连铸设备教材1
连铸机设备PPT幻灯片课件
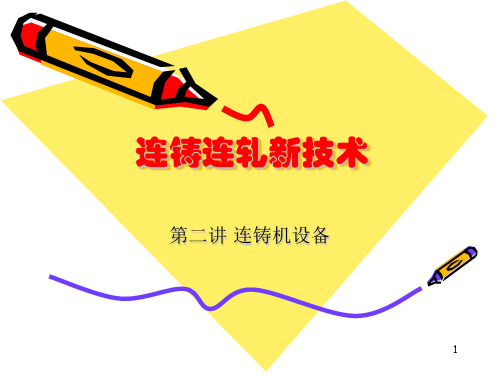
长水口又称保护套管,用于钢包与中间包之间保护 注流不被二次氧化,同时也避免了注流的吸气、飞溅以 及敞开浇注的卷渣问题。
图2-4 长水口保护装置 (a)卡口型;(b)液压型;(c)叉型 1一钢包;2一氩气;3~钢水;4一中间包;5一浇注位置
19
钢包回转台
图2-5 钢包回转台 (a)直臂式;(b)双臂单独升降式;(c)带钢包加盖功能 钢包回转台是现代连铸中应用最普遍的运载和承托钢包进行浇 注的设备,通常设置于钢水接受跨与浇注跨柱列线之间。钢包回转 台能够在转臂上同时承放两个钢包,一个用于浇注,另一个处于待 浇状态。
2
2.1.2 弧形、椭圆形连铸机的表示方法
连铸机的规Leabharlann 表示如下: aRb—c这里:a——机数,若其数为1,则可省略; R——机型为弧形或椭圆形连铸机; b——连铸机的圆弧半径,m;若椭圆形连铸机
为多个半径之乘积,也标志可浇铸坯 的最大厚度; c ——表示拉辊坯辊身长度,mm,它标志着连
铸机可容纳的连铸坯的最大宽度。 B=C-(150~200)mm
1一钢包注流位置;2一中间包水口位置;3一挡渣墙
21
中间包车结构有哪些特点?
中间包车是承载和运送中间包的特殊车辆,根据工艺操作要求,中间包车 必须具备如下功能:
(1)将中间包由预热位置移到浇钢位置上,在浇钢结束后还应移出浇钢位置, 因此中间包车应具有运行功能; 。
(2)在安放中间包时,首先将中间包提起,使水口离开结晶器盖一定高度后 再进入浇钢位置,下降中间包,使水口对准结晶器中心,因此它应具有升降和 微调功能;
内壁之间的滑动摩擦,因此结晶器内壁的材质应有良好的耐磨性和较高的再结晶 温度。 (5)重量要轻,以减少振动时的惯性力。为提高铸坯表面质量,结晶器的振动广 泛采用高频率小振幅,最高已达4 00次/min,在高频振动时惯性力不可忽视, 过大的惯性力不仅影响到结晶器的强度和刚度,进而也影响到结晶器运动轨迹的 精度。
连铸设备课件

1.钢包回转台; 2.中间包车; 3.结晶器; 4.结晶器振动装置; 5.扇形段及二次冷却装置; 6.配水系统;7.拉矫机;8. 脱引锭装置; 9.铸坯切割装置(火焰切割); 10.铸坯输出装置及 引锭杆存放;11.液压系统;12.电器及自动化系统
方坯连铸设备构成示意图(连浇小车式)
1
3
2
4
6
7 11
组装而成,这种结晶器制造调节较方便,一般在板坯、大 方坯连铸机上使用。 管式结晶器主要由铜管、内水套、外水套三层组成,水流 通过内水套与铜管间的水缝冷却铜管。。
我厂1-4#机结晶器主要设备参数见下表:
项目
1#连铸机 2#连铸机 3#连铸机 4#连铸机
型式
管式
管式
断面形状尺寸 (与成品铸坯 基本相同)
1.2.1、按结构分
1.方坯; 2.板坯; 3.圆坯; 4.异型坯; 5.方坯和板坯兼用 6.薄板坯连铸机
1.3、我厂连铸机机型
名称 1#机 2#机 3#机 4#机
机型 R6000全弧形4机4流连铸机 R8000全弧形4机4流连铸机 R8000全弧形4机4流连铸机 R11000全弧形4机4流连铸机
固定螺 栓松
8
12 9 10
1.钢包回转台(连浇车);2.中间包车;3.结晶器;4.结晶器振动装置;5.导向段及二次冷却装置; 6.配水系统;7.拉矫机;8.引锭杆及送、脱引锭装置;9.铸坯切割装置(火焰切割、液压机械切割); 10.铸坯输出装置;11.液压系统;12.电器及自动化系统
方坯连铸设备构成示意图(大包回转台式)
2.2.3 结晶器
结晶器是连铸设备中最关键的部件,即连铸机的心脏。 作用是在连续浇钢过程中通过热交换使钢水出结晶器时凝
连铸电控操作说明书
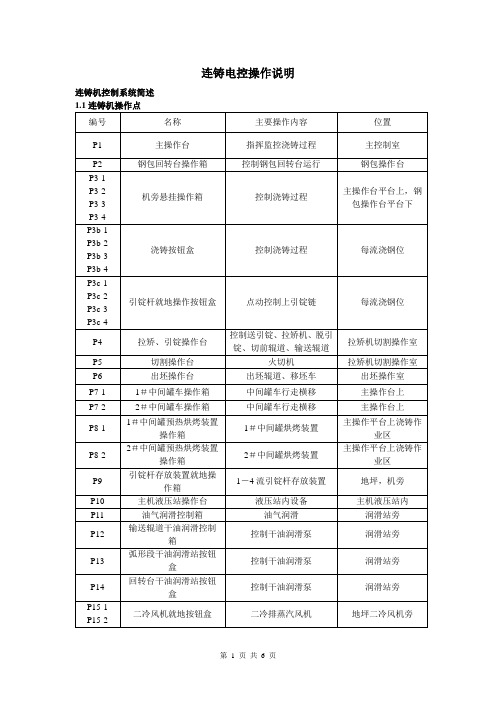
连铸电控操作说明连铸机控制系统简述1.2 钢包回转台控制钢包回转台正常驱动采用一台电机,变频调速。
事故驱动采用液压马达。
钢包回转台在P2操作箱上进行控制,主要控制内容有:“反转”“停”“正传”选择开关;“慢速反转”“慢速正传”带点动按钮;“事故回转”按钮。
1.3 大包加盖装置控制大包加盖装置共有两套。
分别采用电液推杆驱动。
1#加盖装置和2#加盖装置分别在P2上进行控制。
控制内容有:“加盖”“开盖”带灯按钮,“停”按钮;“升”“降”带灯按钮。
1.4 中间罐车控制中间罐车驱动采用二台变频调速电机。
中间罐车主要在P7操作箱上进行控制,主要控制内容有:中间罐车行走“左行”“停”“右行”选择开关;“点动”“点退”点动按钮。
中间罐车点动主要用于在浇注位水口对中。
中间罐升降“上升”“停”“下降”选择开关;“水平调整”带灯按钮。
中间罐横移“前移”“后移”带灯按钮。
1.5 二冷室排汽风机控制二冷室排汽风机共有两套。
各由一台电机驱动。
二冷室排汽风机主要在主控室PC工作站和P15操作箱上进行控制,在P15操作箱上可以选择操作地点。
控制项目有:风机“开”“停”按钮。
风机“就地”“远程”选择开关。
1.6 二冷水喷淋系统控制二冷水系统主要有以下检测、控制设备组成:总管压力检测;总管温度检测;每流支管气动切断阀;每流O段流量检测和电动调节阀调节,每流Ⅰ段流量检测和电动调节阀调节,每流Ⅱ段流量检测和电动调节阀调节,每流Ⅲ段流量检测和电动调节阀调节。
二冷水设二种工作方式选择:自动-手动。
自动方式下随“浇铸”、“停浇”按钮一起启动、停止,手动控制有开-关控制,在P3箱上操作。
二冷水调节系统的控制:二冷水调节系统的控制在主控室PC操作站上进行,通过计算机画面可以选择二冷水调节方式:自动方式-半自动方式-手动方式。
流量设定、阀门开度设定均可通过计算机画面进行。
(1)控制原则二冷水各段独立自成系统。
在浇铸前操作工根据浇铸的铸坯断面及钢种选定冷却组别,计算机自动调用配水模型进行生产。
连铸工教程1

第一章概况1.连铸机的机型经历了由立式、立弯式、直结晶器弧形、弧形、椭圆形到水平式的发展过程。
其铸机的高度由高到低。
2.连铸机按浇注铸坯断面分类有方坯连铸机、板坯连铸机、圆坯连铸机、异型坯连铸机、方、板坯兼用连铸机。
3.目前连续铸钢车间主要布置形式有两种:连铸机的中心线与厂房柱列线相垂直者为横向布置,连铸机中心线与厂房柱列相平行者为纵向布置。
4.一台连铸机具有独立传动系统的机组数目,称为连铸机的机数。
5.一台连铸机能同时浇注的铸坯根数称为连铸机的流数。
6.影响铸机拉速因素有钢种、断面、钢水温度等。
7.弧形连铸机的铸机半径与铸坯厚度有关。
8.立弯式连铸机比弧形连铸机,结晶器内夹杂易上浮。
9.连铸机的机型对铸坯内夹杂物的数量和分布有着重要影响。
10.对铸机而言,热装热送技术的关键是生产无缺陷_铸坯。
11.连铸坯按铸坯断面分类有方坯、板坯、园坯、异型坯。
12.目前,连铸只能浇镇静钢。
13.连续铸钢的三大工艺制度是温度制度,拉速制度,冷却制度。
14.高效连铸的含意包括高质量、高拉速、高作业率和高连浇率等四个方面的内容。
15.我国连铸技术的发展,总体而言,经历了达产、全连铸及当前正在进行的__铸机高效化等几个阶段。
16.近终形连铸机指的是:出铸机连铸坯接近成品。
17.为发挥冶炼设备的能力,保证连铸与炼钢匹配,连铸的能力应大于炼钢的能力10%~20%。
18.弧形连铸机的参数有:铸坯断面尺寸、拉坯速度、圆弧半径、液相深度、铸机流数。
19.直径是450mm的圆坯的断面尺寸表示方法是φ450 mm。
第二章冷却、传热1.钢液的凝固温度随着钢的成分而发生变化,溶于钢中的元素都具有降低钢液凝固点的作用。
2.钢水温度过高,气体在钢中的溶解度就过大,对钢质危害的影响也愈大。
3.连铸机拉速提高,铸坯液芯长度增加,引起铸坯出结晶后坯壳厚度变薄,二次冷却段的铸坯易产生鼓肚变形 ,矫直时由于铸坯仍有液芯而产生内裂等。
4.控制钢水温度的出发点,首先尽可能减少钢包过程温降 ,以降低出钢温度;其次尽可能稳定炼钢操作,提高出钢温度的命中率,避免高温出钢;第三是加强生产调度和钢包周转。
《连铸工艺与设备》讲稿1

另外,还可以按铸坯断面形状分为方坯连铸机、圆坯连铸机、板坯连铸机、异形坯连铸机、方/板坯兼用型连铸机等。
按钢水的静压头可分为高头型、低头型和超低头型连铸机等。
3.1立式连铸机
立式连铸机是20世纪50年代至60年代初的主要机型。立式连铸机,从中间罐到切割装置等主要设备均布置在垂直中心线上,整个机身矗立在车间地平面以上。采用立式连铸机
图0-2 1972年以来我国连铸坯产量和连铸比的增长
1-钢总产量;2-连铸比;3-连铸坯产量
3连铸机的机型及其特点
连铸机的分类方式很多。按结晶器是否移动可以分为两类:
1)固定式结晶器:包括固定振动结晶器的各种连铸机,如立式连铸机、立弯式连铸机、弧形连铸机、椭圆形连铸机、水平式连铸机等。这些机型已成为现代化连铸机的基本机型,如图3所示。
进入20世纪60年代,弧形连铸机的问世,使连铸技术出现了一次飞跃。世界第一台弧形连铸机于1964年4月在奥地利百录厂诞生。同年6月由我国自行设计制造的第1台方坯和板坯兼用弧形连铸机在重钢三厂投入生产。此后不久,在前联邦德国又上马了1台宽板弧形连铸机,并开发应用了浸入式水口和保护渣技术。同年英国谢尔顿厂率先实现全连铸生产,共有4台连铸机11流,主要生产低合金钢和低碳钢,浇注断面为140mm×140mm和432mm×632mm的铸坯。也开发应用了浸入式水口和保护渣技术。1967年由美钢联工程咨询公司设计并在格里厂投产1台采用直结晶器、带液心弯曲的弧形连铸机。同一年在胡金根厂相继投产了2台超低头板坯连铸机,浇注断面为(150~250)mm×(1800~2500)mm的铸坯,该铸机至今仍在运行。
连铸机械设备培训教材.(DOC)

一、连铸设备一览(一)、连铸设备:1钢包回转台、2中包车、3结晶器、4整体段、5扇型段、6机前辊道、7切割机、8机下辊道、9输出辊道、10去毛刺、11喷印机、12横移台车、13转盘、14输送辊道(二)、技术性能(见表1)表1 技术性能序号名称技术参数1 结晶器型式直结晶器、在线调宽规格(890×1550)×900×(200、300)足辊φ150×160,二节辊一对2 整体段型式垂直弯曲型,五点顶弯规格分200、230两种规格辊子φ150×1600,二节辊2对φ180×1600,二节辊2对φ200×1600,三节辊2对φ220×1600,三节辊7对φ120×110,一节辊5对3 扇形段型式四支柱升降式,行程为190~350mm规格每段由5对辊子组成,每流共有17个扇形段,NO.2~NO.8为弧形段(其中NO.6~NO.8电磁搅拌段,NO.9~NO.10为矫直段(5点矫直),NO.11~NO.18为水平段辊子φ240×1600,一体辊5对φ250×1600,一体辊5对φ280×1600,一体辊10对φ300×1600,一体辊15对(其中有6根EMS)辊φ310×1600,一体辊6根φ310×1600,二体辊14对φ310×1600,一体辊40根对4 引锭杆台车走行承载(t)15速度(m/min)24速比100.654轨距(mm)4500车轮(mm)4800序号名称技术参数卷动对中速度(m/min)5.4链子94节×300mm电动机30KW,120r.p.m 平减速机I=16.862蜗轮减速机I=49/2链轮φ600电动机内藏闸式,I=6行程(mm)240承载(N)50000速比24导程(mm)85 引锭杆卷上承载(t)13电动机15KW,1200r.p.m 速比542.02高速(m/min) 2钢绳(mm)φ18卷简(mm)φ1150扬程(m)φ166 放气装置气源(Mpa)N2,0.4~0.8汽缸φ125/φ36×600st 冷却水(Mpa)0.4工作气压(Mpa)0.05~0.107 间接水结晶器铜板(Mpa)0.8 辊子、轴承座(Mpa)0.5 框架(Mpa)0.4 直接冷却水(Mpa)0.7 直接冷却水(Mpa)0.4(三)、拆装工序及技术要求表2:拆装工序及技术要求序号项目拆装工序技术要求1 更换结晶器1)在中控室停结晶器各冷却水和整体段环路水,在4米液压站停整体段间接水,并做防冻。
连铸工艺与设备1

连铸工艺与设备1连铸工艺与设备1连铸是一种现代钢铁生产工艺,是通过连续浇铸技术将液态钢铁直接铸造成连续坯,进而实现高效率的钢材生产。
连铸工艺与设备是该工艺实施所必需的组成部分,对于钢铁企业的生产效率和质量控制具有重要影响。
连铸工艺的主要步骤包括:浇注、结晶器、凝固、拉伸、切割和冷却等。
首先,通过浇注将液态钢铁注入结晶器中,结晶器中装有冷却剂,使钢水迅速冷却并凝固形成坯料。
然后,通过拉伸机械将坯料进行拉伸,拉伸过程中继续凝固,最终形成长期坯料。
接下来,切割机械将长期坯料切割成合适的长度,并通过冷却设备对坯料进行冷却,使其达到适宜的温度。
连铸工艺与设备应具备以下特点:高效率、高质量和节能环保。
首先,高效率是指连铸工艺与设备能够实现高产量和高利用率。
连铸工艺可以连续生产钢材,大大提高了生产效率。
而连铸设备的设计和制造应该保证设备的稳定性,减少故障和停工时间。
其次,高质量要求连铸工艺与设备能够实现钢材的一致性和均匀性。
结晶器的设计和冷却剂的使用都需要考虑坯料的凝固速度和结晶质量。
同时,拉伸机械的控制能够保证坯料的拉伸速度均匀,从而保证钢材的质量。
最后,节能环保是指连铸工艺与设备应该尽可能减少能源消耗和环境污染。
例如,在冷却过程中可以利用循环水来降低能耗,并且对废水进行处理。
近年来,随着工业技术的不断发展,连铸工艺与设备也得到了提升和改进。
连铸工艺的铸造速度和坯料尺寸得到了提高,可以生产出更大尺寸的钢材。
同时,连铸设备的自动化程度不断提高,减少了人工操作,提高了生产效率和安全性。
在连铸过程中,还可以采用一些先进的监测仪器和控制系统,对铁水的成分、温度和流动情况进行实时监测,从而保证钢材质量的稳定性和一致性。
总之,连铸工艺与设备是实现高效率、高质量和节能环保的钢铁生产的重要组成部分。
随着技术的发展,连铸工艺与设备也在不断改进和完善,为钢铁企业的发展提供了强大的支持。
同时,工艺与设备的优化也促进了钢铁产业的可持续发展。
连铸设备教学课件PPT

拉坯速度
• 通常,连铸机冶金长度确定后,铸机可能
达到的最大拉速也就随之确定,拉速和冶
金长度是相互联系、相互制约的。
• 铸机可达到的最大拉速按下式计算:
式中
vmax
K 2Lm
2
vmax: 最大理论拉速,m/min K: 凝固系数,mm ·min-0.5 Lm: 冶金长度,m : 最小坯壳厚度,mm
• 在铸坯内钢水完全凝固之前,上部结构和立式 连铸机相同。
• 在铸坯完全凝固之后,用顶弯设备将铸坯顶弯, 使铸坯在水平方向进行切割和出坯,大大减小 设备总高度
• 小断面(100mm*100mm)铸坯完全凝 固时间短,大断面150mm*150mm以上) 铸坯完全凝固时间长。大断面不适合通过顶弯 降低设备高度。顶弯设备庞大。
• 内外弧冷却强度不一致。所以要合理布 置二冷强度。
设备高度的降低,使得弧形连铸机得到广 泛使用
多点矫直弧形连铸机基本特点
多点矫直弧形连铸机基本特点
• 原理和设备和单点矫直弧形连铸机一样。 • 拉速增加,使得钢水不能在四分之一圆弧内完
全凝固,因此在矫直时,铸坯中心还有钢液液 芯,形成所谓带液芯矫直。 • 单点矫直会导致带液芯矫直时的一次变形量大, 铸坯中心区产生裂纹缺陷。而将一次变形变成 多次变形,可解决这一问题。
• 铸机长度按冶金长度确定,取1.1倍冶金长度。
连铸机总体尺寸(长度)
• 连铸机总长度是指从结晶器外弧线(即 连铸机基准线)至冷床后固定挡板的距 离,与采用的引锭杆型式有关。
• 如图
连铸机总体尺寸(长度)
• L=R十L1十L2+ L3十L4十L5
- 1、下载文档前请自行甄别文档内容的完整性,平台不提供额外的编辑、内容补充、找答案等附加服务。
- 2、"仅部分预览"的文档,不可在线预览部分如存在完整性等问题,可反馈申请退款(可完整预览的文档不适用该条件!)。
- 3、如文档侵犯您的权益,请联系客服反馈,我们会尽快为您处理(人工客服工作时间:9:00-18:30)。
目录1. 概述1.1连铸技术的发展1.2连铸机的机型1.2.1 立式连铸机1.2.2 立弯式连铸机1.2.3 弧形连铸机1.2.4 直弧形连铸机1.2.5 水平连铸机1.3方坯连铸机1.3.1 方坯连铸1.3.2 罗克普型小方坯连铸机1.4铸坯热送2. 连铸机及其参数计算2.1 铸坯断面2.2 拉坯速度2.3 机身长度2.4 弧形半径2.5 连铸机流数2.6 连铸机生产能力计算2.7 方坯连铸机的工艺布置2.7.1 连铸机总体尺寸2.7.2 方坯连铸机工艺流程2.7.3 连铸机在车间内的布置3. 浇注设备3.1 钢包及其运载设备3.2 钢包回转台3.3 中间罐3.4 中间罐车3.4.1 中间罐车的型式3.4.2 中间罐车的总体结构4. 结晶器及其振动机构4.1 结晶器4.1.1 结晶器内坯壳的形成4..2 结晶器的型式和构造4. 2.1 结晶器振动的目的4. 2.2 结晶器振动方式4. 2.3 结晶器振动机构的类型4.2.4 结晶器振动机构介绍4.2.5 结晶器振动的运动参数5. 二冷区铸坯导向装置5.1 二冷装置的作用与工艺要求5.2 二次冷却区的传热5.2.1 二冷区热平衡5.3 二冷区铸坯导向装置的结构5.3.1 小方坯连铸机二冷装置5.3.2 大方坯连铸机二冷装置5.3.3 板坯连铸机二冷装置5.3.4 二冷区扇形段更换方法5.3.5 二冷区支承导向部件结构6. 拉矫机6.1 拉矫机的技术要求6.2 拉矫机的型式与结构6.3 矫直的基本原理和矫直力的确定6.4 拉坯力的计算与确定7. 引锭杆及其存放装置7.1 引锭杆的形式与结构7.1.1 引锭杆的形式7.1.2 引锭杆结构7.2 引锭杆的脱锭与存放装置8. 火焰切割机8.1 火焰切割机结构8.2 切割枪及切割咀1. 概述1.1连铸技术的发展连续铸钢自问世以来,它便得到迅速的发展。
这主要是由于它与传统的“模铸-开坯”工艺相比(见图1),具有如下突出的优点:简化了生产钢坯的工艺流程,节约了大量的能源。
据日本资料介绍,连铸的能源消耗仅为模铸工艺的20.8%-13.5%。
我国每吨连铸坯综合节能约为130kg标准煤,若实行连铸坯的热送还能再节省5kg左右的标准煤。
由于能在一个机组上连续浇铸出钢坯来,可以提高金属收得率达7%-8%,成材率提高10%-15%。
成本还可以降低约10%-12%。
可以采用计算机自动控制,易于实现连续生产。
从根本上改变了工人劳动条件,生产率相应得到提高。
由于连铸的优越性,许多钢厂纷纷采用连铸取代模铸工艺,并出现全连铸炼钢车间。
各国连铸比不断提高。
经过几十年各国对连铸技术的研究、开发,使得连铸新工艺、新技术发展很快。
近年来,以高拉速、高连浇率、高作业率、高铸坯无缺陷率(或称为无清理率)的高效连铸是连铸生产的重要发展方向,也是迅速提高我国连铸生产水平的重要手段。
小方坯1302拉速>4米/分、1502拉速>3米/分;产量每流13-15万吨;作业率达90%。
板坯拉速可提高到1.8-2米/分左右,作业率达90%,双流板坯铸机单月产量也已达到32-35万吨的水平。
我厂2#板坯连铸机经改造,原设计为50万吨/年,改造后为85万吨/年左右。
拉速和作业率都比现在的拉速和作业率要有所提高。
随着炼钢技术的发展,炉外精炼的采用RH、VOD、LF炉、吹Ar等工艺使供连铸的钢水质量有了明显改善;连铸采用保护浇铸以及连铸液面控制电磁搅拌等新技术的应用,使铸坯表面质量进一步提高,内部缺陷进一步减少。
这不仅扩大了连铸浇铸的钢种,而且为铸坯红送创造了有利条件。
目前连铸发展为连铸连轧短流程新工艺。
薄板坯连铸可浇成50-100mm厚的连铸坯,热送加热炉,然后热连轧机组直接轧制成最小厚度约1.2mm的热轧带卷,该工艺是以最短的工艺流程,在一条连续的作业线上直接生产带卷的高新技术。
我国邯钢、包钢包等厂家已经引进了这种新技术。
1.2 连铸机的机型连铸机的机型直接影响连铸坯的产量、质量、投资和效益。
最早应用于工业生产的是立式连铸机,历经几十年的不断发展,图1-1至今已形成完整的机型型谱。
通常称为传统连铸机,主要有立式、立弯式、弧形式和水平连铸机等。
在其大发展的同时,广大连铸工作者为获得更高质量的铸坯,进一步提高连铸机的拉坯速度,相继开发出多种形式的连铸机,这里称其为新型连铸机。
下面仅对其中几种主要新型机作简要叙述,详见图1-1。
1.2.1 立式连铸机如图1-1(1)所示,其基本特征是:连铸机的各主体设备:结晶器及其振动装置、二次冷却支承导向装置、拉坯设备及切割装置等均从上到下配置在同一铅垂生产线,且在浇铸过程中铸坯没有受到任何强制变形过程。
因而具有如下优点:(1)由于钢水铅垂注入结晶器内,四周冷却条件相同,易于调节控制,因而钢水结晶固易达到最佳状态。
且钢水中各种非金属夹杂物易于上浮,铸坯内夹杂物最少,横断面结晶组织对称。
(2)连铸机的主体设备结构均简单,且可省去一套矫直装置。
(3)铸坯在结晶凝因过程中,不受任何机械外力作用。
为获得高质量铸坯创造更有利的条件。
其主要缺点是:(1)铸机机身很高,由此带来一系列问题:钢水的静压大,极易产生鼓肚变形。
机械设备的维护检修很不方便。
施工工作量都很大(不论是向空中还是往地下),因而投资较多。
(2)铸坯定尺长度受到限制,发展困难。
随着生产率进一步提高,铸坯尺寸要增大,拉速需加快,都迫使立式连铸机还要加高,其缺点会更加突出,发展受到严重限制。
1.2.2 立弯式连铸机如图1-1(2)所示,它的主要特征是:铸机机身上部都与立式铸机完全相同,在铸坯完全凝固后,经过弯坯装置,将铸坯弯曲90o成水平,然后在水平位置矫直、切断成定尺,水平出坯。
该机型的主要优点是:(1)完全保留了立式连铸机的主要工艺与铸坯质量高的长处。
(2)显然机身较立式铸机高度有所降低。
更重要的是从此开拓了连铸机水平出坯的新途径,坯长不再受限制。
其主要缺点是:尽管铸机机身高度有所降低,但在铸坯尺寸进一步加大,拉速再提高时,铸坯的液相深度会越来越长,机身至弯坯前还是太高。
这样该机型所显示的优越性会越发不明显。
甚至难于克眼由于高度带来的困难。
特别是在主要设备的组成上,除了比立式铸机减少一套翻钢与出坯装置外,又增加了弯坯装置和矫直设备,二者重量相差无几。
1.2.3 弧形连铸机在不断寻求降低连铸机高度的过程中,到60年代初,我国及瑞士首先研制成功了圆弧形连铸机(如图1-1(3))。
从此,连铸机获得了突破性迅猛进展。
圆弧形连铸机的基本特征是:从位于最上面的结晶器及紧相连的二次冷却支导装置到拉矫机,受到矫直辊施加的外力被矫直。
该机型具有如下优点:(1)机身高度低,仅为立式铸机高度的1/3,由此带来一系列优越性:对设备和维护、检修以及事故处理等都比较方便。
钢水的静压力较小,因而大大减少因鼓肚引起铸坯的内裂和偏析。
(2)在克服立弯式连铸机缺点的同时,保持和发扬了其水平出坯的特长。
定尺长度不再受限制,为实现高速浇铸创造了良好的条件。
它的主要缺点是:(1)鉴于钢水完全是在1/4圆弧中进行冷却凝固的,其中夹杂物上浮自然会受到阻碍,又很容易向内弧富集,会造成夹杂物偏析。
(2)整个铸机占地面积比立式铸机大。
(3)连铸机设备制造、安装、维修、对中、找正比较困难。
1.2.4 直弧形连铸机近年来,在总结立式连铸机和全弧形连铸机优缺点的基础上,提出采用直结晶器,具有弯曲过渡的弧形段,然后矫直水平出坯的直弧形连铸机如图1-1中3b。
这种机型的连铸机采用直结晶器,并具有一个2.5M以上的直线段,因而它具有立式连铸机铸坯质量好的优点。
同时,二冷又采用了较大的弧形段,矫直水平出坯因而又具有弧形机中提高拉速、增加产量的优点;采用特殊的弯曲和矫直结构;可带液芯进行弯曲和矫直。
防止铸坯由于矫直引起的内袭纹。
1.2.5 水平连铸机目前它(如图)1-1中4)的工艺和装备在国外已较为成熟,正在向扩大钢种、断面形状和尺寸的方向发展。
该机型的主要特征是:在浇铸过程中铸坯始终保持水平运动,不受弯曲或矫直,系属无氧化浇铸。
表1:连铸机的机型比较表二钢厂1#、2#连铸机为R8m直弧型板坯连铸机,3#方板坯兼容连铸机为R8m直弧形连铸机。
1.3.方板连铸机1.3.1 方坯连铸小方坯连铸一般指断面尺寸≤160×160mm2的小方坯或与之面积相当的其他断面形状的铸坯。
小方坯连铸具有设备简单,建设投资省、生产率高、生产成本低等优点,所以小方坯连铸发展较快。
特别是用小方坯连铸机生产普碳钢钢筋、棒、线材较为经济。
近年来小方坯连铸采用保护浇铸、液面控制和电磁搅拌以及计算机过程控制等新技术,可浇合金钢等钢种。
浇铸断面尺寸>160×160mm2的方坯或与之面积相当短形坯为大方坯。
大方坯和小方坯在浇注工艺上无实质区别。
在设备结构较小方坯连铸机复杂,如结晶器除应用管式结晶器之外,根据需要也有采用组合式的二冷装置根据坯子断面大小,采用不同数量的夹持辊等。
它既可浇普碳钢,也可浇合金钢或不锈钢。
方坯连铸机的流数,一般为1-4流,流间距为900-1400mm。
根据炼钢炉容量、浇注时间浇铸断面和拉速来确定流数。
小方坯连铸机配合大炉子生产,则流数较多。
原武钢-炼钢出钢量270t,铸坯断面为180×180mm2、200×200mm2已属大方坯,考虑到炉机配合,连铸机设计为一台8机8流。
二钢厂转炉出钢量为80t,考虑到炉机配合,采用一台一板二方+并列二机二流方坯兼容并列连铸机,方坯为4流。
1.3.2 罗克普型小方坯连铸机近年来,小方坯连铸机普遍采用罗克普型刚性引锭杆。
用刚性引锭杆代替传统的链式引锭杆,可使二次冷却装置进一步简化,有利于二冷喷咀布置和处理事故快等优点。
个别厂家大方坯连然机也有采用刚性引定杆,但二次冷却装置为防止铸坯鼓肚而必须增加一定排数夹持辊。
从而失去了采用罗克普刚性引锭杆的优点。
相反增加刚性引锭杆存放设备。
因此,大多数大方坯连铸机仍然采用传统的链式引锭杆。
1.4 铸坯热送铸坯热送一般是指从连铸机出来的坯子,温度为200-950℃的连铸坯直接装入加热炉,然后进行轧制。
节能效果较为明显,因而也是很多厂家追求的目标。
但热送必须具有如下条件:其一,要提高连铸坯的质量,使不精整率达到80%以上。
为此,连铸机要配备必要的质量判别、跟踪和保证系统。
其二,要采用高温连铸坯的生产技术,如气-雾冷却,全部出坯辊道置于保温罩内,热送直接轧制的连铸坯角部加热炉。
其三,要按照轧制计划所规定的钢种、钢材规格、轧制速度,组织连铸机和轧机同步作业。
目前许多国内连铸机生产都在组织热送,有的新建连铸-轧钢短流程生产。
一些使用固定断面坯为原料的中小型轧机及线材轧机,是连铸方坯直接热送的有利前提。
铸坯热送工艺的不断完善和迅速发展,必将使炼钢轧钢流程再来一次飞跃。