硅刻蚀
单晶硅刻蚀工艺原理
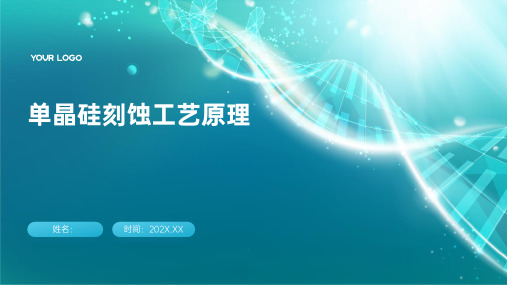
刻蚀设备的结构和工作原理
01
02
干法刻蚀设备结构和工作原理
干法刻蚀设备通常由气体供给系统、 反应室和抽气系统组成。 气体供给系统用于提供刻蚀气体, 例如氟化氢等。 反应室是刻蚀反应的主要场所,其 中单晶硅样品与刻蚀气体发生反应。 抽气系统用于抽出反应室内的废气。
湿法刻蚀设备结构和工作原理
湿法刻蚀设备通常由溶液供应系统、 反应室和排液系统组成。 溶液供应系统用于提供刻蚀溶液, 例如酸性溶液或碱性溶液。 反应室是刻蚀反应的主要场所,其 中单晶硅样品与刻蚀溶液发生化学 反应。 排液系统用于排出反应室内的废液。
流量控制的方法和技巧
可以使用流量计来实时监测刻蚀槽内的流量 需要校准流量计,以确保准确的流量控制 根据具体的刻蚀工艺需求,调整并优化流量控制参数
压力控制参数
压力对刻蚀速率和表面质量的影 响
适当的压力可以加快刻蚀速率,但过高的压 力可能导致不均匀刻蚀或过刻 压力的变化还可以影响晶圆表面的质量和平 整度
单晶硅刻蚀工艺原理
姓名:
时间:202X.XX
Catalogue 目录
1. 单晶硅刻蚀工艺概述
2. 单晶硅刻蚀工艺参数
3. 单晶硅刻蚀工艺设备
4. 单晶硅刻蚀工艺的问题与
解决方法
5. 单晶硅刻蚀工艺的优化与
改进
01
单晶硅刻蚀工艺概述
单晶硅材料及其应用
单晶硅的特性与优势
单晶硅具有高纯度和优异的电学特性。 单晶硅具有优异的机械特性和热稳定性。 单晶硅在半导体行业中广泛应用。
适当的物质浓度控制可以改善刻蚀的剖面形貌,并 避免过度刻蚀或残留物的产生
物质浓度控制的方法和调 节策略
可以使用浓度计来监测刻蚀槽内的物质浓度,并进 行实时调节
硅刻蚀-工作报告
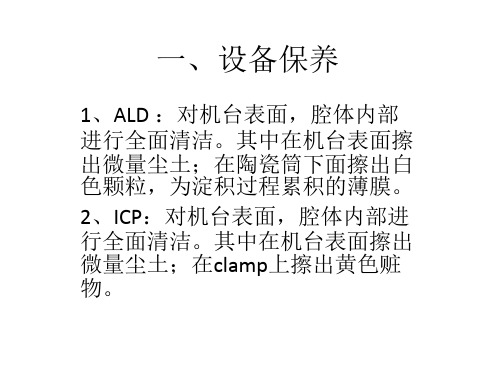
四、工作任务
1、设备维修:查明ICP工艺腔破真 空后无法抽下去的原因。 2、工艺开发计划:如需要,可摸 索SiO2、SiN槽刻蚀工艺。
三、设备使用
1、ALD:无人使用。 2、ICP:9.2、9.5日林猛各使用一次,刻 蚀Ge 3um,做电子束光刻标记。此工艺 是将2吋Ge片粘到4吋SiO2片上后再刻蚀。 从Ge片表面颜色来看,刻蚀很不均匀,可 能是散热不均匀导致。 9.10日樊捷闻刻蚀SiO2槽,陪片刻蚀结果 为,中间慢,边缘快;刻蚀SiO2光片(Si 片表面只有一层均匀的SiO2)均匀性良好, 故此结果跟工艺有关。此工艺为刻蚀SiO2 线条条件。
一、设备保养
1、ALD :对机台表面,腔体内部 进行全面清洁。其中在机台表面擦 出微量尘土;在陶瓷筒下面擦出白 色颗粒,为淀积过程累积的薄膜。 2、ICP:对机台表面,腔体内部进 行全面清洁。其中在机台表面擦出 微量尘土;在clamp上擦出黄色赃 物。
二、设备维护
1、ALD:状态良好,可正常运行。 2、ICP:做保养时,需破真空。之后抽真空, 工艺腔的压力无法被其对应的干泵抽下,导 致分子泵无法启动。后将传送腔与工艺腔之 间的阀门打开,用传送腔的干泵抽工艺腔的 真空,可以抽动,当压力降到100Torr以下时, 关闭阀门,用工艺腔干泵抽,就可以往下抽, 当降到80Torr时,分子泵开启。 此情况,在上学期末,放假前两天保养时也 出现过,对此,牛津工程师也很是不解。这 两天他们会派人过来维修。
多晶硅刻蚀工艺

多晶硅刻蚀工艺
多晶硅刻蚀是一种重要的半导体工艺步骤,它可以通过化学反应
将多晶硅转化为低电阻或高电阻硅材料。
该工艺通常使用非晶硅或其
他绝缘材料作为掩模,以控制刻蚀模式和形状。
多晶硅的刻蚀过程可以通过干法或湿法来实现。
在干法工艺中,
刻蚀介质通常是气体混合物,如氟化物和氯化物。
这种方法足够快速,对环境的污染较小,但需要高温和特殊的反应器。
在湿法工艺中,刻
蚀介质是强酸和强碱,例如氢氟酸和五氧化二磷。
这种方法刻蚀速度
较慢,但比较容易操作,成本也相对较低。
多晶硅的刻蚀必须控制好方向性和等深度,以获得高质量的硅材料。
此外,刻蚀过程中还需要注意反应的选择性,以免影响整个工艺
流程的稳定性和可靠性。
总之,多晶硅刻蚀工艺是制造半导体器件中的重要步骤,经过多
年的研究和改进已经变得更为成熟、可靠。
背硅刻蚀工艺
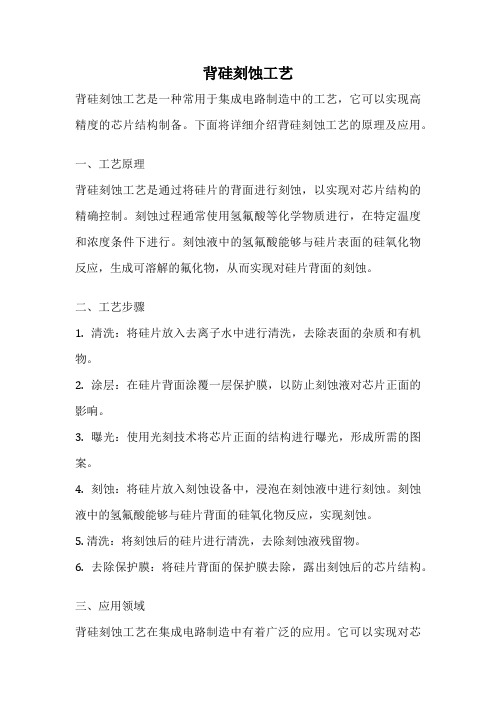
背硅刻蚀工艺
背硅刻蚀工艺是一种常用于集成电路制造中的工艺,它可以实现高精度的芯片结构制备。
下面将详细介绍背硅刻蚀工艺的原理及应用。
一、工艺原理
背硅刻蚀工艺是通过将硅片的背面进行刻蚀,以实现对芯片结构的精确控制。
刻蚀过程通常使用氢氟酸等化学物质进行,在特定温度和浓度条件下进行。
刻蚀液中的氢氟酸能够与硅片表面的硅氧化物反应,生成可溶解的氟化物,从而实现对硅片背面的刻蚀。
二、工艺步骤
1. 清洗:将硅片放入去离子水中进行清洗,去除表面的杂质和有机物。
2. 涂层:在硅片背面涂覆一层保护膜,以防止刻蚀液对芯片正面的影响。
3. 曝光:使用光刻技术将芯片正面的结构进行曝光,形成所需的图案。
4. 刻蚀:将硅片放入刻蚀设备中,浸泡在刻蚀液中进行刻蚀。
刻蚀液中的氢氟酸能够与硅片背面的硅氧化物反应,实现刻蚀。
5. 清洗:将刻蚀后的硅片进行清洗,去除刻蚀液残留物。
6. 去除保护膜:将硅片背面的保护膜去除,露出刻蚀后的芯片结构。
三、应用领域
背硅刻蚀工艺在集成电路制造中有着广泛的应用。
它可以实现对芯
片背面的结构制备,例如背面电极、背面通孔等。
同时,背硅刻蚀工艺还可用于形成背面反射层,提高光电器件的效率。
此外,背硅刻蚀工艺还可以用于刻蚀硅片背面的缺陷,提高硅片的质量。
背硅刻蚀工艺是一种重要的集成电路制造工艺,它可以实现对芯片背面结构的精确制备。
在当前的半导体技术发展中,背硅刻蚀工艺的应用将会越来越广泛。
通过不断优化工艺参数和设备性能,背硅刻蚀工艺将能够实现更高精度的芯片制备,推动集成电路技术的发展。
dse刻蚀设备原理
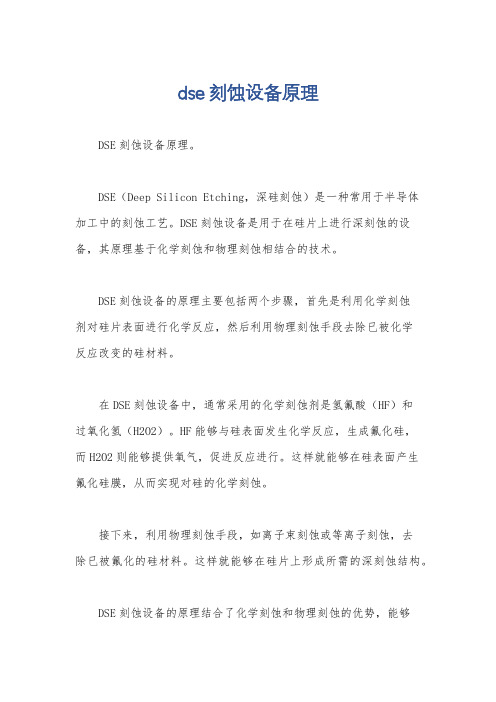
dse刻蚀设备原理
DSE刻蚀设备原理。
DSE(Deep Silicon Etching,深硅刻蚀)是一种常用于半导体
加工中的刻蚀工艺。
DSE刻蚀设备是用于在硅片上进行深刻蚀的设备,其原理基于化学刻蚀和物理刻蚀相结合的技术。
DSE刻蚀设备的原理主要包括两个步骤,首先是利用化学刻蚀
剂对硅片表面进行化学反应,然后利用物理刻蚀手段去除已被化学
反应改变的硅材料。
在DSE刻蚀设备中,通常采用的化学刻蚀剂是氢氟酸(HF)和
过氧化氢(H2O2)。
HF能够与硅表面发生化学反应,生成氟化硅,
而H2O2则能够提供氧气,促进反应进行。
这样就能够在硅表面产生
氟化硅膜,从而实现对硅的化学刻蚀。
接下来,利用物理刻蚀手段,如离子束刻蚀或等离子刻蚀,去
除已被氟化的硅材料。
这样就能够在硅片上形成所需的深刻蚀结构。
DSE刻蚀设备的原理结合了化学刻蚀和物理刻蚀的优势,能够
实现对硅材料的高效深刻蚀,广泛应用于半导体器件制造、MEMS (Micro-Electro-Mechanical Systems,微机电系统)制造等领域。
总的来说,DSE刻蚀设备的原理是利用化学刻蚀和物理刻蚀相
结合的技术,通过化学反应和物理去除的方式实现对硅材料的深刻蚀,为半导体加工和微纳加工提供了重要的工艺手段。
硅的干法刻蚀简介

→着硅珊MOS器件的出现,多晶硅渐渐成为先进器件材料的主力军。
除了用作MOS栅极之外多晶硅还广泛应用于DRAM的深沟槽电容极扳填充,闪存工艺中的位线和字线。
这些工艺的实现都离不开硅的干法刻蚀技术其中还包括浅槽隔离的单晶硅刻蚀和金属硅化物的刻蚀。
为了满足越来越苛刻的要求,业界趋向于采用较低的射频能量并能产生低压和高密度的等离子体来实现硅的干法刻蚀。
感应耦合等离子刻蚀技术(ICP)被广泛应用于硅及金属硅化物刻蚀,具有极大技术优势和前景。
它比典型的电容耦合(CCP)等离子刻蚀技术高出10 ̄20倍。
此外,其对离子浓度和能量的独立控制扩大了刻蚀工艺窗口及性能。
硅栅(Poly Gate)的干法刻蚀:随着晶体管尺寸的不断缩小对硅栅的刻蚀就越具有挑战性。
这种挑战体现在对关键尺寸(CD)及其均匀性的控制,即对栅氧化层选择比的提高,对剖面轮廓的一致性控制以及减少等离子导致的损伤。
因为受到光刻线宽的限制,为达到最后的CD 线宽要求往往需要先对光阻进行缩小处理,然后进一步往下刻蚀。
BARC打开后,再以光阻为阻挡层将TEOS 打开。
接着把剩余的光阻去除,再以TEOS作为阻挡层对硅栅进行刻蚀。
为了保护栅极氧化层不被损伤,通常要把硅栅的刻蚀分成几个步骤:主刻蚀、着陆刻蚀和过刻蚀。
主刻蚀通常有比较高的刻蚀率但对氧化硅的选择比较小。
通过主刻蚀可基本决定硅栅的剖面硅的干法刻蚀简介应用材料中国,葛强轮廓和关键尺寸。
着陆刻蚀通常对栅极氧化层有比较高的选择比以确保栅极氧化层不被损伤。
一旦触及到栅极氧化层后就必须转成对氧化硅选择比更高的过刻蚀步骤以确保把残余的硅清除干净而不损伤到栅极氧化层。
CL2,HBr,HCL是硅栅刻蚀的主要气体,CL2和硅反应生成挥发性的SiCl4而HBr和硅反应生成的SiBr4 同样具有挥发性。
通常会在这些主刻蚀气体中加入小流量的氧气,一方面是为了在侧壁生成氧化硅从而增加对侧壁的保护;另一方面也提高了对栅极氧化层的选择比。
第七讲 硅的深刻蚀技术
硅的深刻蚀技术硅RIE刻蚀的基本原理含有F, Cl, Br,I单质或者化合物气体均可以作为硅的刻蚀剂,添加一些辅助气体有助于提高它的选择性,常用刻蚀剂组合如:CF4/O2, CF2CL2, CF3CL, SF6/O2/CL2,CCL4, NF3, CCL4, CHF3等不管上述哪一种化合物作为刻蚀剂,在等离子体中都会存在大量的卤素原子,它们以化学吸附方式与硅表面结合,在没有外力作用的情况下,反应生成的产物分离的速率很慢,特别是Cl,Br,I原子更是如此,构成了Si与其它活性成份进一步接触的障碍,但是,当它们得到电子之后,就会与Si 一起离开表面,所以,重掺杂的N型硅会显著增加自发反应的速度。
这种反应是热力学上自发进行的反应,只要使它们相遇便能够促成反应,因此它是各向同性的,从热力学观点出发,按照F, Cl, Br, I顺序,它们与Si自发反应的能力逐渐减弱,I并不常用,可能是它的蒸汽压比较低,与硅的化合物不那么稳定。
各向同性刻蚀的典型剖面高深宽比刻蚀的机理RIE刻蚀效应被分为两种机制:溅射刻蚀化学反应刻蚀研究表明,具有20-40eV以上能量的粒子均有可能通过轰击而使固体表面的原子脱离原来位置,形成溅射刻蚀,它主要是借助离子轰击实现的。
前面曾经讲到离子束刻蚀,方向性是它的重要特征。
化学刻蚀则是借助接触吸附,各向同性地进行,它主要是中性粒子完成的,它的存在需要满足两个方面的条件:1.体系中存在能够形成挥发性化合物的基础物质,并且能够扩散到达硅表面2.最终要挥发的化合物必须有足够的稳定性,以便它一旦形成,便有足够稳定性以减少再次分解的几率。
同时,要创造条件促成其尽快脱离反应界面,如低气压等其实简单地将它们二者相加并不能很好地解释各种实验现象,研究人员发现,中性粒子化学作用与离子轰击相结合所能够产生的刻蚀速率,会十倍于它们单独作用的速率和。
这种倍增的效应被认为是通过提供反应活化能的原理实现的:对于一个普通的化学反应,按照动力学观点,其刻蚀速率:其中Ea是该反应所需要的活化能,也许离子轰击提供了这一克服势垒所必须的能量。
一种改善深硅刻蚀侧壁粗糙度的方法与流程
一种改善深硅刻蚀侧壁粗糙度的方法与流程深硅刻蚀是一种常用的制备微纳结构的工艺,但其容易导致侧壁粗糙度较高。
以下是一种改善深硅刻蚀侧壁粗糙度的方法与流程:1. 前处理:在进行深硅刻蚀之前,首先进行前处理,包括清洗硅片和去除表面污染物,可以采用溶液浸泡或电化学方法。
2. 选择合适的刻蚀气体和条件:选择合适的刻蚀气体和刻蚀条件是改善侧壁粗糙度的关键。
常用的刻蚀气体有CF4、SF6和Cl2等。
合适的刻蚀条件包括功率、气压和刻蚀时间等。
通过调节这些参数,可以控制硅片的表面反应速率,从而改善侧壁粗糙度。
3. 预刻蚀步骤:在进行深硅刻蚀之前,进行一定时间的预刻蚀步骤。
预刻蚀可以去除硅片表面的较高粗糙度,平整表面,并且改善表面反应速率的均匀性。
预刻蚀的时间可以根据实际情况进行调整。
4. 加入掺杂剂:在刻蚀气体中加入适量的掺杂剂,例如Boron Trichloride(BCl3)或Phosphine (PH3)等。
这些掺杂剂可以改变气体的化学反应性质,提高表面反应速率的均匀性,并降低表面粗糙度。
5. 控制刻蚀速率:控制深硅刻蚀的速率也可以改善侧壁粗糙度。
通常情况下,较低的刻蚀速率意味着较高的侧壁质量。
通过调节功率和气压等参数,可以控制刻蚀速率。
6. 后处理:在刻蚀完成后,进行后处理步骤。
后处理可以包括清洗和去除残余物质等步骤,以进一步改善侧壁粗糙度。
总之,改善深硅刻蚀侧壁粗糙度的方法与流程包括前处理、选择合适的刻蚀气体和条件、预刻蚀,加入掺杂剂、控制刻蚀速率和后处理等步骤。
通过这些步骤的合理组合和调节,可以有效改善深硅刻蚀侧壁的粗糙度。
单晶硅刻蚀工艺原理
单晶硅刻蚀工艺原理
单晶硅刻蚀是半导体制造过程中的一个重要步骤,它通过选择性地去除硅材料或薄膜层来形成所需的结构和图形。
单晶硅刻蚀工艺一般包括下列几个步骤:
1. 光刻工艺
- 首先在硅基底上涂覆光阻,通过光刻曝光和显影过程形成所需的图形。
- 正性光阻在曝光区域溶解,负性光阻在曝光区域固化。
2. 刻蚀工艺
- 干法刻蚀:利用等离子体产生的活性离子或自由基对硅进行物理和化学反应,去除未保护区域。
主要有反应离子刻蚀(RIE)和等离子体增强化学气相沉积(PECVD)等。
- 湿法刻蚀:将硅浸没在液体腐蚀剂中,化学反应溶解未保护区域。
常用的腐蚀液包括氢氟酸(HF)、氨水和过氧化氢的混合液。
3. 去胶
去除残余的光阻保护层,可采用干式或湿式剥离的方式。
4. 检查与测试
对刻蚀结构进行检查,确保符合设计要求和电路功能。
通过精确控制刻蚀参数和条件,如温度、压力、气体流量、功率等,可实现对单晶硅的各向异性和垂直刻蚀,从而获得所需的精细结构。
单
晶硅刻蚀工艺广泛应用于集成电路、MEMS器件和其他微纳米结构的制造。
背硅刻蚀工艺
背硅刻蚀工艺背硅刻蚀工艺是一种在半导体加工中常用的工艺技术,它能够实现对硅片背面的刻蚀,以达到特定的目的。
本文将介绍背硅刻蚀工艺的原理、步骤以及应用。
背硅刻蚀工艺是一种用于改变硅片背面特性的技术。
在半导体制造过程中,背硅刻蚀工艺被广泛应用于提高器件性能、降低功耗以及改善工艺可靠性等方面。
通过背硅刻蚀工艺,可以实现对硅片背面的刻蚀,以去除表面缺陷、降低电阻、改善光学特性等。
背硅刻蚀工艺的主要原理是利用化学反应将硅片背面的硅层溶解掉。
具体来说,背硅刻蚀过程中会使用一种特定的刻蚀液,该刻蚀液中含有一种或多种能够与硅反应的化学物质。
当硅片浸泡在刻蚀液中时,刻蚀液会与硅发生反应,并将硅层逐渐溶解掉,最终形成所需的背面结构。
背硅刻蚀工艺的步骤包括清洗、涂覆、曝光、显影、刻蚀等。
首先,需要对硅片进行清洗,以去除表面污染物和氧化层。
然后,在硅片背面涂覆一层光刻胶,用于保护所需保留的背面结构。
接下来,将经过掩膜制备的硅片进行曝光和显影,形成所需的背面图案。
最后,将硅片浸泡在刻蚀液中,进行背硅刻蚀,直到得到所需的背面结构。
背硅刻蚀工艺在半导体制造中有着广泛的应用。
例如,在太阳能电池制造过程中,背硅刻蚀工艺可以提高光电转换效率;在集成电路制造中,背硅刻蚀工艺可以降低晶体管的电阻,提高器件性能。
此外,背硅刻蚀工艺还可以应用于传感器制造、光学器件制造等领域。
总结起来,背硅刻蚀工艺是一种在半导体加工中常用的工艺技术。
通过化学反应将硅片背面的硅层溶解掉,以改变硅片背面的特性。
背硅刻蚀工艺包括清洗、涂覆、曝光、显影、刻蚀等步骤,广泛应用于半导体制造中的各个领域。
该工艺能够提高器件性能、降低功耗、改善工艺可靠性等。
通过背硅刻蚀工艺,可以实现对硅片背面的刻蚀,以达到特定的目的。
- 1、下载文档前请自行甄别文档内容的完整性,平台不提供额外的编辑、内容补充、找答案等附加服务。
- 2、"仅部分预览"的文档,不可在线预览部分如存在完整性等问题,可反馈申请退款(可完整预览的文档不适用该条件!)。
- 3、如文档侵犯您的权益,请联系客服反馈,我们会尽快为您处理(人工客服工作时间:9:00-18:30)。
硅刻蚀技术简介
在半导体制程中,单晶硅与多晶硅的刻蚀通常包括湿法刻蚀和干法刻蚀,两种方法各有优劣,各有特点。
湿法刻蚀即利用特定的溶液与薄膜间所进行的化学反应来去除薄膜未被光刻胶掩膜覆盖的部分,而达到刻蚀的目的。
因为湿法刻蚀是利用化学反应来进行薄膜的去除,而化学反应本身不具方向性,因此湿法刻蚀过程为等向性。
湿法刻蚀过程可分为三个步骤:1) 化学刻蚀液扩散至待刻蚀材料之表面;2) 刻蚀液与待刻蚀材料发生化学反应; 3) 反应后之产物从刻蚀材料之表面扩散至溶液中,并随溶液排出。
湿法刻蚀之所以在微电子制作过程中被广泛的采用乃由于其具有低成本、高可靠性、高产能及优越的刻蚀选择比等优点。
但相对于干法刻蚀,除了无法定义较细的线宽外,湿法刻蚀仍有以下的缺点:1) 需花费较高成本的反应溶液及去离子水;2) 化学药品处理时人员所遭遇的安全问题;3) 光刻胶掩膜附着性问题;4) 气泡形成及化学腐蚀液无法完全与晶片表面接触所造成的不完全及不均匀的刻蚀。
基于以上种种原因,这里就以下三个方面着重介绍下干法刻蚀。
1、硅等离子体刻蚀工艺的基本原理
干法刻蚀是利用射频电源使反应气体生成反应活性高的离子和电子,对硅片进行物理轰击及化学反应,以选择性的去除我们需要去除的区域。
被刻蚀的物质变成挥发性的气体,经抽气系统抽离,最后按照设计图形要求刻蚀出我们需要实现的深度。
干法刻蚀可以实现各向异性,垂直方向的刻蚀速率远大于侧向的。
其原理如图所示,生成CF基的聚合物以进行侧壁掩护,以实现各向异性刻蚀。
刻蚀过程一般来说包含物理溅射性刻蚀和化学反应性刻蚀。
对于物理溅射性刻蚀就是利用辉光放电,将气体解离成带正电的离子,再利用偏压将离子加速,溅击在被蚀刻物的表面,而将被蚀刻物质原子击出(各向异性)。
对于化学反应性刻蚀则是产生化学活性极强的原(分)子团,此原(分)子团扩散至待刻蚀物质的表面,并与待刻蚀物质反应产生挥发性的反应生成物(各向同性),并被真空设备抽离反应腔。
2、硅刻蚀工艺的要求
对于早期器件的刻蚀工艺要求,一般来说要求深度、选择比、掩膜的完全传递和侧壁的陡直度。
随着新型器件的不断出现,对于刻蚀工艺也提出了越来越多的要求,形貌方面比如圆包刻蚀、梯形刻蚀、三角刻蚀等;槽的状态方面要求很高的深宽比、V形槽、保证深度的情况下要求低损伤等等,要想达到各种要求,除了需要我们对影响刻蚀工艺的因素有足够的了解,还需要我们对于光刻工艺和掩膜条件有相当理解。
3、影响硅刻蚀工艺的重要因
影响刻蚀工艺的因素分为外部因素和内部因素。
外部因素主要包括设备硬件的配置以及环境的温度、湿度影响,对于操作人员来说,外部因素只能记录,很难改变,要做好的就是优化工艺参数,实现比较理想的实验结果。
内部因素就是在设备稳定的情况下对工艺结果起到决定性作用,以下所列因素对于刻蚀速率、形貌等均起到重要作用。
1)、工作压力的选择:对于不同的要求,工作压力的选择很重要,压力取决于通气量和泵的抽速,合理的压力设定值可以增加对反应速率的控制、增加反应气体的有效利用率等。
2)、RF功率的选择:RF功率的选择可以决定刻蚀过程中物理轰击所占的比重,对于刻蚀速率和选择比起到关键作用。
RF功率、反应气体的选择和气体通入的方式可以控制刻蚀过程为同步刻蚀亦或是BOSCH工艺。
3)、ICP功率:ICP功率对于气体离化率起到关键作用,保证反应气体的充分利用,我们的设备ICP功率最大值为2500W。
在气体流量一定的情况下,随着ICP功率的增加气体离化率也相应增加,可增加到一定程度时,离化率趋向于饱和,此时再增加ICP功率就会造成浪费。
4)、衬底温度和反应室温度:温度控制对于衬底本身和掩膜(特别是胶掩膜)的意义重大,目前大多数设备采用的是氦气冷却衬底背面的方式,背面控制在20℃左右。
5、反应气体的选择和配比:目前我们的设备通了四路气体SF6 、C4F8 、 O2和CF4 。
其中SF6和C4F8作为反应气体参与刻蚀过程,O2和CF4作为清洗气体负责设备的CLEAN过程。
选择合适的流量和气体通入的时间比会很大程
度上影响刻蚀面的侧壁形貌、反应速率等
Si与GaN刻蚀比较:刻蚀三五族化合物,还要尽量保持被刻蚀界面的化学平衡。
另外,直流偏压的选择,控制反射功率,待刻蚀面积的大小、刻蚀材料的差异等等都会影响到刻蚀面的形貌、刻蚀速率,这些都是要考虑的重要因素。
总而言之,没有万能的程序可以适用所有的要求。
所有的因素都不是单一的,而是相互作用相辅相成的,只有各项条件都相互匹配了才能得到比较理想的不同结果。