率低的部分,断口为韧性的纤维状;(3)中间部分在室温以下温度范围内,断口为混合状(结晶状+纤维状断口)。
根据图1的两条曲线,可以定出冲击吸收功上平台与下平台区间50%的韧脆转变温度ETT50(℃)和脆性断面率为50%的韧脆转变温度FTT50(℃)。
材料断裂实验中的断裂韧性测定和分析
材料断裂实验中的断裂韧性测定和分析材料断裂是工程领域中一个重要的研究课题,因为它直接关系到材料的可靠性和安全性。
在材料断裂实验中,断裂韧性是一个重要的参数,它可以反映材料抵抗断裂的能力。
本文将介绍材料断裂实验中的断裂韧性测定方法和分析过程。
一、断裂韧性的定义和意义断裂韧性是材料在断裂过程中吸收的能量与断裂面积的比值。
它可以反映材料在受力过程中的变形能力和抗断裂能力。
断裂韧性是评价材料抗断裂能力的重要指标,对于工程结构的设计和材料的选择具有重要意义。
二、断裂韧性的测定方法1. 断裂韧性的静态测定方法静态测定方法是通过对材料进行拉伸试验或冲击试验来测定断裂韧性。
拉伸试验是最常用的测定断裂韧性的方法之一。
在拉伸试验中,通过测量材料的应力-应变曲线,可以计算出断裂韧性。
冲击试验是另一种常用的测定断裂韧性的方法。
在冲击试验中,通过测量材料在冲击载荷下的断裂能量,可以计算出断裂韧性。
2. 断裂韧性的动态测定方法动态测定方法是通过对材料进行高速冲击试验或动态加载试验来测定断裂韧性。
高速冲击试验是一种常用的动态测定断裂韧性的方法。
在高速冲击试验中,通过测量材料在高速冲击载荷下的断裂能量,可以计算出断裂韧性。
动态加载试验是另一种常用的动态测定断裂韧性的方法。
在动态加载试验中,通过对材料进行动态加载,观察材料的断裂行为,可以计算出断裂韧性。
三、断裂韧性的分析过程断裂韧性的分析过程主要包括断裂面观察和断裂韧性计算两个步骤。
1. 断裂面观察断裂面观察是通过对材料的断裂面进行显微镜观察,来了解材料的断裂机制和断裂特征。
断裂面观察可以帮助我们判断材料的断裂方式是韧性断裂还是脆性断裂,以及了解断裂过程中的微观损伤和裂纹扩展情况。
2. 断裂韧性计算断裂韧性的计算是通过测量材料在断裂过程中吸收的能量和断裂面积,来计算出断裂韧性。
在静态测定方法中,可以通过拉伸试验或冲击试验得到断裂韧性的计算结果。
在动态测定方法中,可以通过高速冲击试验或动态加载试验得到断裂韧性的计算结果。
- 1、下载文档前请自行甄别文档内容的完整性,平台不提供额外的编辑、内容补充、找答案等附加服务。
- 2、"仅部分预览"的文档,不可在线预览部分如存在完整性等问题,可反馈申请退款(可完整预览的文档不适用该条件!)。
- 3、如文档侵犯您的权益,请联系客服反馈,我们会尽快为您处理(人工客服工作时间:9:00-18:30)。
ICS 77.040.10
Ref. No. ISO 12135:2002/Cor.1:2008(E)
© ISO 2008 – All rights reserved Published in Switzerland
INTERNATIONAL STANDARD ISO 12135:2002 TECHNICAL CORRIGENDUM 1
Published 2008-06-01
INTERNATIONAL ORGANIZATION FOR STANDARDIZATION • МЕЖДУНАРОДНАЯ ОРГАНИЗАЦИЯ ПО СТАНДАРТИЗАЦИИ • ORGANISATION INTERNATIONALE DE NORMALISATION
Metallic materials — Unified method of test for the determination of quasistatic fracture toughness
TECHNICAL CORRIGENDUM 1
Matériaux métalliques — Méthode unifiée d'essai pour la détermination de la ténacité quasi statique
RECTIFICATIF TECHNIQUE 1
Technical Corrigendum 1 to ISO 12135:2002 was prepared by Technical Committee ISO/TC 164, Mechanical testing of metals , Subcommittee SC 4, Toughness testing — Fracture (F), Pendulum (P), Tear (T).
Page 1, Clause 2
Replace the reference to ISO 7500-1:— with the following:
ISO 7500-1, Metallic materials — Verification of static uniaxial testing machines — Part 1: Tension/compression testing machines — Verification and calibration of the force-measuring system Delete the reference to Footnote 1) and the footnote “To be published. (Revision of ISO 7500-1:1999)”. Page 13, Figure 6 Add “(not to scale)”.
Move the note from under the title of Figure 6 to above the title. Page 16, Figure 9, Footnote d) Replace “on” with “or” to give
d
Edge of bend or straight compact specimen.
ISO 12135:2002/Cor.1:2008(E)
Page 21, Figure 11
In NOTE 3, replace “displacement” with “displacements” to give:
NOTE 3 For specimens showing large displacements, clevis hole dimensions shall be enlarged to the values shown in brackets.
Exchange the texts of footnotes a) and b) to give:
©ISO 2008 – All rights reserved3
ISO 12135:2002/Cor.1:2008(E)
Page 26, 5.8.2, list items
Replace c), d), e) and f) with a), b, c) and d).
Page 28, 6.1, list item a)
Place a comma between “determinations” and “or”.
Page 29, 2nd paragraph
Change “1,1” to “1,10” (in two places), to give:
The maximum force F max (see Figure 16) sustained by the specimen is recorded and the ratio F max/F Q calculated. If that ratio exceeds 1,10, K Q is considered to bear an insufficient relation to K lc and the record is then interpreted in accordance with 6.3 or 6.4. If F max/F Q is less than 1,10, K Q is calculated directly in accordance with 6.2.3.
Page 47, A.1.1, 2nd sentence
Delete “of a” to give:
An example SEM photograph is shown in Figure A.1.
4 ©ISO 2008 – All rights reserved
ISO 12135:2002/Cor.1:2008(E)
© ISO 2008 – All rights reserved
5
a b c
d e f g h Figure A.2 — Determination of ∆a SZW
ISO 12135:2002/Cor.1:2008(E)
Page 69, Figure E.2
Replace Figure E.2 with the following.
Key
1 flex bar
2 strain gauges
Figure E.2 — Diagram of three-point band static test arrangement showing details
of flex bar and specimen reports
Page 68, 2nd paragraph
Replace “[10]” with “(see Reference [10])”.
Page 69, 1st paragraph
Replace “[11]” with “(see Reference [11])”.
Page 71, NOTE 2
Replace “[12]” with “(see Reference [12])”.
Page 72, 1st paragraph
Replace “[13]” with “(see Reference [13])”.
Page 75, G.2, list items a), b) and c)
Replace “[14-16]” with “(see References [14] to [16])”.
6 ©ISO 2008 – All rights reserved
ISO 12135:2002/Cor.1:2008(E)
Page 77, H.1
In the first paragraph, replace “[17]” with “(see Reference [17])”.
In the second paragraph, replace “[18-26]” with “(see References [18] to [26])”.
In the third paragraph, replace “[27-38]” with “(see References [27] to [38])”.
Page 77, H.2, first paragraph
Replace “[18-26]” with “(see References [18] to [26])”.
Page 78, H.4.1, 1st paragraph
Replace “[22]” with “(see Reference [22])”.
Page 91, Annex I, title line
Replace “[39]” with “(see Reference [39])”.
©ISO 2008 – All rights reserved7。