本科毕业论文---5000td新型干法水泥熟料生产线水泥粉磨车间工艺设计
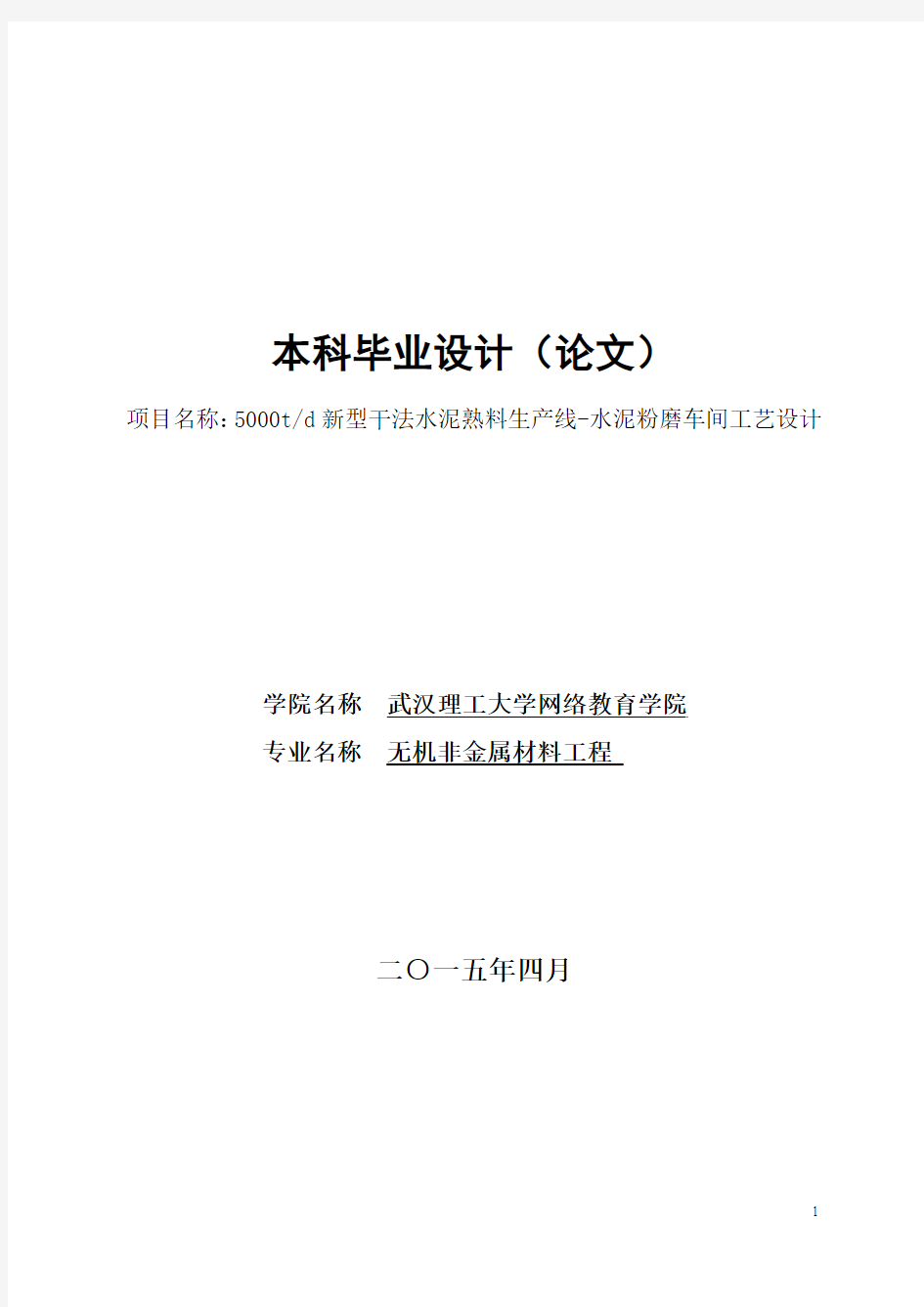
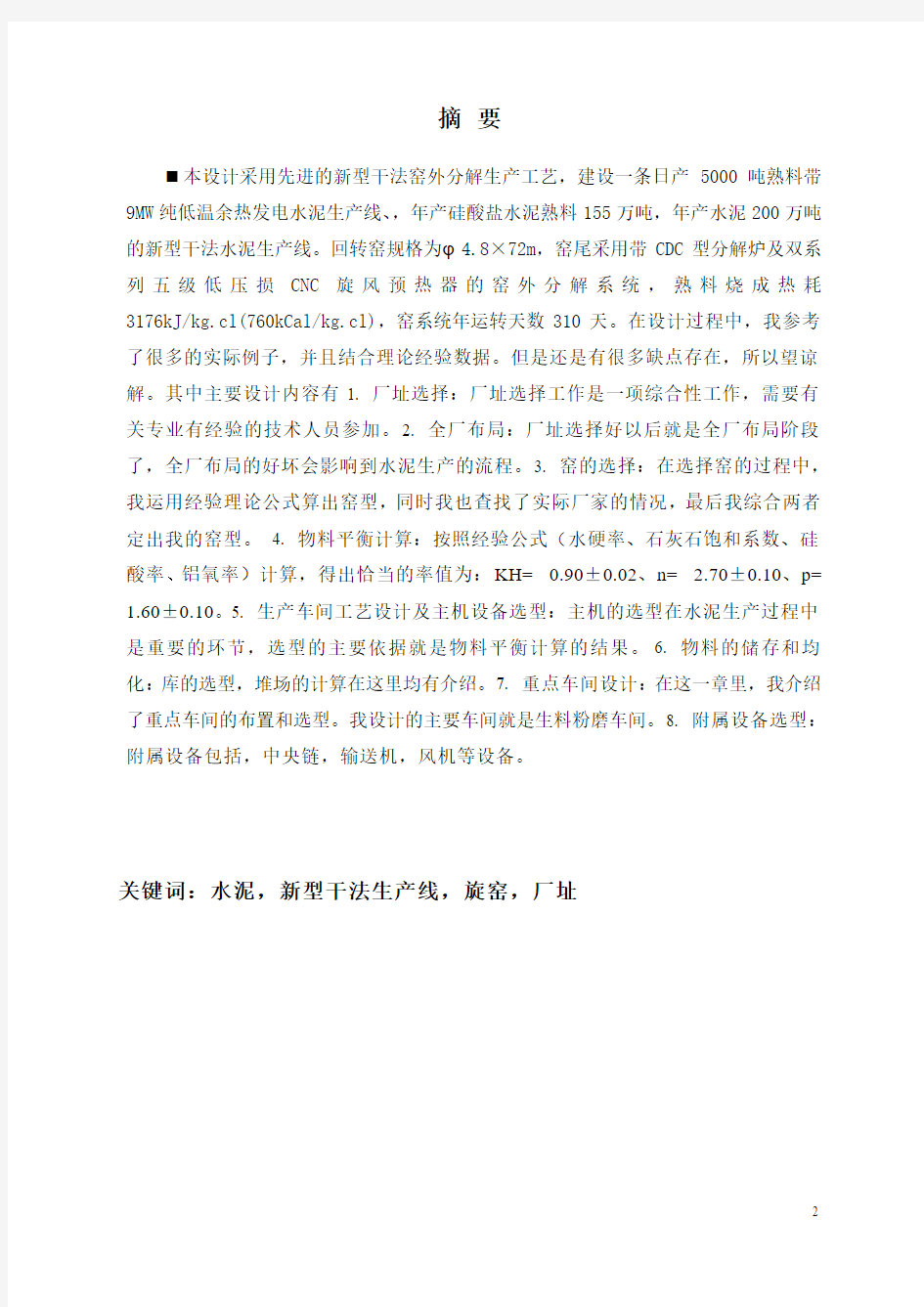
本科毕业设计(论文)
项目名称:5000t/d新型干法水泥熟料生产线-水泥粉磨车间工艺设计
学院名称武汉理工大学网络教育学院
专业名称无机非金属材料工程
二○一五年四月
摘要
本设计采用先进的新型干法窑外分解生产工艺,建设一条日产5000吨熟料带9MW纯低温余热发电水泥生产线、,年产硅酸盐水泥熟料155万吨,年产水泥200万吨的新型干法水泥生产线。回转窑规格为φ4.8×72m,窑尾采用带CDC型分解炉及双系列五级低压损CNC旋风预热器的窑外分解系统,熟料烧成热耗3176kJ/kg.cl(760kCal/kg.cl),窑系统年运转天数310天。在设计过程中,我参考了很多的实际例子,并且结合理论经验数据。但是还是有很多缺点存在,所以望谅解。其中主要设计内容有1. 厂址选择:厂址选择工作是一项综合性工作,需要有关专业有经验的技术人员参加。2. 全厂布局:厂址选择好以后就是全厂布局阶段了,全厂布局的好坏会影响到水泥生产的流程。3. 窑的选择:在选择窑的过程中,我运用经验理论公式算出窑型,同时我也查找了实际厂家的情况,最后我综合两者定出我的窑型。 4. 物料平衡计算:按照经验公式(水硬率、石灰石饱和系数、硅酸率、铝氧率)计算,得出恰当的率值为:KH=0.90±0.02、n= 2.70±0.10、p= 1.60±0.10。5. 生产车间工艺设计及主机设备选型:主机的选型在水泥生产过程中是重要的环节,选型的主要依据就是物料平衡计算的结果。6. 物料的储存和均化:库的选型,堆场的计算在这里均有介绍。7. 重点车间设计:在这一章里,我介绍了重点车间的布置和选型。我设计的主要车间就是生料粉磨车间。8. 附属设备选型:附属设备包括,中央链,输送机,风机等设备。
关键词:水泥,新型干法生产线,旋窑,厂址
目录
第一章总论 (2)
1.1 项目名称 (2)
1.2设计依据 (2)
1.3设计原则和指导思想 (2)
1.4建设规模、生产方法及产品纲领 (2)
1.5设计范围 (3)
1.6建设条件 (3)
1.6.1 原料与燃料 (3)
1.6.2厂址条件 (5)
1.6.3供电条件 (6)
1.6.4 供水条件 (6)
1.6.5气象条件与地震烈度 (6)
1.7技术方案简述 (7)
1.7.1石灰石破碎和储存 (7)
1.7.2辅助原料、原煤破碎 (7)
1.7.3辅助原料及原煤预均化 (7)
1.7.4生料粉磨 (7)
1.7.5生料均化与储存 (8)
1.7.6 烧成系统 (8)
1.7.7 熟料储存及散装 (9)
1.7.8煤粉制备 (9)
1.7.9空压机站 (9)
1.7.10中央化验室 (9)
1.7.11电气自控方案 (10)
1.8余热发电 (10)
第二章配料计算 (11)
2.1生产方法及产品方案 (11)
2.2配料用原、燃料成份数据 (11)
2.3配料率值的选择 (11)
2.4计算煤灰掺入量 (12)
2.5计算干燥原料配合比 (12)
2.6计算湿原料的配合比 (13)
2.7配料计算结果 (14)
2.8评述及建议 (15)
第三章物料平衡 (16)
3.1原燃材料消耗定额计算 (16)
3.2石膏、炉渣、粉煤灰消耗定额计算 (17)
3.3根据配料设计计算出的全厂物料平衡量 (18)
第四章主机平衡 (21)
4.1生产规模与产品品种 (21)
4.2生产方法 (21)
4.3工艺设计及设备选型原则 (21)
4.4主机设备及主要设施配置 (21)
4.4.1石灰石破碎 (21)
4.4.2辅助原料破碎 (22)
4.4.3原煤破碎 (22)
4.4.4联合预均化 (22)
4.4.5 生料粉磨 (23)
4.4.6 窑、磨废气处理 (24)
4.4.7 生料均化及窑尾喂料 (26)
4.4.8 烧成系统 (27)
4.4.9 煤粉制备 (28)
4.4.10 空压机站 (28)
4.4.11 水泥磨 (28)
4.5 全厂工艺主机设备表 (29)
第五章储库平衡 (35)
5.1石灰石储存 (35)
5.2页岩储存 (36)
5.3硅石储存 (37)
5.4铜镍渣储存 (37)
5.5生料均化库 (38)
5.6熟料库 (39)
5.7原煤储存(露天堆场) (39)
5.8石膏储存 (39)
5.9炉渣 (40)
5.10粉煤灰 (41)
5.11熟料配料圆库 (42)
5.12全厂物料储库形式和储存量 (43)
第六章水泥车间工艺计算 (44)
6.1水泥粉磨系统方案比较及选择 (44)
6.2工艺流程简介 (45)
6.3设备参数计算 (46)
6.3.1磨机系统 (46)
6.3.2辊压机系统 (49)
结论.................................................................................................................... 错误!未定义书签。谢辞. (51)
参考文献 (52)
绪论
水泥是国民经济建设的重要基础原材料,目前国内外尚无一种材料可以替代它的地位。作为国民经济的重要基础产业,水泥工业已经成为国民经济社会发展水平和综合实力的重要标志。随着我国经济的高速发展,水泥在国民经济中的作用越来越大。自1985年起我国水泥产量已连续 21年位居世界第一位,现如今已占世界水泥总产量的48%左右。
我国水泥行业利润水平偏低,波动性大,主要是由我国水泥行业集中度低,企业规模偏小,局部区域产能严重过剩,市场过度竞争,以及落后生产力所占比重大,科技含量低,能耗高等诸多因素造成的。我国预热分解技术起步晚,但在“控制总量、调整结构、上大改小”的产业政策指导下和贯彻“发展与淘汰”相结合的结构调整机制下,大力开发、发展预热分解技术,大大提升了新型干法预分解窑(PC)的结构比例,截止到2005年12月底,我国预分解窑已投产615条(不包括香港、澳门、台湾)。
水泥生产主要工艺过程简要包括为“两磨一烧”。按主要生产环节论述为:矿山采运(自备矿山时,包括矿山开采、破碎、均化)、生料制备(包括物料破碎、原料预均化、原料的配比、生料的粉磨和均化等)、熟料煅烧(包括煤粉制备、熟料煅烧和冷却等)、水泥的粉磨(包括粉磨站)与水泥包装(包括散装)等。
新型干法是以悬浮预热和预分解技术装备为核心,以先进的环保、热工、粉磨、均化、储运、在线检测、信息化等技术装备未能基础;采用新技术和新材料;节约资源和能源,充分利用废料、矿渣,促进环境经济,实现人与自然和谐相处的现代化。
第一章总论
1.1 项目名称
项目名称:哈密天山水泥有限责任公司5000t/d熟料水泥生产线工程。
1.2设计依据
厂址地形图及相关设计基础资料。
1.3设计原则和指导思想
1.3.1 坚持贯彻一切为业主着想的思想,精心优化设计方案,保证设计质量,缩短设计和建设周期,实现经济、高效和可靠的原则。
1.3.2 充分重视本项目拟建厂址地处高海拔、大陆性干旱、高寒地区的特殊气候条件,合理配置系统设备设施,确保投产后短期内达标、达产。
1.3.3 坚持节省投资、努力缩短建设周期的原则。总图布置简捷顺畅,减少占地面积。为降低投资,结合当地气候情况,在满足生产的前提下,工艺设施布置尽量露天化。1.3.4 合理确定机械化、自动化水平,以可靠实用为前提,简化生产控制操作过程。1.3.5采用先进可靠的计算机集散控制系统(DCS),确保生产工艺过程运行可靠,工况稳定,节能高效,优化控制,实现管理现代化,大幅度减少生产岗位操作人员,提高劳动生产率。
1.3.6节约用水,最大限度地提高循环水的利用率;优化设计方案,合理利用土地。1.3.7注重节能降耗、环境保护、三废治理、劳动安全和职业卫生,以行之有效的技术措施全面执行各项有关法规。切实加强噪声治理,采取有效措施,尽量降低噪声对周围环境的影响,使工厂投产后满足国家噪声防范标准,努力构建和谐社会。
1.4建设规模、生产方法及产品纲领
1.4.1 建设规模
建设一条5000t/d熟料新型干法水泥生产线,年产熟料155万吨。
1.4.2 生产方法
采用五级旋风预热预分解新型干法水泥生产工艺。
1.4.3 产品纲领
年产水泥熟料155万吨,年产水泥约200万吨。年发电量为5184×104kWh,年供电量为4770×104kWh。
1.4.4设计控制指标
熟料生产能力5000t/d。
熟料28天抗压强度≥57.5MPa。
熟料烧成平均热耗≤760×4.18kJ/kg。
吨熟料工艺电耗:≤64kWh/t。
计量标准符合国家Ⅲ级计量标准。
环保指标符合《水泥工业大气污染物排放标准》(GB4915-2004)排放标准,污水排放满足《污水综合排放标准》(GB8978-1996)表4中的一级标准;厂界噪声控制到《工业企业厂界噪声标准》(GB12348-1990)中的Ⅱ类标准。
1.5设计范围
从原、燃材料进厂破碎到水泥出厂(含散装)的一条5000t/d水泥熟料生产线。
1.6建设条件
1.6.1 原料与燃料
1.6.1.1 石灰质原料
本项目的石灰石来自哈密白石头石灰石矿区。
该矿区石灰石为灰白色粉晶灰岩。灰—灰白色,局部略带乳黄色,粉晶结构,块状构造。矿山石灰石平均化学成分见表1-1。
石灰石平均化学成分表(%)表1-1
由表1-1可以看出,矿石品位高,属生产水泥的优质原料。石灰石开采后,用汽车运送到厂区。
1.6.1.2粘土质原料
本项目铝质原料采用页岩和粉煤灰搭配使用,可以降低热耗,同时充分利用三废资源,减少资源浪费,根据提供的铝质原料情况来看,成分较好,化学成分见表1-2、1-3。
页岩平均化学成分表(%)表1-2
粉煤灰平均化学成分(%)表1-3
1.6.1.3硅质校正原料
由于本项目的页岩和粉煤灰的铝率高,需要增加硅质原料。故本项目采用硅石作为硅质校正原料。主要化学成分见表1-4。
硅石平均化学成分表(%)表1-4
1.6.1.4 铁质校正原料
本项目铁质原料拟外购铜镍冶炼厂的工业废渣---铜镍渣。距拟建厂址约90km。铜镍渣的年需要量约3万t。化学成分见表1-5。
铜镍渣的平均化学成分(%) 表1-5
1.6.1.5燃料
区域煤炭资源预测储量约5708亿t,地质储量384亿t,探明资源储量338.5亿。
本项目采用的烟煤来自哈密三道岭煤矿,该煤矿距拟建厂址约110km,汽车运输进厂。本项目年需要用无烟煤约20万t。
煤的工业分析见表1-6,煤灰的化学成分见表1-7。
煤的工业分析(%)表1-6
煤的化学成分(%)表1-7
1.6.1.6石膏
本项目拟采用哈密热电厂的脱硫石膏及天然石膏作为水泥用缓凝剂。
哈密第一热电厂年产脱硫石膏1.7万t,第二发电厂年产脱硫石膏灰2万t,哈密淖毛湖煤电年产脱硫石膏灰5万t,以上电厂脱硫石膏灰能满足本项目的需求。
天然石膏可从玉门镇赤金公司采购,距哈密730km;还可从吐鲁番采购,运距约750km,可满足生产需求。业主提供的石膏化学成份如表1-8所示。
石膏化学成分表1-8
1.6.1.7混合材
本项目拟采用粉煤灰和炉底渣为混合材。粉煤灰与炉底渣均来自哈密热电厂,汽车运输进厂;混合材还可使用新疆有色集团哈密铜镍冶炼厂的铜镍渣、三道岭煤矿的煤矸石。
1.6.1.8各种原燃材料的进厂粒度、水分等
表1-9
1.6.2厂址条件
拟建厂址位于哈密工业园区重工业加工区。位于哈密市南偏西方向约15km处的哈密市工业园区,北距城市污水处理站约4km,距花园乡约5km。大南湖矿区到该厂址铁路运输距离约71.6km,公路运输距离约67.2km。厂址距哈密~若羌公路约4.5km。
厂址地形平坦,开阔,属山前堆积平原中下部,海拔高程在680~675米之间,地形高差很小。总的地势由北向南倾斜,西北高,东南低。拟建场地为荒漠地,未种植,地表有盐渍化现象,有明显的盐壳、盐霜。本次工程的建设场地长约660米,宽约404米。
1.6.3供电条件
本项目用电由哈密工业园区重工业加工区110kV变电所供电,输电距离约1km另设柴油发电机作保安用电,同时厂区余热发电配电站作为供电电源。
1.6.4 供水条件
哈密地区的水资源主要靠天山降水和冰川补给,水资源相对丰富,水资源总量约为18.9亿m3,其中地表水10.6亿m3,地下水8.3亿m3,石城子水库、榆树沟水库、庙儿沟水库联合向哈密重工业加工园区供水。
本项目水源由哈密工业园区重工业加工区集中供给,输水距离约2km。
1.6.5气象条件与地震烈度
1.6.5.1 气象条件
根据当地气象局提供的资料分析,哈密地区位于欧亚大陆腹地,远离海洋,属于典型的大陆性干旱气候,其特点为:日照充足,热量丰富,气候变化大,降水少,蒸发量大;春季增温较快,此时多风;夏季干热,秋季凉爽,冬季寒冷。具体数据如下:年最高气温42.6℃,年最低气温-28.6℃,年平均气温9.7℃;年平均相对湿度43%;年平均降水量37.1毫米;年平均蒸发量为3064.3毫米;年平均风速2.8m/s,最大风速26m/s,主导风向东北风,历年最大冻土深度127cm,历年最大积雪深度16cm。
年平均气压:964.5hPa
海拔高度:680米。
1.6.5.2 地震烈度
依据《中国地震动峰值加速度区划图》(GB18306-2001图A1),该地区介于地震动峰值加速度0.1g与0.5g范围内,哈密市区以北地区对应地震基本烈度为7度,市区以
南地区对应地震基本烈度为6度,厂址靠近市区,本厂址地震基本烈度按7度考虑。
1.7技术方案简述
1.7.1石灰石破碎和储存
采用LPC1020R20锤式破碎机破碎进厂石灰石,破碎机最大给料粒度为1000×1000×1000mm,当出料粒度≤75mm占95%时,生产能力为800t/h,年利用率27.47%。
由于拟采用的石灰石矿品位高、矿石有害成份含量少,矿体总体质量较好,CaO含量≥51%,质量非常稳定均一,且整个矿区无覆盖土和夹带土,为节省投资,可不作预均化处理,设两座Φ12×28m圆库储存破碎后的石灰石。
1.7.2辅助原料、原煤破碎
辅助原料破碎选用一台NPF16.18反击式破碎机,最大给料粒度≤600mm,出料粒度≤75mm占90%时,生产能力为350t/h,年利用率24.46%。
原煤破碎选用一台PCH1010环锤式破碎机,最大给料粒度≤300mm,出料粒度为30mm 时,生产能力为180t/h,年利用率16.68%。
1.7.3辅助原料及原煤预均化
为便于对页岩、硅石、铁矿石等生产辅助原料和原煤的控制及管理,降低其成份波动,根据本项目的地形特点,工艺采用了对辅助原料、原煤实施联合预均化的方案。设置一座47×240m矩形预均化堆场,辅助原料采用侧堆侧取方式对其进行预均化处理,原煤采用侧堆桥取方式对其进行预均化处理,同时对物料兼起储存作用。在预均化堆场内页岩、硅石、铁矿石和原煤的储量分别为4730t×2、3550t、3840t、2×3445t。
1.7.4生料粉磨
国内生料粉磨通常采用的是立式磨,鉴于当地原料非常干燥,石灰石坚硬难磨的特殊性,生料粉磨采用一套辊压机终粉磨系统。此系统有电耗低、噪音小优点,且天山集团有丰富的使用经验,故本设计采用辊压机生料终粉磨系统。
本项目所选用CDG180140型辊压机终粉磨技术参数为:当入辊压机粒度<45mm,入辊压机综合水分≤8%,出辊压机水分≤0.5%,成品细度为80μm筛筛余10%时,磨损后
期生产能力为350t/h,年利用率53.47%。
1.7.5生料均化与储存
鉴于本项目生产用石灰石CaO含量高,各成份稳定,在强调矿山均化搭配开采的同时设置了辅助原料预均化堆场,生料粉磨采用运行可靠的辊压机和配有在线分析仪的质量控制系统,因此,可适当降低库内生料的储存期,以节省土建费用。
设计采用一座φ18×72m IBAU型生料均化库,生料储量14800t,储存期1.89天。
该库集生料储存、均化和喂料于一体,具有均化效果好、电耗低、系统简单、操作管理方便等优点。
1.7.6 烧成系统
熟料烧成采用一套双列五级CDC预分解系统、φ4.8×72m回转窑和第五代新型空气梁篦式冷却机等设备组成的窑外分解煅烧系统。日产熟料5000t,硅酸盐水泥熟料热耗3176kJ/kg(760kCal/kg.cl),入窑生料的碳酸钙分解率大于92%。窑尾、窑头废气余热分别用于余热发电、烘干原料和原煤。
Φ4.8×72m回转窑,三挡支承,斜度4.0%,主电机功率710kW,直流调速。
⑴预热器及分解炉
窑尾选用一套双列五级CDC预热预分解系统。
该系统热效率高,旋风筒采用多心270°大包角蜗壳,分离效率高,系统阻力小,分解炉结构合理,物料在分解炉内停留时间大于15秒,入窑生料CaCO3分解率大于92%,适合于低挥发份煤的燃烧,入分解炉物料从反应室锥体上部喂入,可有效防止或减少上升烟道的结皮堵塞,提高系统运转率。旋风筒下部设计为斜锥,既可方便设备布置,优化框架结构,又可提高系统收尘效率,方便捅料。采用新型锁风阀,减少了系统漏风。为防止系统结皮堵塞,整个系统配有独特的自动控制喷吹系统以及必要的空气炮,保证预热器系统的正常运行。
⑵回转窑
本工程回转窑采用φ4.8×72m的回转窑,三挡支承,斜度4.0%,主电机功率710kW,直流调速。
采用大窑头罩,降低窑头罩内风速,有利于熟料粉尘沉降。三次风由窑头罩抽取,三次风温度适中。
⑶篦冷机
熟料冷却机采用第五代节能型无磨损稳流冷却机,篦床有效面积为135.74m2,液压传动。出冷却机的熟料温度为环境温度+65℃。与第二代篦冷机相比,每公斤熟料可降低热耗125~170kJ,冷却空气量可减少20~40%,具有单位篦床面积负荷高,篦床面积小,设备重量轻等优点。
第五代节能型无磨损稳流冷却机克服了老式篦冷机因冷却区域划分不够小,中间料层阻力分布不均,造成局部篦床过热易损坏的缺点;篦板的高阻力性,增强了物料层的稳定性;篦板的高穿透性,有利于料层内的气固换热,特别是能有效控制红细料的“红河”现象,增加了二、三次风温度,提高了热能回收。
根据国家环保部门有关规范及要求,本项目窑尾、窑头废气处理推荐采用袋收尘器方案,废气含尘浓度≤30~50mg/Nm3,符合环保排放标准。
1.7.7 熟料储存及散装
熟料储存采用一座φ60×45.5m圆库储存熟料,储量100000t,储期13.2d。库侧设两套熟料散装系统。
由于季节性因素影响,还设置了储量为10万吨的露天熟料堆场。
1.7.8煤粉制备
与传统的钢球风扫磨比,立磨具有系统流程简单、土建费用低(可实现露天布置)、电耗低、噪音小、烘干能力强、入磨粒度大的优点。目前国内立式煤磨加工技术非常成熟可靠,故本项目煤粉制备推荐国产立式磨方案。
当入磨粒度≤40mm,煤粉细度为80μm筛筛余8~10%,入磨水分≤10%,出磨水分≤1%时,生产能力为40t/h,年利用率53.5%。抽取窑头篦冷机热风作为磨机烘干热源。
1.7.9空压机站
厂区设一座空压机站,站内设八台27m3/min螺杆式空压机,分别向全厂气动元件、收尘器和窑尾吹堵系统等处供气。
1.7.10中央化验室
集中控室于一体的中心化验楼负责进出厂原料、燃料、半成品和成品的常规化学分析及物理检验。
1.7.11电气自控方案
本工程采用技术先进、性能可靠的计算机控制系统(即DCS系统)。对主生产线进行集中监视、操作和分散控制,可有效地提高电控设备的可靠性和可维护性,实现控制、监视、操作的现代化。通过中央控制室操作站与工厂管理计算机的网络连接,使管理人员能随时掌握工厂生产的实际情况,实现管理现代化。
1.8余热发电
本工程余热发电规模按5000t/d熟料生产线配套设计,遵循以热定电、节约能源和改善环境的技术原则,充分利用可回收余热量,综合考虑水泥熟料生产线的工艺流程、场地布置、供配电结构、供水设施等因素,利用水泥生产线窑头、窑尾余热资源(窑头废气:155000Nm3/h,窑尾废气:354000Nm3/h),可建设一条装机容量为9000kW的纯低温余热电站。
结合本工程的生产规模及投资环境,拟采用单压纯低温余热发电技术。该技术不使用燃料来补燃,因此不对环境产生附加污染,是典型的资源综合利用工程。主蒸汽的压力和温度较低,运行的可靠性和安全性高,运行成本低,日常管理简单。
综合考虑本工程水泥生产线窑头、窑尾的余热资源分布情况(窑头废气:155000Nm3/h,窑尾废气:354000Nm3/h),和水泥窑的运行状况,确定热力系统及装机方案如下:
系统主机包括:一台AQC单压余热锅炉、一台SP余热锅炉和一套凝汽式汽轮发电机组。
a.AQC单压余热锅炉:利用篦冷机中部抽取的废气(中温段,~400℃),在窑头设置AQC单压余热锅炉,余热锅炉分为过热器、蒸发器和省煤器三段;过热器生产1.35MPa-385℃的过热蒸汽,进入蒸汽母管后通入汽轮发电机组,省煤器生产的180℃热水后,作为AQC余热锅炉蒸发器及SP余热锅炉的给水,出AQC锅炉废气温度降至100℃。AQC锅炉热效率为74.33%。
b.SP余热锅炉:在窑尾设置SP余热锅炉,该锅炉包括过热器和蒸发器,生产1.35MPa-305℃的过热蒸汽,进入蒸汽母管后通入汽轮发电机组,出SP余热锅炉废气温度降到200℃,供生料粉磨烘干使用。SP锅炉热效率为37.51%。
c.汽轮发电机组:通过计算并参考国内5000t/d生产线配置,上述二台余热锅炉生产的蒸汽共可发电7985kW,因此配置9000kW凝汽式汽轮机组一套。
整个工艺流程是:40℃左右的给水经过除氧,由锅炉给水泵加压进入AQC锅炉省煤器后加热成180℃左右的热水,热水分成两部分,一部分送往AQC锅炉,另一部分送往SP锅炉;然后依次经过各自锅炉的蒸发器、过热器产生1.35MPa-385℃和1.35MPa-305℃