现场改善案例八大浪费共47页文档
精益生产管理八大浪费与解决方法详细版之欧阳德创编
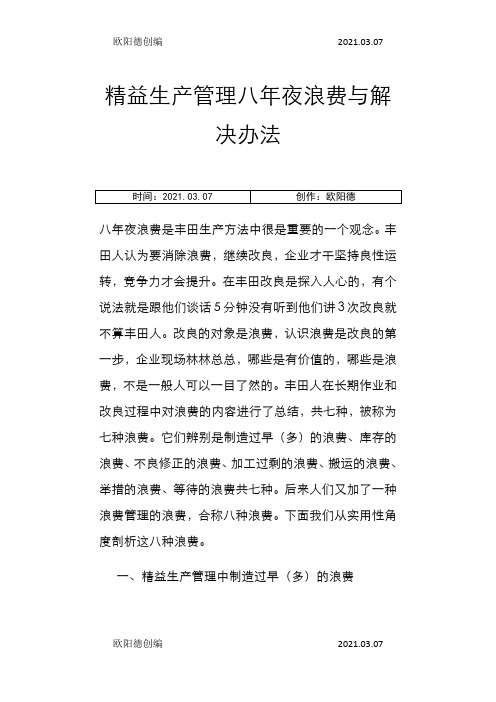
精益生产管理八年夜浪费与解决办法八年夜浪费是丰田生产方法中很是重要的一个观念。
丰田人认为要消除浪费,继续改良,企业才干坚持良性运转,竞争力才会提升。
在丰田改良是探入人心的,有个说法就是跟他们谈话5分钟没有听到他们讲3次改良就不算丰田人。
改良的对象是浪费,认识浪费是改良的第一步,企业现场林林总总,哪些是有价值的,哪些是浪费,不是一般人可以一目了然的。
丰田人在长期作业和改良过程中对浪费的内容进行了总结,共七种,被称为七种浪费。
它们辨别是制造过早(多)的浪费、库存的浪费、不良修正的浪费、加工过剩的浪费、搬运的浪费、举措的浪费、等待的浪费共七种。
后来人们又加了一种浪费管理的浪费,合称八种浪费。
下面我们从实用性角度剖析这八种浪费。
一、精益生产管理中制造过早(多)的浪费界说:所谓制造过早(多)就是前制程制造太早/过多,年夜于客户(或后制程)当期的最小需要量。
制造过早(多)浪费是八年夜浪费中的首恶,在精益生产中则被视为最年夜的浪费。
福特式思维告诉年夜家,在同样的时间内,生产量越多,效率越高,本钱越低,企业越赚钱,所以企业自然有年夜批量连续生产的初始动力。
作为一个整体的企业是如此,那么企业内各部分也是如此,特别是在一些制程较短,关联性较低的企业中,普遍实施计件工资,那么从最基础的员工开始就有多做、早做,甚至偷做的动力,在这种情况下,告知企业里所有人早(多)做是罪恶固然得不到掌声回应。
那么我们就来看看制造过早(多)的浪费。
制造过早(多)浪费的后果主要有三年夜类。
1.直接财务问题。
表示为库存、在制品增加,资金回转率低,制造时间变长,占用资金及利息,会造成库存空间的浪费,在现金流量表上很明显。
2.产生次生问题。
会产生搬运、聚积的浪费;先进先出的工作产生困难;产品积压造成不良产生,物流阻塞制程时间变长,现场工作空间变小,有滞留在库的风险,有不良品的风险。
3.掩盖问题。
为什么“制造过早(多)浪费是八年夜浪费中的首恶,在精益生产中则被视为最年夜的浪费”?因为它带给人们一个安心的错觉,掩盖了各种问题,以及隐藏了由于等待所带来的浪费,没有改良的动力,失去了继续改良的时机。
SMT八大浪费案例
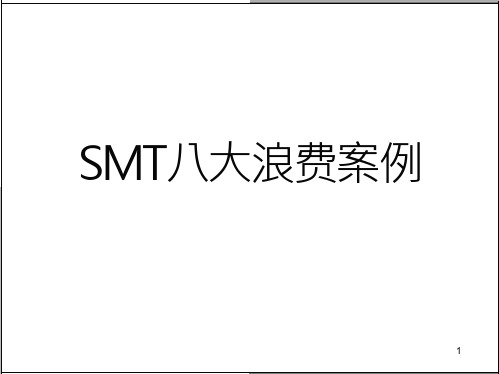
骤及内容 使用电子广告牌 进 行质量监控, 发生 不良立即整 改
改善绩效
通过标准作业指导书及 电子广告牌的推广,该机 种平 均良率由95.79%提 升至 99.31%.
6
1.2 U4空焊不良修正浪费一 、改善前
U4空焊不良率
800 600 400 200
0
DPPM
目标 160
上水位 传感器
下水位 传感器
上下水位 报警装置
改善前
防呆报 警系统
空间利用率 货架空间利用率低 上部空间利用率低
总体空间利用率低
布局物流杂亂 仓库布局为经验布局 物流线路不合理局部物
流量大
1.重新Layout后对各货架实行店面管理及分類管理 保证先进先出,及时來料及时交付生产,降低库存.
2.设置防呆的报警系统,货架上下水位报警,使仓库 人员及时对其进行仓储管控
用200元/m2*1428m2=284800元 2.节约物料架 成本:2500元/个*10个=25000元
五金 仓
待验 区
不良 品仓
改善后充分提 高货架空间利 用率及上部空 间.同时导入看
板管理
被动 仓
办公 区
PCB 仓
新机 种仓
主贵 仓
下料电梯
35
5.2 SMT与PTH半成品库存改善
现狀描述 1.图示为SMT
等待 (流
NA
?
测试存在极大的 检验过剩浪费, 依 据 ECRS,取 消 不必要测试画 面
﹒ 根据测试工程师提供 光的不良
BMA TEST 主要检测 B/L 異物亮点及漏
﹒ 黑画面主要检测: 亮点,画面均匀度,线缺陷,白点,麻点, 静电 白线
八大浪费演示文稿(汽车行业)
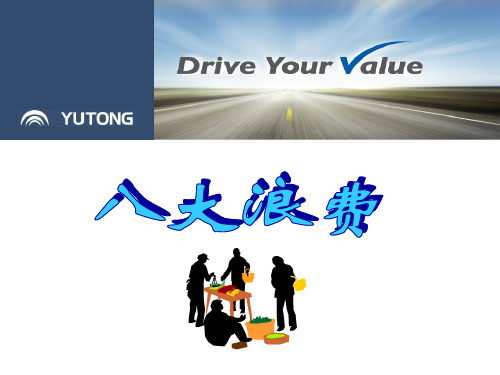
15
3.搬运的浪费
不必要的移动及把东西暂放在一旁
不必要的搬运、工作的移动、预置、改装以及长距离的搬 运流程和活性度差等
表现形式:
•搬运距离很远的地方,小批量的运输 •主副线中的搬运 •出入库次数多的搬运
长距离搬运在制品,
缺乏效率的运输,进 出仓库或在流程之间
搬运原料、零部件或
最终成品。
•破损、刮痕的发生
过多的库存会隐藏的问题点:
•没有管理的紧张感,阻碍改 善的活性化
•设备能力及人员需求的误判 •对场地需求的判断错误 •产品品质变差的可能性 •容易出现呆滞物料
对策:
5.库存的浪费
•库存意识的改革 •U型设备配置
•均衡化生产
•生产流程调整顺畅 •看板管理的贯彻 •快速换线换模 •生产计划安排考虑库存 消化
34
•因不良造成人员及工程增多的浪费
•材料费增加
对策:
7. 不良品的浪费
•自动化、标准作业 •防误装置
•在工程内做出品质保证
原因:
•标准作业欠缺 •过分要求品质 •人员技能欠缺 •品质控制点设定错误 •认为可整修而做出不良 •检查方法、基准等不完备 •设备、模夹治具造成的不良
“三不政策” •一个流的生产方式 •品保制度的确立及运行 •定期的设备、模治具保养 •持续开展“5S活动”
22
4.加工的浪费
因技术(设计、加工)不足造成加工上的浪费
原本不必要的工程或作业被当成必要
表现形式:
•在加工时超过必要以上的距离所造成的浪费
•冲床作业上重复的试模,不必要的动作
•成型后去毛头,加工的浪费 •钻孔后的倒角,纹孔作业的浪费
•最终工序的修正动作
采取不必要的步 骤,以处理零部件; 因为工具与设计不良 ,导致产生不必要的 动作及产生不必要的 瑕疵而造成缺乏效率 的处理;当提供超出 必要的较高品质产品 时,也会造成浪费。
精益生产管理八大浪费与解决方法(详细版)4.doc

精益生产管理八大浪费与解决方法(详细版)4大纲:(一)制造过早(多)的浪费(二)库存的浪费(三)不良修正的浪费(四)加工过剩的浪费(五)搬运的浪费(六)动作的浪费(七)等待的浪费(八)管理的浪费八大浪费是丰田生产方式中非常重要的一个观念。
丰田人认为要消除浪费,持续改善,企业才能保持良性运转,竞争力才会提升。
在丰田改善是探入人心的,有个说法就是跟他们谈话5分钟没有听到他们讲3次改善就不算丰田人。
改善的对象是浪费,认识浪费是改善的第一步,企业现场林林总总,哪些是有价值的,哪些是浪费,不是一般人可以一目了然的。
丰田人在长期作业和改善过程中对于浪费的内容进行了总结,共七种,被称为七种浪费。
它们分别是制造过早(多)的浪费、库存的浪费、不良修正的浪费、加工过剩的浪费、搬运的浪费、动作的浪费、等待的浪费共七种。
后来人们又加了一种浪费-管理的浪费,合称八种浪费。
下面我们从实用性角度剖析这八种浪费。
(一)制造过早(多)的浪费定义:所谓制造过早(多)就是前制程制造太早/过多,大于客户(或后制程)当期的最小需要量。
制造过早(多)浪费是八大浪费中的首恶,在精益生产中则被视为最大的浪费。
福特式思维告诉大家,在同样的时间内,生产量越多,效率越高,成本越低,企业越赚钱,所以企业自然有大批量连续生产的初始动力。
作为一个整体的企业是如此,那么企业内各部门也是如此,特别是在一些制程较短,关联性较低的企业中,普遍实施计件工资,那么从最基础的员工开始就有多做、早做,甚至偷做的动力,在这种情况下,告知企业里所有人早(多)做是罪恶当然得不到掌声回应。
那么我们就来看看制造过早(多)的浪费。
制造过早(多)浪费的后果主要有三大类。
1.直接财务问题。
表现为库存、在制品增加,资金回转率低,制造时间变长,占用资金及利息,会造成库存空间的浪费,在现金流量表上很明显。
2.产生次生问题。
会产生搬运、堆积的浪费;先进先出的工作产生困难;产品积压造成不良发生,物流阻塞制程时间变长,现场工作空间变小,有滞留在库的风险,有不良品的风险。
八大浪费及案例(50页)
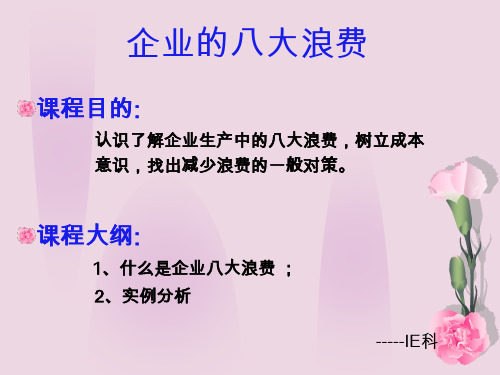
库存的浪费
库存浪费的类型或现象:
成品的库存 零部件、材料的库存
成品库存实例
??
是车间 还是仓 库?
成品库存过多挡住通道
成品库存造成的浪费
成品库存过多不代表资产,没有任何价值 , 只会造成浪费从而增加成本!
成本库存造成的浪费: a.占用保管场所及踏板的浪费; b.造成人员搬运及管理的浪费; c.产品时间长易损坏 d.增加无效成本,造成资金不能灵活流通; e.过剩的在库掩盖了问题的存在
机种切换浪费
虽然转机次数不能减少, 但是每项转机工作的时 间可以缩短,尽可能减到 最短,甚至减到“0”.
改善对策
1. 机种切换浪费
减少机种切换浪费的对策
外部转机的彻底
事前能准备的材料, 治具提前做好准备,交换 出来的材料与治具在机器开始生产后进行整 理.
内部转机的彻底
机器不停下来就没法转机的工作要集中所有 人力, 物力, 用最好的方法进行.
2、通过改善作业位置来消除搬运作业; 3、缩短工位(设备・工程)之间的距离来减少搬运浪费; 3、通过辅助治具来替代人员的搬运作业;
(例如NLP产线MI手插与TUP之间运输夹具的滑轨的使用)
缩短搬运距离
PCB放在线前面
PCB放在机器旁有滑轨的架子上
2.5m
1.2m
用专用架子, 靠近作业区域最近化, 缩短搬运 距离, 节约空间4.6 m2;
管理或人力资源的浪费
所有的事后管理与补救管理浪费 (比如返工;) 对策:在生产过程中就控制好品质;
减少人力资源的浪费 (多能工的培训推广)
理想生产线的构建
1)一个流彻底实施 *移动距离的缩短 *作业标准化 *空间的合理利用 *产量的提升 *不良品的减少
八大浪费及改善技法

1. 管理板 2. 控制投入 3. 过剩生产
24
24
把握状态
消除浪费的步骤
分析原因
寻找消除方法 立即实践
制作小工具 决定维持管理方法
过剩生产
• 按节拍时间,制定标准作业 • 用看板控制序安排方法,重新安排作业
•人员过剩 •设备稼动过剩 •生产浪费大 •业务订单预测有误 •生产计划与统计错误
对策:
•顾客为中心的弹性生产系统
•单件流动—一个流生产线
•看板管理的贯彻 •快速换线换模 •少人化的作业方式 •均衡化生产
注意:
•生产速度快并不代表效率高 •设备余力并非一定是埋没成本 •生产能力过剩时,应尽量先考虑减
对策:
•自动化、标准作业
•防错装置
•在工程内做出品质保证
“三不政策”
•一个流的生产方式
•品保制度的确立及运行
•定期的设备、模夹具保养
•持注续意:开展“5S活动”
•能回收重做的不良
•能修理的不良
•误判的不良
10
➢多余动作浪费
❖是指员工的任何一个对生产流程来说不必要的动作 ❖在一个布局不合理的工位或没有遵循标准化操作的员工,过度
•
•
•
解决方案
• • • •
• • • •
• • • •
•
•
•
•
27
找出浪费因素表(2/2)
我工厂的现状
观察事例
库存
•
•
•
•
•
•
•
•
动作
•
•
•
•
•
•
•
•
《现场八大浪费》课件
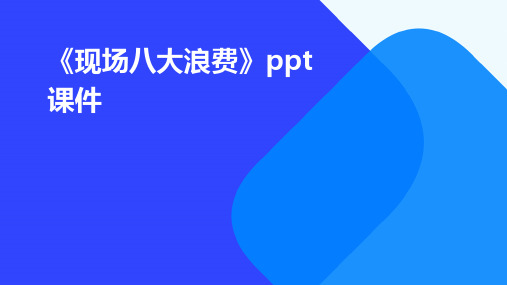
03
消除浪费
04
针对每一种浪费,我们提供了具 体的消除方法。例如,对于过量 生产浪费,我们可以通过调整生 产计划,实现按需生产;对于不 良品浪费,加强品质控制和预防 措施,减少不良品的产生。
实际操作
在ppt课件中,我们通过实际操 作演示了如何消除浪费。参与者 可以在实际操作中学习到实用的 方法和技巧,以便在工作中应用 。
详细描述
搬运浪费往往是由于生产布局不合理、生产线配置不当等原因造成的。这种浪费 不仅增加了物流成本和时间成本,还可能导致物品损坏、效率降低等问题。
动作浪费
总结词
动作浪费是指生产过程中操作人员的不必要动作或低效动作 ,如过多的步行、弯腰、伸手等。
详细描述
动作浪费通常是由于工作台设计不合理、工具摆放不当等原 因造成的。这种浪费不仅增加了操作人员的劳动强度,还影 响了工作效率,增加了疲劳和工伤的风险。
库存浪费
总结词
库存浪费是指过多的原材料、在制品、成品等库存积压,导致资金占用、管理成本增加和资源浪费。
详细描述
库存浪费通常是由于预测不准确、生产计划不合理、供应链协同不力等原因造成的。这种浪费不仅占 用了企业的流动资金,还可能掩盖了生产过程中的问题,使企业失去改进和优化的机会。
制造不良浪费
总结词
THANKS FOR WATCHING
感谢您的观看
产生原因
生产流程设计不合理
生产流程中存在过多的加工、 搬运和等待环节,导致资源利
用效率低下。
生产计划安排不当
生产计划不准确或不合理,导 致生产过程中出现过多的等待 和库存。
员工技能水平不足
员工技能水平不足或操作不熟 练,导致生产过程中出现过多 的不良品和加工浪费。
精益生产管理八大浪费与解决方法(详细版)
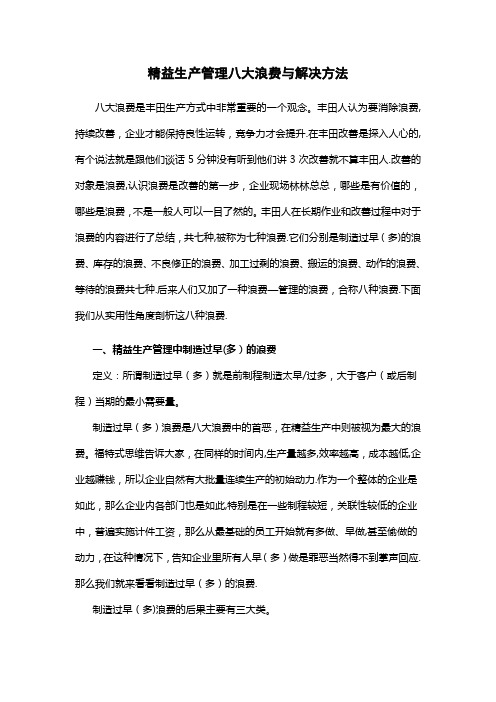
精益生产管理八大浪费与解决方法八大浪费是丰田生产方式中非常重要的一个观念。
丰田人认为要消除浪费,持续改善,企业才能保持良性运转,竞争力才会提升.在丰田改善是探入人心的,有个说法就是跟他们谈话5分钟没有听到他们讲3次改善就不算丰田人.改善的对象是浪费,认识浪费是改善的第一步,企业现场林林总总,哪些是有价值的,哪些是浪费,不是一般人可以一目了然的。
丰田人在长期作业和改善过程中对于浪费的内容进行了总结,共七种,被称为七种浪费.它们分别是制造过早(多)的浪费、库存的浪费、不良修正的浪费、加工过剩的浪费、搬运的浪费、动作的浪费、等待的浪费共七种.后来人们又加了一种浪费—管理的浪费,合称八种浪费.下面我们从实用性角度剖析这八种浪费.一、精益生产管理中制造过早(多)的浪费定义:所谓制造过早(多)就是前制程制造太早/过多,大于客户(或后制程)当期的最小需要量。
制造过早(多)浪费是八大浪费中的首恶,在精益生产中则被视为最大的浪费。
福特式思维告诉大家,在同样的时间内,生产量越多,效率越高,成本越低,企业越赚钱,所以企业自然有大批量连续生产的初始动力.作为一个整体的企业是如此,那么企业内各部门也是如此,特别是在一些制程较短,关联性较低的企业中,普遍实施计件工资,那么从最基础的员工开始就有多做、早做,甚至偷做的动力,在这种情况下,告知企业里所有人早(多)做是罪恶当然得不到掌声回应.那么我们就来看看制造过早(多)的浪费.制造过早(多)浪费的后果主要有三大类。
1.直接财务问题。
表现为库存、在制品增加,资金回转率低,制造时间变长,占用资金及利息,会造成库存空间的浪费,在现金流量表上很明显。
2。
产生次生问题。
会产生搬运、堆积的浪费;先进先出的工作产生困难;产品积压造成不良发生,物流阻塞制程时间变长,现场工作空间变小,有滞留在库的风险,有不良品的风险。
3。
掩盖问题.为什么“制造过早(多)浪费是八大浪费中的首恶,在精益生产中则被视为最大的浪费”?因为它带给人们一个安心的错觉,掩盖了各种问题,以及隐藏了由于等待所带来的浪费,没有改善的动力,失去了持续改善的时机。