第二章╲t材料的脆性断裂与强
材料的脆性断裂

πc 2σ 2 We = (2.13) E 16 式中,c为裂纹半长;σ 为外加应力;E是弹性模量。
2 2 平面应变状态: 2 πc σ We = (1 - μ ) (2.14) 式中,μ 为泊松比。 E 2)产生新断面所需的表面能 Ws=4cγ (2.15) 式中,γ为单位面积上的断裂表面能,单位为J/m2。 3)裂纹扩展过程中的能量平衡 设裂纹进一步扩展2dc,则单位面积所释放的能量为 dWe/2dc , 形 成 新 的 单 位 表 面 积 所 需 的 表 面 能 为 (dWs/2dc) 。 因此,当 (dWe/2dc) <(dWs/2dc) 时,为稳定状态,裂 纹不会扩展; 当(dWe/2dc) >(dWs/2dc)时,裂纹失稳,迅速扩展; 当(dWe/2dc) =(dWs/2dc)时,为临界状态。
(2.17)
2 Eγ σc = πc 如果是平面应变状态,则为: 2 Eγ σc = (1 - μ 2 ) πc
由此推出的临界应力为:
(2.19)
(2.20)
18
在外载荷作用下,若无外界能源加入, 理解纹开始扩展时,形成裂纹新表面的 能量 W 是由裂纹开裂过程中所释放出 来的弹性应变能 U 所提供的。 W 与 U 都与裂纹半长 c 有关,两者所组成的总 能量称为自由能 E : E=-U+W U 前面的 " - " 表示弹性应变能减少。
(2.5)
将(2.3),(2.4)和(2.5)式代入(2.1)式,得
γ x γ E γ = E = ∴ σ th = σ x a x a
式中,a为晶格常数,随材料而异。
2πx 2 = σ th 2πγ σ th
x γ
(2.6)
7
通常γ 约为aE/100,这样(2.6)式可写成 E aE E σth = = (2.7) a 100 10 一般材料性能的典型数值为:E=300GPa,γ =1J/m2, a=3×10-10m,代入(2.6)式算出
无机材料的脆性断裂与强度..

σ
该理论只考虑了裂纹端部一点的应力
实际上裂纹端部的应力状态很复杂。
Griffith 借鉴上述理论结果,从能量的角度研究了裂 纹扩展的条件:物体内储存的弹性应变能的降低大于等 于由于开裂形成两个新表面所需的表面能,即物体内储 存的弹性应变能的降低(或释放)是裂纹扩展的动力。
三. Griffith理论模型
应等于释放出的弹性应变能,可用图中曲线下所 包围的面积来计算,有:
V
2 0
th
sin
th 2
cos
th
2 x dx
2x 2 0
设材料形成新表面的表面能为 ,则 V ,2 有:
th 2
th
2
在接近平衡位置O的区域,曲线可以用直线代替(弹 性形变),服从虎克定律:
形状有关。
应力场强度因子有如下的特性:
a) 应力场强度因子仅与荷载与裂纹几何 尺寸有关,而与坐标无关。 b)裂纹顶端附近的应力和位移分布,完全 由应力场强度因子来确定。 c) 应力场强度因子是裂纹尖端应力场大小 的比例因子,因为应力分量正比于应力强 度因子。
求KⅠ的关键在于求几何形状因子Y,可以通过实验 得到,也可查询几何形状因子数据手册。
脆性和韧性
脆性、韧性和断裂之间的关系: (1)微裂纹决定了材料的实际断裂强度; (2)断裂韧性因材料种类的不同而有极大的差异 ;
这个差异是由于不同材料中断裂韧性有明显 的不同
(3)材料的断裂韧性低,它的断裂就是脆性断裂。
为什么金属有较好的韧性,而陶瓷和玻璃韧性很差?
因为陶瓷和玻璃材料里有裂纹所形成的应力集中区, 无法产生大量的位错,不像金属那样通过塑性形变 把集中的应力释放掉,裂纹发展得很迅速就显得很 脆。
材料的脆性断裂范文

材料的脆性断裂范文材料的脆性断裂是指在受到应力作用时,材料很快且突然地发生断裂现象。
相比之下,塑性断裂是指材料在受到应力作用时发生塑性变形,即产生塑性流动,直到最终断裂。
脆性断裂通常发生在脆性材料中,例如陶瓷、玻璃和一些金属。
脆性断裂的原因有很多,可以从微观和宏观两个层面进行解释。
首先,从微观层面来看,脆性断裂主要是由于材料中的微观缺陷引起的。
材料中存在各种形式的缺陷,如晶格缺陷、孔洞或裂纹。
当外部应力施加到材料上时,应力集中于缺陷周围,导致局部应力非常高,从而发生断裂。
此外,微观缺陷还可以作为裂纹的起始点,在外部应力的作用下裂纹扩展,最终导致材料的完全破坏。
其次,从宏观层面来看,脆性断裂还与材料的结构和形状有关。
晶体结构的不规则性和结晶缺陷可以导致应力集中,从而增加材料的脆性。
此外,材料的形状和尺寸也会影响脆性断裂的发生。
当材料的粗细比较大时,断裂形式可能更加脆性,因为裂纹的扩展路径更直接。
此外,材料的温度和湿度也会影响脆性断裂的发生。
高温和高湿环境会导致材料内部的微观缺陷扩展和形成新的裂纹,从而加剧脆性断裂的发生。
针对脆性断裂的问题,可以采取一些措施来改善材料的断裂韧性。
首先,加入适量的合金元素可以改变材料的晶界形态,减少晶界裂纹的形成,并增加材料的韧性。
其次,合理控制材料的热处理过程可以调整晶粒大小和组织结构,从而改善材料的韧性。
此外,合理设计材料的形状和尺寸,减少应力集中区域的存在,也可以降低材料的脆性断裂风险。
总之,材料的脆性断裂是由微观缺陷和宏观结构等多种因素共同作用引起的。
了解脆性断裂的原因和机制,可以指导我们采取适当的措施来改善材料的韧性,提高材料的断裂强度和可靠性。
第二章 材料的脆性断裂与强度
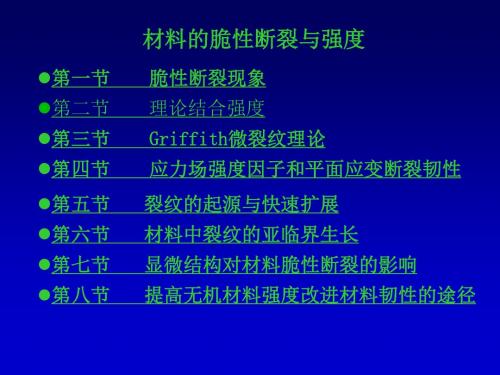
裂纹的三种扩展方式或类型 Ⅰ型(掰开型)张开或拉伸型,裂纹表面直 接分开。
Ⅱ型(错开型)滑开或面内剪切型,两个裂 纹表面在垂直于裂纹前缘的方向上相对滑动。 Ⅲ型(撕开型)外剪切型,两个裂纹表面在
平行于裂纹前缘的方向上相对滑动。
裂纹长度与断裂应力的关系:
等有关的系数.
k c c
1 2
k 是与材料、试件尺寸、形状、受力状态
在接近平衡位置 O 的区域,曲线可以用直线代替,服 从虎克定律:
x E E a
a 为原子间距 x 很小时 sin
因此,得:
2x
2x
th
E a
可见,理论结合强度只与弹性模量,表面能和晶 格距离等材料常数有关。 通常, 约为 aE ,这样,
E th 10
100
五.裂纹扩展的动力和阻力
1.裂纹扩展的动力 Irwin将裂纹扩展单位面积所降低的弹性 应变定义为应变能释放率或裂纹扩展力。 对于有内裂纹 2c 的薄板:
G
d we 2dc
c
E
2
其中 G为裂纹扩展的动力。
对于有内裂的薄板:
K
a c
临界状态:G c K c
E
2
(平面应力状态)
Inglis研究了具有孔洞的板的应力集中问题,得 到结论:孔洞两个端部的应力几乎取决于孔洞的长度 和端部的曲率半径,而与孔洞的形状无关。 Griffith根据弹性理论求得孔洞端部的应力 A
A c a2 1 2 , a c
c A 1 2
式中, 为外加应力。
K
3 xy 2r cos 2 sin 2 cos 2
材料结构与性能(第二章力学性能断裂与强度)

th
E 10
2021/7/12
博学善建 | 厚德大成
断裂强度理论值和测定值
材料
Al2O3晶须 铁晶须 奥氏型钢 硼 硬木 玻璃 NaCl Al2O3刚玉
Th
c
Kg/m
m2
th/ c
5000 1540 3.3
3000 2048 3480 — 693 400 5000
1300 2.3 320 6.4 240 14.5 10.5 — 10.5 66.0 10 40.0 44.1 113
2021/7/12
博学善建 | 厚德大成
Orowan
理论结合强度( Orowan近似)
Orowan以应力—应变正弦函数曲线 的形式近似的描述原子间作用力随原
子间距的变化。 thSin2x
模 型
2021/7/12
原子间约束力和距离间的关系
博学善建 | 厚德大成
断裂功 W 0 2th S2 i x n d x 2 th C2 o x 0 s 2th
• 着眼于裂纹尖端应力集中区域的力场和应 变场分布;
• 研究裂纹生长、扩展最终导致断裂的动态 过程和规律;
• 研究抑制裂纹扩展、防止断裂的条件。 • 给工程设计、合理选材、质量评价提供判
据。
2021/7/12
博学善建 | 厚德大成
断裂理论
§2-6 理论结合强度
固体的强度——固体材料抵抗破坏的能力
– 按破坏形式分:屈服强度 断裂强度
• 考虑裂纹尖端的曲率半径是一个变数,即不等
于r0 ,其一般式为:
c =y ( s E / c )1/2
• y是裂纹的几何(形状)因子。
2021/7/12
博学善建 | 厚德大成
第二章 无机材料的脆性断裂与强度

合力入手
理论结合强度推导
固体的强度都能根据化学 组成、晶体结构与强度之 间的关系来计算,不同材 料有不同的组成、结构、 键合方式 简化
th sin
2x
σth –理论结合强 度(材料原子 间结合力的最 大值)
原子间结合力与距离的关系
将材料拉断时,产生两个新表面,因此使单位面 积的原子平面分开所作的功等于产生两个单位面 积的新表面所需的表面能,材料才能断裂。 th 2x 2 分开单位原子平面所作的功:v th sin dx 0 设材料形成新表面的表面能为,则v 2
当r<<C,θ→0时,即为裂纹尖端处 的一点,则掰开性(I型)裂纹尖端 的应力: K1 xx yy 2r 使裂纹扩展的主要动力是 yy
应力场强度因子 与几何形状因子
K 1 2r A
2 2r
c Y c
Y-几何形状因子。与裂纹形式、试件几 何形状有关。求KI的关键在于求Y 断裂力学的内容:求不同条件下的Y Y也可由实验测定 各种条件下的Y已汇编成册,可供查阅。
裂纹扩展的动力-即裂纹扩展2dc,单位 表面所释放的能量(弹性应变能降低):
dwe c 2 G 2dc E
则:临界状态
Gc
c c 2
E
对有内部裂纹的薄板:
K1 c
2
K1c cc
2
2
K 1c 则: G (平面应力状态) c E 2 2 (1 ) K1c (平面应变状态) Gc E
按照断裂力学观点,提出新的判据
(新设计思想和选材准则)
引入一个考虑裂纹尺寸并表征材料特性的 临界值常数KIC,称为平面应变断裂韧性。
第二章无机材料的断裂与强度_材料物理
能
量
Ws
cc We
亚稳 失稳
裂纹
a 长度
We+Ws
在图中We+ Ws出现了一个极大值点。在极大值点左侧 (c<cc),裂纹不会自动扩大,说明不会发生断裂;在极大值 点右侧(c> cc),裂纹会自动扩大,发生断裂。临界状态 时:
d dW c W e s d d c 4 c c E 2 2 0
临界应力为:
c
2Ec1/2
E1/2
c
平面应变状态:
(2.7)格里菲斯公式
c (12E2)c1/2
脆性材料
将裂纹存在时的断裂强度与理论断裂强度对比,得到
m c
c a0
1/ 2
c a
1/2
(2.8)
上式说明:
裂纹在其两端引起了应力集中,将外加应力
1/2
放大
c a0
倍。
结果使局部地区达到理论强度,而导致断裂。
单边切口梁法(SENB法) 1. 试样形状及尺寸
试件几何形状几受力状态
尺寸比例: c / W=0.4~0.6; W / S=1/4; BW / 2
2. 试样制备
用金刚石内圆切割机切割成长条状试样 打磨抛光
✓ 保证试样受拉表面的光洁度达到7; ✓ 棱角互相垂直,边棱纵向导角45; ✓ 试样高度和宽度在整个试样长度范围内的变化不超过0.2mm。
0
x
2ms
0
in2xdx
m
(2.2)
对无限小的位移, (2.1)式可简化为
m
2x
(2.3)
根据胡克定律
E x
a0
(2.4)
由(2.3)和(2.4)得 2ma0
材料物理性能 第二部分 材料的断裂
脆性断裂 是材料断裂前没有明显的宏观塑性变形,没有明显的迹象,往往
表现为突然发生的快速断裂过程。 根据断裂时应力和时间的关系,断裂大致可以分为两大类: 一类称为瞬时断裂,指的是在以较快的速率持续增大的应
力作用下发生的断裂; 另一类称为延迟断裂,包括材料在以缓慢的速率持续增大
的外力作用下发生的断裂、材料在承受恒定 外力作用一段 时间之后发生的断裂以及以及材料在交变荷载作用一段时 间之后发生的断裂等。延迟断裂有时也称为疲劳断裂
2、Griffith的理论推导 裂纹的存在使得实际材料的断裂强度σC低于理论结合强σth
Griffith从能量平衡的观点出发,认为 裂纹扩展的条件是:物体内储存的弹性 应变能的减小大于或等于开裂形成两个 新表面所需增加的表面能。反之,裂纹 不会扩展。即物体内储存的弹性应变能 的是裂纹扩展的动力
外力力做功 弹性应变能
实际断裂强度c
2 c E
临界情况 c
c
E
4c
裂纹的存在使得实际材料的断裂强度σC低于理论结合强σth。 裂纹扩展条件为:
2
c a
E a
实际材料中存在的微裂纹或缺陷端部处的应力状态比Inglis所 考虑的椭圆孔的情况要复杂 得多。因此,Griffith的微裂纹理 论是从能量的角度出发研究裂纹扩展条件的。
当
<
时为稳态状态,裂纹不会扩展;
反之,为失稳定状态,裂纹发生迅速扩展;
当:
=
则为裂纹扩展的临界状态。
因为:
则,平面应力状态的临界应力为:
c
2E C
平面应变状态的临界应力为:
c
2E (1 u2 )c
Griffith推导的结果与(2.12)基本一致,只系数稍有差别,与 (2.6)理论强度公式类似。(2.6)中a为原子间距,而上式中c 为裂纹半长,可见使a、 c在同一数量级,就可以使材料达到理论 强度
材料物理性能(第二章材料的脆
热膨胀系数
01
热膨胀系数:材料在温度升高时,单位长度的材料会沿温度升高方向 膨胀的长度。
02
热膨胀系数是材料常数之一,与材料的化学成分、晶体结构、微观组 织等有关,不同的脆性材料具有不同的热膨胀系数。
03
热膨胀系数的大小反映了材料受温度变化时尺寸稳定性的好坏,热膨 胀系数越小,尺寸稳定性越好。
脆性材料的热导率一般较小,这是因为脆性材料的晶格结构较为紧密 ,不易传递热量。
电导率
01
电导率:材料中电导电流密度与电场强度之比,反映了材料的 导电性能。
02
电导率的大小与材料的导电性能有关,电导率越大,材料的导
电性能越好。
脆性材料的电导率一般较小,这是因为脆性材料的晶格结构较
03
为紧密,不易传导电子。
脆性材料的弹性模量一般较大 ,这是因为脆性材料在受到外 力作用时不易发生塑性变形。
泊松比
泊松比是材料常数之一,与材料的化学成分、 晶体结构、微观组织等有关,不同的脆性材料
具有不同的泊松比。
脆性材料的泊松比一般较小,这是因为脆性材料在受 到外力作用时不易发生横向变形。
泊松比:材料在单向拉伸或压缩时,横向应变 与轴向应变之比的负值,反映了材料横向变形 的特性。
硬度
总结词
脆性材料的硬度较高,这是因为脆性材料中的原子间相互作用力较强。
详细描述
由于脆性材料中的原子间相互作用力较强,使得其表面硬度较高,不易被划伤 或磨损。
耐磨性
总结词
脆性材料的耐磨性较差,这是因为脆性 材料在摩擦过程中容易发生脆性断裂。
VS
详细描述
脆性材料在摩擦过程中,由于其内部的原 子间相互作用力较弱,容易在摩擦力的作 用下材料的力学性能
第二章材料得脆性断裂与强度
第⼆章材料得脆性断裂与强度第⼆章材料得脆性断裂与强度§2.1 脆性断裂现象⼀、弹、粘、塑性形变在第⼀章中已阐述得⼀些基本概念。
1.弹性形变正应⼒作⽤下产⽣弹性形变,剪彩应⼒作⽤下产⽣弹性畸变。
随着外⼒得移去,这两种形变都会完全恢复。
2.塑性形变就是由于晶粒内部得位错滑移产⽣。
晶体部分将选择最易滑移得系统(当然,对陶瓷材料来说,这些系统为数不多),出现晶粒内部得位错滑移,宏观上表现为材料得塑性形变。
3.粘性形变⽆机材料中得晶界⾮晶相,以及玻璃、有机⾼分⼦材料则会产⽣另⼀种变形,称为粘性流动。
塑性形变与粘性形变就是不可恢复得永久形变。
4.蠕变:当材料长期受载,尤其在⾼温环境中受载,塑性形变及粘性形变将随时间⽽具有不同得速率,这就就是材料得蠕变。
蠕变得后当剪应⼒降低(或温度降低)时,此塑性形变及粘性流动减缓甚⾄终⽌。
蠕变得最终结果:①蠕变终⽌;②蠕变断裂。
⼆.脆性断裂⾏为断裂就是材料得主要破坏形式。
韧性就是材料抵抗断裂得能⼒。
材料得断裂可以根据其断裂前与断裂过程中材料得宏观塑性变形得程度,把断裂分为脆性断裂与韧性断裂。
1.脆性断裂脆性断裂就是材料断裂前基本上不产⽣明显得宏观塑性变形,没有明显预兆,往往表现为突然发⽣得快速断裂过程,因⽽具有很⼤得危险性。
因此,防⽌脆断⼀直就是⼈们研究得重点。
2.韧性断裂韧性断裂就是材料断裂前及断裂过程中产⽣明显宏观塑性变形得断裂过程。
韧性断裂时⼀般裂纹扩展过程较慢,⽽且要消耗⼤量塑性变形能。
⼀些塑性较好得⾦属材料及⾼分⼦材料在室温下得静拉伸断裂具有典型得韧性断裂特征。
3.脆性断裂得原因在外⼒作⽤下,任意⼀个结构单元上主应⼒⾯得拉应⼒⾜够⼤时,尤其在那些⾼度应⼒集中得特征点(例如内部与表⾯得缺陷与裂纹)附近得单元上,所受到得局部拉应⼒为平均应⼒得数倍时,此过分集中得拉应⼒如果超过材料得临界拉应⼒值时,将会产⽣裂纹或缺陷得扩展,导致脆性断裂。
虽然与此同时,由于外⼒引起得平均剪应⼒尚⼩于临界值,不⾜以产⽣明显得塑性变形或粘性流动。
- 1、下载文档前请自行甄别文档内容的完整性,平台不提供额外的编辑、内容补充、找答案等附加服务。
- 2、"仅部分预览"的文档,不可在线预览部分如存在完整性等问题,可反馈申请退款(可完整预览的文档不适用该条件!)。
- 3、如文档侵犯您的权益,请联系客服反馈,我们会尽快为您处理(人工客服工作时间:9:00-18:30)。
裂纹的形成
表面裂纹:一个硬质粒子(如研磨粒子)受到力P的作用 而穿入脆性固体的表面,可能引起局部屈服,塑性形变造 成的残余应力将激发出表面裂纹。
形成于表面加工(切割、研磨、抛光)或粒子冲刷过程。
残余应力 工艺缺陷
侧向裂纹 径向裂纹
材料表面受 研磨粒子损 伤后形成的 裂纹
工艺缺陷包括大孔洞、大晶粒、夹杂物等,形成于材料制 备过程中。与原料的纯度、颗粒尺寸、粒度的分布、颗粒 形貌等有关。
•c) 应力场强度因子是裂纹顶端应力场大小 的比例因子,因为应力分量正比于应力强 度因子。
求 K 的关键在于求Y:
大而薄的板,中心穿透裂纹, Y 大而薄的板,边缘穿透裂纹, Y 1.12 三点弯曲切口梁: s/w=4 时
Y
1.933.07c / w14.5
c/
w
2
25.07
说明,断裂应力受现有的裂纹长度制约
二. 裂纹尖端应力场分布
1957 年 lrwin 欧 文 应 用弹性力学的 应力场理论对 裂纹尖端附近 的应力场进行 了分析,对Ⅰ 型裂纹得到如 下结果(图 2.6)。
K xy
2r
cos
2
1
sin
2
sin
3
2
K yy
2r
cos
2
1
sin
2
sin
断裂力学的分类: 断裂力学根据裂纹尖端塑性区域的范围,分为两大类: (1)线弹性断裂力学---当裂纹尖端塑性区的尺寸远小于 裂纹长度,可根据线弹性理论来分析裂纹扩展行为。 (2)弹塑性断裂力学---当裂纹尖端塑性区尺寸不限于小 范围屈服,而是呈现适量的塑性,以弹塑性理论来处理。
裂纹的三种扩展方式或类型 Ⅰ型(掰开型)张开或拉伸型:裂纹表面直 接分开。 Ⅱ型(错开型)滑开或面内剪切型:两个裂 纹表面在垂直于裂纹前缘的方向上相对滑动。 Ⅲ型(撕开型)外剪切型:两个裂纹表面在
够的外部能量,裂纹扩展将会停止。
因此,在讨论能量平衡时,必须考虑 裂纹在扩展过程中由于塑性变形所引起的 能量消耗,有时这种能量消耗要比所需要 的表面能大很多(几个数量级)。
(4) 控制强度的三个参数
弹性模量E:取决于材料的组分、晶体的结构、 气孔。对其他显微结构较不敏感。
断裂能 f :不仅取决于组分、结构,在很大 程度上受到微观缺陷、显微结构的影响,是一 种织构敏感参数,起着断裂过程的阻力作用。 裂纹半长度c:材料中最危险的缺陷,其作用 在于导致材料内部的局部应力集中,是断裂的 动力因素。
:
K K
c
,所设计的
构件才是安全的,这一判据考虑了裂纹尺寸。
经典强度理论与断裂力学强度理论的比较 ★
经典强度理论 断裂强度理论
断裂准则: f/n
K1 = ( c )½ K1c
有一构件,实际使用应力为1.30GPa,有下列两种钢供 选:
甲钢: f =1.95GPa,
K1c =45Mpa·m 1\2
一. 弹、粘、塑性形变
➢弹性形变(畸变):正应力、剪应力作用下可以恢
复的形变。(一般固体材料) ➢塑性形变:晶粒内部的位错滑移不可恢复的
永久形变(晶体材料)
➢粘性形变:―――不可恢复永久形变(无机材料中非
晶相、玻璃、有机高分子材料、金属材料等)
➢蠕
变:―――在高温条件,上述的塑性形变和
粘性形变将随时间而具有不同的速率。最后发生蠕
设分开单位面积原子平面所作的功为 V ,则
V
2 0
th
sin
2x
dx
th 2
cos
2x 2 0
th
设材料形成新表面的表面能为 (这里是断裂表面 能,不是自由表面能),则 V 2 , 即
th 2
th
2
在接近平衡位置O的区域,曲线可以用直线代替(弹 性形变),服从虎克定律:
ws 4c
式中 为单位面积上的断裂表面能,单位为 J m2。
临界条件的分析: 欲使裂纹扩展,应变能降低的数量应等能
量(应变能的释放率)为 d we; 形成新的单
位表面积所需的表面能为2dcd ws ,因此:
2dc
当 d we < d ws 时,为稳定状态,
三. 突发性断裂与裂纹缓慢生长
裂纹的存在及其扩展行为决定了材料抵抗断裂的 能力。
在临界状态下,当断裂源处裂纹尖端的横向拉应力 =结合强度→裂纹扩展→引起周围应力再分配→裂 纹的加速扩展→突发性断裂。
当裂纹尖端处的横向拉应力尚不足以引起扩展,但在 长期受力情况下(周围高温或腐蚀性气体),会出现 裂纹的缓慢生长。
到结论:孔洞两个端部的应力几乎取决于孔洞的长度
和端部的曲率半径,而与孔洞的形状无关。
Griffith根据弹性理论求得孔洞端部的应力 A
A 1 2 c , a2
a
c
A 1 2
c
式中, 为外加应力。
如果 c ,即为扁平的锐裂纹,则 c 很大,这
时可略去式中括号内的1,得:
2 c
E x E
a
a 为原子间距,
x 很小时,
sin 2x 2x
因此,得:
E
th
a
可见,理论结合强度只与弹性模量,表面能和晶
格距离等材料常数有关。 通常, 约为 aE ,这样, 100
E th 10
要得到高强度的固体,就要求 E 和 大,a 小。
第三节 Griffith微裂纹理论
1920年Griffith为了解释玻璃的理论强度与实际强 度的差异,提出了微裂纹理论,后来逐渐成为脆性断 裂的主要理论基础。
c/w
3
25.8
c/
w
4
图2.7列举出几种情况下的Y值:
四 临界应力场强度因子及断裂韧性
K 反映了裂纹尖端应力场的强度,是决
定弹性材料中裂纹行为的重要力学参数。 ✓1.根据经典强度理论,在设计构件时,
断裂准则是 [ ] ,允许应力 f n
或 ys n , f 为断裂强度; ys 为屈服强度;
c
如果是平面应变状态,
2E
c
1 2 c
Griffith采用钠钙玻璃制成的薄壁圆管作
了实验研究(P45),Griffith的微裂纹理论能 说明脆性断裂的本质――微裂纹扩展。
对于塑性材料,Griffith公式不再适用,
因为塑性材料在微裂纹扩展过程中裂纹尖端
的局部区域要发生不可忽略的塑性形变,需
要不断消耗能量,如果不能供给所需要的足
裂纹不会扩2d展c ; 2dc
当 d we > d ws时,裂纹失稳,扩展;
2dc
2dc
当
d we
2dc
=
d ws
2dc
时,为临界状态。
w 又因为
d e
2dc
=
d
c2
2dc E
2
c
E
2
d ws d 4c 2
2dc 2dc
因此,临界条件为: 2 c 2 E
临界应力:
2E
c
第二节 理论结合强度
要推导材料的理论强度,应从原子间的结合力入 手,只有克服了原子间的结合力,材料才能断裂。
Orowan(奥罗万)提出了以正弦曲线来近似原子间 约束力随原子间的距离X的变化曲线(见图2.1)。
得出:
sin
th
2
式中, th为理论结合强度, 为正弦曲线的波长。
材料断裂时,将产生两个新表面;使单位面积原子平 面分开所做的功等于产生两个新表面所需的表面能。
A
当
A
,th
裂纹扩
展, c 增大 增A
加断裂 。
二. 裂纹扩展的临界条件
2
c E
ca
a
E c 4c
➢ 1. Inglis只考虑了裂纹端部一点的应力,实际上裂 纹端部的应力状态很复杂。
➢ 2. Griffith从能量的角度研究裂纹扩展的条件:物体 内储存的弹性应变能的降低大于、等于由于开裂
K
xx
yy 2 r
yy是裂纹扩展的主要动力
三. 应力场强度因子及几何形状因子
将 yy 换成 A r c
K 2r 2 2 r c Y c
A
K 是反映裂纹间断应力场强度的强度因子,
Y 为几何形状因子,它和裂纹型式,试件几何
形状有关。
应力场强度因子有如下的特性: •a) 应力场强度因子仅与荷载与裂纹几何尺 寸有关,而与坐标无关。 •b)裂纹顶端附近的应力和位移分布,完全 由应力场强度因子来确定。
乙钢: f =1.56GPa,
K1c =75Mpa·m 1\2
传统设计:甲钢的安全系数: 1.5, 乙钢的安全系数 1.2
断裂力学观点: 最大裂纹尺寸为1mm, Y=1.5
甲钢的断裂应力为: =1.0GPa
乙钢的断裂应力为: = 1.67GPa
五.裂纹扩展的动力和阻力
1.裂纹扩展的动力
Irwin将裂纹扩展单位面积所降低的弹性
第二章 材料的脆性断裂与强度
第一节 脆性断裂现象 第二节 理论结合强度 第三节 Griffith微裂纹理论 第四节 应力场强度因子和平面应变断裂韧性 第五节 裂纹的起源与快速扩展 第六节 材料中裂纹的亚临界生长 第七节 显微结构对材料脆性断裂的影响 第八节 提高无机材料强度改进材料韧性的途径
第一节 脆性断裂现象
(平面应力状态)
K c
2E
2
1
(平面应变状态)
K c 与材料本征参数 E、、 等物理
量有关,它 反映了具有裂纹的材料对外界 作用的一种抵抗能力,也可以说是阻止裂 纹扩展的能力,是材料的固有性质。
3
2
K cos sin cos 3
xy 2r 2 2 2
式中 K 与外加应力,裂纹长度,裂纹种类和受力 1