冶金过程分析监测系统
冶金企业自动化系统的分级

冶金企业自动化系统的分级一、背景介绍冶金企业作为重要的工业部门之一,其生产过程需要依靠自动化系统来实现高效、安全、稳定的生产。
冶金企业自动化系统的分级是为了满足不同层次的管理需求,确保生产过程的顺利进行。
本文将详细介绍冶金企业自动化系统的分级标准及其应用。
二、分级标准1. 一级系统:生产控制系统一级系统是冶金企业自动化系统的核心,主要负责控制整个生产过程。
其功能包括生产计划制定、生产过程控制、设备状态监测等。
一级系统需要具备以下特点:- 实时性:能够实时监测生产过程中的各项指标,并对异常情况进行及时处理。
- 稳定性:能够保证系统的稳定运行,不受外界干扰影响。
- 可靠性:能够确保系统的可靠性,避免因系统故障导致生产中断。
- 扩展性:能够根据生产需求进行系统的扩展,满足不同规模的生产要求。
2. 二级系统:过程监控系统二级系统是对一级系统的补充和支持,主要负责对生产过程中的关键参数进行监测和控制。
其功能包括设备状态监测、异常报警、数据分析等。
二级系统需要具备以下特点:- 精确性:能够准确监测和控制生产过程中的关键参数,确保生产的稳定性和质量。
- 可视化:能够通过图表、曲线等形式直观地展示生产过程中的数据和变化趋势。
- 分析能力:能够对生产过程中的数据进行分析,提供决策支持和优化建议。
- 与一级系统的集成:能够与一级系统实现数据的共享和交互,实现信息的无缝传递。
3. 三级系统:管理信息系统三级系统是冶金企业自动化系统的管理层,主要负责对生产过程进行监控和管理。
其功能包括生产计划制定、资源调度、成本控制等。
三级系统需要具备以下特点:- 综合性:能够对整个冶金企业的生产过程进行综合管理,实现资源的合理利用。
- 决策支持:能够提供决策支持和优化建议,帮助管理层做出科学决策。
- 数据分析:能够对生产过程中的数据进行分析,发现问题和改进的空间。
- 与一、二级系统的集成:能够与一、二级系统实现数据的共享和交互,实现信息的无缝传递。
冶金企业自动化系统的分级

冶金企业自动化系统的分级一、引言冶金企业自动化系统的分级是指根据自动化程度和功能需求,将冶金企业的自动化系统划分为不同的级别。
通过分级可以更好地管理和控制冶金生产过程,提高生产效率和质量,降低能耗和人力成本。
本文将详细介绍冶金企业自动化系统的分级标准和各级别的功能要求。
二、冶金企业自动化系统的分级标准根据冶金企业的规模、工艺流程和自动化需求,将自动化系统分为以下几个级别:1. 一级自动化系统:一级自动化系统是冶金企业最基础的自动化系统,主要用于数据采集和监控。
该级别的系统主要包括传感器、数据采集设备、数据传输设备和监控终端。
通过采集和传输设备,将生产过程中的各种数据传输到监控终端,实时监测生产状态,提供数据支持给管理层做出决策。
2. 二级自动化系统:二级自动化系统是在一级自动化系统基础上增加了控制功能。
该级别的系统主要包括控制设备、执行机构和控制终端。
通过控制设备和执行机构,实现对冶金生产过程的控制,如温度控制、压力控制、流量控制等。
控制终端用于设置控制参数和监测控制效果。
3. 三级自动化系统:三级自动化系统是在二级自动化系统基础上增加了优化功能。
该级别的系统主要包括优化算法、模型预测和自动调节。
通过优化算法和模型预测,对冶金生产过程进行优化调度,提高生产效率和质量。
自动调节功能可以根据实时数据进行自动调整,保持生产过程的稳定性。
4. 四级自动化系统:四级自动化系统是在三级自动化系统基础上增加了智能化功能。
该级别的系统主要包括人工智能、机器学习和大数据分析。
通过人工智能和机器学习技术,对冶金生产过程进行智能化管理和优化。
大数据分析可以对海量数据进行分析和挖掘,发现潜在的规律和问题,提供决策支持。
三、各级别自动化系统的功能要求1. 一级自动化系统功能要求:- 实时数据采集和传输:采集和传输冶金生产过程中的各种数据,如温度、压力、流量等。
- 数据监控和报警:实时监测生产状态,及时发现异常情况并报警。
过程分析系统简介
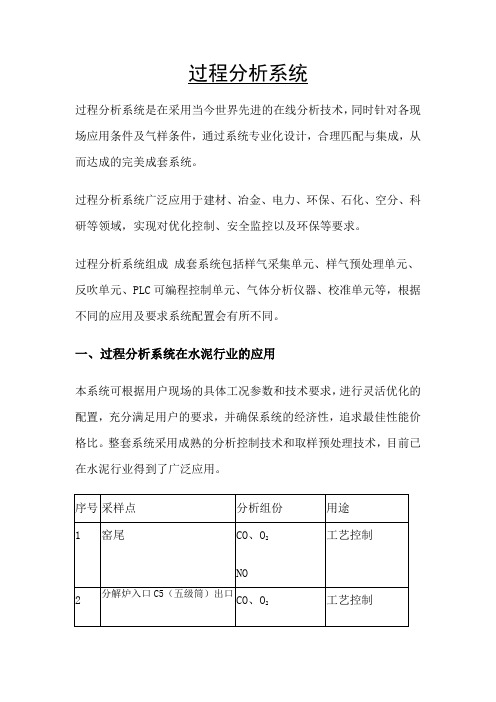
过程分析系统
过程分析系统是在采用当今世界先进的在线分析技术,同时针对各现场应用条件及气样条件,通过系统专业化设计,合理匹配与集成,从而达成的完美成套系统。
过程分析系统广泛应用于建材、冶金、电力、环保、石化、空分、科研等领域,实现对优化控制、安全监控以及环保等要求。
过程分析系统组成成套系统包括样气采集单元、样气预处理单元、反吹单元、PLC可编程控制单元、气体分析仪器、校准单元等,根据不同的应用及要求系统配置会有所不同。
一、过程分析系统在水泥行业的应用
本系统可根据用户现场的具体工况参数和技术要求,进行灵活优化的配置,充分满足用户的要求,并确保系统的经济性,追求最佳性能价格比。
整套系统采用成熟的分析控制技术和取样预处理技术,目前已在水泥行业得到了广泛应用。
二、过程分析系统在冶金行业的应用
三、过程分析系统在电力行业的应用
四、其他
根据工艺要求或安全需要用于气体在线分析。
主要技术参数:
1、测量范围:
SO2 0-100ppm至0-20% CH4 0-200ppm至0-20% NO 0-200ppm至0-20% CO 0-100ppm至0-100% CO2 0-100ppm至0-100% O2 0-500ppm至0-25%
2、响应时间: 1.5秒
3、模拟输出 4—20mA DC
4、气体流量1.2—1.6L/min
5、电源AC220V±10% 50±0.5Hz 150VA。
SCR炉铸区CO检测分析系统故障分析及控制改进

SCR炉铸区CO检测分析系统故障分析及控制改进张伟旗【摘要】针对SCR炉铸区CO检测分析系统故障进行分析及控制改进,系统检测分析响应速度快,准确度、精度及稳定性高,故障率低,有利于及时调整与监控铜液的氧含量,铸锭质量好,铜杆线氧含量波动小,完全能满足国内外客户对高端铜细线及超微线的特殊需求.【期刊名称】《有色设备》【年(卷),期】2016(000)006【总页数】6页(P34-39)【关键词】CO检测分析系统;故障率;控制改进【作者】张伟旗【作者单位】江西铜业集团铜材有限公司,江西贵溪335424【正文语种】中文【中图分类】TG23;TG291烟气分析在冶金、石油化工、火力发电、水泥及化肥等行业占有重要地位。
行业不同,其烟气成分也不尽相同,主要包括CO、CO2、SO2、O2及氮氧化物等气体。
江铜引进美国南线铜业公司SCR3000/4500二条铜杆连铸连轧生产线,分别于2003、2006年建成投产,而作为该生产线自动化控制的重要组成部分,其SCR炉铸区CO监测分析系统能实时、精确、高效地采集燃烧样气中CO的相关数据,分析工艺流程中的介质组成,能为铜杆连铸连轧生产提供相关的控制依据,实现该自动化生产线的连铸过程控制,将直接影响到铜液铸造、锭坯结晶的质量好坏及铜杆后序加工质量,甚至最终产品质量[1]。
然而,尽管罗斯蒙特Rosemount CO监测分析技术在世界上领先,但其设计过程监控和数据采集存在一些缺陷,应用技术尚有不足之处,在使用过程中存在问题也不少,且随着该公司产能的不断攀升及生产组织模式的变化,SCR炉铸区烟气含尘和含水增加,导致CO监测分析系统故障率过高,铜液温度难以控制,氧含量变化大,铸锭夹杂缺陷率高,导致铜杆线产品氧含量超标,客户意见大、投诉率高,严重影响企业的形象及社会经济效益,使企业发展陷入窘境。
因而对SCR炉铸区CO检测分析系统故障进行分析、研究,且作针对性的控制改进,对改善和提高SCR铜杆连铸连轧生产线的工艺装备技术水平,至关重要。
有色冶金全流程高效转化智能协同控制关键技术及应用_概述及解释说明

有色冶金全流程高效转化智能协同控制关键技术及应用概述及解释说明1. 引言1.1 概述有色冶金行业是指对非铁金属矿石(如铜、镍、铅、锌等)进行冶炼、提纯及加工的产业,其在国民经济发展中具有重要地位。
随着科技的不断进步和市场需求的增长,有色冶金企业面临着提高生产效率和质量,降低能耗排放的压力。
因此,针对有色冶金全流程的智能化协同控制技术应运而生。
本文主要介绍了有色冶金全流程高效转化智能协同控制关键技术及应用。
通过采用智能传感与数据采集技术、数据处理与分析技术以及高效转化控制算法与模型预测技术,实现了对有色冶金过程的精确监测和控制。
同时,结合实际应用案例分析,在某XX冶炼厂成功应用了智能协同转炉控制系统以及数据驱动的能源优化方法,并总结了2020年A市某有色冶金企业全流程智能协同控制项目的实施经验。
1.2 文章结构本文主要分为以下几个部分:2. 有色冶金全流程高效转化智能协同控制关键技术及应用在这一部分,我们将详细介绍有色冶金全流程高效转化智能协同控制的概述,并重点介绍其中的关键技术。
这些技术包括智能传感与数据采集技术、数据处理与分析技术以及高效转化控制算法与模型预测技术。
2.1 全流程高效转化智能协同控制概述我们将阐述有色冶金全流程高效转化智能协同控制的基本原理和目标。
通过实现全过程的信息收集和处理以及精确的控制策略,使得有色冶金行业能够提高生产效率、降低成本以及优化资源利用。
2.2 关键技术介绍在这一小节中,我们将详细介绍几个关键技术,包括智能传感与数据采集技术、数据处理与分析技术以及高效转化控制算法与模型预测技术。
通过使用这些关键技术,可以有效地实现对有色冶金过程中关键参数的监测和优化控制。
2.3 应用案例分析我们将介绍几个实际应用案例,包括XX冶炼厂智能协同转炉控制系统的应用实践、XX冶炼厂数据驱动的能源优化在行业中的推广以及2020年A市某有色冶金企业全流程智能协同控制项目的实施经验总结。
通过这些案例,我们可以更清楚地了解有色冶金全流程智能协同控制技术的实际效果和应用前景。
冶金行业中的质量控制方法与技术

冶金行业中的质量控制方法与技术在现代工业生产中,质量控制是确保产品质量的关键环节。
冶金行业作为重要的基础产业,对于质量控制更是尤为重视。
本文将介绍冶金行业中常用的质量控制方法与技术,并讨论其应用与效果。
一、质量控制方法1. 严格进货检验:冶金行业的原材料对产品质量有着重要影响。
因此,严格的进货检验是确保产品质量的第一步。
通过对原材料的化学成分、物理性能等进行检测,可以以保证产品的质量稳定性。
2. 过程控制:冶金生产过程中,合理的过程控制是保证产品质量的重要手段。
通过监测关键工艺参数,如温度、压力、流量等,实时调整操作参数,以确保产品在生产过程中达到预定的质量标准。
3. 检测分析:冶金行业在产品质量控制中广泛应用各种检测分析技术。
例如,化学成分分析、金相检测、力学性能测试等。
这些检测分析手段能够及时发现产品中的缺陷和问题,并及时调整生产工艺,保障产品的质量稳定性。
二、质量控制技术1. 先进的制造技术:随着科技的进步,冶金行业也不断引入先进的制造技术。
例如,数控机床、激光切割设备等。
这些技术的应用,可以提高产品的加工精度和一致性,从而提高产品的质量水平。
2. 自动化控制系统:针对冶金行业生产过程中复杂多变的特点,引入自动化控制系统是实现高质量生产的有效手段。
自动化控制系统能够实现对关键参数的实时监测和调整,提高生产效率和产品质量的稳定性。
3. 数据分析与智能决策:通过大数据分析技术,冶金企业能够收集和存储大量的生产数据,并利用智能决策技术进行数据分析和运营优化。
通过分析数据,企业可以找到生产中的不合理因素,并及时做出调整,提高产品质量和生产效益。
三、质量控制效果评估1. 控制图分析:控制图是质量控制中的常用工具,能够直观反映产品的质量稳定性。
通过对生产过程中的关键参数进行统计和分析,可以判断产品变异是否在可接受范围内,并及时采取措施进行调整。
2. 系统审核与认证:为了评估企业的质量管理水平和产品质量稳定性,冶金企业常常进行ISO质量管理体系认证。
在线分析技术如何改善过程控制
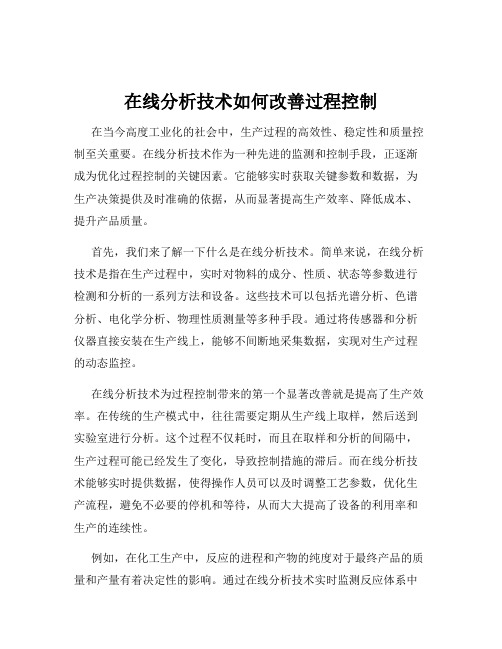
在线分析技术如何改善过程控制在当今高度工业化的社会中,生产过程的高效性、稳定性和质量控制至关重要。
在线分析技术作为一种先进的监测和控制手段,正逐渐成为优化过程控制的关键因素。
它能够实时获取关键参数和数据,为生产决策提供及时准确的依据,从而显著提高生产效率、降低成本、提升产品质量。
首先,我们来了解一下什么是在线分析技术。
简单来说,在线分析技术是指在生产过程中,实时对物料的成分、性质、状态等参数进行检测和分析的一系列方法和设备。
这些技术可以包括光谱分析、色谱分析、电化学分析、物理性质测量等多种手段。
通过将传感器和分析仪器直接安装在生产线上,能够不间断地采集数据,实现对生产过程的动态监控。
在线分析技术为过程控制带来的第一个显著改善就是提高了生产效率。
在传统的生产模式中,往往需要定期从生产线上取样,然后送到实验室进行分析。
这个过程不仅耗时,而且在取样和分析的间隔中,生产过程可能已经发生了变化,导致控制措施的滞后。
而在线分析技术能够实时提供数据,使得操作人员可以及时调整工艺参数,优化生产流程,避免不必要的停机和等待,从而大大提高了设备的利用率和生产的连续性。
例如,在化工生产中,反应的进程和产物的纯度对于最终产品的质量和产量有着决定性的影响。
通过在线分析技术实时监测反应体系中各物质的浓度变化,操作人员可以精确控制反应条件,如温度、压力、反应物的添加速度等,确保反应按照预期的方向进行,最大程度地提高反应转化率和选择性,从而提高生产效率和经济效益。
其次,在线分析技术有助于提升产品质量的稳定性。
产品质量的一致性是企业在市场竞争中立足的关键之一。
在线分析技术能够实时检测产品中的关键质量指标,如成分含量、杂质水平、物理性能等,一旦发现偏差,立即采取纠正措施,从而将质量波动控制在最小范围内。
以制药行业为例,药品的质量直接关系到患者的健康和生命安全,因此对生产过程的控制要求极为严格。
通过在线分析技术,如高效液相色谱(HPLC)和近红外光谱(NIR),可以实时监测药品生产过程中活性成分的含量、杂质的种类和含量等关键指标。
人工智能在冶金自动化中的应用

人工智能在冶金自动化中的应用一、引言随着科技的不断发展,人工智能(Artificial Intelligence,AI)已经成为当今世界的热门话题。
人工智能技术在各个领域都有广泛的应用,其中之一便是冶金自动化。
本文将探讨人工智能在冶金自动化中的应用,并详细介绍其在冶金过程中的具体应用场景和优势。
二、人工智能在冶金自动化中的应用场景1. 生产过程优化人工智能技术可以通过分析大量的数据,帮助冶金企业优化生产过程。
通过对冶金生产过程中的各种参数进行实时监测和分析,人工智能系统可以自动调整生产参数,提高生产效率和产品质量。
例如,通过人工智能系统对冶炼过程中温度、压力、流量等参数的实时监测和分析,可以实现精确控制,提高冶金产品的质量和产量。
2. 故障预测与维护人工智能技术可以通过对设备传感器数据的实时监测和分析,预测设备故障,并提前采取维护措施。
通过建立故障预测模型,人工智能系统可以根据设备的运行状态和历史数据,预测设备故障的可能性,并提醒相关人员采取相应的维护措施。
这样可以减少设备故障对生产过程的影响,提高生产的稳定性和可靠性。
3. 质量控制人工智能技术可以通过对产品质量数据的实时监测和分析,实现质量控制的自动化。
通过建立质量预测模型,人工智能系统可以根据生产过程中的各种参数,预测产品的质量,并自动调整生产参数,以实现产品质量的稳定控制。
这样可以减少人为因素对产品质量的影响,提高产品的一致性和稳定性。
4. 能源消耗优化人工智能技术可以通过对能源消耗数据的实时监测和分析,优化能源的使用效率。
通过建立能源消耗预测模型,人工智能系统可以根据生产过程中的各种参数,预测能源消耗的趋势,并自动调整生产参数,以实现能源消耗的最优化。
这样可以减少能源的浪费,降低生产成本,提高企业的竞争力。
三、人工智能在冶金自动化中的优势1. 数据分析能力强人工智能技术可以通过对大量的数据进行分析,提取出有用的信息,为冶金企业提供决策支持。
- 1、下载文档前请自行甄别文档内容的完整性,平台不提供额外的编辑、内容补充、找答案等附加服务。
- 2、"仅部分预览"的文档,不可在线预览部分如存在完整性等问题,可反馈申请退款(可完整预览的文档不适用该条件!)。
- 3、如文档侵犯您的权益,请联系客服反馈,我们会尽快为您处理(人工客服工作时间:9:00-18:30)。
ZYF-602冶金过程分析检测系统
武汉正元自动化仪表有限公司
一、研究背景
ZY-602系列冶金过程分析系统是专业为冶金行业的转炉煤气回收过程、高炉喷煤过程、高炉炉顶、重力除尘、以及各种工业煤气气柜等设备所配套的成套在线过程分析系统,是以在线气体自动分析仪器为核心,运用现代传感器技术、自动测量技术、自动控制技术、计算应用技术以及相关的专业分析田间和通讯网络所组成的新一代工业在线分析气体分析系统。
ZY-602系列冶金过程分析监测系统适用于钢铁、化工、煤气化、生物气化等领域,测量焦炉煤气、高炉煤气、转炉煤气、混合煤气、发生炉煤气、生物燃气等可燃气体的热值和不同成分的体积浓度。
转炉煤气分析系统(CO、O2)
高炉煤气分析系统(CO、CO2、H2)
焦炉煤气分析流程(O2)
煤粉制备、高炉喷煤分析系统(CO、O2)
干熄焦分析系统(H2、O2、CO、CO2)
二、技术指标
样气处理系统技术指标
●全不锈钢取样探头运行时问≥5年,且免维护
●经处理后洁净样气含尘粒度≤03Μμm
●系统滞后时问≤4min(管线长度≤50水)
●系统单线连续采样在线运行时问≤24小时
●过滤装置不更换时间≥3年
●所有取样过滤装置均为全不锈钢焊接,完全免维护
分析系统技术指标
分析系统检测量程
CO:0-75%(红外检测)
CO2:0-25%(红外检测)
H2:0-75%(热导检测)
CH4:0-40%(可选)(红外检测)
N2:0-100%(归一法)
零漂≤±1.0%,周SF★线性度≤±1.0%周SF
重复性≤±l.0%,周SF★灵敏度≤±0.5%
环境温度:+5–45℃:
输出信号:标准电流4-20mA信号
数据通迅:PROFIBUS、ETHERNET
报警状态信号:光源干接点
技术指标
三、主要特点
●采用国际先进、具有自主知识产权的NDIR非分光红外和TCD热导气体分析
技术
●一台仪器同时测量燃气中CO、CO2、CH4、H2、O2、CnHm六种气体的体积浓
度
●能够自动计算、显示煤气的热值,热值单位Kcal/m3和MJ/m3可以自由切
换
●测量CnHm浓度,保证焦炉煤气、混合煤气、发生炉煤气、秸秆燃气等气体
热值的准确性
●CnHm气体对CH4测量结果无干扰,能够精确测量CH4的浓度
●CO、CO2、CH4以及对H2测量结果无干扰
●气体采样流量变化对H2热导传感器测量结果无影响
●中、英文软件操作界面,并且可以自由切换
●具备RS-232数字输出和4-20mA模拟输出接口
●内置进口调零气象,可以实现空气自动调零
●可选配预处理装置,可以实现7d*24h模式连续不间断测试
四、主要应用
高炉工艺点及系统选型表
高炉喷煤工艺点及系统选型表
转炉工艺点及系统选型表.
焦炉、兰炭炉工艺点及系统选型表
干熄焦工艺点及系统选型表
燃气厂、动力厂、冷轧、热轧、连铸厂工艺点及系统选型表
五、注意事项
使用本产品注意以下事项:
请在所规定的环境条件下使用,避免阳光直射和有水滴滴到仪器上; 请在不含腐蚀性气体的环境下使用;
请避免放置在大功率用电装置的附近;
请避免撞击及强烈振动;
请不要用湿手操作设备;
请将仪器外壳可靠接地。