鲁姆斯丙烷脱氢制丙烯技术介绍
丙烷脱氢制丙烯工艺[要略]
![丙烷脱氢制丙烯工艺[要略]](https://img.taocdn.com/s3/m/db8cb87ada38376bae1faea6.png)
丙烷脱氢制丙烯工艺[要略]丙烷脱氢制丙烯工艺三问“丙烷脱氢”——丙烯新工艺“丙烷脱氢”是现今国内丙烯生产新工艺的热点之一,备注市场的关注和青睐。
“丙烷脱氢”是现今国内丙烯生产新工艺的热点之一,备注市场的关注和青睐。
<<隐藏国内丙烯市场存在较大的需求缺口,为了使得下游产品市场更健康长久发展,解决原料丙烯的缺量问题,市场中跃跃欲试的企业越来越多。
目前有两个热点,其一煤化工路线,煤制烯烃;其二,丙烷脱氢。
丙烷脱氢工艺因其丙烯收率相对较高,目前备受市场关注和青睐。
目前较为成熟的丙烷脱氢工艺主要有三种:Oleflex 工艺、Catofin 工艺和 PDH 工艺。
Oleflex 工艺由 UOP 公司开发并于 1990 年实现工业化生产,工艺主要采用催化剂连续再生方法,该工艺制取丙烯的产率约为86×4%,氢气产率约为3×5%。
Catofin 工艺是由鲁姆斯等公司联合开发,可生产丙烯、异丁烯、正丁二烯等产品。
该工艺采用固定床催化反应器,并用取切换操作的方法,丙烯转化率高达 90%左右。
PDH 工艺是由德国林德公司和巴斯夫公司合作开发,主要生产丙烯和异丁烯。
该工艺采用装填催化剂的管式反应器。
目前该项目在国内仍是一片空白。
天津渤海化工集团投资建设目前国内首套、世界单套规模最大的丙烯生产装置——60 万吨/年丙烷脱氢制丙烯,项目引进鲁玛斯技术公司专有的 Catofin 脱氢技术,该项目位于天津临港工业园区内,投资 34.8 亿元,计划 2012-2013 年投产。
原料丙烷将由日本丸红提供。
面对新鲜事物,蜂拥者不乏少数,目前国内很多厂家也都在酝酿上马丙烷脱氢项目,特别是下游工厂,主要是应对棘手的原料供应问题。
想法总是好的,但是笔者心存几个疑虑,想和大家分享一下。
第一,国内尚没有成功案例。
一切为新的事物,即便天津渤海化工集团项目真能如期投产,那么从试运行到商业化运作,产品质量需要一个过程去赢得市场的认同,新的技术很有可能遇到这样或者那样的问题有待解决,这个过程可能会较长。
丙烷脱氢制丙烯工艺流程(精)

丙烷脱氢制丙烯工艺流程(精)概述丙烷脱氢制丙烯是一种重要的化工工艺,旨在通过取代烷基中的一个氢原子,将丙烷转化为丙烯。
丙烯是一种重要的原料,广泛应用于合成各种有机化合物以及塑料、橡胶、纤维等领域。
本文将介绍精细化工工艺中的丙烷脱氢制丙烯工艺流程,包括反应机、催化剂、反应条件等方面。
工艺流程反应机反应机是丙烷脱氢制丙烯工艺流程的核心设备。
在工业生产中,常用的反应器有管式反应器、零重力反应器等。
管式反应器是一种常见的连续式反应设备,与传统的批量反应器相比,具有占地面积小、产品质量稳定等优点。
而零重力反应器则可以提高反应物料之间的混合度,使反应物料更加均匀地进入反应管,提高反应的效率。
催化剂在丙烷脱氢制丙烯的过程中,催化剂起到关键作用,能够促进反应的进行。
常用的催化剂有氧化钙、氧化镁、氧化铝等,其中氧化铝催化剂成本相对较低,因此得到广泛应用。
催化剂的选择需要考虑不仅反应速率,而且反应产品的产率和纯度。
反应条件丙烷脱氢制丙烯的反应条件需要保证催化剂活性,同时不影响设备结构的安全性。
常用的反应条件包括反应温度、反应压力、空速等。
一般来说,反应温度越高,反应速率越快,但催化剂活性也会降低,反应压力也受到一定的限制。
空速则需要根据具体反应器进行优化,以保证反应效率和反应物料的流动性。
生产注意事项丙烷脱氢制丙烯是一种高温和高压的化学反应过程,因此在生产过程中需要注意安全问题。
首先,在催化剂的投入过程中需要避免空气和水汽进入反应器内部,以免影响催化剂的活性。
其次,在反应过程中需要进行随时监测,以保证产品的质量和纯度。
最后,在生产过程中需要做好应急准备工作,以应对可能发生的意外情况。
结论丙烷脱氢制丙烯工艺流程是一项非常重要的化工工艺,对各种有机化学合成以及塑料、橡胶、纤维等领域的生产都有着重要的影响。
在生产过程中,需要考虑设备设施、催化剂、反应条件等多方面的问题,并做好应急准备工作,以确保工艺流程可以稳定持续地进行,并得到良好的效果。
丙烷脱氢制丙烯工艺及技术要点分析

丙烷脱氢制丙烯工艺及技术要点分析作者:孙涛来源:《名城绘》2020年第09期摘要:近年,伴随着国内社会技术发展,在化工企业日常生产中,会产生很多的碳酸硫酚,这类碳酸的化学物质主要是丙烯或者丙烷。
丙烯是国内化工企业最基础的石化原料,国内民用的液化气就是由丙烷构成。
化工企业通过应用催化脱氢技术,可以将低附加值的丙烷转化为市场缺乏的丙烯原料,这有非常重要的经济和社会的效益。
丙烷脱氢的丙烯生产技术,往往比较单一,副产品大多数是氢气,需要根据现有的乙烯联合产品,使用丙烯催化裂化制剂,并且生产线路的控制。
相比丙烷的脱氢技术来讲,要及时地对现有工艺和催化剂做好优化组合。
关键词:丙烷脱氢;制丙烯;工艺技术;要点分析引言在丙烷的生产制造当中,要加强丙烷的脱氢,才能够提高丙烷的产品质量水平。
在加强期间,要做好安全的控制,使用自动化的设备、安全仪表和报警装置来对丙烯生产装置内部的温度、压力流量做好适当的监控。
一、丙烷脱氢丙烯技术安全措施生产设置内部还要安装自动化的控制系统、安全仪表及有毒气体的检测和报警系统,要及时地将这些反应温度、压力流量等数据融入到检测系统内部。
做好加热装置关键设备的控制,然后在设备内部,要投入一定的物料,及时地对这些物料的粉碎度,以风向做好数据的采集,确保仪表安全有效。
还要保持参数有足够的数据,在操作和调整期间,要严格遵循先降温后降量的方式,做好反应温度的控制,避免设备内部出现腐蚀问题的产生。
要有效地去提高现有装置内部设备和管线的核心控制,对于系统内部要做到合理的筛查,控制好原料内部的含硫量,要减少硫化氢气体产生。
要保证生产车间内部的物料合理流动,还要做好加热炉多个火焰的管理,避免火焰直接接触到设备,而出现罐炉热量分布不均衡。
提高对热辐射的交换控制。
采取必要的措施来检查锅炉的开关,进而去防止锅炉出现的爆炸问题。
脱氢装置容易产生爆炸,因而就要对反应装置做好科学的管理,保证脱氢技术和工艺更加安全,如图1所示。
丙烷脱氢

一、概述丙烯主要用于生产聚丙烯、丙烯腈、丁辛醇、丙烯酸等产品,目前,丙烯供应主要来自石脑油裂解制乙烯和石油催化裂化。
2004-2010年间,乙烯产能增长34%,而丙烯产能仅增长25%。
随着丙烯下游产品需求量不断增长,丙烯资源短缺的状况还会进一步加剧。
因此,近年开发扩大丙烯来源的丙烷脱氢(PDH)制丙烯生产工艺成为备受关注的热点。
二、丙烷脱氢制丙烯技术情况丙烷脱氢制丙烯技术主要包括催化脱氢制丙烯、氧化脱氢制丙烯、膜反应器脱氢制丙烯以及CO2逆水煤气法脱氢制丙烯技术[2]。
2.1 丙烷催化脱氢技术丙烷催化脱氢技术根据催化剂体系的不同主要有铬系催化剂、铂系催化剂。
2.1.1 铬系催化剂丙烷催化脱氢的Catofin 工艺就采用Cr203/Al2O3催化剂,由于铬系催化剂稳定性差,且具有毒性,随着环境保护呼声的日益提高,开发低Cr含量的催化剂才有一定的前景。
2.1.2 铂系催化剂丙烷Oleflex催化脱氢工艺,采用贵金属Pt催化剂,Pt催化剂对热更稳定,可在更苛刻条件下操作。
铂催化剂对环境友好,活性较高,但其稳定性选择性还不是很理想。
2.2 丙烷氧化脱氢技术丙烷氧化脱氢为放热反应,无需外界加热,不必向过程提供热能,可节省能源,同时反应不受热力学平衡的限制。
因此氧化脱氢具有诱人的前景。
但该技术面临的困难之一是在氧化脱氢的反应条件下,很容易发生丙烷的完全氧化反应,一旦发生完全氧化反应,将放出大量热量,使温度急剧上升,不仅丙烷完全氧化,而且所产生的丙烯更容易氧化成CO~CO2(因为丙烯比丙烷更不稳定)。
因此,开发低温型高选择性催化剂是丙烷氧化脱氢的研究方向。
两种技术比较丙烷催化脱氢的选择性较高,其缺点是要耗费大量的能量。
若能把催化脱氢和氧化脱氢的优点结合起来,设计双功能型催化剂。
在催化脱氢体系引入少量氧,氧在活化丙烷的同时实现对氢气高选择性氧化,实现化学平衡移动的同时自身提供热量。
这个过程可能打破脱氢反应热力学限制,同时解决氧化脱氢反应在高烷烃转化率下的低碳烯烃选择性问题。
丙烷制脱氢丙烯工艺简介及发展概况分析
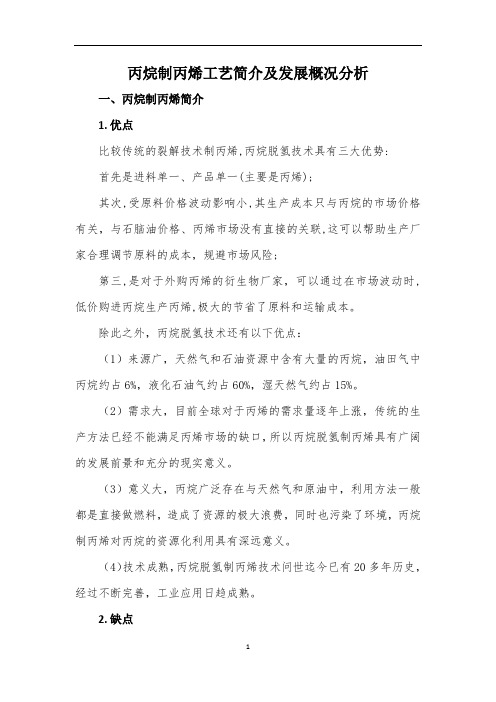
丙烷制丙烯工艺简介及发展概况分析一、丙烷制丙烯简介1.优点比较传统的裂解技术制丙烯,丙烷脱氢技术具有三大优势:首先是进料单一、产品单一(主要是丙烯);其次,受原料价格波动影响小,其生产成本只与丙烷的市场价格有关,与石脑油价格、丙烯市场没有直接的关联,这可以帮助生产厂家合理调节原料的成本,规避市场风险;第三,是对于外购丙烯的衍生物厂家,可以通过在市场波动时,低价购进丙烷生产丙烯,极大的节省了原料和运输成本。
除此之外,丙烷脱氢技术还有以下优点:(1)来源广,天然气和石油资源中含有大量的丙烷,油田气中丙烷约占6%,液化石油气约占60%,湿天然气约占15%。
(2)需求大,目前全球对于丙烯的需求量逐年上涨,传统的生产方法已经不能满足丙烯市场的缺口,所以丙烷脱氢制丙烯具有广阔的发展前景和充分的现实意义。
(3)意义大,丙烷广泛存在与天然气和原油中,利用方法一般都是直接做燃料,造成了资源的极大浪费,同时也污染了环境,丙烷制丙烯对丙烷的资源化利用具有深远意义。
(4)技术成熟,丙烷脱氢制丙烯技术问世迄今已有20多年历史,经过不断完善,工业应用日趋成熟。
2.缺点(1)丙烷制丙烯装置的原料主要是以丙烷为主,而国内丙烷量有限,而且指标参差不齐,无法满足装置对丙烷的要求,装置原料需从国外进口。
目前国内进口气几乎全部是海运,而进口码头配套设施有限,要建设丙烷制丙烯装置,首先要解决的是丙烷供应。
新建和规划丙烷制丙烯项目,要么有其配套码头设施,要么距离液化气码头较近。
(2)技术方面,目前用来丙烷脱氢制丙烯的两种技术均来自于国外,装置规模大,投资高,建设周期相对较长,因此准入门槛高。
(3)尽管大量的丙烷脱氢催化剂被开发出来,但是这些催化剂的性能(活性,选择性和稳定性)仍需要提高。
(4)生产过程中会生成一些易燃、易爆物质,主要有丙烷、丙烯、氢气以及甲烷、少量乙烷和乙烯。
氢气作为甲类易燃物,爆炸范围宽,点火能量低,高压氢气泄漏遇静电就可能发生燃烧或爆炸;丙烷、丙烯比重较空气重,会在地面积累并向四周扩散,遇空气可形成爆炸性气体,遇高热、明火容易发生火灾爆炸。
丙烷制脱氢丙烯工艺简介及发展概况分析

丙烷制脱氢丙烯⼯艺简介及发展概况分析丙烷制丙烯⼯艺简介及发展概况分析⼀、丙烷制丙烯简介1.优点⽐较传统的裂解技术制丙烯,丙烷脱氢技术具有三⼤优势:⾸先是进料单⼀、产品单⼀(主要是丙烯);其次,受原料价格波动影响⼩,其⽣产成本只与丙烷的市场价格有关,与⽯脑油价格、丙烯市场没有直接的关联,这可以帮助⽣产⼚家合理调节原料的成本,规避市场风险;第三,是对于外购丙烯的衍⽣物⼚家,可以通过在市场波动时,低价购进丙烷⽣产丙烯,极⼤的节省了原料和运输成本。
除此之外,丙烷脱氢技术还有以下优点:(1)来源⼴,天然⽓和⽯油资源中含有⼤量的丙烷,油⽥⽓中丙烷约占6%,液化⽯油⽓约占60%,湿天然⽓约占15%。
(2)需求⼤,⽬前全球对于丙烯的需求量逐年上涨,传统的⽣产⽅法已经不能满⾜丙烯市场的缺⼝,所以丙烷脱氢制丙烯具有⼴阔的发展前景和充分的现实意义。
(3)意义⼤,丙烷⼴泛存在与天然⽓和原油中,利⽤⽅法⼀般都是直接做燃料,造成了资源的极⼤浪费,同时也污染了环境,丙烷制丙烯对丙烷的资源化利⽤具有深远意义。
(4)技术成熟,丙烷脱氢制丙烯技术问世迄今已有20多年历史,经过不断完善,⼯业应⽤⽇趋成熟。
2.缺点(1)丙烷制丙烯装置的原料主要是以丙烷为主,⽽国内丙烷量有限,⽽且指标参差不齐,⽆法满⾜装置对丙烷的要求,装置原料需从国外进⼝。
⽬前国内进⼝⽓⼏乎全部是海运,⽽进⼝码头配套设施有限,要建设丙烷制丙烯装置,⾸先要解决的是丙烷供应。
新建和规划丙烷制丙烯项⽬,要么有其配套码头设施,要么距离液化⽓码头较近。
(2)技术⽅⾯,⽬前⽤来丙烷脱氢制丙烯的两种技术均来⾃于国外,装置规模⼤,投资⾼,建设周期相对较长,因此准⼊门槛⾼。
(3)尽管⼤量的丙烷脱氢催化剂被开发出来,但是这些催化剂的性能(活性,选择性和稳定性)仍需要提⾼。
(4)⽣产过程中会⽣成⼀些易燃、易爆物质,主要有丙烷、丙烯、氢⽓以及甲烷、少量⼄烷和⼄烯。
氢⽓作为甲类易燃物,爆炸范围宽,点⽕能量低,⾼压氢⽓泄漏遇静电就可能发⽣燃烧或爆炸;丙烷、丙烯⽐重较空⽓重,会在地⾯积累并向四周扩散,遇空⽓可形成爆炸性⽓体,遇⾼热、明⽕容易发⽣⽕灾爆炸。
鲁姆斯公司Catofin工艺丙烷脱氢工艺
个操作周期。引人丙烷原料之前�将富氢燃料气引人反应器�在一 个 很 短 的 时 间 里 除 去 催 化 剂 床 所 吸 附 的 氧 并 加 热 �这 个 还 原 步 骤 因 为减少了进料的氧化燃烧�从而降低了原料的损耗。
反 应 器 系 统 由 一 连 串 平 行 反 应 器 组 成 �并 以 循 环 方 式 操 作 �从 而 形 成 一 些 反 应 器 正 投 入 生 产 �而 另 一 些 反 应 器 则 正 在 预 热 � 再 生 � 还 有 一 些 反 应 器 在 抽 真 空 、蒸 汽 吹 扫 、重 新 加 压 、催 化 剂 还 原 或 阀 门变动�以便统筹提高生产效率。
Catofin 工 艺 (见图 3)分为 4 个 工段�丙 烷脱 氢 制 丙 烯 (反 应 工 段 )、反 应 器 排 放 料 的 压 缩 (压 缩 工 段 )、产 品 的 回 收和 精 制 (回 收 工 段 和 精 制 工 段 ) 。C a t o f i n 工 艺 采 用 固 定 床 和 C r 2 O 3 - A 12 0 3 催 化 剂 将 丙 烷 转 化 为 丙 烯 �没 有 转 化 的 丙 烷 循 环 使 用 �因 此 丙 烯 是 单 一 产 品 。
Cat ofin 催 化 脱 氢 工 艺 利 用 平 行 绝 热 固 定 床 反 应 器 �其 主 要 特 点为�工艺过程中加入蒸汽和氧气�蒸汽可使反应物分压降低�加 快 转 化 �并 减 少 催 化 剂 结 焦 、延 长 寿 命 。氧 气 可 与 部 分 氢 气 生 成 H 2O � 使化学平衡向正方向移动�提高丙烷转化率。
Car otin 工 艺 为 在 固 定 床 反 应 器 内 发 生 的 吸 热 反 应 �按 循 环 方 式 操 作 使 主 物 料 实 现 连 续 不 问 断 流 动 。在 一 个 全 循 环 中 �要 进 行 烃 蒸气脱氢�反应器内用蒸汽清洗、空气吹扫、预热催化剂并烧掉少 量 沉 积在 催化 剂上 的 结焦 (基于 催化剂 的质量分 数 <0� 1�)� 然 后 抽 真 空、 复原 �开 始 另一 次循环 。 Catofin 工 艺丙 烷 生 成 丙烯 的 总 转 化 率为 85�� 用 1� 18t 丙烷 生产 1t 丙烯。
鲁姆斯丙烷脱氢反应器再生控制程序
鲁姆斯丙烷脱氢反应器再生控制程序鲁姆斯丙烷脱氢反应器再生控制程序主要有两种主流工艺。
一、1. UOP公司的Oleflex工艺Oleflex工艺采用4个串联移动床反应器,以Pt/Al2O3为催化剂,采用铂催化剂(DeH-12)的径流式反应器使丙烷加速脱氢。
催化剂连续再生,使用氢作为原料的稀释剂,反应温度为550~650℃,丙烯收率约为85%,氢气产率为3.6%,乙烯收率很低,通常乙烯与其它副产品一起被当作燃料烧掉给丙烯脱氢反应器提供热量。
因此这一反应的产品只有丙烯。
2. ABB公司的Lumms- Catofin工艺Catofin工艺采用逆流流动固定床技术,在反应器中空气向下、烃类向上流动,烃蒸汽在铬催化剂上脱氢。
3. PDH工艺Linde&BASF4. STAR工艺——Philips/Uhde5. FBD-4工艺——Snamprogetti—Yarsintez 后三种没有在运行的大型工业化装置,国内的主流丙烷脱氢采用UOP的工艺比较多。
二、1.一种丙烷氧化脱氢制丙烯的方法,其特征在于,丙烷原料与氧化剂引入脱氢反应器中,与催化剂接触,进行氧化脱氢反应生成丙烯,反应物流与催化剂气固分离,分离出的反应物流进入产品分离装置进一步分离出丙烯、丙烷和氧化剂,其中,所述的丙烷和氧化剂循环回脱氢反应器中继续反应,所述的催化剂为负载型金属氧化脱氢催化剂和废催化裂化催化剂的混合物。
2.按照权利要求1所述的丙烷氧化脱氢制丙烯的方法,其特征在于,以催化剂总重量为基准,以金属计,所述的负载型金属氧化脱氢催化剂含有5-15wt%的金属活性组分和耐热无机氧化物载体,所述金属活性组分选自Cr、Co、Ni、Mo和RE中的一种或几种,所述耐热无机氧化物载体选自A1203、Ti02、Ce02、Si02、MCF分子筛和SBA-15分子筛中的一种或几种的混合物。
3.按照权利要求2所述丙烷氧化脱氢制丙烯的方法,其特征在于,所述的催化剂中,负载型金属氧化脱氢催化剂所占比例为50wt%~95wt%,废催化裂化催化剂的占比为5wt%-50wt%。
丙烷脱氢鲁姆斯工艺
丙烷脱氢鲁姆斯工艺《丙烷脱氢鲁姆斯工艺:我的独特体验》哎呀,说起丙烷脱氢鲁姆斯工艺,我可有不少话要说呢。
我第一次接触到丙烷脱氢鲁姆斯工艺,那是在一个超级大的化工厂里。
我刚走进厂子,就被那些巨大的设备给震住了。
一个个大罐子像巨人一样矗立着,还有错综复杂的管道,就像蜘蛛网似的到处都是。
我当时就在想,这丙烷脱氢鲁姆斯工艺到底是咋在这些大家伙里运作的呢?我跟着一个老师傅,他可算是这方面的行家了。
他带我来到一个像小山一样的反应装置前,指着它说:“看,这里面就是丙烷脱氢鲁姆斯工艺施展魔法的地方。
”我凑近了看,那装置的外壳有点泛着金属的冷光,上面还有一些小仪表,指针在滴滴答答地走着,就像一个个小卫士在随时报告里面的情况。
老师傅开始给我详细讲这个工艺。
他说啊,丙烷脱氢鲁姆斯工艺呢,就像是一场精心编排的舞蹈。
首先啊,丙烷就像一个个小演员,被送进这个大装置里。
那丙烷的纯度可重要了,就好比演员的基本功得扎实一样。
要是丙烷不纯,那这场“舞蹈”可就乱套了。
然后呢,在这个装置里,温度就像指挥家手中的指挥棒。
老师傅一边说,一边指着旁边的温度显示仪,那上面的数字不断地跳动着。
他说,这个温度得控制得特别精准才行,高一点低一点都不行。
就像跳舞的时候,音乐的节奏得恰到好处。
比如说,要是温度高了那么一点点,那丙烷这个小演员可能就会变得太“兴奋”,反应就会过头,产生一些不需要的东西。
要是温度低了呢,那就像是音乐节奏太慢,丙烷就没劲儿去进行脱氢反应了。
还有啊,压力在这个工艺里也是个关键的角色。
我看到装置上有一些压力表,指针稳稳地指着一个刻度。
老师傅说,压力就像是给小演员们设定的舞台空间。
压力太大,丙烷就会觉得太挤,到处乱撞,反应就会变得乱七八糟的。
压力太小呢,又像是舞台太空旷,丙烷之间的互动就不够,反应也不完全。
我在那儿听老师傅讲的时候,还发生了一个小插曲。
有个年轻的工人跑过来,慌慌张张地说有个小仪表好像有点不正常。
老师傅一听,眉头一皱,就赶紧走过去查看。
丙烷脱氢制丙烯技术分析
丙烷脱氢制丙烯技术分析发表时间:2018-08-07T09:18:25.380Z 来源:《建筑模拟》2018年第11期作者:李恒允张坤鹏[导读] 目前全球丙烯及其衍生物需求量不断增长,为了满足对丙烯日益增长的需求,丙烷脱氢制丙烯技术越来越受到重视。
山东东明石化集团有限公司摘要:目前全球丙烯及其衍生物需求量不断增长,为了满足对丙烯日益增长的需求,丙烷脱氢制丙烯技术越来越受到重视。
本文介绍了各种丙烷脱氢工艺技术的现状,主要从工程的角度,对催化脱氢工艺从操作方式、供热方式、操作条件、反应器、催化剂以及能耗和固定投资等不同方面进行对比分析,指出了各种工艺的优点和不足,并提出了发展方向。
关键词:丙烷;丙烯;脱氢工艺技术丙烯是一种重要的有机化工原料,用于生产聚丙烯、丙烯睛、丁醇、辛醇、环氧丙烷、异丙醇、丙苯、丙烯酸等产品[1]。
目前,丙烯的供应主要来自石脑油裂解制乙烯和石油催化裂化过程的副产品,世界上有66%的丙烯来自烃类蒸汽裂解制乙烯装置,32%来自炼油厂催化裂化装置,少量由丙烷脱氢和其他的烯烃转化和裂化反应得到[2-3]。
本文重点对各种丙烷脱氢制丙烯工艺从操作方式、供热方式、操作条件、反应器、催化剂以及能耗和固定投资等方面进行对比和评述。
目前已工业化的丙烷脱氢技术有UOP公司的Oleflex工艺、鲁姆斯公司的Catofin工艺、林德公司的Linde工艺、菲利浦石油公司的Star工艺、俄罗斯雅罗斯拉夫尔研究院与意大利Snamprogetti工程公司联合开发的FBD-3脱氢工艺[4,5],下面将分别从不同角度对其进行对比介绍。
1 操作方式丙烷催化脱氢各工艺按操作方式分为间歇式操作和连续式操作。
其中,Oleflex和FBD-3工艺属于连续性工艺,Catofin、Linde和Star工艺属于间歇式生产工艺[6-9]。
连续式操作在反应性能上要比间歇式操作优越。
连续式操作,无论是移动床还是流化床反应器,都能够保持反应均匀稳定,催化剂的活性和反应温度不随反应时间的推移而改变,可以通过连续补充催化剂的方式维持催化剂的稳定。
- 1、下载文档前请自行甄别文档内容的完整性,平台不提供额外的编辑、内容补充、找答案等附加服务。
- 2、"仅部分预览"的文档,不可在线预览部分如存在完整性等问题,可反馈申请退款(可完整预览的文档不适用该条件!)。
- 3、如文档侵犯您的权益,请联系客服反馈,我们会尽快为您处理(人工客服工作时间:9:00-18:30)。
Korean J. Chem. Eng., 24(6), 921-926 (2007)
SHORT COMMUNICATION
Repetitive control of CATOFIN process
Seung-Taek Seo, Wangyun Won*, Kwang Soon Lee*,†, Chansul Jung** and Seokho Lee**
†
Fig. 1. Process flow diagram of the CATOFIN process.
To whom correspondence should be addressed. E-mail: kslee@sogang.ac.kr
the set point tracking is the major task of the controller in the CATOFIN process. The reactors in the CATOFIN process are under repetitive (or cyclic) operation where the results of a previous run affect the operation of the upcoming runs. In a loose sense, however, the reactors
AbstractThe CATOFIN process is a propane dehydrogenation process for production of propylene. It uses multiple adiabatic fixed-bed reactors where dehydrogenation and regeneration (decoking) are performed alternatively over roughly ten minutes of period for each operation. Taking advantage of the periodic operation, the present research concerns the development of a repetitive control method to improve the operation of the CATOFIN process. The controller is designed to perform feedback action during the regeneration cycle and to perform only state estimation during the dehydrogenation cycle. To improve the performance while overcoming the nonlinearity of the process, a linearized timevarying process was derived from a first-principle model and used for the controller design. Key words: CATOFIN Process, Repetitive Control, Fixed-bed Reactor
922
S.-T. Seo et al.
can be said to undergo batch operation since some resetting operations are inserted between Dehyd and Regen cycles. It is obvious that an advanced industrial control technique like MPC (Model Predictive Control) is not adequate for the CATOFIN reactor since the process is not under a steady state operation. In this research, a repetitive control (RC) method has been developed for CATOFIN reactor operation as one of the essential modules of an on-line optimization system of the CATOFIN process. The RC method is a special control technique for repetitive processes [9,10]. It can perform not only real-time feedback control but also cycle-wise information feedback. Due to the latter action, it can achieve perfect tracking, overcoming cycle-wise repeated disturbances and model error. The RC method proposed in this research is based on the model obtained by linearization of a first-principle model around the operating trajectories in the previous cycle. The repetitive controller was devised to regulate the bed temperatures measured at two axial positions on desired values at the end of each Regen cycle. The flow rate and temperature of the feed air for the Regen cycle were chosen as the manipulated variables (MV’s). PROCESS DESCRIPTION 1. Reactions and Reactor Operation Eqs. (1) and (2) show the dominant reactions taking place during Dehyd and Regen, respectively [6].
INTRODUCTION Ethylene and propylene, the basic precursor feedstocks in the petrochemical industry, have been mainly produced by thermal cracking of naphtha, ethane and propane. Recently, the CATOFIN process has emerged as a competitive propylene production process due to its higher product selectivity, energy efficiency, and low operating cost with the advance of the catalyst [1]. The CATOFIN process consists of multiple parallel adiabatic fixed-bed reactors, where dehydrogenation (Dehyd) of propane and catalyst regeneration (Regen) by decoking are carried out alternatively over roughly ten minutes of period for each operation. During the Dehyd operation, bed temperature is gradually decreased by the endothermic reaction. Then the bed temperature is restored to the original state during the exothermic Regen period. By exquisite scheduling of the multiple reactor beds, Dehyd incessantly takes place in a same number of reactors so that propylene production can be continuous. Fig. 1 shows a process flow diagram of the CATOFIN process. However, optimal operation of the reactors in the CATOFIN process is a tricky issue because of complex dynamics caused by the unsteady operation and inherent nonlinearity. There have been a large number of studies on propane Dehyd and catalyst Regen from reaction kinetics to reactor dynamics and control. The references in [2-8] are only a part of them. However, the CATOFIN process is relatively new and the dynamics and control studies on the concerned reactor seem to be rare in the open literature according to the authors’ survey. In the industrial CATOFIN process, the main concern is to maintain the reactor operation at the optimum condition overcoming the gradual catalyst deactivation. This is a combined problem of optimization, on-line model identification, and control. The major mission of the controller is to steer the reactor to new set points dictated by the optimizer. Hence