氯化钾镀锌液浮油、混浊原因及预防
氯化钾镀锌工艺手册

氯化钾镀锌工艺手册1、氯化钾镀锌工艺规范 (2)2、镀液的配制 (2)3、主要成分的控制 (3)3.1氯化锌 (3)3.2氯化钾 (3)3.3 硼酸 (4)3.4 添加剂 (5)4、主要工艺参数的控制 (6)4.1 镀液温度 (6)4.2 镀液PH (6)4.3 搅拌 (6)4.4 电流密度 (6)4.5阳极 (6)5、镀液维护要点 (7)6、铁杂质问题 (7)6.1铁杂质的影响与判定 (7)6.2除铁方法 (7)7、加氯化铵的问题 (7)8、氯化钾镀锌常见故障及处理方法 (9)氯化钾镀锌是20世纪80年代初发展起来的一种光亮镀锌工艺。
我国近几年来添加剂开发有了显著进展,温度范围大为扩大、电流密度范围宽、分散能力和深镀能力已与碱性无氰镀锌相当,故发展速度明显加快。
近年来,电镀添加剂研究开发上取得了显著进展,使得氯化钾镀锌工艺水准达到一个全新的高度,成功地解决了传统氯化钾镀锌工艺的三大难题:(1)镀层的耐盐雾实验性能比碱性镀锌差;(2)添加剂的分解产物多;(3)铁杂质易超标。
氯化钾镀锌的优点:①氯化钾镀锌组成中无铵、无络合剂和螯合剂。
电镀废水处理比较简单。
②电流效率高达96%~99%,沉积速度快,约可增加25%~30%的产量,并可直接在难镀的基体材料如铸铁、锻钢、高碳钢等上镀锌。
③镀液导电性好,槽压低(挂镀3~5V、滚镀6~8V),能源消耗比氰化镀锌、锌酸盐镀锌低,约可节电50%之多,而且镀液操作温度宽(5~65℃),适应性很强。
④镀锌层结晶细致,具有极佳的光亮度和整平性,类似亮镍、亮铬的色泽。
⑤该工艺所得的镀层,适合低铬、超低铬钝化和三价铬钝化。
钝化膜色泽鲜艳,特别是白色、蓝白色钝化膜酷似装饰铬镀层。
⑥镀层延展性良好,加厚也不易龟裂和起泡,20μm厚的锌层无明显脆性。
⑦镀液稳定,操作维护简单可靠,镀液成本费用低廉。
氯化钾镀锌缺点:①镀液中有大量的氯离子,对设备有一定的腐蚀。
②对镀前处理要求较高,工件入槽前脱脂、除锈要干净,工件保持活化状态,才能保证锌层与基体良好的结合力。
氯化钾镀锌镀层出现黑斑点原因及排除

氯化钾镀锌镀层出现黑斑点原因及排除
1、前处理不良:加强镀前处理后再进行试验,观察故障现象是否消失。
若仍未排除故障,则再检查其他原因。
2、镀液中氯化物含量太低,而电流密度过高:取250ml镀液,采用逐渐提高氯化钾(钠)含量进行霍尔槽试验。
若随着氯化物含量的提高,霍尔槽阴极试片上的黑色条纹逐渐向高电流密度端移动并逐渐消失,则表明原镀液中氯化物含量偏低,应根据试验结果补加氯化钾(钠)。
若电流密度过高,则应适当减小阴极电流密度。
3、镀液中有机杂质含量过多:取500ml镀液,加入3g/L左右活性炭,强烈搅拌30min,静置8h后过滤镀液。
将处理前、后的镀液进行霍尔槽试验,若经过处理的镀液,霍尔槽阴极试片镀层比未处理的有明显改善,则说明镀液中有机杂质过多,应根据试验结果确定活性炭的加入量,向镀液中加入活性炭处理,并过滤镀液。
氯化物镀锌常见故障处理
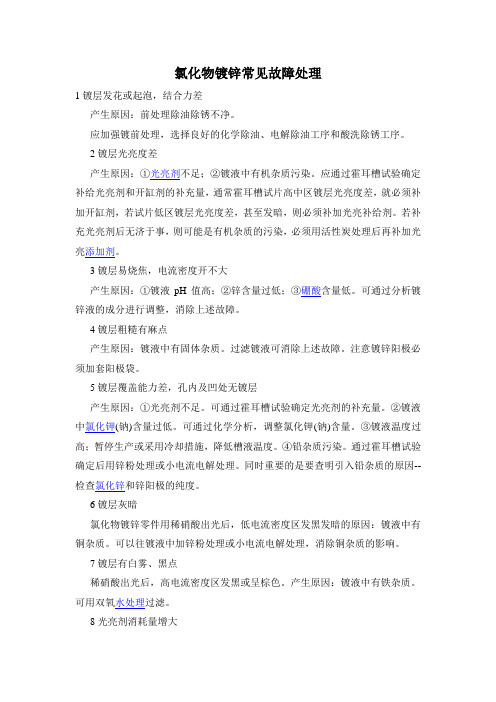
氯化物镀锌常见故障处理1镀层发花或起泡,结合力差产生原因:前处理除油除锈不净。
应加强镀前处理,选择良好的化学除油、电解除油工序和酸洗除锈工序。
2镀层光亮度差产生原因:①光亮剂不足;②镀液中有机杂质污染。
应通过霍耳槽试验确定补给光亮剂和开缸剂的补充量,通常霍耳槽试片高中区镀层光亮度差,就必须补加开缸剂,若试片低区镀层光亮度差,甚至发暗,则必须补加光亮补给剂。
若补充光亮剂后无济于事,则可能是有机杂质的污染,必须用活性炭处理后再补加光亮添加剂。
3镀层易烧焦,电流密度开不大产生原因:①镀液pH值高;②锌含量过低;③硼酸含量低。
可通过分析镀锌液的成分进行调整,消除上述故障。
4镀层粗糙有麻点产生原因:镀液中有固体杂质。
过滤镀液可消除上述故障。
注意镀锌阳极必须加套阳极袋。
5镀层覆盖能力差,孔内及凹处无镀层产生原因:①光亮剂不足。
可通过霍耳槽试验确定光亮剂的补充量。
②镀液中氯化钾(钠)含量过低。
可通过化学分析,调整氯化钾(钠)含量。
③镀液温度过高;暂停生产或采用冷却措施,降低槽液温度。
④铅杂质污染。
通过霍耳槽试验确定后用锌粉处理或小电流电解处理。
同时重要的是要查明引入铅杂质的原因--检查氯化锌和锌阳极的纯度。
6镀层灰暗氯化物镀锌零件用稀硝酸出光后,低电流密度区发黑发暗的原因:镀液中有铜杂质。
可以往镀液中加锌粉处理或小电流电解处理,消除铜杂质的影响。
7镀层有白雾、黑点稀硝酸出光后,高电流密度区发黑或呈棕色。
产生原因:镀液中有铁杂质。
可用双氧水处理过滤。
8光亮剂消耗量增大产生原因:①镀液温度高。
最好采用冷却措施将降低槽液温度或采用间歇生产;②镀液中氯化钾、氯化锌含量过高,使镀液浊点降低,光亮剂析出。
通过分析镀液成分,稀释镀液;③工件除油不净,将大量油污带入镀液中,消耗光亮添加剂中的载体光亮剂。
保证镀锌零件电镀前除油要彻底。
9镀层有条纹产生原因:①光亮剂失调,配槽时添加剂严重不足。
可通过霍耳槽试验,补充添加剂的用量。
氯化钾镀锌发雾的原因及对策
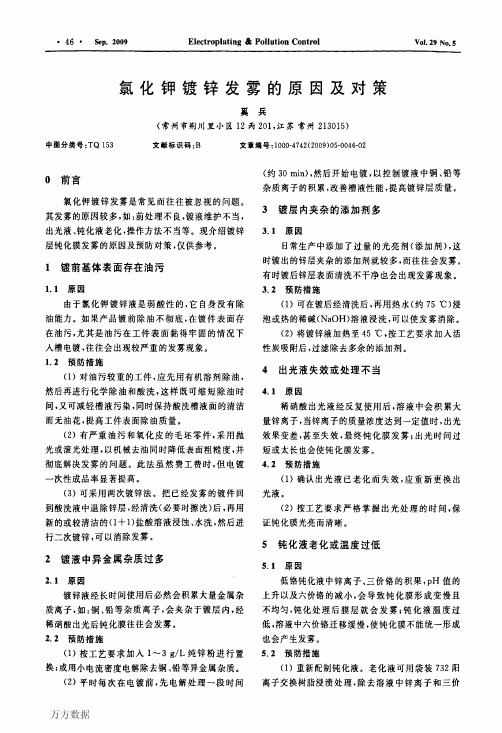
造成阳极磷膜脱落并钝化。以为少挂阳极就可节省 阳极消耗,反而事与愿违。部分阳极钝化后,剩余未 钝化的阳极电流密度更大,钝化更快。升高槽电压 后,恶性循环,最终可能几乎全部钝化。 当采用板状阳极时,背面几乎不导电,阳极设置 时,板的间距不宜大于10 cm。采用钛阳极筐盛装 磷铜阳极球、块时,导电的比表面积大些,钛篮间距 也不宜大于20
(约30 min),然后开始电镀,以控制镀液中铜、铅等 杂质离子的积累,改善槽液性能,提高镀锌层质量。
3镀层内夹杂的添加剂多
3.1
原因
日常生产中添加了过量的光亮剂(添加剂),这 时镀出的锌层夹杂的添加剂就较多,而往往会发雾。 有时镀后锌层表面清洗不干净也会出现发雾现象。
3.2预防措施
1镀前基体表面存在油污
(1)对油污较重的工件,应先用有机溶剂除油, 然后再进行化学除油和酸洗,这样既可缩短除油时 间,又可减轻槽液污染,同时保持酸洗槽液面的清洁 而无油花,提高工件表面除油质量。 (2)有严重油污和氧化皮的毛坯零件,采用抛 光或滚光处理,以机械去油同时降低表面粗糙度,并 彻底解决发雾的问题。此法虽然费工费时,但电镀 一次性成品率显著提高。 (3)可采用两次镀锌法。把已经发雾的镀件回 到酸洗液中退除锌层,经清洗(必要时擦洗)后,再用 新的或较清洁的(1+1)盐酸溶液浸蚀、水洗,然后进 行二次镀锌,可以消除发雾。
阳极易钝化时,部分呈不溶性阳极态,镀液中主 盐Cu2+的质量浓度下降。而补充硫酸铜,不但成本 比用阳极的高,且难溶解,容易引入杂质,是得不偿
失的。
2.1-2
阳极消耗后补换不及时
作为可溶性阳极,阳极总会不断消耗而变小、变 窄、变薄,表观面积越来越小,阳极电流密度越来越 大,越易钝化。应及时检查阳极,对板状阳极,面积 变小后应及时更换,换下来的小阳极可装于钛阳极 筐中继续使用,并不造成浪费。生产中最严重的是 阳极已溶解只剩下液面上的头子,还认为完好。顺 便提及,不少人问到为何镀锌、镍、铜的阳极溶解后 呈花瓶状,液位下腐蚀最快而成瓶颈状,甚至溶断。 这一现象是由氧差电池(一种宏电池现象)造成的 “水线下腐蚀”:液平面接触空气中的氧,水线下的金 属部分接触含氧较高的水或溶液,下部溶液含氧量 相对较低,上下之间形成氧差宏电池,水线下的部分 成为阳极,液位较下部分成为阴极,故水线下的部分 金属,因电化学腐蚀而加快腐蚀速率,最后呈瓶颈
氯化钾镀锌工艺的常见问题及镀液维护
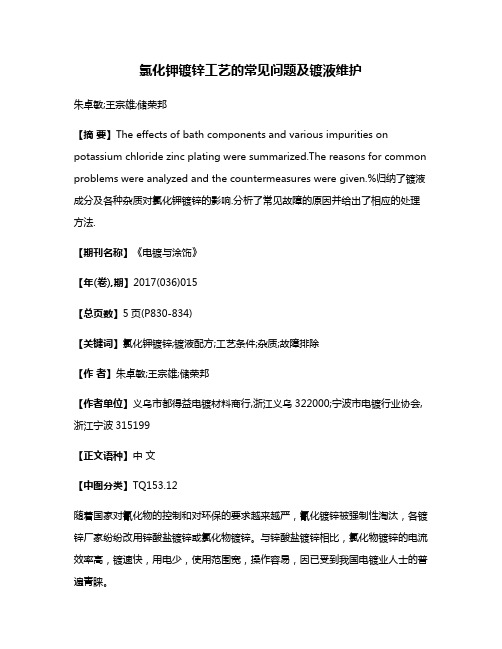
氯化钾镀锌工艺的常见问题及镀液维护朱卓敏;王宗雄;储荣邦【摘要】The effects of bath components and various impurities on potassium chloride zinc plating were summarized.The reasons for common problems were analyzed and the countermeasures were given.%归纳了镀液成分及各种杂质对氯化钾镀锌的影响.分析了常见故障的原因并给出了相应的处理方法.【期刊名称】《电镀与涂饰》【年(卷),期】2017(036)015【总页数】5页(P830-834)【关键词】氯化钾镀锌;镀液配方;工艺条件;杂质;故障排除【作者】朱卓敏;王宗雄;储荣邦【作者单位】义乌市都得益电镀材料商行,浙江义乌322000;宁波市电镀行业协会,浙江宁波315199【正文语种】中文【中图分类】TQ153.12随着国家对氰化物的控制和对环保的要求越来越严,氰化镀锌被强制性淘汰,各镀锌厂家纷纷改用锌酸盐镀锌或氯化物镀锌。
与锌酸盐镀锌相比,氯化物镀锌的电流效率高,镀速快,用电少,使用范围宽,操作容易,因已受到我国电镀业人士的普遍青睐。
此外,氯化钾镀锌外观好、光亮平整,能钝化出多种颜色,白钝后更像镀铬件,在铸铁和高碳钢上也容易电镀,而且镀液组成简单、性能稳定,在日常生产中除带出损失外很少消耗,一般只需定期补充添加剂即可维持。
氯化钾与氯化锌的质量浓度比一般控制在3∶(1 ~ 2)。
氯化钾的质量浓度每增大10 g/L,光亮剂的浊点就下降3 °C。
镀液的配制方法如下:(1) 先用50 ~60 °C的水将计算量的氯化钾溶解,用勺子撇去液面浮渣,稍作澄清后过滤入镀槽,弃去沉渣。
(2) 将溶解好的氯化锌加入镀槽。
(3) 以10倍量的沸水溶解硼酸,硼酸完全溶解后,在缓慢搅拌镀液的情况下将硼酸加入其中。
氯化钾镀锌常见故障分析

涂 料 涂 装 与 电 镀
维普资讯
47
氯化 钾镀 锌 常 见 故 障分 析
田永 良 (成都 飞机 工业集 团公 司热表分厂 ,四川成都 ,610092)
摘 要 本 文依据 实践经验对氯化钾镀锌的一些 常见故 障进行 了分析 ,并提 出了纠正措施 。 关键词 镀锌 ;故障分析 ;实用技 术
3 常见故障分析
产 生 原 因 ①温度过高 ② 光 亮 剂 不 足 ③pH值 过高 ④ 过高 ,钾盐少 ⑤硼酸不足 ⑥ 重金 属离 子杂 质影 响
纠 正 方 法 ①降低温度 ② 补 充 光 亮 剂 ③调整 pH值至工艺范 围 ④调整溶液成分 ⑤补充硼酸 ⑥用 2g/L锌粉处理溶液
1 前 言
氯化钾镀锌 ,不含络合 物,废水处理简单 ,镀 液 稳定、维护简单 ,电流效率高达 95%以上 ,可允许较 大电流密度。适 宜各种铸铁、高碳钢 和热处理零 件 的电镀 。但分散 能力不够好 ,亮度 比氯化铵镀锌 略 逊一些 ,钝化膜结合强度较差 ,镀层性脆。通过选用
3.1 故 障现 象 :漏镀
这项环保工程和电镀废水零排放技术 ,受到了
有污水排放 ,仍对环境有污染 。换言之,达标排放只 全 国 电镀 界 的好评 ,也 受 到 了广 州 市 电镀 协 会 和 香
能减轻环境污染 ,却不能消除环境污染 。达标排放 港电镀商会专家们的高度赞赏。广东省环保局、广
一 年多的运行实践表明 ,在满负荷运行时,扣除
加剧 了水 资 源 的短 缺 。
运行费用后 尚能盈利 30余万元。实现了经济效益 、
(2)电镀 废 水达 标 排放 ,只表 明废水 中的各 种 污 社 会效 益和 环境 效益 较为完 美 的统一 。
常见13种氯化钾镀锌 故障分析告诉你答案
常见13种氯化钾镀锌故障分析告诉你答案本篇汇总了氯化钾镀锌的常见故障,包括镀层不光亮、发雾、结合力差、烧焦、黑色条纹、厚度不均、脆性、沉积速度慢、分散能力差、镀液浑浊等。
介绍了这些疵病的产生原因及其处理方法。
提出了应加强工艺管理、认真做好镀液维护、定期进行净化等措施,以期避免或减少故障发生。
氯化钾镀锌是由最早的无氰氯化铵镀液发展而来的一种无铵弱酸性光亮镀锌工艺。
其优点是:(1)镀液导电性好,槽压低,节省电能;(2)镀层结晶细致、光亮、平整;(3)电流效率高,沉积速度快;(4)镀液分散能力好;(5)适用于铸件直接电镀;(6)废水处理简便,解决了环境污染的问题。
因此,氯化钾镀锌在工业上得到了广泛应用。
但是,在日常生产中难免会发生质量故障,主要原因在于镀液维护不力,组分失调或受到有害杂质干扰,以及工件前处理不良。
本篇拟就氯化钾镀锌中常见故障的产生原因及其处理方法进行汇总和介绍。
各种常见故障的产生原因及其处理方法1.镀层不光亮产生原因:(1) 镀液浓度过低(即氯化锌、氯化钾和硼酸的含量均低);(2) 光亮剂不足;(3) pH 过高;(4) 镀液温度过高;(5) 阴极电流密度小;(6) 金属铁杂质多;(7) 有机杂质多。
处理方法:(1) 通过分析,补加氯化锌、氯化钾和硼酸至工艺规范;(2) 适当添加光亮剂;(3) 用稀盐酸溶液调节pH 至工艺规范;(4) 降低镀液温度至工艺规范;(5) 适当提高阴极电流密度;(6) 加入~ 2 mL/L 的双氧水(w = 30%),充分搅拌后,用w = 5% 的氢氧化钠调节pH 至,沉淀、过滤后可除去氢氧化铁;(7) 在镀液温度为45 °C 时加入1 ~ 3 g/L 活性炭,搅拌约30 min 后过滤;或采用高锰酸钾法处理,即先用稀盐酸调低pH 至3 ~ 4,然后在搅拌的情况下将溶有~ 1 g/L 高锰酸钾的热水均匀加入镀液中,再继续搅拌30 min ,然后静置过滤,可除去有机物。
氯化钾镀锌主要成分及工艺条件的控制
氯化钾镀锌主要成分及工艺条件的控制前言氯化钾镀锌是上世纪80年代发展起来的一种光亮镀锌工艺。
近年来,我国在电镀添加剂研究开发上取得了显著进展,使得氯化钾镀锌工艺水准达到一个全新的高度,例如:LAN-930氯化钾镀锌工艺较为成功地解决了传统氯化钾镀锌工艺的3大难题:(1)镀层的耐盐雾试验性能比碱性镀锌差;(2)添加剂的分解产物多;(3)铁杂质易超标。
新型氯化钾镀锌添加剂的使用,降低了电镀生产厂商的生产成本,促进了国内电镀锌工艺朝更利于节约成本且环境友好的方向发展。
1·氯化钾镀锌成分及工艺条件的控制氯化钾镀锌工艺的常用配方的工艺条件范围是比较宽广的,其主要成分及工艺条件为:氯化锌30~80g/L,氯化钾180~280g/L,硼酸20~30g/L,添加剂适量,pH值4.5~6.0,10~50℃。
1.1 氯化钾镀锌液主要成分的控制1.1.1 氯化锌氯化锌系主盐,溶于水中会大量放热。
当溶液的pH值≥6.2时,有沉淀产生。
锌离子的质量浓度≥90g/L 时,光亮电流密度范围扩大,但镀液的分散能力和深镀能力会有所下降。
锌离子的质量浓度较低时,光亮电流密度的上限下降,高电流密度区易烧焦,此时的深镀能力较好,但镀层沉积速率较慢。
可增加阳极面积,同时保持镀液较低的pH值,从而使锌离子的质量浓度逐渐上升。
对挂镀而言,当氯化锌的质量浓度为60~70g/L 时,镀液的分散能力最好。
氯化钾镀锌液中无强配位剂,其分散能力和深镀能力不如氰化物镀锌,更加不如无氰碱性锌酸盐镀锌。
有人喜欢在氯化钾镀锌液中加入少量氯化铵,但镀液中加入氯化铵后其分散能力和深镀能力均无改善;又会增加电镀废水的达标难度,所以当使用优良氯化钾镀锌光亮剂时,一般不建议加入氯化铵。
1.1.2 氯化钾氯化钾是弱的配位剂和导电盐,其质量浓度应适当。
当其质量浓度恰当时,镀液的导电性最好,过多或过少都会降低镀液的电导率,从而影响镀液的分散能力和深镀能力。
大量氯离子的存在能增加阴极极化,提高镀液的分散能力和深镀能力,促进阳极的正常溶解。
实验四 氯化钾法镀锌
实验四氯化钾法镀锌一、实验目的学习电镀的原理和方法二、实验原理本实验为无氰电镀法,以锌片为阳极,镀件为阴极,以烧杯为电镀槽进行电镀,电镀液的主要成分为ZnCl2和KCl。
ZnCl2提供电镀所需锌离子,含量高,可以提高阴极电流密度和电流效率,并减少其他杂质的污染但会降低分散能力和深镀能力,过高会使镀层粗糙。
含量过低,浓度极差大电流密度开不大,会使光亮区变窄高电流密度区烧焦现象,一般要求40-100g/L.KCl主要起导电作用,浓度低,分散能力低,镀层光亮度下降,浓度过高引入过多氯离子,加速锌阳极自溶解,一般200g/L.H3BO3缓蚀剂,,防止镀液PH升高,25-30g/L光亮剂提高镀层光亮性,每L镀液中加入20ml为宜。
正极反应:Zn-2e=Zn2+ 2H2O-4e=O2+4H+负极反应:Zn2++2e=Zn 2H++2e=H2三、仪器与试剂直流稳压电源,滑线变阻器,烧杯,镀液,出光液,酸洗液,1:1盐酸酸洗液,硝酸四、实验步骤1.镀件前处理用砂纸打磨2片铁片去锈--除油--酸洗2.电镀按照P213图连接好装置,检查线路连接无误。
100ml烧杯中加入4/5体积电镀液,接通电源,调节电压在2.5v,调节变阻器使电流分别为0.1A,0.2,0.3,0.4,0.5,0.6,0.7,0.8,0.9A时对镀件进行电镀,时间为10min 3.镀件后处理冷水冲洗--出光液--水洗---晾干五、注意事项1.通电前,电压档开最小,电流档开最大2.导线的铜丝不能浸入电镀液,鳄鱼夹也不能接触镀液3.铁片镀件不能台靠近烧杯壁,影响锌离子的移动,影响电镀效果4.1:1酸洗时1-2s,即取出用水冲洗,倒立5.出光液浸1-2s,即水洗晾起来六、实验现象记录分析观察镀件的镀层质量镀层的颜色,致密与否,光亮程度,覆盖是否均匀等方面进行评定七、思考题1,2。
氯化钾镀锌由原材料引起的故障三例
试片 ,结果显示 :实验 一试片出现的现象和 现在槽 液
赫尔槽试 片现象一致 ,试片发花且低 电流 密度区发灰 不 亮 ,露 底O . 5 c m左 右 。可 以确定 是这 次新 进 的一 批氯化锌有 问题 ,里面含有超标的铅杂质 。
板锌 板 的溶解 度 与镀液 的p H 值 和温 度都相 关 ,通 常 , p H 值低 、槽液 的温度高 ,锌板溶解速度就 比较快 :一般 情 况下 ,要保持足够 的阳极面积 ,以维持 镀液 中锌离子
浓度 ,尽量 少加或不加氯化锌。 在 电镀 原 材 料 中 ,氯化 锌 的质 量还 存 在 较 多 的问 题 ,主要是生产商 没有把铜 、铅杂质 除掉 。所 以,在采
根据 上述故 障 ,对槽液进行处理。往槽 液里加入
2 g / L @ g 锌粉 ,搅拌0 5 h ,沉淀2 h 后过 滤至 清液。最 后 ,阴极挂 瓦楞 铁板 ,按0 . 1 — 0 2 A / d m 小 电流 电解
验 判断 ,应该是 受到铅 杂质 的污染。
电子 因得 不到锌离子而在镀件 上骤集 ,尤其是在 电流密
度较大 的边 角造成 镀层烧 焦。为防止烧焦 ,只好 降低 电
联想 到是加料 之后 出现 的问题 ,于是 问题聚焦 到 原材料 上。由于硼酸还是原 先使 用的,所 以应该不会
出现问题 ,而氯化锌和 氯化钾 是新进 的- - ̄ l : L 。为查 找 问题 出在 哪一种 原料上 ,随即取来 分析纯 的氯化锌和 氯化钾 ,平行做 两组对 比试验 ,分别按 氯化锌5 0 g / L , 氯化 钾2 2 0 g / L ,硼 酸3 0 g / L ,添 加剂 按 正常开 缸 量
低 电流密度 区发黑甚至经硝酸 出光后露 出底层金属 。 根据赫 尔槽 实验 ,取槽液2 5 0 mL ,给 电流0 . 3 A,通 电1 0 mi n ,水 洗 出光 吹干后 观察 试 片 ,试 片发 花且