自动分拣系统仿真
十大物流仿真软件汇总

1十大物流仿真软件汇总目录( 一) Flexsim2( 二) RaLC(乐龙 )2( 三) Witness(SDX) .2( 四) Automod3( 五) ShowFlow3( 六) SIMAnimation .4( 七) Arena4( 八) Supply chain guru .5( 九) Classwarehouse .5( 十) SimLab52(一) FlexsimFlexsim 是美国的三维物流仿真软件, 能应用于系统建模、仿真以及实现业务流程可视化 .Flexsim中的对象参数可以表示根本上所有的存在的实物对象,如机器装备、操作人员、传送带、叉车、仓库、集装箱等, 同时数据信息可以用Flexsim 丰富的模型库表示出来 .Flexsim具有层次构造,可以使用继承来节省开发时间 . 而且它还是面向对象的开放式软件 . 对象、视窗、图形用户界面、菜单列表、对象参数等都是非常直观的 . 由于 Flexsim 的对象是开放的 , 所以这些对象可以在不同的用户、库和模型之间进展交换 , 再结合对象的高度可自定义性 , 可以大大提高建模的速度 .Flexsim 的用户性和可移植性扩展了对象和模型的生命周期.(二) RaLC(乐龙 )RaLC(乐龙 ) 软件 , 是XX乐龙人工智能软件( 日本人工智能效劳有限公司在华子公司 ) 提供的 . 它是面向对象的 , 物流配送中心所使用的根本搬运器械设备即对象事物, 包括各种传送带、自动立体仓库、平板车等, 以及工作人员的装卸、分拣、叉车搬运等, 全部以按钮的形式摆放在工具栏上, 而且可以对对象物体的配置来进展设计, 用于对各类对象物体的形状和规格建模也十分直观 .RaLC 乐龙系列软件在建模速度、建模操作简便性、模拟和仿真准确度等方面都处于世界领先水平 .(三) Witness(SDX)Witness(SDX) 由英国 Lanner 集团用数十年系统仿真经历开发出的, 它是面3向工业系统 , 商业系统流程的动态系统建模仿真软件平台 , 是离散型的仿真软件 , 流程的仿真动态演示是三维的 , 是世界上该领域的主流仿真软件之一 . 它提供了大量描述工业系统的模型元素 , 如生产线上的加工中心、传送设备、缓冲存储装置等 .(四) AutomodAutomod是由 Autosumulation旗下的Brooks软件部门开发的,它由AutoMod、AutoStat 和 AutoView 三个模块组成 .AutoMod 模块提供给用户一系列的物流系统模块来仿真现实世界中的物流自动化系统. 主要包括输送机模块、自动化存取系统、基于路径的移动设备、起重机模块等 .AutoStat 模块为仿真工程提供增强的统计分析工具 , 由用户定义测量和实验的标准 , 自动在 AutoMod的模型上执行统计分析 .AutoView 可以允许用户通过 AutoMod模型定义场景和摄像机的移动 , 产生高质量的 AVI 格式的动画 . 用户可以缩放或者平移视图 , 或使摄像机跟踪一个物体的移动 .AutoView 可以提供动态的场景描述和灵活的显示方式 , 是目前市面上比拟成熟的三维物流仿真软件 .(五) ShowFlowShowFlow是来自英国的仿真软件, 可为制造业和物流业提供建模、仿真、动画和统计分析工具 , 可以提供生产系统的生产量 , 确定瓶颈位置 , 估测提前期和报告资源利用率 , 还可以被用来支持投资决定 , 校验制造系统设计的合理性 , 通过对不同的制造策略进展仿真实验来找出最优解 . 主要包括系统建模、仿真、统计分析、动画和文档输出等模块.(六) SIMAnimationSIMAnimation 是美国 3i 公司设计开发的集成化物流仿真软件 , 其基于图象的仿真语言 , 用以简化仿真模型的建立 . 不同于其他的仿真系统 , 它可以处理系统物理元素和逻辑元素 .SIMAnimation 具有多方面特点 :①建模能力强 , 具有准确性较高的建模功能;②在仿真软件开发和终端用户实用方面, 具有较高的灵活性 ;③参数化建模是 SIMAnimation 较之其他软件的独特优势 , 它可以通过多元非线性参数设置 , 建立准确度较高的三维实体 ;④SIMAnimation 仿真运行完毕后可根据统计数据生成仿真报告 , 仿真报告以表格、直方图、饼状图等形式表示 , 显示了各个物流设备的利用率、空闲率、阻塞率等数据 . 用户可根据仿真报告提供的数据对物流系统的优缺点进展判断 , 做出科学决策 .(七) ArenaArena 是美国 System Modeling 公司开发的可视化的通用交互集成的仿真软件, 很好地解决了计算机仿真与可视化的有机集成 , 具备高级仿真器的易用性和专用仿真语言的柔性 . 它是一种集成的仿真软件 , 在物流中的主要运用有 :①在生产过程中 , 进展设备布置 , 实现工件加工轨迹的可视化仿真等 ;②在生产管理中 , 进展生产方案、库存管理、生产控制和产品市场的预测和分析等 ;③在生产价值分析方面 , 可进展生产系统经济性、风险性分析, 从而改良生产、降低本钱或辅助企业投资决策;④可实现企业流程再造可视化仿真优化, 实现敏捷供给链管理的可视化仿真决策等 .(八) Supply chain guruSupply chain guru 是来自美国的供给链战略规划仿真软件 , 它允许用户输入或导入供给链网络信息 , 并使用人工智能和嵌入的知识库 , 用以自动建立强大的离散事件仿真和网络优化模型. 用户可以测定改变供给链构造或策略所带来的影响 , 优化模型以选择改良的供给源关联, 仿真多个供给链设计方案以评估效劳和费用之间的折中 , 预测库存投资、运输费用以及生产情况, 为企业提供预算功能.(九) ClasswarehouseClasswarehouse 是来自英国的仓库物流仿真软件, 一种专门用于仓库设计的仿真软件 . 通过在虚拟的计算机环境来进展设计、改良和测试复杂的仓库解决方案 . 它还能帮助公司评估产品的产量、人员的组织以及设备情况, 来量化本钱、效率以及效劳水平 .Classwarehouse 所解决的实际问题X围很广, 从对新建仓库的设计、评估 , 到对已有仓库的某个具体生产工艺的改良, 再到如何在改变供给链和客户需求时保证本钱、效劳和效率三者间的平衡和优化. 除了 Arena 和 Supply chain guru,其他都为三维软件,其中Flexsim和RaLC有很好的面向对象性,Supply chain guru 是专门的供给链仿真软件 ,Classwarehouse 是专门的仓库仿真软件 . 物流系统仿真软件(十) SimLabSimlab是来自于中国XX百蝶公司的教学应用软件,一种专门以教学实验实训为目的物流仿真软件,Simlab 可以让使用者以物流系统中不同的角色进入虚拟的场景中进展任务实训,分单人任务和多人协同完成任务两种,让学生以游戏对抗的方式来到达实训的目的,是一种比拟新颖的教学手段,Simlab 的主要6功能有:① 真实再现物流企业运作环境;② 逼真的物流相关设备操作体验;③ 交互功能:人机互动与人人互动;④ 极其准确朴实的数据仿真,信息系统与虚拟现实系统无缝对接;⑤ 实验过程中灵活可控,教师备课极其方便;⑥ 配有科学的实验评价体系和自动综合评分系统。
基于PLC的物料分拣控制系统设计

基于PLC的物料分拣控制系统设计一、引言随着工业自动化的发展和智能制造的推进,物料分拣是生产线上一个重要的环节。
物料分拣控制系统的设计和实施,将大大提高生产效率和质量。
本文将重点介绍基于PLC(可编程逻辑控制器)的物料分拣控制系统的设计。
二、系统需求分析物料分拣控制系统的设计旨在实现对多种不同物料的准确分拣和定位。
系统需要满足以下功能要求:1.可以识别并准确分辨多种不同物料的属性和特征,如尺寸、形状、颜色等。
2.可以通过PLC控制多个机械手和传送带等设备,实现物料的抓取和移动。
3.可以根据设定的优先级和规则,对物料进行分拣和分类,并且能够处理异常情况。
4.可以与其他系统集成,如上位机、仓储管理系统等,实现数据传输和互通。
三、系统设计方案基于上述需求,我们提出以下物料分拣控制系统的设计方案:1.硬件部分(1)传感器:利用视觉传感器和激光传感器等,获取物料的属性信息。
(2)执行器:采用电磁阀、气缸、伺服机械手等,实现物料的抓取和移动。
(3)PLC:选择合适的PLC进行控制,具备足够的输入输出点数、计算能力和通信功能。
(4)传送带:设置适当的传送带来实现物料的输送和分拣。
2.软件部分(1)PLC程序:通过Ladder Diagram或者Structured Text语言编写PLC程序,根据传感器信号来判断物料的属性,控制执行器对物料进行抓取和移动,实现分拣功能。
(2)图像处理算法:利用计算机视觉技术,对物料的图像进行处理和识别,提取出物料的特征信息。
(3)规则引擎:根据设定的规则和优先级,对物料进行分类和分拣。
(4)数据库:根据需要,设计数据库来存储物料的属性信息、分拣结果和异常情况等数据。
四、系统实施和测试在实施物料分拣控制系统之前,需要进行细致的系统测试和调试。
首先,通过对传感器和执行器的测试,验证其正常工作。
然后,编写PLC程序,并进行模拟仿真,验证分拣功能的正确性。
接下来,与其他系统进行集成测试,确保数据传输和互通的可靠性。
案例二:摘果式自动分拣系统
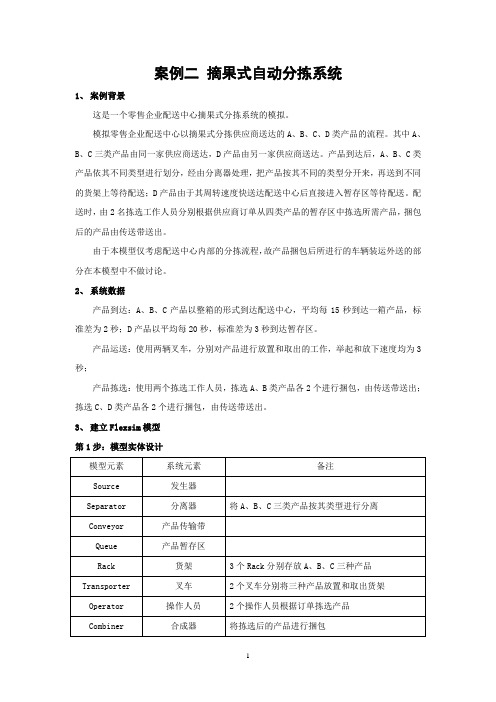
案例二摘果式自动分拣系统1、案例背景这是一个零售企业配送中心摘果式分拣系统的模拟。
模拟零售企业配送中心以摘果式分拣供应商送达的A、B、C、D类产品的流程。
其中A、B、C三类产品由同一家供应商送达,D产品由另一家供应商送达。
产品到达后,A、B、C类产品依其不同类型进行划分,经由分离器处理,把产品按其不同的类型分开来,再送到不同的货架上等待配送;D产品由于其周转速度快送达配送中心后直接进入暂存区等待配送。
配送时,由2名拣选工作人员分别根据供应商订单从四类产品的暂存区中拣选所需产品,捆包后的产品由传送带送出。
由于本模型仅考虑配送中心内部的分拣流程,故产品捆包后所进行的车辆装运外送的部分在本模型中不做讨论。
2、系统数据产品到达:A、B、C产品以整箱的形式到达配送中心,平均每15秒到达一箱产品,标准差为2秒;D产品以平均每20秒,标准差为3秒到达暂存区。
产品运送:使用两辆叉车,分别对产品进行放置和取出的工作,举起和放下速度均为3秒;产品拣选:使用两个拣选工作人员,拣选A、B类产品各2个进行捆包,由传送带送出;拣选C、D类产品各2个进行捆包,由传送带送出。
3、建立Flexsim模型第1步:模型实体设计第2步:实体布局及其参数设置产品送达部分从左边的实体库中将source、combiner、conveyor和Queue拖到模型视图中,并布局连接,如图1所示。
图1 产品送达部分的模型视图(1)Source的参数设置双击发生器,在source下的Inter-Arrivaltime的下拉选项中选择Statistical Distribution来寻找分布函数,如图2所示:图2 Source属性页的Inter-Arrivaltime设置点击Inter-Arrivaltime下拉菜单后的参数编辑按钮进行编辑,选择normal的正态分布,如图3所示。
图3 分布函数的选择视图单击后,编辑为Statistical Distribution: normal(15,2,1)。
基于PLC控制的柔性生产线中自动分拣系统的研究

基于PLC控制的柔性生产线中自动分拣系统的研究一、内容综述随着科技的不断发展,自动化技术在各个领域得到了广泛的应用。
在制造业中,柔性生产线作为一种新型的生产模式,以其高效、灵活的特性逐渐成为企业提高生产效率和降低成本的关键手段。
而自动分拣系统作为柔性生产线中的重要环节,其性能直接影响到整个生产线的运行效率和产品质量。
因此研究基于PLC控制的柔性生产线中自动分拣系统具有重要的理论和实际意义。
本文首先对国内外自动分拣系统的发展趋势进行了梳理,分析了各种自动分拣技术的特点和优缺点,为后续的研究提供了理论依据。
接着本文详细介绍了PLC控制的基本原理、结构特点以及在自动分拣系统中的应用,通过对PLC控制在自动分拣系统中的实际应用案例进行分析,揭示了PLC控制在提高自动分拣系统性能方面的作用机制。
在此基础上,本文提出了一种基于PLC控制的柔性生产线中自动分拣系统的设计方案,该方案充分考虑了柔性生产线的特点,采用了模块化设计思想,使得系统具有良好的可扩展性和可维护性。
同时本文还针对该方案进行了详细的仿真分析,验证了其可行性和有效性。
本文对基于PLC控制的柔性生产线中自动分拣系统的发展前景进行了展望,指出了当前研究中存在的问题和挑战,并提出了未来研究的方向和建议。
1. 柔性生产线的概念和特点柔性生产线是一种高度自动化的生产方式,它通过将各种生产设备、工具和控制系统连接在一起,实现对整个生产过程的实时监控和管理。
柔性生产线的主要特点包括高度灵活性、快速换线能力、高效率和低成本。
高度灵活性:柔性生产线可以根据生产需求快速调整生产线的布局和配置,以适应不同产品的生产。
这使得企业能够迅速应对市场变化,提高生产效率和降低库存成本。
快速换线能力:柔性生产线具有很强的换线能力,可以在短时间内完成产品结构的转换,从而实现多品种、小批量的生产。
这有助于企业在激烈的市场竞争中保持竞争力。
高效率:柔性生产线采用先进的自动化设备和技术,实现了生产过程的高度自动化和智能化。
基于PLC的物料分拣传送控制系统的设计与实现

基于PLC的物料分拣传送控制系统的设计与实现1. 引言1.1 背景介绍物料分拣传送系统是现代生产线中必不可少的一部分,它可以有效地提高物料分拣的效率和准确性,降低人工成本和错误率。
传统的物料分拣传送系统多采用人工操作或简单的机械传送装置,存在着工作效率低、错误率高、适应性差等问题。
随着科技的不断发展和进步,基于PLC的物料分拣传送控制系统应运而生,它利用先进的电气控制技术和自动化技术,实现了传统系统无法实现的功能和优势。
基于PLC的物料分拣传送控制系统具有高性能、可靠性强、灵活性好等特点,可以根据不同的需求和物料特性进行个性化定制,能够满足现代生产线对物料分拣传送的高效、精准要求。
在自动化生产中,PLC已经成为控制系统的核心部件,广泛应用于各种领域,包括工业自动化、交通运输、能源设备等。
因此,研究基于PLC的物料分拣传送控制系统的设计与实现具有重要的意义和价值。
通过此研究,可以提高生产线的自动化水平,提升生产效率,降低成本,实现智能化生产,促进工业的发展和进步。
1.2 研究意义基于PLC的物料分拣传送控制系统能够实现对物料的高效分拣和传送,提高了生产效率和质量,降低了人力成本,使生产过程更加智能化。
这对于促进制造业转型升级,提高企业竞争力具有重要意义。
基于PLC的物料分拣传送控制系统能够实现物料的实时监测和数据采集,为生产过程提供了重要的数据支撑。
通过数据分析和处理,可以实现生产过程的优化和智能化管理,提高生产效率和质量。
基于PLC的物料分拣传送控制系统具有灵活性强、可靠性高、成本低等诸多优点,适用于各种规模和类型的制造企业。
研究基于PLC 的物料分拣传送控制系统的设计与实现,对于推动工业自动化发展,提高制造业水平,具有重要的理论和实践价值。
1.3 研究目的本文旨在设计和实现一种基于PLC的物料分拣传送控制系统,旨在解决传统物料分拣传送系统中存在的一些不足之处,提高物料分拣传送效率和准确性。
具体目的包括:1. 研究分析传统物料分拣传送系统的设计原理和工作流程,总结其优缺点;2. 提出基于PLC的物料分拣传送系统设计方案,探讨其适用性和优势;3. 进行PLC编程与控制逻辑设计,确保系统能够稳定运行并实现准确的物料分拣传送;4. 设计物料传送控制系统的硬件,选择合适的传感器、执行器等设备,保证系统可靠性和稳定性;5. 进行系统实验并对实验结果进行分析,评估系统的性能和可靠性;6. 评估设计与实现的效果,找出存在的问题并提出改进方向;7. 展望未来,探讨如何进一步完善基于PLC的物料分拣传送控制系统,提高其智能化和自动化水平。
基于Factory IO的视觉分拣系统仿真
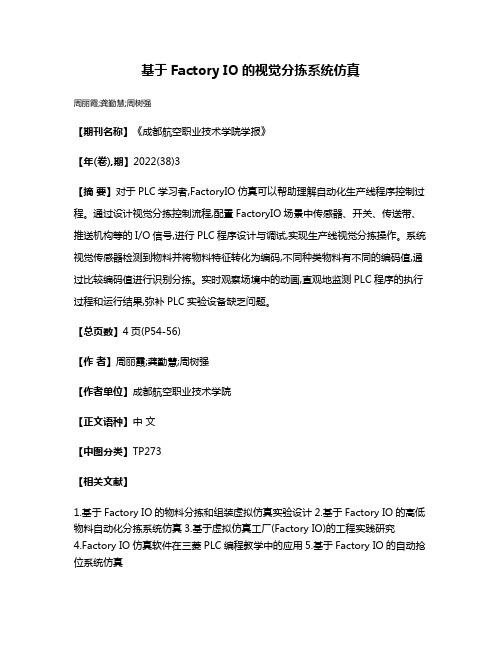
基于Factory IO的视觉分拣系统仿真
周丽霞;龚勤慧;周树强
【期刊名称】《成都航空职业技术学院学报》
【年(卷),期】2022(38)3
【摘要】对于PLC学习者,FactoryIO仿真可以帮助理解自动化生产线程序控制过程。
通过设计视觉分拣控制流程,配置FactoryIO场景中传感器、开关、传送带、推送机构等的I/O信号,进行PLC程序设计与调试,实现生产线视觉分拣操作。
系统视觉传感器检测到物料并将物料特征转化为编码,不同种类物料有不同的编码值,通过比较编码值进行识别分拣。
实时观察场境中的动画,直观地监测PLC程序的执行过程和运行结果,弥补PLC实验设备缺乏问题。
【总页数】4页(P54-56)
【作者】周丽霞;龚勤慧;周树强
【作者单位】成都航空职业技术学院
【正文语种】中文
【中图分类】TP273
【相关文献】
1.基于Factory IO的物料分拣和组装虚拟仿真实验设计
2.基于Factory IO的高低物料自动化分拣系统仿真
3.基于虚拟仿真工厂(Factory IO)的工程实践研究
4.Factory IO仿真软件在三菱PLC编程教学中的应用
5.基于Factory IO的自动抢位系统仿真
因版权原因,仅展示原文概要,查看原文内容请购买。
基于AutoMod的自动分拣系统建模与仿真

G ij I u k n, — i HA GZ e gmig AOL-i , UY — u 。 Yu x Z N h n— n  ̄ eL HU n (.c olf uo t nB in nvri P s &T l o 1Sho A tmao , e ig iesy f ot ee mmu i tn, ej g10 7 o i j U to s c nc i sB in 8 6 ao i 0
[ 要】 摘 首先分 析了 自动分拣 系统 的控制信息流 、 真需求 以及仿 真建模功能要求 , 仿 然后 结合 A t o u M d三维仿 真软件 , 出 o 提 了 自动分拣 系统 的三维建模思路 和方法 ,并结 合基于 A t o 仿真软件建立 的交叉带式 和翻盘式 自动分拣 系统 的仿真模型 , u Md o 说 明 了具体的实现方法 , 提高 了物流 自动分拣 系统 三维建模的效率 。 [ 关键  ̄] t d 自动分拣系统 ; Auo ; Mo 仿真建模 ; 精确度 [ 中图分类-12 39  ̄ F 7 . - 【 文献标识码】 A 【 文章编号】0 5 1 2 2 1 )8 0 3 — 3 10 — 5X( 0 0 0 — 13 0
不 同功 能模 块的建模方法 。结 合 A tM d仿 真软件分别建立 uo o
了交叉 带式 翻盘式 自 动分拣 系统的仿真模 型 , 明 了具体_ 说 的
实现方法 。
2 I 自动分拣 系统仿真建模分析
21 自动分 拣 系统 的控 制信 息流 分析 .
常 见 的 物 流 自动 分 拣 系 统 主 要 有 交 叉 带 式 分 拣 系 统 、 滑
3-PPRR并联分拣机器人机构的运动学建模与仿真

J n 2 1 u. 01
3P R - P R并联分拣 机器人机构的运动学建模 与仿真
王锦 煜 , 马 雪梅 , 陈安 军
( 南大 学 机 械工 程 学院 , 江 江苏 无锡 24 2 ) 1 12 摘 要: 对具 有 空间三 平移 自由度 的 3P R .P R并联 分拣机 器人 进行 运 动 学分析 。 于机 构 的运 动约 基
ma i u a o , t e n e s d s l c me t o u i n a d h f r r d s l c me t o u i n o h n p l t r h i v r e ip a e n s l to s n t e o wa d ip a e n s l t s f t e o p r le o o e e p e e t d T e mo e s o e o i n c e e a i n r l t n h p e we n t r e a a l lr b tw r r s n e . h d l fv l c t a d a c l r t e a i s i s b t e h e y o o
一
0— 之 间的旋转 变换 矩 阵为 Y
sn i 0
动 副 ( ) 转动 副 ( )和转 动 副 ( 。 支链 中 , P 、 R R) 各 2个 移 动副 垂直 放 置 , 中 A 为驱 动副 。 其 移动 副 B 、 动 转 副 c及 转动 副 D 为 中 间关 节 , 同处 CD 平 面 内且
广泛关注 _ J 分拣作业 是大多数流水 生产线上的 l。
一
张 勇等 首先 提 出了 3P R -P R并联 机构 , 对其 进行 了 刚 度 分 析 和 尺 寸 设 计 。 串联 机 构 相 比 , 与 3P R -P R并联 机 构 将 驱 动装 置 安 装 在 机 架 上 , 在很 大程度 上 降低 了机 构 的质 量 , 动平 台能 够 获 得很 使 高的速 度 和加速 度 。 因此 3P RR并联 机 器 人在 轻 -P 工 业领 域 中的高 速分 拣 、 放 等 操作 方 面 具 有 明显 抓
- 1、下载文档前请自行甄别文档内容的完整性,平台不提供额外的编辑、内容补充、找答案等附加服务。
- 2、"仅部分预览"的文档,不可在线预览部分如存在完整性等问题,可反馈申请退款(可完整预览的文档不适用该条件!)。
- 3、如文档侵犯您的权益,请联系客服反馈,我们会尽快为您处理(人工客服工作时间:9:00-18:30)。
实验2 自动分拣系统仿真
1.实验目的
通过建立一个传送带系统,学习Flexsim提供的运动系统的定义;学习Flexism提供的conveyor 系统的建模,进一步学习模型调整与系统优化。
2.实验内容
(1)系统描述与系统参数
分拣系统的流程描述和系统参数如下。
①四种货物A,B,C,D各自独立到达高层的传送带入口端:
A的到达频率服从正太分布函数normal(400,50)s。
B的到达频率服从正态分布函数normal(200,40)s。
C的到达频率服从正态分布函数normal(500,100)s。
D的到达频率服从正太分布函数normal(500,100)s。
D的到达频率服从均匀分布函数uniform(150,30)s。
②四种不同的货物烟一条传送带,根据品种的不同由分拣装置将其推入到四个不同的分拣道口,经各自的分拣道到达操作台。
③每个检验包装操作台需操作工一名,货物经检验合格后打包,被取走。
④没检验一件货物占用时间为uniform(60,20)s。
⑤每种货物都可能有不合格产品。
检验合格的产品放入箱笼;不合格的通过地面传送带送往检修处修复;A的合格率为95%,B为96%,C的合格率为97%,D的合格率为98%。
传送带的传送速度采用默认速度。
(2)实验要求
对上述传送分拣系统进行建模,仿真系统一天8h的运行状况,并完成思考。
3.实验步骤
(1)构建模型布局。
打开Flexism3.0,新建一个模型。
从对象库中拖放所需的对象到建模视图中并根据实验内容的描述修改各实体的名字,如图1。
1
图
(2)定义工件流程。
按住A键,同时用鼠标左键点击SourceA对象并且按住鼠标左键不放,然后拖动鼠标至Queue1对象。
此时会出现一条黄线连接SourceA 和Queue1对象。
然后松开鼠标左键,黄线将变成一条黑线,表示SourceA对象和Queue1对象的端口已经连接上。
如上所述将SourceB,SourceC,SourceD与Queue1相连接;Queue1与Conveyor1相连;Conveyor1与ConveyorA相连;Conveyor1与ConveyorB相连;Conveyor1与ConveyorC相连;Conveyor1与
ConveyorD相连;ConveyorA与ProcessorA相连;ConveyorB与ProcessorB相连;ConveyorC 与ProcessorC相连;ConveyorD与ProcessorD相连;ProcessorA与Conveyor2、QueueA相连;ProcessorB与Conveyor2、QueueB相连;ProcessorC与Conveyor2、QueueC相连,ProcessorD与Conveyor2、QueueD相连;Conveyor2与Sink相连。
按住S键将ProcessorA与OperatorA相连;同理将ProcessorB与OperatorB相连;ProcessorC与OperatorC相连;ProcessorD与OperatorD相连。
连接后的模型如图2所示。
图2
(3)定义对象参数
双击SourceA对象,打开其参数对话框,在“发生器的界面”将物品类型选取默认设置“1”;修改产品流出间隔时间,从“到达时间间隔”下拉框中选择使用正态分布,如图3;并修改选项的默认参数点击Template按钮修改其中的棕褐色的参数值:将“10”改为“400”,“2”改为“50”如图示4。
点击“发生触发器”,在“离开触发”下拉菜单中选择颜色设置。
“确定”,参数框中的“应用”Source;点击5使用默认设置将物品设置为红色,如图
图3
图4
5
图
同理,将SourceB的“物品类型”设置为2,到达频率服从正太分布normal(400,50s)颜色设置为绿色;SourceC的“物品类型”设置为3,到达频率服从正太分布normal(200,40s)颜色设置为蓝色;SourceD的“物品类型”设置为4,到达频率服从uniform(500,100)s颜色设置为白色。
Queue1使用默认设置。
Conveyor1的“布局”菜单中将分段数设置为“4”,点击“应用”,每段的“length”改为“5”,“section1”的“rise”设置为“3”如图6,点击“应用”;点击“临时实体流”界面中“连续判断送往端口”前面的方框,在“送往端口”下拉菜单中选择“将临时实体发送到与实体类型号相同的端口”,如图7;点击“应用”,“确定”。
图6
7
图
ConveyorA的“布局”界面中将“length”设置为8.4,“rise”设置为“-3”,点击“应用”,如图8;在“临时实体流”界面中点击“拉动”前面的方框,在拉动条件中选择“只拉入类型为1的临时实体”,如图9;点击“应用”,“确定”。
图8
图9
同理设置ConveyorB、ConveyorC、ConveyorD,相应的将“拉动条件”中的拉动类型分。
”3“类型,”2“类型,”1别改为“类型
ProcessorA“处理时间”界面的“处理时间”下拉菜单中选择“使用均匀分布”,如图10,修改选项的默认参数:点击Template按钮修改其中的棕褐色的参数值将最小值设置为20,最大值设置为60,点击“确定”,如图11,点击“应用”;“临时实体流”的“送往端口”下拉菜单中选择“按照百分比将实体发送到输出端口”,如图12,修改选项的默认参数:点击Template按钮修改其中的棕褐色的参数值端口1设置为95%,端口2设置为“5%”,点击“确定”如图13,点击“应用”;在“操作员”界面中点击“处理时使用操作员”前面的方框,如图14;点击“应用”,“确定”。
图10
11 图
图12
13
图
图14
同理设置ProcessorB、ProcessorC、ProcessorD,相应的将输出百分比设置为:端口1:96%,端口2:4%;端口1:97%,端口2:3%;端口1:98%,端口2:2%。
将Conveyor2的“length”设置为20,“nroflegs”设置为0,点击“应用”,“确定”,如图15。
15
图
为了满足实验要求将暂存区QueueA、QueueB、QueueC、QueueD的最大容量设置为10000,以QueueA为例,将在“暂存区”界面中“最大容量”设置为10000,如图16所示。
图16
(4)编译运行仿真
先点击编译按钮,在点击运行按钮如图16.
图16
(5)分析
根据实验给出的数据首先将一天定义为8h进行仿真:
Source A、Source B、Source C、Source D发送该分拣系统一天的总货物流量为1.货物的总量为629。
.
2.通过分析不能发现系统能够承受的最大日流量等于A、B、C、D处理器日最大处理能力之和。
查看统计报告(附录1)ProcessorA:空闲:90.3%,加工处理:9.7%,日最大加工量:748;ProcessorB:空闲:80.6%,加工处理:19.4%,日最大加工量:731;ProcessorC:空闲:86.7%,加工处理:1
3.3%,日最大加工量:725;ProcessorD:空闲:56.4%,加工处理:43.6%,日最大加工量:729。
系统日最大处理量为:2933。
3.作为该系统的物流主管可以从两个方面对系统进行调整:①处理器A、B、C的使用率偏低可增加货物A、B、C的进入量;②处理器D相比A、B、C繁忙得多,货物处理量是A的4倍多,是B的2倍多,是C的3倍多,可以适时的从A,B,C抽调人员到D处理器。
4.同过查看系统运行24h的标准报告(附件2),各处理器加工处理的工件数量与计算仿真8h每个处理器多余的倍数也有差异。
按一天倍,3的系统相比都多余8h运行
一个月与运行8h的系统相比每个处理器处理的物品数大约是30倍。
通过分析发现仿真时间越长数据波动性越小。
5.将合格的产品放在箱笼中,没累计20哥打包送走:
在QueueA的属性栏中有一项“成批”,在“成批操作”前面的方框里打钩,将“批量规格”设置为20,点击“应用”,如图17所示;在“临时实体流”属性栏中“使用运输工具”前的方框中打钩,如图18;点击“应用”,“确定”。
图17
18
图
按住S键将运输机与暂存区连接,按住A键将暂存区与吸收器SinkA QueueAQueueA连接。
同理设置QueueB,QueueC,QueueD,如图19。
19图。