锅炉热效率测试方案
1锅炉反平衡热效率测试方案(2)
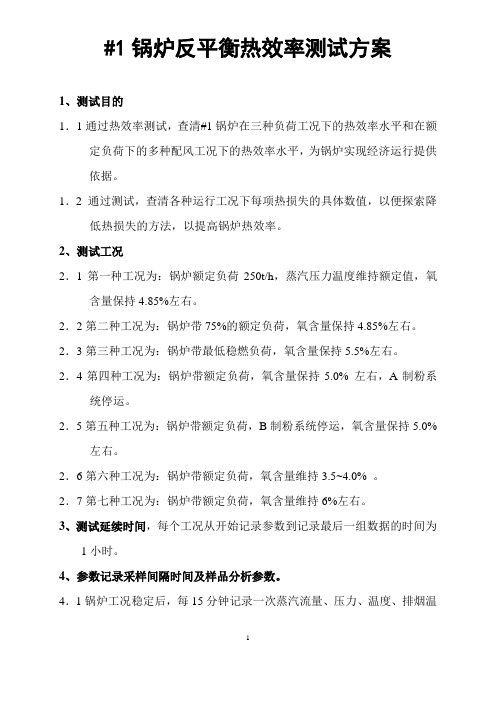
#1锅炉反平衡热效率测试方案1、测试目的1.1通过热效率测试,查清#1锅炉在三种负荷工况下的热效率水平和在额定负荷下的多种配风工况下的热效率水平,为锅炉实现经济运行提供依据。
1.2 通过测试,查清各种运行工况下每项热损失的具体数值,以便探索降低热损失的方法,以提高锅炉热效率。
2、测试工况2.1第一种工况为:锅炉额定负荷250t/h,蒸汽压力温度维持额定值,氧含量保持4.85%左右。
2.2第二种工况为:锅炉带75%的额定负荷,氧含量保持4.85%左右。
2.3第三种工况为:锅炉带最低稳燃负荷,氧含量保持5.5%左右。
2.4第四种工况为:锅炉带额定负荷,氧含量保持5.0% 左右,A制粉系统停运。
2.5第五种工况为:锅炉带额定负荷,B制粉系统停运,氧含量保持5.0%左右。
2.6第六种工况为:锅炉带额定负荷,氧含量维持3.5~4.0% 。
2.7第七种工况为:锅炉带额定负荷,氧含量维持6%左右。
3、测试延续时间,每个工况从开始记录参数到记录最后一组数据的时间为1小时。
4、参数记录采样间隔时间及样品分析参数。
4.1锅炉工况稳定后,每15分钟记录一次蒸汽流量、压力、温度、排烟温度、烟气氧含量等主要参数,其它次要参数每30分钟记录一次。
4.2 烟气取样(分析),每20分钟一次。
并分析含O2、CO、CO2量及烟气中的含灰量。
4.3 煤粉取样,每个试验工况二次。
分析低位发热值和各元素含量。
4.4 飞灰取样,每个试验工况二次。
分析飞灰中的可燃物(含碳量)。
4.5 灰渣取样,要求在整个试验工况期间连续或等时间间隔进行,以保证样品的代表性。
分析炉渣含碳量。
5、测试前的准备工作5.1人员组织与分工。
安排好锅炉运行工况调整人员,记录参数人员、取样人员、化验人员以及每组人员的技术负责人、测试总负责人。
5.2 对每组人员进行测试的过程讲解,使每个人熟悉在何时完成哪种工作,怎么完成。
5.3 各组人员分别准备所需工具、量具、记录表格、分析仪器、取样容器、化验药品等,并完成仪器仪表所需的校验工作。
燃煤工业锅炉热效率测试方案

目录1 试验目的 (1)2 试验依据 (1)3 试验工况 (1)4 测试内容和方法 (1)5 测试所需仪器 (2)6 试验条件及要求 (3)7 试验组织与分工 (3)8 安全注意事项 (3)※※※※※※公司工业锅炉热效率测定试验方案1 试验目的本次试验为运行试验,目的是确认锅炉热效率是否符合《燃煤锅炉能效限定值及能效等级》的要求。
2 试验依据2.1 GB/T 10184-1988《电站锅炉性能试验规程》2.2 DL/T 964-2005《循环流化床锅炉性能试验规程》2.3 TSG G0002-2010《锅炉节能技术监督管理规程》3 试验工况3.1 锅炉在额定负荷下的热效率;3.2 锅炉在70%负荷下的热效率。
4 测试内容和方法4.1 排烟处烟气成份测量(O2、CO2、CO)、排烟温度、压力在出口烟道开1个测量孔,测量3个测点,采用烟气分析仪测量。
4.2环境温度、空气湿度及大气压用干、湿球温度计测量环境温度及空气湿度,用大气压力表测取大气压,试验时每15分钟测量记录一次,取平均值。
4.3 锅炉外壁温度红外线测温仪4.4 燃料特性分析燃料的元素分析、工业分析、发热量、含水量由热工性能实验室测试。
4.5 燃料的消耗量、灰渣量就地表计和或磅称计量。
4.6 给水温度、给水压力就地表计读数。
4.7 给水流量就是表计读数。
4.8 饱和蒸气压力、温度,过热蒸汽压力、温度就地仪表读数。
4.9 饱和蒸气湿度蒸汽含盐量和锅水含盐量。
4.10 炉水、给水、蒸汽取样每隔30分钟取样一次并分析其品质。
4.11 燃料、炉渣、飞灰取样每隔30分锅炉取样一次,每次不少于1公斤。
5 测试所需仪器下表给出了试验所需的主要仪器设备。
试验所需的仪器、设备清单6 试验条件及要求6.1若锅炉达不到试验要求,则由试验时再确定运行方式,可根据现场实际情况调整,由试验人员和厂家共同商定。
6.2试验期间燃用设计燃料或事先商定的燃料。
6.3试验期间应尽量保持锅炉各参数的稳定,锅炉主要附属设备处于良好状态,无严重漏风、烟气和蒸汽现象,试验前锅炉受热面进行吹扫冲洗。
锅炉的热效率的测定

单位时间内锅炉有效利用热量占锅炉输入热量的百分比,或相应于每千克燃料(固体和液体燃料),或每标准立方米(气体燃料)所对应的输入热量中有效利用热量所占百分比为锅炉热效率,是锅炉的重要技术经济指标,它表明锅炉设备的完善程度和运行管理水平。
锅炉的热效率的测定和计算通常有以下两种方法:1.正平衡法用被锅炉利用的热量与燃料所能放出的全部热量之比来计算热效率的方法叫正平衡法,又叫直接测量法。
正平衡热效率的计算公式可用下式表示:热效率=有效利用热量/燃料所能放出的全部热量*100%=锅炉蒸发量*(蒸汽焓-给水焓)/燃料消耗量*燃料低位发热量*100%式中锅炉蒸发量——实际测定,kg/h;蒸汽焓——由表焓熵图查得,kJ/kg;给水焓——由焓熵图查得,kJ/kg;燃料消耗量——实际测出,kg/h;燃料低位发热量——实际测出,kJ/kg。
上述热效率公式没有考虑蒸汽湿度、排污量及耗汽量的影响,适用于小型蒸汽锅炉热效率的粗略计算。
从上述热效率计算公式可以看出,正平衡试验只能求出锅炉的热效率,而不能得出各项热损失。
因此,通过正平衡试验只能了解锅炉的蒸发量大小和热效率的高低,不能找出原因,无法提出改进的措施。
2.反平衡法通过测定和计算锅炉各项热量损失,以求得热效率的方法叫反平衡法,又叫间接测量法。
此法有利于对锅炉进行全面的分析,找出影响热效率的各种因素,提出提高热效率的途径。
反平衡热效率可用下列公式计算。
热效率=100%-各项热损失的百分比之和=100%-q2-q3-q4-q5-q6式中q2——排烟热损失,%;q3——气体未完全燃烧热损失,%;q4——固体未完全燃烧热损失,%;q5——散热损失,%;q6——灰渣物理热损失,%。
大多时候采用反平衡计算,找出影响热效率的主因,予以解决。
锅炉性能试验方案

#2炉性能试验方案编制:校核:审查:批准:1前言为获取SCR烟气脱硝改造、空预器改造和引风机改造设计所需的锅炉运行参数及相应设备性能,xxxxxx电厂特委托XXX研究院有限公司进行#2炉的锅炉热效率、空预器性能、省煤器出口烟气参数、引风机进/出烟气参数、FGD增压风机进/出口烟气压力、烟囱进口烟气压力等项性能测试。
本方案是各项热力项目测试的指导性文件,制定了试验的方法及为确保测试精度所应采取的测试手段。
2测试依据➢《电站锅炉性能试验规程》(GB 10184-1988);➢《入炉煤样品的采取方法》(DL/T 567.2-1995);➢《飞灰和炉渣样品的采集》(DL/T 567.3-1995);➢《入炉煤、飞灰和炉渣样品的制备》(DL/T 567.4-1995);➢《飞灰和炉渣可燃物测定方法》(DL/T 567.5-1995);➢《锅炉机组性能试验规程》(ASME PTC4.1);➢《电站锅炉风机现场试验规程》(DL469-2004 B类试验);➢《电除尘器性能测试方法》(GB/T13931-2002);➢《固定污染源排气中颗粒物测定与气态污染物采样方法》(GB/T16157-1996);➢技术协议及有关联络会议纪要。
3测试内容及方法3.1 测试内容(1)100%、80%、70%负荷工况下锅炉热效率试验;(2)100%、80%、70%负荷工况下空预器性能试验;(3)100%、80%、70%负荷工况下电除尘器性能试验;(4)100%负荷工况下省煤器出口烟气参数测试(流量、温度、成份、负压等);(5)100%负荷工况下引风机进口烟气参数测试(流量、负压、烟温);(6)100%负荷工况下引风机出口烟气压力测试;(7)100%负荷工况下增压风机进/出口烟气压力测试;(8)100%负荷工况下烟囱进口烟气压力测试;(9)入炉煤工业分析、元素分析、发热量分析及可磨性指数分析;(10)锅炉入炉煤灰成份分析。
3.2 测量项目及方法3.2.1 锅炉反平衡炉效、空预器漏风3.2.1.1 排烟温度测量测量方法:排烟温度的测量按等截面网格法布置热电偶。
蒸汽锅炉的燃烧效率测试及其方法

蒸汽锅炉的燃烧效率测试及其方法蒸汽锅炉燃烧效率测试及其方法蒸汽锅炉是一个重要的热力设备,广泛应用于化工、电力、纺织、印染、食品等众多领域。
为确保蒸汽锅炉正常运行,提高其生产效率、降低能源消耗,进行燃烧效率测试是必不可少的环节。
一、什么是蒸汽锅炉燃烧效率?蒸汽锅炉燃烧效率是指燃料在燃烧过程中转化为蒸汽所使用的热量与燃料自身所含热量之比,也可以说是蒸汽锅炉燃料的利用效率。
燃烧效率的高低直接影响到蒸汽锅炉的经济性、安全性、环保性等多个方面。
二、蒸汽锅炉燃烧效率测试方法常用的蒸汽锅炉燃烧效率测试方法主要包括总量法、热损失法和公称比热法。
1. 总量法总量法(全量测试法)是指在同一燃料负荷条件下监测燃气、燃油或燃煤的进口和排出口的温度、压力、流量等参数,通过对燃料的化学分析和排出口烟气中的气体含量分析等来确定锅炉热效率。
这种方法的最大特点就是它能够测量锅炉的全部热损失。
2. 热损失法热损失法是指通过测量蒸汽锅炉进口和排出口的温度、压力等参数,计算蒸汽锅炉的热损失,从而得出燃烧效率。
这种方法广泛应用于小型锅炉的测试,计算方法简单,但精度比总量法稍低。
3. 公称比热法公称比热法是基于烟气温度的变化来计算燃烧效率的。
该方法不需要测量烟气中气体成分,通过测量进口和排出口的烟气温度,计算出烟气平均温度,进而计算锅炉主要热损失的比例,得到燃烧效率。
此方法的优点在于节约成本,效率高。
三、燃烧效率测试过程燃烧效率测试需要在负荷稳定、锅炉正常运行条件下进行。
测试前需要准备好测试仪器,按要求连接好检测仪器、烟气通道等。
测试过程中应注意及时记录各项数据,并进行数据处理和统计分析。
一般来说,燃烧效率测试需要进行多次才能得出可靠的结果。
四、如何提高蒸汽锅炉燃烧效率提高蒸汽锅炉的燃烧效率可以从以下几个方面进行:1. 选用优质的燃料选用优质的煤、燃油或天然气等燃料,是提高燃烧效率的重要途径之一。
2. 进行经常性的维护经常性的维护可以确保蒸汽锅炉处于最佳工作状态,降低热损失,提高燃烧效率。
锅炉测试方案(1)

锅炉测试方案一、测试目的:为了了解锅炉在运行中的能量利用程度及能量使用方面进行测试,制定针对性的措施,以提高锅炉运行效率,充分对燃料进行利用,提高锅炉运行经济性。
二、测试原理:测试原理采用能量平衡原理,即输入能量=输出能量,公式为Qr=Q1+Q2+Q3+Q4+Q5+Q6,式中Qr-输入能量,Q1-有效能量,Q2-排烟热损失,Q3-气体未完全燃烧损失,Q4-机械未完成燃烧损失,Q5-散热损失,Q6-灰渣物理热损失。
通过正反平衡测试对锅炉效率及各部分的损失有更深一步的认识,及η1=Q1/Qr,或η1=1-(η2+η3+η4+η5+η6)。
当正反平衡测试结果之差小于5%时,测试结果采用正反平衡结果的平均值,即η=(η1+η1)/2。
三、测试仪器:烟气分析仪、红外测温仪、超声波流量计、皮尺、磅秤、大气压力表、环境温度计。
四、测试标准:《工业锅炉热工性能试验规程》 (GB/T 10180-2003)、《工业锅炉能效测试与评价规则》 (TSG G0003-2010)、《燃煤工业锅炉节能监测》(GBT 15317-2009)五、注意事项:1、锅炉负荷稳定且在正常范围内运行70%左右;2、实验期间协调企业工作人员不要开启排污;3、在实验期间对每次入炉煤及排出的炉渣及飞灰进行取样;4、每10-15min记录一组参数。
六、测试项目:序号测试及采集项目数据来源1耗煤量现场煤斗车称量数据;并根据之前其测试报告预估效率为80%左右,以炉渣及灰渣质量核实实际的耗煤量。
2煤的发热值测试期间取样化验,企业提供化验数据作参考3煤的灰含量测试期间取样化验,企业提供化验数据作参考4蒸汽/给水流量同企业协调,在测试过程中不排污,用超声波流量计测试锅炉给水流量近似等于蒸汽流量5蒸汽/给水温度测温仪测试 并与其表计读数对比,若差距不大,可用其读数6蒸汽/给水压力根据现场给泵出口压力,汽包压力,蒸汽压力相互核实;若读数明显有误,则可根据给泵、锅炉名牌进行大致的估算7炉渣/飞灰质量现场称量8炉渣/飞灰温度在炉渣及飞灰排出口测温仪直接测试9排烟温度及烟气成分空预器出口尾部烟道(1m左右)进行测试,待排烟温度温度稳定后才可读数10入炉冷空气温度送风机房六、测试项目11炉体表面温度距门(孔)300mm以外的温度不超过50℃,炉顶温度不超过70℃(每平米布置一个测点)七、现场测试计算表格制定针对性的措施,以提高锅炉运行效率,+Q2+Q3+Q4+Q5+Q6,式中Qr-输入能量,Q1-5-散热损失,Q6-灰渣物理热损失。
锅炉热效率测试方案
锅炉热效率测试方案为了解毛铺酒厂锅炉运行热效率和为确定下步锅炉改造方向,根据《锅炉节能技术监督管理规程》和按照《工业锅炉能效测试与评价规则》对毛铺酒厂3台锅炉进行能效测试。
一、测试方法锅炉运行工况热效率简单测试采用反平衡法,相关测量要求按照GB/T 10180要求的方法进行测量。
二、测试要求1.热效率测试应当不少于2次;2.两次反平衡测试测得的效率之差均应当不大于2%。
三、测试条件1.锅炉在额定参数下处于安全、热工况稳定的运行状态;2.辅机与锅炉出力相匹配并运行正常,系统不存在跑、冒、滴现象;3.测试所用燃料符合设计燃料的要求;4.锅炉及辅机系统各测点布置满足测试大纲要求。
四、测试项目1.排烟温度t py,℃;2.排烟处过量空气系数;3.排烟处CO含量,%(ppm);4.入炉冷空气温度t lk,℃;5.飞灰可燃物含量C fh,%;6.漏煤可燃物含量C lm,%;7.炉渣可燃物含量C lz,%;8.燃料收到基低位发热量Q net.v.ar,kJ/kg;收到基灰分A ar,%;9.测试开始和结束的时间。
五、正式测试时间1、锅炉正常燃烧1小时后开始测试;2、测试时间内至少包括一个完整的燃料添加和出渣周期(分厂应先将煤斗填平正常燃烧后添加燃煤时必须填平并计量);3、烟气测量次数不少于5次,每次间隔时间均匀,测试开始、结束各一次(对于排烟温度、排烟处过量空气系数、排烟处CO 含量按测量数据算术平均值作为计算值)。
六、测试项目1. 排烟热损失(q 2)2. 气体未完全燃烧热损失(q 3)3. 固体未完全燃烧热损失(q 4)4. 散热损失(q 5)5. 灰渣物理热损失(q 6)6. 热效率;()65432j 100q q q q q ++++-=η七、测试报告1. 锅炉能效测试综合报告2. 锅炉能效测试项目3. 锅炉能效测试测点布置及测试仪表说明4. 能效测试结果汇总表八、测试小组成员及分工名称人员 职责综合分析组 生产技术科设备组2、 对测试细节进行全面监督;3、 对测试数据进行统计分析,并出具相关报告;4、 对照国家相关规定,寻找不合格项目,并制定锅炉下步改造计划。
锅炉效率检测报告 cma
锅炉效率检测报告一、引言锅炉是工业生产中常用的热能转换装置,其效率直接关系到能源的利用率和环境保护。
因此,对锅炉的效率进行检测和评估显得十分重要。
本报告旨在通过对锅炉效率的检测,分析锅炉的热能转换效率以及存在的问题,并提出相应的改进措施,以提高锅炉的能源利用效率。
二、方法与实验2.1 实验目的本次实验旨在通过测量锅炉的各项参数,计算出锅炉的热效率,并对结果进行分析和评价。
2.2 实验步骤1.准备工作:收集锅炉相关信息,包括锅炉型号、出力、燃料种类等;2.测量锅炉输入能量:通过测量燃料的质量和燃烧热值,计算锅炉输入的能量;3.测量锅炉输出能量:测量锅炉的蒸汽输出量,计算锅炉输出的能量;4.计算锅炉热效率:根据测量结果和公式,计算锅炉的热效率;5.分析和评价:根据计算结果,对锅炉的热效率进行分析和评价,并提出改进措施。
2.3 实验结果实验结果如下表所示:锅炉型号锅炉出力(吨/小时)燃料种类燃料质量(吨)燃烧热值(MJ/吨)蒸汽输出量(吨/小时)热效率ABC-123 10 煤 2 28 9 80%三、分析与讨论3.1 锅炉热效率分析根据实验结果计算得出,ABC-123型号的锅炉热效率为80%。
热效率是指锅炉转换输入能量为有用输出能量的比例,其数值越高表示能源利用效率越高。
3.2 热效率评价根据锅炉热效率的评价标准,80%的热效率处于较高水平。
但仍存在改进的空间,下面是对该锅炉热效率的评价:1.优点:热效率高,能源利用效率较好,符合能源节约和环保要求。
2.不足之处:仍存在一定的能源浪费问题,需要进一步提高热效率。
3.3 提高热效率的改进措施为了进一步提高锅炉的热效率,可以采取以下改进措施:1.锅炉优化设计:优化锅炉的燃烧系统、换热系统和控制系统,提高能源转换效率。
2.燃料选择:选择更高热值的燃料,提供更多的燃料能量输入。
3.废热利用:合理利用锅炉排出的废热,如余热回收、余热发电等方式,提高能源利用效率。
锅炉热效率实验方法
目录1.概述...................................... 错误!未定义书签。
2.应用范围.................................. 错误!未定义书签。
3.引用标准、规程、标准...................... 错误!未定义书签。
4.测试项目及方式............................ 错误!未定义书签。
5.利用仪器、仪表............................ 错误!未定义书签。
6.实验应具有的条件.......................... 错误!未定义书签。
7.测点清单及测点布置........................ 错误!未定义书签。
8.危险点分析及操纵方法...................... 错误!未定义书签。
9. 平安防护方法............................ 1错误!未定义书签。
10.组织分工............................... 1错误!未定义书签。
1.概述实验目的本次实验的目的在于了解国投大同能源有限责任公司#1、2锅炉的运行状况,查明锅炉机组的平安经济运行指标,特进行大修前锅炉热效率实验。
设备简述国投大同能源有限责任公司2×480t/h锅炉是采纳哈尔滨锅炉厂有限责任公司设计制造的HG-480/.7L型循环流化床锅炉,采纳单汽包、自然循环、高温超高压一次中间再热、高温绝热旋风分离器、单炉膛平稳通风、前墙给料、固态冷却排渣。
锅炉均由以下三部份组成:第一部份为锅筒、炉膛及冷渣机。
炉膛采纳全膜式水冷壁结构,炉膛前上部沿宽度方向别离布置有3片水冷屏(蒸发受热面)、8片屏式过热器(二级过热器)和6片屏式再热器(热段再热器)。
炉膛底部是水冷壁管弯制而成的水冷风室。
风室底部的点火风道内布置有2台床下点火燃烧器,炉膛下部密相区布置有6支床上启动燃烧器,用于锅炉启动点火和低负荷稳燃。
供热锅炉燃烧效率测试方法研究
供热锅炉燃烧效率测试方法研究1、引言供热锅炉是在冬季供热系统中不可或缺的设备,为了确保供热的效果,锅炉的燃烧效率必须得到保证。
煤火锅炉主要依靠燃料固体的燃烧产生热量,如何提高燃烧效率,不仅关乎到热能的利用率,也关系到能源的节约和环境的保护。
因此,研究供热锅炉燃烧效率测试方法,对于推广高效环保的供热技术,促进节能减排具有重要意义。
2、燃烧效率的定义与计算方法燃烧效率是指燃料输入锅炉内的热量和能够转化为实际输出热量的比例。
假设热值为Q1,燃料输入锅炉的热量为Q2,锅炉实际输出的热量为Q3,则燃烧效率η为:η=(Q3/Q2) × 100%=Q3/Q1 × 100%其中Q1为单位燃料产生的热值。
计算燃烧效率需要准确测量Q1、Q2和Q3,这需要选用合适的测试方法。
3、燃烧效率测试方法目前燃烧效率测试方法主要分为直接法、间接法和流量法三种。
(1)直接法直接法是通过直接测量燃料和空气的质量或体积来计算燃烧效率。
直接法测试的精度高,可反映出燃烧过程中燃料和氧气以适当的比例混合的情况,是目前公认的最精确的测试方法之一。
直接法有实验室法和现场法,实验室法包括平衡燃爆法、制气燃爆法、氧代燃烧法等,现场法则采用烟气分析仪等设备直接测量燃烧效率。
(2)间接法间接法是通过测量锅炉内烟气或水蒸气中氧气、CO、CO2等成分浓度,并考虑胶质热损失计算燃烧效率。
间接法设备简单、测试过程便捷,但精度不如直接法高,由于测量时依赖烟气中氧气、CO、CO2等成分浓度的测量准确性,所以必须严格控制实验条件以保证测试结果的可靠性。
(3)流量法流量法是通过热量平衡计算法来计算燃料的输入热量和输出热量,再据此计算燃烧效率。
流量法又可分为平衡法和计量法,平衡法需要对水、气体和燃料进行流量测量,计算输入热量;计量法仅需通过测量热载体的供水和回水温度、流量计算输出热量和热损失,并依此计算燃烧效率。
4、燃烧效率测试方法的情况讨论以上三种测试方法各有优劣,选择何种测试方法应根据测试目的、测试条件以及测试人员技术水平等因素来综合考虑。
- 1、下载文档前请自行甄别文档内容的完整性,平台不提供额外的编辑、内容补充、找答案等附加服务。
- 2、"仅部分预览"的文档,不可在线预览部分如存在完整性等问题,可反馈申请退款(可完整预览的文档不适用该条件!)。
- 3、如文档侵犯您的权益,请联系客服反馈,我们会尽快为您处理(人工客服工作时间:9:00-18:30)。
链条燃煤锅炉热效率测试方案项目名称:水管链条锅炉能效测试测试方法:锅炉运行工况热效率简单测试(反平衡法)锅炉型号: SZL10-1.25-W.A 委托单位:郴州钻石钨制品有限责任公司测试地点:郴州钻石钨制品有限责任公司湖南欧吉能源科技有限公司年月日目录一、项目概述......................................第 1 页1.1 背景......................................第 1 页1.2 锅炉设备..................................第 1 页二、测试目的......................................第 2 页三、测试原理......................................第 2 页3.1 基本原理..................................第 2 页 3.2 计算方式..................................第 3 页3.3 热量计算..................................第 4 页四、测试方法......................................第 6 页五、测试项目......................................第 7 页六、测试点布置及仪表说明..........................第 8 页6.1 测点布置..................................第 8页6.2 测试仪表..................................第 9 页七、测试费用预算..................................第 9 页八、附录一:费用预算..............................第 10页附录二:锅炉检测数据和计算结果综合表..........第 11页1. 项目概述1.1 背景郴州钻石钨制品有限责任公司是目前世界上知名的钨制品企业之一,钨制品生产线项目设计产能为年产仲钨酸铵10000吨,于2003年7月1日试生产,主要产品为偏钨酸铵、蓝钨、黄钨和仲钨酸铵。
公司采用2台燃煤链条炉产生蒸汽,产生的蒸汽主要用于压煮车间,由于在生产过程中锅炉虽一直处于满负荷运行状态,但未能输出额定的蒸汽压力,因此,很有必要对锅炉进行一次热效率测试,为改进锅炉运行工况做参考。
1.2 锅炉设备郴州钻石钨制品有限责任公司所用的2台燃煤锅炉均产自湘潭锅炉厂,两台锅炉均24小时满负荷运行,总的燃煤消耗量为60~70吨/天,实际出力效率在60%左右。
2台燃煤链条炉的主要参数如表1表1 燃煤链条炉的参数锅炉型号蒸发量(t/h) 蒸汽压力(MPa)蒸汽温度(℃)燃煤消耗量(kg/h)1# DZL6-1.25-AII 6 1.25 194 11062# SZL10-1.25-W.A 10 1.25 194 1839 两台锅炉给煤装置采用传统的煤斗加煤法,煤块混杂挤压,形成密实煤层,通风阻力大,燃煤层表面板结,炉排易烧损,块大的煤不易烧尽,颗粒状的煤粉易掉漏,炉渣含碳量不稳定,锅炉的整体热效率不理想入炉煤力度相差较大,煤层厚度不均匀,经常出现燃料煤燃烧不完全、炉渣残碳含量较高及炉膛温度偏低等现象。
2. 测试目的(1)了解和熟悉锅炉运行时热量的收、支平衡关系,即锅炉热平衡的组成。
(2)测定锅炉的各项热损失,并分析研究减少热损失的途径,确定锅炉的热效率。
(3)针对锅炉的运行状况,制定出解决方案,不断降低热损失,减少燃料消耗,提高锅炉热效率。
3. 测试原理3.1基本原理锅炉工作是将燃料释放的热量最大限度的传递给汽水工质,剩余的没有被利用的热量以各种不同的方式损失掉了。
锅炉热效率测定实验的基本原理就是锅炉在稳定工况下进出热量的平衡。
根据锅炉热平衡概念,可画出锅炉热平衡图如图1所示。
rQ6Q5Q 4Q 3Q 2Q图1 锅炉热平衡图输入锅炉热量=锅炉利用热量+各种热损失 图中(1)r Q (kJ/kg):锅炉输入热量; (2)2Q (kJ/kg):排烟热损失;(3)3Q (kJ/kg):化学未完全燃烧热损失;(4)4Q (kJ/kg):机械未完全燃烧热损失,链条炉包括:炉渣机械未完全燃烧热损失4lz Q ,飞灰机械未完全燃烧热损失4fh Q 与漏煤机械未完全燃烧热损失4lm Q 三项;(5)5Q (kJ/kg):锅炉向环境散热热损失; (6)6Q (kJ/kg):灰渣物理热损失等其他热损失。
3.2计算方式锅炉热效率为锅炉利用热量1Q 占输入热量r Q 的百分数,用gl η(%)表示。
它可由输入-输出热量法或热损失法通过实验求得。
(1)输入-输出热量法:1100gl rQ Q η=⨯% (2)热损失法:gl η=100-(2q +3q +4q +5q +6q ) %3.3热量计算 (1) 输入热量r Qr Q = Q net ,ad + rx Q (1) 式中 Q net ,ad ――燃料收到基低位发热量, kJ/kgrx Q ――燃料物理显热, kJ/kg本实验中,实验室的基准温度取环境温度,输入热量只计燃料收到基低位发热量Q net ,ad 。
(2) 锅炉有效利用热量gl Q热水锅炉每小时有效吸热量gl Q 按下式计算:'''3()10gl rs rs Q G i i =-⨯ kJ/h (2)式中 G ――热水锅炉每小时加热水量, kg/h ;'rs i ,''rs i ――热水锅炉进水及出水的焓,kJ/kg 。
(3) 机械未完全燃烧热损失4Q链条炉44444lz fh cjh lm Q Q Q Q Q =+++ kJ/kg (3)44100rQ q Q =⨯ % 式中4lz Q ――炉渣机械未完全燃烧热损失, kJ/kg ; 4fh Q ――飞灰机械未完全燃烧热损失, kJ/kg ;4cjhQ ――沉降灰机械未完全燃烧热损失, kJ/kg ; 4lmQ ――炉排漏煤机械未完全燃烧热损失,kJ/kg 。
本实验中,只计炉渣机械未完全燃烧热损失4lz Q 和飞灰机械未完全燃烧热损失4fh Q ,其计算公式为:clz clzlzylz C C a A Q -=10027.3274kJ/kg ; (4) c fhc fh fhy fh C C a A Q -=10027.3274 kJ/kg 。
(5)式中 clz C 、c fh C ――分别为炉渣和飞灰中可燃物含量百分数,%;lz a 、fh a ――分别为炉渣、飞灰量占入炉煤总灰量的质量份额。
(4) 排烟热损失2Q排烟热损失按下式计算: 042[()](1)100py py k lk q Q I a V ct =-- kJ/kg ;(6) 22100%rQ q Q =⨯ 式中py I ――排烟的焓,kJ/kg ,由烟气离开锅炉最后一个受热面处的烟气温度py ϑ和该处的过量空气系数py a 所决定, py ϑ值在热平衡实验中测定;py a ――排烟处的过量空气系数,热平衡实验时,py a 值可由烟气分析测定气体成分,然后计算求得;0k V ——每kg 燃料完全燃烧时所需的理论空气量,m 3; ()lk ct ——每3Nm 干空气连同其带入的10g 水蒸气在温度为t ℃时的焓;由于固体不完全燃烧热损失的存在,对1kg 燃料所生成的烟气容积需乘以4(1)100q -的修正值。
通常排烟热损失是锅炉热损失中较大的一项,一般装有省煤器的水管锅炉,2q 约为%12~%6;不装省煤器时,往往高达20%以上。
(5) 化学未完全燃烧热损失3Q4342(126.36358.18107.98590.79)(1)100gy m n q Q V CO CH H C H =+++-(7) 33100%rQ q Q =⨯式中:gy V ――取样点处干烟气容积,如下式:20.3751.866y ygy C S V RO CO+=+ 3/Nm kg (8)y C 、y S ――燃料收到基成分质量含量百分数,%;CO 、4CH 、2H 、m n C H ――取样点处干烟气中可燃气体CO 、4CH 、2H 、m n C H 的容积百分比,%。
燃煤锅炉可认为 420,0,0m n CH H C H ===。
(6) 散热损失参照国家标准,根据锅炉实际情况估算。
(7) 灰渣物理热损失6Q 6()100ar lz lzr lzA a ct Q Q C =- kJ/kg (9)66100%rQ q Q =⨯ 式中:lz t ——灰渣离开炉膛时的温度,当不直接测量时,链条炉lz t =600℃;lz c ——为炉渣可燃物含量,/kJ (⋅kg ℃) 它们由下式计算40.71 5.0210lz lz c t -=+⨯ /kJ (⋅kg ℃) (10)本实验中,只计算灰渣造成的热物理损失。
4. 测试方法本测试采用反平衡法(热损失法),反平衡试验法是测定出锅炉的各项热损失,而计算确定其热效率。
可以从各项热损失的分析中找出减少热损失方式,合理利用能源、提高锅炉热效率的途径。
5. 测试项目(1)燃料(煤)的取样和检测,包括收到基低位发热量Q net.ad,MJ/kg,收到基灰分A ar,%等特性;(2)主蒸汽的压力(P)、温度(t gq)和锅炉出力(D);(3)给水温度t gs ,℃;(4) 炉渣可燃物含量C lz,%;(5) 飞灰可燃物含量C fh,%;(6)漏煤可燃物含量C lm,%;(7)排烟处RO2、O2、CO含量,%;(8)入炉冷空气温度t lk,℃;(9)排烟温度θpy,℃。
6. 测试点布置及测试仪表说明6.1 测点布置6.2 测试仪表7.测试费用预算本次热工测试预算的费用为()万元,详见附录一。
预算主要包括以下项目:检测费、仪器仪表费、人工费、差旅费和不可预见费等。
费用预算锅炉检测数据和计算结果综合表锅炉型号:测试日期:。