硅片切割线痕的起因与降低方法
多线切割线痕产生原因

多线切割线痕产生原因
1.硅片表面出现单一的一条阴刻线(凹槽)、一条阳刻线(凸出),并不是由于碳化硅微粉的大颗粒造成的,单晶硅、多晶硅在拉制过程中出现的硬质点造成跳线,而形成的线痕;
2.硅片表面集中在同一位置的线痕,很乱且不规则;①机械原因、②导轮心震过大、③多晶硅铸锭的大块硬质晶体;
3.硅片切割第一刀出现线痕,硅片表面很多并不太清晰:①沙浆粘度不够、碳化硅微粉粘浮钢线少、切削能力不够,②碳化硅微粉有大颗粒物,③钢线圆度不够、带沙量降低,④钢线的张力太小产生的位移划错,⑤钢线的张力太大、线弓太小料浆带不过去,⑥打沙浆的量不够,⑦线速过高、带沙浆能力降低,⑧沙、液比例不合适,⑨热应力线膨胀系数太大,⑩各参数适配性差。
4.切割中集中在某一段的废片,是由于跳线引起的;跳线的原因:①导轮使用时间太长、严重磨损引起的跳线(导轮使用次数一般为75-85次),②沙浆的杂
质进入线槽引起的跳线。
5.常见阴刻线线痕,由于晶棒本身有生成气孔,切割硅片后可见像硅表面一样亮的阴刻线,并不是线痕。
6.常见线痕:①进刀口:由于刚开始切割,钢线处在不稳定状态,钢线的波动产生的线痕(进线点质硬,加垫层可消除线摆);②倒角处的线痕:由于在粘结硅棒时底
部残留有胶,到倒角处钢线带胶切割引起的线痕,③硅棒后
面的线痕:钢线磨损、造成光洁度、圆度都不够,带沙量低、切削能力下降、线膨胀系数增大引起的线痕。
切片专项培训(一)

1.2多线切割微观机理
多线切割过程微观机理如图2所示,在切割线和单晶表面充满了SiC颗粒 和砂浆悬浮液的混合物,推动晶棒向线网方向移动,导致切割线弯曲。 弯曲角度通常在1°~5°之间[1]。由钢线造成的压力在不同接触区域并不 相同。在钢线正下方达到最大值。由于钢线横向震动会将压力施加到侧 面,而侧面的切割质量会直接影响Si片最终表面质量,有效控制钢线张 力,减小钢线震动就成为多线切割技术的一项重要指标。
济的切割技术解决这一难题,多线切割技术应运而生。多线切割方 式已经取代了内圆切割方式成为主流的Si片加工方式。
多线切割的机理及影响因素
1.1多线切割宏观机理 如图1所示,将开方处理后的晶棒料通过玻璃板
固定在不锈钢工件上,然后放置到切割机的相应区域 。导轮经过开槽工艺处理在轮体上刻有与所使用切割 线直径相适合的精密线槽,钢线通过来回顺序缠绕在 4个导轮的线槽上而形成上下两个平行线网。如图1所 示,发动机带动导轮旋转,导轮带动切割钢线高速走 动,线速一般为10~20 m/s。在工作台两侧的砂嘴将 砂浆均匀地喷在线网上,砂浆(主要成分为SiC和 PEG)随着切割线进入晶棒进行切割作业。同时晶棒 随工作台缓慢向下推进,一般经过5~10 h的切割,晶 棒完全通过线网,上千的晶片便切割完成。钢线张力 (一般设定在20~30N之间)在先进的闭环反馈控制下保 持不变。放线轮放出新的钢线,同时收线轮收集已用 过的钢线。切割晶棒最大直径是由导轮轴之间的空间 大小和工作台垂直行程决定的,常见的是6、8英寸晶 棒料。
2主流多线切割技术状况
2.1 国外多线切割设备的发展现状
多线切割机床属于大型精密数控机床,具有精度高、控制系统复杂、技 术难度大等特点,目前国际上比较知名的生产企业主要有瑞士Meyer Burger公司、HCT公司、日本Takatori公司、NTC公司等。 Meyer Burger公司生产的多线切割设备主要包括DS261, DS264, DS265, DS271, Brick Master这几个系列产品。一流的Si片表面质量和低的TTV 使DS261在半导体多线切割界有着重要地位,主要应用领域为12英寸 (300 mm ) Si片。具有快速高效,表面质量良好,完整的工件导向等特点。 DS264是一款高产量低成本的机型。由于使用了超细的切割线,大大 提高了切割效率和产量,另外模块化的设计使得操作更加方便。DS265 在高效率高质量,操作方便的基础上,增加了可供用户选择的功能;用户 可根据需要选择金刚石线锯或者切割用砂浆,而且该机型可快速转换至 小批量生产。DS271是DS系列的顶峰产品,它的装载长度达到了1020 mm,可以同时处理4根长度为250 mm的单晶,大大提高了产量,适应 光伏产业对Si片的高质、高量的要求。
硅片线痕分析

硅片线痕分析分类:线痕按表现形式分为杂质线痕、划伤线痕、密布线痕、错位线痕、边缘线痕等。
各种线痕产生的原因如下:1、杂质线痕:由多晶硅锭内杂质引起,在切片过程中无法完全去除,导致硅片上产生相关线痕。
表现形式:(1)线痕上有可见黑点,即杂质点。
(2)无可见杂质黑点,但相邻两硅片线痕成对,即一片中凹入,一片凸起,并处同一位置。
(3)以上两种特征都有。
(4)一般情况下,杂质线痕比其它线痕有较高的线弓。
改善方法:(1)改善原材料或铸锭工艺,改善IPQC检测手段。
(2)改善切片工艺,采用粗砂、粗线、降低台速、提高线速等。
其它相关:硅锭杂质除会产生杂质线痕外,还会导致切片过程中出现“切不动”现象。
如未及时发现处理,可导致断线而产生更大的损失。
2、划伤线痕:由砂浆中的SIC大颗粒或砂浆结块引起。
切割过程中,SIC颗粒“卡”在钢线与硅片之间,无法溢出,造成线痕。
表现形式:包括整条线痕和半截线痕,内凹,线痕发亮,较其它线痕更加窄细。
改善方法:(1)针对大颗粒SIC(2.5~3D50),加强IQC检测;使用部门对同一批次SIC先进行试用,然后再进行正常使用。
(2)导致砂浆结块的原因有:砂浆搅拌时间不够;SIC水分含量超标,砂浆配制前没有进行烘烤;PEG水分含量超标(重量百分比<0.5%);SIC成分中游离C(<0.03%)以及<2μm微粉超标。
其它相关:SIC的特性包括SIC含量、粒度、粒形、硬度、韧性等,各项性能对于切片都有很大的影响。
3、密布线痕(密集型线痕):由于砂浆的磨削能力不够或者切片机砂浆回路系统问题,造成硅片上出现密集线痕区域。
表现形式:(1)硅片整面密集线痕。
(2)硅片出线口端半片面积密集线痕。
(3)硅片部分区域贯穿硅片密集线痕。
(4)部分不规则区域密集线痕。
(5)硅块头部区域密布线痕。
改善方法:(1)硅片整面密集线痕,原因为砂浆本身切割能力严重不足引起,包括SIC颗粒度太小、砂浆搅拌时间不够、砂浆更换量不够等,可针对性解决。
硅片存在的问题及解决方法

硅片厚薄不均原因分析
环境
地面共振
车间温湿度变化大 导向条质量
辅料
槽距不均匀 小滑轮槽 距不均匀 无 切片机张力 不稳定
人员
树脂导向条错位,未放过滤袋/过滤网
工件和托板/工件夹紧螺丝未拧紧
线径不均匀
使用搅拌时间不到的砂浆
厚薄不 均
砂浆配置比例 主辊/导轮质量问题
工艺设计不科学
二次切割程序
工艺入门
切片工艺是设备(包括设备状态和设备准备),切割材料和基于耗材的切 割条件的综合。为确保好的切割和保持尽可能高的收率,就必须认真对待 下面每一步。
设备准备 砂浆 操作人
收率
硅块
钢线
Page 1
不同工艺参数的影响
回收砂浆
悬浮液 硅片厚度 温度 砂子粒径 TTV
线痕
砂浆流量
进给速率 设备稳定性
钢线磨损度
Page 3
花污片原因分析
环境
超纯水
辅料
柠檬酸 草 酸 乳酸 责任心差
人员
不遵守时间
违规脱胶 违规清洗
回收液质量
清洗剂质量
酸的更换量
花污片
超声波衰减
清洗剂更换量 温控不准确 预冲洗喷淋管 堵塞
自来水压力泵 时间控制器
清洗剂PLC控制系统
工艺
仪器
机器
Page 4
花污片预防和返工措施
1. 切割液掺有次氯酸,特别是回收液,对硅片腐蚀特别严重。(请品管 部门分析切割 液的成分) 2. 预冲洗的水压(2.5MPa),水质(中水),流量(5000l/h),角度(10),冲洗时 间(30-40min)等,总之预冲洗要硅片表面无明显脏污,才能进入脱胶 3. 脱胶时尽量全泡,水温50-60℃,加3%的草酸或柠檬酸或乳酸,自然倒伏。 4. 脱胶插片完毕,25-30℃纯水中超声10分钟,超声功率在2000w左右,水要循环。 (插片槽改成具有超声功能) 5. 清洗剂(不同厂家)大部分都是重量比为5%的比例,温度设为60℃,超声3-5分钟。 6. 关键是员工有没有执行和我们提供的设备工具能否满足需要. 7. 如果是个老厂,突然出现花污片了一般要在辅料上找问题(切割液 清洗液 回收液等). 8. 更换时一定要用标准容器,更换量视故硅片规格和数量而定.一般6和6.5寸8000pcs全换 一次,4000pcs时更换一半. 9. 污片返工关键技术:直接经过两槽清洗剂槽,时间3分钟,两槽纯水槽5分钟;花片返工关键 技术:0.2%的氢氟酸100l纯水,浸泡1分钟,先过纯水,再过清洗剂槽。合格率极低。 另外也可采用快速极冷法物理剥离赃物和硅片。
PV800线痕分析

PV800线痕分析分类:线痕按表现形式分为杂质线痕、划伤线痕、密布线痕、错位线痕、边缘线痕等。
各种线痕产生的原因如下:1、杂质线痕:由多晶硅锭内杂质引起,在切片过程中无法完全去除,导致硅片上产生相关线痕。
表现形式:(1)线痕上有可见黑点,即杂质点。
(2)无可见杂质黑点,但相邻两硅片线痕成对,即一片中凹入,一片凸起,并处同一位置。
(3)以上两种特征都有。
(4)一般情况下,杂质线痕比其它线痕有较高的线弓。
改善方法:(1)改善原材料或铸锭工艺,改善IPQC检测手段。
(2)改善切片工艺,采用粗砂、粗线、降低台速、提高线速等。
其它相关:硅锭杂质除会产生杂质线痕外,还会导致切片过程中出现“切不动”现象。
如未及时发现处理,可导致断线而产生更大的损失。
2、划伤线痕:由砂浆中的SIC大颗粒或砂浆结块引起。
切割过程中,SIC颗粒“卡”在钢线与硅片之间,无法溢出,造成线痕。
表现形式:包括整条线痕和半截线痕,内凹,线痕发亮,较其它线痕更加窄细。
改善方法:(1)针对大颗粒SIC(2.5~3D50),加强IQC检测;使用部门对同一批次SIC先进行试用,然后再进行正常使用。
(2)导致砂浆结块的原因有:砂浆搅拌时间不够;SIC水分含量超标,砂浆配制前没有进行烘烤;PEG水分含量超标(重量百分比<0.5%);SIC成分中游离C(<0.03%)以及<2μm 微粉超标。
其它相关:SIC的特性包括SIC含量、粒度、粒形、硬度、韧性等,各项性能对于切片都有很大的影响。
3、密布线痕(密集型线痕):由于砂浆的磨削能力不够或者切片机砂浆回路系统问题,造成硅片上出现密集线痕区域。
表现形式:(1)硅片整面密集线痕。
(2)硅片出线口端半片面积密集线痕。
(3)硅片部分区域贯穿硅片密集线痕。
(4)部分不规则区域密集线痕。
(5)硅块头部区域密布线痕。
改善方法:(1)硅片整面密集线痕,原因为砂浆本身切割能力严重不足引起,包括SIC颗粒度太小、砂浆搅拌时间不够、砂浆更换量不够等,可针对性解决。
多线切割硅片线痕问题研究
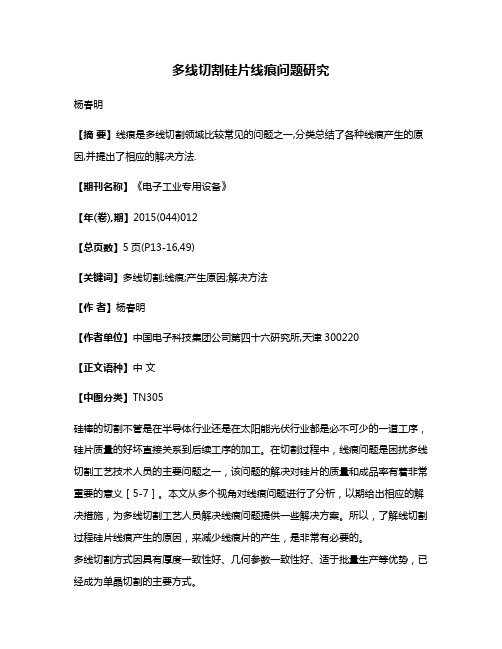
多线切割硅片线痕问题研究杨春明【摘要】线痕是多线切割领域比较常见的问题之一,分类总结了各种线痕产生的原因,并提出了相应的解决方法.【期刊名称】《电子工业专用设备》【年(卷),期】2015(044)012【总页数】5页(P13-16,49)【关键词】多线切割;线痕;产生原因;解决方法【作者】杨春明【作者单位】中国电子科技集团公司第四十六研究所,天津300220【正文语种】中文【中图分类】TN305硅棒的切割不管是在半导体行业还是在太阳能光伏行业都是必不可少的一道工序,硅片质量的好坏直接关系到后续工序的加工。
在切割过程中,线痕问题是困扰多线切割工艺技术人员的主要问题之一,该问题的解决对硅片的质量和成品率有着非常重要的意义[5-7]。
本文从多个视角对线痕问题进行了分析,以期给出相应的解决措施,为多线切割工艺人员解决线痕问题提供一些解决方案。
所以,了解线切割过程硅片线痕产生的原因,来减少线痕片的产生,是非常有必要的。
多线切割方式因具有厚度一致性好、几何参数一致性好、适于批量生产等优势,已经成为单晶切割的主要方式。
多线切割机的原理如图1所示,通过伺服电机控制的放线轮拉出的镀铜拉丝绕过几个起转向作用的滑轮,然后经过控制张力的控制器,在切割室内连续缠绕在2~4个主导轮上,形成一个在水平面上弥补的平行线网。
而在线网的上方,单晶的两侧布置有砂浆喷灌提供稳定的砂浆流量。
钢丝绕过线网后再通过滑轮和张力控制器回到收线轮上,在切割时高速运动的钢线携带附着在钢丝上的SiC磨料对硅棒进行研磨从而达到切割的目的。
在切割过程中钢线通过滑轮的引导,在导轮上形成一张线网,而待加工硅棒通过工作台的下降或上升实现工作的供给,把硅棒按一定晶格方向切割成片。
针对切割过程中随时可能出现的线痕现象,我们提取了某月某一周的质量统计数据,如图2所示。
3.1 线痕产生图3为线痕产生示意图。
3.2 线痕分类线痕按照形状分为单一线痕、硬质点线痕和均匀线痕。
关于近段时间切片一部出现线痕异常的分析
关于近段时间切片一部出现线痕异常的分析近段时间切片一部有个别机台出现整刀线痕,经各方面调查初步得认定为以下几个方面的原因:1、主辊、加工仓及绕线仓的清理不彻底2、晶棒模座与晶棒底座,螺丝未上紧,机器工件固定螺母的索紧度不够。
3、大砂浆罐底部砂浆未经搅拌直接使用4、切片工艺优化上存在着不足5、砂浆的换浆量、比重、粘度没有按照工艺标准6、来料碳化硅的质量不稳定(D50超标)7、钢丝的带砂量低、主辊磨损异常改善措施:1、针对各别操作工的对机器清理程度不重视1)、加强对员工上、下班会议的宣导。
2)、要求班长,副班长在上班期间,监督与巡查对机器的清理程度3)、对事故后发现有人为机台清理不干净的,要严肃处理4)、定时的对机台全面清洗(每月一次或每半月一次根据生产任务状况合理安排)5)、当班班长、主任在开机前对主辊的清洁度进行抽检6)对主辊的清理必须用丝光毛巾,严禁用普通白毛巾(普通白毛巾掉毛,致使线网清理不干净)。
7)对主辊清理完后要用手去触摸主辊,检查主辊有无毛刺、凹槽等,若有异常则更换主辊。
2、螺丝的索紧度1)、加强对粘胶房发棒索紧工的管理力度2)、要求操作工在领棒时必须进行自检3)、开机前一定要点检进给台上紧螺母3、砂浆罐底部砂浆的使用方法由于砂浆罐里的砂浆在长时间的搅拌中会产生一定的沉淀,导致砂浆罐底部砂浆的密度,以及砂的颗粒可能会比上层的大,所针对底部砂浆以前采用回抽150kg到同样的沙浆罐里在搅拌,可在实际生产中由于种种原因执行有一定的困难。
1)、请生产采购和设备部配合切片部,改造沙浆罐。
方案,切片部和技术部商讨制定,正在执行中。
4、切片工艺优化1)技术部已对现有工艺以及生产实况进行分析。
2)现以对19#--24#的工艺实验性的优化了线速。
5、换浆量、比重、粘度的控制。
严格控制一个循环8次的加浆量控制在每刀使用沙浆190kg(280÷8+155=190kg)严格控制每次的换浆量误差为±2.5kg换浆时一定要用数显叉车称准。
太阳能硅片密集性与硬点线痕的由来
太阳能硅片密集性与硬点线痕的由来
随着绿色能源的盛行,绿色能源当中的主力太阳能储能发电技术正成为最有可能代替传统能源的新能源。
但太阳能发电硅片较为脆弱,容易在生产或运输中因不当的操作和运输方式而产生各种损伤。
在本文中,小编将为大家介绍硅片上密集性线痕与硬点线痕是如何产生的。
密集性线痕
此线痕是由于砂浆的切割能力不足引起的。
切割能力的不足,主要为砂浆粘度不够、碳化硅微粉粘浮钢线少、砂浆不能很好的混合于悬浮液中,配合性不好。
但最常遇到的根本原因为,sic的切割强度偏低或者sic圆度系数过高即sic颗粒形状较圆,锋利的棱角较少。
sic的强度在其原料生产时便决定了,sic的微粉化并不会改变其强度。
如果sic本身材料的强度过低,切割时与硅棒作用,棱角被磨平钝化,切割能力不足,导致硅片表面出现大面积的均匀线痕;但如果在sic的微粉化过程中由于工艺不当,颗粒在切割前已经
被磨平,那同样也会造成切割能力不足导致密集性线痕。
对于后者,只要在高倍显微镜下进行来料检验即可观测到,就可避免生产中造成的损失,而对于前者则需要分析sic的成分和晶型强度再做判断。
目前很多厂家为了节约成本使用回收砂进行切割,但由于回收砂的质量不稳定,因此常有可能会面临由于切割能力不足导致的密集性线痕问题。
主要原因是回收时如果不同厂家砂浆混合,回收后的sic微粉之间、sic微粉与悬浮液之间存在配合性的问题,同时也可能存在sic颗粒已经过度磨损的问题。
这种使用回收砂造成的密集性线痕可以通过加大砂浆密度,降低工作台速度,减少使用回收砂的比例和加大砂浆更换量在一定程度上得到控制。
硬点线痕。
造成硅片的不良原因
原因有很多,但是真正工艺上的原因很少,主要还是认为的因素比较容易造成多的缺角(包括很多车间里面,比如说清洗,检验等隐裂:来料、预清洗、插片、清洗、拉运、分选;崩边:C角、胶面、加工、搬运;亮点:杂质;毛边:搬运、加工。
在太阳能电池制造过程中,用氢氧化钠和异丙醇制取单晶硅时表面发花,时什么原因?怎么样才能处理好呢?一般来说呢是有机物没有彻底的清洗干净!第二是氢氧化钠没有清洗干净!造成硅片线性斜的原因大概有哪些?1线速不能低于或超过砂浆的切割能力。
如果低于砂浆的切割能力,就会出现线痕片甚至断线;反之,如果超出砂浆的切割能力,就可能导致砂浆流量跟不上,从而出现厚薄片甚至线痕片等2砂浆流量要充分3钢线的张力硅片出现线痕可能是由那些原因引起的?这要看具体的发生状况及硅片线痕的走向:主要影响有砂浆的颗粒不均、跳线、主轮开槽及砂浆内有杂物。
1.原料--硅块本身就存在缺陷如杂质等,造成硅块密度不一致或者说分布不均匀,容易造成线痕;2.辅料--辅料质量不佳,如材质不对、杂质等,另外也有可能是辅料重复使用次数过多;3.设备--设备机台各项参数不应该版本统一,应该因机而各异;4.人为--可能性最大因数,有意无意或者消极工作导致. 但是目前线痕是多数公司存在的普遍现象主要看线痕比率体现线切水平和成片率 .可以从多方面考虑降低线痕: 一.原料从开方后检测下手,控制可能导致线痕的硅块流入线切工序二.辅料控制辅料质量和使用次数, 避免辅料造成的损失,得不偿失;三.设备完善的保养机制独有的工艺配方四.人员从积极方面考虑降低线痕率如奖励机制替代处罚机制主要是人员工作积极性毕竟人在生产中起主导作用五.完善的制程控制完善的制程检验过程, 及时发现并纠正不当操作六.完准的数据和反舞弊制度如各大数据程序支持和反舞弊制度说到底关键在人工艺设备操作数据等等都需要靠人完成密布线痕: 密布线痕是砂浆的问题,砂浆的切割能力低,要解决这个问题可以将切割速度调整慢一点,还要在浆料问题上做的更加细致。
pv600.硅片线痕分析
pv600.硅片线痕分析分类:线痕按表现形式分为杂质线痕、划伤线痕、密布线痕、错位线痕、边缘线痕等。
各种线痕产生的原因如下:1、杂质线痕:由多晶硅锭内杂质引起,在切片过程中无法完全去除,导致硅片上产生相关线痕。
表现形式:(1)线痕上有可见黑点,即杂质点。
(2)无可见杂质黑点,但相邻两硅片线痕成对,即一片中凹入,一片凸起,并处同一位置。
(3)以上两种特征都有。
(4)一般情况下,杂质线痕比其它线痕有较高的线弓。
改善方法:(1)改善原材料或铸锭工艺,改善IPQC检测手段。
(2)改善切片工艺,采用粗砂、粗线、降低台速、提高线速等。
其它相关:硅锭杂质除会产生杂质线痕外,还会导致切片过程中出现“切不动”现象。
如未及时发现处理,可导致断线而产生更大的损失。
2、划伤线痕:由砂浆中的SIC大颗粒或砂浆结块引起。
切割过程中,SIC颗粒“卡”在钢线与硅片之间,无法溢出,造成线痕。
表现形式:包括整条线痕和半截线痕,内凹,线痕发亮,较其它线痕更加窄细。
改善方法:(1)针对大颗粒SIC(2.5~3D50),加强IQC检测;使用部门对同一批次SIC 先进行试用,然后再进行正常使用。
(2)导致砂浆结块的原因有:砂浆搅拌时间不够;SIC水分含量超标,砂浆配制前没有进行烘烤;PEG水分含量超标(重量百分比<0.5%);SIC成分中游离C(<0.03%)以及<2μm微粉超标。
其它相关:SIC的特性包括SIC含量、粒度、粒形、硬度、韧性等,各项性能对于切片都有很大的影响。
3、密布线痕(密集型线痕):由于砂浆的磨削能力不够或者切片机砂浆回路系统问题,造成硅片上出现密集线痕区域。
表现形式:(1)硅片整面密集线痕。
(2)硅片出线口端半片面积密集线痕。
(3)硅片部分区域贯穿硅片密集线痕。
(4)部分不规则区域密集线痕。
(5)硅块头部区域密布线痕。
改善方法:(1)硅片整面密集线痕,原因为砂浆本身切割能力严重不足引起,包括SIC颗粒度太小、砂浆搅拌时间不够、砂浆更换量不够等,可针对性解决。
- 1、下载文档前请自行甄别文档内容的完整性,平台不提供额外的编辑、内容补充、找答案等附加服务。
- 2、"仅部分预览"的文档,不可在线预览部分如存在完整性等问题,可反馈申请退款(可完整预览的文档不适用该条件!)。
- 3、如文档侵犯您的权益,请联系客服反馈,我们会尽快为您处理(人工客服工作时间:9:00-18:30)。
硅片切割线痕的起因与降低方法
摘要线痕的存在会影响电池片的生产工艺。
是太阳能硅片生产中比较重要的一个问题。
本文分析了多晶太阳能级硅片产生线痕的原因.并针对各不同成因。
对降低和避免硅片线痕的措施进行了探讨。
关键词硅片线痕起因降低方法
前言
硅棒的切割不管是在半导体行业还是太阳能光伏行业都是必不可少的一道工序,硅片质量的好坏直接关系到后续工序的制造和加工。
线痕是影响硅片表面质量的一个比较重要因索。
半导体行业对硅片表面质量要求较高,但其线痕并不是一个大问题,因为相对而言其硅片较厚,切割过后有一抛光研磨过程可以去除线痕;而光伏行业的硅片非常薄(160-220um),因此研磨工艺在太阳能行业是不适用的。
线痕的存在还会影响电池片的生产工艺,易造成破片。
1.线痕的分类
线痕按照形状分有单一线痕,密集性线痕和硬点线痕。
硅片表面的单一线痕,有深有浅,一般线痕较小还是可以接受为合格片;密集性线痕体现为整个或者部分硅片表面出现多条由深至浅状的线痕;而硬点线痕出现的毫无规律,但是其形状似单一线痕。
但是线痕上可以明显看到有硬点的存在。
对于单晶来说,线痕主要有密集性线痕和单一线痕;对于多晶来说,三种都存在,即比单晶增加一种由于硬点造成的线痕。
2.单一线痕
单一线痕主要产生的原因和处理措施为:
1)跳线。
跳线造成的线痕一般会集中在晶棒的某一段,但有时也会整根棒跳线,从而导致切割后整根棒几乎都有线痕片。
造成跳线的主要原因为:
a,杂质(碎硅片,砂浆中的杂质)进入线槽或者粘附于线网,若上一次切割完毕后线网未清理干净或者砂浆过滤袋质量出现问题,则很容易发生这种情况;
b, 导轮磨损过大,导轮使用寿命有限制,超过一定时间则需要更换导轮;
c,钢线张力太小,线弓过大产生滑移,一般在工艺稳定的情况下,这种情况不易发生,如为此种情况,须适当调整工艺;
d,硅棒对接位置不好也易引起跳线。
为了尽量避免跳线,每次切割完毕后清理工作要做到位,确保线网上的杂质都被气枪吹尽,切割前砂浆循环足够时间,使砂浆中携带的杂质都被有效过滤,每次切割前确认导轮使用时间是否超出限制,如果超出及时更换。
2) 断线。
断线后的晶棒即使能够挽救回来,或多或少会产生线痕片。
影响断线的主要因素为:
a,钢丝本身缺陷,如①钢丝强度偏底;②钢丝内含夹杂物,钢丝的断面照片可以明显看到成不相容相的颗粒;③钢丝存在表面缺陷,当切割受力时这些杂质和缺陷成为应力承受的薄弱部位,易于断裂。
b,收(放)线端异常受力,如①工字轮变形;②放线端线头穿错也称压线;③收(放)线端工字轮毛刺,收、放线时钢丝被刮在其上引起断线;④收(放)线端走线部件即滑轮、滚套的表面质量和工作状态,放线轮的跟随性不佳,滑轮滚套异常磨损,张力检测设备故障等引起收(放)线侧张力的波动或钢丝异常受力断线;⑤收线端排线质量不平整引起收线张力急剧跳动从而断线;⑥收(放)线侧张力瞬时波动超过了钢丝的承载极限,或承受异常应力(如剪切应力)作用引起断线;
c,切割工艺出现异常,①张力设定合理性;②砂浆配置参数,砂浆配比或质量影响到钢丝携带砂浆量及切削能力,直接对钢线的磨损量造成影响,随着磨损量的增大,一方面钢线表面缺陷增多,另一方面载荷横断面积减少,一旦钢线的磨损量超过所能承受的范围,钢线断裂;③杂质,砂浆中混入硬质异物(如碎片),或在过线轮、导轮上有硬质颗粒卡住对钢丝造成刮伤,同上面也提到的杂质异物,轻则跳线,重则断线;④粘胶不当或硅棒粘接位置不好等原因的跳线,导致某些线槽内有多根钢丝相互压线引起断线。
由此可见,控制断线首先要求有比较良好钢线的质量,其次是要控制好切割的工艺,其中砂浆的配置是一个比较重要的环节。
砂浆由SiC和悬浮液PEG混合配置而成,SiC颗粒较为细小,根据粒径范围分为不同规格,一般粒子越细,切出的硅片表面越光滑,但对应的切割能力也下降。
微粉由于颗粒细,易在包装、运输、存放过程中挤压团结,因此配置配制沙浆是时倒料应慢,避免猛倒造成微粉沉底结块搅拌不开,造成砂浆密度与预期的不一致或者不均匀而影响切割。
碳化硅微粉在空气中极容易受潮团结,分散性降低,在料浆中形成假性颗粒物和团积物,砂浆过搅拌也会吸收水分造成此问题,因此应避免微粉裸漏在空气中时间过长和过搅拌,烘砂的目的也在于此,一般把碳化硅微粉在80-90度烘箱里,烘8小时以上,来优化碳化硅微粉的各项指标。
当然砂浆配置如果采用集中供应系统,会减少诸多人工配置的不稳定因素,更利于砂浆质量的稳定。
断线后的补救措施是比较繁琐和耗时的,根据断线的部位和切割的比例有不同的处理方法:
一、断线情况发生在进线端,我们可以采用倒走线的方式,把张力臂的力更换一下,
然后进行反向切割,切割速度一定要慢,确保在反向切割的途中不会出现意外;
二、断线情况发生在出线端,继续接上后把接的线头绕到收线轮上(多绕几圈);
三、断线情况发生在线网中间,将线网出线端到断线的那段线网剪断,调整好切割室的
滑轮,接好钢线,然后把线头绕到收线轮上(多绕几圈);
四、两头断线:①切割30%以内,直接把工作台抬起,用乙二醇对晶棒进行浸泡,洗去
硅片上砂浆,使片子完全张开,重新编制线网,慢走线,把晶棒压人线网内,继续切割;②切割30%以上,将晶棒工作台抬起,用水将硅片冲洗干净后使用吹风机吹干到硅片全部自动分离时重新将晶棒压入线网。
也有采用钢线焊接仪,可以在断线的时候把钢线焊接起来,然后采取慢走线的方式把焊接的地方走出来绕到收线轮上。
但是到目前为止如果钢线缠绕到导轮上,这种情况现在还没有有效的解决方法。
3)停机。
切片机在有些报警下会自动停机,等报警消除后重新开始切割,基体的停机报警项可从机器的维护说明上查得,因为机器的停顿,重新启动后,由于导轮心震,刚线不能完全按原位置切割,线痕于是产生了,这种情况相对于前两种较少。
4)粘胶过多。
粘胶过多引起的线痕一般在靠进粘胶面附近切割快结束的倒角处,由于胶水涂抹过多溢出,刮胶不彻底或者有的胶水固化时间较快来不及刮胶,导致切割时钢线带胶切割,而携带砂浆的能力下降,引起切削线痕。
因此胶量要严格控制,从成本控制的角度,这也是
有益的。
如果使用自动粘胶系统可以大大的排除这些人为的不利因素,也会减少因粘胶问题而造成的掉棒损失。
5)进刀口钢线波动。
由于刚开始切割,钢线处在不稳定状态,钢线的波动产生进刀口线痕,进线点质硬,比如多晶的切割一般会由此问题,加垫层(导向条)可消除线摆。
6)钢线磨损过度(但未造成断线)。
此线痕一般出现于硅棒的后面,钢线磨损、带沙量低、切削能力下降、线膨胀系数增大引起的线痕。
7)硅片切割第一刀出现线痕。
可能为碳化硅微粉有大颗粒物,钢线的张力太小产生的位移划错,钢线的张力太大、线弓太小料浆带不过去,线速过高、带沙浆能力降低等等。
对于钢线张力问题,略作调整即可,而碳化硅微粉有大颗粒物,经过一刀切割后微量的大颗粒变细或者变钝.也就不影响正常切割。
3.密集性线痕
此线痕是由于砂浆的切割能力不足引起的。
切割能力的不足,主要为砂浆粘度不够、碳化硅微粉粘浮钢线少、砂浆不能很好的混合于悬浮液中,配合性不好。
但最常遇到的根本原因为,sic的切割强度偏低或者sic圆度系数过高即sic颗粒形状较圆,锋利的棱角较少。
sic 的强度在其原料生产时便决定了,sic的微粉化并不会改变其强度。
如果sic本身材料的强度过低,切割时与硅棒作用,棱角被磨平钝化,切割能力不足,导致硅片表面出现大面积的均匀线痕;但如果在sic的微粉化过程中由于工艺不当,颗粒在切割前已经被磨平,那同样也会造成切割能力不足导致密集性线痕。
对于后者,只要在高倍显微镜下进行来料检验即可观测到,就可避免生产中造成的损失,而对于前者则需要分析sic的成分和晶型强度再做判断。
目前很多厂家为了节约成本使用回收砂进行切割,但由于回收砂的质量不稳定,因此常有可能会面临由于切割能力不足导致的密集性线痕问题。
主要原因是回收时如果不同厂家砂浆混合,回收后的sic微粉之间、sic微粉与悬浮液之间存在配合性的问题,同时也可能存在sic颗粒已经过度磨损的问题。
这种使用回收砂造成的密集性线痕可以通过加大砂浆密度,降低工作台速度,减少使用回收砂的比例和加大砂浆更换量在一定程度上得到控制。
4.硬点线痕
对于多晶,比单晶多一种造成线痕的原因,那就是硬点。
此线痕与硅片切割的工艺和辅料无关,主要取决于多晶铸锭的原料和工艺。
5.结论
由上文所述,钢丝的明显质量缺陷会引起线痕的发生,但在钢丝无明显缺陷时,切割工艺的适当优化可以降低线痕的出现机率,砂浆的过滤、线网的清理和胶量的控制能很大程度的减少线痕的产生。
SiC的质量对硅片的切割有着重大的影响,一旦SiC的质量产生问题则会产生大量的密集性线痕片而造成巨大损失。
因此对辅料的监控和检验有着犹为重要的意义。
同样对于多晶的硬点线痕,控制硅原料质量和坩埚氮化硅涂层工艺比较重要。