钢的热处理工艺代号及标注示例
铸钢件常见热处理
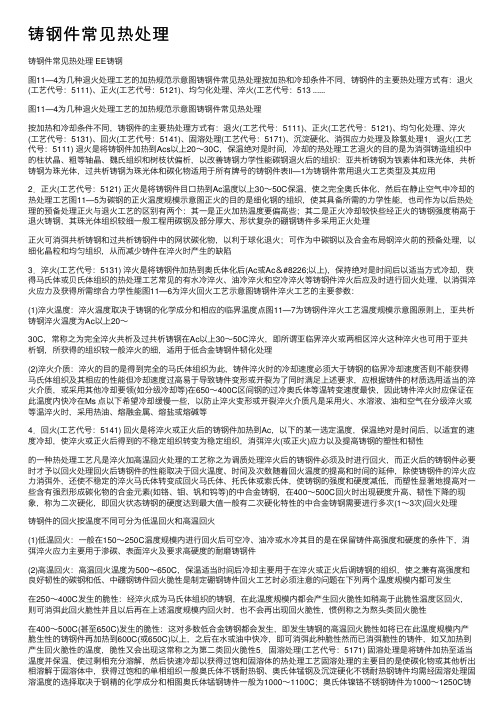
铸钢件常见热处理铸钢件常见热处理 EE铸钢图11—4为⼏种退⽕处理⼯艺的加热规范⽰意图铸钢件常见热处理按加热和冷却条件不同,铸钢件的主要热处理⽅式有:退⽕(⼯艺代号:5111)、正⽕(⼯艺代号:5121)、均匀化处理、淬⽕(⼯艺代号:513 ......图11—4为⼏种退⽕处理⼯艺的加热规范⽰意图铸钢件常见热处理按加热和冷却条件不同,铸钢件的主要热处理⽅式有:退⽕(⼯艺代号:5111)、正⽕(⼯艺代号:5121)、均匀化处理、淬⽕(⼯艺代号:5131)、回⽕(⼯艺代号:5141)、固溶处理(⼯艺代号:5171)、沉淀硬化、消弭应⼒处理及除氢处理1.退⽕(⼯艺代号:5111) 退⽕是将铸钢件加热到Acs以上20~30C,保温绝对是时间,冷却的热处理⼯艺退⽕的⽬的是为消弭铸造组织中的柱状晶、粗等轴晶、魏⽒组织和树枝状偏析,以改善铸钢⼒学性能碳钢退⽕后的组织:亚共析铸钢为铁素体和珠光体,共析铸钢为珠光体,过共析铸钢为珠光体和碳化物适⽤于所有牌号的铸钢件表ll—1为铸钢件常⽤退⽕⼯艺类型及其应⽤2.正⽕(⼯艺代号:5121) 正⽕是将铸钢件⽬⼝热到Ac温度以上30~50C保温,使之完全奥⽒体化,然后在静⽌空⽓中冷却的热处理⼯艺图11—5为碳钢的正⽕温度规模⽰意图正⽕的⽬的是细化钢的组织,使其具备所需的⼒学性能,也司作为以后热处理的预备处理正⽕与退⽕⼯艺的区别有两个:其⼀是正⽕加热温度要偏⾼些;其⼆是正⽕冷却较快些经正⽕的铸钢强度稍⾼于退⽕铸钢,其珠光体组织较细⼀般⼯程⽤碳钢及部分厚⼤、形状复杂的硼钢铸件多采⽤正⽕处理正⽕可消弭共析铸钢和过共析铸钢件中的⽹状碳化物,以利于球化退⽕;可作为中碳钢以及合⾦布局钢淬⽕前的预备处理,以细化晶粒和均匀组织,从⽽减少铸件在淬⽕时产⽣的缺陷3.淬⽕(⼯艺代号:5131) 淬⽕是将铸钢件加热到奥⽒体化后(Ac或Ac•以上),保持绝对是时间后以适当⽅式冷却,获得马⽒体或贝⽒体组织的热处理⼯艺常见的有⽔冷淬⽕、油冷淬⽕和空冷淬⽕等铸钢件淬⽕后应及时进⾏回⽕处理,以消弭淬⽕应⼒及获得所需综合⼒学性能图11—6为淬⽕回⽕⼯艺⽰意图铸钢件淬⽕⼯艺的主要参数:(1)淬⽕温度:淬⽕温度取决于铸钢的化学成分和相应的临界温度点图11—7为铸钢件淬⽕⼯艺温度规模⽰意图原则上,亚共析铸钢淬⽕温度为Ac以上20~30C,常称之为完全淬⽕共析及过共析铸钢在Ac以上30~50C淬⽕,即所谓亚临界淬⽕或两相区淬⽕这种淬⽕也可⽤于亚共析钢,所获得的组织较⼀般淬⽕的细,适⽤于低合⾦铸钢件韧化处理(2)淬⽕介质:淬⽕的⽬的是得到完全的马⽒体组织为此,铸件淬⽕时的冷却速度必须⼤于铸钢的临界冷却速度否则不能获得马⽒体组织及其相应的性能但冷却速度过⾼易于导致铸件变形或开裂为了同时满⾜上述要求,应根据铸件的材质选⽤适当的淬⽕介质,或采⽤其他冷却要领(如分级冷却等)在650~400C区间钢的过冷奥⽒体等温转变速度最快,因此铸件淬⽕时应保证在此温度内快冷在Ms 点以下希望冷却缓慢⼀些,以防⽌淬⽕变形或开裂淬⽕介质凡是采⽤⽕、⽔溶液、油和空⽓在分级淬⽕或等温淬⽕时,采⽤热油、熔融⾦属、熔盐或熔碱等4.回⽕(⼯艺代号:5141) 回⽕是将淬⽕或正⽕后的铸钢件加热到Ac,以下的某⼀选定温度,保温绝对是时间后,以适宜的速度冷却,使淬⽕或正⽕后得到的不稳定组织转变为稳定组织,消弭淬⽕(或正⽕)应⼒以及提⾼铸钢的塑性和韧性的⼀种热处理⼯艺凡是淬⽕加⾼温回⽕处理的⼯艺称之为调质处理淬⽕后的铸钢件必须及时进⾏回⽕,⽽正⽕后的铸钢件必要时才予以回⽕处理回⽕后铸钢件的性能取决于回⽕温度、时间及次数随着回⽕温度的提⾼和时间的延伸,除使铸钢件的淬⽕应⼒消弭外,还使不稳定的淬⽕马⽒体转变成回⽕马⽒体、托⽒体或索⽒体,使铸钢的强度和硬度减低,⽽塑性显著地提⾼对⼀些含有强烈形成碳化物的合⾦元素(如铬、钼、钒和钨等)的中合⾦铸钢,在400~500C回⽕时出现硬度升⾼、韧性下降的现象,称为⼆次硬化,即回⽕状态铸钢的硬度达到最⼤值⼀般有⼆次硬化特性的中合⾦铸钢需要进⾏多次(1~3次)回⽕处理铸钢件的回⽕按温度不同可分为低温回⽕和⾼温回⽕(1)低温回⽕:⼀般在150~250C温度规模内进⾏回⽕后可空冷、油冷或⽔冷其⽬的是在保留铸件⾼强度和硬度的条件下,消弭淬⽕应⼒主要⽤于渗碳、表⾯淬⽕及要求⾼硬度的耐磨铸钢件(2)⾼温回⽕:⾼温回⽕温度为500~650C,保温适当时间后冷却主要⽤于在淬⽕或正⽕后调铸钢的组织,使之兼有⾼强度和良好韧性的碳钢和低、中硼钢铸件回⽕脆性是制定硼钢铸件回⽕⼯艺时必须注意的问题在下列两个温度规模内都可发⽣在250~400C发⽣的脆性:经淬⽕成为马⽒体组织的铸钢,在此温度规模内都会产⽣回⽕脆性如稍⾼于此脆性温度区回⽕,则可消弭此回⽕脆性并且以后再在上述温度规模内回⽕时,也不会再出现回⽕脆性,惯例称之为熬头类回⽕脆性在400~500C(甚⾄650C)发⽣的脆性:这对多数低合⾦铸钢都会发⽣,即发⽣铸钢的⾼温回⽕脆性如将已在此温度规模内产脆⽣性的铸钢件再加热到600C(或650C)以上,之后在⽔或油中快冷,即可消弭此种脆性然⽽已消弭脆性的铸件,如⼜加热到产⽣回⽕脆性的温度,脆性⼜会出现这常称之为第⼆类回⽕脆性5.固溶处理(⼯艺代号:5171) 固溶处理是将铸件加热⾄适当温度并保温,使过剩相充分溶解,然后快速冷却以获得过饱和固溶体的热处理⼯艺固溶处理的主要⽬的是使碳化物或其他析出相溶解于固溶体中,获得过饱和的单相组织⼀般奥⽒体不锈耐热钢、奥⽒体锰钢及沉淀硬化不锈耐热钢铸件均需经固溶处理固溶温度的选择取决于钢精的化学成分和相图奥⽒体锰钢铸件⼀般为1000~1100C;奥⽒体镍铬不锈钢铸件为1000~1250C铸钢中含碳量越⾼,难熔合⾦元素越多,则其固溶温度应越⾼含铜的沉淀硬化铸钢,由于铸态有硬质富铜相在冷却过程中沉淀,致使铸钢件硬度升⾼为软化组织、改善加⼯性能,铸钢件需经固溶处理其固溶温度为900~950C经快冷后可得到铜的质量分数为1.0%~1.5%的过饱和单相组织6.沉淀硬化处理(时效处理) 铸件经固溶处理或淬⽕后,在室温或⾼于室温的适当温度保温,在过饱和固溶体中形成溶质原⼦偏聚区和(或)析出弥散漫衍的强化相⽽使⾦属硬化的处理称为沉淀硬化处理(或时效处理)在⾼于室温下进⾏的称为⼈⼯时效其实质是:在较⾼的温度下,⾃过饱和固溶体中析出碳化物、氮化物、⾦属间化合物及其他不稳定的中间相,并弥散漫衍于基体中,故⽽使铸钢的综合⼒学性能和硬度提⾼时效处理的温度直接影响铸钢件的最终性能时效温度过低,沉淀硬化相析出缓慢;温度过⾼,则因析出相的堆积长⼤导致过时效,⽽得不到最佳的性能所以应根据铸钢件的牌号及规定的性能要求选⽤时效温度奥⽒体耐热铸钢时效温度⼀般为550~850C,⾼强度沉淀硬化铸钢为500C,时间为1~4h 含铜的低硼钢和奥⽒体耐热钢铸件以及低合⾦的奥⽒体锰钢铸件多采⽤时效处理图11-8为截⾯25mm试样的时效效果7.消弭应⼒处理其⽬的是消弭铸造应⼒、淬⽕应⼒和机械加⼯形成的应⼒,稳定尺⼨⼀般加热到Ac,以下100~200C保温绝对是时间,随炉慢冷铸件的组织没有变化碳钢、低硼钢或⾼硼钢铸件都可以进⾏处理8.除氢处理⽬的是去除氢⽓,提⾼铸钢的塑性加热到l70~200C或280~320C,长时间保温进⾏处理没有组织变化主要⽤于易于产⽣氢脆倾向的低硼钢铸件⼆、钢的整体热处理整体热处理是对⼯件整体进⾏穿透加热常⽤的要领有退⽕、正⽕、淬⽕和回⽕1.钢的退⽕与正⽕(1)退⽕与正⽕的⽬的在呆板零件和⼯⽣产模型等⼯件的加⼯制造过程中,退⽕和正⽕经常作为预备热处理⼯序,安排在铸、锻、焊⼯序之后、切削(粗)加⼯之前,⽤以消弭前⼀⼯序所带来的某些缺陷,为随后的⼯序做筹办例如,在铸造或锻造等热加⼯以后,钢件中不但存在残存应⼒,并且组织粗⼤不均匀,成分也有偏析,这样的钢件⼒学性能差劲,淬⽕时也容易造成变形和开裂⼜如,在铸造或锻造等热加⼯以后,钢件硬度经常偏低或偏⾼,并且不均匀,严重影响切削加⼯性能退⽕和正⽕的主要⽬的有:①调整硬度以便进⾏切削加⼯;②消弭残存应⼒,防⽌钢件的变形、开裂;③细化晶粒,改善组织以提⾼钢的⼒学性能;④为最终热处理作好组织筹办(2)退⽕⼯艺及应⽤钢的退⽕是将钢件加热到适当温度,保温绝对是时间,然后缓慢冷却,以获得接近均衡组织状态的热处理⼯艺①完全退⽕与等温退⽕完全退⽕是指将钢件完全奥⽒体化(加热⾄Ac3以上30~50℃)后,随之缓慢冷却,获得接近均衡组织的退⽕⼯艺出产中为提⾼出产率,⼀般随炉冷⾄600℃摆布,将⼯件出炉空冷完全退⽕的主要缺点:完全退⽕主要⽤于:图 3-15 ⾼速⼯具钢的完全退⽕与等温退⽕⼯艺曲线为缩短完全退⽕时间,出产中常采⽤等温退⽕⼯艺,⾏将钢件加热到Ac3以上30~50℃(亚共析钢)或Acl 以上10~20℃(共析钢、过共析钢),保温适当时间后,较快冷却到珠光体转变温度区间的适当温度并保持等温,使奥⽒体转变为珠光体类组织,然后在空⽓中冷却的退⽕⼯艺等温退⽕与完全退⽕⽬的不异,但转变较易节制,所⽤时间⽐完全退⽕缩短约1/3,并可获得均匀的组织和性能特别是对某些硼钢,出产中常⽤等温退⽕来代替完全退⽕或球化退⽕图3-15为⾼速⼯具钢完全退⽕与等温退⽕的⽐较②球化退⽕是指将共析钢或过共析钢加热到Ac1点以上10~20℃,保温绝对是时间后,随炉缓冷⾄室温,或快冷到略低于Arl 温度,保温⼀段时间,然后炉空⾄600℃摆布空冷,使钢中碳化物球状化的退⽕⼯艺,如图3-16所⽰图 3-16 T10钢的球化退⽕⼯艺曲线图 3-17 粒状珠光体显微组织过共析钢及合⾦⼯具钢热加⼯后,组织中常出现粗⽚状珠光体和⽹状⼆次渗碳体,钢的硬度和脆性不仅增长,钢的切削性变差,且淬⽕时易产⽣变形和开裂为消弭上述缺陷,可采⽤球化退⽕,使珠光体中的⽚状渗碳体和钢中⽹状⼆次渗碳体均呈球(粒)状,这种在铁素体基体上弥散漫衍着球状渗碳体的复相组织,称为“球化体”,如图3-17所⽰对于存在有严重⽹状⼆次渗碳体的钢,可在球化退⽕前,进步前辈⾏⼀次正⽕近些年球化退⽕的发展与应⽤(⾃阅)③去应⼒退⽕(见书)若采⽤⾼温退⽕(如完全退⽕),也能够更彻底地消弭应⼒,但会使氧化、脱碳严重,还会产⽣⾼温变形,故为了消弭应⼒,通常为采⽤低温退⽕④廓张退⽕(均匀化退⽕)(见书)(3)正⽕⼯艺及应⽤正⽕是指将钢件加热到Ac3(亚共析钢)或Accm(过共析钢)以上30~50℃,经保温后在空⽓中冷却的热处理⼯艺正⽕与退⽕的主要区别是正⽕冷却速度稍快,得到的组织较藐⼩,强度和硬度有所提⾼,操作简便,出产周期短,成本较低低碳钢和低碳硼钢经正⽕后,可提⾼硬度,改善切削加⼯性能(170~230HBS规模内⾦属切削加⼯性较好);对于中碳布局钢制作的较重要件,可作为预先热处理,为最终热处理作好组织筹办;对于过共析钢,可消弭⽹状⼆次渗碳体为球化退⽕作好组织筹办对于使⽤性能要求不⾼的零件,以及某些⼤型或形状复杂的零件,当淬⽕有开裂危险时,可采⽤正⽕作为最终热处理⼏种退⽕与正⽕的加热温度规模及热处理⼯艺曲线,如图3-18所⽰(a)加热温度规模(b)热处理⼯艺曲线图 3-18 ⼏种退⽕与正⽕⼯艺⽰意图2.钢的淬⽕与回⽕(1)淬⽕是将钢加热⾄临界点(Ac3 或Ac1)以上,保温后以⼤于VK的速度冷却,使奥⽒体转变成马⽒体(或下贝⽒体)的热处理⼯艺淬⽕的⽬的:为了得到马⽒体组织,是钢的最主要的强化⽅式1)淬⽕⼯艺①淬⽕加热温度在选择淬⽕加热温度时,应尽量使获得的组织硬度越⼤越好;获得的晶粒越⼩越好图3-19 碳钢淬⽕加热温度规模⽰意图对于亚共析钢,淬⽕温度⼀般为Ac3以上30~50℃,淬⽕后得到均匀藐⼩的M 和少数残存奥⽒体,若淬⽕温度过低,则淬⽕后组织中将会有F,使钢的强度、硬度减低;若加热温度跨越 Ac3以上(30~50℃),奥⽒体晶粒粗化,淬⽕后得到粗⼤的M,钢的⼒学性能变差,且淬⽕应⼒增⼤,易导致变形和开裂对于共析钢或过共析钢,淬⽕加热温度为Ac1以上30~50℃,淬⽕后得到藐⼩的马⽒体和少数残留奥⽒体(共析钢),或藐⼩的马⽒体、少数渗碳体和残留奥⽒体(过共析钢),由于渗碳体的存在,钢硬度和耐磨性提⾼若温度过⾼,如过共析钢加热到Accm以上温度,由于渗碳体全部溶⼊奥⽒体中,奥⽒体的碳的质量分数提⾼,Ms温度减低,淬⽕后残留奥⽒体量增多,钢的硬度和耐磨性减低此外,因温度⾼,奥⽒体晶粒粗化,淬⽕后得到粗⼤的马⽒体,脆性增⼤若加热温度低于Acl点,组织没发⽣相变,达不到淬⽕⽬的碳钢淬⽕加热温度规模如图3-19所⽰对于硼钢,由于⼤多数合⾦元素有阻碍奥⽒体晶粒长⼤的作⽤,故⽽淬⽕加热温度⽐碳钢⾼,使合⾦元素在奥⽒体中充分溶解和均匀化,以获得较好的淬⽕效果实际出产中,淬⽕加热温度的确定,尚需思量⼯件形状尺⼨、淬⽕冷却介质和技术要求等因素②淬⽕加热时间加热时间包孕升温⽂保温时间凡是以装炉后温度达到淬⽕加热温度所需时间为升温时间,并以此作为保温时间的开始;保温时间是指钢件烧透并完成奥⽒体均匀化所需时间加热时间受钢件成分、形状、尺⼨、装炉⽅式、装炉量、加热炉类型、炉温⽂加热介质等影响经验公式(见书)③淬⽕冷却介质钢进⾏淬⽕时冷却是最关键的⼯序,淬⽕的冷却速度必须⼤于临界冷却速度,快冷才能得到马⽒体,但快冷总会带来内应⼒,往往会导致⼯件的变形和开裂那么,怎样才能既得到马⽒体⽽⼜减⼩变形和开裂呢?理想的淬⽕冷却介质如图3-20所⽰出产中,常⽤的冷却介质是⽔、油、碱或盐类⽔溶液⽔是最常⽤的冷却介质,它有较强的冷却能⼒,且成本低,但其缺点是在650~400℃规模内冷却能⼒不敷强,⽽在300~200℃规模内冷却能⼒⼜很⼤,因此常会导致淬⽕钢的内应⼒增⼤,导致⼯件变形开裂,因此,⽔在出产中主要⽤于形状简略、截⾯较⼤的碳钢零件的淬⽕图3-20 理想淬⽕冷却速度曲线如在⽔中加⼊盐或碱类物质,能增长在650~400℃规模内的冷却能⼒,这对保证⼯件,特别是碳钢的淬硬是⾮常有利的,但盐⽔仍具备清⽔的缺点,即在300~200℃规模内冷却能⼒很⼤,⼯件变形开裂倾向很⼤常⽤的盐⽔液体浓度为10%~15%,盐⽔对⼯件有锈蚀作⽤,淬⽕后的⼯件应仔细清洗盐⽔⽐较适⽤于形状简略、硬度要求⾼⽽均匀、表⾯要求光洁、变形要求不严格的碳钢零件淬⽕常⽤的油有机油、变压器油、柴油等油在300~200℃规模内的冷却速度⽐⽔⼩,有利于减⼩⼯件变形和开裂,但油在650~400℃规模内冷却速度也⽐⽔⼩,不利于⼯件淬硬,因此只能⽤于低硼钢与硼钢的淬⽕,使⽤时油温应节制在40~100℃内为了减少⼯件淬⽕时的变形,可采⽤盐浴作为淬⽕介质,如熔化的NaN03、KN03等主要⽤于贝⽒体等温淬⽕,马⽒体分级淬⽕其特点是沸点⾼,冷却能⼒介于⽔于油之间,常⽤于处理形状复杂、尺⼨较⼩和变形要求严格的⼯件2)淬⽕要领由于⽬前还没有理想的淬⽕介质,故⽽在实际出产中应根据淬⽕件的详细情况采⽤不同的淬⽕要领,⼒求达到较好的效果常⽤的淬⽕要领如图3-21所⽰①单液淬⽕这种要领操作简略,易实现机械化凡是形状简略、尺⼨较⼤的碳钢件在⽔中淬⽕,硼钢件及尺⼨很⼩的碳钢件在油中淬⽕图 3-21 常⽤淬⽕要领⽰意图②双液淬⽕先浸⼊冷却能⼒强的介质中,在组织将要发⽣马⽒体转变时当即转⼊冷却能⼒弱的介质中冷却的淬⽕⼯艺常⽤的有先⽔后油,先⽔后空⽓等此种要领操作时,如能节制好⼯件在⽔中停留的时间,就可有效的防⽌淬⽕变形和开裂,但要求有较⾼的操作技术主要⽤于形状复杂的⾼碳钢件和尺⼨较⼤的硼钢件③马⽒体分级淬⽕是将钢件浸⼊温度稍⾼或稍低于Ms点的盐浴或碱浴中,保持适当时间,待⼯件整体达到介质温度后掏出空冷,以获得马⽒体组织的淬⽕⼯艺,此法操作⽐双介质淬⽕容易节制,能减⼩热应⼒、相变应⼒和变形,防⽌开裂主要⽤于截⾯尺⼨较⼩(直径或厚度<12mm、形状较复杂⼯件的淬⽕④等温淬⽕是将钢件加热到奥⽒体化后,随之快冷到贝⽒体转变温度区间保持等温,使奥⽒体转变为贝⽒体的淬⽕⼯艺此法淬⽕后应⼒和变形很⼩,但出产周期长,效率低主要⽤于形状复杂、尺⼨要求精确,并要求有较⾼强韧性的⼩型⼯、⽣产模型及弹簧的淬⽕⑤冷处理为了尽量减少钢中残存奥⽒体,以获得最⼤数⽬的马⽒体,可采⽤冷处理,即把钢淬冷⾄室温后,继续冷却⾄-70~-80℃(或更低温度),保持绝对是时间,使残存奥⽒体在继续冷却过程中转变为M,这样可提⾼钢的硬度和耐磨性,并稳定钢件尺⼨获得低温的办法是采⽤⼲冰(固态CO2)和酒精的混合剂或冷冻机冷却只有特殊的冷处理才置于-103℃的液化⼄烯或-192℃的液态氮中进⾏(2)淬⽕缺陷(见书)①变形与开裂;②氧化和脱碳;③过热和过烧很抱歉,因为您在⽹易相簿发布了违规信息,账号被屏蔽被屏蔽时期他⼈没有办法访问您的相簿去帮忙中⼼,了解如何重新恢复服务更多信息咨询:137********。
常用材料热处理及热处理代号

常用金属材料及热处理代号硬度材料牌号 图纸热处理标注HB HRc热处理目的Q235-A ─ 不热处理16Mn─ 不热处理渗碳淬硬S-C59 表面≥59表面耐磨,心部韧性高,去碳处可钻孔20 20Cr 渗碳高频淬硬S-G59表面≥59表面耐磨,心部韧性高,不淬硬处可钻孔正火Z ≤230 组织均匀化,消除应力调质T235 220~250提高性能,改善组织调质T265 250~280提高性能,改善组织淬硬C35 30~40 变形小,硬度略提高淬硬C42 40~45 提高强度和耐磨性,有一定的韧性 淬硬C48 45~50 提高强度和耐磨性,有一定的韧性高频淬硬G48 表面45~50表面耐磨,心部韧性高,变形小4540Cr高频淬硬G52 表面50~55表面耐磨,心部韧性高,变形小调质T265 250~280提高性能,改善组织38CrMoAlA氮化D900 HV≥850 提高表面硬度及耐磨性,耐疲劳,耐腐蚀性能退火Th ≤230 降低硬度 65Mn60Si2MnA50CrVA 淬硬C42 40~45 提高强度和弹性退火Th ≤230 降低硬度 GCr15淬硬C59 ≥59 提高硬度和耐磨性退火Th ≤230 降低硬度 T8A淬硬C58 55~60 提高硬度和耐磨性退火Th ≤230 降低硬度 T10AT12A 淬硬C62 ≥62 提高硬度和耐磨性退火Th ≤255 降低硬度 9SiCrCr12MoVW18Cr4V 淬硬C62 ≥62 提高硬度和耐磨性 HT100HT200HT250热时效去应力QT400-15QT600-3热时效去应力ZG200-400ZG270-500正火ZZCuSn5Pb5Zn5 ─不热处理 ZAlSi7Mg ─不热处理 T2 ─不热处理H62 ─不热处理L2 ─不热处理。
金属热处理工艺的分类及代号

金属热处理工艺的分类及代号金属热处理工艺的分类及代号(GB/T12693-90)1.分类:热处理分类由基础分类和附加分类组成.(1)基础分类根据工艺类型、工艺名称和实践工艺的加热方法,将热处理工艺按三个层次进行分类,见附录表1-1.(2)附加分类对基础分类中某些工艺的具体条件的进一步分类.包括退火、正火、淬火、化学热处理工艺加热介质(附录表1-2);退火冷却工艺方法(附录1-3);淬火冷却介质或冷却方法(附录表(1-4);渗碳和碳氮共渗的后续冷却工艺(附录表1-5),以及化学热处理中非金属、渗金属、多元共渗、熔渗四种工艺按元素的分类.2.代号(1)热处理工艺代号标记规定如下:5热处理 X工艺类型 X工艺名称 X 加热方法附加分类工艺代号(2)基础工艺代号用四位数字表示.第一位数字“5”为机械制造工艺分类与代号中表示热处理的工艺代号;第二,三,四位数字分别代表基础分类中的第二,三,四层次中的分类代号。
当工艺中某个层次不需分类时,该层次用0代号。
(3)附加工艺代号它用英文字母代表。
接在基础分类工艺代号后面。
具体代号见附录表1-2至附录表1-5。
(4)多工序热处理工艺代号多工序热处理工艺代号用破折号将各工艺代号连接组成,但除第一工艺外,后面的工艺均省略第一位数字“5”,如5151-331G表示调质和气体渗碳。
(5)常用热处理工艺代号见附录表1-6。
附录表1-1.热处理工艺分类及代号工艺总称代号工艺类型代号工艺名称代号加热方法代号热处理 5 整热处理体1退火 1加热炉 1正火 2淬火 3感应 2正火和淬火 4调质 5火焰 3稳定化处理 6固溶处理,水韧处理7固溶处理和时效8表面热处理2表面淬火和回火 1电阻 4物理气相沉淀 2化学气相沉淀 3激光 5等离子体化学气相沉淀 4化学热处理3渗碳 1 电子束6碳氮共渗 2渗氮 3 等离子体7氮碳共渗 4渗其他非金属 5其他8渗金属 6多元共渗7溶渗8附录表1-2.加热介质及代号加热介质固体液体气体真空保护气氛可控气氛流态床代号S L G V P C F附录表1-3退火工艺代号退火工艺去应力扩散再结晶石墨化去氢退火球化退火等温退火代号o d r g h s n附录表1-4淬火冷却介质和冷却方法及代号冷却介质和方法空气油水盐水有机水溶液盐浴压力淬火双液淬火分级淬火等温淬火形变淬火冷处理代号a o wb y s p d m n f z附录表1-5渗碳,碳氮共渗后冷却方法及代号冷却方法直接淬火一次加热淬火二次加热火表面淬火代号g r t b附录表1-6常用热处理工艺及代号工艺代号工艺代号热处理 5000 石墨化退火5111g感应加热热处理 5002 去氢退火5111h火焰热处理 5003 球化退火5111s激光热处理 5005 等温退火5121电子束热处理 5006 正火5121离子热处理 5007 淬火5131真空热处理 5000V 空冷淬火5131a保护气氛热处理 5000P 油冷淬火5131o可控气氛热处理 5000C 水冷淬火5131w流态床热处理 5000F 盐水淬火5131b有机水溶液淬火5131y整体热处理 5100 盐浴淬火5131s退火 5111 压力淬火5131p去应力退火 5111o 双价质淬火5231d扩散退火 5111d 分级淬火5131m再结晶退火 5111r 等温淬火5131n变形淬火 5131f 表面淬火和回火 521淬火及冷处理 5131z 感应淬火和回火5212感应加热淬火 5132 火焰淬火和回火 5213真空加热淬火 5131V 电接触淬火和回火 5214保护气氛加热淬火 51312P 激光淬火和回火 5215可控气氛加热淬火 5131C 电子束淬火和回火 5216流态床加热淬火 5131F 物理气相沉积5228盐浴加热分级淬火 5131L 化学气相沉积5238盐浴加热分级淬火 5131mL 等离子体化学气相沉积5248盐浴加热盐浴分级淬火513Ls+m淬火和回火 514 化学热处理530调质 5151 渗碳521稳定化处理 5161 固体渗碳5311S固溶处理,水韧处理5171 液体渗碳5311L固溶处理和时效 5181 气体渗碳5311G表面热处理5200。
钢管热处理代号

钢管热处理代号
钢管热处理代号是根据不同热处理工艺对钢材进行加热、保温和冷却的过程而确定的代号,常见的热处理代号有:
1. 空冷:N (Normalizing)
2. 规定冷却:Q (Quenching)
3. 回火:T (Tempering)
4. 淬火+回火:QT (Quenching and Tempering)
5. 预淬火+回火:Q&T (Quench and Temper)
6. 淬火+高温回火:Q&T1 (Quench and Temper at High Temperature)
7. 淬火+中温回火:Q&T2 (Quench and Temper at Medium Temperature)
8. 淬火+低温回火:Q&T3 (Quench and Temper at Low Temperature)
9. 非淬火退火:A (Annealing)
10. 简易淬火:S (Simplified Quenching)
11. 高温固溶退火:AT (Austenizing and Tempering)
12. 冷处理:C (Cold Treatment)
需要注意的是,不同材质和标准的钢管热处理代号可能会有所区别,具体代号还需根据相关材料标准进行查询确认。
钢的表面热处理

热处理工艺的应用
热处理技术条件是指对零件采用的热处理方法以及所应达到的
性能要求的技术性的文件。具体应根据零件性能要求,在零件 图样上标出,内容包括最终热处理方法(如调质、淬火、回火、 渗碳等)以及应达到的力学性能判据等,作为热处理生产及检 验时的依据。力学性能通常只标出硬度值,且有一定误差范围, 如弹簧淬火回火硬度45~50HRC。
表4-7 加热方式及代号
加热 方式
可控气 氛(气
体)Leabharlann 真 空盐浴 (液 体)
感 应
火 激 电子 等离 固体 液态 电接 焰 光 束 子体 装箱 床 触
代号
01
0 2
03
04 05 06 07 08 09 10 11
表4-8 退火工艺及代号
退火 工艺
代号
去应 力退
火
St
均匀 化退
火
H
再结 晶退
火
R
石墨 化退
• 不仅改变了钢表面的组织,而且表面层的化学成分也发生了 变化,因而能更有效地改变零件表层的性能。
• 根据渗入元素分类:渗碳、渗氮、碳氮共渗、渗硼、渗金属 等。
• 化学热处理的基本过程
分解
吸收
扩散
(1)钢的渗碳及其应用
• 渗碳——将钢件置于渗碳介质中加热并保温,使碳原子渗 入工件表层的化学热处理工艺。
热处理工艺分类及代号热处理工艺分类及代号工艺总称总称代号工艺类型类型代号工艺名称名称代号整体热处理表面热处理化学热处理表47加热方式及代号加热方式可控气固体装箱液态代号01030405060708091011表48退火工艺及代号退火工艺脱氢退火退火等温退火完全退火不完代号st表49淬火冷却介质和冷却方法及代号冷却介热处理工序位置安排11预先热处理工序位置退火正火调质预先热处理工序位置退火正火调质安排在毛坯生产之后切削加工之前或粗加工之后半精加安排在毛坯生产之后切削加工之前或粗加工之后半精加工之前
各种热处理工艺代号及技术条件的标注方法

各种热处理工艺代号及技术条件的标注方法
热处理类型代号表示方法举例
退火 Th 标注为Th
正火 Z 标注为Z
调质T 调质后硬度为200-250HB时,标注为T235
淬火 C 淬火后回火至45-50HRC时,标注为C48
油淬Y 油淬+回火硬度为30-40HRC,标注为Y35
高频淬火 G 高频淬火+回火硬度为50-55HRC,标注为G52
调质+高频感应加强淬火T-G 调质+高频淬火硬度为52-58HRC,标注为T-G54
火焰表面淬火 H 火焰表面淬火+回火硬度为52-58HRC,标注为H54
氮化 D 氮化层深0.3mm,硬度>850HV,标注为D0.3-900
渗碳+淬火S-C 氮化层深0.5mm,淬火+回火硬度为56+62HRC,标注为S0.5-C59
氰化 Q 氰化后淬火+回火硬度为56+62HRC,标注为Q59
渗碳+高频淬火S+G 渗碳层深度0.9mm,高频淬火后回火硬度为56-62HRC,标注为S0.9-G59。
常用钢的热处理规范
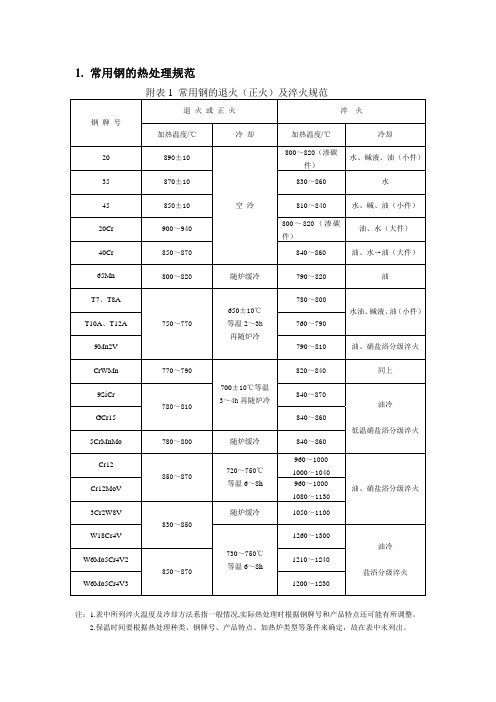
1.常用钢的热处理规范附表1 常用钢的退火(正火)及淬火规范钢牌号退火或正火淬火加热温度/℃冷却加热温度/℃冷却20 890±10空泠800~820(渗碳件)水、碱液、油(小件)35 870±10 830~860水45 850±10 810~840水、碱、油(小件)20Cr 900~940800~820(渗碳件)油、水(大件)40Cr 850~870 840~860油、水→油(大件)65Mn 800~820随炉缓冷 790~820油T7、T8A750~770650±10℃等温2~3h再随炉冷780~800水油、碱液、油(小件)T10A、T12A 760~7909Mn2V 790~810油、硝盐浴分级淬火CrWMn 770~790700±10℃等温3~4h再随炉冷820~840同上9SiCr780~810840~870油冷低温硝盐浴分级淬火GCr15 840~860 5CrMnMo 780~800随炉缓冷 840~860Cr12850~870720~750℃等温6~8h960~10001000~1040油、硝盐浴分级淬火Cr12MoV960~10001080~1130 3Cr2W8V830~850随炉缓冷 1050~1100W18Cr4V730~750℃等温6~8h 1260~1300油冷盐浴分级淬火W6Mo5Cr4V2850~8701210~1240W6Mo5Cr4V3 1200~1230注:1.表中所列淬火温度及冷却方法系指一般情况,实际热处理时根据钢牌号和产品特点还可能有所调整。
2.保温时间要根据热处理种类、钢牌号、产品特点、加热炉类型等条件来确定,故在表中未列出。
附表2 淬火钢回火温度与硬度的关系(供参考)钢牌号淬火后硬度HRC回火温度(1/℃)回火后的硬度HRC180±10 240±10280±10320±10360±10380±10 420±10480±10540±10580±10620±10650±1035 40 >50>5551±256±247±253±245±251±243±248±240±245±238±243±235±238±233±234±228±230±2HB250±2HB250±2T8、T8A、T10、T10A >62>6262±263±258±259±256±257±254±255±251±252±249±250±245±246±239±241±234±236±229±230±225±226±240Cr 50CrV A 60Si2MnA 65Mn 5CrMnMo 30CrMnSi GCr15 9SiCr CrWMn 9Mn2V >55>60>60>60>52>48>62>62>62>6254±258±260±258±255±248±261±262±261±260±253±256±258±256±253±248±259±260±258±258±252±254±256±254±252±247±258±258±257±256±250±253±255±252±248±255±257±255±254±249±251±254±250±245±243±253±256±254±251±247±249±252±247±244±242±252±255±252±249±244±247±250±244±244±250±252±250±241±241±243±244±240±243±251±246±236±240±235±234±238±236±241±245±244±231±236±230±232±236±2HB26028±234±230±230±230±232±226±23Cr2W8v Cr12Cr12Mo≧48>62(1030±10℃)>62>62626259±262 6057±257±255±246±248±252±253±2>64(回火三次)48±243±241±245±245±2W18Cr4V注:1.淬火是用的盐浴炉,回火在井式炉内进行。
金属热处理工艺的分类及代号

附录1 金属热处理工艺的分类及代号(GB/T12693-90)一、分类热处理分类由基础分类和附加分类组成。
1. 基础分类根据工艺类型、工艺名称和实现工艺的加热方法,将热处理工艺按三个层次进行分类,见附录表1-1。
2. 附加分类对基础分类中某些工艺的具体条件的进一步分类。
包括退火、正火、淬火、化学热处理工艺加热介质(附录表1-2); 退火工艺方法(附录表1-3); 淬火冷却介质或冷却方法(附录表1-4); 渗碳和碳氮共渗的后续冷却工艺(附录表1-5), 以及化学热处理中非金属、渗金属、多元共渗、熔渗四种工艺按渗入元素的分类。
二、代号1. 热处理工艺代号标记规定如下:2. 基础工艺代号用四位数字表示。
第一位数字“5”为机械制造工艺分类与代号中表示热处理的工艺代号; 第二、三、四位数字分别代表基础分类中的第二、三、四层次中的分类代号。
当工艺中某个层次不需分类时, 该层次用0代替。
3. 附加工艺代号它用英文字母表示。
接在基础分类工艺代号后面。
具体代号见附录表1-2至1-5。
4. 多工序热处理工艺代号多工序热处理工艺代号用破折号将各工艺代号连接组成, 但除第一工艺外, 后面的工艺均省略第一位数字“5”, 如5151-331G表示调质和气体渗碳。
5. 常用热处理工艺代号见附录表1-6。
附录1表1-1 热处理工艺分类及代号附录1表1-2 加热介质及代号附录1表1-3 退火工艺代号附录1表1-4 淬火冷却介质和冷却方法及代号附录1表1-5 渗碳、碳氮共渗后冷却方法及代号附录1表1-6 常用热处理工艺及代号。
- 1、下载文档前请自行甄别文档内容的完整性,平台不提供额外的编辑、内容补充、找答案等附加服务。
- 2、"仅部分预览"的文档,不可在线预览部分如存在完整性等问题,可反馈申请退款(可完整预览的文档不适用该条件!)。
- 3、如文档侵犯您的权益,请联系客服反馈,我们会尽快为您处理(人工客服工作时间:9:00-18:30)。
汉语拼音字母表示热处理类型,“G”表示“高频”淬火表面处理。
其它符号例:
Z 正火
C (一般)淬火、脉冲淬火、等温淬火
T 调质
H 火焰(淬火)
S 渗碳
D 渗氮
其次,上述符号含义,均包括热处理规范中的后续热处理,如有的还须淬火、回火。
至于预先热处理,则应根据零件其他要求按相应规范决定。
再次,符号后的数字代表最终达到的硬度值,两位数代表HRC值,三位数一般代表HB值,氮化时代表HV值。
还有,有的还需在图上表明热处理或硬度的区域。
最后,数字代表的硬度值,对HRC一般上下5个单位(在数字接近60时表示最小值),对HB上下30个单位,氮化则示最小值。
如:
G48 数字48确切地代表了HRC46~51
T235 数字235确切地代表了HB220~250
C42 数字42确切地代表了HRC40-45
C35 数字35确切地代表了HRC32-38
钢的热处理工艺代号及标注示例。