复合材料层合板分层疲劳性能研究进展
厚复合材料层压板胶粘接头疲劳性能及局部应力研究
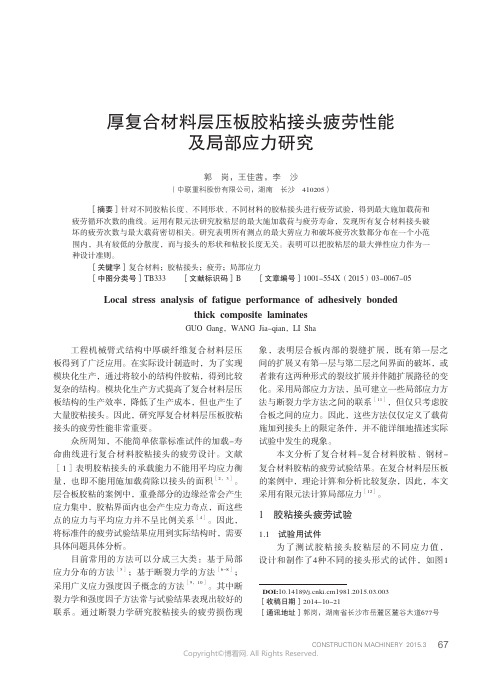
厚复合材料层压板胶粘接头疲劳性能及局部应力研究郭岗,王佳茜,李沙(中联重科股份有限公司,湖南长沙410205)[摘要]针对不同胶粘长度、不同形状、不同材料的胶粘接头进行疲劳试验,得到最大施加载荷和疲劳循环次数的曲线。
运用有限元法研究胶粘层的最大施加载荷与疲劳寿命,发现所有复合材料接头破坏的疲劳次数与最大载荷密切相关。
研究表明所有测点的最大剪应力和破坏疲劳次数都分布在一个小范围内,具有较低的分散度,而与接头的形状和粘胶长度无关。
表明可以把胶粘层的最大弹性应力作为一种设计准则。
[关键字]复合材料;胶粘接头;疲劳;局部应力[中图分类号]TB333 [文献标识码]B [文章编号]1001-554X(2015)03-0067-05Local stress analysis of fatigue performance of adhesively bondedthick composite laminatesGUO Gang,WANG Jia-qian,LI Sha工程机械臂式结构中厚碳纤维复合材料层压板得到了广泛应用。
在实际设计制造时,为了实现模块化生产,通过将较小的结构件胶粘,得到比较复杂的结构。
模块化生产方式提高了复合材料层压板结构的生产效率,降低了生产成本,但也产生了大量胶粘接头。
因此,研究厚复合材料层压板胶粘接头的疲劳性能非常重要。
众所周知,不能简单依靠标准试件的加载-寿命曲线进行复合材料胶粘接头的疲劳设计。
文献[1]表明胶粘接头的承载能力不能用平均应力衡量,也即不能用施加载荷除以接头的面积[2,3]。
层合板胶粘的案例中,重叠部分的边缘经常会产生应力集中,胶粘界面内也会产生应力奇点,而这些点的应力与平均应力并不呈比例关系[4]。
因此,将标准件的疲劳试验结果应用到实际结构时,需要具体问题具体分析。
目前常用的方法可以分成三大类:基于局部应力分布的方法[5];基于断裂力学的方法[6-8];采用广义应力强度因子概念的方法[9,10]。
含孔复合材料层合板的疲劳寿命研究
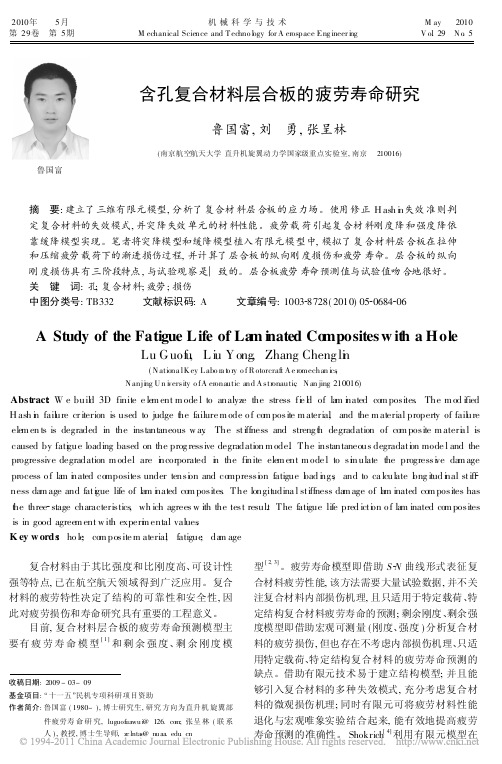
2010年第29卷5月第5期机械科学与技术M echanical Science and T echno l ogy for A erospace Eng ineer i ng M ay V o.l 292010N o .5收稿日期:2009-03-09基金项目: 十一五 民机专项科研项目资助作者简介:鲁国富(1980-),博士研究生,研究方向为直升机旋翼部件疲劳寿命研究,luguof uawu i @126.co m;张呈林(联系人),教授,博士生导师,z clntae @nu aa .edu .cn鲁国富含孔复合材料层合板的疲劳寿命研究鲁国富,刘 勇,张呈林(南京航空航天大学直升机旋翼动力学国家级重点实验室,南京 210016)摘 要:建立了三维有限元模型,分析了复合材料层合板的应力场。
使用修正H ash i n 失效准则判定复合材料的失效模式,并突降失效单元的材料性能。
疲劳载荷引起复合材料刚度降和强度降依靠缓降模型实现。
笔者将突降模型和缓降模型植入有限元模型中,模拟了复合材料层合板在拉伸和压缩疲劳载荷下的渐进损伤过程,并计算了层合板的纵向刚度损伤和疲劳寿命。
层合板的纵向刚度损伤具有三阶段特点,与试验观察是一致的。
层合板疲劳寿命预测值与试验值吻合地很好。
关 键 词:孔;复合材料;疲劳;损伤中图分类号:TB332 文献标识码:A 文章编号:1003 8728(2010)05 0684 06A Study of the Fatigue Life of La m i nated Co mposites w it h a HoleLu G uof u ,L i u Y ong ,Zhang Cheng li n(N ationa lK ey L abo ra t o ry o f R otorcraft A e romechan i cs ,N anji ng U n i versity o fA eronautic and A stronautic ,N an jing 210016)Abst ract :W e buil d 3D finite e le m ent m ode l to analyze the stress fi e l d of la m i n ated co m posites .The m od ified H ash i n fail u re cr iterion is used to judge t h e failure m ode o f co m posite m ateria,l and the m aterial property of fail u re ele m en ts is degraded in the instantaneous w ay .The stiffness and streng t h degradation of co m posite m ateri a l is caused by fati g ue loading based on the prog ressive degradation m ode.l The instantaneous degradati o n mode l and the progressive degradation m odel are i n corporated i n the finite ele m ent m ode l to si m ulate the progressi v e da m age process o f la m i n ated co mposites under tensi o n and co mpressi o n fatigue l o ad i n gs ,and to ca lculate l o ng itud i n al stiff ness da m age and fati g ue life of la m i n ated co m posites .The longitudina l stiffness da m age of l a m inated co m posites has t h e three stage characteristics ,wh ich agrees w ith the test resul.t The fatigue life pred icti o n o f la m inated co m posites is in good agree m ent w ith experi m ental values .K ey w ords :ho le ;co m posite m ateria;l fatigue ;da m age 复合材料由于其比强度和比刚度高、可设计性强等特点,已在航空航天领域得到广泛应用。
复合材料结构的疲劳性能分析

复合材料结构的疲劳性能分析复合材料是一种由两种或两种以上的材料复合而成的材料,具有很好的物理、化学性能以及机械性能,因此被广泛应用于航空航天、汽车、建筑等领域。
然而,复合材料的疲劳性能一直是一个关注的焦点问题。
本文将从复合材料的组成结构、疲劳破坏机制以及疲劳寿命预测等方面对复合材料的疲劳性能进行分析。
首先,复合材料的疲劳性能与其组成结构密切相关。
复合材料通常由纤维增强体和基体组成。
纤维增强体可以是碳纤维、玻璃纤维等,而基体则可以是树脂、金属等。
纤维增强体的方向性和体积分数对复合材料的疲劳性能有着重要的影响。
一般来说,纤维增强体的方向与加载方向垂直时,复合材料的强度和刚度较高;而纤维增强体的方向与加载方向平行时,复合材料的疲劳性能较好。
此外,纤维增强体的体积分数越高,复合材料的强度和刚度也就越高。
因此,在设计复合材料的结构时,应考虑纤维增强体方向和体积分数的选择,以提高复合材料的疲劳性能。
其次,复合材料的疲劳破坏机制是影响其疲劳性能的重要因素之一。
复合材料的疲劳破坏可以分为纤维破裂疲劳和基质破裂疲劳两种情况。
纤维破裂疲劳主要是由于纤维断裂引起的,而基质破裂疲劳则是由于基质中的微裂纹逐渐扩展导致的。
在实际应用中,为了提高复合材料的疲劳性能,可采取一些措施,如选择纤维的合适强度和刚度,增加基质的韧性等。
最后,预测复合材料的疲劳寿命是保证其安全可靠使用的关键。
目前,预测复合材料的疲劳寿命主要采用振动、疲劳试验和有限元分析等方法。
通过振动试验,可以获取复合材料在不同载荷下的保偏频率和阻尼比等参数,进而得到其应力-振动幅度周期关系曲线;通过疲劳试验,可以获得复合材料在不同循环加载下的应力变形曲线,从而分析其疲劳破坏机制;而有限元分析则可以模拟复合材料在不同载荷下的应力分布,进一步预测其疲劳寿命。
当然,这些方法都需要依赖于大量的实验数据和精确的材料模型,因此还需要不断地改进和完善。
综上所述,复合材料的疲劳性能是一个复杂而重要的问题。
挖补修理复合材料层合板静力压缩与疲劳性能试验研究

DOI:10.19936/ki.2096-8000.20210528.015挖补修理复合材料层合板静力压缩与疲劳性能试验研究苏雨茹,关志东*,王鑫,张书铭,黎增山(北京航空航天大学航空科学与工程学院,北京100191)摘要:挖补修理是应用较广的复合材料结构永久性修理方法。
本文对热补仪固化的湿铺层挖补修理和预浸料挖补修理复合材料层合板的静力压缩和压-压疲劳性能进行试验研究。
试件挖补斜度为1:30,有3种损伤大小。
疲劳试验的峰值和谷值为70%和7%限制载荷,共100万次。
疲劳过程中采用无损C扫描检测试件的损伤及扩展情况。
记录静力及疲劳后静力的应变数据、破坏载荷及破坏模式。
试验结果表明:两种修理方式的试件在疲劳过程中均未出现损伤及扩展现象,疲劳后试件刚度未有降低;修理方式、是否经过疲劳和损伤大小对试件的屈曲载荷和破坏载荷没有影响;端部压溃试件比中部折断试件破坏载荷更高;两种修理方式的破坏载荷均可达限制载荷的200%以上,修理效果较为理想。
关键词:挖补修理;湿铺层;热补仪;压缩性能;压-压疲劳;复合材料中图分类号:TB332文献标识码:A文章编号:2096-8000(2021)05-0098-061前言复合材料作为一种新型高性能材料,具有比强度高、比刚度高、耐高温、抗疲劳等优异特性,已被广泛应用于航空领域[1]°飞机复合材料结构在使用过程中不可避免地会产生各种损伤,威胁到结构的使用安全[2],需对其进行修理以恢复使用功能⑻°胶接挖补修理是一种永久性修理法,修理后结构强度恢复率高,表面具有良好的气动性能。
一般采用预浸料作为修理材料,当固化设备及材料缺少时,工程上常采用湿铺贴方式代替预浸料修理方式,配合使用热补仪更有利于外场修理。
修理后结构的承载能力是表征结构性能的关键因素。
复合材料结构在工况中不仅会受到静载,还经常会受到疲劳载荷的影响。
国内外学者对复合材料挖补修理结构进行了大量研究。
研究结果表明,挖补修理层合板的拉伸和压缩强度恢复率均可达到80%以上[4,5]°刘遂等[6-8]对挖补修理后的平面编织混杂铺层层合板的拉伸性能进行了试验及数值研究。
纤维增强复合材料疲劳性能研究进展
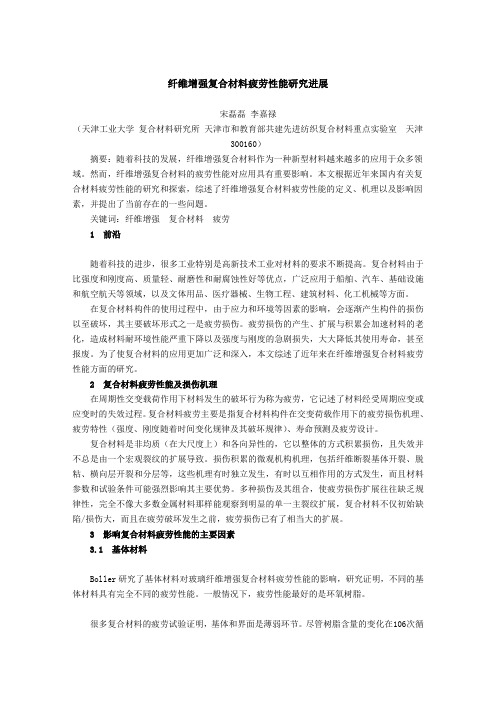
纤维增强复合材料疲劳性能研究进展宋磊磊李嘉禄(天津工业大学复合材料研究所天津市和教育部共建先进纺织复合材料重点实验室天津300160)摘要:随着科技的发展,纤维增强复合材料作为一种新型材料越来越多的应用于众多领域。
然而,纤维增强复合材料的疲劳性能对应用具有重要影响。
本文根据近年来国内有关复合材料疲劳性能的研究和探索,综述了纤维增强复合材料疲劳性能的定义、机理以及影响因素,并提出了当前存在的一些问题。
关键词:纤维增强复合材料疲劳1 前沿随着科技的进步,很多工业特别是高新技术工业对材料的要求不断提高。
复合材料由于比强度和刚度高、质量轻、耐磨性和耐腐蚀性好等优点,广泛应用于船舶、汽车、基础设施和航空航天等领域,以及文体用品、医疗器械、生物工程、建筑材料、化工机械等方面。
在复合材料构件的使用过程中,由于应力和环境等因素的影响,会逐渐产生构件的损伤以至破坏,其主要破坏形式之一是疲劳损伤。
疲劳损伤的产生、扩展与积累会加速材料的老化,造成材料耐环境性能严重下降以及强度与刚度的急剧损失,大大降低其使用寿命,甚至报废。
为了使复合材料的应用更加广泛和深入,本文综述了近年来在纤维增强复合材料疲劳性能方面的研究。
2 复合材料疲劳性能及损伤机理在周期性交变载荷作用下材料发生的破坏行为称为疲劳,它记述了材料经受周期应变或应变时的失效过程。
复合材料疲劳主要是指复合材料构件在交变荷载作用下的疲劳损伤机理、疲劳特性(强度、刚度随着时间变化规律及其破坏规律)、寿命预测及疲劳设计。
复合材料是非均质(在大尺度上)和各向异性的,它以整体的方式积累损伤,且失效并不总是由一个宏观裂纹的扩展导致。
损伤积累的微观机构机理,包括纤维断裂基体开裂、脱粘、横向层开裂和分层等,这些机理有时独立发生,有时以互相作用的方式发生,而且材料参数和试验条件可能强烈影响其主要优势。
多种损伤及其组合,使疲劳损伤扩展往往缺乏规律性,完全不像大多数金属材料那样能观察到明显的单一主裂纹扩展,复合材料不仅初始缺陷/损伤大,而且在疲劳破坏发生之前,疲劳损伤已有了相当大的扩展。
纤维增强复合材料层合板分层扩展行为研究进展
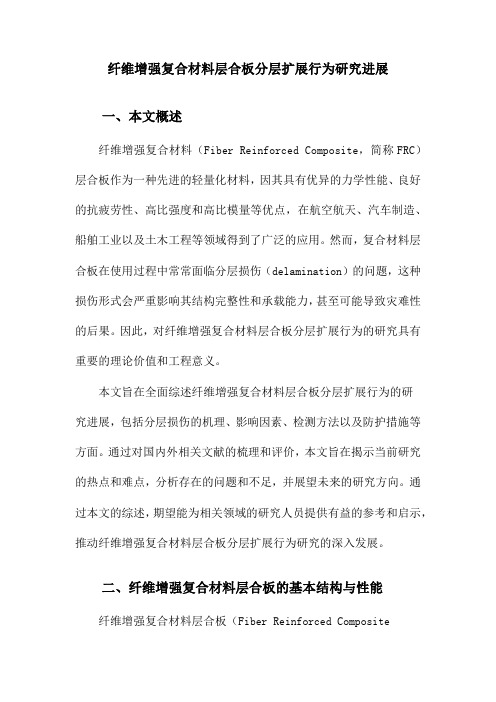
纤维增强复合材料层合板分层扩展行为研究进展一、本文概述纤维增强复合材料(Fiber Reinforced Composite,简称FRC)层合板作为一种先进的轻量化材料,因其具有优异的力学性能、良好的抗疲劳性、高比强度和高比模量等优点,在航空航天、汽车制造、船舶工业以及土木工程等领域得到了广泛的应用。
然而,复合材料层合板在使用过程中常常面临分层损伤(delamination)的问题,这种损伤形式会严重影响其结构完整性和承载能力,甚至可能导致灾难性的后果。
因此,对纤维增强复合材料层合板分层扩展行为的研究具有重要的理论价值和工程意义。
本文旨在全面综述纤维增强复合材料层合板分层扩展行为的研究进展,包括分层损伤的机理、影响因素、检测方法以及防护措施等方面。
通过对国内外相关文献的梳理和评价,本文旨在揭示当前研究的热点和难点,分析存在的问题和不足,并展望未来的研究方向。
通过本文的综述,期望能为相关领域的研究人员提供有益的参考和启示,推动纤维增强复合材料层合板分层扩展行为研究的深入发展。
二、纤维增强复合材料层合板的基本结构与性能纤维增强复合材料层合板(Fiber Reinforced CompositeLaminates)是一种由多层不同方向、不同性质的单层复合材料叠加而成的结构材料。
这种材料因其优异的力学性能,如高强度、高模量、良好的抗疲劳性能以及优良的抗腐蚀性能,在航空航天、汽车制造、船舶工程、土木工程等领域得到了广泛的应用。
在基本结构上,纤维增强复合材料层合板主要由基体材料和增强纤维两部分组成。
基体材料通常为热固性或热塑性树脂,起到粘结和固定增强纤维的作用。
增强纤维则主要由高性能纤维如碳纤维、玻璃纤维、芳纶纤维等构成,这些纤维以其高强度、高模量特性赋予了层合板良好的力学性能。
纤维增强复合材料层合板的性能特点主要体现在以下几个方面:其具有较高的比强度和比模量,即单位质量所能承受的力量和抵抗变形的能力,这使得它在轻量化设计方面具有显著优势。
T700复合材料层合板拉_拉疲劳性能

Fatigue lives of laminates with holes Diameter / mm 12. 36 12. 36 12. 34 6. 38 6. 40 6. 38 6. 38 80 85 90 Stress level / % Fatigue life 71298 65789 17658 32623 29687 35228 397326
1. 3
光滑板试验
1 组光滑板拉拉疲劳试验加载方式为正弦波, 加载 频 率 10Hz, 应 力 比 均 为 0. 1 , 引伸计跨距为 130mm。一定循环次数后, 通过材料试验机所带的 应变引伸计测量各试件应变, 获得试件的刚度变化 。 状况 试件内部损伤采用超声 C 扫描技术检测。 1 组光滑板试验共选择 70% 、 65% 和 60% 三个 60% 应力 应力水平, 前两个应力水平各取 3 个试件, 水平取 1 个试件。 各试件疲劳寿命见表 3 。 从表中可以看出, 除 T700KF13 试件结果明显偏离被去掉外, 每个应力 试验具有较 水平的光滑板疲劳寿命分散性均较小, 。 T700 T300 好的置信度 由于 碳纤维相比 碳纤维的 延伸率较大, 因而出现大规模的纤维断裂时间点较 迟且偏差小, 这也是 T700 层合板比 T300 层合板疲 劳寿命分散性小的原因之一。
表1 Table 1 Group No. 1 2 3 Diameter D / mm — 12. 5 6. 4 试验件尺寸表 geometry of specimens Length L / mm 230 300 300 Width W / mm 38 50 38 Thickness h / mm 50 50 50
由于具有优越的力学性能, 复合材料在现代航 空航天结构上得到了广泛的应用, 并且越来越多的 应用于飞行器的主承力结构。国际上最新型的大型 787 和 A350 上, 客机 B复合材料占全机结构比重已 经超过了 50% 。结构材料的疲劳性能, 对飞机的可 靠性和安全性起着决定性影响, 因此复合材料疲劳 性能方面的研究对于保证飞机的安全和提高飞机使 用寿命具有重要的意义。 但相对于金属, 复合材料 结构的复杂性使其对其损伤机理和损伤扩展机制的 研究都要复杂困难的多。 从 20 世纪 70 年代末开始, 国内外研究人员开 展了一系列对于复合材料疲劳方面的研究 , 取得了 。其中, 大量的研究成果 对于目前较为成熟的 T300 型碳纤维增强复合材料的疲劳性能的实验和 寿命预测研究开展较多, 取得了很多有应用价值的 T700 新型纤维增强复合材料得到了 成果。近年来, T700 以其更好 日益增多的应用, 相对于 T300 纤维, 的加工工艺得到的更优秀的拉伸强度, 正逐渐开始 替代 T300 纤维。但对 T700 碳纤复合材料的疲劳性 能方面的研究, 目前仍然还较为缺乏。 本研究对 T700 /9368 复合材料试件进行了拉拉疲劳试验, 对试件刚度衰减和疲劳损伤扩展进行 了初步研究, 并建立了疲劳损伤模型, 对试件的疲劳
复合材料的分层研究
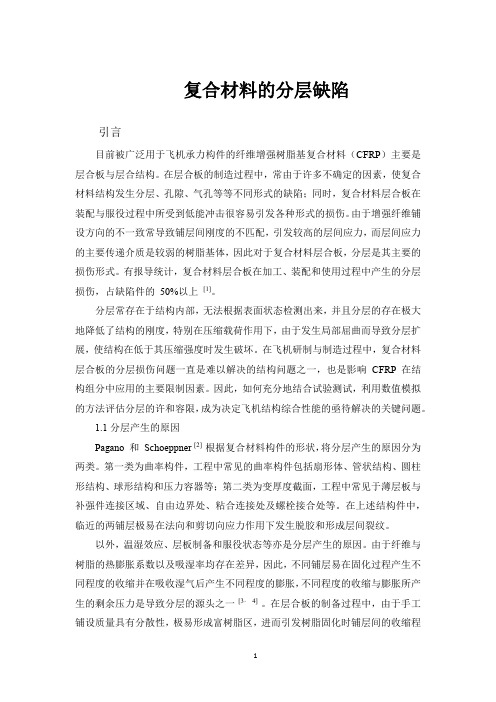
复合材料的分层缺陷引言目前被广泛用于飞机承力构件的纤维增强树脂基复合材料(CFRP)主要是层合板与层合结构。
在层合板的制造过程中,常由于许多不确定的因素,使复合材料结构发生分层、孔隙、气孔等等不同形式的缺陷;同时,复合材料层合板在装配与服役过程中所受到低能冲击很容易引发各种形式的损伤。
由于增强纤维铺设方向的不一致常导致铺层间刚度的不匹配,引发较高的层间应力,而层间应力的主要传递介质是较弱的树脂基体,因此对于复合材料层合板,分层是其主要的损伤形式。
有报导统计,复合材料层合板在加工、装配和使用过程中产生的分层损伤,占缺陷件的50%以上[1]。
分层常存在于结构内部,无法根据表面状态检测出来,并且分层的存在极大地降低了结构的刚度,特别在压缩载荷作用下,由于发生局部屈曲而导致分层扩展,使结构在低于其压缩强度时发生破坏。
在飞机研制与制造过程中,复合材料层合板的分层损伤问题一直是难以解决的结构问题之一,也是影响CFRP 在结构组分中应用的主要限制因素。
因此,如何充分地结合试验测试,利用数值模拟的方法评估分层的许和容限,成为决定飞机结构综合性能的亟待解决的关键问题。
1.1分层产生的原因Pagano 和Schoeppner [2] 根据复合材料构件的形状,将分层产生的原因分为两类。
第一类为曲率构件,工程中常见的曲率构件包括扇形体、管状结构、圆柱形结构、球形结构和压力容器等;第二类为变厚度截面,工程中常见于薄层板与补强件连接区域、自由边界处、粘合连接处及螺栓接合处等。
在上述结构件中,临近的两铺层极易在法向和剪切向应力作用下发生脱胶和形成层间裂纹。
以外,温湿效应、层板制备和服役状态等亦是分层产生的原因。
由于纤维与树脂的热膨胀系数以及吸湿率均存在差异,因此,不同铺层易在固化过程产生不同程度的收缩并在吸收湿气后产生不同程度的膨胀,不同程度的收缩与膨胀所产生的剩余压力是导致分层的源头之一[3,4] 。
在层合板的制备过程中,由于手工铺设质量具有分散性,极易形成富树脂区,进而引发树脂固化时铺层间的收缩程度差异,使层间具有较低的力学特性,极易形成分层[5,6] 。
- 1、下载文档前请自行甄别文档内容的完整性,平台不提供额外的编辑、内容补充、找答案等附加服务。
- 2、"仅部分预览"的文档,不可在线预览部分如存在完整性等问题,可反馈申请退款(可完整预览的文档不适用该条件!)。
- 3、如文档侵犯您的权益,请联系客服反馈,我们会尽快为您处理(人工客服工作时间:9:00-18:30)。
复合材料层合板分层疲劳性能研究进展
发表时间:2019-03-13T16:03:02.393Z 来源:《中国西部科技》2019年第2期作者:陈春露单鹏宇[导读] 介绍了近年来复合材料层合板分层疲劳模型、数值模拟、以及Ⅰ型Ⅱ型和混合型分层疲劳性能试验的研究进展,并对复合材料层合板分层疲劳性能进一步的研究进行了展望。
哈尔滨玻璃钢研究院有限公司复合材料层合板具有比强度高、比刚度大、抗疲劳性能好等一系列优点,能满足飞机结构重量轻、寿命长和可靠性高等特殊技术要求,已广泛应用于各航天航空领域。
与此同时,许多和复合材料有关的问题逐渐凸显出来,如疲劳和耐久性,以及疲劳下的裂纹扩展及由
此引起的分层现象。
由于复合材料层合板在工作中经常受到交变载荷的作用,所以对于层合板的疲劳研究,人们给予越来越多的关注[1],层合板的疲劳性能对复合材料的损伤容限设计、耐久性设计等有重要的意义。
1传统疲劳模型
传统的疲劳模型,如剩余刚度模型[2、3、5]、剩余强度模型[3、4]和疲劳寿命模型[6-11],是通过建立材料结构的S-N曲线来估算材料结构的疲劳可靠性。
这类宏观模型作为设计工具,已广泛应用于工程结构。
但是,宏观模型的估算结果通常是保守的,并且不能够建立损伤和循环数间的关系。
2分层疲劳模型
研究疲劳损伤扩展问题最著名的,也是最为广泛应用的是Paris法则。
该法则将疲劳裂纹扩展速率与能量释放率和模式比联系起来。
3 模拟
F.Shen[12]等采用虚拟裂纹闭合技术使用三维有限元模型模拟了含不同厚度圆形分层的编织和非编织复合材料的分层,计算了分层前缘应变能量释放率分布和分层前缘随循环次数的增长,并讨论了对称和非对称边界的情况,结果显示:纤维排布方向对局部应变能释放率分布有很大的影响;为节省计算时间普遍采用的四分之一模型由于边界作用会带来一定的误差。
S.C.Pradhan和T.E.Tay[13]采用三维有限元单元用ABAQUS软件模拟了中间带圆孔的聚四氟乙烯分层对碳纤维编织复合材料在压缩疲劳载荷下应变能释放率随分层前缘的变化,并用超声C扫描仪确定分层的扩展状态。
模拟与实验结果显示良好的吻合。
4三种不同类型试验研究4.1Ⅰ型和Ⅱ型
5结论及展望
TE Tay[18]曾对1990-2001年的层合板分层疲劳断裂的描述和分析的发展进行了回顾。
本文对近年各种分层疲劳扩展的模型、数值模拟、Ⅰ型II型和混合型分层疲劳试验的研究进展进行了总结。
由于不同的铺层形式、成型工艺、固化制度、载荷条件和环境等因素,会导致不同的分层疲劳的过程、机制和性能。
现有的各种研究对于各种影响分层疲劳性能的因素并没有十分周全的考虑,很多只是对于实验结果的半经验拟合。
提出包含各种影响因素的分层疲劳模型,发展更符合实际的层间单元模型,以及对分层疲劳微观机制的进一步研究,是未来分层疲劳研究的主要方向。
参考文献
[1] 张培新. 复合材料层压板层间应力分析和疲劳寿命估算[D].西北工业大学硕士学位论文,2005.
[2] 翟红军,姚卫星. 纤维增强树脂基复合材料的疲劳剩余刚度研究进展[J]. 力学进展, 2002, 32 (1): 69-80.
[3] 王小玲. 含损伤复合材料层合板疲劳特性研究[D]. 中国民航大学硕士学位论文, 2009.
[4] 魏巍, 邓忠民. 含分层损伤的复合材料层合板剩余强度的研究[N]. 材料研究学报, 2007, (21): 373-375.
[5] 蒋咏秋. 复合材料由于损伤导致刚度降得估算. 西安交通大学学报[N], 1990, 24 (6): 15-19.
[6] 徐颖. 复合材料层合板冲击损伤及冲击后疲劳寿命研究[D]. 南京航空航天大学博士学位论文, 2007.
[7] 诸强, 杨智春, 张开达. 一种计及分层效应的复合材料层合板疲劳寿命计算方法[N]. 西北工业大学学报, 2005, 23 (6): 708-712.
[8] 陈群志, 关志东等. 分层缺陷对复合材料结构疲劳寿命影响研究[J]. 机械强度, 2004, 26 (S): 121-123.
[9] 张培新. 复合材料层压板层间应力分析和疲劳寿命估算[D]. 西北工业大学硕士学位论文, 2005.
[10] 董兴建, 李亚智, 孟光等. 复合材料层压板疲劳寿命预测方法[N]. 上海交通大学学报, 2004, 38 (10): 1748-1752.
[11] 董兴建. 复合材料层压板疲劳寿命预测方法研究[D]. 西北工业大学硕士学位论文, 2002.
[12] F.Shen, K.H.Lee, T.E.Tay. Modeling delamination growth in laminated composites[J]. Composites Science and Technology, 2001, (61): 1239-1251.
[13] S.C.Pradhan, T.E.Tay. Three-dimensional finite element modelling of delamination growth in notched composite laminates under compression loading[J].. Engineering Fracture Mechanics, 1998, 60 (2): 157-171.
[14] A Argüelles, J.Vi?a, A.F.Canteli, A.Lopez. Influence of the Matrix Type on the Mode I Fracture of Carbon-Epoxy Composites Under Dynamic Delamination[J]. Experimental Mechanics, 2010.
[15] M. Beghini, L.Bertini, P.Forte. Experimental investigation on the influence of crack front to fiber orientation on fatigue delamination growth rate under mode II[J] . Composites Science and Technology, 2006, (66): 240-247.
[16] M.Kenane, M.L.Benzeggagh. Mixed-mode delamination fracture toughness of unidirectional glass/epoxy composites under fatigue loading[J]. Composites Science and Technology, 1997, (57): 597-605.
[17] N.Blanco etc. Mixed-mode delamination growth in carbon-fibre composite laminates under cyclic loading[J]. International Journal of Solids and Structures, 2004, (41): 4219-4235.
[18] TE Tay. Characterization and analysis of delamination fracture in composites: An overview of developments from 1990 to 2001[J]. Appl Mech Rev, 2003, 56 (1): 1-32.。