铝合金轮毂制造工艺及特点分析
铝合金轮毂的8种典型生产工艺

铝合金轮毂的8种典型生产工艺轮毂,别名轮圈,即轮胎内廓用以支撑轮胎的圆桶形、中心装配在轴上的部件。
常见的汽车轮毂有钢质轮毂及铝合金质轮毂。
钢质轮毂的强度高,常用于大型载重汽车;但钢质轮毂质量重,外形单一,不符合如今低碳、时尚的理念,正逐渐被铝合金轮毂替代。
目前市场上乘用车的原厂轮毂基本都是铝合金轮毂。
铝合金轮毂的生产工艺主要有以下几种:1、重力铸造金属型重力铸造是指在常压下,液体金属靠重力作用充填金属铸型而获得铸件的一种铸造方法,这也是一种古老的铸造方法。
2、低压铸造低压铸造是将铸型放在一个密闭的炉子上面,型腔的下面用一个管(叫升液管)和炉膛里的金属液相通。
3、挤压铸造法4、铸造旋压铸旋分“低压铸造+旋压”和“重力铸造+旋压”两种工艺。
5、常规锻造锻造是铝轮毂应用较早的成形工艺之一。
6、铸造锻造法它是将铸件作为锻造工序的坯料使用,对其进行塑X加工的方法。
7、半固态模锻工艺所谓半固态模锻,就是将半固态坯料加热到有50%左右体积液相的半固态状态后一次模锻成形,获得所需的接近尺寸成品零件的工艺,这是一种介于固态成形和液态成形之间的崭新工艺。
近10年来,半固态成形技术在国外获得了广泛的应用,已逐步成为各先进工业国家竞相发展的一个新领域,被专家学者称为21世纪新一代新兴的金属成形技术。
预计在相当长的一段时期内,半固态成形的主要市场是汽车工业,应用最成功和最广泛的是汽车铝合金零件。
美国已建成数家铝合金半固态模锻工厂,其中美国的AEMP(Alumax Enginered metal Process)公司与Superior工业公司合作于1992年在阿肯色州建成了全球首家半固态模锻铝合金汽车轮毂厂。
用半固态模锻代替低压铸造生产ZL101铝合金车轮毂,不仅能减少机械加工量和提高生产率,而且还可以提高机械X能,减轻质量。
8、锻造旋压比较高端的成形工艺,目前国内只有10%左右企业采用该工艺进行生产,产品主要供应国内外的大巴、货车及高端轿车市场。
《2024年7A04高强铝合金轮毂锻造成形工艺研究》范文
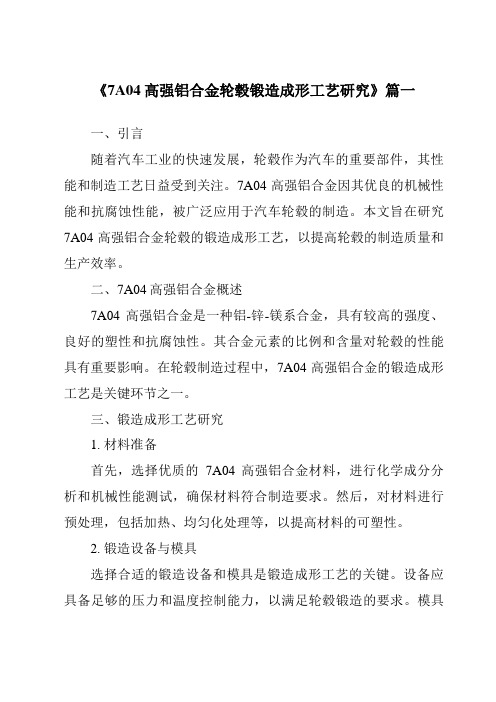
《7A04高强铝合金轮毂锻造成形工艺研究》篇一一、引言随着汽车工业的快速发展,轮毂作为汽车的重要部件,其性能和制造工艺日益受到关注。
7A04高强铝合金因其优良的机械性能和抗腐蚀性能,被广泛应用于汽车轮毂的制造。
本文旨在研究7A04高强铝合金轮毂的锻造成形工艺,以提高轮毂的制造质量和生产效率。
二、7A04高强铝合金概述7A04高强铝合金是一种铝-锌-镁系合金,具有较高的强度、良好的塑性和抗腐蚀性。
其合金元素的比例和含量对轮毂的性能具有重要影响。
在轮毂制造过程中,7A04高强铝合金的锻造成形工艺是关键环节之一。
三、锻造成形工艺研究1. 材料准备首先,选择优质的7A04高强铝合金材料,进行化学成分分析和机械性能测试,确保材料符合制造要求。
然后,对材料进行预处理,包括加热、均匀化处理等,以提高材料的可塑性。
2. 锻造设备与模具选择合适的锻造设备和模具是锻造成形工艺的关键。
设备应具备足够的压力和温度控制能力,以满足轮毂锻造的要求。
模具的设计和制造应考虑轮毂的形状、尺寸和精度要求,确保锻造过程中轮毂的形状和尺寸精度。
3. 锻造过程锻造过程包括加热、锻打、冷却等步骤。
首先,将7A04高强铝合金材料加热至适当的温度,以降低材料的塑性变形抗力。
然后,通过锻打的方式使材料发生塑性变形,形成所需的轮毂形状。
最后,进行冷却处理,使轮毂的内部组织得到充分稳定。
4. 工艺参数优化在锻造过程中,应优化工艺参数,包括加热温度、锻打速度、冷却方式等。
通过实验和仿真分析,确定最佳的工艺参数组合,以提高轮毂的制造质量和生产效率。
同时,要关注模具的使用和维护,以延长模具的使用寿命。
四、研究结果与分析通过对7A04高强铝合金轮毂锻造成形工艺的研究,我们得到了以下结果:1. 优化了材料准备过程,提高了材料的可塑性;2. 选择了合适的锻造设备和模具,提高了轮毂的形状和尺寸精度;3. 通过优化工艺参数,提高了轮毂的制造质量和生产效率;4. 分析了锻造过程中可能出现的缺陷和问题,提出了相应的解决措施。
《7A04高强铝合金轮毂锻造成形工艺研究》
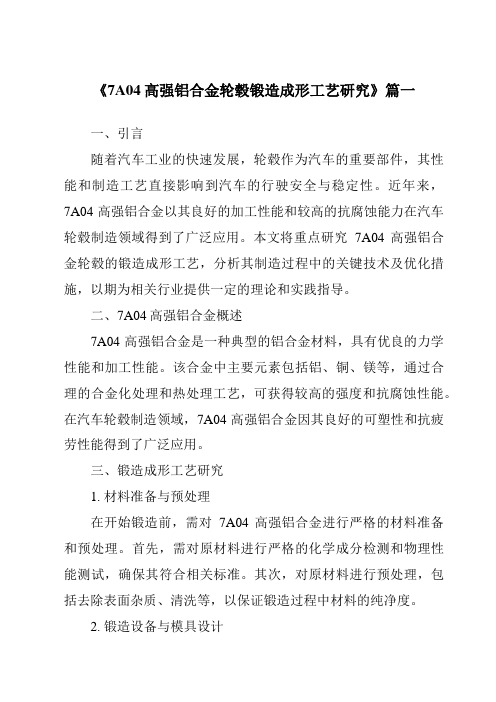
《7A04高强铝合金轮毂锻造成形工艺研究》篇一一、引言随着汽车工业的快速发展,轮毂作为汽车的重要部件,其性能和制造工艺直接影响到汽车的行驶安全与稳定性。
近年来,7A04高强铝合金以其良好的加工性能和较高的抗腐蚀能力在汽车轮毂制造领域得到了广泛应用。
本文将重点研究7A04高强铝合金轮毂的锻造成形工艺,分析其制造过程中的关键技术及优化措施,以期为相关行业提供一定的理论和实践指导。
二、7A04高强铝合金概述7A04高强铝合金是一种典型的铝合金材料,具有优良的力学性能和加工性能。
该合金中主要元素包括铝、铜、镁等,通过合理的合金化处理和热处理工艺,可获得较高的强度和抗腐蚀性能。
在汽车轮毂制造领域,7A04高强铝合金因其良好的可塑性和抗疲劳性能得到了广泛应用。
三、锻造成形工艺研究1. 材料准备与预处理在开始锻造前,需对7A04高强铝合金进行严格的材料准备和预处理。
首先,需对原材料进行严格的化学成分检测和物理性能测试,确保其符合相关标准。
其次,对原材料进行预处理,包括去除表面杂质、清洗等,以保证锻造过程中材料的纯净度。
2. 锻造设备与模具设计选择合适的锻造设备和模具是锻造成形工艺的关键。
根据轮毂的形状和尺寸要求,设计合理的模具结构,确保在锻造过程中能够获得理想的轮毂形状和尺寸精度。
同时,选择合适的锻造设备,如液压机、机械压力机等,以满足轮毂锻造过程中的压力和温度要求。
3. 锻造过程与控制在锻造过程中,需严格控制温度、压力和时间等参数。
首先,将预处理后的材料加热至适当的温度范围,以降低材料的塑性变形抗力。
其次,在设定的压力下进行锻造,通过多次锻打和整形,使材料逐渐成形为所需的轮毂形状。
最后,对锻造过程中的温度、压力和时间进行实时监控和调整,以确保轮毂的成形质量和性能。
四、关键技术及优化措施1. 合金成分优化通过对7A04高强铝合金的合金成分进行优化,可以进一步提高其力学性能和抗腐蚀性能。
通过调整合金中各元素的含量比例,以及采用先进的合金化处理技术,可以提高材料的强度、硬度、延展性和抗疲劳性能。
铝合金车轮生产工艺

铝合金车轮生产工艺铝合金车轮是汽车轮胎的重要组成部分,具有重量轻、刚性好、具有良好的制动和减震性能等优点。
铝合金车轮的生产工艺主要包括原料选取、铸造、热处理、机械加工、表面处理等几个步骤。
首先,原料选取。
铝合金车轮的主要原料是铝合金,在选择原料时需要优先考虑合金的强度、耐久性和耐腐蚀性能。
常用的铝合金有A356、A357、A356.2等,其中A356是最常用的材料之一。
第二,铸造。
铸造是铝合金车轮生产的核心环节。
传统的铸造工艺有压铸和重力铸造两种。
压铸是将铸液压入金属模具中进行冷却凝固,然后取出成品。
重力铸造是将铸液倒入模具中,通过重力作用使其凝固。
近年来,尤其是在高性能车轮的生产中,还使用了低压铸造和半固态铸造等先进技术。
第三,热处理。
热处理是为了提高铝合金车轮的强度和耐久性。
常用的方法有T6热处理和气体热处理。
T6热处理是指对铝合金车轮进行固化处理,通过加热和冷却过程来改变合金的晶体结构,提高强度。
气体热处理则是将铝合金车轮放入特定的气体环境中加热,实现强化效果。
第四,机械加工。
机械加工是为了使铝合金车轮达到更加精确的尺寸和形状要求。
常见的机械加工方式包括车削、铣削、切削等操作,可以将铝合金车轮的外形和内部孔洞进行加工和修整。
最后,表面处理。
表面处理是为了提高铝合金车轮的耐腐蚀性、装饰性和表面硬度。
常见的表面处理方法有喷砂、阳极氧化、电镀等。
喷砂是通过喷砂机将合适颗粒的砂浆喷射到铝合金车轮表面,去除表面氧化层和不良物质。
阳极氧化是通过施加电流和特定电解液使铝合金车轮表面生成一层氧化膜,提高其耐腐蚀性和装饰性。
电镀则是将铝合金车轮浸入镀液中进行电化学反应,使其表面镀上一层金属或合金,提高硬度和耐腐蚀性。
综上所述,铝合金车轮的生产工艺包括原料选取、铸造、热处理、机械加工和表面处理等几个重要步骤,每个步骤都对最终产品的质量和性能有着重要影响。
通过科学合理的工艺流程和控制,可以生产出优质的铝合金车轮。
铝合金轮毂制作工艺

铝合金轮毂制作工艺引言铝合金轮毂广泛应用于汽车、摩托车等交通工具中,它具有轻质、高强度、耐腐蚀等优点,成为现代车辆的重要组成部分。
本文将详细介绍铝合金轮毂制作工艺,包括材料选择、铸造工艺、加工工艺等内容,以期为读者深入了解铝合金轮毂制作工艺提供有效的参考。
材料选择铝合金轮毂的材料选择是制作工艺的首要考虑因素。
常见的铝合金材料有A356、A357、6061等,这些铝合金具有良好的加工性能、强度和耐腐蚀性。
根据使用环境、车辆类型和制造成本等因素,选择合适的铝合金材料非常重要。
铸造工艺铸造是铝合金轮毂制作的主要工艺之一。
铸造工艺可以根据具体要求分为压力铸造和重力铸造两种类型。
压力铸造压力铸造是将熔化的铝合金通过高压注入模具中,在短时间内冷却凝固形成轮毂的工艺。
该工艺具有高生产效率、良好的铸件表面质量和一致性等优点。
具体步骤如下:1.准备工作:准备好模具、铸造设备和熔炉等。
2.加热熔化:将铝合金料加入炉内进行加热熔化,控制好熔化温度和时间。
3.注入模具:熔化的铝合金通过喷射系统,高压注入模具中,填充整个模腔。
4.冷却凝固:注入模具后,通过冷却系统冷却轮毂,使其凝固成型。
5.模具开启:等待轮毂完全凝固后,打开模具取出轮毂。
重力铸造重力铸造是利用重力作用使熔化的铝合金流入模腔中形成轮毂的工艺。
相比于压力铸造,重力铸造工艺成本较低,适用于制作较大尺寸的轮毂。
具体步骤如下:1.准备工作:准备好模具、铸造设备和熔炉等。
2.加热熔化:将铝合金料加入炉内进行加热熔化,控制好熔化温度和时间。
3.浇注:熔化的铝合金通过铸造设备,由上方浇注入模具中,利用重力作用填充整个模腔。
4.冷却凝固:注入模具后,通过冷却系统冷却轮毂,使其凝固成型。
5.模具开启:等待轮毂完全凝固后,打开模具取出轮毂。
加工工艺铝合金轮毂制作完成后,还需要进行进一步的加工工艺,以提高轮毂的精度和表面质量。
常见的加工工艺包括机加工、热处理和喷涂等。
机加工机加工是通过机械设备对铝合金轮毂进行精细加工的工艺。
铝合金轮毂制造工艺

铝合金轮毂制造工艺铝合金轮毂是现代汽车制造中常用的一种轮毂材料,它具有轻质、高强度、耐腐蚀等优点,因此被广泛应用于汽车制造中。
本文将介绍铝合金轮毂的制造工艺。
一、铝合金轮毂的材料选择铝合金轮毂的材料选择非常重要,它直接影响到轮毂的质量和性能。
目前常用的铝合金材料有A356、A357、A356.2、A357.2等。
其中,A356和A357是最常用的两种材料,它们具有良好的铸造性能和机械性能,可以满足轮毂的要求。
二、铝合金轮毂的铸造工艺铝合金轮毂的制造工艺主要包括铸造、热处理、机加工等环节。
其中,铸造是最关键的一步,它直接影响到轮毂的质量和性能。
1.模具制造模具是铸造的关键,它的制造质量直接影响到铸造件的质量。
模具的制造需要根据轮毂的形状和尺寸进行设计,然后制造出模具。
模具的制造需要考虑到铸造过程中的收缩率和变形,以保证铸造件的尺寸精度和形状精度。
2.熔炼铝合金铝合金轮毂的铸造采用熔炼铝合金的方法。
首先将铝合金料放入熔炉中加热,使其熔化。
然后加入一定量的熔剂和精炼剂,以去除杂质和气泡。
最后将熔融的铝合金倒入模具中进行铸造。
3.铸造铸造是铝合金轮毂制造的关键环节。
在铸造过程中,需要控制铝合金的温度、流速和压力等参数,以保证铸造件的质量和性能。
铸造完成后,需要进行冷却和固化,以保证铸造件的尺寸精度和形状精度。
三、铝合金轮毂的热处理工艺铝合金轮毂的热处理工艺是为了改善轮毂的性能和耐腐蚀性。
常用的热处理工艺有T6、T7、T8等。
其中,T6是最常用的一种热处理工艺,它可以提高铝合金轮毂的强度和硬度,同时保持良好的韧性和耐腐蚀性。
四、铝合金轮毂的机加工工艺铝合金轮毂的机加工工艺是为了加工轮毂的表面和孔洞等部位。
常用的机加工工艺有车削、铣削、钻孔等。
机加工工艺需要根据轮毂的形状和尺寸进行设计,以保证加工精度和表面质量。
五、铝合金轮毂的质量检测铝合金轮毂的质量检测是为了保证轮毂的质量和性能。
常用的质量检测方法有外观检查、尺寸检查、硬度检测、化学成分分析等。
铝合金车轮的制造工艺技术
铝合金车轮的制造工艺技术铝合金车轮是现代汽车工业中常用的重要部件之一,具有重量轻、强度高、耐腐蚀等优点。
其制造工艺技术主要包括原料选择、熔炼、铸造、热处理和机械加工等几个步骤。
首先,在制造铝合金车轮时,需要选择合适的原料。
常用的原料主要是高纯度的铝和添加一定比例的合金元素,如硅、镁、锰等。
这些合金元素能够提高铝合金的强度和硬度,同时还能提高铝在高温下的稳定性。
接下来,制造铝合金车轮的第二个步骤是熔炼。
选择好原料后,需要将其放入熔炉中进行熔化,以保证原料可以完全溶解在一起,形成均匀的熔体。
在熔炼过程中,需要控制好温度和搅拌速度,以确保合金元素能够均匀地分布在铝熔体中。
第三个步骤是铸造。
将熔化好的铝合金液体倒入车轮的模具中,然后通过快速冷却和凝固来形成车轮的形状。
在铸造过程中,需要控制好冷却速度和温度,以确保车轮能够具有良好的强度和表面质量。
铝合金车轮的第四个工艺步骤是热处理。
通过热处理,可以进一步优化车轮的性能,主要是通过控制合金元素的扩散和再结晶来实现。
常用的热处理方法包括T4和T6两种,在热处理过程中,需要控制好温度和时间,以确保车轮能够达到设计要求的强度和硬度。
最后一个步骤是机械加工。
在完成以上步骤后,还需要对车轮进行进一步的加工和整形,以确保其尺寸精确和表面平整。
常见的机械加工工艺包括车削、镗床、磨削等,这些工艺能够有效地提高车轮的尺寸精度和表面质量。
综上所述,铝合金车轮的制造工艺技术包括原料选择、熔炼、铸造、热处理和机械加工等几个步骤。
这些工艺能够使车轮具有良好的强度、硬度和表面质量,提高汽车的性能和安全性。
车轮是车辆中至关重要的组成部分,它直接关系到汽车的操控性、安全性和舒适性。
铝合金车轮作为一种轻量化、高强度的选材方案,得到了广泛的应用。
下面将进一步详细介绍铝合金车轮的制造工艺技术。
首先,原料的选择是铝合金车轮制造的关键一步。
铝合金车轮的主要原料是高纯度的铝以及添加一定比例的合金元素,例如硅、镁、锰等。
浅析铝合金轮毂制造工艺
浅析铝合金轮毂制造工艺随着社会的快速发展,人们的生活水平以及经济水平也是越来越高。
汽车节能化成为了未来汽车发展的必要趋势,所以人们对于汽车节能降耗的要求也是不断的提高。
铝合金轮毂的优势就是强度高、质量轻、价格合理、成型度好以及回收率高等,而这些正好能够符合人们对汽车减少耗油、降低自重以及减少环境污染的需求。
因此,研究鋁合金轮毂的制造工艺,对我国汽车工业绿色发展具有非常重要的意义。
1铝合金轮毂的特点(1)优点:首先,铝合金轮毂可以减少环境污染,提高环境质量。
铝合金轮毂质量很轻,在汽车中应用可以减少汽车总重量,减少汽车消耗,进一步减低废弃废物的产生,提高环境质量;其次,铝合金轮毂的高强度及较高的热传导系数,可以有效的提高汽车驾驶司机的安全性。
汽车在行驶过程中由于温度过高造成的爆胎事故屡见不鲜,造成这种现象的主要原因就是汽车在制动过程中会产生大量的热能,这些热量会通过轮毂传递到轮胎上,造成轮胎爆炸。
而铝合金轮毂的热传导系数达到了钢轮毂、铁轮毂的三倍,能够降低制动热能的传导,提高汽车行驶的司机安全;最后,汽车中应用铝合金轮毂,与之配合的大多是子午线轮胎,同其它轮胎相比,子午线轮胎能够有效的减少汽车震动和缓冲,增加汽车司机驾驶的舒适度;(2)缺点。
首先,铝合金材料的硬度没有钢轮毂高,在生产铝合金轮毂是有一定的几率会出现砂眼的状况;其次,铝制材料较脆,在使用时会出现一定的小裂纹状况,并且这些裂纹很难察觉,会减低汽车的安全性;最后,铝合金轮毂无内胎汽车中使用时,会有内气不足的现象,且其造价也比普通轮毂要高。
2铝合金轮毂制造工艺2.1铸造法图1 铝合金轮毂重力铸造示意图铝合金轮毂最普通的制造方法就是铸造法,其具备生产成本低廉、品种丰富多样以及适应性较强的特点,其工艺方法分为四种。
(1)压力铸造法。
压力铸造法指的是在高压的作用下,液态金属以较高的速度填充压铸型腔形成铸件的工艺方法。
压力铸造法由于铸机的生产效率高,完全不需要通过大量的后续加工就可以直接使用,有效缩减了加工设备的使用,并且节约了材料的运用。
《7A04高强铝合金轮毂锻造成形工艺研究》范文
《7A04高强铝合金轮毂锻造成形工艺研究》篇一一、引言随着汽车工业的快速发展,轻量化、高强度和高耐久性的轮毂材料已成为市场的重要需求。
7A04高强铝合金以其优良的机械性能、加工性能和抗腐蚀性能,成为制造汽车轮毂的理想材料。
本文针对7A04高强铝合金轮毂的锻造成形工艺进行深入研究,探讨其成形过程中的关键技术和影响因素,以提高轮毂的成形质量和生产效率。
二、7A04高强铝合金的特性7A04高强铝合金是一种以铝为基础的合金,通过添加适量的合金元素(如铜、镁、锰等)提高其强度和耐腐蚀性。
该合金具有优良的加工性能、抗腐蚀性能和高强度,广泛应用于航空、航天、汽车等工业领域。
三、锻造成形工艺7A04高强铝合金轮毂的锻造成形工艺主要包括原材料准备、模具设计、锻造过程和后续处理四个部分。
(一)原材料准备选用合格的7A04高强铝合金锭料,进行熔炼、精炼和均匀化处理,以获得纯净、组织均匀的合金材料。
同时,对材料进行热处理,以提高其成形性能。
(二)模具设计根据轮毂的形状和尺寸要求,设计合理的模具结构。
模具应具有良好的强度、耐磨性和热稳定性,以保证锻造过程的顺利进行。
(三)锻造过程锻造过程包括预处理、成形和后处理三个阶段。
预处理阶段主要对合金材料进行加热和保温,使其达到理想的锻造温度。
成形阶段通过模具将材料锻造成预定形状的轮毂。
后处理阶段包括冷却、去毛刺和热处理等工艺,以提高轮毂的机械性能和表面质量。
(四)后续处理对锻造后的轮毂进行表面处理,如喷涂、氧化等,以提高其耐腐蚀性和美观度。
同时,对轮毂进行质量检测,确保其符合设计要求。
四、关键技术和影响因素(一)模具设计及制造技术模具的设计和制造是锻造成形工艺的关键环节。
模具的结构应合理、尺寸应准确,以保证轮毂的成形质量和生产效率。
同时,模具的材料和热处理工艺也应考虑周全,以提高模具的使用寿命和降低制造成本。
(二)锻造温度及变形速率控制锻造温度和变形速率对轮毂的成形质量和机械性能有重要影响。
《7A04高强铝合金轮毂锻造成形工艺研究》范文
《7A04高强铝合金轮毂锻造成形工艺研究》篇一一、引言随着汽车工业的快速发展,轮毂作为汽车的重要部件,其性能和制造工艺对汽车的整体性能有着重要的影响。
7A04高强铝合金以其出色的力学性能、抗腐蚀性能以及良好的加工性能,广泛应用于轮毂制造。
因此,研究7A04高强铝合金轮毂的锻造成形工艺,对提升轮毂制造技术和产品质量具有重要意义。
二、7A04高强铝合金的特性和应用7A04高强铝合金是一种铝、锌、镁、铜等元素构成的合金,具有优良的机械性能和抗腐蚀性能,其强度高、塑性好、耐腐蚀。
由于其优秀的物理和化学性能,7A04高强铝合金广泛应用于航空航天、汽车制造等领域,特别是轮毂等重要部件的制造。
三、锻造成形工艺研究(一)材料准备首先,选择优质的7A04高强铝合金原材料,经过严格的检验和测试,确保其符合制造要求。
此外,还需要准备好必要的模具、工具和设备。
(二)锻造工艺流程锻造工艺主要包括坯料加热、锻造变形、热处理等步骤。
在坯料加热阶段,需要控制好加热温度和时间,以避免材料的过热或过烧。
在锻造变形阶段,通过控制模具和压力,使材料发生塑性变形,形成所需的轮毂形状。
在热处理阶段,通过淬火、回火等工艺,进一步提高材料的机械性能和抗腐蚀性能。
(三)工艺参数优化针对7A04高强铝合金的锻造成形工艺,需要进行工艺参数的优化。
主要包括模具设计、锻造温度、锻造压力、热处理工艺等方面的优化。
通过实验和模拟,找出最佳的工艺参数组合,以提高轮毂的成形质量和生产效率。
四、实验与结果分析(一)实验方法采用实验的方法,对7A04高强铝合金轮毂的锻造成形工艺进行研究。
通过改变模具设计、锻造温度、锻造压力等工艺参数,观察轮毂的成形质量和机械性能的变化。
(二)实验结果通过实验,发现当模具设计合理、锻造温度和压力适当时,可以获得成形质量好、机械性能优良的轮毂。
同时,通过优化热处理工艺,可以进一步提高轮毂的抗腐蚀性能。
此外,还发现通过合理的工艺参数组合,可以提高生产效率,降低生产成本。
- 1、下载文档前请自行甄别文档内容的完整性,平台不提供额外的编辑、内容补充、找答案等附加服务。
- 2、"仅部分预览"的文档,不可在线预览部分如存在完整性等问题,可反馈申请退款(可完整预览的文档不适用该条件!)。
- 3、如文档侵犯您的权益,请联系客服反馈,我们会尽快为您处理(人工客服工作时间:9:00-18:30)。
铝合金轮毂制造工艺及特点分析
【摘要】铝合金轮毂以其质量轻、减震性优良、散热快、寿命长等特点,在现代汽车制造中得到了广泛的应用。
本文概述了铝合金轮毂的一些常见的制造工艺,并对其特点进行了简要分析。
【关键词】铝合金;轮毂;制造工艺;特点
长期以来,钢制轮毂占据着汽车轮毂生产的主导地位。
随着人们对汽车的舒适度、节能环保等方面要求的提高,钢制轮毂已不再适应现代汽车的需求。
铝合金轮毂的出现,以优异的性能和迅猛的技术发展取代了钢制轮毂的主导地位,在现代汽车中得到了广泛的应用。
1.铝合金轮毂的优点及性能要求
铝合金轮毂与钢制轮毂相比,具有质量轻、节省能源的优点。
由于材质的差异,铝合金轮毂的质量可比钢制轮毂减轻三到四成,可以有效提高轮毂的转动惯性,使汽车易于加速,并减少了制动所需的能耗,从而降低了油耗。
此外,由于铝合金的振动性能比钢强,可以减少震动,改善车辆的重心,平衡性能优于钢制轮毂,尤其在高速行驶时可以得到明显的体现。
在散热方面,铝合金轮毂的散热系数是钢制轮毂的两到三倍,在高速行驶时仍然可以保持合适的温度,减少爆胎的危险,提高了行车安全。
鉴于铝合金轮毂的优点,在制造铝合金轮毂的时候,就必须将这些优点全部发挥出来,才能使得铝合金轮毂充分体现其优良的性能。
一般来说,一个合格的铝合金轮毂必须具备以下几个特点:(1)材质、尺寸、形状准确合理,这样才能充分发挥轮毂的作用,具有通用性;(2)汽车在行驶时,轮毂的横、纵向振摆小,失衡量与惯性矩小;(3)在保证轻便的同时,还要具有足够的强度、韧性和稳定性;(4)可分离性好;(5)性能具有持久性。
2.铝合金轮毂制造工艺及特点分析
2.1铸造法
铝合金轮毂的铸造法成形具有适应性强、品种多样、生产成本较低的优点,已经成为生产铝合金轮毂最普遍的方法,在全世界的铝合金轮毂中,采用铸造法生产的占80%以上。
其工艺方法主要有重力铸造、低压铸造、压力铸造以及挤压铸造等。
2.1.1重力铸造法
重力铸造法是指金属在熔融的状态下依靠自身重力的作用注入模具中而获得铸件的一种工艺方法。
重力铸造法大致可分为制芯、浇铸、整理三个步骤,每
一个步骤都在严格的工艺参数下进行。
重力铸造工艺得到的铸件机械性能高,该工艺还具有生产效率高、工序简单、铸件缺陷少、较易实现机械自动化等优点。
2.1.2低压铸造法
低压铸造指金属液体在压力作用下充填型腔以形成铸件的一种铸造方法,由于所需要的压力较小,所以称为低压铸造。
其工艺流程大致分为熔化、低压铸造成型、热处理、机加、涂装几个步骤。
低压铸造时液体金属充型平稳,铸件成型好,形成的轮廓清晰,表面光滑。
铸件致密,机械性能高。
此外,该工艺所需的设备简单,同样易于实现机械自动化生产。
2.1.3压力铸造法
压力铸造法是指在高压下使液态金属以较高的速度充填压铸型型腔而获得铸件的一种工艺方法。
该工艺得到的铸件尺寸精度高,表面光洁度好,强度与硬度均表现良好,产品性能稳定。
同时,该工艺的生产依靠压铸机等设备生产效率高,无需进行大量的后续加工产品便可直接使用,既节省材料又减少了加工设备。
但这种铸造工艺对内凹复杂的铸件生产较为困难,而且易产生气孔,对高熔点合金压铸寿命低。
2.1.4挤压铸造法
挤压铸造法是在为解决普通压铸与传统挤压铸造两项技术存在的缺陷而提出的一种铸造方法,它综合了两者的优势,其核心工艺便是用普通压铸充型,用传统挤压铸造补缩。
挤压铸造件比低压铸造件的力学性能高:产品既有接近锻件的优良力学性能,又有精铸件一次精密成形的高效率、高精度。
其投资大大低于低压铸造法。
2.2锻造法
锻造法是指利用冲击力或压力使金属变形而获得所需形状和尺寸的锻件的一种生产工艺,主要分为自由锻和模锻。
该方法是最早应用于铝合金轮毂的成型工艺之一,锻造法生产出来的铝合金轮毂具有高强度、高韧性以及高抗疲劳强度等优点,相比铸造工艺,锻造法还具有抗腐蚀性好、尺寸精确、易于加工等特点。
锻造法的缺点是生产工艺复杂,生产成本高。
2.3旋压法
旋压法是一种结合了锻造、挤压等工艺特点,根据材料的塑性特点设置合理的工艺参数,对毛坯产生连续变形作用而逐渐成形的一种加工方法。
旋压法是生产铝合金轮毂的先进方法,该方法生产的轮毂可以使金属保持较高的致密度和轮毂的动平衡,在保证轮毂钢度的同时,又可以使轮毂轻便耐用。
轮毂旋压的方式主要有普通旋压和强力旋压两种,普通旋压主要是改变坯料
的形状、壁厚基本不变或改变很少的一种旋压成型工艺。
普通旋压工艺的优点在于制模周期短、工序紧凑、制品范围广、可以成形一些不易成形的稀有金属等。
强力旋压工艺既改变坯料形状有改变壁厚,其生产效率要高于普通旋压,适用范围也大为扩展。
铝合金轮毂旋压成型工艺具有不受尺寸限制、性能优良、安全性好、节省材料等优点,弥补了低压铸造无法满足大尺寸、高负荷的高端产品市场需求以及锻造法生产成本高的缺陷。
2.4半固态模锻法
半固态模锻法是锻造的一种,是指将固态和液态金属混合成形的一种生产工艺。
用半固态模锻法生产的铝合金轮毂,力学性能高于压铸和挤压铸造工艺,具有机械性能好、成品率高、材料利用率高以及生产效率高等优点,而且可以显著减少机械加工量,减少能源消耗,可生产出复杂形状。
但半固态模锻法要求的技术高,对锭坯组织结构要求严格,模具结构复杂,对设计人员以及生产人员的技术要求都比较高。
在国外主要应用于铝合金零部件方面,是未来发展最具潜力的新兴金属成形技术,目前实际应用还较少,有待进一步开发。
3.结语
近年来,由于我国汽车工业的快速发展,铝合金轮毂市场潜力日趋显现,需求不断扩大;同时跨国公司的采购量出口量也在迅猛增长,使我国铝合金轮毂需求持续增长。
我国铝合金轮毂生产企业虽然已形成较大规模,但技术含量仍就不高,缺乏高科技含量的产品,轮毂制造企业只有努力提高自身的加工工艺,增强铝合金轮毂的设计研发能力,适应市场的需求,根据产品特点选择合适的制造工艺,才能在国际竞争中立于不败之地。
[科]
【参考文献】
[1]张海渠等.铝合金轮毂成形工艺的应用与研究进展[J].沈阳大学学报,2011,23(4).
[2]郑祥健,金龙兵,王国军,陶志民.铝合金轮毂的生产和市场现状[J].轻合金加工技术,2004,(7):8~11.
[3]李颖,王晨,段海全.铝合金轮毂的结构设计及性能分析[J].三门峡职业技术学院学报,2011,(zl).
[4]李晓敏.我国汽车铝合金轮毂发展现状及建议[J].轻金属,2011,(6):3~7.。