铝合金高效高速数控加工机床新成果
精密高效电加工关键技术取得重大突破---国家863计划、数控机床重大专项电加工课题实施成果综述

组, 在科 技部 、 工信 部重 大专项 办公 室 的具 体领 导及 指导下 , 在课 题责 任 单位 及 主 要 参加 单 位 的 大力 支 持下 , 大批 专家 及 工程 技 术 人 员 围绕 课 题 的 目标 一 任务 , 经过 不懈努 力 , 同攻 关 , 电加 工 领域 关 键 协 在
摘要 : 通过 对 近年 来 电加 工领 域 实施 国 家高技 术研 究 发展 计 划 (6 8 3计 划) 国 家科技 重 大专 和 项“ 高档数 控机床 与基 础制 造装备 ” 况的 综述 , 全 面地 介 绍 了近年 来 我 国电加 工领 域 突破 的 一 情 较 些 关键技 术及取 得 的成果 , 阐述 了这 些项 目实施所 带 来的重 大作 用和意 义。
YeJ n u
(S zo l t mahnn c i o l eerh Is tt C . L d S zo 0 , hn uh uEe r ciigMahn T o R sac n t ue o , t , uh u2 C ia) co e i 1 1 5 1
Ke r s o —r dt n lma hnn EDM ; 6 ln; inf a ts eils bet n NC ma ywo d :n n ta i o a i c iig; 8 3 pa sg i c n p ca u jcs i — i
c i s ke e h o o y; r t h ne ; y tc n l g fui
20 0 9年 初 , 国家 科 技 重 大专 项 “ 档 数 控 机 床 与 基 高 础制 造装备 ” 以下 简称 数 控 机床 重 大 专项 ) 种 加 ( 特
工有关 课题 正式 立 项 招标 , 中有 关 电加 工 方 面 的 其
高速切削加工实验报告

高速切削加工实验报告1. 引言高速切削加工是一种先进的制造技术,通过提高切削速度和优化刀具材料与结构,可以加快加工速度、提高加工效率和加工精度。
本实验旨在通过对铝合金进行高速切削加工,探究加工参数对加工效果的影响,为实际加工提供依据。
2. 实验方法2.1 材料准备选取工业常用的6061铝合金作为实验材料,该材料具有良好的机械性能和加工性能。
2.2 实验设备* 高速切削机床:使用一台高速切削机床进行实验,该设备能够实现高速切削并准确控制加工参数。
* 刀具:选用合适的高速切削刀具,具备良好的切削性能和刚性。
* 冷却液:使用专用的冷却液,避免材料在高速切削过程中引起过热。
* 测量仪器:使用数控测量仪器对实验结果进行测量和记录,保证数据的准确性。
2.3 实验步骤1. 将铝合金工件固定在高速切削机床上,并确认其位置和稳定性。
2. 选择合适的切削刀具,并调整好刀具安装参数。
3. 设置高速切削加工参数,如切削速度、进给速度、切削深度等。
4. 启动高速切削机床,进行加工。
5. 实时记录切削过程中的数据,如工件表面温度、切削力、切削动力等。
6. 完成加工后,对工件进行后续处理,如去毛刺、抛光等。
7. 使用数控测量仪器对工件进行尺寸测量,并记录测量结果。
3. 实验结果3.1 加工参数对加工效果的影响在实验中,我们选取了不同的切削速度、进给速度和切削深度进行加工,并记录了加工过程中的数据和加工效果。
图1 展示了不同切削速度下的加工效果。
可以观察到,随着切削速度的增加,加工效率明显提高,同时工件表面质量也有所改善。
然而,当切削速度达到一定范围时,过高的切削速度会导致材料过热和刀具磨损的加剧,从而降低切削质量。
图2 展示了不同进给速度下的加工效果。
可以发现,在一定范围内,增加进给速度可以提高加工效率,但过高的进给速度会导致切屑堆积、刀具磨损和精度下降。
图3 展示了不同切削深度下的加工效果。
可以看到,增加切削深度可以在一定程度上提高加工效率,但同时也会增加材料的变形和切削力,从而降低加工质量。
动车组铝合金车体大部件数控加工方法

某 公 司生产 的时速 3 5 0 k m / h“ 和谐 号 ”动 车组
现加工尺寸 4 4的 自动补偿 。
是 我国高速铁路运营的主要车型 。动车组车体采用轻 型6 0 0 5 A铝合金挤压材料 焊接 而成 ,外形 呈流线 型 , 降低 了高 速运行 时的空气阻力和噪声 。动车组铝合金 车体 主要 由侧墙 、车顶 、车体 、底架 、地板 等大部件 组成 。车体 大部 件的数 控加工是车体生产线 的关键工 序 ,其加工效率 和加工 质量严 重影响动车组整条生产 线 的生产能力 ,以及动 车组 的运营可靠性。 车体大部件 由 6 0 0 5 A铝合金 挤压 型材焊 接而 成 ,
其显著特点是焊接成型 的大尺 寸 、中空结构 件。唐 车 公司在大型龙 门式五坐标加工 中心 F o o k e上进行车体
1 侧墙 窗 口自动测量
由于侧墙焊接工艺 1 3 趋成 熟且稳定 ,窗 口表 面的 平 整度也 越来越 好 ,但侧墙上 表面还是存在一定 的平 整度误差 ,侧墙 全长方 向的平整度 不会超 过 1 5 m m, 同时侧墙 在 方 向存在一定的挠度 ,因此需要 在窗 口 的轮廓上测 量上 表 面高度 值 ,在 c型槽 上测 量侧 向 偏差 ,以实 现对 窗 口外 轮廓 的等厚度 ( 7 m m 余量 ) 加工 的 自动补偿 和窗 口绕 z 轴的旋 转。 根据侧墙 加工 的工 装夹 具 在机 床 坐标 系 中的 位 置 ,在侧墙 的中心位置初步建立工件 坐标 系 G 5 4 ,然
2 . S c h o o l o f Me c h a n i c a l E n  ̄ n e e i f n g ,D a l i a n J i a o t o n g U n i v e r s i t y , D a l i a n L i a o n i n g 1 1 6 0 2 8工方法
铝合金雕刻机-产品百科

铝合金雕刻机|产品百科铝合金雕刻机是一种高精度、高速度、高效率的机械设备,用于将各种材料雕刻成三维复杂的形状和图案,广泛应用于广告、艺术、版画、雕刻、模具、凸版印刷、电路板、标牌等行业。
一、铝合金雕刻机的技术优势1.高精度:采用进口高精度丝杆和导轨,满足高精度的雕刻需求。
2.高速度:采用高速主轴,加工效率高,速度快。
3.高效率:可进行多道雕刻、多工件同时加工,提高生产效率。
4.操作简单:采用人性化操作界面,简单易懂,易于操作。
5.安全可靠:采用全封闭式设计,防护性好,安全可靠。
6.材料适应性强:适用于各种材料的雕刻,包括木材、亚克力、PVC、ABS、铝合金等。
7.广泛应用:适用于广告、艺术、雕刻、模具、凸版印刷、电路板、标牌等行业,并可根据不同的需求定制机器。
二、铝合金雕刻机的结构和原理铝合金雕刻机大体结构包括机床架、工作台、主轴、驱动系统、控制系统等部分。
1.机床架:机床架由梁式结构框架组成,整体性能稳定,刚性强,适用于高速雕刻和高负荷加工。
2.工作台:工作台是机床的移动部分,用于支持和固定加工件,通常采用吸盘式或夹具式,易于调整和固定。
3.主轴:主轴是铝合金雕刻机的核心部件,负责将刀具带动加工件实现雕刻。
主轴采用高速电机或高速气动主轴,转速高,精度高,可根据不同加工需求选择不同规格的主轴。
4.驱动系统:驱动系统是铝合金雕刻机的关键部件之一,包括马达驱动和伺服驱动两种方式,可实现高速、高精度的运动控制。
5.控制系统:控制系统是铝合金雕刻机的大脑,采用CNC数控系统,可实现可编程、自动化控制,支持手动、自动、示教等多种操作方式,具有良好的用户体验。
三、铝合金雕刻机的应用范围1.广告行业:适用于各种广告制品的雕刻,如广告牌、展板、门头等。
2.艺术品领域:适用于艺术品、雕塑等复杂造型的雕刻和加工。
3.建筑行业:适用于建筑材料、门窗、地板等需进行花纹雕刻和加工的产品。
4.模具行业:适用于各种模具、衬板等复杂形状的加工和雕刻。
金属加工机械的数字化制造与产业升级
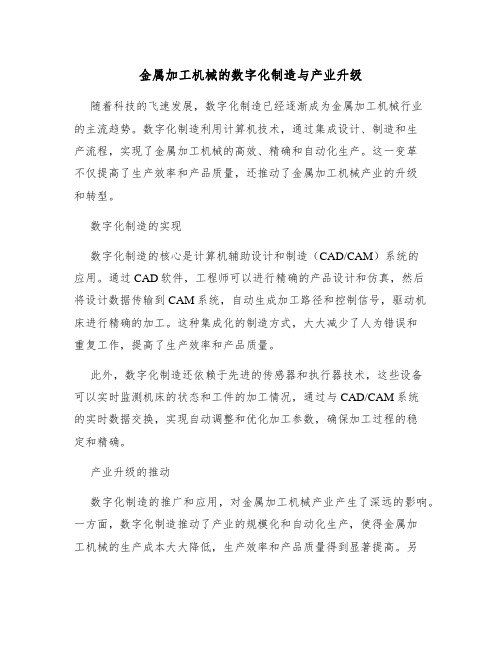
金属加工机械的数字化制造与产业升级随着科技的飞速发展,数字化制造已经逐渐成为金属加工机械行业的主流趋势。
数字化制造利用计算机技术,通过集成设计、制造和生产流程,实现了金属加工机械的高效、精确和自动化生产。
这一变革不仅提高了生产效率和产品质量,还推动了金属加工机械产业的升级和转型。
数字化制造的实现数字化制造的核心是计算机辅助设计和制造(CAD/CAM)系统的应用。
通过CAD软件,工程师可以进行精确的产品设计和仿真,然后将设计数据传输到CAM系统,自动生成加工路径和控制信号,驱动机床进行精确的加工。
这种集成化的制造方式,大大减少了人为错误和重复工作,提高了生产效率和产品质量。
此外,数字化制造还依赖于先进的传感器和执行器技术,这些设备可以实时监测机床的状态和工件的加工情况,通过与CAD/CAM系统的实时数据交换,实现自动调整和优化加工参数,确保加工过程的稳定和精确。
产业升级的推动数字化制造的推广和应用,对金属加工机械产业产生了深远的影响。
一方面,数字化制造推动了产业的规模化和自动化生产,使得金属加工机械的生产成本大大降低,生产效率和产品质量得到显著提高。
另一方面,数字化制造也催生了新的商业模式和服务模式,如个性化定制、远程诊断和维护等,为用户提供更加灵活和便捷的服务。
数字化制造还推动了金属加工机械产业的技术创新和研发能力的提升。
通过数字化制造技术,企业可以更加快速地开发新产品和新技术,满足市场的需求和变化。
同时,数字化制造也促进了产业链上下游企业的协同创新和合作,推动了整个产业链的升级和转型。
金属加工机械的数字化制造是产业发展的重要趋势和必然选择。
通过数字化制造技术的应用,金属加工机械产业可以实现高效、精确和自动化的生产,提高生产效率和产品质量,推动产业的升级和转型。
同时,数字化制造也为企业提供了更多的创新和合作机会,为用户提供更加灵活和便捷的服务。
因此,金属加工机械产业应该积极探索和推广数字化制造技术,以适应市场的需求和变化,实现可持续发展。
我国首台400kJ数控全液压对击模锻锤研制成功

我国首台400kJ数控全液压对击模锻锤研制成功
佚名
【期刊名称】《锻压装备与制造技术》
【年(卷),期】2012(47)6
【摘要】近日,我国首台400kJ数控全液压对击模锻锤在江苏百协精锻机床有限公司研制成功,结束了国内大型精密模锻成形设备完全依靠进口的历史。
【总页数】1页(P8-8)
【关键词】模锻锤;全液压;数控;成形设备;精密模锻;机床;精锻
【正文语种】中文
【中图分类】TG315.3
【相关文献】
1.国内首台全自动多线切片机研制成功/我国高精度激光机床问世/国内首台鼠牙盘齿数控成形磨床 [J],
2.海安百协程控全液压模锻锤通过省级鉴定;不断创新结硕果合锻四项新产品通过鉴定;上海冲剪机床厂研制成功机械电子伺服数控板料折弯机 [J],
3.我国核反应堆专用机器人研发取得技术进展/中科院重庆研究院小型拉曼光谱仪样机研制成功/国内首台大型无模铸造成形机研制成功 [J],
4.中国首台多功能数控CPE顶管辊模孔型加工机床研制成功 [J], 臧昭农
5.我国首台新型数控全液压对击锤通过技术评审 [J],
因版权原因,仅展示原文概要,查看原文内容请购买。
国外超精密数控机床概述

国外超精密数控机床概述20世纪50年代后期,美国首先开始进行超精密加工机床方面的研究,当时因开发激光核聚变实验装置和红外线实验装置需要大型金属反射镜,急需反射镜的超精密加工技术和超精密加工机床。
人们通过使用当时精度较高的精密机床,采用单点金刚石车刀对铝合金和无氧化铜进行镜面切削,以此为起点,超精密加工作为一种崭新的机械加工工艺得到了迅速发展。
1962年,Union Carbide公司首先开发出的利用多孔质石墨空气轴承的超精密半球面车床,成功地实现了超精密镜面车削,尺寸精度达到士0.6 um,表面粗糙度为Ra0.025um,从而迈出了亚微米加工的第一步。
但是,金刚石超精密车削比较适合一些较软的金属材料,而在航空航天、天文、军事等应用领域的卫星摄像头方面,最为常用的却是如玻璃、陶瓷等脆性材料的非金属器件。
用金刚石刀具对这些材料进行切削加工,则会使己加工表面产生裂纹。
而超精密磨削则更有利于脆性材料的加工。
Union Carbide公司的另一代表性产品是其在1972年研制成功的R-0方式的非球面创成加工机床。
这是一台具有位置反馈的双坐标数控车床,可实时改变刀座导轨的转角0和半径R,实现非球面的镜面加工。
加工直径达380mm,工件的形状精度为士0.63um,表面粗糙度为Ra0.025 um。
摩尔公司(Mood Special Tool)于1968年研制出带空气主轴的Moori型超精密镜面车床,但为了实现脆性材料的超精密加工,该公司又于1980年在世界上首次开发出三坐标控制的M-18AG型超精密非球面金刚石刀具车削、金刚石砂轮磨削机床。
该机床采用空气主轴,回转精度径向为0.075pm;采用Allen-Braley 7320数控系统;X,Z 轴行程分别为410mm和230mm,其导轨的平直度在全长行程范围内均在0.5um以内,B轴的定位精度在3600范围内是0.38um;采用金刚石砂轮可加工最大直径为356mm的各种非球面的金属反射镜。
最新版铝加工项目解决方案

最新版铝加工项目解决方案随着现代工业的快速发展,铝加工项目成为了一个热门的选择。
铝加工项目主要涉及到对铝材料的切割、钻孔、曲线和平面成型等加工工艺。
对于铝加工项目,解决方案的设计对提高生产效率、减少人工成本以及改善产品质量至关重要。
本文将介绍最新版铝加工项目解决方案。
一、自动化生产线自动化生产线是目前铝加工项目中最主要的解决方案之一、自动化生产线可以实现对铝材料的自动化切割、钻孔和成型等过程,大大提高了生产效率和质量。
该解决方案主要包括以下几个关键技术:1.机器人技术:采用机器人对铝材料进行切割、钻孔和成型等加工工艺,减少了人工操作的需求,提高了生产效率和质量。
2.自动化控制技术:通过自动化控制系统对生产线进行控制和调度,实现生产过程的自动化管理和控制,提高了生产效率和产品质量。
3.智能传感技术:利用智能传感技术对加工过程中的关键参数进行实时监测和控制,确保加工质量的稳定和一致性。
4.数据分析和优化技术:利用数据分析和优化技术对生产过程中的数据进行实时分析和优化,找出生产过程中存在的问题并提出相应的解决方案,提高生产效率和质量。
二、精密加工技术精密加工技术是解决铝加工项目中精密加工问题的另一种重要方案。
精密加工技术主要通过提高加工的精度和稳定性来改善产品质量。
该解决方案主要包括以下几个关键技术:1.高速加工技术:采用高速切削和钻孔技术,提高了加工速度和质量,同时减少了加工过程中的振动和声响。
2.精度控制技术:采用精密的加工工艺和设备,实现对产品尺寸和形状的精确控制,确保产品质量的稳定性和一致性。
3.表面处理技术:采用表面处理技术进行产品表面的抛光、喷涂和镀膜等工艺,提高产品的耐腐蚀性和美观度。
4.精密检测技术:采用精密的检测设备对产品进行实时检测和监控,确保产品质量的稳定和符合要求。
三、绿色制造技术绿色制造技术是解决铝加工项目中环境污染问题的重要方案。
绿色制造技术主要通过减少能源消耗、降低排放和回收利用等手段,实现对环境的保护和减少对自然资源的消耗。
- 1、下载文档前请自行甄别文档内容的完整性,平台不提供额外的编辑、内容补充、找答案等附加服务。
- 2、"仅部分预览"的文档,不可在线预览部分如存在完整性等问题,可反馈申请退款(可完整预览的文档不适用该条件!)。
- 3、如文档侵犯您的权益,请联系客服反馈,我们会尽快为您处理(人工客服工作时间:9:00-18:30)。
铝合金高效高速数控加工机床新成果高效高速加工技术(HEM-HSM)实际上是一种工序复合化高速加工技术,即在一台高功能高速数控加工中心(MC)机床上,实现对零件高金属切除率mrr (metalremovalrate)的高速粗加工/高速半粗加工(HEM)和高零件表面积切除速率的高速半精加工/高速精加工(HSM)多种工序的复合加工,和常规切削加工和典型高速加工技术(HSM)相比,HEM-HSM加工具有明显的优势,是一种高加工生产率与高加工质量集成融合的高速加工技术。
能实现这种一次装夹完成粗精工序复合加工(HEM-HSM)的高速数控加工机床可称为高效高速数控加工机床。
现今,用于HEM-HSM加工应用的高效高速数控MC机床多为五轴联动和配备有高功率高转速/高转矩主轴,并已成为许多航宇制造业用户特别关注的现代化先进关键制造装备之一。
“目前许多世界着名的数控机床制造商都为航宇制造业推出了多种类型用于大型铝合金材和钛合金材整体结构件HEM-HSM加工应用的五轴联动高速数控MC机床,实现高效率高速粗加工和高质量高速精加工的良好融合,满足用户对高生产率大型高速加工设备的迫切需要。
”国际模协秘书长罗百辉指出,用于诸如铝合金等轻合金材的HEM-HSM加工设备和用于诸如钛合金等硬合金材的HEM-HSM加工设备具有较大的不同。
近10多年来,适用于轻负载切削的高功率高速主轴和高速刀具设计制造技术取得了显着进步,同时对铝合金材HEM-HSM加工技术及其工程应用研究也已比较成熟,因而铝合金高效高速数控MC机床在航宇制造业得到较广泛应用。
铝合金材HEM-HSM加工需要高功率高转速主轴用于大型铝合金材航宇整体结构件HEM-HSM加工应用的高速数控MC机床,机床主轴应具有足够高的功率、转速、适当转矩和足够宽的可调控的转速范围,也就是说要求机床主轴功率/转矩每转速特性应适合于航宇铝合金等轻合金材的高效高速切削加工之工艺要求。
从金属切削加工基本原理可知,对金属材工件铣削加工时有:mrr=PS×MRF=aeapzfZn×10-3(cm3/min)(1)PS=SPF×mrr(kW)(2)PS/n=T/9555≈T×10-4(3)这儿,mrr:金属切除率,cm3/min;PS:主轴功率,kW;MRF:金属切除指数(MetalRemovalFactor),cm3?min-1/kW;ae:切宽WOC(径向切深,RadialDepthofCut),mm;ap:切深DOC(轴向切深,AxialDepthofCut),mm;fZ:刀每齿进给量,mm/刃转;z:刀齿数;n:主轴转速,r/min;SPF:主轴功率指数(SpindlePowerFactor),kW/cm3?min-1;且SPF=1/MRF;T:主轴转矩,Nm。
从式(1)与式(2)可看出,为取得高金属切除率mrr,作为HEM-HSM加工应用的高速数控MC机床之主轴首先应具有足够高的功率。
典型铝合金材(如7075)主轴功率指数SPF为0.015kW/cm3?min-1。
对功率60~120kW电主轴,一般可具有金属切除率mrr达4000~8000cm3/min的高切削能力。
工业实践表明,铝合金材相对可加工性系数Kr一般大于3(2.0~7.5),属很容易切削材,同时高速切削时所需的切削力比常规切削要低30~50%以上。
而从式(3)可清晰看出,在确定的高主轴功率场合下,这就要求主轴应具有足够高的转速才能和低切削负载加工应用相适应。
实际上,这正是铝合金材采用HSM 实现高速精加工或半精加工的典型应用场合,即要求主轴运行在高功率高转速区。
如对铝合金材的HSM精加工应用场合,一般要求主轴转速高于18000r/min,典型为18,000~35,000r/min;通常,HSM半精加工主轴转速为18,000~24,000r/min,HSM精加工主轴转速为24,000~35,000r/min;主轴转矩不低于5Nm即可,典型值为10~50Nm。
从式(3)还可看出,对确定的主轴功率,主轴转速和转矩是为相互制约的一对参数。
为此,如适当降低主轴转速可获得较高主轴转矩,或说可产生较大加工切削力,而这又正是铝合金材采用HEM实现高效高速粗加工的典型应用场合。
如作为铝合金材的HEM粗加工应用场合,一般要求主轴转速不高于15,000r/min,通常HEM粗加工主轴转速为10,000~14,000r/min,HEM半粗加工主轴转速为14,000~18,000r/min,主轴转矩要求在50~150Nm。
这就是说,用于大型铝合金材航宇整体结构件HEM-HSM加工应用的高效高速数控MC机床应配置高功率高转速的电主轴,其功率通常高于40~120kW(取决于需求的金属切除率mrr),转速可控范围应宽于数千至数万r/min;转矩多在20~150Nm,最大功率/转速比在0.01数量级(0.005~0.015),切削速度1500~6000m/min,切削力多为数百到1000N,加工进给速度10~20m/min,金属切除率mrr达4000~8000cm3/min,典型刀具接口为HSK-A63。
德国著名电主轴制造商MN公司生产的HCS230-22,000/120高速电主轴可作为此类电主轴的一个典型实例,其功率/转矩-转速特性曲线如图2所示。
该高速电主轴额定功率120kW(S6-40%:155kW),额定转矩84Nm(S6-40%:108Nm),基速13,800r/min,最高转速22,000r/min,最大功率/转速比0.011,刀具接口HSK-A80,主轴轴向刚性达160N/μm,径向刚性496N/μm。
此外,诸如瑞士IBAG、FISCHER、RENAUD、德国IMT、JAGER和意大利OMLAT等许多数控机床电主轴制造商都能提供这类用于诸如铝合金等轻合金材HEM-HSM应用的高功率高速电主轴,并在高速数控机床上得到了广泛实际应用。
如意大利OMLAT公司高速电主轴OMC-230-230/635也具有和图2相类似的功率/转矩-转速特性曲线,额定功率80kW(S6-60%:100kW),基本转速12,000r/min,基本转矩64NmS6-60%:80Nm),最高转速达24,000r/min,最大功率/转速比0.008,设计有HSK-A63刀具接口。
这儿就不一一列举了。
铝合金材立式高效高速数控加工机床众所周知,机械切削加工机床装备是实现切削加工工艺的基本平台。
因此,为适应大型零件HEM-HSM加工工艺要求,立式HEM-HSM数控MC机床多继承了传统高速加工机床可使运动部件轻量化的“箱中箱”(BoxInBox)结构设计,对传统大型龙门结构机床采用一种高架立柱过桥式横梁主轴部件可移动的、对称式机床结构设计(简称“高架桥式龙门移动”结构)。
这种结构机床,龙门立柱和工作台是不动的,X/Y/Z轴运动分别由横梁、主轴溜板部件来完成,A(B)、C轴运动则集中在主轴头上来实现。
高架桥式龙门移动结构设计机床优点在于:?机床结构具有较好开放性,且直接通过刀具实现五轴运动(工件不运动),适合加工大型零件;?坐标运动部件质量轻,不但适合于高速移动,并且刚性好;?对称结构设计,有利于减轻温度热变形影响,提高了精度;?所有导轨表面均高于刀具切削点,有利于导轨表面清洁保持,延长了导轨使用寿命;?采用适当集成化电主轴铣头装置,可实现5坐标联动和多面体加工于一台机床上;?设备占地面积减少;需要时X向行程容易加长。
这种大型HEM-HSM数控MC机床在航宇制造业中已得到了较广泛的应用,成为加工大型飞机整体结构件的关键设备。
世界许多着名机床制造商都推出了用于铝合金材HEM-HSM加工的立式高效高速数控MC机床,以满足航宇制造业用户之迫切需求。
图3所示的为美国MAGCincinnati机床公司新近为航空飞机制造业推出的HyperMach五轴数控型面铣削中心,可用于实现大型复杂飞机铝合金材的HEM-HSM切削加工。
该机床为高架桥式龙门移动结构,工作进给速度60m/min,快速移动速度100m/min,配置有集成化A/B或A/C旋转轴的大功率主轴头,其功率/转矩-转速特性能与图1要求相适应。
带A/B轴主轴头标配主轴额定功率100kW(S6-40%:125kW),转矩79Nm(S6-40%:99Nm),基速12,000r/min,最高转速18,000r/min,刀具接口HSK-A100;或可选配主轴额定功率60kW,转矩29Nm,基速20,000r/min,最高转速30,000r/min,刀具接口HSK-A63。
带A/C轴主轴头标配主轴额定功率60kW,转矩29Nm,基速20,000r/min,最高转速30,000r/min,刀具接口HSK-A63;或可选配主轴额定功率85kW(S6-40%:91kW),转矩85Nm(S6-40%:106Nm),基速9600r/min,最高转速20,000r/min,刀具接口HSK-A100。
据Cincinnati公司宣称,在HyperMach 机床上加工一铝合金材大型飞机薄壁零件,仅费时30min。
同样的零件若在典型高速铣床上加工需3hr,而在普通数控床则需8hr以上。
波音公司就购置有这种高效高速五轴数控加工机床用于加工C-17军用运输机和波音787民用客机的如框、肋、壁板和梁等大型铝合金材整体结构件,其金属切除率mrr可高达7374cm3/min,即每分钟可产生约20kg铝合金切屑。
据报道,俄罗斯联合航空公司(UAC)花费约900万美元从Cincinnati公司购买了一台V1200铺丝机和2台额定功率85kW和最高转速20,000r/min的单主轴HyperMach机床(一台床身长12.6m,另一台18.2m)用于MS-21系列客机结构件的制造。
著名数控机床制造商德国Handtmann公司新推出的GANTRYTS双主轴高架桥式龙门移动式高速五轴数控MC机床,机床最大长度可达47,000mm,最宽达5400mm,Z坐标可任选1000/1200/1500mm;直线轴快速移动速度50m/min,加速度0.5g。
其结构特点是设计有两个Z向滑板,各带一个Y向铣头,铣头可独立Y向运动。
采用这种结构,两滑板在Y和Z向可自由移动且相互独立。
安装在Y轴上的两主轴Y行程为2×2300mm,或2×2400mm。
因此,通过合适的编程,两主轴可同时加工两个相同的或镜像对称的两个零件。
机床设计有集成化A/C旋转轴的主轴头,配置有和图2特性曲线相类似的高功率高转速电主轴,连续功率可任选为45/70/100kW,最高转速30,000/30,000/18,000r/min,刀具接口HSK-A63/A100,可实现HEM-HSM加工大型复杂飞机铝合金材、复合材料和薄钢板结构件。