设备振动故障在线检测技术案例分析
振动诊断分析案例(十七)

振动故障分析诊断案例1 前某风机在检修前的监测中发现电机前端存在部件配合松动的故障现象分析判断轴承存在有跑外圈或轴承间隙增大的故障现象袁通过在4月份的大修中进行拆检更换轴承和端盖发现确实存在跑外圈的故障现象袁此报告既含有轴承故障特征,也具径向特别是垂直方向振动大;2除基频分量外还有较大的倍频分量特别是3到10倍频,3振动可能具有高度的方向性;4可能有分数倍频分量,这些分量随着时间的增长而增大,其中机械松动分为A/B/C 型机械松动,A 型松动1倍频占主要分量袁主要是基础变形或底座松动造成,B 型松动1-2倍频占主要分量,主要是螺栓松动袁框架结构裂纹轴承座裂纹等造成,C 型松动特征是出现大量高次谐波,频谱中存在精确的0.5倍频和1倍频遥出现此现象的原因有轴承衬套在其盖内松动,轴承松动并在轴上旋转袁轴承间隙过大,叶轮在轴上松动等。
2 分析2.1 型号6314轴承相关特征频率型号6314轴承相关特征如表1所示2.2 振动值情况风机的振动值如表2所示2.3 分析情况1)振动值分析遥,该设备自2月份以来振动值均处于较高的水平,其中径向水平和垂直方向振动值大于轴向振动,一般风机径向振动大有以下几方面原因,平行不对中引起,风叶不平衡引起,基础薄弱或松动引起[ 2)谱图分析电机前后端加速度波形图中均未出现明显的周期冲击信号,但频谱中均有对应的轴承SKF 6314滚动体50Hz,与保持架150Hz 故障特征频率及其谐频分量存在如图13 诊断1)加速度波形未出现明显周期冲击信号,速度值及加速度值频谱图中均存在1/2/3及大量高次谐频袁,属于C 型机械松动故障,内部零部件配合松动故障,特征为出现精确的0.5倍频及大量高次谐频遥 2)频谱中存在明显的轴承外圈频率及其谐频,诊断为轴承跑外圈。
4 处理结果通过检修拆检发现电机前端轴承跑外圈袁前端端盖因跑外圈而磨损严重袁验证了分析的正确性袁如图2。
振动诊断分析案例(十五)
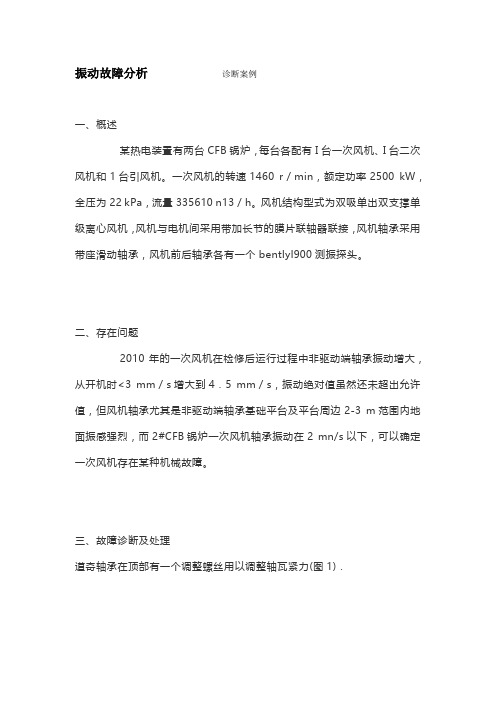
振动故障分析诊断案例一、概述某热电装置有两台CFB锅炉,每台各配有I台一次风机、I台二次风机和1台引风机。
一次风机的转速1460 r/min,额定功率2500 kW,全压为22 kPa,流量335610 n13/h。
风机结构型式为双吸单出双支撑单级离心风机,风机与电机间采用带加长节的膜片联轴器联接,风机轴承采用带座滑动轴承,风机前后轴承各有一个bentlyl900测振探头。
二、存在问题2010年的一次风机在检修后运行过程中非驱动端轴承振动增大,从开机时<3 mm/s增大到4.5 mm/s,振动绝对值虽然还未超出允许值,但风机轴承尤其是非驱动端轴承基础平台及平台周边2-3 m范围内地面振感强烈,而2#CFB锅炉一次风机轴承振动在2 mn/s以下,可以确定一次风机存在某种机械故障。
三、故障诊断及处理道奇轴承在顶部有一个调整螺丝用以调整轴瓦紧力(图1).按照风机厂家说明书要求,轴承安装时需将力矩扳手调整至2500 in.lb(约282 N·m)拧紧调整螺丝。
发现轴承振动增大后,将力矩扳手调整至280 N·m重新上紧,调整螺丝不动。
对机组振动进行监测,以进一步分析故障原因,风机测点布置。
见图2。
由表l可知。
风机测点4水平方向振动最大,振动值为4.7 mm /s。
从测点4水平方向测点的时域波形(图3)和振动速度频谱(图4)可以看出,振动频谱主要表现为1倍频,同时伴随较丰富的谐频,从时域波形来看,有周期性冲击碰摩现象;而测点3的振动速度频谱有丰富谐频及整分数倍频率(图5)。
分析认为可能原因为:①轴瓦磨损或轴瓦间隙偏大;②机组动静部分间隙不均造成周期性的碰摩,可能是风机轴封碰摩或叶轮与机壳处气隙过小引起摩擦;③转子的运行过程出现不平衡或不对中。
锅炉停炉进行年度例行检修,借此机会对风机进行检查,重点是针对状态监测分析的原因做相应检查。
①检查风机轴瓦,风机轴瓦完好。
根据厂家图纸要求重新调整风机轴瓦间隙、找正对中。
机械振动分析技术在故障预测中的应用案例

机械振动分析技术在故障预测中的应用案例引言:故障预测是机械维护和设备管理的重要组成部分,通过分析机械振动数据可以提前发现故障迹象,预测设备的运行状态。
机械振动分析技术可以帮助企业提高设备可靠性,降低维修成本,提高生产效率。
本文将介绍两个机械振动分析技术在故障预测中的应用案例,分别是基于时域分析和频域分析的方法。
案例一:基于时域分析的机械故障预测方法背景:某工厂的离心泵是生产装置中的关键设备,但近期频繁出现故障,造成生产中断和高额维修费用。
为了提前发现故障迹象,降低故障率,工厂决定采用机械振动分析技术。
方法:1. 数据采集:工程师安装加速度计和振动传感器,定期采集泵的振动数据。
2. 时域分析:将采集到的振动数据进行时域分析,计算出振动信号的包络谱和时域波形图。
3. 故障诊断:通过对包络谱和时域波形图的分析,识别泵的故障迹象,并查找可能的故障源。
4. 故障预测:根据故障迹象和振动特征,建立故障预测模型,并对未来的振动数据进行预测。
结果:经过分析和诊断,工程师发现泵的轴承存在严重的磨损,可能导致泵的故障。
根据振动数据建立的故障预测模型预测了轴承的寿命,并提出了维修建议。
工厂按照建议进行维修,成功地避免了设备故障和生产中断。
案例二:基于频域分析的机械故障预测方法背景:某电力公司有一台重要的汽轮发电机组,但近期出现了振动异常的情况,令人担忧。
为了保证发电机组的安全运行,电力公司决定采用机械振动分析技术。
方法:1. 数据采集:工程师使用振动传感器采集发电机组的振动数据,并记录下来。
2. 频域分析:将振动数据转化为频域信号,进行频谱分析,得到频谱图和频域特征。
3. 故障诊断:通过对频谱图和频域特征的分析,识别异常振动的频率和幅值,并与故障手册中的故障特征进行对比。
4. 故障预测:根据异常振动频率和幅值的变化趋势,预测发电机组的故障类型和发展趋势。
结果:经过分析和诊断,工程师发现发电机组的转子存在磨损,导致了振动异常。
汽轮发电机组振动故障诊断及案例
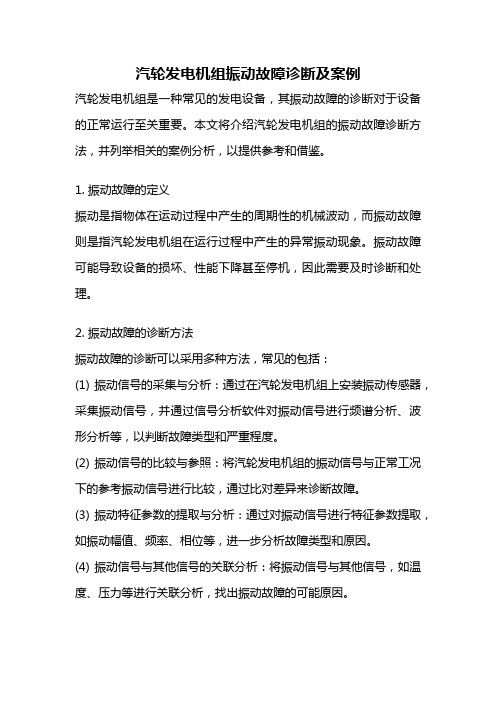
汽轮发电机组振动故障诊断及案例汽轮发电机组是一种常见的发电设备,其振动故障的诊断对于设备的正常运行至关重要。
本文将介绍汽轮发电机组的振动故障诊断方法,并列举相关的案例分析,以提供参考和借鉴。
1. 振动故障的定义振动是指物体在运动过程中产生的周期性的机械波动,而振动故障则是指汽轮发电机组在运行过程中产生的异常振动现象。
振动故障可能导致设备的损坏、性能下降甚至停机,因此需要及时诊断和处理。
2. 振动故障的诊断方法振动故障的诊断可以采用多种方法,常见的包括:(1) 振动信号的采集与分析:通过在汽轮发电机组上安装振动传感器,采集振动信号,并通过信号分析软件对振动信号进行频谱分析、波形分析等,以判断故障类型和严重程度。
(2) 振动信号的比较与参照:将汽轮发电机组的振动信号与正常工况下的参考振动信号进行比较,通过比对差异来诊断故障。
(3) 振动特征参数的提取与分析:通过对振动信号进行特征参数提取,如振动幅值、频率、相位等,进一步分析故障类型和原因。
(4) 振动信号与其他信号的关联分析:将振动信号与其他信号,如温度、压力等进行关联分析,找出振动故障的可能原因。
3. 振动故障的案例分析3.1 轴承故障案例描述:汽轮发电机组在运行中出现明显的振动,经过诊断发现是轴承故障导致的。
通过更换轴承,振动问题得到解决。
3.2 不平衡故障案例描述:汽轮发电机组在运行中出现严重的振动,经过诊断发现是转子不平衡导致的。
通过进行动平衡处理,振动问题得到解决。
3.3 轴间不对中故障案例描述:汽轮发电机组在运行中出现振动,经过诊断发现是轴间不对中导致的。
通过调整轴间对中,振动问题得到解决。
3.4 齿轮故障案例描述:汽轮发电机组在运行中出现振动,经过诊断发现是齿轮故障导致的。
通过更换齿轮,振动问题得到解决。
3.5 基础刚度不足故障案例描述:汽轮发电机组在运行中出现振动,经过诊断发现是基础刚度不足导致的。
通过增加基础刚度,振动问题得到解决。
转动设备振动状态在线监测系统案例分析

分析。振动趋势见图 4。
图 2 转炉煤气加压站 2# 机 F2Y 振动频谱对比
图 3 为 2018 年 3 月 13 日和 3 月 26 日 F2Y 测点振动时域 波形对比图,由图可见,F2Y 测点振动时域波形在一个周期内为 典型的正弦波,故障状态下的时域波形较正常运行状态下的时 域波形振幅明显增大。根据通频振动值是随着时间的推移缓慢 爬升的特点和以往的经验,判定该机组振动大是由于转子积灰 严重,造成转子不平衡故障引起,且振动值已接近报警值,同以 往停机检修前振动值相近,故及时通知相关部门,建议尽快停机 检修,转子清理并做动平衡,避免发生跳机故障。
但也面临非常大的挑战。如何有效维护机电一体化设备,是目前 故障诊断技术的重要议题。针对这一议题,给出故障诊断技术的 相关分析,并详细介绍机电一体化设备的故障特点。另外,根据 自身生产工作的实际经验,简要分析在实际设备故障诊断中需 要注意的问题,为机电一体化设备的安全生产提供理论依据。
参考文献 [1] 迟会港.机电一体化设备故障诊断及维护保养分析[J].企业技术开
场,2016(35):273. [5] 毛胜辉,戴明宏.茶叶机电一体化压缩设备的故障诊断技术分析
[J].福建茶叶,2018(5):155. 也 编辑 王永洲页
骴 髈 髗 设备管理与维修 2019 翼6(下)
图 1 转炉煤气加压站 2# 机振动趋势
图 3 转炉煤气加压站 2# 机 F2Y 时域波形对比
转动设备振动状态在线监测系统案例分析
王洪奎袁赵永江
渊 首钢京唐钢铁联合有限责任公司袁河北唐山 063200冤
摘 要:利用振动趋势尧频谱图尧时域波形图及轴心轨迹图等分析手段袁对在线监测数据进行处理和分析袁发现设备异常及时处理袁 避免非计划停机遥 关键词:振动;在线监测;故障诊断 中图分类号:TP29 文献标识码:B DOI:10.16621/ki.issn1001-0599.2019.06D.129
设备故障的振动识别方法及其实例分析

设备故障的振动识别方法及其实例分析引言在工业生产和设备运行过程中,设备故障是不可避免的问题。
而振动识别方法是一种常用的故障诊断手段,通过监测设备振动信号来判断设备的健康状态。
本文将介绍振动识别方法的基本原理,并通过实例分析来说明其在故障诊断中的应用。
振动识别方法的基本原理振动信号是指设备在运行过程中由于不平衡、机械间隙、磨损等原因产生的机械振动信号。
振动识别方法通过对振动信号进行采集、处理和分析,来判断设备的工作状态和存在的故障。
振动信号的采集振动信号的采集可以通过加速度传感器或振动传感器来实现。
这些传感器会将振动信号转化为电信号,并传送给振动分析设备进行后续处理。
振动信号的处理振动信号的处理包括滤波、特征提取和特征选择等步骤。
滤波主要是通过去除噪声和干扰信号,提取出设备故障产生的特征信号。
特征提取是指通过数学方法将振动信号转化为一组特征参数,用于描述设备的振动特性。
常用的特征参数有时间域特征(如均值、方差、峰值等)、频域特征(如功率谱密度、频率谱等)和小波变换特征等。
特征选择是指从提取的特征参数中选择出与设备故障相关性较高的特征进行分析。
常用的特征选择方法有相关性分析、方差分析和主成分分析等。
振动信号的分析振动信号的分析可以通过传统的统计分析方法和机器学习方法来实现。
传统的统计分析方法包括峰值分析、频谱分析、相关性分析等。
这些方法通过对特征参数的分析,来判断设备是否存在故障。
机器学习方法则是通过建立模型来实现振动信号的分类和识别。
常用的机器学习方法有支持向量机(SVM)、决策树、神经网络等。
这些方法可以通过训练样本集来学习设备的正常工作状态和不同故障状态的振动特征,从而实现振动信号的自动分类和识别。
振动识别方法的实例分析以下是一个通过振动识别方法进行设备故障诊断的实例分析。
假设有一台电机,在运行过程中产生了明显的振动。
我们通过加速度传感器采集了电机的振动信号,并对振动信号进行了滤波和特征提取。
汽轮发电机组振动故障诊断及案例

汽轮发电机组振动故障诊断及案例汽轮发电机组是一种常见的发电设备,其工作过程中可能出现振动故障。
振动故障会对设备的正常运行产生严重影响,因此进行振动故障的诊断和处理具有重要意义。
下面将列举一些关于汽轮发电机组振动故障诊断的案例。
1. 振动频率突然增大:在汽轮发电机组运行过程中,突然出现振动频率增大的情况。
经过检查发现,发电机组的轴承出现损坏,导致轴承摩擦不均匀,进而引起振动频率的增大。
解决方法是更换轴承并进行润滑。
2. 振动频率突然减小:在汽轮发电机组工作中,振动频率突然减小。
经过检查发现,发电机组的风扇叶片出现松动,导致不稳定振动。
解决方法是重新固定风扇叶片。
3. 振动幅值异常增大:在汽轮发电机组运行过程中,振动幅值突然增大。
经过检查发现,发电机组的基础螺栓松动,导致机组整体不稳定,振动幅值增大。
解决方法是重新紧固基础螺栓。
4. 振动频率出现谐振:在汽轮发电机组运行中,出现振动频率与机组自身固有频率相同的谐振现象。
经过检查发现,机组的结构刚度不足,导致谐振频率与机组自身频率相同。
解决方法是增加机组的结构刚度。
5. 振动频率与转速相关:在汽轮发电机组运行中,振动频率与转速呈线性关系,振动频率随转速增加而增加。
经过检查发现,机组的动平衡出现问题,导致振动频率与转速相关。
解决方法是进行机组的动平衡调整。
6. 振动频率与电流相关:在汽轮发电机组运行中,振动频率与电流呈线性关系,振动频率随电流增大而增大。
经过检查发现,机组的电机绝缘出现问题,导致电流异常,并引起振动频率的变化。
解决方法是更换电机绝缘材料。
7. 振动频率与负载相关:在汽轮发电机组运行中,振动频率与负载呈线性关系,振动频率随负载增加而增加。
经过检查发现,机组的轴向间隙不合适,导致振动频率与负载相关。
解决方法是调整轴向间隙。
8. 振动频率与温度相关:在汽轮发电机组运行中,振动频率与温度呈线性关系,振动频率随温度升高而增加。
经过检查发现,机组的冷却系统出现故障,导致温度升高并引起振动频率的变化。
振动分析案例(48个实例)

实例No.3 某汽轮机叶片断裂故障
转子不平衡 !
上海石化自备电厂5#汽轮机轴承座振动速度突增至5. 25毫米/ 秒, 有效值,而6#机仅为0. 466毫米/秒,有效值;振动速度频谱均为 一倍转速频率50赫兹。诊断为转子不平衡,据历史经验,汽轮 14 机叶片又断了!停机检查证实的确断了五片转子叶片!
故 障 诊 断 实 例 分 析 之 四
某透平膨胀机叶片断裂故障
(转子不平衡和流体动力激振故障)
罗克韦尔自动化(厦门 )有限公司 大连分公司
15
实例No.4某透平膨胀机叶轮叶片断裂故障
1989年1月27 日某透平膨胀 机振动和噪声 突增。频谱显 示1RPM和 8RPM频率 分量最大分别 达5.91和4.68 毫米/秒,有 效值,比正常 机分别大18和 25倍。诊断为 转子不平衡, 并且已断一片 叶片(出口导 叶为8片叶片, 即静子叶片通 过频率为 8 RPM)。
断了一片叶片!
19 离心叶轮14片转子叶片已断一片叶片的透平膨胀机叶轮照片
故 障 诊 断 实 例 分 析 之 五
某锅炉风机 地脚螺栓松动故障
罗克韦尔自动化(厦门 )有限公司 大连分公司
20
实例No.5某锅炉风机基础地脚螺栓松动故障
松动
3#和4#测点处地脚螺栓松动
21
故 障 诊 断 实 例 分 析 之 六
某大型风机 轴承座松动故障
罗克韦尔自动化(厦门 )有限公司 大连分公司
22
实例No.6
5#风机轴承座松动故障
3#轴承座振动3H,3V,3A
1#轴承座振动1H,1V,1A 2#轴承座振动2H,2V,2A
4#轴承座振动4H,4V,4A
汽轮机
轴流式风机
- 1、下载文档前请自行甄别文档内容的完整性,平台不提供额外的编辑、内容补充、找答案等附加服务。
- 2、"仅部分预览"的文档,不可在线预览部分如存在完整性等问题,可反馈申请退款(可完整预览的文档不适用该条件!)。
- 3、如文档侵犯您的权益,请联系客服反馈,我们会尽快为您处理(人工客服工作时间:9:00-18:30)。
设备振动故障在线检测
振动分析过程涉及到确定振动严重程度,辨别频率和特征、不同峰值和特征对应的机械和电气部件,形成分析结论,如果有必要,提供维修建议。
干这行的都知道,分析振动不是简单的,也不能自动化。
你没有想过为什么?这里有几个原因:
1) 设备有很多故障:现实中设备的振动故障模式与我们在培训和书本中学到的大不相同。
我们学到的机械和电气故障都是最纯粹的形式-好像设备总是1个故障导致振动。
设备通常会有多个故障源导致振动。
至少,所有设备都有一些不平衡和不对中。
当其它故障发展时,时间波形就会变的复杂,难以分析。
振动数据不再和我们学到的故障模式匹配。
2) 振动因果效应:对于每一个动作,都有一个反应。
我们测量的一些振动,是其它故障的影响。
例如,造成转子不平衡的力可能看起来像不对中,松动或摩擦。
当你车子的轮胎不平衡时,车子在行驶时就会振动和摇晃。
3) 很多故障有类似的振动故障模式:由于设备转子以一定的转速运动,振动是周期性的力产生的。
很多机械和电气有相似的频率特征,使得很难区分不同故障。
学习振动分析需要一定的时间。
参加培训、阅读技术资料和专业书籍、浏览在线资源、会提高振动分析技能和缩短学习曲线。
有一个诊断技术会快速的找到大多数振动故障的根源。
它可能是所有振动诊断技术中最强大的。
它随同振动分析一直存在,只是没有得到更多的关注,很难找到这方面的信息。
这个技术是什么?它就是相位分析。
什么是相位?
相位就是转动部件参考一个固定位置得到的瞬时位置信息。
相位告诉我们振动的方向。
相位研究就是收集设备和结构的相位数据和评估,揭示部件之间相对运动的信息。
振动分析中,相位分为:绝对相位和相对相位。
绝对相位使用一个传感器和光电传感器。
每个测点,振动分析仪计算光电触发点和振动波形中下一个正峰之间的时间。
时间差转换成角度,显示为绝对相位。
相位能以转轴频率或转轴谐频(同步频率)进行测量。
转子动平衡时需要绝对相位。
相对相位通过多通道振动分析仪同时使用两个或多个同样类型的传感器采集交叉通道的振动波形计算得到的。
1个传感器作为固定参考放置在设备上(通常是轴承座),另一个传感器移动到不同的测点。
在每个测点,振动分析仪比较固定传感器和移动传感器之间的时间波形。
相对相位就是特定频率时间波形的时间差,转换为角度。
相对相位不需要光电传感器,所以在任何频率测量相位。
两种相位测量方法都很简单。
相对相位是比较方便的一种方法,因为不用停机安装反光带,且可以在任何频率测量。
大多数单通道振动分析仪可以测量绝对相位,市面上大多数多通道振动分析仪包含绝对相位和相对相位两种测量功能。
什么时候使用相位分析
每个人都需要相位分析。
当设备的振动故障源不清楚或需要确定可疑的振动源时,就需要使用相位分析。
相位分析测点可能只包括设备轴承部位或包括整个设备从地基到轴承。
下面是相位如何帮助振动分析的例子。
软脚
软脚用来描述机组框架变形。
电机地脚,机泵和其它部件不平,其它问题,如加工误差,地脚弯曲或扭曲,安装平面不平等都会造成软脚。
软脚会加剧振动和对轴承、密封、联轴器施加过度应力。
软脚会造成电机定子基座变形,造成气隙不均,导致2X线频的振动。
使用激光对中仪,逐次松动设备的地脚,矫正软脚。
当设备运转时,相位用来确认软脚。
测量地脚安装平面和地脚的垂直相位。
如果连接是紧的,两者相位相同。
如果相位差超过20度,地脚是松动的或机组的框架断裂或不稳。
轴承翘曲和轴弯曲
相位可用来检测轴承翘曲和轴弯曲。
测量轴承座轴向4个位置的相位。
如果轴承是翘曲或转轴弯曲,每个方向的相位都不相同。
如果转轴是直的,轴承没有翘曲,每个方向的相位是相同的。
不平衡确认
1X转频通常以为转子不平衡,可以使用相位确认不平衡。
测量轴承座垂直方向和水平方向上的相位,如果相位差约为90度,故障
是不平衡。
如果相位差接近0度或180度,这是有反映力引起的振动。
偏心的带轮和轴不中都是反映力。
松动,弯曲或扭曲
相位可以用来检测结构松动和由刚度弱或共振造成的弯曲和扭曲。
测量每个连接点的垂直相位如图11,如果连接点松动,相位差会是180度。
连接紧的,相位不会变化。
轴不对中
使用相位可以轻松的确认转轴不对中。
对每个轴承的垂直,水平,轴向进行测量,记录相位和振动。
对各个测点的水平方向、垂直方向、轴向数据进行对比。
如果联轴器两侧测点相位接近,对中良好。
图12中,径向方向联轴器两侧测点相位差180度,轴向方向相同。
数据说明是转轴平行不对中。
工作变形模态分析
工作变形模态分析软件ODS可以用来动画处理设备结构简图。
ODS是在设备工作时分析转动部件和结构运动的一种测量技术。
ODS 是相位分析的扩展,用计算机建立设备模型,输入相位和振动幅值数据或同时测量的时间波形,进行动画处理。
动画可以直观的进行
故障诊断。
ODS测试可以确认很多机械故障和共振问题,例如松动,软脚,开焊,不对中,不平衡,共振造成的弯曲或扭曲,结构刚度弱和基础问题。
图13是1个关于3个直接耦合转子的简单ODS,相位和振幅是由固定安装在透平发电机上位移传感器测得的,包括X、Y。
ODS软件使用列表中的数据动画处理高-低压透平转子和发电机转子。
右侧ODS动画显示了设备在3600rpm时,各个转子的振动形式和转子之间的相对运动。
很多设备由于基础劣化,松动,支撑结构共振或轴承故障造成异常振动。
相位可以研究包括从设备到基础数百个测点的数据。
好的ODS软件很容易分析大量测点的相位和振动幅值数据。
ODS分析涉及设备运动的解释和描述。
结论
振动测试是以可靠性为中心的维修管理的重要组成部分。
振动传感器,振动分析仪和软件可以提供机组状态的关键信息。
这个环节薄弱部分就是振动分析师解释振动数据,诊断故障,预测剩余寿命的能力。
相位分析是一个很有用的诊断工具。
每个振动分析师都
应该使用相位以提高振动分析的准确性。