橡胶疲劳的一些问题
橡胶耐疲劳性能影响因素

橡胶耐疲劳性能影响因素就橡胶材料而言,疲劳寿命是指橡胶材料在重复变形的过程中,当其承受的局部变形应力超过橡胶的延伸率或应力极限时,疲劳过程开始,以至于最后达到破坏。
这种疲劳破坏的开始点是由于橡胶表面或内部的不均匀性所造成的。
橡胶材料的破坏主要是由于其内部的缺陷或微裂纹引发的裂纹不断传播和扩展而导致的。
按照分子运动论的观点,橡胶材料的动态疲劳破坏归因于材料本身分子链上化学键的断裂,即试样在受到周期应力一应变作用过程中,应力不断地集中于化学键能比较弱的部位而产生微裂纹,继而发展成为裂纹并随着时间的推移而逐步扩展开来。
裂纹发展是一个随着时间而发展,涉及到橡胶材料的分子链连续断裂的粘弹性非平衡动态变化过程。
这一微观发展过程在宏观上的表现是,橡胶材料在动态应力一应变的疲劳过程中,裂纹穿过试样不断扩展,直到断裂以及产生与之所伴随的热效应。
橡胶材料的动态疲劳过程一般可以分为三个阶段:第一阶段是应力剧烈变化,出现橡胶材料在应力作用下变软的现象;第二阶段是应力缓慢变化,橡胶材料表面或内部产生微裂纹,经常称之为破坏核;第三阶段是微裂纹发展成为裂纹并连续不断地扩展开,直到橡胶材料完全出现断裂破坏现象,最后这一阶段是橡胶材料疲劳破坏的最重要的阶段。
使用炭黑填充的天然橡胶硫化胶在一定负荷下多次拉伸变形时,橡胶的物理机械性能在疲劳过程中,拉伸强度先是逐步上升的,经过一个极大值后再开始下降,而撕裂强度、动态弹性模量和力学损耗因子的变化则相反。
在疲劳过程中,胶料的拉伸强度几乎保持不变。
300%定伸应力的疲劳开始阶段明显增大,然后增大趋于缓慢;扯断伸长率则随疲劳周期的变化而下降,在高应变疲劳条件下,具有拉伸结晶性的橡胶抗疲劳破坏性能较好。
未使用补强剂补强的橡胶材料,其破坏形态一般表现为塑性破坏,而使用炭黑或其它活性填料作补强剂的橡胶材料则表现为脆性破坏,且随着各种防老剂的加入,其破坏形态由脆性破坏逐步向准塑性破坏形态转变。
天然橡胶在受到一定频率的应力作用的条件下,由于分子链的内摩擦而生热是其动态疲劳破坏的另外一种因素。
fesafe橡胶疲劳案例
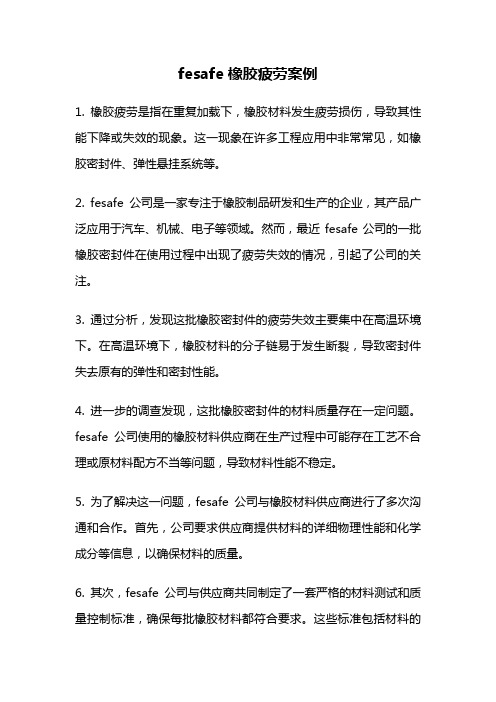
fesafe橡胶疲劳案例1. 橡胶疲劳是指在重复加载下,橡胶材料发生疲劳损伤,导致其性能下降或失效的现象。
这一现象在许多工程应用中非常常见,如橡胶密封件、弹性悬挂系统等。
2. fesafe公司是一家专注于橡胶制品研发和生产的企业,其产品广泛应用于汽车、机械、电子等领域。
然而,最近fesafe公司的一批橡胶密封件在使用过程中出现了疲劳失效的情况,引起了公司的关注。
3. 通过分析,发现这批橡胶密封件的疲劳失效主要集中在高温环境下。
在高温环境下,橡胶材料的分子链易于发生断裂,导致密封件失去原有的弹性和密封性能。
4. 进一步的调查发现,这批橡胶密封件的材料质量存在一定问题。
fesafe公司使用的橡胶材料供应商在生产过程中可能存在工艺不合理或原材料配方不当等问题,导致材料性能不稳定。
5. 为了解决这一问题,fesafe公司与橡胶材料供应商进行了多次沟通和合作。
首先,公司要求供应商提供材料的详细物理性能和化学成分等信息,以确保材料的质量。
6. 其次,fesafe公司与供应商共同制定了一套严格的材料测试和质量控制标准,确保每批橡胶材料都符合要求。
这些标准包括材料的硬度、拉伸强度、断裂伸长率等性能指标。
7. 此外,为了减少橡胶密封件在高温环境下的疲劳失效,fesafe公司开始研发新的材料配方。
通过添加抗氧化剂和增塑剂等添加剂,提高橡胶材料的耐热性和耐老化性能,从而延长橡胶密封件的使用寿命。
8. 在新材料配方的基础上,fesafe公司还优化了橡胶密封件的结构设计。
通过改变密封件的几何形状和尺寸,减少材料的应力集中,降低疲劳损伤的发生概率。
9. 此外,fesafe公司还引入了先进的生产设备和工艺,提高橡胶密封件的加工精度和一致性。
通过精确控制材料的硬度和尺寸等参数,减少橡胶材料的内部缺陷,提高密封件的整体性能。
10. 经过一系列的改进和优化,fesafe公司的橡胶密封件的疲劳失效问题得到了有效的解决。
新的材料配方和结构设计使得橡胶密封件在高温环境下具有更好的耐久性和密封性能,满足了客户的需求。
橡胶曲挠疲劳改善方法
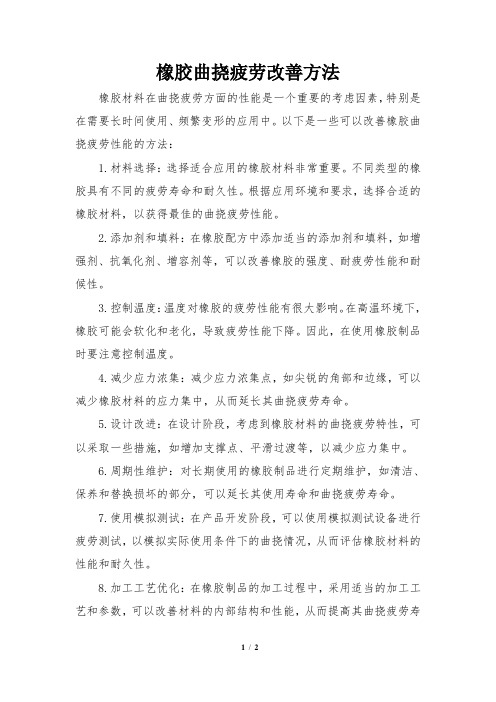
橡胶曲挠疲劳改善方法
橡胶材料在曲挠疲劳方面的性能是一个重要的考虑因素,特别是在需要长时间使用、频繁变形的应用中。
以下是一些可以改善橡胶曲挠疲劳性能的方法:
1.材料选择:选择适合应用的橡胶材料非常重要。
不同类型的橡胶具有不同的疲劳寿命和耐久性。
根据应用环境和要求,选择合适的橡胶材料,以获得最佳的曲挠疲劳性能。
2.添加剂和填料:在橡胶配方中添加适当的添加剂和填料,如增强剂、抗氧化剂、增容剂等,可以改善橡胶的强度、耐疲劳性能和耐候性。
3.控制温度:温度对橡胶的疲劳性能有很大影响。
在高温环境下,橡胶可能会软化和老化,导致疲劳性能下降。
因此,在使用橡胶制品时要注意控制温度。
4.减少应力浓集:减少应力浓集点,如尖锐的角部和边缘,可以减少橡胶材料的应力集中,从而延长其曲挠疲劳寿命。
5.设计改进:在设计阶段,考虑到橡胶材料的曲挠疲劳特性,可以采取一些措施,如增加支撑点、平滑过渡等,以减少应力集中。
6.周期性维护:对长期使用的橡胶制品进行定期维护,如清洁、保养和替换损坏的部分,可以延长其使用寿命和曲挠疲劳寿命。
7.使用模拟测试:在产品开发阶段,可以使用模拟测试设备进行疲劳测试,以模拟实际使用条件下的曲挠情况,从而评估橡胶材料的性能和耐久性。
8.加工工艺优化:在橡胶制品的加工过程中,采用适当的加工工艺和参数,可以改善材料的内部结构和性能,从而提高其曲挠疲劳寿
命。
改善橡胶材料的曲挠疲劳性能需要综合考虑材料的特性、使用环境和设计等因素。
根据实际情况,可以采取多种方法来优化橡胶制品的疲劳性能,以确保其长时间稳定的使用。
影响橡胶制品疲劳(屈扰、动态变形)的因素
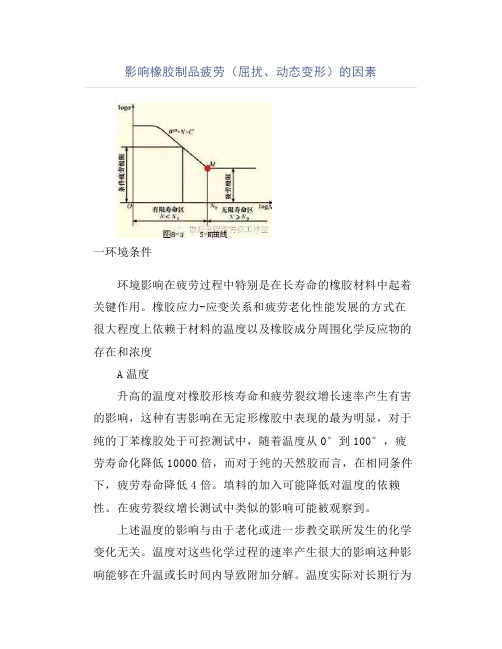
影响橡胶制品疲劳(屈扰、动态变形)的因素一环境条件环境影响在疲劳过程中特别是在长寿命的橡胶材料中起着关键作用。
橡胶应力-应变关系和疲劳老化性能发展的方式在很大程度上依赖于材料的温度以及橡胶成分周围化学反应物的存在和浓度A温度升高的温度对橡胶形核寿命和疲劳裂纹增长速率产生有害的影响,这种有害影响在无定形橡胶中表现的最为明显,对于纯的丁苯橡胶处于可控测试中,随着温度从0°到100°,疲劳寿命化降低10000倍,而对于纯的天然胶而言,在相同条件下,疲劳寿命降低4倍。
填料的加入可能降低对温度的依赖性。
在疲劳裂纹增长测试中类似的影响可能被观察到。
上述温度的影响与由于老化或进一步教交联所发生的化学变化无关。
温度对这些化学过程的速率产生很大的影响这种影响能够在升温或长时间内导致附加分解。
温度实际对长期行为地影响程度取决于配方设计;固化剂,抗氧化剂等这些因素以后讨论。
B臭氧在一个长期的疲劳测试中,有臭氧存在很大程度上会增大裂纹的增长速率和缩短寿命。
由于应力集中,弹性体网链在裂纹尖端很容易与臭氧反应,臭氧与主要聚合物分子链的碳-碳双键发生反应引起断链。
当瞬间的能量释放速率超过一个小的起点,就会发生由于臭氧袭击而引起的裂纹增长,这个起点由Gz表示,Gz通常比机械疲劳起点T更小,Gz的值恨得程度上取决于配方设计,特别是抗氧化剂和抗臭氧剂存在。
对于没有加入任何这些物质的橡胶来说,Gz=0.1J/m2,当有抗臭氧剂存在时,Gz会增大10倍或更多,相比较而言,机械疲劳起点大约为T=50J/m2,臭氧看起来不影响机械疲劳起点的值,其他化学物质能够以一种类似臭氧的方式侵袭橡胶。
Gent和Mrath研究了在一个很大的范围内温度对臭氧增长速的影响。
两个物理量被发现可以控制列为裂纹增长率da/dt,在玻璃化转变温度附近裂纹增长速率是与v温度成比例的,而与臭氧无关。
在足够高的温度下(Q-Tg>100°),裂纹增长速率完全依赖于臭氧浓度而与温度无关。
橡胶疲劳断裂形态

橡胶疲劳断裂形态橡胶是一种具有优异机械性能和耐磨耐腐蚀特性的弹性材料,广泛应用于各个领域。
然而,在长期使用过程中,橡胶材料可能会出现疲劳断裂现象。
疲劳断裂是指材料在受到重复加载作用下,由于应力集中和损伤累积,最终导致断裂失效。
橡胶疲劳断裂形态多种多样,常见的有裂纹扩展型、剪切型和磨损型。
下面将详细介绍这些形态。
裂纹扩展型是指在橡胶材料中出现裂纹,并随着加载次数的增加逐渐扩展。
这种疲劳断裂形态常见于高应力和高应变下的橡胶材料,如橡胶密封件和橡胶弹簧等。
裂纹扩展型的疲劳断裂通常呈现出断裂口较为平整和光滑的特点,裂纹呈尖锐形状,断裂面较为干净。
裂纹扩展型的疲劳断裂是由于材料内部的微观缺陷和损伤导致的,随着裂纹的扩展,材料的强度逐渐降低,最终导致断裂失效。
剪切型是指在橡胶材料中出现剪切变形,并伴随着裂纹的形成和扩展。
剪切型的疲劳断裂常见于橡胶材料在剪切应力作用下的情况,如橡胶管道和橡胶密封圈等。
剪切型疲劳断裂通常表现为断裂面上有明显的剪切纹路,呈现出类似撕裂的特征。
剪切型疲劳断裂的形成是由于橡胶材料在受到剪切应力作用下,发生内部断裂和相对滑移,造成裂纹的形成和扩展。
磨损型是指橡胶材料在长期使用过程中,由于摩擦和磨损作用,最终导致断裂失效。
磨损型的疲劳断裂常见于橡胶轮胎和橡胶密封件等应用场景。
磨损型疲劳断裂通常表现为断裂面上有明显的磨损痕迹和划痕,呈现出类似磨损的特征。
磨损型疲劳断裂的形成是由于橡胶材料在受到摩擦和磨损作用下,表面逐渐磨损,最终导致断裂失效。
总结起来,橡胶疲劳断裂形态包括裂纹扩展型、剪切型和磨损型。
裂纹扩展型的疲劳断裂主要是由于材料内部的微观缺陷和损伤导致的,呈现出断裂口平整光滑的特点。
剪切型的疲劳断裂主要是由于橡胶材料在受到剪切应力作用下发生内部断裂和相对滑移,呈现出撕裂的特征。
磨损型的疲劳断裂主要是由于橡胶材料在长期使用过程中受到摩擦和磨损作用,表面逐渐磨损,呈现出磨损的特征。
了解橡胶疲劳断裂形态对于预防和控制疲劳断裂失效具有重要意义。
橡胶的热、氧、光、疲劳老化

橡胶的热、氧、光、疲劳老化橡胶在热氧老化过程中的结构变化有几种?热由“热”引起的老化可谓贯穿于橡胶的整个生命周期,如聚合过程中聚合温度、树脂合成过程中的固化放热、挤出注塑等加工过程中的加工温度、橡胶贮存条件下的环境温度、使用过程中来自于太阳的暴晒或使用环境温度等等。
“热”对橡胶老化的影响主要体现在其分子链的运动方面,温度升高,橡胶分子链运动加剧,当材料受热温度超过其临界温度,分子聚集态结构、结晶度等会发生变化,则会直接影响高分子材料的物理性能,尤其是材料的力学性能,如在极寒环境下,橡胶会变脆,韧性大大下降,极易折断。
当材料受热温度超过化学键的键能时,会引起分子链的断裂,进而发生热降解或交联,从而导致橡胶使用性能的下降,尤其是在有氧气存在的条件下,极易造成热氧老化,加剧高橡胶的降解。
氧“氧”可以说是无处不在,是导致橡胶老化的又一重要因素。
橡胶分子结构中的不饱和双键、羰基、叔碳基等,极易受到氧的攻击,从而形成大分子过氧自由基或过氧化物,然后导致橡胶分子链中弱键部位发生断裂,进而造成橡胶分子量的下降,某些链的断裂和分解会进一步产生自由基,引发大分子链的氧化,从而发生老化。
当有热和光照存在的条件下,橡胶还会发生热氧老化和光氧老化,加剧材料的老化,这种老化基本是不可逆的,会大大缩短材料的使用寿命。
橡胶在热氧老化过程中的结构变化可分为二类:一类是以分子链降解为主的热氧老化反应(裂解化);二类是以分子链之间交联为主的热氧老化(结构化)。
天然橡胶等含有异戊二烯橡胶、丁基橡胶、二元乙丙橡胶、均聚型氯醇橡胶及共聚氯醇橡胶等。
这类橡胶在发生热氧老化后的外观表现为变软、发粘。
顺丁橡胶含有丁二烯的橡胶在热氧老化过程中,发生的主要是交联反应,类似的橡胶品种还有NBR/SBR/CR/ERDM/FPM/CSM等。
这类橡胶在发生热氧老化后的外观表现为变硬、变脆。
有时还有光老化:“太阳光照”除了会造成橡胶的温度升高而发生热老化外,其光线中的紫外线是导致橡胶(特别是户外应用时)老化的主要原因,这主要是因为大多数橡胶材料的化学键键能都在紫外光能量范围内,当橡胶吸收了光能后,会引起化学键的断裂,导致橡胶大分子链的断裂,进而导致光老化,尤其是在有氧存在的条件下,还能够引起橡胶的光氧老化,加剧材料的老化降解。
橡胶疲劳寿命影响因素概述

就橡胶材料而言,它是指橡胶材料在重复变形的过程中,当其承受的局部变形应力超过橡胶的延伸率或应力极限时,疲劳过程开始,以至于最后达到破坏。
这种疲劳破坏的开始点是由于橡胶表面或内部的不均匀性所造成的。
橡胶材料的破坏主要是由于其内部的缺陷或微裂纹引发的裂纹不断传播和扩展而导致的。
按照分子运动论的观点,橡胶材料的动态疲劳破坏归因于材料本身分子链上化学键的断裂,即试样在受到周期应力一应变作用过程中,应力不断地集中于化学键能比较弱的部位而产生微裂纹,继而发展成为裂纹并随着时间的推移而逐步扩展开来。
裂纹发展是一个随着时间而发展,涉及到橡胶材料的分子链连续断裂的粘弹性非平衡动态变化过程。
这一微观发展过程在宏观上的表现是,橡胶材料在动态应力一应变的疲劳过程中,裂纹穿过试样不断扩展,直到断裂以及产生与之所伴随的热效应。
橡胶材料的动态疲劳过程一般可以分为三个阶段:第一阶段是应力剧烈变化,出现橡胶材料在应力作用下变软的现象;第二阶段是应力缓慢变化,橡胶材料表面或内部产生微裂纹,经常称之为破坏核;第三阶段是微裂纹发展成为裂纹并连续不断地扩展开,直到橡胶材料完全出现断裂破坏现象,最后这一阶段是橡胶材料疲劳破坏的最重要的阶段。
使用炭黑填充的天然橡胶硫化胶在一定负荷下多次拉伸变形时,橡胶的物理机械性能在疲劳过程中,拉伸强度先是逐步上升的,经过一个极大值后再开始下降,而撕裂强度、动态弹性模量和力学损耗因子的变化则相反。
在疲劳过程中,胶料的拉伸强度几乎保持不变。
300%定伸应力的疲劳开始阶段明显增大,然后增大趋于缓慢;扯断伸长率则随疲劳周期的变化而下降,在高应变疲劳条件下,具有拉伸结晶性的橡胶抗疲劳破坏性能较好。
未使用补强剂补强的橡胶材料,其破坏形态一般表现为塑性破坏,而使用炭黑或其它活性填料作补强剂的橡胶材料则表现为脆性破坏,且随着各种防老剂的加入,其破坏形态由脆性破坏逐步向准塑性破坏形态转变。
天然橡胶在受到一定频率的应力作用的条件下,由于分子链的内摩擦而生热是其动态疲劳破坏的另外一种因素。
橡胶材料的疲劳性能分析
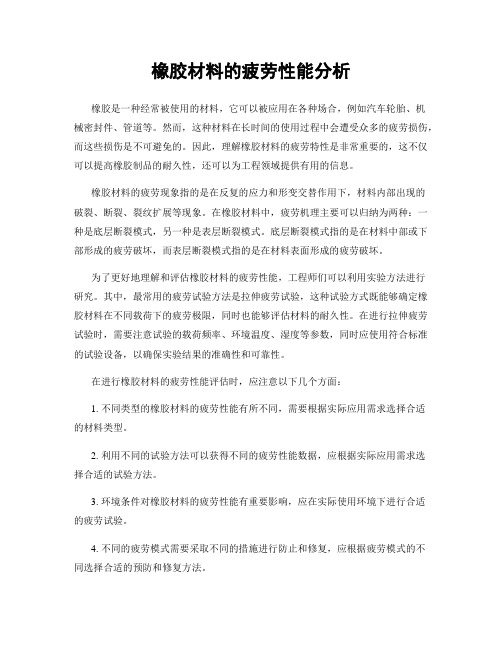
橡胶材料的疲劳性能分析橡胶是一种经常被使用的材料,它可以被应用在各种场合,例如汽车轮胎、机械密封件、管道等。
然而,这种材料在长时间的使用过程中会遭受众多的疲劳损伤,而这些损伤是不可避免的。
因此,理解橡胶材料的疲劳特性是非常重要的,这不仅可以提高橡胶制品的耐久性,还可以为工程领域提供有用的信息。
橡胶材料的疲劳现象指的是在反复的应力和形变交替作用下,材料内部出现的破裂、断裂、裂纹扩展等现象。
在橡胶材料中,疲劳机理主要可以归纳为两种:一种是底层断裂模式,另一种是表层断裂模式。
底层断裂模式指的是在材料中部或下部形成的疲劳破坏,而表层断裂模式指的是在材料表面形成的疲劳破坏。
为了更好地理解和评估橡胶材料的疲劳性能,工程师们可以利用实验方法进行研究。
其中,最常用的疲劳试验方法是拉伸疲劳试验,这种试验方式既能够确定橡胶材料在不同载荷下的疲劳极限,同时也能够评估材料的耐久性。
在进行拉伸疲劳试验时,需要注意试验的载荷频率、环境温度、湿度等参数,同时应使用符合标准的试验设备,以确保实验结果的准确性和可靠性。
在进行橡胶材料的疲劳性能评估时,应注意以下几个方面:1. 不同类型的橡胶材料的疲劳性能有所不同,需要根据实际应用需求选择合适的材料类型。
2. 利用不同的试验方法可以获得不同的疲劳性能数据,应根据实际应用需求选择合适的试验方法。
3. 环境条件对橡胶材料的疲劳性能有重要影响,应在实际使用环境下进行合适的疲劳试验。
4. 不同的疲劳模式需要采取不同的措施进行防止和修复,应根据疲劳模式的不同选择合适的预防和修复方法。
综上所述,橡胶材料的疲劳性能是影响橡胶制品寿命和性能的重要因素,能够对该领域的工程师们提供有益的信息。
因此,对橡胶材料的疲劳性能进行深入研究和评估是非常重要的,可以帮助我们更好地理解材料的性能和特点,从而提高橡胶制品的质量和可靠性。
- 1、下载文档前请自行甄别文档内容的完整性,平台不提供额外的编辑、内容补充、找答案等附加服务。
- 2、"仅部分预览"的文档,不可在线预览部分如存在完整性等问题,可反馈申请退款(可完整预览的文档不适用该条件!)。
- 3、如文档侵犯您的权益,请联系客服反馈,我们会尽快为您处理(人工客服工作时间:9:00-18:30)。
天然橡胶就橡胶材料而言,它是指橡胶材料在重复变形的过程中,当其承受的局部变形应力超过橡胶的延伸率或应力极限时,疲劳过程开始,以至于最后达到破坏。
这种疲劳破坏的开始点是由于橡胶表面或内部的不均匀性所造成的。
橡胶材料的破坏主要是由于其内部的缺陷或微裂纹引发的裂纹不断传播和扩展而导致的。
按照分子运动论的观点,橡胶材料的动态疲劳破坏归因于材料本身分子链上化学键的断裂,即试样在受到周期应力一应变作用过程中,应力不断地集中于化学键能比较弱的部位而产生微裂纹,继而发展成为裂纹并随着时间的推移而逐步扩展开来。
裂纹发展是一个随着时间而发展,涉及到橡胶材料的分子链连续断裂的粘弹性非平衡动态变化过程。
这一微观发展过程在宏观上的表现是,橡胶材料在动态应力一应变的疲劳过程中,裂纹穿过试样不断扩展,直到断裂以及产生与之所伴随的热效应。
橡胶材料的动态疲劳过程一般可以分为三个阶段:第一阶段是应力剧烈变化,出现橡胶材料在应力作用下变软的现象;第二阶段是应力缓慢变化,橡胶材料表面或内部产生微裂纹,经常称之为破坏核;第三阶段是微裂纹发展成为裂纹并连续不断地扩展开,直到橡胶材料完全出现断裂破坏现象,最后这一阶段是橡胶材料疲劳破坏的最重要的阶段。
使用炭黑填充的天然橡胶硫化胶在一定负荷下多次拉伸变形时,橡胶的物理机械性能在疲劳过程中,拉伸强度先是逐步上升的,经过一个极大值后再开始下降,而撕裂强度、动态弹性模量和力学损耗因子的变化则相反。
在疲劳过程中,胶料的拉伸强度几乎保持不变。
300%定伸应力的疲劳开始阶段明显增大,然后增大趋于缓慢;扯断伸长率则随疲劳周期的变化而下降,在高应变疲劳条件下,具有拉伸结晶性的橡胶抗疲劳破坏性能较好。
未使用补强剂补强的橡胶材料,其破坏形态一般表现为塑性破坏,而使用炭黑或其它活性填料作补强剂的橡胶材料则表现为脆性破坏,且随着各种防老剂的加入,其破坏形态由脆性破坏逐步向准塑性破坏形态转变。
天然橡胶在受到一定频率的应力作用的条件下,由于分子链的内摩擦而生热是其动态疲劳破坏的另外一种因素。
当疲劳生热的温度低于120℃时,天然橡胶制品内部将发生化学交联键的结构变化,主要是发生交联键及链段的热裂解反应,首先是多硫交联键减少,而单、双键逐渐增加。
总的表现是交联键的密度在增加,宏观的表现为胶料的硬度和定伸应力增加。
由于胶料内部发生了以上微观结构的变化,从而进一步造成产品内部的生热继续,当生热温度超过120℃(如到达130℃、140℃、150℃)时,橡胶材料总的交联密度逐步下降。
疲劳破坏的最后阶段,橡胶材料的外观表现将接近混炼胶状态。
此时的橡胶已经完全丧失弹性.产品也将失去了实际使用价值。
影响疲劳寿命的因素弹性体的性质研究表明,在低应变疲劳条件下,橡胶的玻璃化转变温度愈高,耐疲劳破坏性能愈好;在高应变疲劳条件下,具有拉伸结晶性的橡胶耐疲劳破坏性能较好。
疲劳裂纹增长也与弹性体种类有关,NR和BR对应变速率不敏感,而SBR等由于具有较大的粘弹性,对应变速率较为敏感。
(针对这方面的研究和表述最多,但是与本次研究关系不大,因此简要带过)应变周期随频率的增加,橡胶的疲劳破坏加快,但当频率增加到一定程度后继续增加时,其疲劳寿命变化就不再显著。
主要是由于低频条件下,机械疲劳破坏引起的分子链断裂起决定作用;高频条件下,由于产生较大的升热,因此,破坏的主要原因已不是机械疲劳,而是高温引起的热降解,此时化学变化对橡胶的破坏起重要作用。
另外,频率对非结晶橡胶有显著的影响,对结晶橡胶的影响不显著,因为非结晶橡胶存在叠加在动态割口增长上的时间依赖性连续裂纹增长。
裂纹增长中的这种稳定增长部分在频率微0.2Hz以下非常重要,它的引发归根于粘弹性效应。
对NR(天然橡胶)胶料的研究结果表明,最小应变增加时尽管能量输人降低,但样品的疲劳寿命却增加,说明施加于样品的最小应变是影响疲劳寿命的主要因素。
还有许多橡胶制品的例子表明应变周期在很大程度上影响制品的性能。
操作温度操作温度对橡胶耐疲劳破坏性能的影响相当复杂,因为疲劳中同时发生了不可逆的化学变化(如降解)。
另外高温还影响材料的模量和扯断伸长率。
但在大多数试验中,随温度的增加,NR和SBR的疲劳寿命都降低,只是前者不如后者明显。
静态应力橡胶制品在使用时往往要预先加载,产生一定的变形,然后再进行疲劳实验,此预压力导致的应力称为静态应力,引起的变形,称为静态应变。
与金属的疲劳寿命随静态应力的增大而降低不同,橡胶的疲劳寿命随静态应力/应变的增加而增加,直至达到一个最大值,而后逐渐减小,并且应变结晶性橡胶和非应变结晶性橡胶疲劳寿命的增加的原因不同。
前者因为橡胶在裂纹尖端发生了应变结晶,可以阻止裂纹的进一步增长;后者因为往复循环应变能的降低。
空气氛围空气氛围对橡胶疲劳裂纹增长的影响也比较显著。
一般惰性环境(如氮气)使疲劳裂纹增长速率下降,氧和臭氧使疲劳裂纹增长加速。
与氧的影响相比,臭氧裂纹可在更低的应力下发生,0.5×10-6的臭氧可以使疲劳裂纹增长速率增加40%-80%。
此外,填料、硫化系统、硫化状态、抗氧剂对橡胶的疲劳性能均有一定的影响。
橡胶的阻尼热:由于橡胶复合材料的滞后损失大而导热性差,此类材料在承受循环载荷的同时伴随有较高的热生成,使材料表面和内部温度升高,加速了材料的疲劳破坏。
因此,研究此类材料在循环载荷下温度变化的一般规律,是对该类材料进行疲劳强度分析和寿命预报不可缺少的内容。
大部分橡胶疲劳的实验都是将阻尼热考虑进去,甚至直接研究橡胶材料在周期载荷下产热对材料疲劳性能的影响。
橡胶材料疲劳的相关理论研究撕裂能法:撕裂能T的最初数学定义式为:式中U——弹性应变能;A一一断裂表面积(无应变状态)在循环载荷作用下.裂纹增长速率为:式中c——裂纹长度;n——周期数;Tmax——每一周期所达到的最大撕裂能。
裂纹长度从c i增长到c j所需的周期数可以通过对式(2)的积分得到代入T与c的关系式,就可得到疲劳寿命与变形幅值、初始裂纹尺寸、裂纹增长特性之间的定量关系。
承受拉伸循环变形的矩形层合件中心区域的应变能是裂纹增长的主要原因.当层间裂纹扩展δc时,单位长度材料的能量损失δV为:式中Wc——试件中心区域的应变能密度;t——试件厚度。
撕裂能表达式为:1989年,Huang等采用帘线完全被橡胶包覆的复合材料模型,研究r帘线端头裂纹的产生过程。
由于周期性载荷使帘线端头处的橡胶产生高应力集中,该处橡胶便产生铜钱状裂纹。
材料中产生半径为c的铜钱状裂纹所导致的能耗可表示为:W为应变能密度。
铜钱状裂纹扩展时的撕裂能(应变能释放速率)T为:其中.k是与应变状态有关的常数,结合Lake等提出的疲劳裂纹增长四阶段规律,Huang最终得到的材料疲劳寿命方程为:以断裂力学为基础的撕裂能法在橡胶复合材料疲劳损伤研究中已取得了初步进展,但其主要困难在于确定撕裂能、裂纹尺寸、载荷或变形间的关系。
另外,该方法假定材料疲劳破坏的主要原因是橡胶相裂纹的增长,没有考虑帘线中纤维的断裂和橡胶.帘线界面剥离。
因此,撕裂能法基于橡胶相理想裂纹的假设只能适用于特定的材料模型和载荷范围。
疲劳寿命{S——N)曲线法1992年,万志敏等以人造丝增强橡胶复合材料为对象,研究了单向帘线一橡胶复合材料的疲劳寿命,试件应力与应变循环次数(N)的关系曲线如图所示。
研究表明。
单向帘线一橡胶复合材料的疲劳损伤表现为阶段过程,稳态损伤AB段)过程和加速损伤导致的断裂过程(BC段)。
在应变比为0.1、频率为3Hz时的S-N曲线如图2所示。
稳态疲劳寿命(即疲劳寿命)方程为:式中e b ——施加的应变值;Nb ——稳态疲劳寿命。
采用尼龙增强橡胶来模拟航空斜交轮胎的胎体材料,评价了试样的尺寸、加载频率及波形对疲劳寿命的影响。
图3所示为不同长/宽比(L /W)的试件(W 为19.05 mm)在频率分别为l 和10 Hz 时的S —N 曲线。
2n 2lgN= -[lgf()+lg(+-3)+[1gG-lg(-1)-(-1)lgC -lgE]βλλβββλ显然,加载频率使疲劳极限降低,对疲劳寿命影响很大,而试样L/W的影响不大。
载荷序列对损伤累积过程的影响,基于动态蠕变的线性累积损伤模型。
对于两级加载,材料至整体破坏时的累积损伤为:式中D——累积损伤值;△ε1——第一级加载的动态蠕变量;△ε2——第二级加载的动态蠕变量;△εf1——第一级载荷单独作用时材料至整体破坏的动态蠕变量;△εf2——第二级载荷单独作用时材料至整体破坏的动态蠕变量。
S—N曲线对于研究橡胶复合材料的疲劳寿命是非常必要的,它所表现出的特征能使较大范围的应力、应变与疲劳寿命间的关系一目了然.可为材料的优化提供依据。
但是由于疲劳试验数据的分散性、试件加工尺寸的偏差、材料的原始缺陷等原因,只有通过获取大子样空间,运用概率统计的方法来处理,才能得到准确的疲劳特性和可靠寿命。
损伤力学方法根据损伤力学和不可逆热力学,以循环蠕变为损伤变量,建立了单向橡胶复合材料的损伤演化方程:式中M,B一一材料常数;σ*——拉伸应力幅值;σ0——平均应力;E pi——初始循环模量。
这是一非线性损伤累积。
损伤率不仅与应力幅值、平均应力有关,还和当时的损伤值有关。
而频率对损伤率的影响是通过初始循环模量反映的。
对该方程积分可得到疲劳寿命:疲劳寿命与应力幅值和频率的关系如图4所示。
目前,以损伤力学为基础对橡胶复合材料疲劳损伤演化的研究仅限于单层材料,而实际结构中使用的多为层合材料,层合材料的一个潜在问题就是层间开裂。
这类材料的疲劳损伤机理为:在循环载荷作用下,裂纹在层间产生并向内部扩展,最终脱层破坏。
因此,研究层合的橡胶复合材料的疲劳损伤更具实际意义。
有关疲劳实验研究橡胶材料,离不开讨论阻尼所产生的热能,这是因为橡胶材料对温度是十分敏感的,温度变化稍大,橡胶材料性能就会表现出较大的变化。
因此查阅到的大部分实验都是与阻尼热有关的。
试件相关数据:试件经模压成型,为哑铃状,有效工作段尺寸为60 mm×25 mm×2 .7 mm。
所施加的载荷为正弦波形P =P0+P0sin wt ,每个试件首先被准静态拉伸至平均载荷P0,然后施加正弦载荷至所需要的值。
试验频率为f =5Hz ,环境温度为T =24℃。
应力幅值对单位时间内热生成率的影响:随应力幅值的增加,材料在单位时间内热生成率与总滞后损失之比下降。
这种现象是由材料的非线性粘弹性或者材料内部结构变化引起的。