冲压模具毕业设计英文原文和汉语翻译(完整版)
模具毕业设计外文翻译(英文+译文)
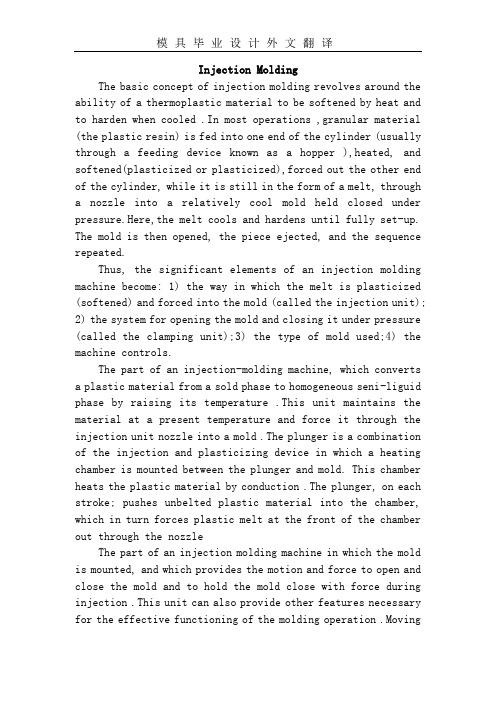
Injection MoldingThe basic concept of injection molding revolves around the ability of a thermoplastic material to be softened by heat and to harden when cooled .In most operations ,granular material (the plastic resin) is fed into one end of the cylinder (usually through a feeding device known as a hopper ),heated, and softened(plasticized or plasticized),forced out the other end of the cylinder, while it is still in the form of a melt, through a nozzle into a relatively cool mold held closed under pressure.Here,the melt cools and hardens until fully set-up. The mold is then opened, the piece ejected, and the sequence repeated.Thus, the significant elements of an injection molding machine become: 1) the way in which the melt is plasticized (softened) and forced into the mold (called the injection unit);2) the system for opening the mold and closing it under pressure (called the clamping unit);3) the type of mold used;4) the machine controls.The part of an injection-molding machine, which converts a plastic material from a sold phase to homogeneous seni-liguid phase by raising its temperature .This unit maintains the material at a present temperature and force it through the injection unit nozzle into a mold .The plunger is a combination of the injection and plasticizing device in which a heating chamber is mounted between the plunger and mold. This chamber heats the plastic material by conduction .The plunger, on each stroke; pushes unbelted plastic material into the chamber, which in turn forces plastic melt at the front of the chamber out through the nozzleThe part of an injection molding machine in which the mold is mounted, and which provides the motion and force to open and close the mold and to hold the mold close with force during injection .This unit can also provide other features necessary for the effective functioning of the molding operation .Movingplate is the member of the clamping unit, which is moved toward a stationary member. the moving section of the mold is bolted to this moving plate .This member usually includes the ejector holes and mold mounting pattern of blot holes or “T” slots .Stationary plate is the fixed member of the clamping unit on which the stationary section of the mold is bolted .This member usually includes a mold-mounting pattern of boles or “T” slots. Tie rods are member of the clamping force actuating mechanism that serve as the tension member of the clamp when it is holding the mold closed. They also serve as a gutted member for the movable plate .Ejector is a provision in the clamping unit that actuates a mechanism within the mold to eject the molded part(s) from the mold .The ejection actuating force may be applied hydraulically or pneumatically by a cylinder(s) attached to the moving plate, or mechanically by the opening stroke of the moving plate.Methods of melting and injecting the plastic differ from one machine to another and are constantly being implored .conventional machines use a cylinder and piston to do both jobs .This method simplifies machine construction but makes control of injection temperatures and pressures an inherently difficult problem .Other machines use a plasticizing extruder to melt the plastic and piston to inject it while some hare been designed to use a screw for both jobs :Nowadays, sixty percent of the machines use a reciprocating screw,35% a plunger (concentrated in the smaller machine size),and 5%a screw pot.Many of the problems connected with in ejection molding arise because the densities of polymers change so markedly with temperature and pressure. thigh temperatures, the density of a polymer is considerably cower than at room temperature, provided the pressure is the same.Therefore,if molds were filled at atmospheric pressure, “shrinkage” would make the molding deviate form the shape of the mold.To compensate for this poor effect, molds are filled at high pressure. The pressure compresses the polymer and allows more materials to flow into the mold, shrinkage is reduced and better quality moldings are produced.Cludes a mold-mounting pattern of bolt holes or “T” slots. Tie rods are members of the clamping force actuating mechanism that serve as the tension members of clamp when it is holding the mold closed. Ejector is a provision in the calming unit that actuates a mechanism within the mold to eject the molded part(s) form the mold. The ejection actuating force may be applied hydraulically or pneumatically by a cylinder(s) attached to the moving plate, or mechanically by the opening stroke of the moving plate.The function of a mold is twofold: imparting the desired shape to the plasticized polymer and cooling the injection molded part. It is basically made up of two sets of components: the cavities and cores and the base in which the cavities and cores are mounted. The mold ,which contains one or more cavities, consists of two basic parts :(1) a stationary molds half one the side where the plastic is injected,(2)Moving half on the closing or ejector side of the machine. The separation between the two mold halves is called the parting line. In some cases the cavity is partly in the stationary and partly in the moving section. The size and weight of the molded parts limit the number of cavities in the mold and also determine the machinery capacity required. The mold components and their functions are as following:(1)Mold Base-Hold cavity (cavities) in fixed, correctposition relative to machine nozzle.(2)Guide Pins-Maintain Proper alignment of entry into moldinterior.(3)Spree Bushing (spree)-Provide means of entry into moldinterior.(4)Runners-Conroy molten plastic from spree to cavities.(5)Gates-Control flow into cavities.(6)Cavity (female) and Force (male)-Control the size,shape and surface of mold article.(7)Water Channels-Control the temperature of mold surfacesto chill plastic to rigid state.(8)Side (actuated by came, gears or hydrauliccylinders)-Form side holes, slots, undercuts and threaded sections.(9)Vent-Allow the escape of trapped air and gas.(10)Ejector Mechanism (pins, blades, stripper plate)-Ejectrigid molded article form cavity or force.(11)Ejector Return Pins-Return ejector pins to retractedposition as mold closes for next cycle.The distance between the outer cavities and the primary spree must not be so long that the molten plastic loses too much heat in the runner to fill the outer cavities properly. The cavities should be so arranged around the primary spree that each receives its full and equal share of the total pressure available, through its own runner system (or the so-called balanced runner system).The requires the shortest possible distance between cavities and primary sprue, equal runner and gate dimension, and uniform culling.注射成型注射成型的基本概念是使热塑性材料在受热时熔融,冷却时硬化,在大部分加工中,粒状材料(即塑料树脂)从料筒的一端(通常通过一个叫做“料斗”的进料装置)送进,受热并熔融(即塑化或增塑),然后当材料还是溶体时,通过一个喷嘴从料筒的另一端挤到一个相对较冷的压和封闭的模子里。
冲压弯曲件冲压模具设计说明书(包含中英翻译)
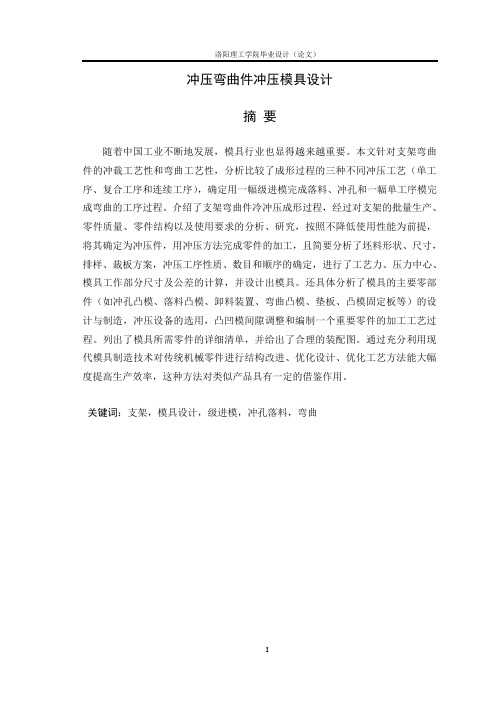
冲压弯曲件冲压模具设计摘要随着中国工业不断地发展,模具行业也显得越来越重要。
本文针对支架弯曲件的冲裁工艺性和弯曲工艺性,分析比较了成形过程的三种不同冲压工艺(单工序、复合工序和连续工序),确定用一幅级进模完成落料、冲孔和一幅单工序模完成弯曲的工序过程。
介绍了支架弯曲件冷冲压成形过程,经过对支架的批量生产、零件质量、零件结构以及使用要求的分析、研究,按照不降低使用性能为前提,将其确定为冲压件,用冲压方法完成零件的加工,且简要分析了坯料形状、尺寸,排样、裁板方案,冲压工序性质、数目和顺序的确定,进行了工艺力、压力中心、模具工作部分尺寸及公差的计算,并设计出模具。
还具体分析了模具的主要零部件(如冲孔凸模、落料凸模、卸料装置、弯曲凸模、垫板、凸模固定板等)的设计与制造,冲压设备的选用,凸凹模间隙调整和编制一个重要零件的加工工艺过程。
列出了模具所需零件的详细清单,并给出了合理的装配图。
通过充分利用现代模具制造技术对传统机械零件进行结构改进、优化设计、优化工艺方法能大幅度提高生产效率,这种方法对类似产品具有一定的借鉴作用。
关键词:支架,模具设计,级进模,冲孔落料,弯曲Stamping Bending Stamping Mold DesignABSTRACTWith China's industrial developing constantly, mold industry is becoming more and more important. Based on the stent bending blanking process and bending process, Comparative analysis of the process of forming three different stamping process (single processes, complex processes and continuous processes) confirm completion of the blanking, punching and a single procedure completed the bending modulus processes. On the cover of the cold bending stents,right after the cover of the mass production, quality components, and the use of structural components of the analysis, research, in line with lower performance prerequisite to the identification of stampings, Stamping method used to complete the processing components, and a brief analysis of the blank shape, size, layout, the conference board, stamping processes in nature, number and sequence determination. For the process, the center of pressure, the die size and the tolerance of the calculation, design mold. Also analyzes the mold of the main components (such as mould, punch hole punch, unloader device, punch, plate, bending plate etc) design and manufacturing, stamping equipment selection, punch-gap adjustment and establishment of a vital parts machining process. Die requirements set out a detailed list of parts, and gives a reasonable assembly. By fully utilizing modern manufacturing technology to mold traditional mechanical parts for structural improvements, design optimization, process optimization methods can greatly enhance production efficiency, the method of similar products have some reference.KEY WORDS: stents,mold design,progressive die,punching blanking, bending目录前言 (1)第1章对加工零件的工艺分析 (5)1.1零件分析 (5)1.1.1 冲压件的工艺分析 (5)1.1.2 分析比较和确定工艺方案 (6)1.1.3 弯曲件的工艺分析 (7)第2章冲裁模 (8)2.1 冲压模具的工艺分析与设计计算 (8)2.2 工作力的计算 (10)2.2.1 落料力 (10)2.2.2 冲孔力 (10)2.2.3 卸料力 (11)2.2.4 推料力 (11)2.2.5 冲侧刃缺口的力 (12)2.2.6 总冲压力 (12)2.3 确定模具压力中心 (12)2.4确定凸、凹模刃口尺寸 (15)2.4.1 冲孔部分 (16)2.4.2 落料部分 (17)2.5 成型零部件的结构设计 (18)2.5.1冲孔凸模结构设计 (18)2.5.2冲孔凸模结构设计 (19)2.5.3凹模结构设计 (19)2.6 模具的整体设计 (20)2.6.1选择模具结构形式 (20)2.6.2操作方式 (20)2.6.3模架类型 (21)2.6.4定位方式的选择 (21)2.6.5卸料和出料方式的选择 (21)2.6.6导向方式选择 (21)2.6.7定位零件设计 (21)2.6.8导料板设计 (21)2.6.9卸料板设计 (22)2.6.10垫板设计 (23)2.6.11模柄选择 (24)2.6.12凸模固定板的设计 (25)2.6.13导柱导套选择 (26)2.6.14模座选择 (26)2.6.15螺钉、销钉的选用 (27)2.6.16装配图设计 (27)2.6.17模架的选取 (27)2.6.18冲压设备的选择 (28)第3章弯曲模 (29)3.1冲压零件的工艺分析 (29)3.2模具结构 (29)3.3必要的计算 (29)3.3.1弯曲力的计算 (30)3.3.2弹顶器的计算 (31)3.3.3回弹量的确定 (31)3.3.4弯曲凸模的圆角半径 (31)3.3.5弯曲凹模的圆角半径及其工作部分的深度 (31)3.3.6弯曲凸模和凹模之间的间隙 (32)3.3.7弯曲凸模和凹模宽度尺寸的计算 (32)3.4模具总体设计 (33)3.4.1凹模结构设计 (33)3.4.2凸模结构设计 (34)3.4.3定位板结构设计 (34)3.4.4模柄选择 (35)3.4.5模架的选取 (35)3.4.6销钉的选用 (36)3.4.7压力机的选取 (36)3.4.8装配图设计 (37)第4章模具制造技术要求 (38)4.1表面粗糙度及标准 (38)4.2加工精度 (39)4.2.1尺寸偏差 (39)4.2.2形位公差 (39)4.2.3配合要求 (39)结论 (41)谢辞 (42)参考文献 (43)外文资料翻译 (45)前言冷冲压是利用安装在压力机上的冲模对材料施加压力,使其产生分离或塑性变形,从而获得所需要零件(俗称冲压件或冲件)的一种压力方法。
冲压模具成型外文翻译参考文献
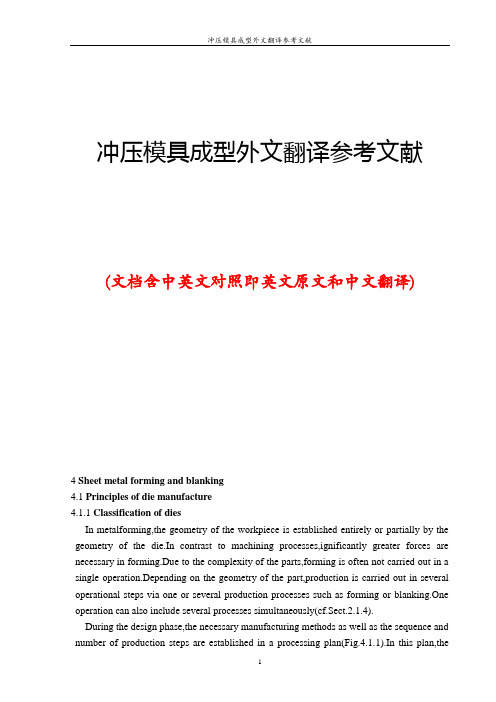
冲压模具成型外文翻译参考文献(文档含中英文对照即英文原文和中文翻译)4 Sheet metal forming and blanking4.1 Principles of die manufacture4.1.1 Classification of diesIn metalforming,the geometry of the workpiece is established entirely or partially by the geometry of the die.In contrast to machining processes,ignificantly greater forces are necessary in forming.Due to the complexity of the parts,forming is often not carried out in a single operation.Depending on the geometry of the part,production is carried out in several operational steps via one or several production processes such as forming or blanking.One operation can also include several processes simultaneously(cf.Sect.2.1.4).During the design phase,the necessary manufacturing methods as well as the sequence and number of production steps are established in a processing plan(Fig.4.1.1).In this plan,theavailability of machines,the planned production volumes of the part and other boundary conditions are taken into account.The aim is to minimize the number of dies to be used while keeping up a high level of operational reliability.The parts are greatly simplified right from their design stage by close collaboration between the Part Design and Production Departments in order to enable several forming and related blanking processes to be carried out in one forming station.Obviously,the more operations which are integrated into a single die,the more complex the structure of the die becomes.The consequences are higher costs,a decrease in output and a lower reliability.Fig.4.1.1 Production steps for the manufacture of an oil sumpTypes of diesThe type of die and the closely related transportation of the part between dies is determined in accordance with the forming procedure,the size of the part in question and the production volume of parts to be produced.The production of large sheet metal parts is carried out almost exclusively using single sets of dies.Typical parts can be found in automotive manufacture,the domestic appliance industry and radiator production.Suitable transfer systems,for example vacuum suction systems,allow the installation of double-action dies in a sufficiently large mounting area.In this way,for example,the right and left doors of a car can be formed jointly in one working stroke(cf.Fig.4.4.34).Large size single dies are installed in large presses.The transportation of the parts from oneforming station to another is carried out mechanically.In a press line with single presses installed one behind the other,feeders or robots can be used(cf.Fig.4.4.20 to 4.4.22),whilst in large-panel transfer presses,systems equipped with gripper rails(cf.Fig.4.4.29)or crossbar suction systems(cf.Fig.4.4.34)are used to transfer the parts.Transfer dies are used for the production of high volumes of smaller and medium size parts(Fig.4.1.2).They consist of several single dies,which are mounted on a common base plate.The sheet metal is fed through mostly in blank form and also transported individually from die to die.If this part transportation is automated,the press is called a transfer press.The largest transfer dies are used together with single dies in large-panel transfer presses(cf.Fig.4.4.32).In progressive dies,also known as progressive blanking dies,sheet metal parts are blanked in several stages;generally speaking no actual forming operation takes place.The sheet metal is fed from a coil or in the form of metal ing an appropriate arrangement of the blanks within the available width of the sheet metal,an optimal material usage is ensured(cf.Fig.4.5.2 to 4.5.5). The workpiece remains fixed to the strip skeleton up until the laFig.4.1.2 Transfer die set for the production of an automatic transmission for an automotive application-st operation.The parts are transferred when the entire strip is shifted further in the work flow direction after the blanking operation.The length of the shift is equal to the center line spacing of the dies and it is also called the step width.Side shears,very precise feeding devices or pilot pins ensure feed-related part accuracy.In the final production operation,the finished part,i.e.the last part in the sequence,is disconnected from the skeleton.A field of application for progressive blanking tools is,for example,in the production of metal rotors or stator blanks for electric motors(cf.Fig.4.6.11 and 4.6.20).In progressive compound dies smaller formed parts are produced in several sequential operations.In contrast to progressive dies,not only blanking but also forming operations areperformed.However, the workpiece also remains in the skeleton up to the last operation(Fig.4.1.3 and cf.Fig.4.7.2).Due to the height of the parts,the metal strip must be raised up,generally using lifting edges or similar lifting devices in order to allow the strip metal to be transported mechanically.Pressed metal parts which cannot be produced within a metal strip because of their geometrical dimensions are alternatively produced on transfer sets.Fig.4.1.3 Reinforcing part of a car produced in a strip by a compound die setNext to the dies already mentioned,a series of special dies are available for special individual applications.These dies are,as a rule,used separately.Special operations make it possible,however,for special dies to be integrated into an operational Sequence.Thus,for example,in flanging dies several metal parts can be joined together positively through the bending of certain metal sections(Fig.4.1.4and cf.Fig.2.1.34).During this operation reinforcing parts,glue or other components can be introduced.Other special dies locate special connecting elements directly into the press.Sorting and positioning elements,for example,bring stamping nuts synchronised with the press cycles into the correct position so that the punch heads can join them with the sheet metal part(Fig.4.1.5).If there is sufficient space available,forming and blanking operations can be carried out on the same die.Further examples include bending,collar-forming,stamping,fine blanking,wobble blanking and welding operations(cf.Fig.4.7.14 and4.7.15).Fig.4.1.4 A hemming dieFig.4.1.5 A pressed part with an integrated punched nut4.1.2 Die developmentTraditionally the business of die engineering has been influenced by the automotive industry.The following observations about the die development are mostly related to body panel die construction.Essential statements are,however,made in a fundamental context,so that they are applicable to all areas involved with the production of sheet-metal forming and blanking dies.Timing cycle for a mass produced car body panelUntil the end of the 1980s some car models were still being produced for six to eight years more or less unchanged or in slightly modified form.Today,however,production time cycles are set for only five years or less(Fig.4.1.6).Following the new different model policy,the demands ondie makers have also changed prehensive contracts of much greater scope such as Simultaneous Engineering(SE)contracts are becoming increasingly common.As a result,the die maker is often involved at the initial development phase of the metal part as well as in the planning phase for the production process.Therefore,a muchbroader involvement is established well before the actual die development is initiated.Fig.4.1.6 Time schedule for a mass produced car body panelThe timetable of an SE projectWithin the context of the production process for car body panels,only a minimal amount of time is allocated to allow for the manufacture of the dies.With large scale dies there is a run-up period of about 10 months in which design and die try-out are included.In complex SE projects,which have to be completed in 1.5 to 2 years,parallel tasks must be carried out.Furthermore,additional resources must be provided before and after delivery of the dies.These short periods call for pre-cise planning,specific know-how,available capacity and the use of the latest technological and communications systems.The timetable shows the individual activities during the manufacturing of the dies for the production of the sheet metal parts(Fig.4.1.7).The time phases for large scale dies are more or less similar so that this timetable can be considered to be valid in general.Data record and part drawingThe data record and the part drawing serve as the basis for all subsequent processing steps.They describe all the details of the parts to be produced. The information given in theFig.4.1.7 Timetable for an SE projectpart drawing includes: part identification,part numbering,sheet metal thickness,sheet metal quality,tolerances of the finished part etc.(cf.Fig.4.7.17).To avoid the production of physical models(master patterns),the CAD data should describe the geometry of the part completely by means of line,surface or volume models.As a general rule,high quality surface data with a completely filleted and closed surface geometry must be made available to all the participants in a project as early as possible.Process plan and draw developmentThe process plan,which means the operational sequence to be followed in the production of the sheet metal component,is developed from the data record of the finished part(cf.Fig.4.1.1).Already at this point in time,various boundary conditions must be taken into account:the sheet metal material,the press to be used,transfer of the parts into the press,the transportation of scrap materials,the undercuts as well as thesliding pin installations and their adjustment.The draw development,i.e.the computer aided design and layout of the blank holder area of the part in the first forming stage–if need bealso the second stage–,requires a process planner with considerable experience(Fig.4.1.8).In order to recognize and avoid problems in areas which are difficult to draw,it is necessary to manufacture a physical analysis model of the draw development.With this model,theforming conditions of the drawn part can be reviewed and final modifications introduced,which are eventually incorporated into the data record(Fig.4.1.9).This process is being replaced to some extent by intelligent simulation methods,through which the potential defects of the formed component can be predicted and analysed interactively on the computer display.Die designAfter release of the process plan and draw development and the press,the design of the die can be started.As a rule,at this stage,the standards and manufacturing specifications required by the client must be considered.Thus,it is possible to obtain a unified die design and to consider the particular requests of the customer related to warehousing of standard,replacement and wear parts.Many dies need to be designed so that they can be installed in different types of presses.Dies are frequently installed both in a production press as well as in two different separate back-up presses.In this context,the layout of the die clamping elements,pressure pins and scrap disposal channels on different presses must be taken into account.Furthermore,it must be noted that drawing dies working in a single-action press may be installed in a double-action press(cf.Sect.3.1.3 and Fig.4.1.16).Fig.4.1.8 CAD data record for a draw developmentIn the design and sizing of the die,it is particularly important to consider the freedom of movement of the gripper rail and the crossbar transfer elements(cf.Sect.4.1.6).These describe the relative movements between the components of the press transfer system and the die components during a complete press working stroke.The lifting movement of the press slide,the opening and closing movements of the gripper rails and the lengthwise movement of the whole transfer are all superimposed.The dies are designed so that collisions are avoided and a minimum clearance of about 20 mm is set between all the moving parts.4 金属板料的成形及冲裁4. 模具制造原理4.1.1模具的分类在金属成形的过程中,工件的几何形状完全或部分建立在模具几何形状的基础上的。
模具设计及制作专业毕业设计外文翻译-中英文对照

IntroductionAlthough the Greek philosopher Democritus had postulated the existence of atoms in the first century BC and Dalton’s atomic theory of 1807 laid the basis for the existence of atoms before the turn of the twentieth century. Indeed, at that time an influential school of German physicists led by Ernst Mach considered the atomic model to be merely a useful picture with no basis in reality.1.1 THE EXISTENCE OF ATOMSThe situation was dramatically changed by an explosion of experimental investigation over the fifteen years between 1897 and 1912. in the 1870s, technical improvements in the construction of vacuum pumps had made possible the investigation of electrical phenomenon in evacuated tubes and the discovery of invisible rays which traveled between an electrically negative electrode (cathode) and an electrically positive electrode (anode) in such a tube.These rays came to be known as cathode rays. At first there was considerable controversy over their nature, but a series of experiments carried out by J.J. Thomson in 1897 demonstrated conclusively that the cathode rays consisted of a stream of negatively charged particles, presumably emitted by atoms in the cathode (Fig. 1.1).Thomson’s measurements of the deflection of the rays by electric and magnetic fields enabled the speed of the particles to be measured and also the ratio of the charge of a particle to its mass. By the turn of the century, the charge-mass radio of these particles, which came to be called electrons, could be measured to quite high precision.However, to give absolute values of the charge and mass, experiments of a different type were required. The most successful were investigations where macroscopic particles such as oil droplets were charged in some way and their motion in electric fields observed. A relatively straightforward measurement of the mass of the oil droplets enabled the charge of the charge of the electron to be measured. The famous experiments carried out by Millikan between 1909 and 1916 gave a value for this charge as 1.592±.002×10-19 coulomb, less than 1 percent lower than that accepted today. This, combined with Thomson’s results, gave a value for the electron’s mass of approximately 9×10-31 kg.Fig. 1.1Schematic diagram of J.J. Thomson’s cathode ray tube Electrons emitted by the cathode are accelerated through the anode. The beam of electrons hits the phosphorescent screen, producing a luminous spot.The measurement of electric charge made possible a direct measurement of atomic masses. Back in 1830, Faraday had carried out experiments on electrolysis. He had used his results to suggest that if matter were atomic, then electricity should also be atomic, but the converse is also true.The flow of electric current between two metallic plates in an electrolyte results in a measurable in increase in the mass of one electrode. The mass of metal deposited per unit charge flowing can be measured. Assuming that the motion of atoms between electrodes in due to the fact that each atom in the electrolyte carries a specified number of excess electrons, the mass of a single atom can be calculated.The investigation of cathode ray tubes produced another important line of experimentation. In 1895 Röntgen had discovered that cathode rays impinging on glass or metal produced a new type of ray –the X-ray. These rays were shown to have wave-like properties and in 1899 their wavelength was estimated by the Dutch physicists Haga and Wind to be of the order of 10-10m, using diffraction at a v-shaped slit. In 1906 Marx demonstrated that the speed of the waves was equal to that of light to within experimental error, and it became generally accepted that X-rays were electromagnetic radiation like light, but with much shorter wavelengths. In 1912 Laue in Germany and Bragg in England demonstrated the diffraction of X-rays by the regular pattern of atoms in a crystal lattice. These diffraction patterns gave the first direct evidence of the existence of atoms and of their sizes. An example is shown in Fig. 1.2.Fig. 1.2Laue diffraction pattern caused by the diffraction of X-rays by the regular lattice of atoms in rock salt.In 1897, Rutherford had found that pieces of the naturally occurring element uranium emitted two types of ray which were termed α rays and βrays. Both could be deflected by electric and magnetic fields and were therefore presumed to consist of charge particles. The βparticles were found to have the same charge and mass as cathode ray electrons, so were assumed to be electrons. The αrays, on the other hand, were considerably more massive. Measurements of their charge and mass suggested that they consisted of helium atoms from which two electrons had been removed. This was confirmed by Rutherford and Royds in 1909, who fired α rays into a sealed and evacuated vessel and showed that helium accumulated in it. The evidence was conclusive that an α particle consisted of a helium atom from which two electrons had been removed.This experiment also confirmed suggestions about the physical meaning of the atomic number Z. This number had been introduced to define the order of elements in the periodic table. Hydrogen had Z=1, helium Z=2and so on. The identification of α particles with helium atoms suggested that Z defined the number of electrons in a particular atom.By 1912, therefore, direct evidence existed on the mass of individual atoms and the size of these atoms. Even more interestingly, the electron appeared to be a constituent of atom, suggesting some internal structure.1.2 THE SIZE OF ATOMSTurning from the historical development of the subject, it is worthwhile to sum up the measurement of atomic masses and dimensions.As mentioned above, direct measurement of atomic masses can be made using electrolysis. A typical electrolysis cell might consist of two copper electrodes immersed in a bath of copper sulphate (Fig. 1.3). A potential difference between the electrodes causes a current to flow an the deposition of copper on the cathode.Fig. 1.3 Electrolytic cell. The anode and cathode are immersed in an electrolyte such as copper sulphate solution. Positively charged copper ions are attracted to the cathode and are deposited there.Several assumptions have to be made. First, it is assumed that in solution the copper sulphate crystals split up, giving free atoms of copper and that these free atoms have an excess positive charge.Second, using chemical knowledge that copper is reasonable extrapolation from the chemical valence theory, if it is assumed that chemical bonds result from the exchange of electrons, and that the lightest atom, hydrogen, has only a single electron to exchange. A copper atom in this state is referred to as being doubly ionized, Cu++. A final assumption is that all copper ions attracted to the cathode stick to it and gain further electrons to become electrically neutral again. The experiment then consists of driving a known quantity of electricity through the cell and measuring the increase in mass of the cathode. Experiments can be carried out with different elements and results confirm the atomic theory and the theory of valence. Most interesting for our discuss is the calculation of the mass of an atom of hydrogen, the lightest element. This turns out to be 1.67×10-27 kg, approximately 1800 times that of an electron.Knowing atomic masses, and the density of materials, it is straightforward to obtain values for atomic dimensions. The only problem is that unless the atoms in a sample of material are arranged in a regular pattern, the answer is not very meaningful. For crystalline substances, X-ray diffraction enable the arrangement of atoms to be discovered. The dimensions of the crystal structure can then be calculated.Fig. 1.4 A single cell of the simple cubic lattice of sodium chloride. The lattice is held together by the attraction between the positively charged sodium ion and the negatively charged chlorine ion.For example, crystals of rock salt (sodium chloride, NaCl) are found to have a cubic structure, with sodium and chlorine ions on alternate corners (Fig. 1.4). If M is the kilogram molecular weight of NaCl and ρ the density of the crystal, the volume of one kg-molecule is/V M ρ=There are 2N atoms is one kg-molecule, where N is Avogadro ’s number. Therefore the distance between the centres of atoms, d is given by:3/(2)d M N ρ=For sodium chloride, this works out as 2.8×10-10m and similar results are obtained for other crystals.Of course, such calculations only tell us the distance between the centres of the atoms and hence the maximum possible size for an atom. To go further, it is necessary to investigate the structure of the atom itself.2.3 THE NUCLEAR MODEL OF THE ATOMFig. 2.2 Classical models of the atom. (a) Thomson’s model. Small, negatively charged electrons are held in a dense, positively charged body.(b) Rutherford’s model. The vast majority of the mass and all the positive charge are concentrated in a relatively tiny nucleus, surrounded by electrons. In both pictures the size of the electrons and of the nucleus are exaggerated. The nucleus should be at least 1000 times smaller and the electrons many times smaller again.In order to explain the result, Rutherford proposed a new model in which all the positive charge and most of the mass of the atom resided in a central nucleus, surrounded by electrons orbiting in free space. The size of the nucleus would be small compared with the size of the atom (Fig.2.2(b)). This model would give a qualitative explanation for Geiger and Marsden’s results as most of the αparticles would pass through the atom without encountering any matter, but a very few would collide with the massive nucleus. However, much more importantly, this model gives a precise quantitative agreement between theory and experiment.Because of the seminal nature of this model, it is worthwhile looking at Rutherford’s analysis in detail. Only classical of physics is required .Fig 2.3Path of αparticle (charge +2e) in the field of the nucleus (charge +Ze). The nucleus is at the origin and is very much more massive than the α particle. The force F is due to electrostatic repulsion.The analysis of the scattering experiment falls into two parts. First, it it necessary to obtain an expression for the deflection of a single αparticle as a function of its kinetic energy and its trajectory relative to the nucleus. The particle and the nucleus are assumed to be very small, and the nucleus is assumed to have a positive charge Ze where e is the electronic charge and Z the atomic number. The α particle has a charge of +2e and the force between it and the nucleus is given by Coulomb’s law. Figure 2.3 shows through situation, with the nucleus situated at the origin. The α particle starts far enough away from the nucleus for the interaction force to be negligible and travels parallel to the χ-axis. An important parameter of the motion is the impact parameter, b, which defines the minimum distance between the nucleus and the particle if the particle were mot deflected.Electrostatic repulsion means that the particle is deflected through an angle Θ and it is obvious that the smaller the value of b, the greater is the value of Θ.It is now possible to work out a value for Θ in terms of b and the kinetic energy of the particle T. Since the mass of the nucleus is much greater than that of the α particle, the kinetic energy and hence the speed of the particle before and after deflection remains the same. However the particle ’s direction of motion has changed and the law of conservation of momentum gives an expression for the absolute value of the change in momentum (Fig.2.4)()212sin /2p p p m υ∆=-=Θ (2.1)Where m is the mass of the particle, and υ its speed.From Newton ’s second law,this change of momentum must be equal to the force acting on the particle, integrated over the whole time that the particle is in the field of the nucleus. Therefore,02sin(/2)p m Fdt υ∞∆=Θ=⎰ (2.2) Figure 2.3shows the direction of F a particular position of the particle, defined by through angle φ, as shown, by symmetry, it can be seen that the integral in (2.2) is given by00cos I Fdt F dt ϕ∞∞==⎰⎰ (since the integral of the component parallel to the χ-axis, F sin φ, must be zero, by symmetry ).Fig 2.4 Change in momentum of an α particle during interaction with through nucleus.A change of variables for integration enables (2.2) to be rewritten:()()/2()/22sin /2cos (/)m F dt d d ππυϕϕϕ-Θ--ΘΘ=⎰ (2.3)(see Fig 2.3 for the changed limits of integration).Finally, (dt/d φ) is equal to 1/ω where ω is the angular speed of the particle about the origin. Since the force acting on the particle is radial, the angular momentum of the particle is the same for any value of φ, and ω must be given by the equation2mr m b ωυ=Therefore2(/)/dt d r b ϕυ=Coulomb ’s law gives2202/4F Ze r πε=so that substituting in (2.3) and integrating through right hand side gives an expression for Θ in terms of υ and b220cot(/2)(2/)m Ze b πευΘ= (2.4)or, in terms of the kinetic energy T of the particle20cot(/2)(4/)T Ze b πεΘ= (2.5)This gives an equation for the scattering angle in terms of the kinetic energy and impact parameter of the particle and of the charge on the nucleus, Ze.介绍虽然希腊哲学家德谟克利特曾推测了在公元前一世纪原子的存在和道尔顿的原子理论1807年奠定了原子的存在,在20世纪之交以前。
冲压模具外文英语文献翻译
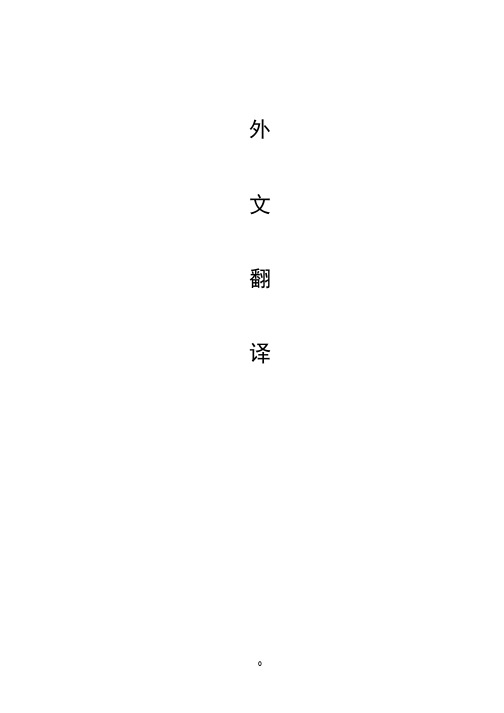
外文翻译Heat Treatment of Die and Mould Oriented Concurrent Design LI Xiong,ZHANG Hong-bing,RUAN Xue —yu,LUO Zhong —hua,ZHANG YanTraditional die and mould design,mainly by experience or semi —experience ,is isolated from manufacturing process.Before the design is finalized ,the scheme of die and mould is usually modified time and again ,thus some disadvantages come into being,such as long development period,high cost and uncertain practical effect.Due to strong desires for precision,service life,development period and cost,modern die and mould should be designed and manufactured perfectly.Therefore more and more advanced technologies and innovations have been applied,for example,concurrent engineering,agile manufacturing virtual manufacturing,collaborative design,etc.Heat treatment of die and mould is as important as design,manufacture and assembly because it has a vital effect on manufacture ,assembly and service life .Design and manufacture of die and mould have progressed rapidly ,but heat treatment lagged seriously behind them .As die and mould industry develops ,heat treatment must ensure die and mould there are good state of manufacture ,assembly and wear —resistant properties by request. Impertinent heat treatment can influence die and mould manufacturing such as over —hard and —soft and assembly .Traditionally the heat treatment process was made out according to the methods and properties brought forward Abstract:Many disadvantages exist in the traditional die design method which belongsto serial pattern. It is well known that heat treatment is highly important to thedies. A new idea of concurrent design for heat treatment process of die andmould was developed in order to overcome the existent shortcomings of heattreatment process. Heat treatment CAD/CAE was integrated with concurrentcircumstance and the relevant model was built. These investigations canremarkably improve efficiency, reduce cost and ensure quality of R and D forproducts.Key words:die design; heat treatment; mouldby designer.This could make the designers of die and mould and heat treatment diverge from each other,for the designers of die and mould could not fully realize heat treatment process and materials properties,and contrarily the designers rarely understood the service environment and designing thought. These divergences will impact the progress of die and mould to a great extent. Accordingly,if the process design of heat treatment is considered in the early designing stage,the aims of shortening development period,reducing cost and stabilizing quality will be achieved and the sublimation of development pattern from serial to concurrent will be realized.Concurrent engineering takes computer integration system as a carrier,at the very start subsequent each stage and factors have been considered such as manufacturing,heat treating,properties and so forth in order to avoid the error.The concurrent pattern has dismissed the defect of serial pattern,which bring about a revolution against serial pattern.In the present work.the heat treatment was integrated into the concurrent circumstance of the die and mould development,and the systemic and profound research was performed.1 Heat Treatment Under Concurrent CircumstanceThe concurrent pattern differs ultimately from the serial pattern(see Fig.1).With regard to serial pattern,the designers mostly consider the structure and function of die and mould,yet hardly consider the consequent process,so that the former mistakes are easily spread backwards.Meanwhile,the design department rarely communicates with the assembling,cost accounting and sales departments.These problems certainly will influence the development progress of die and mould and the market foreground.Whereas in the concurrent pattern,the relations among departments are close,the related departments all take part in the development progress of die and mould and have close intercommunion with purchasers.This is propitious to elimination of the conflicts between departments,increase the efficiency and reduce the cost.Heat treatment process in the concurrent circumstance is made out not after blueprint and workpiece taken but during die and mould designing.In this way,it is favorable to optimizing the heat treatment process and making full use of the potential of the materials.2 Integration of Heat Treatment CAD/CAE for Die and MouldIt can be seen from Fig.2 that the process design and simulation of heat treatment are the core of integration frame.After information input via product design module and heat treatment process generated via heat treatment CAD and heat treatment CAE module will automatically divide the mesh for parts drawing,simulation temperature field microstructure analysis after heat—treatment and the defect of possible emerging (such as overheat,over burning),and then the heat treatment process is judged if the optimization is made according to the result reappeared by stereoscopic vision technology.Moreover tool and clamping apparatus CAD and CAM are integrated into this system.The concurrent engineering based integration frame can share information with other branch.That makes for optimizing the heat treatment process and ensuring the process sound.2.1 3-D model and stereoscopic vision technology for heat treatmentThe problems about materials,structure and size for die and mould can be discovered as soon as possible by 3-D model for heat treatment based on the shape of die and mould.Modeling heating condition and phase transformation condition for die and mould during heat treatment are workable,because it has been broken through for the calculation of phase transformation thermodynamics,phase transformation kinetics,phase stress,thermal stress,heat transfer,hydrokinetics etc.For example,3-D heat—conducting algorithm models for local heating complicated impression and asymmetric die and mould,and M ARC software models for microstructure transformation was used.Computer can present the informations of temperature,microstructure and stress at arbitrary time and display the entire transformation procedure in the form of 3-D by coupling temperature field,microstructure field and stress field.If the property can be coupled,various partial properties can be predicted by computer.2.2 Heat treatment process designDue to the special requests for strength,hardness,surface roughness and distortion during heat treatment for die and mould,the parameters including quenching medium type,quenching temperature and tempering temperature and time,must be properlyselected,and whether using surface quenching or chemical heat treatment the parameters must be rightly determined.It is difficult to determine the parameters by computer fully.Since computer technology develops quickly in recent decades,the difficulty with large—scale calculation has been overcome.By simulating and weighing the property,the cost and the required period after heat treatment.it is not difficult to optimize the heat treatment process.2.3 Data base for heat treatmentA heat treatment database is described in Fig.3.The database is the foundation of making out heat treatment process.Generally,heat treatment database is divided into materials database and process database.It is an inexorable trend to predict the property by materials and process.Although it is difficult to establish a property database,it is necessary to establish the database by a series of tests.The materials database includes steel grades,chemical compositions,properties and home and abroad grades parallel tables.The process database includes heat treatment criterions,classes,heat preservation time and cooling velocity.Based on the database,heat treatment process can be created by inferring from rules.2.4 Tool and equipment for heat treatmentAfter heat treatment process is determined,tool and equipment CAD/CAE systemtransfers the information about design and manufacture to the numerical control device.Through rapid tooling prototype,the reliability of tool and the clamping apparatus can be judged.The whole procedure is transferred by network,in which there is no man—made interference.3 Key Technique3.1 Coupling of temperature,microstructure,stress and propertyHeat treatment procedure is a procedure of temperature-microstructure—stress interaction.The three factors can all influence the property (see Fig.4).During heating and cooling,hot stress and transformation will come into being when microstructure changes.Transformation temperature-microstructure and temperature—microstructure—and stress-property interact on each other.Research on the interaction of the four factors has been greatly developed,but the universal mathematic model has not been built.Many models fit the test nicely,but they cannot be put into practice.Difficulties with most of models are solved in analytic solution,and numerical method is employed so that the inaccuracy of calculation exists.Even so,comparing experience method with qualitative analysis,heat treatment simulation by computer makes great progress.3.2 Establishment and integration of modelsThe development procedure for die and mould involves design,manufacture,heat treatment,assembly,maintenance and so on.They should have own database and mode1.They are in series with each other by the entity—relation model.Through establishing and employing dynamic inference mechanism,the aim of optimizing design can be achieved.The relation between product model and other models was built.The product model will change in case the cell model changes.In fact,it belongs to the relation of data with die and mould.After heat treatment model is integrated into the system,it is no more an isolated unit but a member which is close to other models in the system.After searching,calculating and reasoning from the heat treatment database,procedure for heat treatment,which is restricted by geometric model,manufacture model for die and mould and by cost and property,is obtained.If the restriction is disobeyed,the system will send out the interpretative warning.All design cells are connected by communication network.3.3 Management and harmony among membersThe complexity of die and mould requires closely cooperating among item groups.Because each member is short of global consideration for die and mould development,they need to be managed and harmonized.Firstly,each item group should define its own control condition and resource requested,and learn of the request of up- and-down working procedure in order to avoid conflict.Secondly,development plan should be made out and monitor mechanism should be established.The obstruction can be duly excluded in case the development is hindered.Agile management and harmony redound to communicating information,increasing efficiency,and reducing redundancy.Meanwhile it is beneficial for exciting creativity,clearing conflict and making the best of resource.4 Conclusions(1) Heat treatment CAD/CAE has been integrated into concurrent design for die and mould and heat treatment is graphed,which can increase efficiency,easily discover problems and clear conflicts.(2)Die and mould development is performed on the same platform.When the heat treatment process is made out,designers can obtain correlative information and transfer self-information to other design departments on the platform.(3)Making out correct development schedule and adjusting it in time can enormously shorten the development period and reduce cost.References:[1] ZHOU Xiong-hui,PENG Ying-hong.The Theory and Technique of Modern Die and Mould Design and Manufacture[M].Shanghai:Shanghai Jiaotong University Press 2000(in Chinese).[2] Kang M,Park& Computer Integrated Mold Manufacturing[J].Int J Computer Integrated Manufacturing,1995,5:229-239.[3] Yau H T,Meno C H.Concurrent Process Planning for Finishing Milling and Dimensional Inspection of Sculptured Surface in Die and Mould Manufacturing[J].Int J Product Research,1993,31(11):2709—2725.[4] LI Xiang,ZHOU Xiong-hui,RUAN Xue-yu.Application of Injection Mold Collaborative Manufacturing System [J].JournaI of Shanghai Jiaotong University,2000,35(4):1391-1394.[5] Kuzman K,Nardin B,Kovae M ,et a1.The Integration of Rapid Prototyping and CAE in Mould Manufacturing[J].J Materials Processing Technology,2001,111:279—285.[6] LI Xiong,ZHANG Hong—bing,RUAN Xue-yu,et a1.Heat Treatment Process Design Oriented Based on Concurrent Engineering[J].Journal of Iron and Steel Research,2002,14(4):26—29.文献出处:LI Xiong,ZHANG Hong-bing,RUAN Xue—yu,LUO Zhong—hua,ZHANG Yan.Heat Treatment of Die and Mould Oriented Concurrent Design[J].Journal of Iron and Steel Research,2006,13(1):40- 43,74模具热处理及其导向平行设计李雄,张鸿冰,阮雪榆,罗中华,张艳摘要:在一系列方式中,传统模具设计方法存在许多缺点。
冲压模具设计外文翻译
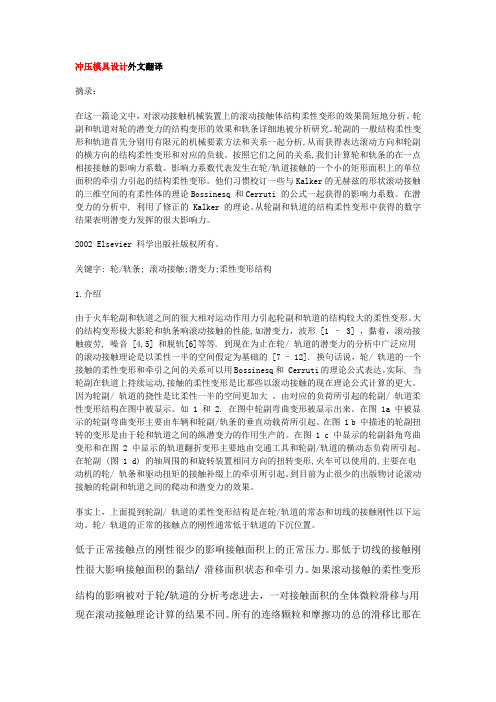
冲压模具设计外文翻译摘录:在这一篇论文中,对滚动接触机械装置上的滚动接触体结构柔性变形的效果简短地分析。
轮副和轨道对轮的潜变力的结构变形的效果和轨条详细地被分析研究。
轮副的一般结构柔性变形和轨道首先分别用有限元的机械要素方法和关系一起分析,从而获得表达滚动方向和轮副的横方向的结构柔性变形和对应的负载。
按照它们之间的关系,我们计算轮和轨条的在一点相接接触的影响力系数。
影响力系数代表发生在轮/轨道接触的一个小的矩形面积上的单位面积的牵引力引起的结构柔性变形。
他们习惯校订一些与Kalker的无赫兹的形状滚动接触的三维空间的有柔性体的理论Bossinesq 和Cerruti 的公式一起获得的影响力系数。
在潜变力的分析中, 利用了修正的 Kalker 的理论。
从轮副和轨道的结构柔性变形中获得的数字结果表明潜变力发挥的很大影响力。
2002 Elsevier 科学出版社版权所有。
关键字: 轮/轨条; 滚动接触;潜变力;柔性变形结构1.介绍由于火车轮副和轨道之间的很大相对运动作用力引起轮副和轨道的结构较大的柔性变形。
大的结构变形极大影轮和轨条响滚动接触的性能,如潜变力,波形 [1 – 3] ,黏着,滚动接触疲劳, 噪音 [4,5] 和脱轨[6]等等. 到现在为止在轮/ 轨道的潜变力的分析中广泛应用的滚动接触理论是以柔性一半的空间假定为基础的 [7 –12]. 换句话说,轮/ 轨道的一个接触的柔性变形和牵引之间的关系可以用Bossinesq和 Cerruti的理论公式表达。
实际, 当轮副在轨道上持续运动,接触的柔性变形是比那些以滚动接触的现在理论公式计算的更大。
因为轮副/ 轨道的挠性是比柔性一半的空间更加大。
由对应的负荷所引起的轮副/ 轨道柔性变形结构在图中被显示。
如 1 和 2. 在图中轮副弯曲变形被显示出来。
在图 1a 中被显示的轮副弯曲变形主要由车辆和轮副/轨条的垂直动载荷所引起。
在图 1 b 中描述的轮副扭转的变形是由于轮和轨道之间的纵潜变力的作用生产的。
模具设计相关专业毕业论文(外文原文+翻译)之翻译[管理资料]
![模具设计相关专业毕业论文(外文原文+翻译)之翻译[管理资料]](https://img.taocdn.com/s3/m/63ac390ff705cc1754270968.png)
可行成形图在汽车覆盖件冲压工艺高效设计的应用Dae-Cheol Ko a,Seung-Hoon Cha b,Sang-Kon Lee c,Chan-Joo Lee b,Byung-Min Kim d,*a ILIC, Pusan National University, 30 Jangjeon-Dong, Kumjeong-Gu, Busan609-735, South Koreab Precision Manufacturing Systems Division, Pusan National University, 30Jangjeon-Dong, Kumjeong-Gu, Busan 609-735, South Koreac PNU-IFAM, Joint Research Center, Pusan National University, 30Jangjeon-Dong, Kumjeong-Gu, Busan 609-735, South Koread School of Mechanical Engineering, Pusan National University, 30 Jangjeon-Dong, Kumjeong-Gu, Busan 609-735, South Korea摘要:本文提出使用可行的成形图来表示无断裂和起皱的安全区域,进而有效和快速地设计冲压工艺方法。
要确定可行的成形图,有限元分析对应于正交实验设计的过程变量组合。
随后,基于成形极限图的有限元分析,确定断裂和起皱的特征值。
所有组合的特征值在整个过程中,通过人工神经网络训练进行了一系列预测。
可行的成形图从所有组合的过程变量中最终确定。
以汽车覆盖件如转动架和车轮毂的冲压工艺作为实例来验证利用成形图的进行过程设计有效性。
有限元模拟结果与实验模拟结果比较表明,利用可行的成形图来进行冲压工艺的设计是有效的并适用于实际的过程。
冲压模具中英文翻译
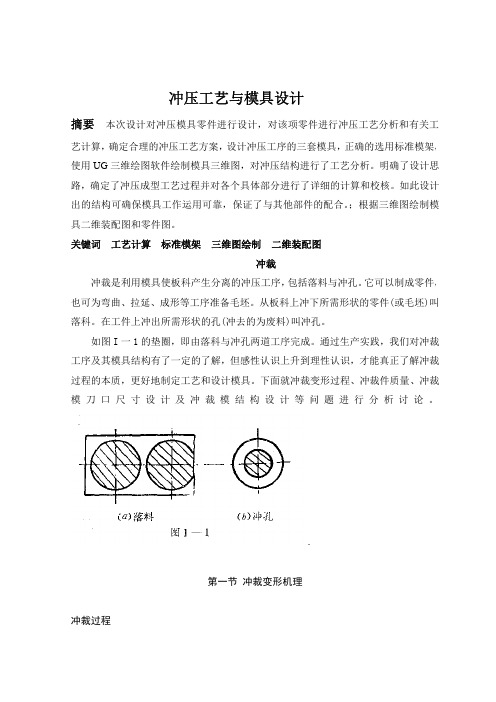
冲压工艺与模具设计摘要本次设计对冲压模具零件进行设计,对该项零件进行冲压工艺分析和有关工艺计算,确定合理的冲压工艺方案,设计冲压工序的三套模具,正确的选用标准模架,使用UG三维绘图软件绘制模具三维图,对冲压结构进行了工艺分析。
明确了设计思路,确定了冲压成型工艺过程并对各个具体部分进行了详细的计算和校核。
如此设计出的结构可确保模具工作运用可靠,保证了与其他部件的配合。
;根据三维图绘制模具二维装配图和零件图。
关键词工艺计算标准模架三维图绘制二维装配图冲裁冲裁是利用模具使板科产生分离的冲压工序,包括落料与冲孔。
它可以制成零件,也可为弯曲、拉延、成形等工序准备毛坯。
从板科上冲下所需形状的零件(或毛坯)叫落科。
在工件上冲出所需形状的孔(冲去的为废料)叫冲孔。
如图I一1的垫圈,即由落科与冲孔两道工序完成。
通过生产实践,我们对冲裁工序及其模具结构有了一定的了解,但感性认识上升到理性认识,才能真正了解冲裁过程的本质,更好地制定工艺和设计模具。
下面就冲裁变形过程、冲裁件质量、冲裁模刀口尺寸设计及冲裁模结构设计等问题进行分析讨论。
.第一节冲裁变形机理冲裁过程由图1—2所示的冲裁变形过程可以看出,凸模与凹棋组成上下刃口,材料放在凹模上,凸模逐步下降使材料产生变形,直至全部分离完成冲裁。
随着凸模作用在材料上的外力在数量上的变化,材料上的外力在数量上的变化,材料内部的变形不断发展。
整个冲裁过程的变形分为三个阶段(图1—2)。
1、弹性变形阶段凸模接触材队由于凸模加压,材料发生弹性压缩与弯曲并挤入凹模洞口。
这时材料内应力没有超过屈服极限,若凸模卸压,材料即恢复原状,故称弹性变形阶段。
2、塑性变形阶段凸模继续加压,材料内应力达到屈服极限,部份金属被挤入凹模洞口,产生塑剪变形,得到光亮的蛆切断面。
因凸、凹摸间存在间陷,故在塑剪变形的同时还伴有材料的弯曲与拉伸。
3、断裂分离阶段外力继续增加材料内应力不断增大,在凸、凹模刀口处由于应力集中,内应力首先越过抗剪强度,出现微裂。
- 1、下载文档前请自行甄别文档内容的完整性,平台不提供额外的编辑、内容补充、找答案等附加服务。
- 2、"仅部分预览"的文档,不可在线预览部分如存在完整性等问题,可反馈申请退款(可完整预览的文档不适用该条件!)。
- 3、如文档侵犯您的权益,请联系客服反馈,我们会尽快为您处理(人工客服工作时间:9:00-18:30)。
Heat Treatment of Die and MouldOriented Concurrent Design LI Xiong,ZHANG Hong-bing,RUAN Xue—yu,LUOZhong—hua,ZHANG YanAbstract:Many disadvantages exist in the traditional die design methodwhich belongs to serial pattern. It is well known that heattreatment is highly important to the dies. A new idea of concurrentdesign for heat treatment process of die and mould was developedin order to overcome the existent shortcomings of heat treatmentprocess. Heat treatment CAD/CAE was integrated with concurre ntcircumstance and the relevant model was built. Theseinvestigations can remarkably improve efficiency, reduce cost andensure quality of R and D for products.Key words:die design; heat treatment; mouldTraditional die and mould design,mainly by experience or semi—experience,is isolated from manufacturing process.Before the design is finalized,the scheme of die and mould is usually modified time and again,thus some disadvantages come into being,such as long development period,high cost and uncertain practical effect.Due to strong desires for precision,service life,development period and cost,modern die and mould should be designed and manufactured perfectly.Therefore more and more advanced technologies and innovations have been applied,for example,concurrent engineering,agile manufacturing virtual manufacturing,collaborative design,etc.Heat treatment of die and mould is as important as design,manufacture and assembly because it has a vital effect on manufacture,assembly and service life.Design and manufacture of die and mould have progressed rapidly,but heat treatment lagged seriously behind them.As die and mould industry develops,heat treatment must ensure die and mould there are good state of manufacture,assembly and wear—resistant properties by request.Impertinent heat treatment can influence die and mould manufacturing such as over—hard and—soft and assembly.Traditionally the heat treatment process was made out according to the methods and properties brought forward by designer.This could make the designers of die and mould and heat treatment diverge from each other,for the designers of die and mould could not fully realize heat treatment process and materials properties,and contrarily the designers rarely understood the service environment and designing thought. These divergences will impact the progress of die and mould to a great extent. Accordingly,if the process design of heat treatment is considered in the early designing stage,the aims of shortening development period,reducing cost and stabilizing quality will be achieved and the sublimation of development pattern from serial to concurrent will be realized.Concurrent engineering takes computer integration system as a carrier,at the very start subsequent each stage and factors have been considered such as manufacturing,heat treating,properties and so forth in order to avoid the error.The concurrent pattern has dismissed the defect of serial pattern,which bring about a revolution against serial pattern.In the present work.the heat treatment was integrated into the concurrent circumstance of the die and mould development,and the systemic and profound research was performed.1 Heat Treatment Under Concurrent CircumstanceThe concurrent pattern differs ultimately from the serial pattern(see Fig.1).With regard to serial pattern,the designers mostly consider the structure and function of die and mould,yet hardly consider the consequent process,so that the former mistakes are easily spread backwards.Meanwhile,the design department rarely communicates with the assembling,cost accounting and sales departments.These problems certainly will influence the development progress of die and mould and the market foreground.Whereas in the concurrent pattern,the relations among departments are close,the related departments all take part in the development pro gress of die and mould and have close intercommunion with purchasers.This is propitious to elimination of the conflicts between departments,increase the efficiency and reduce thecost.Heat treatment process in the concurrent circumstance is made out not after blueprint and workpiece taken but during die and mould designing.In this way,it is favorable to optimizing the heat treatment process and making full use of the potential of the materials.2 Integration of Heat Treatment CAD/CAE for Die and MouldIt can be seen from Fig.2 that the process design and simulation of heat treatment are the core of integration frame.After information input via product design module and heat treatment process generated via heat treatment CAD and heat treatment CAE module will automatically divide the mesh for parts drawing,simulation temperature field microstructure analysis after heat—treatment and the defect of possible emerging (such as overheat,over burning),and then the heat treatment process is judged if the optimization is made according to the result reappeared by stereoscopic vision technology.Moreover tool and clamping apparatus CAD and CAM areintegrated into this system.The concurrent engineering based integration frame can share information with other branch.That makes for optimizing the heat treatment process and ensuring the process sound.2.1 3-D model and stereoscopic vision technology for heat treatmentThe problems about materials,structure and size for die and mould can be discovered as soon as possible by 3-D model for heat treatment based on the shape of die and mould.Modeling heating condition and phase transformation condition for die and mould during heat treatment are workable,because it has been broken through for the calculation of phase transformation thermodynamics,phase transformation kinetics,phase stress,thermal stress,heat transfer,hydrokinetics etc.For example,3-D heat —conducting algorithm models for local heating complicated impression and asymmetric die and mould,and M ARC software models for microstructuretransformation was used.Computer can present the informations of temperature,microstructure and stress at arbitrary time and display the entire transformation procedure in the form of 3-D by coupling temperature field,microstructure field and stress field.If the property can be coupled,various partial properties can be predicted by computer.2.2 Heat treatment process designDue to the special requests for strength,hardness,surface roughness and distortion during heat treatment for die and mould,the parameters including quenching medium type,quenching temperature and tempering temperature and time,must be properly selected,and whether using surface quenching or chemical heat treatment the parameters must be rightly determined.It is difficult to determine the parameters by computer fully.Since computer technology develops quickly in recent decades,the difficulty with large—scale calculation has been overcome.By simulating and weighing the property,the cost and the required period after heat treatment.it is not difficult to optimize the heat treatment process.2.3 Data base for heat treatmentA heat treatment database is described in Fig.3.The database is the foundation of making out heat treatment process.Generally,heat treatment database is divided into materials database and process database.It is an inexorable trend to predict the property by materials and process.Although it is difficult to establish a property database,it is necessary to establish the database by a series of tests.The materials database includes steel grades,chemical compositions,properties and home and abroad grades parallel tables.The process database includes heat treatment criterions,classes,heat preservation time and cooling velocity.Based on the database,heat treatment process can be created by inferring from rules.2.4 Tool and equipment for heat treatmentAfter heat treatment process is determined,tool and equipment CAD/CAE system transfers the information about design and manufacture to the numerical control device.Through rapid tooling prototype,the reliability of tool and the clamping apparatus can be judged.The whole procedure is transferred by network,in which there is no man—made interference.3 Key Technique3.1 Coupling of temperature,microstructure,stress and propertyHeat treatment procedure is a procedure of temperature-microstructure—stress interaction.The three factors can all influence the property (see Fig.4).During heating and cooling,hot stress and transformation will come into being when microstructure changes.Transformation temperature-microstructure and temperature—microstructure—and stress-property interact on each other.Research on the interaction of the four factors has been greatly developed,but the universal mathematic model has not been built.Many models fit the test nicely,but they cannot be put into practice.Difficulties with most of models are solved in analytic solution,and numerical method is employed so that the inaccuracy of calculation exists.Even so,comparing experience method with qualitative analysis,heat treatment simulation by computer makes great progress.3.2 Establishment and integration of modelsThe development procedure for die and mould involves design,manufacture,heat treatment,assembly,maintenance and so on.They should have own database and mode1.They are in series with each other by the entity—relation model.Through establishing and employing dynamic inference mechanism ,the aim of optimizing design can be achieved.The relation between product model and other models was built.The product model will change in case the cell model changes.In fact,it belongs to the relation of data with die and mould.After heat treatment model is integrated into the system,it is no more an isolated unit but a member which is close to other models in the system.After searching,calculating and reasoning from the heat treatment database,procedure for heat treatment,which is restricted by geometric model,manufacture model for die and mould and by cost and property,is obtained.If the restriction is disobeyed,the system will send out the interpretative warning.All design cells are connected by communication network.3.3 Management and harmony among membersThe complexity of die and mould requires closely cooperating amongitem groups.Because each member is short of global consideration for die and mould development,they need to be managed and harmonized.Firstly,each item group should define its own control condition and resource requested,and learn of the request of up-and-down working procedure in order to avoid conflict.Secondly,development plan should be made out and monitor mechanism should be established.The obstruction can be duly excluded in case the development is hindered.Agile management and harmony redound to communicating information,increasing efficiency,and reducing redundancy.Meanwhile it is beneficial for exciting creativity,clearing conflict and making the best of resource.4 Conclusions(1) Heat treatment CAD/CAE has been integrated into concurrent design for die and mould and heat treatment is graphed,which can increase efficiency,easily discover problems and clear conflicts.(2) Die and mould development is performed on the same platform.When the heat treatment process is made out,designers can obtain correlative information and transfer self-information to other design departments on the platform.(3) Making out correct development schedule and adjusting it in time can enormously shorten the development period and reduce cost.References:[1] ZHOU Xiong-hui,PENG Ying-hong.The Theory and Technique of Modern Die and Mould Design and Manufacture[M].Shanghai:Shanghai Jiaotong University Press 2000(in Chinese).[2] Kang M,Park& Computer Integrated Mold Manufacturing[J].Int J Computer Integrated Manufacturing,1995,5:229-239.[3] Yau H T,Meno C H.Concurrent Process Planning for Finishing Milling and Dimensional Inspection of Sculptured Surface in Die and Mould Manufacturing[J].Int J Product Research,1993,31(11):2709—2725.[4] LI Xiang,ZHOU Xiong-hui,RUAN Xue-yu.Application of Injection Mold Collaborative Manufacturing System [J].JournaI of Shanghai Jiaotong University,2000,35(4):1391-1394.[5] Kuzman K,Nardin B,Kovae M ,et a1.The Integration of Rapid Prototyping and CAE in Mould Manufacturing [J].J Materials Processing Technology,2001,111:279—285.[6] LI Xiong,ZHANG Hong—bing,RUAN Xue-yu,et a1.Heat Treatment Process Design Oriented Based on Concurrent Engineering[J].Journal of Iron and Steel Research,2002,14(4):26—29.文献出处:LI Xiong,ZHANG Hong-bing,RUAN Xue—yu,LUO Zhong—hua,ZHANG Yan.Heat Treatment of Die and Mould Oriented Concurrent Design[J].Journal of Iron and Steel Research,2006,13(1):40-43,74模具热处理及其导向平行设计李雄,张鸿冰,阮雪榆,罗中华,张艳摘要:在一系列方式中,传统模具设计方法存在许多缺点。