八大浪费案例
合集下载
八大浪费案例(组装)

Fire Clip壓合
時間 4.2
人
1
設備 1
Fire Clip裝配&鎖緊
時間 人10
12.7 3
制造過多浪費案例2-現狀描述
目前生產的形式為多機種少批量,因客戶訂單變更導致成品呆滯的 現象時有發生,由此造成製造過剩的浪費非常嚴重!
呆滯庫存數量為:
制
造
1100Kpcs/月
過
剩
平均呆滯時間為:
浪
費
6.5個月
改善前
3人
改善后
等待浪費案例2-現狀描述
風散組裝線由于產線不平衡且測試段是瓶頸,測試段堆 積許多待測風扇,其後工站-包裝存在等待的浪費
在
制
品
浪
31
等待浪費案例2-對策&效果
。對策﹕增加測試機台﹐合理配置人員以消除瓶頸 。效果﹕提高線平衡率和UPPH.
線線平平衡衡率率提提高高 平衡率
UPPH
UUPPPPHH提提升升
將clip檢查作 業和Clip彎曲 檢查作業合并
E
C CRS
S
將Clip彎曲 檢查作業反復 5次簡化壓3次
29
等待浪費案例1-效果對比
壓clip
時間 4.2S
人
1
設備 1
工時
22.1S
25
20
15
10
5
0 改善前
改善后
12.4S
Clip彎曲檢查
時間 8S
人
2
設備 2
30
人力
5人
5 4 3 2 1 0
19
搬運浪費案例1-改善對策
。優化產線布局﹐將部品加工設備直接搬到產 線上來﹐并通過加裝滑槽的方式﹐使加工好的 產品直接流到產線上。
八大浪费

12种动作浪费的源头都可以追溯到“动作经济原则”。动作经济原则又 叫动作舒适原则,是由吉尔布雷斯在20世纪20年代首创,后经若干 学者详加研究改进而成的改善作业方法的一项基本手法,是基础工 业工程手法体系中主要的组成部分之一。共有三大类22项
5、加工浪费
定义:
加工过剩的浪费也叫过分 加工的浪费,是指在品质 、规格及加工过程上的投入 主动超过客户需求从而 造成企业资源浪费的情况。 加工过剩浪费分四种情况: 过剩品质、过剩加工、 过剩检验、过剩设计
8、管理浪费
定义:
在制造现场,管理的目 的是使人机料处于最佳 的受控状态,对于问题 的处理和解决做到快速 有效,能够有效地提高 效率,维持高的质量水 平、低的成本水平及快 的物流速度,恰到好处 的交期,从而提高企业 的身体体质和市场竞争力
产生原因:
(1)管理浪费之等待浪费 ①等待上级的指示 ②等待外部的回复 ③等待下级的汇报 ④等待生产现场的联系
4、动作浪费
产生原因:
解决方法: 定义:
动作浪费指生产中在动作 上的不合理而导致的时间 、效率、场地、人员及 人身等方面的浪费。 (1)操作不精简、多余 (2)设计不合理 ①可同时完成但未同时 ②不必要但被增加 ③可同规格但不同 ④未考虑调整/转换/取放 ⑤物料需要翻找 (1)按经济原则设计工站 操作并进行标准化 (2)设计必须经过验证 才可以实施 (3)根据人因工程学理论 设计符合人体工效 的作业方法
南山轻合金有限公司
八大浪费
目
1
录
八大浪费的起源
2
八大浪费具体分类
3
八大浪费的案例
1、八大浪费的起源
八大浪费是丰田生产方式中非常重要的一 个观念。丰田人认为要消除浪费,持续改 善,企业才能保持良性运转,竞争力才会 提升。丰田人在长期作业和改善过程中对 于浪费的内容进行了总结,共七种,被称 为七大浪费。后来人们又加了一种浪费管理的浪费,合称八大浪费。
八大浪费的培训

建立智能调度系统,实现车辆和 人员的实时调度和监控,提高运 输效率和服务质量。
REPORT
06
实战演练:团队如何开展减 少浪费活动
制定减少浪费计划和目标
分析现状
对现有的生产流程、物料使用、人员配置等进行全面 分析,找出存在的浪费现象。
制定目标
根据分析结果,制定具体的减少浪费目标,如降低不 良品率、减少库存量等。
企业管理制度不健全或执行不力,导致员工行为不规范,造成资源 浪费。
REPORT
04
识别与消除浪费方法论述
现场观察法
直接观察工作流程
深入现场,实地查看工作流程,了解实际操作情况,发现 浪费现象。
与员工交流
与员工面对面交流,了解他们的想法和建议,共同发现浪 费问题。
记录并分析
详细记录观察到的浪费现象,分析原因,提出改进措施。
01
浪费概述与分类
浪费定义及影响
浪费定义
在生产和服务过程中,未能创造 价值或增加成本的活动,即资源 (时间、人力、物力、财力等) 的无效或低效使用。
浪费影响
导致企业成本增加、效率降低、 质量不稳定、客户满意度下降等 负面影响,严重制约企业的竞争 力和可持续发展。
八大浪费简介
不良、修理的浪费
01
指因产品质量问题导致的浪费,包括不良品的产生、返修、报
员工对操作不熟悉,导致动作不连贯 、效率低下。
等待时间浪费
生产计划不合理
生产计划安排不当,导致员工等待物料、设备、 上道工序等。
设备故障
设备故障频发,导致生产中断,员工需要等待设 备维修。
物料供应不及时
物料供应不及时或物料品质问题,导致生产停滞 ,员工等待物料到来。
加工过剩浪费
REPORT
06
实战演练:团队如何开展减 少浪费活动
制定减少浪费计划和目标
分析现状
对现有的生产流程、物料使用、人员配置等进行全面 分析,找出存在的浪费现象。
制定目标
根据分析结果,制定具体的减少浪费目标,如降低不 良品率、减少库存量等。
企业管理制度不健全或执行不力,导致员工行为不规范,造成资源 浪费。
REPORT
04
识别与消除浪费方法论述
现场观察法
直接观察工作流程
深入现场,实地查看工作流程,了解实际操作情况,发现 浪费现象。
与员工交流
与员工面对面交流,了解他们的想法和建议,共同发现浪 费问题。
记录并分析
详细记录观察到的浪费现象,分析原因,提出改进措施。
01
浪费概述与分类
浪费定义及影响
浪费定义
在生产和服务过程中,未能创造 价值或增加成本的活动,即资源 (时间、人力、物力、财力等) 的无效或低效使用。
浪费影响
导致企业成本增加、效率降低、 质量不稳定、客户满意度下降等 负面影响,严重制约企业的竞争 力和可持续发展。
八大浪费简介
不良、修理的浪费
01
指因产品质量问题导致的浪费,包括不良品的产生、返修、报
员工对操作不熟悉,导致动作不连贯 、效率低下。
等待时间浪费
生产计划不合理
生产计划安排不当,导致员工等待物料、设备、 上道工序等。
设备故障
设备故障频发,导致生产中断,员工需要等待设 备维修。
物料供应不及时
物料供应不及时或物料品质问题,导致生产停滞 ,员工等待物料到来。
加工过剩浪费
成来电气精益管理项目八大浪费课件

以客户为中心
以客户为中心是精益管理的重要原则之一,它要求企 业始终关注客户需求,以满足客户需求为出发点,设 计和优化自身的产品和服务。
通过以客户为中心,企业可以更好地理解客户需求,提 高客户满意度和忠诚度,并创造更大的价值。
数据驱动决策
01
数据驱动决策是精益管理的重要 原则之一,它要求企业基于数据 和分析进行决策,而不是基于经 验和直觉。
库存
库存浪费是指过多的原材料、在制品和成品积压在仓库中,导致仓储成本增加和 资金占用。
解决方案:实施精益库存管理,通过精确的需求预测和计划,降低库存水平,实 现库存周转率的提高。
过程浪费
过程浪费是指生产过程中存在的不增 值的环节或动作。
解决方案:对生产过程进行价值流分 析,识别并消除不增值的环节或动作 ,提高生产效率。
成来电气精益管理项目八大浪费课 件
目录
• 八大浪费的识别 • 八大浪费的根源分析 • 消除八大浪费的策略 • 实施精益管理的关键要素 • 成来电气精益管理项目案例分享
01
八大浪费的识别
定义与特点
八大浪费是指
过度生产、等待、运输、库存、 过程(加工)、动作、不良品和 多余的附带动作。
八大浪费的特点是
全员参与
全员参与是精益管理的另一个关键要素,它 强调企业内部的每个员工都应该参与到精益 管理的实践中来。
通过全员参与,企业可以更好地整合资源、 提高工作效率、减少浪费,并增强员工的归
属感和责任感。
跨部门协作
精益管理要求企业打破部门壁垒,加强跨部门协作, 以提高整体效率和效益。
通过跨部门协作,企业可以更好地整合资源、优化流 程、提高工作效率,并减少重复和浪费。
项目实施过程
现场改善案例(八大浪费)

4.IE的改善意識(2)
7) 兩人的知識大于一人的智慧﹐全員參與才 可以共同進步﹔ 8) 改善不應大量投資﹔ 9) 積極尋找解決問題的方法而不是不可行的 理由﹔ 10)不要為現狀辯解﹐實事求是﹔
二. 现场IE改善<1>何谓标准工 时
标准时间是指,“一个熟练工用规定的 作业方法以标准速度进行作业时所需的 作业时间”。
基礎IE概論
一. 基礎工業工程概述
二. 现场IE三原则 三. 現場IE改善
四. IE活動的導入與推進
五. 基礎IE改善手法
一.基礎工業工程概述 1.什么是工業工程(IE)?
工業 工程
INDUSTRIAL ENGINEERING
20年代后期﹕起源于美國 80年代初期﹕引進我國大陸
2.IE的定義
“工業工程,是對人員、物料、設備、能源和
搬 运
浪 费
移动费时费力
空间、时间、人力和工具浪费 搬运过程中的放置、堆积、移 动、整理等都造成浪费。
浪费
不良造成额外成本
常见的不良造成的損失: ☆ 材料损失 ☆ 设备折旧 ☆ 人工损失 ☆ 能源损失 ☆ 价格损失 ☆ 订单损失 ☆ 信誉损失
动作
浪费
多余动作 增加强度降低效率
常见的12种浪费动作: ① 两手空闲 ⑦ 转身角度大 ② 单手空闲 ⑧ 移动中变换动作 ③ 作业动作停止 ⑨ 未掌握作业技巧 ④ 动作幅度过大 ⑩ 伸背动作 ⑤ 左右手交换 ⑾ 弯腰动作 ⑥ 步行多 ⑿ 重复/不必要动作
加工 浪费
过剩的加工造成浪费
常见的加工浪费: ☆ 加工余量 ☆ 过高的精度 ☆ 不必要的加工 过剩加工造成的浪费: ☆ 设备折旧 ☆ 人工损失 ☆ 辅助材料损失 ☆ 能源消耗
SMT八大浪费案例
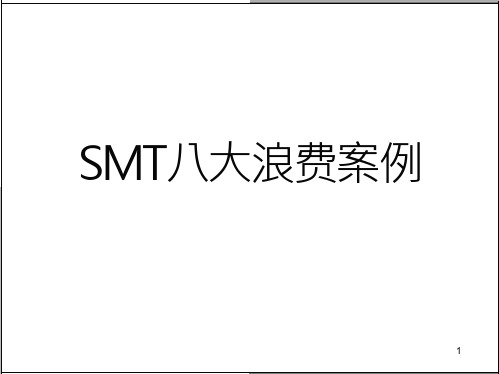
标准作业指导书, 清楚定义作业步
骤及内容 使用电子广告牌 进 行质量监控, 发生 不良立即整 改
改善绩效
通过标准作业指导书及 电子广告牌的推广,该机 种平 均良率由95.79%提 升至 99.31%.
6
1.2 U4空焊不良修正浪费一 、改善前
U4空焊不良率
800 600 400 200
0
DPPM
目标 160
上水位 传感器
下水位 传感器
上下水位 报警装置
改善前
防呆报 警系统
空间利用率 货架空间利用率低 上部空间利用率低
总体空间利用率低
布局物流杂亂 仓库布局为经验布局 物流线路不合理局部物
流量大
1.重新Layout后对各货架实行店面管理及分類管理 保证先进先出,及时來料及时交付生产,降低库存.
2.设置防呆的报警系统,货架上下水位报警,使仓库 人员及时对其进行仓储管控
用200元/m2*1428m2=284800元 2.节约物料架 成本:2500元/个*10个=25000元
五金 仓
待验 区
不良 品仓
改善后充分提 高货架空间利 用率及上部空 间.同时导入看
板管理
被动 仓
办公 区
PCB 仓
新机 种仓
主贵 仓
下料电梯
35
5.2 SMT与PTH半成品库存改善
现狀描述 1.图示为SMT
等待 (流
NA
?
测试存在极大的 检验过剩浪费, 依 据 ECRS,取 消 不必要测试画 面
﹒ 根据测试工程师提供 光的不良
BMA TEST 主要检测 B/L 異物亮点及漏
﹒ 黑画面主要检测: 亮点,画面均匀度,线缺陷,白点,麻点, 静电 白线
骤及内容 使用电子广告牌 进 行质量监控, 发生 不良立即整 改
改善绩效
通过标准作业指导书及 电子广告牌的推广,该机 种平 均良率由95.79%提 升至 99.31%.
6
1.2 U4空焊不良修正浪费一 、改善前
U4空焊不良率
800 600 400 200
0
DPPM
目标 160
上水位 传感器
下水位 传感器
上下水位 报警装置
改善前
防呆报 警系统
空间利用率 货架空间利用率低 上部空间利用率低
总体空间利用率低
布局物流杂亂 仓库布局为经验布局 物流线路不合理局部物
流量大
1.重新Layout后对各货架实行店面管理及分類管理 保证先进先出,及时來料及时交付生产,降低库存.
2.设置防呆的报警系统,货架上下水位报警,使仓库 人员及时对其进行仓储管控
用200元/m2*1428m2=284800元 2.节约物料架 成本:2500元/个*10个=25000元
五金 仓
待验 区
不良 品仓
改善后充分提 高货架空间利 用率及上部空 间.同时导入看
板管理
被动 仓
办公 区
PCB 仓
新机 种仓
主贵 仓
下料电梯
35
5.2 SMT与PTH半成品库存改善
现狀描述 1.图示为SMT
等待 (流
NA
?
测试存在极大的 检验过剩浪费, 依 据 ECRS,取 消 不必要测试画 面
﹒ 根据测试工程师提供 光的不良
BMA TEST 主要检测 B/L 異物亮点及漏
﹒ 黑画面主要检测: 亮点,画面均匀度,线缺陷,白点,麻点, 静电 白线
八大浪费案例

• 線體布局優化改善
•沖模物流
•塑模物流
•暫存 區
•待檢 區
•成品 區
•成品 區
•待檢 區
•暫存 區
•沖模物流
•塑模物流
五﹑庫存浪费
• 倉庫存儲量大﹐大 部分物料在倉庫存 放時間也比較長
• 現場暫存區原料較 多。
改善對策
• 計算物流﹔設定庫存量﹑定貨點﹔設立庫 存過少和過多的警示線嚴格控制庫存量
六﹑等待浪费
•等待上站產品的到來
• 平衡生產線﹔ • 計算制程瓶頸﹐控制排程﹐不
盲目生產 • 降低等待和WIP
改善對策 •瓶頸 •11.75 s •平衡率74.2% •平衡率89.8%
七﹑动作浪费
• 由于擺放不合理﹐員工工作時需要頻 繁轉身﹑彎腰﹑起立等
改善對策
• 重新設計工作台
八﹑管理浪費
• 天車稼動率不 高﹐卻經常發 生多人等待天 車的現象。八大浪费案例Fra bibliotek•目錄
一 不良修正浪費 二 製造過多浪費 三 加工過剩浪費 四 搬運浪費 五 庫存浪費 六 等待浪費 七 動作浪費 八 管理浪費
一﹑不良修正浪费
各工段都可能造成加工不良﹐一旦產生 不良﹐所有的工作都不會產生價值﹐成為 了浪費。
• 抽樣檢驗 • 魚骨分析 • 質量控制圖 • DOE實驗 • ……
改善對策
二﹑制造過多浪费
• 制造過早導致在制堵塞在下一工段。造成 現場擁擠﹐5S情況差
三﹑加工過剩浪费
自動機零件加工部的精度是10條﹐而部 分零件對于精度要求其實沒那么高﹐屬于 加工浪費。后來與客戶溝通﹐把精度降到 50條﹐大大降低了加工時間。
四﹑搬運浪费
• 下一工站設置不合理﹐搬運距離過長
改善對策
•沖模物流
•塑模物流
•暫存 區
•待檢 區
•成品 區
•成品 區
•待檢 區
•暫存 區
•沖模物流
•塑模物流
五﹑庫存浪费
• 倉庫存儲量大﹐大 部分物料在倉庫存 放時間也比較長
• 現場暫存區原料較 多。
改善對策
• 計算物流﹔設定庫存量﹑定貨點﹔設立庫 存過少和過多的警示線嚴格控制庫存量
六﹑等待浪费
•等待上站產品的到來
• 平衡生產線﹔ • 計算制程瓶頸﹐控制排程﹐不
盲目生產 • 降低等待和WIP
改善對策 •瓶頸 •11.75 s •平衡率74.2% •平衡率89.8%
七﹑动作浪费
• 由于擺放不合理﹐員工工作時需要頻 繁轉身﹑彎腰﹑起立等
改善對策
• 重新設計工作台
八﹑管理浪費
• 天車稼動率不 高﹐卻經常發 生多人等待天 車的現象。八大浪费案例Fra bibliotek•目錄
一 不良修正浪費 二 製造過多浪費 三 加工過剩浪費 四 搬運浪費 五 庫存浪費 六 等待浪費 七 動作浪費 八 管理浪費
一﹑不良修正浪费
各工段都可能造成加工不良﹐一旦產生 不良﹐所有的工作都不會產生價值﹐成為 了浪費。
• 抽樣檢驗 • 魚骨分析 • 質量控制圖 • DOE實驗 • ……
改善對策
二﹑制造過多浪费
• 制造過早導致在制堵塞在下一工段。造成 現場擁擠﹐5S情況差
三﹑加工過剩浪费
自動機零件加工部的精度是10條﹐而部 分零件對于精度要求其實沒那么高﹐屬于 加工浪費。后來與客戶溝通﹐把精度降到 50條﹐大大降低了加工時間。
四﹑搬運浪费
• 下一工站設置不合理﹐搬運距離過長
改善對策
八大浪费案例(举例之成型)参考文档

18
等待浪費2--現狀描述
模具動作
1.開模 2.頂針頂出 3.頂針退回 4.合模
機械手動作
8
6 15
7
模內2 作業 影3響周4期
1.主臂下降
2.前進 3.夾產品 4.后退
5.主臂上升
6.橫出 7.放產品 8.橫入
19
等待浪費2—對策&效果
製品名稱︰Neo后飾板成型加工 工站名稱︰Neo后飾板成型加工
其他動作 6.6S
1 2 3 4 5 6 7 8 9 10 11 12 13
13.7 14 15
15.9
開模 4S
頂針頂出 1.6S
前進時間 0.5S
頂針退回 1S
等待 3.5S
下降 1.2S 前進取產品 1S 退回,上升 1.4S
合模 6.6S
其他動作 6.6S
2.2S
20
等待浪費2—對策&效果
3
不良修正浪費1--對策&效果
改善對策:
在削毛邊工站後增加一上檢 人員,檢查面板來料不良
改善效不果良: 報廢減少20%
4
不良修正浪費2--現狀描述
F產品銘牌產品用真空盤包裝,裝箱時采用直接疊加方
式,搬運過程中出現碰刮傷,不良率為25%,需投入2人
從事修復作業5来自不良修正浪費2- -對策&效果
改善對策:
26
管理浪費1—對策&效果
1.DT(II)成型加工多功能機械手治具架
快 速 換 線 機 械 手 治 具 架
27
管理浪費2--現狀描述
此為緊急物料﹐由于缺乏有效管制方式﹐頻繁 出現斷料而導致主線出現停線現象
28
管理浪費2—對策&效果
等待浪費2--現狀描述
模具動作
1.開模 2.頂針頂出 3.頂針退回 4.合模
機械手動作
8
6 15
7
模內2 作業 影3響周4期
1.主臂下降
2.前進 3.夾產品 4.后退
5.主臂上升
6.橫出 7.放產品 8.橫入
19
等待浪費2—對策&效果
製品名稱︰Neo后飾板成型加工 工站名稱︰Neo后飾板成型加工
其他動作 6.6S
1 2 3 4 5 6 7 8 9 10 11 12 13
13.7 14 15
15.9
開模 4S
頂針頂出 1.6S
前進時間 0.5S
頂針退回 1S
等待 3.5S
下降 1.2S 前進取產品 1S 退回,上升 1.4S
合模 6.6S
其他動作 6.6S
2.2S
20
等待浪費2—對策&效果
3
不良修正浪費1--對策&效果
改善對策:
在削毛邊工站後增加一上檢 人員,檢查面板來料不良
改善效不果良: 報廢減少20%
4
不良修正浪費2--現狀描述
F產品銘牌產品用真空盤包裝,裝箱時采用直接疊加方
式,搬運過程中出現碰刮傷,不良率為25%,需投入2人
從事修復作業5来自不良修正浪費2- -對策&效果
改善對策:
26
管理浪費1—對策&效果
1.DT(II)成型加工多功能機械手治具架
快 速 換 線 機 械 手 治 具 架
27
管理浪費2--現狀描述
此為緊急物料﹐由于缺乏有效管制方式﹐頻繁 出現斷料而導致主線出現停線現象
28
管理浪費2—對策&效果
- 1、下载文档前请自行甄别文档内容的完整性,平台不提供额外的编辑、内容补充、找答案等附加服务。
- 2、"仅部分预览"的文档,不可在线预览部分如存在完整性等问题,可反馈申请退款(可完整预览的文档不适用该条件!)。
- 3、如文档侵犯您的权益,请联系客服反馈,我们会尽快为您处理(人工客服工作时间:9:00-18:30)。
4
二、制造過多浪费
• 制造過早導致在制堵塞在下一工段。造成 現場擁擠﹐5S情況差
5
三、加工過剩浪费
自動機零件加工部的精度是10條﹐而部 分零件對于精度要求其實沒那么高﹐屬于 加工浪費。后來與客戶溝通﹐把精度降到 50條﹐大大降低了加工時間。
6
四、搬運浪费
• 下一工站設置不合理﹐搬運距離過長
7
改善對策
站產 待上 等
到來 品的
等待上站產品的到來
11
改善對策
瓶頸 11.75s
• 降 低 等 待 和 盲 目 生 產
• • 計 算 制 程 瓶 頸 , 控 制 排 程 , 不 平 衡 生 產%
12
七、动作浪费
• 由于擺放不合理﹐員工工作時需要頻 繁轉身、彎腰、起立等
• 線體布局優化改善
沖模物流
塑模物流
暫存 區
待檢 區
成品 區
成品 區
待檢 區
暫存 區
沖模物流
8
塑模物流
五、庫存浪费
• 倉庫存儲量大﹐大 部分物料在倉庫存 放時間也比較長
9
• 現場暫存區原料較 多。
改善對策
• 計算物流﹔設定庫存量、定貨點﹔設立庫 存過少和過多的警示線嚴格控制庫存量
10
六、等待浪费
13
改善對策
• 重新設計工作台
14
八、管理浪費
• 天車稼動率不 高﹐卻經常發 生多人等待天 車的現象。
15
改善對策
• 制作稼動率分析圖 • 優化排程﹐合理錯峰
16
模具類八大浪費案例
1
目錄
一 二 三 四 五 六 七 八 不良修正浪費 製造過多浪費 加工過剩浪費 搬運浪費 庫存浪費 等待浪費 動作浪費 管理浪費
2
一、不良修正浪费
各工段都可能造成加工不良﹐一旦產生 不良﹐所有的工作都不會產生價值﹐成為 了浪費。
3
改善對策
• • • • • 抽樣檢驗 魚骨分析 質量控制圖 DOE實驗 ……