水泥粉磨技术及应用
水泥粉磨技术及应用

立磨 不须 另外 设置选 粉分 级系统 ,而 辊压 机则 必须 单独设 置 ,系统 比 立磨 复杂 。 2 . 改造现有 磨机 内部结构
水泥粉磨 通常采 用单风机直 通式 闭路 ,粗 粉返 回磨机 内继续 粉磨 , 直至选 粉达 到合格 细 度 。与开路 相 比 ,最 大的特 点是 可 以减少 过粉磨 现 象 ,通 过选 粉机 调 节成 品细 度 ,有利 于提 高产 品细度 和 生产 效 率 , 细度筛余 通常都 可控制在 3 %以下 。闭路系统 两个重点 指标是 选粉机 的 选 粉效 率和循 环 负荷 。选粉机 成品细 度不变 时 ,循环 负荷 随喂 入 的物 料 粒度 变粗 而增 加 ,随选 出的粗 粉粒 度变 细而 降低 。提高 出磨 细度 和 选 粉效 率是 闭路 系统 高效 率生产 的关键 。实际生 产 中 ,调 整研 磨体级 配等 方案 来 降低 出磨 细度 筛余 ,能 够起 到 优化 闭路 系统 的工 艺参 数 , 提高生产 能力 的作用 。 3 . 高细高产 磨粉磨 工艺 针 对普 通球磨 机粉 磨效 率低 而发 展的 一种新 型粉 磨技 术 , 目前 相 当广 泛 ,如 筛分 磨 、小段 磨 、高细磨 以及 高细 筛分 磨等 ,结 构形式 总 体相 同 ,都属 于这一 范畴 。高 细高 产磨 可 以应 用 于很 多形式 ,是 由普 通磨机 内部结构 改造 而成 ,由于磨机 直径 以及 长径 比不 改变 ,工 艺及 系统 配置 也 不 会 改 变 。 因 此 ,球 磨 机 使 用 的工 艺流程 ,对 高细 高产 磨都可 适用 。国内 以开 路磨 为 主 ,即在 原有 开 路系统 基础 上 ,通 过磨 机 改造 来 实现 开路 高细 高产 粉 磨 ,原为 闭路 系统 的 ,也按 此改 为闭路
粉磨工艺

第五章粉磨工艺第一节粉磨的目的和要求粉磨是将颗粒状物料通过机械力的作用变成细粉的过程。
对于生料和水泥粉磨过程来说,也是几种原料细粉均匀混合的过程。
粉磨的目的是使物料表面积增大,促使化学反应的迅速完成.粉磨产品细度常用筛余量和比表面积来表示。
一•生料粉磨的目的和要求生料的细度直接影响窑内锻烧时熟料的形成速度。
生料细度越细,则生料各组分间越能混合均匀,窑内锻烧时生料各组分越能充分接触,使碳酸钙分解反应、固相反应和固液相反应的速度加快,有利于游离氧化钙的吸收;但当生料细度过细时,粉磨单位产品的电耗将显著增加,磨机产量迅速降低,而对熟料中游离氧化钙的吸收并不显著。
生料中的粗颗粒,特别是一些粗大的石英(结晶Si0 :)和方解石晶体的反应能力低,且不能与其他氧化物组分充分接触,这就造成锻烧反应不完全,使熟料,f-Ca 0 增多,严重影响熟料质量,所以必须严格加以控制,而颗粒较均匀的生料,能使熟料锻烧反应完全,并加速熟料的形成,故有利于提高窑的产量和熟料的质量。
因此,生料的粉磨细度,用管磨机生产时通常控制在0. 08mm 方孔筛筛余10 %左右,0.2m m 方孔筛筛余小于 1. 5 %为宜。
闭路粉磨时,因其粗粒较少,产品颗粒较均匀,因而可适当放宽0. 08mm 筛筛余,但仍应控制。
.2mm 筛筛余,对于原料中含石英质原料和粗质石灰岩时,生料细度应细些,特别要注意0. 2mm 筛筛余量。
二•水泥粉磨的目的及要求水泥的细度越细,水化与硬化反应就越快,水化愈易完全,水泥胶凝性质的有效利用率就越高,水泥的强度,尤其是早期强度也愈高,而且还能改善水泥的泌水性、和易性等。
反之,水泥中有过粗的顺粒存在,粗颗粒只能在表面反应,从而损失了熟料的活性。
一般试验条件下,水泥颗粒大小与水化的关系是:0--l0μm ,水化最快,3--30μm ,是水泥主要的活性组分;.>60μm ,水化缓慢;>90μm ,表面水化,只起集料作用。
水泥比表面积与水泥有效利用率(一年龄期)的关系是:,水化最快,300M 2 /kg 时,只有44 %可水化发挥作用;700 M 2 /kg 时,有效利用率可达80 %左右;1000 M 2 /kg 时,有效利用率可达90 %-95 %。
水泥粉磨节能降耗的技术措施

水泥粉磨节能降耗的技术措施摘要:文章首先对水泥粉磨节能降耗技术的现状进行了阐述,接着对不同粉磨技术及设备能耗比较进行了分析,最后讨论了水泥粉磨节能降耗的技术措施。
关键词:水泥粉磨;节能降耗;技术措施一、前言为了节能降耗,水泥生产企业均采取新型干法窑、节能磨机系统、低温余热发电的建设。
水泥(熟料)的粒度控制在节能、降耗及增加混合材掺量等方面作用显著,个别企业对此有较深认识并采取一定措施。
水在通过改善水泥的粒度,来充分发挥熟料的性能,对整个水泥行业节能降耗的作用是非常巨大的。
二、水泥粉磨节能降耗技术的现状我国目前中小型水泥厂的生料制备和水泥粉磨设备一般采用球磨机一级圈流工艺,球磨机的规格多是Ф2.2~3.2m×6.5~13.0m的2仓磨,选粉机多为传统的离心式或旋风式选粉机,普遍存在生产能力低、能耗高、产品质量不尽如人意,特别是实行ISO水泥检验标准后,问题更为突出。
使用新型干法熟料后,问题就转移到粉磨的系统工艺、主机设备及其内部结构等方面。
主要表现在:①物料(熟料)入磨粒度大、磨机长径比小、仓数少、研磨体(钢段)规格偏大、表面积小和耐磨性差,导致物料在磨内研磨时间短,水泥成品比表面积小(一般不超过300m2/kg)。
②磨机内部结构不合理,单层隔仓板对物料没有筛分作用,水泥颗粒分布范围宽,粉磨效率降低。
③选粉机选粉效率低,不能及时将3~32μm的微粉选出。
虽然80μm筛余<4%,但产生的3~32μm颗粒(特别是熟料、矿渣等易磨性差的物料)少,比表面积小。
同时从众多的水泥厂经了解,存在着降低产品内在质量、袋重严重不足,浪费资源等现象。
没有从内部挖潜,使用新技术、新设备、新工艺,从加强内部管理等方面进行工作。
诸如这种降低成本的做法是极不正确的,损害了消费者的利益,危害着工程质量,严重违背职业道德。
三、不同粉磨技术及设备能耗比较水泥粉磨是把电能转换成机械能,再把机械能转换成物料的表面能的过程。
水泥助磨剂技术的应用现状及发展
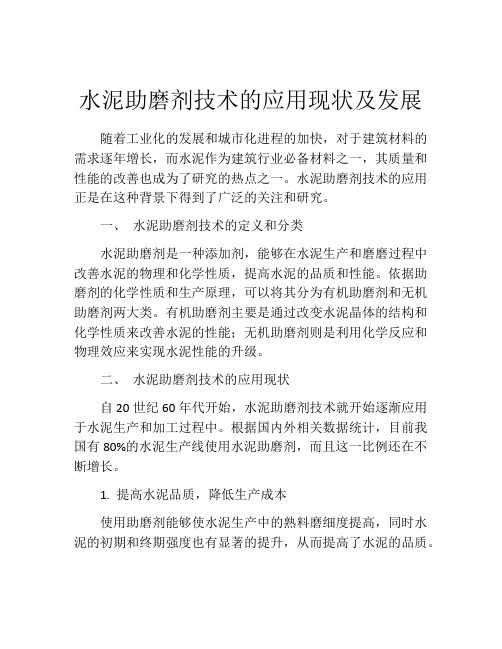
水泥助磨剂技术的应用现状及发展随着工业化的发展和城市化进程的加快,对于建筑材料的需求逐年增长,而水泥作为建筑行业必备材料之一,其质量和性能的改善也成为了研究的热点之一。
水泥助磨剂技术的应用正是在这种背景下得到了广泛的关注和研究。
一、水泥助磨剂技术的定义和分类水泥助磨剂是一种添加剂,能够在水泥生产和磨磨过程中改善水泥的物理和化学性质,提高水泥的品质和性能。
依据助磨剂的化学性质和生产原理,可以将其分为有机助磨剂和无机助磨剂两大类。
有机助磨剂主要是通过改变水泥晶体的结构和化学性质来改善水泥的性能;无机助磨剂则是利用化学反应和物理效应来实现水泥性能的升级。
二、水泥助磨剂技术的应用现状自20世纪60年代开始,水泥助磨剂技术就开始逐渐应用于水泥生产和加工过程中。
根据国内外相关数据统计,目前我国有80%的水泥生产线使用水泥助磨剂,而且这一比例还在不断增长。
1. 提高水泥品质,降低生产成本使用助磨剂能够使水泥生产中的熟料磨细度提高,同时水泥的初期和终期强度也有显著的提升,从而提高了水泥的品质。
另外,加入助磨剂能够使水泥熟料的生产温度下降,减少了能耗和生产成本。
2. 提高生产效率使用助磨剂的水泥生产线,生产效率相对于没有使用的水泥生产线也有所提高,因为助磨剂能够使水泥磨机运行更加稳定,同时也减少了机器的维修和更换的频率。
3. 减轻环境污染传统的水泥生产过程中,噪音、粉尘和废气是不可避免的环境污染问题。
而使用助磨剂可以减少水泥生产中的粉尘和废气排放,同时减少机器的振动和噪音污染。
三、水泥助磨剂技术的发展趋势虽然已经取得了一定的发展与成就,但是水泥助磨剂技术的应用仍面临着不少挑战和发展空间。
未来的发展趋势主要有以下几个方面:1. 绿色环保当前社会对环境保护的要求越来越高,很多企业都在致力于实现绿色生产。
水泥助磨剂技术的发展也应当朝着这个方向推进,选择无污染无危险的助磨剂,以达到绿色环保的目标。
2. 降低成本虽然水泥助磨剂能够提高水泥品质,但这也不应该成为提高产品价格的理由。
水泥粉磨工艺技术

水泥粉磨工艺技术破碎与粉磨统称为粉碎。
行业内习惯将大块物料加工变为小块物料的过程称之为破碎;将粗颗粒物料变为细粉的过程称之为粉磨。
水泥生产过程中的粉磨工艺分为:生料制备工艺和水泥制成工艺两大部分,简称为生料粉磨和水泥粉磨。
石灰石、粘土、铁粉等配合磨细称为生料;熟料、石膏、混合材料配合磨细称为水泥。
一、水泥生产物料粉碎的目的(1)物料经过粉碎后,单位质量的物料表面积(比表面)增加,因而可以提高物理作用的效果及化学反应的速度;(2)几种不同物料在粉体状态下,容易达到混合均匀的效果。
(3)粉状物料也为烘干、运输和储存等提供了方便,并为煅烧熟料和制成水泥,保证出厂水泥的合格率创造了条件。
二、合理控制生料细度当粉磨细度在0.08mm方孔筛筛余10%以下时,随着筛余量的减少,粉磨单位产品的电耗将显著增加,产量也相应降低;因此,生料粉磨细度,通常控制在0.08mm方孔筛筛余10%左右,0.20mm方孔筛筛余小于1.0%为宜。
用大型球磨生产时,由于产品粒度较均匀,粗大颗粒较少。
在易烧性允许的前提下,0.08mm 方孔筛余可放宽至12~16%,但应控0.20mm方孔筛筛小于1.5%。
三、研磨体及其级配物料在粉磨过程中,一方面需要冲击作用,另一方面需要研磨作用。
不同规格的研磨体配合使用,还可以减少相互之间的空隙率,使其与物料的接触机会多,有利于提高能量利用率;在研磨体装载量一定的情况下,小钢球比大钢球的总表面积大;要将大块物料击碎,就必须钢球具有较大的能量,因此,钢球(段)的尺寸应该较大;需要将物料磨得细一些,就应选择小些的钢球(段)。
因此在粉磨作业时,要正确选择研磨体且必须进行合理的级配。
四、研磨体级配基本原则(1)入磨物料的平均粒径大,硬度高,或要求产品粗时,钢球的平均径应大些,反之应小些。
磨机直径小,钢球平均球径也应小。
一般生料磨比水泥磨的钢球平均球径大些。
(2)开路磨机,前一仓用钢球,后一仓用钢段。
(3)研磨体大小必须按一定比例配合使用。
现代水泥工业中高效节能的粉磨技术

●
Z H A O J i h ui , W A N G D o n g mi n , WA N G X ue g u a n g
( S c h o o l o f C h e m i c a 1 a n d E n v i r o n m e n t a 1 E n g i n e e r i n g ,C h i n a U n i v e r s i t y
水泥粉磨工艺技术特点与工艺改进措施分析

建材发展导向2018年第06期1121 水泥粉磨工艺技术特点1.1 开流粉磨工艺技术特点开流粉磨技术优点在于流程简单、操作便捷、使用设备较少、成本低、设备维护简单。
不过该种技术效率和产量不高,如若对产品粒度要求较严格时,被磨细的物料会在磨内形成冲层,进而形成粉磨,且还有部分数量颗粒会夹杂到成品当中,甚至还会出现粘结、包球等现象。
1.2 圈流粉磨工艺技术特点该种技术常常使用的是长管磨作为磨机,所以导致在磨内物料出现长时间停留,使得过粉磨大幅减少,从而达到提高了磨机的产量,具有效率高、能耗低、循环负荷小的特点。
而且可以采取不同级别的选粉技术来把控成品粒度,实际磨出物料较细。
不过该种技术流程较为复杂、操作难度较大,需要投入大量资金。
1.3 混合粉磨工艺技术特点混合粉末技术能够有效助磨熟料的粉磨,减少熟磨使用数量,降低能源消耗。
并且该项技术可以有效降低煅烧生料中石灰石所产生的二氧化碳,降低对环境的污染。
2 水泥粉磨工艺改进措施2.1 粉磨研磨体工艺改进措施用于水泥粉磨加工的原材料要求能够把小块物料变为颗粒,所以要用到巨大冲力把大块物料打碎,并且还要选用相应设备来控制物料大小间的空隙,尽可能将原材料和粉磨机接触面积加大,以便于能够将水泥粉磨效率提升。
要想改进粉磨研磨体工艺可从如下几方面着手:第一,在确保粉磨细度条件得到满足的基础上,合理加大物料接触面或增加设备循环次数,将研磨设备直径减小,以便于提升设备工作效率。
第二,如若要采取等级不同的两种等级钢锻,则应当选用平均组合钢锻。
如若是采取三段钢锻,就应当要结合具体情况来组合。
第三,磨设备如果是相邻的两个仓都是钢球,就需要确保后面最大,前面最小的原则,并根据特定比例来选用2-3级或3-5级钢锻,进而确定最佳研磨设备。
第四,如若所采用原材料硬度较大、颗粒较大,出料细度要求不高的情况下,可以选用较大直径的研磨设备,反之就选用直径较小的设备,即结合具体研磨要求来选择相应直径设备。
陶瓷球在水泥粉磨系统中的应用及调试

陶瓷球在水泥粉磨系统中的应用及调试1. 应用背景水泥粉磨系统是水泥生产线中的关键部分,对于水泥的细磨及质量稳定具有重要作用。
传统的水泥粉磨系统中常使用钢球作为磨砂介质,但钢球存在磨损大、占据空间、易生锈等问题,因此人们开始寻求替代品来提高粉磨效率和降低生产成本。
陶瓷球因其具有优异的耐磨性、抗腐蚀性和对环境友好等特点,成为了水泥粉磨系统中的理想选择。
2. 应用过程陶瓷球的应用可以分为以下几个步骤:2.1 选择合适的陶瓷球类型根据具体的水泥粉磨系统要求以及生产线的工艺情况,选择合适的陶瓷球类型。
常见的陶瓷球材质包括氧化铝陶瓷球、氧化锆陶瓷球等,这些不同材质的陶瓷球在耐磨性和抗腐蚀性能上略有差异,需要根据具体情况进行选择。
2.2 调整球磨机参数根据所选的陶瓷球类型,进行球磨机参数的调整。
主要包括磨机转速、进料量、磨介质的补给量等。
由于陶瓷球相对于钢球具有较小的比重,因此可能需要适当增加进料量和磨介质的补给量,以保证磨机的正常运转和磨砂效果。
2.3 添加陶瓷球到磨机中将选择好的陶瓷球加入到球磨机中,并与原有的钢球混合使用。
由于陶瓷球的硬度较高,可以增加球磨机的磨砂效果,提高粉磨效率。
同时,由于陶瓷球的抗腐蚀性能好,可以减少磨机和水泥中的金属污染,提高水泥产品的质量。
2.4 调试球磨机参数在添加陶瓷球后,需要进行球磨机参数的再次调试。
主要包括磨机转速、进料量、磨介质的补给量等。
通过逐步增加转速和调整进料量,观察磨机的运行情况和水泥的磨砂效果,找到最佳的参数组合,以达到提高磨砂效率和降低生产成本的目标。
3. 应用效果通过在水泥粉磨系统中应用陶瓷球,可以获得以下几个方面的应用效果:3.1 提高粉磨效率陶瓷球具有较高的硬度和良好的耐磨性,可以增加球磨机对水泥的细磨效果,提高水泥的磨砂效率。
相对于传统的钢球,陶瓷球的使用能够大幅降低水泥粉磨系统的能耗,提高生产线的产能和经济效益。
3.2 降低生产成本陶瓷球相对于钢球来说,在生产成本方面具有一定的优势。
- 1、下载文档前请自行甄别文档内容的完整性,平台不提供额外的编辑、内容补充、找答案等附加服务。
- 2、"仅部分预览"的文档,不可在线预览部分如存在完整性等问题,可反馈申请退款(可完整预览的文档不适用该条件!)。
- 3、如文档侵犯您的权益,请联系客服反馈,我们会尽快为您处理(人工客服工作时间:9:00-18:30)。
水泥粉磨技术及应用
摘要:水泥粉磨技术随着技术发展,已经越来越成熟。
本文介绍了相关粉末工艺的分类,提出了当今粉末工艺与设备存在的问题,并针对问题提出了相关解决办法,具有一定借鉴价值。
关键词:水泥粉末工艺设备节能
一、水泥粉磨工艺研究分类
1.开路粉磨,最普通的工艺形式
最大特点为产品细度一次粉磨完成,系统辅助设备少,流程简单,操作方便。
细度影响粉磨效率较大,一些情况下细粉容易凝聚,产生粘球及过粉磨等现象,粉磨效率也因此降低。
就物料而言,影响开路磨产量和细度的原因,一是入料粒度,物料从入磨到出磨变为成品有限粉磨时段内,产量与细度的矛盾就愈突出;二是物料的易磨性,当配料中诸如矿渣、钢渣等难磨物料的掺入量愈大,产量与细度的矛盾也愈突出。
若多种因素同时存在,对产量和细度的影响就更为加剧。
在这种情况下,开路工艺的劣势便突显出来,根据生产需要,进行设备结构改造或工艺更新来满足水泥的粉磨要求。
2.闭路粉磨
水泥粉磨通常采用单风机直通式闭路,粗粉返回磨机内继续粉磨,直至选粉达到合格细度。
与开路相比,最大的特点是可以减少过粉磨现象,通过选粉机调节成品细度,有利于提高产品细度和生产效率,细度筛余通常都可控制在3%以下。
闭路系统两个重点指标是选粉机的选粉效率和循环负荷。
选粉机成品细度不变时,循环负
荷随喂入的物料粒度变粗而增加,随选出的粗粉粒度变细而降低。
提高出磨细度和选粉效率是闭路系统高效率生产的关键。
实际生产中,调整研磨体级配等方案来降低出磨细度筛余,能够起到优化闭路系统的工艺参数,提高生产能力的作用。
3.高细高产磨粉磨工艺
针对普通球磨机粉磨效率低而发展的一种新型粉磨技术,目前相当广泛,如筛分磨、小段磨、高细磨以及高细筛分磨等,结构形式总体相同,都属于这一范畴。
高细高产磨可以应用于很多形式,是由普通磨机内部结构改造而成,由于磨机直径以及长径比不改变,工艺及系统配置也不会改变。
因此,球磨机使用的工艺流程,对高细高产磨都可适用。
国内以开路磨为主,即在原有开路系统基础上,通过磨机改造来实现开路高细高产粉磨,原为闭路系统的,也按此改为闭路生产。
4.挤压粉磨
20世纪80年代中期辊压机问世,标志着粉磨技术的重大进步。
10多年来,我国辊压机装备和工艺技术发展非常迅速。
挤压粉磨工艺有早期的预粉磨发展到目前的联合粉磨、半终粉磨以及终粉磨系统。
挤压粉磨工艺分混合粉磨系统、联合粉磨系统、挤压预粉磨系统、半终粉磨系统以及终粉磨系统。
二、水泥粉磨技术存在问题
我国经济建设快速发展,水泥生产逐渐以新型干法替代过去的普通回转窑和机械化立窑。
生产规模大,熟料强度高、质量均匀稳定。
一些机械化立窑水泥厂改为水泥粉磨站,但由于这些厂的粉磨设备和系统工艺均存在缺陷,必须进行必要的技术改造。
1.磨机小、产量低、能耗高
我国水泥粉磨有相当数量以直径在3m以下的中小型球磨机,有相当一部分的水泥企业水泥磨实际平均台时产量低于相应磨机设
计产量,与磨机规格较大的水泥企业比,电耗明显偏高。
落后粉磨工艺对电能的有效利用率还低,绝大部分电能没有被利用。
同时不少企业磨机台时产量受原材料、气候等变化的影响,波动较大。
2.细度粗、波动大、强度低
对于出厂水泥,一般企业都能达到国标要求。
但实际运作中,不少企业虽出厂水泥达到了细度要求,但出磨水泥细度波动相当大,除少数生产条件好的企业外,大多数水泥磨出磨水泥质量波动大,不稳定。
另一方面,我国现时水泥仍存在着颗粒偏粗的现象,导致各种物料不能发挥自己最大的物理作用,造成原材料浪费和水泥标号低下,生产成本偏高。
三、设备改善及节能降耗措施
1.发展立磨粉磨系统
就目前水泥粉磨工艺流程而言,有以下几种:立磨粉磨系统、筒辊磨粉磨系统、管磨机粉磨系统及辊压机终粉磨系统等。
粉磨过程电耗要占水泥总电耗的70%以上,粉磨工艺的选择与应用直接影响水泥的质量产量及生产成本,占有举足轻重的地位。
管磨机低效率、管磨机易磨性差,高电耗的矛盾更为突出。
立磨系统产量高、电耗
低,被广泛应用于生料制备。
立磨粉磨机理与辊压机有相似之处,均为料床粉碎。
不同的是,立磨磨辊对物料的接触方式是柱面与平面。
此外,立磨不须另外设置选粉分级系统,而辊压机则必须单独设置,系统比立磨复杂。
2.改造现有磨机内部结构
隔仓板、球配、衬板等磨机自身结构改造是提高磨机效率的重要途径。
目前我国立窑和小型回转窑企业使用磨机大多是ф3.0以下磨机,内部结构不合理,技术落后,粉磨效率低。
这类磨机通过改造还是可以提高其产量的。
3.开流磨的技术改造
第一,国外公司推出的衬板有逐渐统一的趋势。
一仓采用提升衬板即所谓的阶梯衬板,二仓采用分级衬板。
这种分级衬板不是国内常见的锥形分级衬板或平衬板加锥形分级衬板,而是2种甚至3种衬板的组合或复合体。
经过优化组合或复合,一种衬板可发挥不同形式衬板的优势,从而保证了最大限度地将能量输入装球区,并尽量消除磨内死区。
第二,隔仓板对于隔仓装置的改进,除了要关注于篦板的耐冲击耐磨及防堵等方面外,加大中心件通风面积对于加大整个隔仓装置通风面积的影响最大,也是最可行的方案。
因为无论加大篦板孔尺寸或增加开孔数量,都将对篦板强度及其对料球的控制作用产生较大影响。
第三,研磨体尺寸基于粉磨能力和喂料粒度,通用的是“两头小,中间大”的级配方案。
在目前进行技术改造时,采用微型研磨体以强化尾仓的研磨能力。
直径8~12 mm的
小段,单位质量的个数是普通钢段的20倍,总表面积是普通钢段的2.5倍。
研磨效率与研磨体的表面积的0.5~0.7次方成正比。
小段的应用起到了提高产量、增加产品比表面积、适当改善微粉颗粒组成的至关重要的作用。
第四,料段分离装置,对于微型研磨体,有必要设计一个让细粉顺利出磨,但微型研磨体不致跑出磨外的出料篦板装置。
4.科学应用水泥助磨剂
水泥助磨剂是一种添加剂,适量地加入到被粉磨的物料中,能通过它对颗粒表面的物理化学作用,发挥力学效能,得以提高物料的易碎性和分散性,从而提高粉磨细度和降低粉磨电耗。
作用机理,助磨剂是降低粉磨阻力和阻止微粒聚集,通过物理化学吸附于物料表面,颗粒间摩擦力和粘附力减少,表面的电负荷得到中和,使其在磨内的流动性趋好,从而改善磨内的工作环境,进行“粉体流变”。
粉磨过程是机械应力间断地作用于物料的过程,作用期间被磨物料原有的裂缝被延伸扩展,生成新的裂缝;间断期间,不饱合键的吸引力则使裂缝重新愈合,当2种作用力趋于平衡,粉磨细度的增进速率变小甚至下降。
四、结论
当今世界水泥粉磨技术已呈现多元化趋势,且粉磨设备也向大型化、低耗高效及自动化方向发展。
随着科学技术的不断进步,水泥粉磨机理逐渐向节能、高效方面发展,相关工艺技术也必将随之发展。
参考文献
[1]韩仲琦.现代水泥粉磨技术的发展[j].山西建材.2003,42(3)8-12.
[2]王英,何其昂.水泥粉磨技术与装备进步[j].建材发展导向,2003,5(1):52-55.。