汽车车身钣金件料厚的方向及设计规定
钣金类产品设计的基本原则
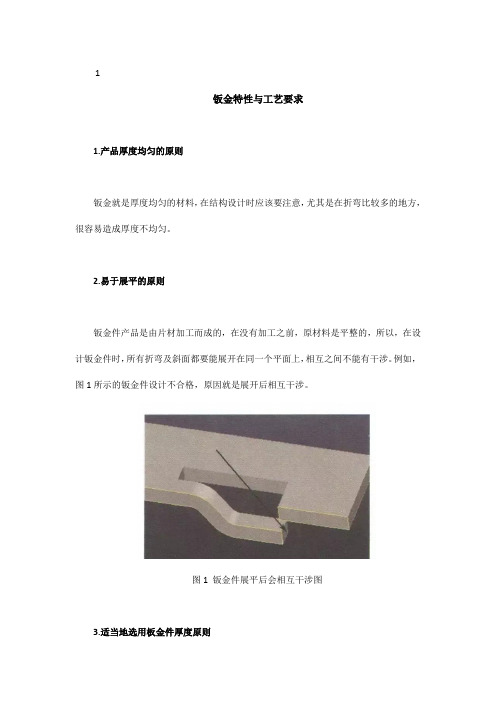
1钣金特性与工艺要求1.产品厚度均匀的原则钣金就是厚度均匀的材料,在结构设计时应该要注意,尤其是在折弯比较多的地方,很容易造成厚度不均匀。
2.易于展平的原则钣金件产品是由片材加工而成的,在没有加工之前,原材料是平整的,所以,在设计钣金件时,所有折弯及斜面都要能展开在同一个平面上,相互之间不能有干涉。
例如,图1所示的钣金件设计不合格,原因就是展开后相互干涉。
图1 钣金件展平后会相互干涉图3.适当地选用板金件厚度原则钣金件厚度从0.03〜4.00mm各种规格都有,但厚度越大越难加工,就越需要大的加工设备,不良率也随之增加。
厚度应根据产品实际的功能来选择,在满足强度及功能的前提下,越薄越好,对于大部分产品,钣金件厚度应控制在1.00mm以下。
4.符合加工工艺原则钣金件产品要符合加工工艺,要易于制造,不符合加工工艺的产品是制造不出来的,就是不合格的设计。
钣金类产品设计的工艺要求钣金▪工艺性:产品在各种加工过程中如冲切、折弯等的难易程度▪工艺要求:设计钣金类产品时应符合这些工艺性。
▪基本加工方式有:冲切、折弯、拉伸、成型等2冲切普通冲切:目前应用最多。
精密冲切:需要精密的冲切模具及高精度的冲切设备,成本要高于普通冲切,一般应用于比较精密的产品。
1.冲切件的外形尽量简单,避免细长的悬臂及狭槽冲切件的凸出或凹入部分的深度和宽度,一般情况下,应不小于1.5/t(t为料厚),同时应该避免窄长的切口与过窄的切槽,以便增大模具相应部位的刃口强度,如图2所示。
图2 避免窄长的悬臂和凹槽2.冲切件外形尽量使排样时废料最少,从而减少原料的浪费将图3所示的设计改进成图4所示的设计,就会以相同的原料增加产品数量,从而减少浪费,降低成本。
图3 原先设计图4 改进后设计3.冲切件的外形及内孔应避免尖角尖角会影响模具的寿命,在产品设计时要注意在角落连接处倒圆角过渡,圆角半径R≥ 0.5t (t为料厚),如图5所示。
图5 倒圆角设计4.冲切件的孔及方孔冲切件的孔优先选用圆孔,冲孔时,受到冲头强度的限制,冲孔的直径不能太小,不然容易损坏冲头。
车门钣金设计规范
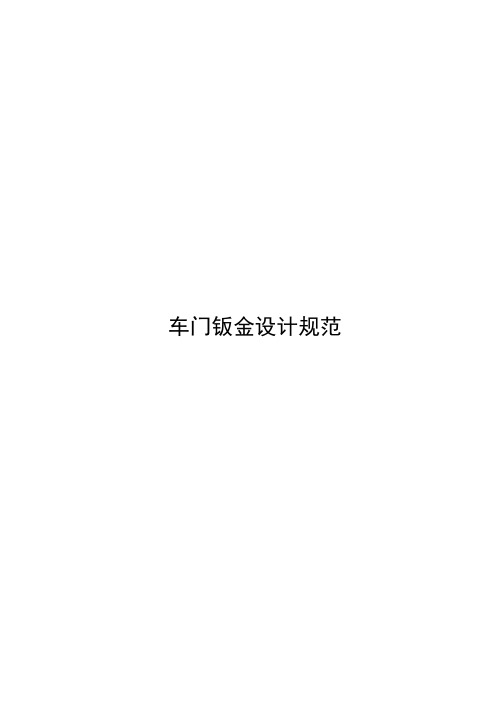
车门钣金设计规范车门钣金设计规范1.范围本标准规定了车门钣金的术语、一般汽车车门钣金的设计规则以及设计方法。
本标准适用于各种轿车,其它车型可参考执行。
2.车门基本简介2.1车门钣金概述1.作为外覆盖件,起装饰作用,保证装配后外观效果,需保证翼子板、侧围、前后门之间的间隙平度满足要求;2.有效保证车门密封性,避免出现漏水、风噪,导致顾客抱怨;3.为开启件,需满足开启及关闭的易操作性;4.车辆在行驶过程中保证车门始终处于关闭状态;5.保证车门很容易的装配到车身骨架上;6.为车身附件安装(外开把手、后视镜、外水切、昵嘈、内水切、门护板、门锁、扬声器、防水膜、升降器等安装)提供必要安装点及型面;7.保证升降系统的正常运行;8.保证行车门在行驶过程中不出现振动;不产生噪音;9.车门售后可更换及可维修性;10.具有承受一定作用力的刚度及强度2.2车门结构类型车门是车身的重要组成部分。
根据车型不同,车门结构形式一般有旋开式车门如图2.1所示、滑动门以及外摆式车门等,还有一些轿车上使用了上下车极方便的鸥翼式车门。
目前轿车车门使用最多的是旋开式车门,应用较多的轿车车门结构全尺寸内外板结构(整体式)、滚压窗框结构(分体式)以及半开放式车门结构(混合式),其结构具有各自不同的特点。
图2.1 旋开式车门2.2.1整体式----即车门面板与门框部分一体成形。
由全尺寸的冲压外板、全尺寸的冲压内板和嵌在内外板间的窗框导轨组成,导轨为U 字形滚压成型件,焊接在内板上,最后外板与内板总成通过包边方式闭合起来,这种车门板金结构在许多早期的车型被普遍采用。
优点:具有较好的完整性,整个车门的刚度较好,一体冲压出来的门板尺寸精度较高,并且加工工序较少、工艺简单。
缺点:窗框外边框通常较宽大,窗框的可装饰性不强,对造型有限制,不太符合现在造型的要求,而且全尺寸的门板需要较大的冲压模具,对冲压模的要求也比较高,整套模具的成本很高,由于窗框是一体冲压而成,废料面积较大,材料利用率较低。
钣金件技术要求

钣金件通用技术标准本标准为产品设计者提供本公司一般的设计要求,也为质检员提供检验与判定的参考依据,同时也作为供应商产品加工的标准。
此标准按钣金制作,也适合其他金属件加工的零配件和产品。
一.材料要求:除图纸特别说明外,一般材料采用优质A3冷板(Q235A)。
材料厚度符合GB709-88标准,其力学性能符合GB2975-82标准,化学成分符合GB222-84,并由供应商提供相关原材料检测报告。
二.表面要求:1.外观:光洁平整,去除毛刺、锐边,无变形等缺陷;2.喷涂:颜色与图纸要求或样件及色板一致,喷涂前必须经过酸洗和磷化处理(参考GB8923-88),无挂滴、条纹、起泡、桔皮、剥落、划伤等缺陷,附着力性能可靠,划格试验不大于1级,具体标准参考表一。
一般情况下涂层厚度在39~120μm之间;3.电镀:表面镀锌结晶细致,色泽均匀,结合牢固,不允许有生锈、表层不干净、划伤、凹坑等缺陷(参考钢铁制作机械镀锌标准要求JB/T8928-1999);4.耐蚀性:中性盐雾实验(GB/T 1771-1991)车身内配件外表面500h后划叉处单边扩蚀宽度≤2mm,未划叉区域无起泡、开裂、剥落、掉粉、明显变色、明显失光等涂膜病态现象内腔中性盐雾120h后红锈面积小于10%.;车身外配件1000h后基体无锈蚀。
5.丝印:文字、图案及颜色依据图纸要求,无偏斜、模糊、重影、针孔等缺陷,具体检验标准参考附表二。
6.对于外观分为A 、B、C、D四个等级。
三.加工:1.下料:非模具开料时必须打磨尖角和毛刺,模具落料时,未注圆角半径取料厚;2.折弯:未注折弯内圆角半径取材料厚度,3.焊接:牢固、平整,无虚焊、夹渣、气孔、堆积、变形等缺陷,影响到装配及外观的部分必须打磨平整;4.精度:未注尺寸公差按GB/T1800.3-1998中的IT14级精度制制作,同时图纸上所标注的尺寸均为表面处理后的状态,具体数据参见表三。
附表一划格试验GB/T 9286-1998系等效采用国际标准ISO 2409:1992《色漆和清漆——划格试验》(第二版),代替等效采用ISO 2409:1972的GB 9286-88。
汽车钣金模具设计规范

设计规范目录一、模具通用规格要求二、模具设计结构、强度要求三、模具材料及淬火硬度四、模具零件制造精度要求一、模具通用规格要求1.1退料装置退料装置要求设计合理,必须保证足够退料力,稳定可靠地将工件和废料退出凸模和凹模口之外,无任何滞阻和粘附现象。
1.2 进料、出料装置1.2.1 合理设计模具进、出料装置,保证进、出料方便可靠。
1.2.2 根据工件特征及模具结构,在进、出件侧要求设置托架,防止板料及冲压的磕碰划伤。
1.2.3 托架长度超出模具底部时,要求设计成折叠式。
1.3 托架装置为便于送料取件要求设置托架装置,采用气动装置或弹性装置(视情况而定),应保证冲压件可靠、平稳升起,冲压件外表面不变形、无擦伤。
气管接头采用3/8,设置在上料者的右侧。
1.4 导向部分采用导柱、导板或导柱加导板三种结构。
1.5 起重装置1.5.1 起重和用于翻转模具的起重,起吊装置采用甲方认可的标准设计,模具尺寸(长+宽)<2500mm时模座应采用起重棒结构,模具尺寸(长+宽)≥2500mm时模座采用插入吊棒式吊耳结构,起重棒要求安装于模具的前后侧。
1.5.2 凡取放不方便的零部件均要求设置起吊螺孔或起重孔,但不得破坏模具结构强度。
1.5.3 起吊螺孔采用公制标准螺孔。
起重孔采用M12或M16,深度为直径的2.5倍。
1.6 安全性及设施1.6.1 模具上的活动部件均要求有安全防护措施,应有防护板、防护罩等。
1.6.2 模具码放用限位器、安全块、防护板、防护罩等可按甲方认可的乙方标准设计。
模具零部件必须充分考虑防松、防崩、防脱落、防反、防冲击等措施;模具的布置应考虑到压机的安全性、合理性以及操作方便性。
1.6.3 模具结构设计,要求充分考虑抗冲击强度,合理的操作空间以及操作的方便性、安全性。
1.6.4 导向机构、限位器、斜楔机构等尽量远离操作区;限位器要求定位可靠并且满足操作方便性。
1.6.5 模具应便于拆装,维修,调整;所有模具结构必须考虑生产中进、出料防护装置及冲压件的顶出装置等;保证手工操作的安全性,良好的视野以及足够的操作空间。
白车身数模质量要求标准

上海同济同捷科技有限公司企业标准TJI/YJY白车身数模质量要求2005-XX-XX发布2005-XX-XX实施上海同济同捷科技有限公司发布前言白车身三维数模是汽车产品设计重要的技术文件,为提高三维数模设计质量,同时使数模层和目录设置规范化,便于管理和查阅,特制定本标准。
本标准由上海同济同捷科技有限公司提供。
本标准由上海同济同捷科技有限公司质量与项目管理中心负责归口管理。
本标准主要起草人:白车身数模质量要求1.范围:本标准适用于本公司负责设计的所有车型的白车身钣金零部件、焊接总成的三维数模。
2. 规范性引用文件2.1 曲面数模输出标准TJI / KG·1002 · A12.2 三维设计数模质量规范TJI / CZ0007· A1-20022.3 车身钣金件料厚方向设计的规定2.4 数模设计更改流程2.5 车身主断面标准2.6 车身装配检查规则2.7 开闭件设计规则2.8 车身包边结构设计要素2.9 车身铰链结构设计要素2.10 白车身三维数模焊接标注的规定TJI / YJY03.07.20053 术语和定义3.1 三维数模三维数字化模型的简称,根据在技术设计各个阶段的用途,三维数模可分为初步数模、工艺数模及NC数模等。
3.2 初步数模根据造型要求或结构设计要求,初步建立的三维数字模型,它能满足控制点、线、面的尺寸,具有必须的结构要素。
主要用于设计构思和方案讨论。
3.3 工艺数模结构设计结束,型面倒角基本完成,没有进行过装配检查的数模。
工艺数模可以提供给模具供应商制定冲压工艺方案和进行模具结构设计。
3.4 铸造数模型面倒角完成,已通过了装配检查,但没有最终数据冻结。
可以用于模具泡沫实型模的制作和加工,也可进行实型铸造。
3.5 NC数模即为冻结数模,可以用于模具的NC加工。
4.白车身数模的质量要求4.1 三维数模的基本要求4.1.1 坐标系:模型一律采用整车坐标系,按右手定则。
钣金件设计规范

钣金件设计规范钣金件设计规范是指针对钣金件的设计和制造过程中需要遵循的一系列规范和要求。
钣金件是指通过对金属板材进行切割、弯曲、冲压、焊接等工艺加工而成的零件。
下面是关于钣金件设计规范的一些要点。
1. 材料选择在设计钣金件时,需要根据零件的功能和工作环境选择合适的材料。
常用的钣金材料有碳钢、不锈钢、铝合金等。
同时,需要考虑材料的强度、硬度、耐腐蚀性等特性。
2. 设计几何形状钣金件的几何形状设计应具备合理性和可制造性。
应尽量减少零件的复杂度,避免过于细小的结构和过于复杂的平面形状。
设计时应考虑材料利用率和制造工艺的可行性。
3. 尺寸公差设计钣金件时,需要在设计图纸中规定尺寸公差。
合适的公差范围能够保证零件的互换性和可靠性。
公差的选择应根据零件的功能和制造工艺来确定。
4. 强度分析钣金件的设计应考虑其强度和刚度。
可以通过有限元分析等工具进行强度分析,以确定零件的最佳结构和材料。
5. 过冲与收口在钣金件的设计中,需要考虑过冲和收口的问题。
过冲是针对冲压加工过程中金属板材的弹性回弹问题,而收口则是为了提高钣金件的牢固性和密封性。
6. 表面处理钣金件在制造完成后,需要进行表面处理以提高其外观质量和耐腐蚀性。
常见的表面处理方法有喷漆、喷粉、电镀等。
7. 组装与安装钣金件的设计应考虑其组装和安装的便利性。
零件之间的连接方式应合理选择,并且连接点应容易访问和维修。
8. 质量控制在钣金件的设计和制造过程中,需要进行严格的质量控制。
设计师和制造人员要清楚了解设计要求,确保零件的质量符合标准。
9. 制造工艺钣金件的制造工艺有很多种,包括切割、冲压、弯曲、焊接等。
不同的制造工艺对零件的形状、尺寸和材料要求不同,设计师要根据具体情况选择合适的制造工艺。
10. 设计文件和验收标准钣金件的设计过程中应编制相应的设计文件,包括设计图纸、工艺文件、检验标准等。
设计师和制造人员要严格按照设计文件的要求进行制造和验收,确保零件符合设计要求。
钣金件设计规范
Q/HRLM 新黎明科技股份有限公司企业技术规范新黎明科技股份有限公司发布目次前言 (5)1范围和简介 (6)1.1范围 (6)1.2简介 (6)1.3关键词 (6)2规范性引用文件 (6)3冲裁 (6)3.1冲裁件的形状和尺寸尽可能简单对称,使排样时废料最少。
. 63.2冲裁件的外形及内孔应避免尖角。
(6)3.3冲裁件应避免窄长的悬臂与狭槽 (7)3.4冲孔优先选用圆形孔,冲孔有最小尺寸要求 (7)3.5冲裁的孔间距与孔边距 (8)3.6折弯件及拉深件冲孔时,其孔壁与直壁之间应保持一定的距离83.7螺钉、螺栓的过孔和沉头座 (8)3.8冲裁件毛刺的极限值及设计标注 (9)3.8.1冲裁件毛刺的极限值 (9)3.8.2设计图纸中毛刺的标注要求 (9)4折弯 (10)4.1折弯件的最小弯曲半径 (10)4.2弯曲件的直边高度 (10)4.2.1一般情况下的最小直边高度要求 (10)4.2.2特殊要求的直边高度 (11)4.2.3弯边侧边带有斜角的直边高度 (11)4.3折弯件上的孔边距 (11)4.4局部弯曲的工艺切口 (12)4.4.1折弯件的弯曲线应避开尺寸突变的位置 (12)4.4.2当孔位于折弯变形区内,所采取的切口形式 (12)4.5带斜边的折弯边应避开变形区 (13)4.6打死边的设计要求 (13)4.7设计时添加的工艺定位孔 (13)4.8标注弯曲件相关尺寸时,要考虑工艺性 (14)4.9弯曲件的回弹 (14)4.9.1折弯件的内圆角半径与板厚之比越大,回弹就越大。
.. 144.9.2从设计上抑制回弹的方法示例 (14)5拉伸 (15)5.1拉伸件底部与直壁之间的圆角半径大小要求 (15)5.2拉伸件凸缘与壁之间的圆角半径 (15)5.3圆形拉伸件的内腔直径 (15)5.4矩形拉伸件相邻两壁间的圆角半径 (15)5.5圆形无凸缘拉伸件一次成形时,其高度与直径的尺寸关系要求165.6拉伸件设计图纸上尺寸标注的注意事项 (16)5.6.1拉伸件产品尺寸的标准方法 (16)5.6.2拉伸件尺寸公差的标注方法 (16)6成形 (16)6.1加强筋 (17)6.2打凸间距和凸边距的极限尺寸 (17)6.3百叶窗 (17)6.4孔翻边 (18)7附录 (19)7.1附录A:高碳钢、低碳钢对应的公司常用材料牌号列表 (19)7.2附录B 压印工艺、压花工艺简介 (20)7.2.1压印工艺 (20)7.2.2压花工艺 (20)8参考文献 (21)前言本规范的其他系列规范:无与对应的国际标准或其他文件的一致性程度:无规范代替或作废的全部或部分其他文件:无与其他规范或文件的关系:无与规范前一版本相比的升级更改的内容:第一版,无升级更改信息。
车门钣金设计规范
车门钣金设计规范车门钣金设计规范1.范围本标准规定了车门钣金的术语、一般汽车车门钣金的设计规则以及设计方法。
本标准适用于各种轿车,其它车型可参考执行。
2.车门基本简介2.1车门钣金概述1.作为外覆盖件,起装饰作用,保证装配后外观效果,需保证翼子板、侧围、前后门之间的间隙平度满足要求;2.有效保证车门密封性,避免出现漏水、风噪,导致顾客抱怨;3.为开启件,需满足开启及关闭的易操作性;4.车辆在行驶过程中保证车门始终处于关闭状态;5.保证车门很容易的装配到车身骨架上;6.为车身附件安装(外开把手、后视镜、外水切、昵嘈、内水切、门护板、门锁、扬声器、防水膜、升降器等安装)提供必要安装点及型面;7.保证升降系统的正常运行;8.保证行车门在行驶过程中不出现振动;不产生噪音;9.车门售后可更换及可维修性;10.具有承受一定作用力的刚度及强度2.2车门结构类型车门是车身的重要组成部分。
根据车型不同,车门结构形式一般有旋开式车门如图2.1所示、滑动门以及外摆式车门等,还有一些轿车上使用了上下车极方便的鸥翼式车门。
目前轿车车门使用最多的是旋开式车门,应用较多的轿车车门结构全尺寸内外板结构(整体式)、滚压窗框结构(分体式)以及半开放式车门结构(混合式),其结构具有各自不同的特点。
图2.1 旋开式车门2.2.1整体式----即车门面板与门框部分一体成形。
由全尺寸的冲压外板、全尺寸的冲压内板和嵌在内外板间的窗框导轨组成,导轨为U 字形滚压成型件,焊接在内板上,最后外板与内板总成通过包边方式闭合起来,这种车门板金结构在许多早期的车型被普遍采用。
优点:具有较好的完整性,整个车门的刚度较好,一体冲压出来的门板尺寸精度较高,并且加工工序较少、工艺简单。
缺点:窗框外边框通常较宽大,窗框的可装饰性不强,对造型有限制,不太符合现在造型的要求,而且全尺寸的门板需要较大的冲压模具,对冲压模的要求也比较高,整套模具的成本很高,由于窗框是一体冲压而成,废料面积较大,材料利用率较低。
白车身钣金零件基础设计指导书
V1.0
编号
IAT/J-SJ4007-1
第 9 页 共 14 页
在钣金设计时为防止弯曲钣金时钣金破裂,需要在钣金弯曲处设计工艺缺口。 3.3.1 工艺缺口设计 1) 工艺缺口形状示意图,见图9、图10:
图9
图10 2) 标准弯曲半径详见表7: 表7 区分 料厚 0.6 0.7 0.8 0.9 1.0 1.2 1.4 1.6 1.8 2.0 2.3 2.6 3.2 4.5 2.0 2.0 3.0 3.0 3.0 3.0 5.0 5.0 5.0 5.0 8.0 8.0 10.0 16.0 标准弯曲半径 铝及合金 钢板、铜板 1.0 1.6 1.6 1.6 2.0 2.0 3.0 3.0 3.0 4.0 4.0 5.0 5.0 8.0 0.5 0.5 0.5 0.5 0.5 0.8 0.8 0.8 1.0 1.0 1.6 1.6 1.6 2.0 最小弯曲半径 冷连轧钢板 热连轧钢板 ———————2.0 2.0 2.0 2.0 2.5 3.0 4.0
4)
当弯曲半径 ≧ 标准弯曲半径 d≈(弯曲半径)× 1.8
3.3.2
翻边部设计注意点
为了防止翻边部出现裂缝及缩痕, 如下图在角部翻边设计切口, 减少翻边弯曲部的拉伸率, 压缩率, 见图 11。
图 11 3.4 钣金件加强筋的设计要求
加强筋分为:圆形加强筋、台型加强筋及三角加强筋,加强筋的作用是增加钣金强度、刚度。 为保证成型及加强筋的效果,需要考虑加强筋的高度。 3.4.1 圆形加强筋 H、R1、R2、R3 对应关系及对应料厚最小加强筋高度,详见表 8 和图 12;
Mn 螺母 A 凸焊在钣 件 B 上,然后直接与 C 焊 接 简 化 为 : (A+B)+C Mn 螺母 A 凸焊在钣 件 B 上, 钣件 C 与其 他件先组成一个分总 成,最后与(A+B)焊 接成一总成简化为: (1)A+B (2)C+其他 (3) (A+B)+(C+其 他) Mn 螺母 A 凸焊在钣 件 B 上,然后与钣件 C 和 D 顺序焊接简化 为: (1)A+B (2) (A+B)+C+D Mn 螺母 A 凸焊在钣 件 B 上,然后钣件 C 与钣件 D 及其他件焊 接,最后与 A+B 组成 一总成简化为: (1)A+B (2)C+D+ 其他 (3) (A+B)+(C+D+ 其他) 上述描述的是安装面 与定位面一致的情况, 如果安装面与该钣件 的定位孔面有一定的 角度
汽车钣金工艺准则
当突台或加强筋到翻边的距离>50mm时,突台或加强筋处要布焊 点。 L>50mm 翻边
突台
机舱总成
前壁板总成
左前纵梁总成
右前纵梁总成
前端模块总成
6 冲压件拔模角设计原则 ① 冲压件翻边的拔模角度一般设计为5度
翻边
② 冲压件突台的拔模角度一般设计为45度,强 度比较好,有时也要根据具体情况定义拔模度 数。
二 焊点工艺篇
1 焊接钣金件数量原则: 钣金件最多只能3层钣金同时焊接,2层钣金件一起焊接称为2层焊接,3 层钣金件一起焊接称为3层焊接。焊点尺寸一般为Ø 6mm
2层焊
3层焊
无法焊接
2 焊点布局原则:
L=8mm(经验值,最好最合理) L=8mm
d 2d
L=40mm─60mm(特殊情况 下最小不能<20mm)
L=40mm─60mm(特殊情况 下最小不能<20mm)
当突台或加强筋到翻边的距离<50mm时,突台或加强筋处不用布 焊点。 L<50mm 翻边 突台
汽车钣金工艺准则
一 设计篇
1 圆角原则: 钣金冲压件上的圆角(内角),其公式为 R=2t+1<4mm ,t为钣金料厚。经 验值为R=5mm or R=6mm,这个数值的倒角最漂亮最合理。
R=2t+1<4mm
t
2 突台设计原则:
>6mm
3 加强筋设计原则:
Ø 6─Ø 8
4 冲压件翻边设计原则
h=2mm─3mm