供应链设计与管理第一章
供应链设计与管理:概念、战略与案例研究++课后答案
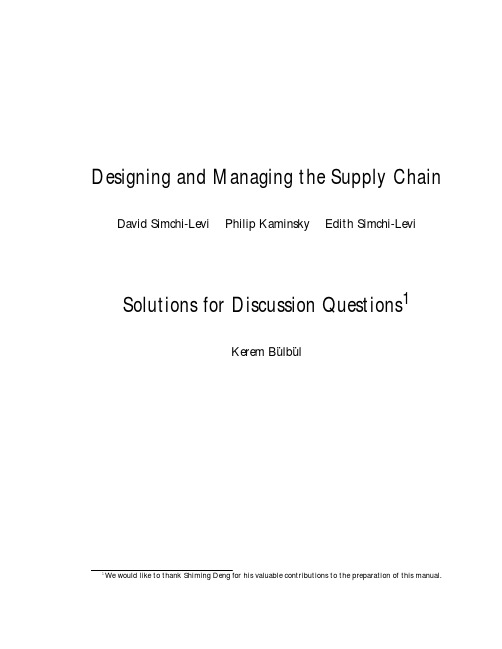
Designing and Managing the Supply Chain David Simchi-Levi Philip Kaminsky Edith Simchi-LeviSolutions for Discussion Questions1Kerem B¨u lb¨u l1We would like to thank Shiming Deng for his valuable contributions to the preparation of this manual.Chapter1Introduction to Supply Chain ManagementDiscussion QuestionsQuestion1Pick any car model manufactured by a domestic auto maker.For example,consider the 2002Ford Thunderbird.a.The supply chain for a car typically includes the following components:1.Suppliers for raw materials2.Suppliers for parts and subsystems3.Automobile manufacturer(Ford,in this example).Within a company,there are alsodifferent departments,which constitute the internal supply chain:i.Purchasing and material handingii.Manufacturingiii.Marketing,etc.4.Transportation providers5.Automobile dealersb.ManyÞrms are involved in the supply chain.1.Raw material suppliers.For instance,suppliers for steel,rubber,plastics,etc.2.Parts suppliers.For instance,suppliers for engines,steering wheels,seats,and elec-tronic components,etc.3.Automobile manufacturer.For instance,Ford.4.Transportation providers.For instance,shippers,trucking companies,railroads,etc.5.Automobile dealers.For example,Hayward Ford.c.All companies involved in the supply chain want to maximize their respective proÞtsby increasing revenue and decreasing cost.However,companies may employ differentstrategies in order to achieve this goal.Some of them focus on customer satisfaction and quick delivery,while others may be more concerned about minimizing inventory holding costs.d.In general,different parts of the supply chain have objectives that are not aligned witheach other.1.Purchasing:Stable order quantities,ßexible delivery lead times and little variationin mix.2.Manufacturing:Long production runs,high quality,high productivity and low pro-duction costs.3.Warehousing:Low inventory,reduced transportation costs and quick replenishmentcapability.4.Customers:Short order lead times,a large variety of products and low prices.Typically,the automobile dealer would like to offer a variety of car colors and conÞg-urations to accommodate different customer preferences,and meanwhile have a short delivery lead time from the manufacturer.However,in order to maximize the length of production runs,and utilize resources more efficiently,the manufacturer would like to aggregate orders from different dealers and offer less variety in car conÞgurations.This is a clear example of conßicting marketing and manufacturing goals.Question2a.The supply chain for a consumer mortgage offered by a bank may involve various com-ponents:1.Marketing companies that handle solicitation to potential customers.2.Credit reporting agencies that evaluate potential customers.3.The bank that extends the mortgage loans.4.Mortgage brokers through which the loans are distributed.b.The marketing companies strive to increase the response rate from homebuyers in orderto maximize their returns.Banks aim at a customer portfolio with a relatively low risk, healthyßow of payments and low average loan maturity date.The brokers would like to maximize their sales commissions.c.Similar to product supply chains,the objective of a service supply chain is to providewhat is needed(in this case a particular type of service,rather than a physical product) at the right location,at the right time,and in a form that conforms to customer require-ments while minimizing systemwide costs.However,there are a number of differences between the two types of supply chains.For instance:1.In a product supply chain,there is both aßow of information and physical products.In a service supply chain,it is primarily information.2.Contrary to a service supply chain,transportation and inventory are major costcomponents in a product supply chain.3.Services typically cannot be held in inventory,so matching capacity with demand isfrequently more important in a service supply chain.4.In a service supply chain,the(explicit)cost of information is higher than in a productsupply chain.Note that in the mortgage example above,the bank has to compensate the credit reporting agency for each credit report it obtains.Question3Many supply chains evolve over time.For example,consider a memory chip supply chain. Production strategies may change during different stages of the product life cycle.When a new memory chip is introduced,price is high,yield is low,and production capacity is tight,and the availability of the product is important.Consequently,production is usually done at plants close to markets,and the management focuses on increasing yield, reducing the number of production disruptions,and fully utilizing capacity.When the product matures,however,its price drops and demand is stabilized for a period of time, so minimizing production cost moves to center stage.To reduce costs,production may be outsourced to overseas foundries,where labor and materials are much cheaper. Question4A vertically integrated company aims at tighter interaction among various business com-ponents,and frequently manages them centrally.Such a structure helps to achieve sys-temwide goals more easily by removing conßicts among different parts of the supply chain through central decision making.In a horizontally integrated company,there is frequently no beneÞt in coordinating the supply chains of each business within the company.Indeed, if every business specializes in its core function,and operates optimally,an overall global optimum may be approached.Question5Effective supply chain management is also important for vertically integrated companies. In such an organizational structure,various business functions are handled by different departments of the company that usually have different internal objectives,and these objectives are not necessarily aligned with each other.This may be due to lack of com-munication among departments or the incentives provided by the upper management.For instance,if the sales department is evaluated based on revenue only,and the manufacturing department is evaluated based on cost only,the company’s proÞt may not be maximized globally.Effective supply chain management is still necessary to achieve globally optimal operations.Question6The sources of uncertainty in this example include:1.Factors such as weather conditions,diseases,natural disasters cause uncertainty inavailability of raw materials,i.e.,peach crop.2.Uncertain lead times during transportation of crop from theÞeld to the processingfacility may affect the quality of peaches,e.g.,they may get spoiled.3.Processing times in the plant,as well as the subsequent warehousing and transportationtimes are subject to uncertainty.4.Demand is not known in advance.Question7A small number of centrally located warehouses allows aÞrm to take advantage of risk pooling in order to increase service levels and decrease inventory levels and costs.However, outbound transportation cost is typically higher,and delivery lead times are longer.On the other hand,by building a larger number of warehouses closer to the end customers,a Þrm can decrease outbound transportation costs and delivery lead times.However,this type of system will have increased total inventory levels and costs,decreased economies of scale,increases warehousing expenses,and potentially increased inbound transportation expenses.Question8The choice of the particular transportation service depends largely on the types and sizes of products the company wants to transport,the inventory and delivery strategies and the need forßexibility:1.A truckload carrier is better if delivering bulky items or small items in large and stablequantities from warehouses to demand points(stores).A good example is the delivery of groceries from warehouses to supermarkets.Note that in this case we would like the demand to be in increments of full truck loads.2.A package deliveryÞrm is more appropriate if relatively small items are delivered fromthe manufacturer/warehouse directly to the customers.Additionally,a package carrier company offers moreßexibility by different modes of transportation depending on the needs of the individual customers.Question91.High inventory levelsi.Advantages:HighÞll rate(service level)and quick order fulÞllment.ii.Disadvantages:High opportunity cost of capital tied in inventory,danger of price declines over time and obsolescence,need for more warehouse space.2.Low inventory levelsi.Advantages:Low inventory holding and warehousing costs.ii.Disadvantages:Higher risk of shortages and lower service levels.Case Discussion Questions—Meditech SurgicalQuestion1Meditech experiences poor service levels for new products,and inventory levels higher than necessary for all products.Question2There are many causes for these problems:1.Demand is not studied in detail.rmation systems that record and monitor demand and inventory are poorly designed.3.Forecasting errors are not tracked.4.There is a tendency to shift the blame to the customers,e.g.,panic ordering.5.There are built-in delays and monthly buckets in the planning system.6.The planning system ampliÞes small variations in demand.7.Poor communication with customers;Meditech doesn’t typically see end-customer de-mand.Question3The customer service manager is directly exposed to the complaints from the customers. Hence,he is in a good position to gauge the scope of the problems.Other managers do not face the customers,and they do not necessarily focus on their satisfaction. Question41.Recognize that demand is predictable,and establish better forecasting systems andaccountability for forecasts.2.Institute better planning systems to eliminate planning delays;reduce the size of systemtime buckets.3.Alternatively,put assembly within the pull system and eliminate bulk inventory com-pletely.4.Develop and implement better information systems.5.Improve communications with customers.Chapter2Logistics Network ConfigurationDiscussion QuestionsQuestion1The factors that affect the performance of the logistics network are not static,i.e.,they change over time.These factors include demand,product design,various costs in the logistics network,regulations,contracts,etc.The effects of these dynamics need to be evaluated periodically in order to determine whether the existing conÞguration is still satisfactory given the new operating environment.For instance,service level requirements may change due to increased competition which typically means that the lead time to fulÞll customer orders needs to be shortened.This may require theÞrm to redesign its logistic network and build new warehouses that are closer to the end customers.Question2The design of the logistics network is a strategic decision that has long lasting effects and impacts all functions within the company.For the success of such a project,many levels of the organization must be involved:1.Upper Management:The new design must be aligned with the vision and strategic goalsof the company.Additionally,such a project may be costly,so management buy-in is essential to ensure that sufficient resources are devoted to the project.2.Sales and Marketing:Demand forecasts and anticipated changes in product design andofferings affect the network and need the involvement of sales and marketing teams. 3.Manufacturing and Operations:The logistics network design has obvious impact on day-to-day operation of theÞrm.In order for the implementation to succeed,it is essential that the people involved with operating the system on a daily basis are involved in its design.Question3The decision that a single warehouse will be built has been made up-front.Therefore,we only need to focus on the location and capacity of the warehouse,and determine how muchspace should be allocated to each product in the warehouse.The main steps of the analysis are outline below.1.Data collectioni.Location of retail stores,existing warehouses(5warehouses located in Atlanta,Boston,Chicago,Dallas and Los Angeles),manufacturing facilities(a single man-ufacturing facility in San Jose),and suppliers.ii.Candidate locations for the new warehouse.rmation about products,i.e.,their sizes,shapes and volumes.iv.Annual demand(past actuals and future estimates)and service level requirements of the retail stores.v.Transportation rates by available modes.vi.Transportation distances from candidate warehouse locations to retail stores.vii.Handling,storage andÞxed costs associated with warehousing.Fixed costs should be expressed as a function of warehouse capacity.viii.Fixed ordering costs,order frequencies and sizes by product or product family. 2.Data aggregation.Demand needs to be aggregated based on distribution patternsand/or product types.Replace aggregated demand data points by a single customer.3.Mathematical model building.4.Model validation based on existing network structure.5.Selection of a few low cost alternatives based on the mathematical model.i.For theÞnal decision,incorporate qualitative factors that were disregarded in themathematical model,e.g.,speciÞc regulations,environmental factors,etc.ii.Optionally,build a detailed simulation model to evaluate these low cost candidate solutions.6.Decide where to locate the centralized warehouse.With the centralized warehouse,service level will increase(less stock-outs)and inven-tory holding costs will decrease due to risk pooling.Also,Þxed costs associated with ware-housing will typically decrease,and inbound transportation costs from the manufacturing facility to the warehouse should be less than the sum of the previous inbound transporta-tion costs.However,we will incur increased outbound transportation costs from the central warehouse to the retailers.In summary,the essential design trade-offis between trans-portation costs on one hand,and inventory holding costs and service level requirements on the other.Question4a.In automobile manufacturing,cars are usually delivered over land,and demand is con-centrated around major cities.Therefore,we would expect warehouses in this industry to be located near large cities with easy access to freeways and railroads.This would help to reduce the delivery lead time to dealerships in the cities.b.In the pharmaceutical industry,overnight delivery is common.Therefore,proximityto a major airport is a factor that should be considered when choosing a warehouse location.Additionally,for raw material warehouses it is important that these are close to natural resources.c.In the book industry,supplier warehouse locations would be affected by the availabilityof nearby natural resources.d.In the aircraft manufacturing industry,sub-assemblies and parts are delivered by thou-sands of suppliers scattered all over the globe to the manufacturing facilities.Therefore, for these supplier warehouses,by far the most signiÞcant consideration is the ability to ship parts easily and on-time,i.e.,the proximity to railroads,freeways,harbors,etc.In such a capital intensive industry,we would also expect that regulations such as tax breaks have an impact on potential warehouse locations.e.With a large customer base shopping for books on-line,short delivery lead times arecrucial.Therefore,in book distribution,we would expect toÞnd large centralized ware-houses on reasonably priced land and where quick transportation modes are available.f.Furniture manufacturing and distribution depends heavily on manual labor.Therefore,warehouses in this industry should be located close to cities with sufficient labor supply.g.In PC manufacturing,outsourcing from all around the world is common where labor ischeaper and regulations favor the huge investments associated with high-tech manufac-turing.These considerations should be factored in when choosing candidate warehouse locations.Question5In the pharmaceutical industry,we would expect more warehouses closer to the end cus-tomers for short delivery lead times.On the other hand,in the chemical industry there would be fewer centralized warehouses in order to consolidate orders and decrease outbound transportation costs.Question6If we expect that the truck would travel empty on its return route,then TL rate would be higher.Considering the example in Section2.2.2,the probability that the truck comes back empty from Illinois(industrial heartland)to New York is lower than the corresponding probability from New York to Illinois which explains the asymmetric cost structure between these two cities.Question71.Handling Costsbor cost of workers in material handling.ii.Costs of conveyors,fork lifts,automated guided vehicles(AGVs),etc.,used to carry the goods in the warehouse.Note that these costs have two components:variable costs that are linearly proportional to the distances the goods are transported over;and purchasing costs of equipment that are proportional to the daily output required from the material handling system,but in a non-linear way because equipment is purchased in discrete quantities.2.Fixed Costsi.Purchasing or rental cost of land.ii.Cost of maintaining and operating the warehouse building which includes annual depreciation and utility costs.iii.Cost of racks that depend on the capacity of the warehouse.iv.The cost of insurance for the facility.3.Storage Costsi.Opportunity cost of capital tied up in inventory.ii.Cost of price declines while inventory is sitting in the warehouse.Note that this includes the risk of obsolete inventory that needs to be salvaged.Question8An exact optimization technique is guaranteed to provide an optimal solution(if one exists) even if it takes a long time.On the other hand,a heuristic algorithm is a method that willÞnd good solutions to the problem in a reasonable amount of time where the terms “good”and“reasonable”depend on the heuristic and the particular problem instance.(See Bramel and Simchi-Levi(1997).)The choice between an exact optimization technique and a heuristic algorithm for a given problem frequently depends on the trade-offbetween solution quality and solution time.Note that even if a heuristic algorithm(by chance)Þnds the optimal solution to a problem,it cannot conÞrm the optimality of the solution. On the other hand,for many problems there are no known optimal algorithms,so heuristics must be used.Question9Simulation is a popular performance evaluation and modeling tool for complex stochastic systems that cannot be evaluated analytically.A simulation model can closely reßect a real system and mimic its behavior,but it has some drawbacks:simulation is a descriptive tool,i.e.,it cannot provide optimal values for system inputs.It generates,for a given set of inputs,sample outputs from the system that are used to compute statistical estimates of the performance measures.Also,accurate simulation models of large systems require extensive development effort,and typically take a long time to run.Thus,we advocate a two-phase approach to solve difficult logistics problems:e a mathematical optimization model to generate a number of good candidatesolutions,taking into account the most important cost components.e a detailed simulation model to evaluate the candidate solutions generated in theÞrst phase.Chapter3Inventory Management and Risk PoolingDiscussion QuestionsQuestion1Companies can cope with uncertainty by1.keeping safety stock,2.shortening production and order lead times,ing risk pooling strategies,4.delaying product differentiation in the supply chain as much as possible,i.e.,aggre-gating demand for parties upstream of the supply chain,and5.by installing systems to achieve information sharing between suppliers and buyers,thus enabling collaborative demand forecasting.Question2In general,higher inventory levels make it easier to maintain higher service levels.However, modern inventory management techniques may make it possible to increase service levels without increasing inventory levels as much as in the past.Question3The variability in demand increases as the average and the variance of lead time increase. Therefore,for a given service level,inventory levels increase with longer lead times and higher lead time variance.Question4The target service level depends on the mission-criticality of the product.For instance, consider a service parts vendor for equipment for which every hour of down time is veryexpensive.(See Example6-5.)In this case,we would expect the management of the vendor company to specify a service level close to100%.Market conditions also play an important role in determining target service levels.For commodities,we would expect relatively high service levels since customers can switch products easily if they do notÞnd the particular product they look for.However,a lower service level may be acceptable if the product has a clear value differentiation compared to its competitors.For instance,customers of a high-end server that is clearly deemed superior to the rest of the market may be willing to wait for1-2weeks if the manufacturer is out-of-stock.Question5√L has two components.TheÞrst component The reorder level s=L∗AV G+z∗ST D∗L∗AV G covers the expected demand during lead time,and the second component z∗√L is the safety stock that protects against deviations from the expected demand ST D∗during lead time.Therefore,immediately before the order arrives,we expect that theÞrst√L.Then,whencomponent is depleted completely and the inventory level is z∗ST D∗√L.an order of Q units arrives,the expected level of inventory is Q+z∗ST D∗Question6In the base-stock policy,at the time the warehouse places an order,this order raises the√r+L.Similar inventory position to the base-stock level(r+L)∗AV G+z∗ST D∗to the reorder level s in the continuous review policy discussed in Question5,this base-stock includes two components:the average demand(r+L)∗AV G until the order arrives√r+L that protects against demand after r+L periods,and the safety stock z∗ST D∗uncertainty during lead time.Thus,just before an order arrives,the expected inventory√r+L.on hand is equal to the safety stock z∗ST D∗In order to determine the expected inventory level right after an order arrives at time t+L,note that when inventory is reviewed at time t,the inventory position is raised to the base-stock level,and an order that was placed at time t−r arrives at time t+L.(SeeFigure3-12.)Therefore,when an order arrives,the expected inventory level is L∗AV G√r+L.units less than the base-stock level,i.e.,is equal to r∗AV G+z∗ST D∗Question7Observe that the longer L1,the more time the system has before allocation of inventory to the retailers need to be made by the cross-dock facility.Thus,the longer L1the more the system can take advantage of the risk pooling concept.Hence,the total amount of inventory is smaller when the cross dock facility is closer to the retail outlet.Question8The answer is not immediately clear because the required safety stock depends both on the average and the variance of the lead time.The retailer would have to make a decision depending on the relative effects of these two factors.See Section3.2.6.Also,your decision would ultimately depend on the requirements of the retailer’s customers.Question9For a mature product,it is reasonable to expect that the price and demand are stable in the short term.However,as the time horizon gets longer,and new products are in-troduced into the market,the demand and price for this particular product decrease and excessive inventories may have to be written off.Thus,inventory holding costs related to obsolescence may be regarded asÞxed in the short term,but not in the long term.Some storage costs are another example of inventory related costsÞxed in the short term,but variable in the long term.For instance,due to large inventories a company may have to rent multiple warehouses for aÞxed lease term.However,if inventory policies are improved and turnover rates are increased in this period of time,then it may be possible to rent fewer warehouses when renewing the lease contracts.Clearly,similar arguments can be made for material handling equipment,storage racks,insurance,personnel,etc. Question10Such deterministic models can be used as proxies for the more realistic stochastic models if the planning horizon is short,and the parameters of the problem are expected to be relatively stable over this time frame.However,most importantly,simple models can illustrate the basic trade-offs in a given type of problem which also translate into more realistic and complex situations.For instance,the optimal policy for the economic lot sizing model balances ordering and inventory holding costs which is a general insight for more sophisticated systems as well.Question11There are implicit and explicit penalties associated with a highly variable demand.For instance:1.As discussed in Sections3.2.5to3.2.7,the level of safety stock is proportional to thevariability in demand,i.e.,the higher the variability in demand the higher the inventory holding costs.2.From a manufacturer’s perspective,highly variable demand means that utilization ofequipment will greatlyßuctuate,and equipment will sit idle when demand is low.3.From a managerial perspective,high variability makes planning a very complex taskthat requires additional resources,sophisticated models and tools.On the other hand,if a company is successful at implementing strategies to cope with high variability in demand,it may be possible to leverage on these to increase market share and/or revenue if the competitors are not as successful.Question12The factors that affect the choice of the supply contract type include the following:1.Business convention:Companies tend to choose the contract form that is most commonin their type of business.rmation availability:The type of information available may dictate what type ofcontract can be implemented in practice.Depending on the contract type,suppliers and buyers require access to different types of information,and some information may be difficult for the supplier to acquire but easier for the retailer,or vice versa.3.Decision making and incentives:To achieve the optimal proÞt for the whole system andto allocate it properly,both suppliers and retailers must understand that decisions must be made collaboratively.All parties must be aware that they have to give up part of the control in their individual systems,and the choice of the supply contract type depends on the level of control that parties are willing to share with each other.1.Buy-back contracts:i.Advantages:(a)Commonly used in many businesses.(b)The coordinating prices are not very sensitive to the demand distribution.ii.Disadvantages:(a)The supplier may have to buy back a large quantity of the product when demandis low.(b)Extra transportation and re-stocking costs for returned items.2.Revenue-sharing contracts:1.Advantages:(a)Easy to understand.(b)The optimal values of the decision variables are not very sensitive to the demanddistribution.2.Disadvantages:(a)Need to monitor the total revenue.3.Quantity-ßexible contracts:i.Advantages:(a)Commonly used in many businesses.ii.Disadvantages:(a)The optimal values of the decision variables are sensitive to the demand distri-bution.(b)Extra transportation and re-stocking costs for returned items.4.Sale-rebate contracts:i.Advantages:(a)It is a direct incentive to the retailer to increase sales.ii.Disadvantages:(a)Difficult to track and implement.。
供应链管理中的产品设计与选型

供应链管理中的产品设计与选型第一章:引言在当今全球化的时代,企业面临越来越激烈的竞争。
供应链管理被提出作为企业竞争力的重要组成部分。
产品设计与选型是供应链的重要环节之一,影响着企业的产品质量、成本和市场竞争力。
本文将讨论供应链管理中产品设计与选型的重要性,并分析如何进行产品设计与选型的策略。
第二章:供应链管理中的产品设计与选型1. 产品设计产品设计是指将产品想法转化为实际成品的过程,包括产品定位、功能设计、结构设计、外观设计等环节。
在供应链管理中,产品设计应结合供应商和客户需求,考虑生产工艺、成本和市场竞争等因素。
2. 选型选型是指在产品设计的基础上,根据功能需求和使用环境,选择适合的材料、器件和技术。
选型应考虑产品的质量、成本、可靠性、可扩展性和维护性等因素,同时也涉及到供应商的选择和合作。
第三章:重视产品设计与选型的重要性1. 提高产品质量优秀的产品设计和选型可以提高产品的质量,减少产品瑕疵和不良率,增强产品的稳定性和耐用性,提高用户的满意度和口碑。
优秀的产品设计也可以提高生产效率和工艺水平,实现产能提升和成本降低。
2. 强化市场竞争力在市场竞争日益激烈的环境中,企业需要通过不断创新和优化产品来满足客户需求,拓展市场占有率。
优秀的产品设计和选型可以提高产品的性能和差异化,吸引更多客户和合作伙伴,赢得市场竞争优势。
3. 实现供应链优化在供应链管理中,产品设计与选型需要与供应商和客户紧密协作,共同优化供应链。
选型可以促进供应商间的竞争和协作,实现材料和零部件的优化利用,同时也可以降低库存成本和运输成本,提高供应链的效率和可靠性。
第四章:如何进行产品设计与选型的策略1. 产品策略产品策略应注重产品的市场需求、客户需求和竞争力分析。
在产品设计中应注意产品的价值、品质和差异化,避免进行无意义和无效的技术创新。
同时应根据产品寿命周期来不断完善和升级产品。
2. 选型策略选型应考虑生产成本、供应商选择和技术可行性等因素,注重产品的可靠性、扩展性和维护性。
供应链管理战略规划与运营

供应链的决策阶段
• 根据作出决策的频率和一个决策所起作 用的持续时间,可以把这些决策分为三 类或三个阶段:
– 供应链战略或设计 – 供应链规划 – 供应链运营
供应链的决策阶段
• 供应链战略或设计
– 在这个阶段,公司要决定如何构建供应链,即确定供应链 的结构和每个环节必须的流程。
– 公司作出的战略性决策包括:生产地点、生产能力、仓储 设施、在不同地点生产或储存的产品、沿不同线路的运输 方式、使用信息系统的类型等决策。
补充库存环节
• 补充库存环节发生在零售商和分销商之 间的界面上,包括补充零售商品库存清 单所涉及的所有过程:
– 零售订货发起 – 零售订单递交 – 零售订单完成 – 零售订货接收
补充库存环节
• 零售订货发起:当零售商满足顾客需求时,他们清空库存 并补充新的货品以满足未来需求。此时,零售商需要设计 一项补充或征订货物的策略。零售订货发起过程的结果是 补充库存订单产生。
生产环节
• 典型的生产环节发生在分销商(或零售商)与制 造商之间的界面上,并包括与更新分销商(或零 售商)库存有关的所有过程。
• 生产环节由顾客订单、补充库存订单或者顾客需 求预测与厂家成品库存数量之间的差额启动。
• 生产环节包括以下过程:
– 分销商、零售商或顾客订单到达; – 生产安排; – 生产和运输; – 货物送达分销商、零售商或顾客。
什么是供应链
注意2:
• 供应链是一个动态系统,它包括不同环节之 间持续不断的信息流、产品流和资金流。供 应链的每个环节都执行不同的程序,并与其 他环节相互作用与影响。
– 沃尔玛向顾客提供信息,同时标出商品价格与使用信息,顾客向沃尔玛支 付货款。
– 沃尔玛将售场信息及补充订单传给分销中心,分销中心将补充订单随送货 车返还给沃尔玛店,然后沃尔玛店将货款转给分销商,分销商又向沃尔玛 提供价格信息和送货日程。
供应链设计与管理——概念战略与案例研究
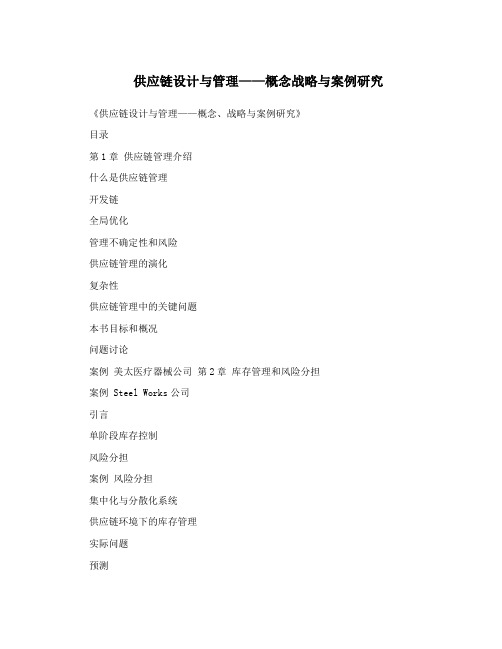
供应链设计与管理——概念战略与案例研究《供应链设计与管理——概念、战略与案例研究》目录第1章供应链管理介绍什么是供应链管理开发链全局优化管理不确定性和风险供应链管理的演化复杂性供应链管理中的关键问题本书目标和概况问题讨论案例美太医疗器械公司第2章库存管理和风险分担案例 Steel Works公司引言单阶段库存控制风险分担案例风险分担集中化与分散化系统供应链环境下的库存管理实际问题预测小结问题讨论案例斯波特?奥波米耶公司第3章物流网络规划案例比斯公司引言网络设计库存策略与物流配置网络的协调案例 ElecComp公司资源配置小结问题讨论案例 H(C(斯塔克有限公司第4章供应合同1案例美国工具厂引言战略性元件面向库存生产,面向订单生产供应链的合同信息不对称下的合同非战略性元件合同小结问题讨论第5章信息价值案例巴里拉公司(A)引言牛鞭效应信息共享和激励机制有效预测协调系统的信息找出所需产品缩短提前期信息和供应链的权衡信息的边际价值递减小结问题讨论案例锐步销售国家橄榄球联盟的球衣第6章供应链整合案例戴尔有限公司引言推动、拉动和推—拉式系统提前期的影响需求驱动战略互联网对供应链战略的影响小结问题讨论案例大的库存修正第7章配送战略案例亚马逊网上商店的欧洲配送战略引言直接装运配送战略转运战略调运2选择合适战略小结问题讨论第8章战略联盟案例金佰利克拉克公司如何使客户好市多持有库存引言战略联盟的框架第三方物流零售商—供应商伙伴关系分销商一体化小结问题讨论案例音像复制服务公司案例史密斯集团第9章采购及外包战略案例 Zara公司引言外包的收益和风险采购,制造决策框架采购战略电子采购小结问题讨论案例旭电公司:从制造商到全球供应链整合者第10章全球物流与风险管理案例沃尔玛为迎合当地的消费习惯而改变策略引言风险管理全球供应链管理中的问题物流的地区差异小结问题讨论第11章协调的产品和供应链设计案例惠普台式喷墨打印机的供应链一个总体框架物流设计供应商参与新产品开发大规模定制小结3问题讨论案例惠普公司:针对大学的网络打印机设计第12章顾客价值案例量身定制引言顾客价值的维度顾客价值评估信息技术和顾客价值小结问题讨论第13章智能定价案例星巴克的经营哲学:揭秘难以捉摸的小杯装卡布基诺引言价格与需求降价价格差异化收益管理智能定价互联网的影响注意事项小结问题讨论案例回扣投诉的含糊回应第14章信息技术和业务流程案例供应链的快速转变引言业务流程的重要性供应链信息技术的目标案例 7—11公司利用先进的技术进行备货供应链管理系统的组件销售和运营计划案例 Adtran的S&OP演变过程集成供应链信息技术小结问题讨论第15章技术标准案例 IBM公司的SOA解决方案使Pacorini集团在全球物流市场中处于领先位置引言4信息技术标准信息技术基础设施面向服务的架构无线射频识别小结问题讨论附录A 电脑啤酒游戏附录B 风险分担游戏附录C 库存电子表格附录D 投标游戏参考文献5。
供应链管理(第5版)课后习题答案
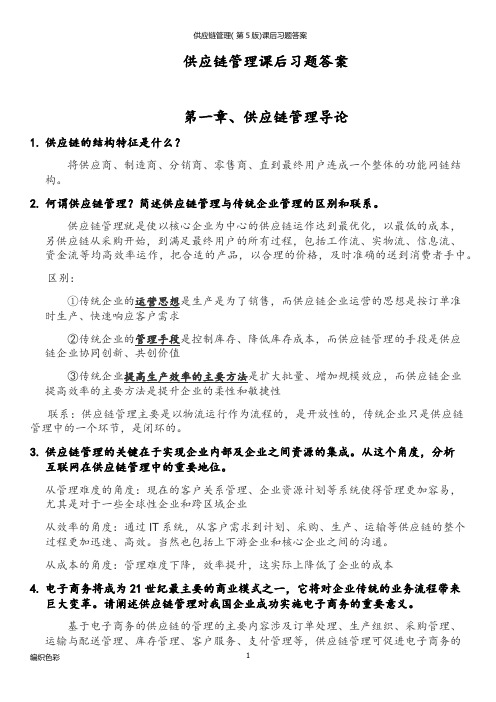
供应链管理课后习题答案第一章、供应链管理导论1.供应链的结构特征是什么?将供应商、制造商、分销商、零售商、直到最终用户连成一个整体的功能网链结构。
2.何谓供应链管理?简述供应链管理与传统企业管理的区别和联系。
供应链管理就是使以核心企业为中心的供应链运作达到最优化,以最低的成本,另供应链从采购开始,到满足最终用户的所有过程,包括工作流、实物流、信息流、资金流等均高效率运作,把合适的产品,以合理的价格,及时准确的送到消费者手中。
区别:①传统企业的运营思想是生产是为了销售,而供应链企业运营的思想是按订单准时生产、快速响应客户需求②传统企业的管理手段是控制库存、降低库存成本,而供应链管理的手段是供应链企业协同创新、共创价值③传统企业提高生产效率的主要方法是扩大批量、增加规模效应,而供应链企业提高效率的主要方法是提升企业的柔性和敏捷性联系:供应链管理主要是以物流运行作为流程的,是开放性的,传统企业只是供应链管理中的一个环节,是闭环的。
3.供应链管理的关键在于实现企业内部及企业之间资源的集成。
从这个角度,分析互联网在供应链管理中的重要地位。
从管理难度的角度:现在的客户关系管理、企业资源计划等系统使得管理更加容易,尤其是对于一些全球性企业和跨区域企业从效率的角度:通过IT系统,从客户需求到计划、采购、生产、运输等供应链的整个过程更加迅速、高效。
当然也包括上下游企业和核心企业之间的沟通。
从成本的角度:管理难度下降,效率提升,这实际上降低了企业的成本4.电子商务将成为21世纪最主要的商业模式之一,它将对企业传统的业务流程带来巨大变革。
请阐述供应链管理对我国企业成功实施电子商务的重要意义。
基于电子商务的供应链的管理的主要内容涉及订单处理、生产组织、采购管理、运输与配送管理、库存管理、客户服务、支付管理等,供应链管理可促进电子商务的发展,使资源在供应链网络中合理流动,来缩短交货周期、降低库存,并且通过提供自助交易的自助式服务以降低成本,提高速度和精确性,增强企业竞争力。
供应链管理基础理论概述
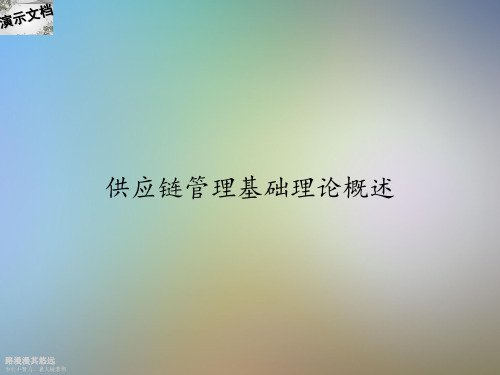
1.2 供应链管理的产生
1.2.1 供应链管理产生的必然性 1.市场需求的变化 2.竞争环境的变化 3.传统管理模式的弊端
1.2 供应链管理的产生
1.2.2 供应链管理产生的可行性 1.信息技术和互联网的发展 2.经济一体化和全球化的形成 3.物流技术与物流管理的发展 4.企业内部管理观念的转变
1.1 供应链的基本概念
1.1.2 供应链的特征 1.复杂性。 2.动态性。 3.市场性。 4.相对性。 5.增值性。 6.风险性。
1.1 供应链的基本概念
1.1.3 供应链的分类 1.内部供应链和外部供应链
内部供应链是指企业内部产品生产和流通过程中 所涉及的采购部门、生产部门、仓储部门、销售部门 等组成的供需网络。
不匹配 匹配
2.3 供应链的设计
3.设计步骤
(1)分析市场竞争环境(2)分析、总结企业现状 (3)提出供应链设计项目,确立供应链设计目标。 (4)分析供应链的组成 (5)分析和评价供应链设计的技术可能性 (6)设计供应链(7)检验供应链
Hale Waihona Puke 2.3 供应链的设计供应链管理基础理论概述
路漫漫其悠远
少壮不努力,老大徒悲伤
第一章 供应链管理基础理论
1.1 供应链的基本概念 1.2 供应链管理的产生 1.3 供应链管理的概念和内涵
1.1 供应链的基本概念
1.1.1 供应链的概念 1.国外关于供应链的定义
(1)美国物流专家马丁·克里斯多夫教 授
(2)美国供应链协会 (3)全球供应链论坛 (4)美国的史蒂文斯
外部供应链是指涵盖企业的并与企业相关的产品 生产和流通过程中所涉及的供应商、生产商、储运商、 零售商以及最终消费者所组成的供需网络。
供应链设计与管理期末复习
Overton Travel Group公司如何预计它的再订购成本和持有成本呢?
03
案例
*
一年的订货次数是12×100=1200(次) 再订购成本包括一次订货中所发生的所有费用,即 工资=16000÷1200=13.33(英镑/次) 雇用成本=3000÷1200=2.50(英镑/次) 花费=6200÷1200=5.17(英镑/次) 检查费=15(英镑/次) 所以再订购成本为13.33+2.50+5.17+15=36 (英镑/次) 持有成本包括持有存货中发生的所有费用,即 借钱的成本=9% 过期率=5% 保险和税费=4% 所以持有成本是年存货的9%+5%+4%=18%
在上述案例中,提前期是2周,存货周期是50/20=2.5周。
假设提前期增加到3周
再订购水平=提前期×需求=LD=3×20=60
但问题是存货水平从没有真正达到60单位,而是在0~50之间变化。
问题
提前期比存货周期短
订货时机
问题
*
再订购水平包括仓库中的存货和在途存货,那么再订购水平就等于前置期的需求减去订单中的货物。 在上述案例中,订购量是50单位,所以在发出另一个订单时,3周的提前期中还有50单位未到达的订货,那么此时的再订购水平为: 再订购水平=提前期需求-在途存货=LD-Q=3×20-50=10(单位) 所以实际的存货降为10单位时应该订购50单位。因为提前期比存货周期长,将始终有至少有一个未完成的订单。
=50×240+60×240/40+18×40/2
总成本
=单位成本×年需求量+年订货成本+库存持有成本
=12720(英镑/年)
再订购水平=提前期的需求=提前期×需求 ROL=LD
供应链设计与管理完整版电子课件
供应链的构成要素包括供应商、制造商、分销商、零售商和最终用户。其中,供应商提供原材料和零部件;制造商进行产品的生产和加工;分销商负责产品的批发和分销;零售商则将产品直接销售给最终用户。
供应链定义及构成要素
类型
根据不同的分类标准,供应链可以分为多种类型,如按范围划分的企业内部供应链和企业外部供应链;按稳定性划分的稳定供应链和动态供应链;按容量划分的平衡供应链和倾斜供应链;以及按复杂性划分的简单供应链和复杂供应链等。
特点
供应链的特点包括复杂性、动态性、交叉性、面向用户需求以及全球一体化。供应链的复杂性体现在其涉及多个企业和部门,且每个企业和部门都有自己的目标和利益诉求;动态性则体现在市场环境的变化和用户需求的不确定性上;交叉性是指供应链中的不同环节之间存在相互影响和制约的关系;面向用户需求则强调供应链应以满足用户需求为出发点和落脚点;全球一体化则反映了全球化背景下供应链的跨国界和跨地域特征。
物联网技术应用
01
03
02
04
智能物流系统构建与实践
THANKS
感谢您的观看。
供应链类型与特点
供应链管理思想及目标
管理思想:供应链管理思想强调以整体最优为目标,通过协调和优化供应链中的各个环节,实现资源的优化配置和高效利用。具体来说,供应链管理思想包括系统观念、合作观念、信息观念和共赢观念。系统观念强调将供应链看作一个整体系统,注重整体效益最大化;合作观念强调供应链中各成员之间的合作与协同,共同应对市场挑战;信息观念强调信息的及时传递和共享,提高决策效率和准确性;共赢观念则强调在追求自身利益的同时,也要关注其他成员的利益诉求,实现共同发展。 目标:供应链管理的目标包括提高客户满意度、降低总成本、缩短交货时间以及提高灵活性等。其中,提高客户满意度是供应链管理的核心目标之一,通过提供优质的产品和服务来满足客户需求;降低总成本则要求通过优化采购、生产、物流等环节来降低整体运营成本;缩短交货时间则要求提高生产和物流效率,缩短从采购到交付的周期;提高灵活性则要求能够快速响应市场变化和客户需求的变化。
供应链管理(高职高专教材)
供应链管理的发展模式
SCM 采购 和供应 观 功 能 分 解 企业 观念 业 务 成就 供 应 链 管 理
流程、功能和组织 集成 SCM 的运 输和物 流观
企 业 观念
业 务 成就
(一)工业采购者的采购与供应观 (二)商业采购者的运输与物流观 (三)供应链管理的集成策略 1.供应链管理的集成策略含义 2.集成化供应链管理策略的目标
前 言
供应链是现代市场兴起的一种重要的市 场主体,供应链管理更是给多家企业带来 的成本更低,服务更高的良好效益。在世 界范围内,许多分散的企业逐渐意识到, 要在竞争激烈的市场中生存下来,必须与 其他企业建立一种战略上的伙伴关系,实 行优势互补,发挥各企业的核心能力,并 且在一种跨企业的集成管理模式下,使各 个企业能够统一协调起来,这样才能够适 应新的环境变化。
(二)制造商方面 (1)要求加强信息共享。 (2)要求认识相互的利益。 (3)要求加强过程的控制执行。 (4)要求成立共同的特别工作组。 (5)要求各方承诺/资源共享。 二、供应链的竞争优势 (1)反应回报 (2)关系回报 (3)重组回报
三、供应链管理对企业的驱动力 1.企业发现依靠内部的产能增强,来 改善投资收益越来越困难,供应链管 理提供了时机。 2.经济全球化,世界范围内的国际贸 易和投资的政策性壁垒的减少,国际 运输和通讯成本的持续降低,使得世 界各地的市场变得更加容易进入。
二、供应链的网络结构 (1)物流。实物型态,单向流通。物 料从供方开始,沿着各个环节向需方移 动。物流是供应链上显而易见的物资 流动。 (2)信息流。信息流分为需求信息和 供应信息,这是两个不同流向的信息 流。 (3)资金流。货币型态,单向流通, 物料是有价值的,物料的流动引发资金 的流动。
供应链管理复习资料
供应链管理复习资料第⼀章⼀.供应链的概念供应链是围绕核⼼企业,通过对信息流、物流、资⾦流的控制,从采购原材料开始,制成中间产品以及最终产品,最后由销售⽹络把产品送到消费者⼿中的将供应商、制造商、分销商、零售商,直到最终⽤户连成⼀个整体的功能⽹链结构。
⼆.什么是供应链管理供应链管理就是使以核⼼企业为中⼼的供应链运作达到最优化,以最低的成本,令供应链从采购开始,到满⾜最终客户的所有过程,包括⼯作流、实物流、资⾦流和信息流等均⾼效率地运作,把合适的产品、以合理的价格,及时准确地送到消费者⼿上。
三. 供应链管理战略的主要内容1.制定供应链管理实施战略;2.确定采⽤推动式或拉动式的供应链;3.确定供应链管理信息技术的战略;4.建⽴有效的绩效测量与评价体系;5.把供应链管理看成企业间资源集成的桥梁。
四.制定供应链管理实施战略1.在企业内外同时采取有⼒措施从企业内部来看,主要是发扬团队的合作精神,从企业外部来看,合作概念的发展已拓展到了以前是竞争对⼿之间的合作2.充分发挥信息的作⽤因为市场的急剧变化,故⽽需要掌握⽤户需求的变化和在竞争中知⼰知彼。
3.供应链企业的组成和运⾏从竞争⾛向合作,从互相保密⾛向信息共享,实际上会给企业带来更⼤的利益。
4.计算机、⽹络技术及⼤数据技术的⼴泛应⽤5.⽅法论的指导我们强调要实现全企业的整体集成,对每⼀时期每⼀项具体任务,都应该有明确的规定和指导⽅法。
6.标准和法规的作⽤要强化标准化组织,使其⼯作能不断跟上环境和市场的变化,各种标准能及时演进。
五.推动式和拉动式供应链1.推动式供应链推动式的供应链运作⽅式以制造商为核⼼,产品⽣产出来后从分销商逐级推向⽤户。
分销商和零售商处于被动接受的地位,各个企业之间的集成度较低,通常采⽤提⾼安全库存量的办法应对需求变动,因此整个供应链上的库存量较⾼,对需求变动的响应能⼒较差。
2.拉动式供应链拉动式供应链的驱动⼒产⽣于最终⽤户,整个供应链的集成度较⾼,信息交换迅速,可以根据⽤户的需求实现定制化服务。
- 1、下载文档前请自行甄别文档内容的完整性,平台不提供额外的编辑、内容补充、找答案等附加服务。
- 2、"仅部分预览"的文档,不可在线预览部分如存在完整性等问题,可反馈申请退款(可完整预览的文档不适用该条件!)。
- 3、如文档侵犯您的权益,请联系客服反馈,我们会尽快为您处理(人工客服工作时间:9:00-18:30)。
Source
原材料
Material Flow 物料流程
中转站
分销商 零售商
Supplier
Converter
Distributor
Retailer
顾客
Supplier
供应商
Converter
Distributor
Value-Added Services
End-User
终端用户 增值服务
Consumers
签订合同Biblioteka 订单会自动传输到供应商或 在思科生产系统中计划中
客户
思科产品
思科产品仅配置非常复杂的订单
整合中心
思科的业务在全球只有 三个中心
80%的订单会被配置,并通过 思科的网站上提交
服务
技术支持电话服务,70% 不需要人工干预
1-6
SCM Definition
供应链管理(Supply Chain Management);
Funds/Demand Flow 资金/需求流量
Information Flow 信息流
保养,维护/售后服务流程 Reuse/Maintenance/After Sales Service Flow
1-7
The SCM Network 供应链管理网络
供应商
制造商
仓库和配送中 心
顾客
运输成本 原材料成本
战略重点
产品创新 软件公司
组件生产商
仓储 半导体
合同制造商
操作/经营 全球物流企业
个人电脑公司
经销商
公司和产 品流
平板显示器
其他
元器件分销商
当地装配
客户关系 最终客户 大企业 消费者
研发
制造
装配
分销
销售,服务,支持
1-5
Cisco’s Value Network
思科公司的价值网络
订单
合同制造商建立和 运输60%的货物直 接到客户
制造成本 运输成本
库存成本
FIGURE 1.1: The logistics network 物流网络
1-8
Key Observations 主要意见
Every facility that impacts costs need to be considered每一个影响成本的因素都应该考虑
Suppliers’ suppliers供应商的供应商 Customers’ customers客户的客户
Efficiency and cost-effectiveness(效率和成本效用) throughout the system is required
购原材料和零部件,制造和装配、仓储和库存跟踪,订单输入,订单管理,分 配到所有渠道,最终交付给客户。
供应链协会The Supply Chain Council
1-4
PC Industry Supply Chain个人电脑产业供应链
Tracing back the screen you stare at for the bulk of your time.
Chapter 1
Introduction to Supply Chain Management
供应链管理介绍
1-1
What Is a Supply Chain?
什么是供应链?
Flow of products and services from:
产品和服务流程:
Raw materials manufacturers原料厂家 Intermediate products manufacturers中间产品制造商 End product manufacturers终端产品制造商 Wholesalers批发商 and distributors分销商 and Retailers零售商
无缝的设计和管理,增值过程跨越组织边界,以满足最终客户的真正需求
美国供应管理协会Institute for Supply Management
Managing supply and demand, sourcing 采购raw materials and parts零部件, manufacturing and assembly装配, warehousing 仓储and inventory tracking库存追踪, order entry 订单输入 and order management, distribution across all channels, and delivery to the customer通过供应和需求管理,采
供应链管理是用于有效集成供应商、制造商、仓库与商店的一系列方 法,通过这些方法,使生产出来的商品能以恰当的数量,在恰当的时 间,被送往恰当的地点,从而实现在满足服务水平要求的同时使系统 的成本最小化。
1-3
Two Other Formal Definitions定义
The design and management of seamless, value-added process across organizational boundaries to meet the real needs of the end customer
• Cost and service levels成本和服务水平
1-2
1.1 What Is Supply Chain Management?什么是供应链管理?
Supply chain management is a set of approaches utilized to efficiently integrate suppliers, manufacturers, warehouses, and stores, so that merchandise is produced and distributed at the right quantities, to the right locations, and at the right time, in order to minimize system wide costs while satisfying service level requirements.
• Connected by transportation and storage activities把运输和储存连接在一起
• Integrated through information, planning, and integration activities
• 通过信息,规划和整合活动结合起来