橡胶耐疲劳性
橡胶耐疲劳性能影响因素

橡胶耐疲劳性能影响因素就橡胶材料而言,疲劳寿命是指橡胶材料在重复变形的过程中,当其承受的局部变形应力超过橡胶的延伸率或应力极限时,疲劳过程开始,以至于最后达到破坏。
这种疲劳破坏的开始点是由于橡胶表面或内部的不均匀性所造成的。
橡胶材料的破坏主要是由于其内部的缺陷或微裂纹引发的裂纹不断传播和扩展而导致的。
按照分子运动论的观点,橡胶材料的动态疲劳破坏归因于材料本身分子链上化学键的断裂,即试样在受到周期应力一应变作用过程中,应力不断地集中于化学键能比较弱的部位而产生微裂纹,继而发展成为裂纹并随着时间的推移而逐步扩展开来。
裂纹发展是一个随着时间而发展,涉及到橡胶材料的分子链连续断裂的粘弹性非平衡动态变化过程。
这一微观发展过程在宏观上的表现是,橡胶材料在动态应力一应变的疲劳过程中,裂纹穿过试样不断扩展,直到断裂以及产生与之所伴随的热效应。
橡胶材料的动态疲劳过程一般可以分为三个阶段:第一阶段是应力剧烈变化,出现橡胶材料在应力作用下变软的现象;第二阶段是应力缓慢变化,橡胶材料表面或内部产生微裂纹,经常称之为破坏核;第三阶段是微裂纹发展成为裂纹并连续不断地扩展开,直到橡胶材料完全出现断裂破坏现象,最后这一阶段是橡胶材料疲劳破坏的最重要的阶段。
使用炭黑填充的天然橡胶硫化胶在一定负荷下多次拉伸变形时,橡胶的物理机械性能在疲劳过程中,拉伸强度先是逐步上升的,经过一个极大值后再开始下降,而撕裂强度、动态弹性模量和力学损耗因子的变化则相反。
在疲劳过程中,胶料的拉伸强度几乎保持不变。
300%定伸应力的疲劳开始阶段明显增大,然后增大趋于缓慢;扯断伸长率则随疲劳周期的变化而下降,在高应变疲劳条件下,具有拉伸结晶性的橡胶抗疲劳破坏性能较好。
未使用补强剂补强的橡胶材料,其破坏形态一般表现为塑性破坏,而使用炭黑或其它活性填料作补强剂的橡胶材料则表现为脆性破坏,且随着各种防老剂的加入,其破坏形态由脆性破坏逐步向准塑性破坏形态转变。
天然橡胶在受到一定频率的应力作用的条件下,由于分子链的内摩擦而生热是其动态疲劳破坏的另外一种因素。
橡胶专业知识介绍
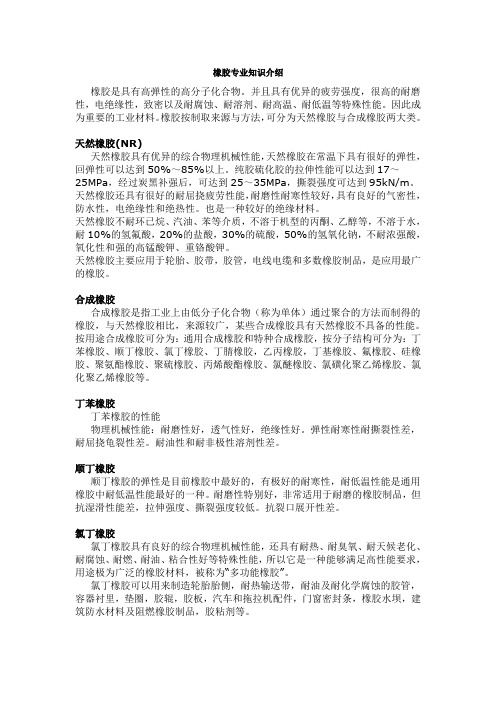
橡胶专业知识介绍橡胶是具有高弹性的高分子化合物。
并且具有优异的疲劳强度,很高的耐磨性,电绝缘性,致密以及耐腐蚀、耐溶剂、耐高温、耐低温等特殊性能。
因此成为重要的工业材料。
橡胶按制取来源与方法,可分为天然橡胶与合成橡胶两大类。
天然橡胶(NR)天然橡胶具有优异的综合物理机械性能,天然橡胶在常温下具有很好的弹性,回弹性可以达到50%~85%以上。
纯胶硫化胶的拉伸性能可以达到17~25MPa,经过炭黑补强后,可达到25~35MPa,撕裂强度可达到95kN/m。
天然橡胶还具有很好的耐屈挠疲劳性能,耐磨性耐寒性较好,具有良好的气密性,防水性,电绝缘性和绝热性。
也是一种较好的绝缘材料。
天然橡胶不耐环已烷、汽油、苯等介质,不溶于机型的丙酮、乙醇等,不溶于水,耐10%的氢氟酸,20%的盐酸,30%的硫酸,50%的氢氧化钠,不耐浓强酸,氧化性和强的高锰酸钾、重铬酸钾。
天然橡胶主要应用于轮胎、胶带,胶管,电线电缆和多数橡胶制品,是应用最广的橡胶。
合成橡胶合成橡胶是指工业上由低分子化合物(称为单体)通过聚合的方法而制得的橡胶,与天然橡胶相比,来源较广,某些合成橡胶具有天然橡胶不具备的性能。
按用途合成橡胶可分为:通用合成橡胶和特种合成橡胶,按分子结构可分为:丁苯橡胶、顺丁橡胶、氯丁橡胶、丁腈橡胶,乙丙橡胶,丁基橡胶、氟橡胶、硅橡胶、聚氨酯橡胶、聚硫橡胶、丙烯酸酯橡胶、氯醚橡胶、氯磺化聚乙烯橡胶、氯化聚乙烯橡胶等。
丁苯橡胶丁苯橡胶的性能物理机械性能:耐磨性好,透气性好,绝缘性好。
弹性耐寒性耐撕裂性差,耐屈挠龟裂性差。
耐油性和耐非极性溶剂性差。
顺丁橡胶顺丁橡胶的弹性是目前橡胶中最好的,有极好的耐寒性,耐低温性能是通用橡胶中耐低温性能最好的一种。
耐磨性特别好,非常适用于耐磨的橡胶制品,但抗湿滑性能差,拉伸强度、撕裂强度较低。
抗裂口展开性差。
氯丁橡胶氯丁橡胶具有良好的综合物理机械性能,还具有耐热、耐臭氧、耐天候老化、耐腐蚀、耐燃、耐油、粘合性好等特殊性能,所以它是一种能够满足高性能要求,用途极为广泛的橡胶材料,被称为“多功能橡胶”。
fesafe橡胶疲劳案例
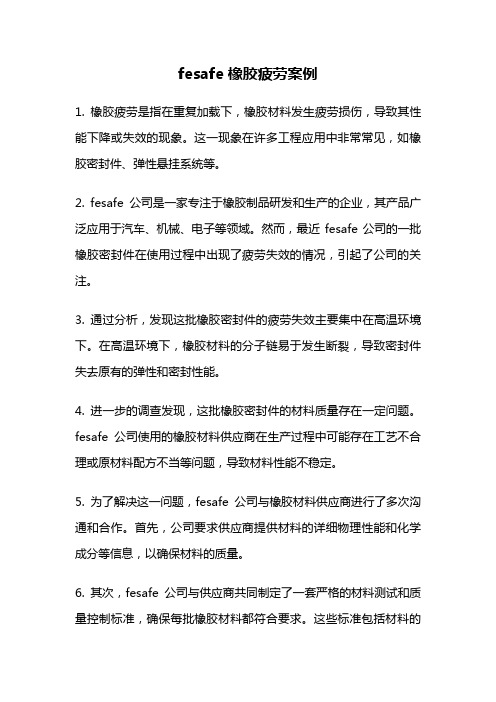
fesafe橡胶疲劳案例1. 橡胶疲劳是指在重复加载下,橡胶材料发生疲劳损伤,导致其性能下降或失效的现象。
这一现象在许多工程应用中非常常见,如橡胶密封件、弹性悬挂系统等。
2. fesafe公司是一家专注于橡胶制品研发和生产的企业,其产品广泛应用于汽车、机械、电子等领域。
然而,最近fesafe公司的一批橡胶密封件在使用过程中出现了疲劳失效的情况,引起了公司的关注。
3. 通过分析,发现这批橡胶密封件的疲劳失效主要集中在高温环境下。
在高温环境下,橡胶材料的分子链易于发生断裂,导致密封件失去原有的弹性和密封性能。
4. 进一步的调查发现,这批橡胶密封件的材料质量存在一定问题。
fesafe公司使用的橡胶材料供应商在生产过程中可能存在工艺不合理或原材料配方不当等问题,导致材料性能不稳定。
5. 为了解决这一问题,fesafe公司与橡胶材料供应商进行了多次沟通和合作。
首先,公司要求供应商提供材料的详细物理性能和化学成分等信息,以确保材料的质量。
6. 其次,fesafe公司与供应商共同制定了一套严格的材料测试和质量控制标准,确保每批橡胶材料都符合要求。
这些标准包括材料的硬度、拉伸强度、断裂伸长率等性能指标。
7. 此外,为了减少橡胶密封件在高温环境下的疲劳失效,fesafe公司开始研发新的材料配方。
通过添加抗氧化剂和增塑剂等添加剂,提高橡胶材料的耐热性和耐老化性能,从而延长橡胶密封件的使用寿命。
8. 在新材料配方的基础上,fesafe公司还优化了橡胶密封件的结构设计。
通过改变密封件的几何形状和尺寸,减少材料的应力集中,降低疲劳损伤的发生概率。
9. 此外,fesafe公司还引入了先进的生产设备和工艺,提高橡胶密封件的加工精度和一致性。
通过精确控制材料的硬度和尺寸等参数,减少橡胶材料的内部缺陷,提高密封件的整体性能。
10. 经过一系列的改进和优化,fesafe公司的橡胶密封件的疲劳失效问题得到了有效的解决。
新的材料配方和结构设计使得橡胶密封件在高温环境下具有更好的耐久性和密封性能,满足了客户的需求。
影响橡胶疲劳寿命的因素
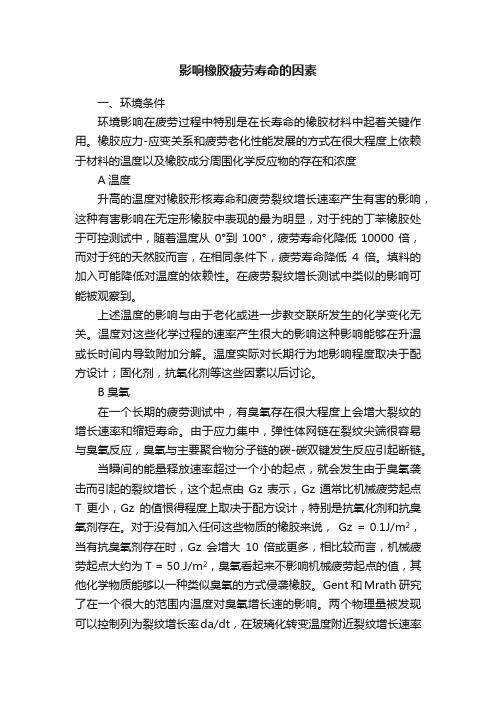
影响橡胶疲劳寿命的因素一、环境条件环境影响在疲劳过程中特别是在长寿命的橡胶材料中起着关键作用。
橡胶应力-应变关系和疲劳老化性能发展的方式在很大程度上依赖于材料的温度以及橡胶成分周围化学反应物的存在和浓度A温度升高的温度对橡胶形核寿命和疲劳裂纹增长速率产生有害的影响,这种有害影响在无定形橡胶中表现的最为明显,对于纯的丁苯橡胶处于可控测试中,随着温度从0°到100°,疲劳寿命化降低10000倍,而对于纯的天然胶而言,在相同条件下,疲劳寿命降低4倍。
填料的加入可能降低对温度的依赖性。
在疲劳裂纹增长测试中类似的影响可能被观察到。
上述温度的影响与由于老化或进一步教交联所发生的化学变化无关。
温度对这些化学过程的速率产生很大的影响这种影响能够在升温或长时间内导致附加分解。
温度实际对长期行为地影响程度取决于配方设计;固化剂,抗氧化剂等这些因素以后讨论。
B臭氧在一个长期的疲劳测试中,有臭氧存在很大程度上会增大裂纹的增长速率和缩短寿命。
由于应力集中,弹性体网链在裂纹尖端很容易与臭氧反应,臭氧与主要聚合物分子链的碳-碳双键发生反应引起断链。
当瞬间的能量释放速率超过一个小的起点,就会发生由于臭氧袭击而引起的裂纹增长,这个起点由Gz表示,Gz通常比机械疲劳起点T更小,Gz的值恨得程度上取决于配方设计,特别是抗氧化剂和抗臭氧剂存在。
对于没有加入任何这些物质的橡胶来说, Gz = 0.1J/m2,当有抗臭氧剂存在时,Gz会增大10倍或更多,相比较而言,机械疲劳起点大约为T = 50 J/m2,臭氧看起来不影响机械疲劳起点的值,其他化学物质能够以一种类似臭氧的方式侵袭橡胶。
Gent和Mrath研究了在一个很大的范围内温度对臭氧增长速的影响。
两个物理量被发现可以控制列为裂纹增长率da/dt,在玻璃化转变温度附近裂纹增长速率是与v温度成比例的,而与臭氧无关。
在足够高的温度下(Q-Tg >100°),裂纹增长速率完全依赖于臭氧浓度而与温度无关。
橡胶疲劳研究综述_王昊

零 的 恒幅 载荷下 某 填 充 橡 胶 的 裂 纹 扩 展 试 验 , 并 通过 对实 测数 据 的分析 将 橡胶裂纹扩展 特 性分 为 并给出了这4个阶段裂纹扩展速率的 4 个阶 段 , 近似 表达 式 , 如图1所示。
关 系 。 对于 结构相 对 规 则 的 简 单 试 样 ( 如简单拉 伸 试 样 和 纯 剪 试 样) 而言, 其远离 裂纹 处 的应 变能
[] R. S. R i v l i n等 8 将 G r i f f i t h的方法应用于橡 胶材料 撕 裂 问题 的研究中 。 他 们 发现 橡胶材料的
方法研究了 最小 应 变 对 两种 合成 橡胶疲劳寿命的 对于应 变结晶 的橡胶 , 循环 加 载 影响 。 一 般 来 说 , 最小 应 变 的 增 大 可 以 提 高 疲 劳 寿 命 。S. M. C a d - w e l l的研究 没 有提 到如 何将 载荷 状态 相 对 简单 的 实验 结 果 应用于 复杂 应 变 条 件 下 橡胶材料疲劳寿 基于 命的 预 测 。 而此 后 一 些 学 者 通 过 研 究 发 现 , 应 变 的疲劳 损 伤参量无 法 将简单拉伸 和 等 双轴拉
[] 劳 损 伤参量 。1 9 4 0年, S. M. C a d w e l l等 1 在 研 究
非填充硫 化 胶的 疲 劳 寿 命 时 发 现 : 在保持应变幅 值恒 定的情况 下 , 天然橡胶的疲劳寿命随着循环 最 小 应 变 的 增 大 而 延 长, 并且在最小应变小于 而 当 最小 应 2 0 0% 的情况 下 都 能 观察 到这 一 现象 , 变超过 这 一 水平 后 , 疲劳寿命又会随着最小应变
载次数; r A0 , B0 和 z 为 橡胶裂纹的 稳 定扩展 速 率 ;
橡胶地垫产品执行标准
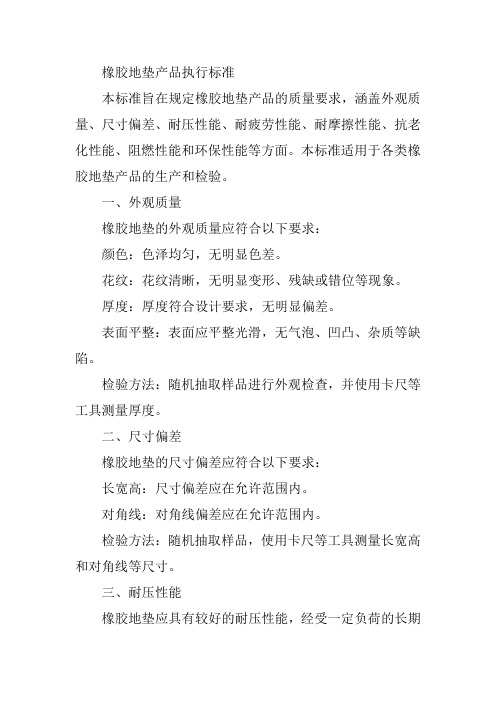
橡胶地垫产品执行标准本标准旨在规定橡胶地垫产品的质量要求,涵盖外观质量、尺寸偏差、耐压性能、耐疲劳性能、耐摩擦性能、抗老化性能、阻燃性能和环保性能等方面。
本标准适用于各类橡胶地垫产品的生产和检验。
一、外观质量橡胶地垫的外观质量应符合以下要求:颜色:色泽均匀,无明显色差。
花纹:花纹清晰,无明显变形、残缺或错位等现象。
厚度:厚度符合设计要求,无明显偏差。
表面平整:表面应平整光滑,无气泡、凹凸、杂质等缺陷。
检验方法:随机抽取样品进行外观检查,并使用卡尺等工具测量厚度。
二、尺寸偏差橡胶地垫的尺寸偏差应符合以下要求:长宽高:尺寸偏差应在允许范围内。
对角线:对角线偏差应在允许范围内。
检验方法:随机抽取样品,使用卡尺等工具测量长宽高和对角线等尺寸。
三、耐压性能橡胶地垫应具有较好的耐压性能,经受一定负荷的长期压力后仍能保持原有性能。
具体指标如下:静态负荷:在规定时间内,橡胶地垫应能承受一定重量的静态负荷而不会变形或损坏。
动态负荷:在规定时间内,橡胶地垫应能承受一定频率和振幅的动态负荷而不会变形或损坏。
检验方法:按照相关标准进行耐压性能测试。
四、耐疲劳性能橡胶地垫应具有较好的耐疲劳性能,能在反复载荷作用下保持原有性能。
具体指标如下:反复载荷:在规定次数的反复载荷作用下,橡胶地垫应能承受一定变形量而不损坏。
温度变化:在不同温度条件下,橡胶地垫的尺寸和性能应无明显变化。
抗老化性能:在长时间使用过程中,橡胶地垫应能保持原有性能而不易老化。
阻燃性能:橡胶地垫应具有一定的阻燃性能,确保在火灾情况下不会加速火势蔓延。
具体指标如下:燃烧时间:在规定时间内,橡胶地垫点燃后应能自熄或被外力移除后火势不再蔓延。
烟气毒性:燃烧过程中产生的烟气应无毒或低毒性,不危害人体健康。
检验方法:按照相关标准进行阻燃性能测试。
环保性能六、环保性能橡胶地垫的环保性能应符合以下要求:甲醛含量和苯等有害物质含量应符合国家相关标准要求。
检验方法:按照相关标准进行环保性能测试。
丁腈橡胶耐疲劳性能的研究
NB R 1 0 0 , 炭 黑N3 3 0 4 0 , 氧化 锌 酸 1 , 硫黄
摘要 : 通 过 压 缩 疲 劳 和 拉伸 疲 劳 试 验对 丁腈 橡 胶 ( NB R ) 耐疲 劳 性 能进 行 研 究 。结果 表 明 : 随着 压 缩疲 劳 次 数 增 大 , 硫化胶的硬度、 永久 变形 和温 升 均 在 疲 劳 前 期 迅 速 增 大 , 随 着 压缩 时 间延 长 , 增速减缓 ; 随 着 拉 伸 疲 劳 次数 增 大 , 硫 化 胶 的3 0 0 %定 伸 应 力 、 拉 伸强 度 和 拉 断伸 长 率 先增 大 后 减 小 , 总交 联 密 度 减小 , 1 0 mi n 时 的应 力 松 弛 系数 和 2 mi n 时 的 应力 松 弛 系数 变 化 趋势 相 同 , 均 先减 小 后 增 大 最后 趋 于 稳定 。
1 . 3 主 要设 备和 仪器
橡 胶 或热 塑性橡 胶 拉 伸应力 应 变性 能 的测定 》 进
行, 拉 伸 比为 1 0 0 %, 拉 伸 速 率 为3 0 0 辊 开炼 机 , 上 海 橡 胶 机 械 厂产
品; M2 0 0 0 一 A型 硫 化 仪 和 G T — T C S 一 2 0 0 0 型 电 子
关键 词 : 丁 腈橡 胶 ; 压缩疲劳 ; 拉伸 疲 劳 ; 应 力 松弛
中 图分 类 号 : TQ 3 3 3 . 7 文 献标 志码 : A 文章 编 号 : 1 0 0 0 — 8 9 0 x( 2 0 1 7 ) 0 5 — 0 2 7 5 — 0 4
橡胶疲劳的一些问题
天然橡胶就橡胶材料而言,它是指橡胶材料在重复变形的过程中,当其承受的局部变形应力超过橡胶的延伸率或应力极限时,疲劳过程开始,以至于最后达到破坏。
这种疲劳破坏的开始点是由于橡胶表面或内部的不均匀性所造成的。
橡胶材料的破坏主要是由于其内部的缺陷或微裂纹引发的裂纹不断传播和扩展而导致的。
按照分子运动论的观点,橡胶材料的动态疲劳破坏归因于材料本身分子链上化学键的断裂,即试样在受到周期应力一应变作用过程中,应力不断地集中于化学键能比较弱的部位而产生微裂纹,继而发展成为裂纹并随着时间的推移而逐步扩展开来。
裂纹发展是一个随着时间而发展,涉及到橡胶材料的分子链连续断裂的粘弹性非平衡动态变化过程。
这一微观发展过程在宏观上的表现是,橡胶材料在动态应力一应变的疲劳过程中,裂纹穿过试样不断扩展,直到断裂以及产生与之所伴随的热效应。
橡胶材料的动态疲劳过程一般可以分为三个阶段:第一阶段是应力剧烈变化,出现橡胶材料在应力作用下变软的现象;第二阶段是应力缓慢变化,橡胶材料表面或内部产生微裂纹,经常称之为破坏核;第三阶段是微裂纹发展成为裂纹并连续不断地扩展开,直到橡胶材料完全出现断裂破坏现象,最后这一阶段是橡胶材料疲劳破坏的最重要的阶段。
使用炭黑填充的天然橡胶硫化胶在一定负荷下多次拉伸变形时,橡胶的物理机械性能在疲劳过程中,拉伸强度先是逐步上升的,经过一个极大值后再开始下降,而撕裂强度、动态弹性模量和力学损耗因子的变化则相反。
在疲劳过程中,胶料的拉伸强度几乎保持不变。
300%定伸应力的疲劳开始阶段明显增大,然后增大趋于缓慢;扯断伸长率则随疲劳周期的变化而下降,在高应变疲劳条件下,具有拉伸结晶性的橡胶抗疲劳破坏性能较好。
未使用补强剂补强的橡胶材料,其破坏形态一般表现为塑性破坏,而使用炭黑或其它活性填料作补强剂的橡胶材料则表现为脆性破坏,且随着各种防老剂的加入,其破坏形态由脆性破坏逐步向准塑性破坏形态转变。
天然橡胶在受到一定频率的应力作用的条件下,由于分子链的内摩擦而生热是其动态疲劳破坏的另外一种因素。
橡胶疲劳寿命影响因素概述
就橡胶材料而言,它是指橡胶材料在重复变形的过程中,当其承受的局部变形应力超过橡胶的延伸率或应力极限时,疲劳过程开始,以至于最后达到破坏。
这种疲劳破坏的开始点是由于橡胶表面或内部的不均匀性所造成的。
橡胶材料的破坏主要是由于其内部的缺陷或微裂纹引发的裂纹不断传播和扩展而导致的。
按照分子运动论的观点,橡胶材料的动态疲劳破坏归因于材料本身分子链上化学键的断裂,即试样在受到周期应力一应变作用过程中,应力不断地集中于化学键能比较弱的部位而产生微裂纹,继而发展成为裂纹并随着时间的推移而逐步扩展开来。
裂纹发展是一个随着时间而发展,涉及到橡胶材料的分子链连续断裂的粘弹性非平衡动态变化过程。
这一微观发展过程在宏观上的表现是,橡胶材料在动态应力一应变的疲劳过程中,裂纹穿过试样不断扩展,直到断裂以及产生与之所伴随的热效应。
橡胶材料的动态疲劳过程一般可以分为三个阶段:第一阶段是应力剧烈变化,出现橡胶材料在应力作用下变软的现象;第二阶段是应力缓慢变化,橡胶材料表面或内部产生微裂纹,经常称之为破坏核;第三阶段是微裂纹发展成为裂纹并连续不断地扩展开,直到橡胶材料完全出现断裂破坏现象,最后这一阶段是橡胶材料疲劳破坏的最重要的阶段。
使用炭黑填充的天然橡胶硫化胶在一定负荷下多次拉伸变形时,橡胶的物理机械性能在疲劳过程中,拉伸强度先是逐步上升的,经过一个极大值后再开始下降,而撕裂强度、动态弹性模量和力学损耗因子的变化则相反。
在疲劳过程中,胶料的拉伸强度几乎保持不变。
300%定伸应力的疲劳开始阶段明显增大,然后增大趋于缓慢;扯断伸长率则随疲劳周期的变化而下降,在高应变疲劳条件下,具有拉伸结晶性的橡胶抗疲劳破坏性能较好。
未使用补强剂补强的橡胶材料,其破坏形态一般表现为塑性破坏,而使用炭黑或其它活性填料作补强剂的橡胶材料则表现为脆性破坏,且随着各种防老剂的加入,其破坏形态由脆性破坏逐步向准塑性破坏形态转变。
天然橡胶在受到一定频率的应力作用的条件下,由于分子链的内摩擦而生热是其动态疲劳破坏的另外一种因素。
橡胶材料的疲劳性能分析
橡胶材料的疲劳性能分析橡胶是一种经常被使用的材料,它可以被应用在各种场合,例如汽车轮胎、机械密封件、管道等。
然而,这种材料在长时间的使用过程中会遭受众多的疲劳损伤,而这些损伤是不可避免的。
因此,理解橡胶材料的疲劳特性是非常重要的,这不仅可以提高橡胶制品的耐久性,还可以为工程领域提供有用的信息。
橡胶材料的疲劳现象指的是在反复的应力和形变交替作用下,材料内部出现的破裂、断裂、裂纹扩展等现象。
在橡胶材料中,疲劳机理主要可以归纳为两种:一种是底层断裂模式,另一种是表层断裂模式。
底层断裂模式指的是在材料中部或下部形成的疲劳破坏,而表层断裂模式指的是在材料表面形成的疲劳破坏。
为了更好地理解和评估橡胶材料的疲劳性能,工程师们可以利用实验方法进行研究。
其中,最常用的疲劳试验方法是拉伸疲劳试验,这种试验方式既能够确定橡胶材料在不同载荷下的疲劳极限,同时也能够评估材料的耐久性。
在进行拉伸疲劳试验时,需要注意试验的载荷频率、环境温度、湿度等参数,同时应使用符合标准的试验设备,以确保实验结果的准确性和可靠性。
在进行橡胶材料的疲劳性能评估时,应注意以下几个方面:1. 不同类型的橡胶材料的疲劳性能有所不同,需要根据实际应用需求选择合适的材料类型。
2. 利用不同的试验方法可以获得不同的疲劳性能数据,应根据实际应用需求选择合适的试验方法。
3. 环境条件对橡胶材料的疲劳性能有重要影响,应在实际使用环境下进行合适的疲劳试验。
4. 不同的疲劳模式需要采取不同的措施进行防止和修复,应根据疲劳模式的不同选择合适的预防和修复方法。
综上所述,橡胶材料的疲劳性能是影响橡胶制品寿命和性能的重要因素,能够对该领域的工程师们提供有益的信息。
因此,对橡胶材料的疲劳性能进行深入研究和评估是非常重要的,可以帮助我们更好地理解材料的性能和特点,从而提高橡胶制品的质量和可靠性。
- 1、下载文档前请自行甄别文档内容的完整性,平台不提供额外的编辑、内容补充、找答案等附加服务。
- 2、"仅部分预览"的文档,不可在线预览部分如存在完整性等问题,可反馈申请退款(可完整预览的文档不适用该条件!)。
- 3、如文档侵犯您的权益,请联系客服反馈,我们会尽快为您处理(人工客服工作时间:9:00-18:30)。
橡胶耐疲劳性
橡胶担当交变循环应力或应变时所引起的局部构造改变和内部缺陷的成长经过,称为橡胶的疲钝。
在动态拉伸、压缩、扭曲和剪切作用下,橡胶制品的性能和构造会产生改变,或发生毁坏,这便是所谓的疲钝毁坏。
它使质料的力学性能降低,并最终导致龟裂或完全断裂。
橡胶的疲钝实质是受力和热的作用时橡胶发生老化的表象,包罗了屈挠疲钝和老化疲钝。
橡胶发生疲钝的条件许多,比方,伸长或压缩;周期性的外力作用等。
假使统一种橡胶在分歧疲钝条件下,再现的耐疲钝性也纷歧样,如自然橡胶和丁苯橡胶经重复变形时,重复变形小,丁苯橡胶的耐疲钝毁坏优于自然橡胶;而重复变形大,自然橡胶的耐疲钝毁坏性则优于丁苯橡胶。
因此务必凭据分歧疲钝条件选择最适宜的橡胶。
硫化胶的疲钝寿命与其物理机械性能亲密联系。
刚度对疲钝寿命有双重影响:在恒定应变条件下,增加刚度,导致应力增大,会低落硫化胶的疲钝寿命;在恒定应力振幅条件下,增加刚度,导致应变低落,能抬高硫化胶的疲钝寿命。
拉伸强度和扯破强度的增加,普通都能抬高疲钝寿命。
在应力振幅较高的条件下,硫化胶的强度性能对疲钝毁坏格外重要。
由于在动态条件下,存在一个最大扯破强度临界值。
硫化胶的强度超出这个临界值时就不出现裂纹扩展;一致则会较快地出现裂纹扩展。
扯断伸长率普通也与疲钝寿命成正比。
在别的条件相似的情形下,滞后性能的增长,能阻缓裂纹扩展,抬高疲钝寿命。
硫化体系对耐疲钝性能的影响很大,古代硫化体系的硫化胶要比有用硫化体系和过氧化物硫化体系的硫化胶耐疲钝性能好。
在恒定形变条件下,硫化胶的疲钝寿命随定伸应力值低落而增长。
在恒定应力的条件下,硫化胶的疲钝寿命随定伸应力增加而增长。
由于变形与定伸应力成反比,在给定应力下,较高定伸应力的橡胶变形较小,有利于疲钝寿命的抬高。
普通说来,高耐磨炉黑比槽法炭黑的疲钝寿命长;增加增添剂的硫化胶其耐疲钝性能有所抬高。
采纳极性、软化点高的软化剂可改良疲钝性能。
防老剂因压制了氧化老化和臭氧老化等疲钝所发生的化学反响,故抬高了橡胶的耐疲钝性能。
硫化胶的疲钝毁坏是在局部产生的,因此能敏捷迁徙的防老剂,对防备硫化胶永劫间疲钝老化相当有用。
但是,这时防老剂从制品外观挥发的速率和被液体介质冲洗的速率也会随之加速。
普通宜采纳芳基烷基苯二胺或二烷基-对苯二胺类防老剂。