氯化钾镀锌由原材料引起的故障三例
氯化钾镀锌镀层出现黑斑点原因及排除

氯化钾镀锌镀层出现黑斑点原因及排除
1、前处理不良:加强镀前处理后再进行试验,观察故障现象是否消失。
若仍未排除故障,则再检查其他原因。
2、镀液中氯化物含量太低,而电流密度过高:取250ml镀液,采用逐渐提高氯化钾(钠)含量进行霍尔槽试验。
若随着氯化物含量的提高,霍尔槽阴极试片上的黑色条纹逐渐向高电流密度端移动并逐渐消失,则表明原镀液中氯化物含量偏低,应根据试验结果补加氯化钾(钠)。
若电流密度过高,则应适当减小阴极电流密度。
3、镀液中有机杂质含量过多:取500ml镀液,加入3g/L左右活性炭,强烈搅拌30min,静置8h后过滤镀液。
将处理前、后的镀液进行霍尔槽试验,若经过处理的镀液,霍尔槽阴极试片镀层比未处理的有明显改善,则说明镀液中有机杂质过多,应根据试验结果确定活性炭的加入量,向镀液中加入活性炭处理,并过滤镀液。
氯化钾镀锌常见故障分析

涂 料 涂 装 与 电 镀
维普资讯
47
氯化 钾镀 锌 常 见 故 障分 析
田永 良 (成都 飞机 工业集 团公 司热表分厂 ,四川成都 ,610092)
摘 要 本 文依据 实践经验对氯化钾镀锌的一些 常见故 障进行 了分析 ,并提 出了纠正措施 。 关键词 镀锌 ;故障分析 ;实用技 术
3 常见故障分析
产 生 原 因 ①温度过高 ② 光 亮 剂 不 足 ③pH值 过高 ④ 过高 ,钾盐少 ⑤硼酸不足 ⑥ 重金 属离 子杂 质影 响
纠 正 方 法 ①降低温度 ② 补 充 光 亮 剂 ③调整 pH值至工艺范 围 ④调整溶液成分 ⑤补充硼酸 ⑥用 2g/L锌粉处理溶液
1 前 言
氯化钾镀锌 ,不含络合 物,废水处理简单 ,镀 液 稳定、维护简单 ,电流效率高达 95%以上 ,可允许较 大电流密度。适 宜各种铸铁、高碳钢 和热处理零 件 的电镀 。但分散 能力不够好 ,亮度 比氯化铵镀锌 略 逊一些 ,钝化膜结合强度较差 ,镀层性脆。通过选用
3.1 故 障现 象 :漏镀
这项环保工程和电镀废水零排放技术 ,受到了
有污水排放 ,仍对环境有污染 。换言之,达标排放只 全 国 电镀 界 的好评 ,也 受 到 了广 州 市 电镀 协 会 和 香
能减轻环境污染 ,却不能消除环境污染 。达标排放 港电镀商会专家们的高度赞赏。广东省环保局、广
一 年多的运行实践表明 ,在满负荷运行时,扣除
加剧 了水 资 源 的短 缺 。
运行费用后 尚能盈利 30余万元。实现了经济效益 、
(2)电镀 废 水达 标 排放 ,只表 明废水 中的各 种 污 社 会效 益和 环境 效益 较为完 美 的统一 。
常见13种氯化钾镀锌 故障分析告诉你答案

常见13种氯化钾镀锌故障分析告诉你答案本篇汇总了氯化钾镀锌的常见故障,包括镀层不光亮、发雾、结合力差、烧焦、黑色条纹、厚度不均、脆性、沉积速度慢、分散能力差、镀液浑浊等。
介绍了这些疵病的产生原因及其处理方法。
提出了应加强工艺管理、认真做好镀液维护、定期进行净化等措施,以期避免或减少故障发生。
氯化钾镀锌是由最早的无氰氯化铵镀液发展而来的一种无铵弱酸性光亮镀锌工艺。
其优点是:(1)镀液导电性好,槽压低,节省电能;(2)镀层结晶细致、光亮、平整;(3)电流效率高,沉积速度快;(4)镀液分散能力好;(5)适用于铸件直接电镀;(6)废水处理简便,解决了环境污染的问题。
因此,氯化钾镀锌在工业上得到了广泛应用。
但是,在日常生产中难免会发生质量故障,主要原因在于镀液维护不力,组分失调或受到有害杂质干扰,以及工件前处理不良。
本篇拟就氯化钾镀锌中常见故障的产生原因及其处理方法进行汇总和介绍。
各种常见故障的产生原因及其处理方法1.镀层不光亮产生原因:(1) 镀液浓度过低(即氯化锌、氯化钾和硼酸的含量均低);(2) 光亮剂不足;(3) pH 过高;(4) 镀液温度过高;(5) 阴极电流密度小;(6) 金属铁杂质多;(7) 有机杂质多。
处理方法:(1) 通过分析,补加氯化锌、氯化钾和硼酸至工艺规范;(2) 适当添加光亮剂;(3) 用稀盐酸溶液调节pH 至工艺规范;(4) 降低镀液温度至工艺规范;(5) 适当提高阴极电流密度;(6) 加入~ 2 mL/L 的双氧水(w = 30%),充分搅拌后,用w = 5% 的氢氧化钠调节pH 至,沉淀、过滤后可除去氢氧化铁;(7) 在镀液温度为45 °C 时加入1 ~ 3 g/L 活性炭,搅拌约30 min 后过滤;或采用高锰酸钾法处理,即先用稀盐酸调低pH 至3 ~ 4,然后在搅拌的情况下将溶有~ 1 g/L 高锰酸钾的热水均匀加入镀液中,再继续搅拌30 min ,然后静置过滤,可除去有机物。
氯化钾镀锌工艺的常见问题及镀液维护
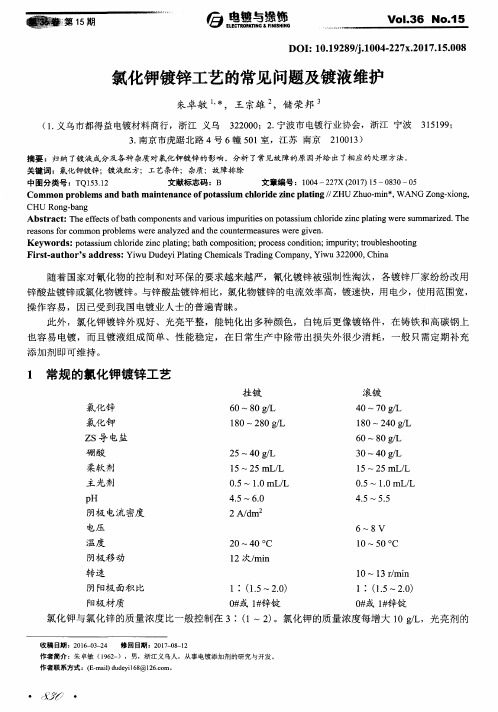
Ke y wo r ds : po t a s s i u m c h l o r i d e z i n c p l a t i n g ; ba t h c o mp os i t i o n ; p r o c e s s c o n d i t i o n; i mp u r i t y; t r o u bl e s ho o t i n g Fi r s t . aut hor’ S a ddr e s s : Yi wu Dud e y i Pl a t i ng Ch e mi c a l s Tr a d i n g Co mp a n y。 Yi wu 3 2 2 0 0 0, Ch i n a
镀液 的配制方法如下 : ( 1 )先用 5 0~6 0。 C的水将计 算量 的氯化钾 溶解 ,用勺子撇去液面浮渣 ,稍作澄清后过滤入镀槽 , 弃去沉渣 。 ( 2 )将 溶解 好 的氯化锌加入镀槽 。
摘 要 :归纳 了镀 液成分及各 种杂质对 氯化钾镀 锌的影 响。分析 了常见故 障的原 因并给 出了相应 的处理 方法 关键 词 :氯化钾镀锌 ;镀 液配方;工艺条件 ;杂质;故障排除 中图分类号 :T Q1 5 3 . 1 2
CH U Ro n g — b a n g
文献标志码 :B
阳极材质
0 ≠ ≠ 或1 群 锌锭
0 ≠ } 或1 ≠ } 锌锭
氯化钾与氯化锌 的质量浓度 比一般 控制在 3:( 1~2 ) 。氯化钾 的质量浓度每增大 1 0 g / L ,光 亮剂 的
氯化钾镀锌主要成分及工艺条件的控制

氯化钾镀锌主要成分及工艺条件的控制前言氯化钾镀锌是上世纪80年代发展起来的一种光亮镀锌工艺。
近年来,我国在电镀添加剂研究开发上取得了显著进展,使得氯化钾镀锌工艺水准达到一个全新的高度,例如:LAN-930氯化钾镀锌工艺较为成功地解决了传统氯化钾镀锌工艺的3大难题:(1)镀层的耐盐雾试验性能比碱性镀锌差;(2)添加剂的分解产物多;(3)铁杂质易超标。
新型氯化钾镀锌添加剂的使用,降低了电镀生产厂商的生产成本,促进了国内电镀锌工艺朝更利于节约成本且环境友好的方向发展。
1·氯化钾镀锌成分及工艺条件的控制氯化钾镀锌工艺的常用配方的工艺条件范围是比较宽广的,其主要成分及工艺条件为:氯化锌30~80g/L,氯化钾180~280g/L,硼酸20~30g/L,添加剂适量,pH值4.5~6.0,10~50℃。
1.1 氯化钾镀锌液主要成分的控制1.1.1 氯化锌氯化锌系主盐,溶于水中会大量放热。
当溶液的pH值≥6.2时,有沉淀产生。
锌离子的质量浓度≥90g/L 时,光亮电流密度范围扩大,但镀液的分散能力和深镀能力会有所下降。
锌离子的质量浓度较低时,光亮电流密度的上限下降,高电流密度区易烧焦,此时的深镀能力较好,但镀层沉积速率较慢。
可增加阳极面积,同时保持镀液较低的pH值,从而使锌离子的质量浓度逐渐上升。
对挂镀而言,当氯化锌的质量浓度为60~70g/L 时,镀液的分散能力最好。
氯化钾镀锌液中无强配位剂,其分散能力和深镀能力不如氰化物镀锌,更加不如无氰碱性锌酸盐镀锌。
有人喜欢在氯化钾镀锌液中加入少量氯化铵,但镀液中加入氯化铵后其分散能力和深镀能力均无改善;又会增加电镀废水的达标难度,所以当使用优良氯化钾镀锌光亮剂时,一般不建议加入氯化铵。
1.1.2 氯化钾氯化钾是弱的配位剂和导电盐,其质量浓度应适当。
当其质量浓度恰当时,镀液的导电性最好,过多或过少都会降低镀液的电导率,从而影响镀液的分散能力和深镀能力。
大量氯离子的存在能增加阴极极化,提高镀液的分散能力和深镀能力,促进阳极的正常溶解。
氯化钾镀锌故障排除一例

氯化钾镀锌故障排除一例常德华【摘要】氯化钾镀锌彩色钝化(六价铬)后得到的是颜色鲜亮的彩虹色,但在生产中,零件钝化烘干后钝化膜表面有一层白雾状的物质,尤其在孔周围的位置这种现象更为明显,经过分析查找发现,原因是钝化溶液中带入的电镀溶液中的有机物(光亮剂)及其分解产物过多。
【期刊名称】《科技风》【年(卷),期】2011(000)021【总页数】1页(P37-37)【关键词】钝化液;有机物及其分解产物【作者】常德华【作者单位】陕西凌云电器集团有限公司,陕西宝鸡721006【正文语种】中文【中图分类】TQ153.15氯化钾镀锌工艺镀液为不含络合剂的单盐镀液,废水易处理;电流效率高,沉积速度快,镀层光亮性和整平性好。
在前段时间的生产中,零件经钝化后出现了故障,笔者在此对故障进行分析排除,供同行朋友参考。
氯化钾镀锌工艺流程如下:除油→热水洗→水洗→酸洗→水洗→水洗→镀锌→水洗→浸亮→水洗→钝化→水洗→热水洗→烘干。
电镀的零件表面烘干后有一层白雾状的物质,特别是在孔周围白雾尤为严重,用手或湿布可以擦去,反复清洗却无效,表面光洁度越高的零件现象越明显。
零件钝化后发雾的原因可能有以下几种:1)前处理除油不彻底;2)镀液被污染,含杂质较多;3)钝化后水洗不干净;4)钝化溶液有问题。
5.1 首先分析前处理除油对零件先进行化学除油,再进行电解除油、酸洗,将电解除油、酸洗过程反复进行3~4次,再开始镀锌→浸亮→钝化→烘干。
零件烘干后白雾状流痕依然存在,原因1)排除。
5.2 溶液是否被污染氯化钾镀锌工艺镀锌并钝化后使得零件表面发雾的情况一般有以下两种:5.2.1 Pb2+杂质污染氯化钾镀锌溶液中,由于锌阳极板材料不纯往往会带入Pb2+杂质,少量的Pb2+杂质会使钝化膜发雾,钝化膜很快变色,大量的Pb2+杂质会使镀层不沉积,看上去似乎有镀层,一经浸亮便很快露底。
正常情况下应控制在0.015g/l以下。
5.2.2 有机杂质污染溶液中的有机杂质主要是光亮剂的分解产物,有机杂质会造成镀层发雾、发脆,结合力变差。
氯化钾镀锌深镀能力差的原因

氯化钾镀锌深镀能力差的原因氯化钾镀锌的深镀能力差,这个问题可不是个小事儿。
说到镀锌,大家可能第一反应就是那种亮闪闪的金属表面,嘿,这可是个保护膜,能让铁铁们不生锈,保持“青春永驻”。
可是呢,氯化钾镀锌这个事儿就有点尴尬了。
咱们不妨来聊聊它为啥总是镀得浅浅的,像个不太会游泳的孩子,总是泡在水边,却不敢下水。
氯化钾的溶解度说起来就有点让人挠头。
它在水里的溶解性比起那些动辄能溶得淋漓尽致的盐可差多了。
想象一下,溶解度不高就好比一个人不爱社交,总是待在一边,不和其他元素交朋友。
这样一来,镀锌的过程就没法进行得那么顺畅,镀层也就成了个“贴膜”的状态,表面看上去还不错,实际上却没什么实质性的保护效果。
就像给你的车贴了张膜,结果一开车就被太阳晒得发烫,根本不能抵挡风吹雨打。
再说了,氯化钾本身的化学特性也不是很友好。
它的离子反应能力相对较弱,不像其他那些活泼的小家伙,能在镀锌过程中积极参与,形成坚固的镀层。
反而,它就像个上了年纪的老大爷,坐在那儿看着热闹,心里想着:“这事儿我不想参与。
”于是,镀锌层就成了一幅画,画得再好看,里面的内容却总是空空如也,真是让人心急如焚。
再来看看操作温度。
这玩意儿可不是随便搞搞就行,温度太高或太低,都会让镀层的质量大打折扣。
氯化钾在高温下的稳定性差,简直就像个小朋友,温度一高,就开始发脾气,反应都变得不稳定。
镀锌的过程中,反应活跃度下降,镀层也就不容易形成,最后造成的结果就是镀得跟个表皮一样,捏起来软软的,根本不够硬朗。
就像吃了个假的榴莲,外表香甜,结果一口下去,满是失望。
然后,咱们再聊聊操作环境。
镀锌过程中的环境因素,真是多得让人眼花缭乱。
比如,空气中的水分、杂质等等。
氯化钾在潮湿的环境下,会吸湿,形成一层薄薄的水膜,这可不是个好兆头。
水膜就像是在给镀层加了一层保护罩,反而不利于镀层的形成。
镀锌的时候,环境必须得干净整洁,不然就像家里没打扫,客人来了却给人留个坏印象,最后自己还得受气。
氯化钾镀锌故障处理

() 适 当减 少工 件装 载量 或增 加阳 极锌板 面积 ; 3 () 通过 分析 ,补 加氯化 锌 至工艺 规范 ; 4 () 采用 置换法 ( 加 1 锌粉 )或 小 电流 5 添 ~3 g纯 密度 电解 除去铜 、铅杂 质 ( 、铅 含 量过 多还 会 使低 铜
维普资讯
第5 期
Vl126 No. o. 5
【 经验交流 】
氯化钾镀锌故障处理
奚兵
( 常州 市荆 川里 新村 l 2丙 2 1 0 ,江 苏 常州
摘 要:汇总 了氯化钾镀锌 的常见故 障, 包括镀层 不光亮 、发
23 1) 10 5
但 是 ,在 日常 生产 中难免 会 发 生质 量 故障 ,主 要 原 因在 于镀 液 维护 不 力 ,组分 失 调或 受 到有 害 杂质 干
ito u e S me me s r ss ul e tk n t l n t h n r d c d. o a u e ho d b a e o e i ae te mi
o c re e f r b e s s c a s e g h nig r c s c u rnc o p o lm , u h s t n t e n p o e s r m a a e n ndr g lrp rfc t n. n g me t a e u a u i a i i o
() 按上述 21 () 222 5 方 法处 理 。 5 .. 6 和 ..() 2
() 调低镀 液温 度至 工艺 规范 ; 1 () 调低 p 至工艺 规范 ; 2 H
2 5 黑色 条纹 ,桔 皮状镀 层 .
2 5 1 产生 原 因 . . () 镀液 p 过 高 ; 1 H () 阴极 电流 密度 大 ; 2 () 镀液温 度 过低 ; 3 () 有机 杂质 多 。 4
- 1、下载文档前请自行甄别文档内容的完整性,平台不提供额外的编辑、内容补充、找答案等附加服务。
- 2、"仅部分预览"的文档,不可在线预览部分如存在完整性等问题,可反馈申请退款(可完整预览的文档不适用该条件!)。
- 3、如文档侵犯您的权益,请联系客服反馈,我们会尽快为您处理(人工客服工作时间:9:00-18:30)。
试片 ,结果显示 :实验 一试片出现的现象和 现在槽 液
赫尔槽试 片现象一致 ,试片发花且低 电流 密度区发灰 不 亮 ,露 底O . 5 c m左 右 。可 以确定 是这 次新 进 的一 批氯化锌有 问题 ,里面含有超标的铅杂质 。
板锌 板 的溶解 度 与镀液 的p H 值 和温 度都相 关 ,通 常 , p H 值低 、槽液 的温度高 ,锌板溶解速度就 比较快 :一般 情 况下 ,要保持足够 的阳极面积 ,以维持 镀液 中锌离子
浓度 ,尽量 少加或不加氯化锌。 在 电镀 原 材 料 中 ,氯化 锌 的质 量还 存 在 较 多 的问 题 ,主要是生产商 没有把铜 、铅杂质 除掉 。所 以,在采
根据 上述故 障 ,对槽液进行处理。往槽 液里加入
2 g / L @ g 锌粉 ,搅拌0 5 h ,沉淀2 h 后过 滤至 清液。最 后 ,阴极挂 瓦楞 铁板 ,按0 . 1 — 0 2 A / d m 小 电流 电解
验 判断 ,应该是 受到铅 杂质 的污染。
电子 因得 不到锌离子而在镀件 上骤集 ,尤其是在 电流密
度较大 的边 角造成 镀层烧 焦。为防止烧焦 ,只好 降低 电
联想 到是加料 之后 出现 的问题 ,于是 问题聚焦 到 原材料 上。由于硼酸还是原 先使 用的,所 以应该不会
出现问题 ,而氯化锌和 氯化钾 是新进 的- - ̄ l : L 。为查 找 问题 出在 哪一种 原料上 ,随即取来 分析纯 的氯化锌和 氯化钾 ,平行做 两组对 比试验 ,分别按 氯化锌5 0 g / L , 氯化 钾2 2 0 g / L ,硼 酸3 0 g / L ,添 加剂 按 正常开 缸 量
低 电流密度 区发黑甚至经硝酸 出光后露 出底层金属 。 根据赫 尔槽 实验 ,取槽液2 5 0 mL ,给 电流0 . 3 A,通 电1 0 mi n ,水 洗 出光 吹干后 观察 试 片 ,试 片发 花且
低 电流 密 度 区 发 灰 不 亮 ,露 底 0 . 5 c m左 右 。 根 据 经
种 导 电盐 ,增加镀液 的导 电性 ,其含量 高 ,电阻小 ,槽 电压就 比较低 ,从 而节省 了电量 。同样 ,氯化锌含 量的
公 司氯化钾镀锌 滚镀 ,4 0 0 0 L 槽子 ,用 1 年 有
余 ,期 间很少 出问题。可有一 次根据化验结果 ,补加
4 0 k g 氯化锌、1 2 0 k g 氯化钾和2 0 k g 硼 酸之后 ,产品 出现 了问题 ,导致镀层无光 ,钝化膜发雾且 变色快 ,
一
晚上 ,第二天早上再试镀 ,结果产品恢复正常。
购 氯化锌时 ,一定 要采购有品牌 的 ,并且 要经过赫 尔槽
实验 方能下槽 。一般 良好的氯化锌 是 白色 晶状组织 ,还
2 . 2
》 . _ 。
表
g / L ,硼酸 2 5 g / L ,各个参 数基 本都 已经达 到工 艺要 求 ,可 为什 么镀 的产 品反而 比之前 的差 呢?经 过 分
纯。 分别 电镀 1 0 mi n ,0 . 3 A,水 洗出光吹 干后观察
锌浓度。 在 氯化 锌 允许 的 浓度 范 围 内 ,要想 获得 良好 的镀 层 ,还 要 与镀 液 的温度 配 合起 来 。一般 情 况 下 ,冬 天 时 ,氯化锌应取上 限 ;夏天时 ,氯化锌应取 下限。 阳极
( 1) 方法一 :赫 尔槽法
面 一 析 ,最后一致认 为问题 出现在原材 料上面 ,原材 料中
含有杂质 。通过赫 尔槽试验 ,分别往赫 尔槽 中加 入氯 工一 化钾和硼酸 ,结果也显示加入硼酸后 的情 况更糟 ,低 程 ~ 嗣 s 电流 密度 区基 本无镀层 ;这更明确说 明是硼酸 带入杂 质 引起 的。细察库房 ,发现硼酸袋 子是 敞开着 的 ,并
表面工程 团・ 经验交流
氯化钾镀锌 由原材料 引起 的故 障三例
③王 超 王 宗雄 ( 宁 波 市 电镀 行 业 协 会 ,浙 江 宁 波 3 1 5 1 9 9 )
( 接上期) 5 案例 二 :由氯化锌 引起 的故 障
一
6 氯化锌的重要性
氯化 锌不仅作 为主盐 提供 锌离子 ,而且本身还是 一
增 加 ,允许 电流 密度上限提高 ,可以采用较高 的 电流 密 度 ,提高沉积速度 和生产效率 ,在镀 锌层厚度不 变的情
况下可 以缩短 电镀 时间 ,还可减 少金 属杂质 的影 响 但 含量过高镀层 结晶粗大 ,镀层粗糙 ,深镀能 力变差。氯 化锌含量不 足时 ,会在阴极上造成 浓差极化 ,一定 量的 浓差极化有好 处 ;但如果浓差极 化过大 ,将造成过 多的
流 密度 ,但 必然 使 生产 效率 降低 、 镀液 的均 镀 能 力下 降 ,致使复 杂镀件难 以得 到合格 的镀层。所 以 ,~般情
况下 ,滚镀 时的氯化锌 允许 浓度 比挂镀时 a '  ̄ f E,氯化锌 含量低 ,有利于提高镀液 的分散 能力和覆盖 能力。滚镀 时氯化锌一般控制在4 0 ~ 6 0 g / L ,挂 镀 时 一 般 控 制在
调整p H 值至正常范围 ,若赫 尔槽试 片高端烧 焦区较 宽 ,首 先调整其他成 分 ,当无明显改善时 ,且镀液 p H 值 升 高 太 快 ,则 可 能硼 酸 质 量 浓度 偏 低 ,可补 加 5 ~1 0 g / L 。硼 酸质 量 浓 度 偏 高, 并 无 害 处 ,只 是 易 于 结 晶析
6 0 - 8 0 g / L ;对 于 铸 铁 件 电镀 锌 时 也 要 使 用 较 高 的 氯 化
添 加 ,各 配置 1 L 镀 液做 赫 尔槽 实验 。 实验一 的氯 化 锌 为上述购进 的氯化锌 ,其余材 料均 为分析 纯 :实验 二 的氯化钾 为 上述购 进 的氯化 钾 ,其余 材料 为分 析