常见13种氯化钾镀锌 故障分析告诉你答案
氯化钾镀锌常见故障分析

涂 料 涂 装 与 电 镀
维普资讯
47
氯化 钾镀 锌 常 见 故 障分 析
田永 良 (成都 飞机 工业集 团公 司热表分厂 ,四川成都 ,610092)
摘 要 本 文依据 实践经验对氯化钾镀锌的一些 常见故 障进行 了分析 ,并提 出了纠正措施 。 关键词 镀锌 ;故障分析 ;实用技 术
3 常见故障分析
产 生 原 因 ①温度过高 ② 光 亮 剂 不 足 ③pH值 过高 ④ 过高 ,钾盐少 ⑤硼酸不足 ⑥ 重金 属离 子杂 质影 响
纠 正 方 法 ①降低温度 ② 补 充 光 亮 剂 ③调整 pH值至工艺范 围 ④调整溶液成分 ⑤补充硼酸 ⑥用 2g/L锌粉处理溶液
1 前 言
氯化钾镀锌 ,不含络合 物,废水处理简单 ,镀 液 稳定、维护简单 ,电流效率高达 95%以上 ,可允许较 大电流密度。适 宜各种铸铁、高碳钢 和热处理零 件 的电镀 。但分散 能力不够好 ,亮度 比氯化铵镀锌 略 逊一些 ,钝化膜结合强度较差 ,镀层性脆。通过选用
3.1 故 障现 象 :漏镀
这项环保工程和电镀废水零排放技术 ,受到了
有污水排放 ,仍对环境有污染 。换言之,达标排放只 全 国 电镀 界 的好评 ,也 受 到 了广 州 市 电镀 协 会 和 香
能减轻环境污染 ,却不能消除环境污染 。达标排放 港电镀商会专家们的高度赞赏。广东省环保局、广
一 年多的运行实践表明 ,在满负荷运行时,扣除
加剧 了水 资 源 的短 缺 。
运行费用后 尚能盈利 30余万元。实现了经济效益 、
(2)电镀 废 水达 标 排放 ,只表 明废水 中的各 种 污 社 会效 益和 环境 效益 较为完 美 的统一 。
长弯管氯化钾镀锌钝化故障处理
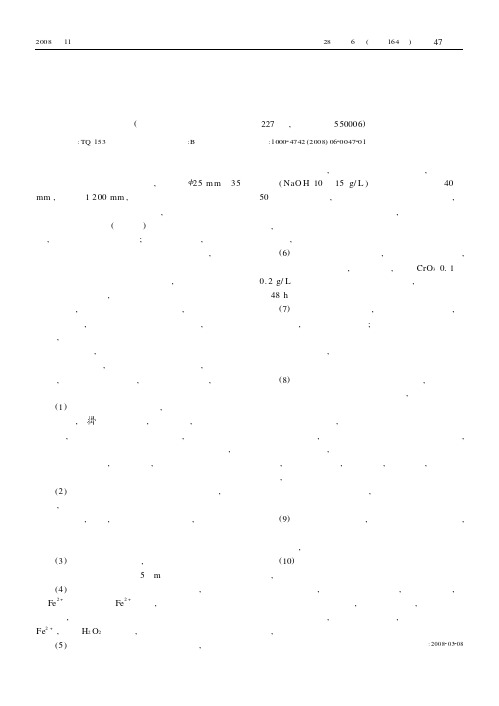
长弯管氯化钾镀锌钝化故障处理童明勇(贵阳市小河经济开发区浦江路227号,贵州贵阳550006)中图分类号:TQ153 文献标识码:B 文章编号:100024742(2008)0620047201 某电镀厂设有氯化钾镀锌生产自动线。
最近承接了一批钢制蛇形的长弯管,其内孔<25m m~35 mm,长度为1200mm,镀锌白钝化业务。
在其加工过程中出现了钝化膜腐蚀变色,尤其是长弯管的管口部分钝化膜腐蚀(长白毛)。
有的钝化件库存一夜后,就出现发雾、发黄现象;彩钝化件变红,甚至出现发黑疵病。
笔者针对上述故障进行了处理,现对处理过程略谈几点体会。
笔者到现场查看了已镀成品,发现镀锌白钝化膜层发蓝雾、发黄,在弯管口上方局部长“白毛”。
经厂方介绍,镀锌件白钝化发生故障后,对所有镀槽进行了大处理,出光、活化、钝化液全部更新,但故障仍存在,未得到介决。
笔者于是查看了最近几天的镀液分析报告单,所有主要技术参数基本正常。
又查看了赫尔槽试片,光亮剂添加情况也正常,同时到车间里,从前处理工序查起,检查了各道工序,针对出现故障现象作了如下分析和处理。
(1)前处理电解除油工序,由于管状镀件容易互相粘合,挂不交叉分挂,管口朝下,很难除去表面油污,尤其是管内油污。
同样道理,酸洗工序也很难将锈除净。
因氯化钾镀液本身没有除油能力,如除油、除锈不干净,带入镀液,极易造成镀锌层钝化后发雾。
(2)氯化钾镀锌光亮剂在夏天温度高时,极易分解,分解物极易和金属离子共沉积。
又由于分解产物易氧化,因此,在高温、潮湿环境中,钝化膜表现为发雾、发黄。
笔者建议应选择耐高温、稳定性高的添加剂。
(3)零件镀锌层太薄,钝化膜也易发黄。
应尽量控制镀锌层厚度不小于5μm。
(4)跌落镀槽中的零件应及时取出,避免镀液内Fe2+的积累。
若Fe2+过高,高电流密度区镀件表面烧焦,钝化后也易产生发雾现象。
平时要控制Fe2+,可用H2O2处理后,过滤。
(5)钢制长弯异形管氯化钾镀锌后,仅靠阴极杠由行车上下移动很难彻底清洗管内残留镀液和有机夹杂物。
氯化钾镀锌工艺的常见问题及镀液维护
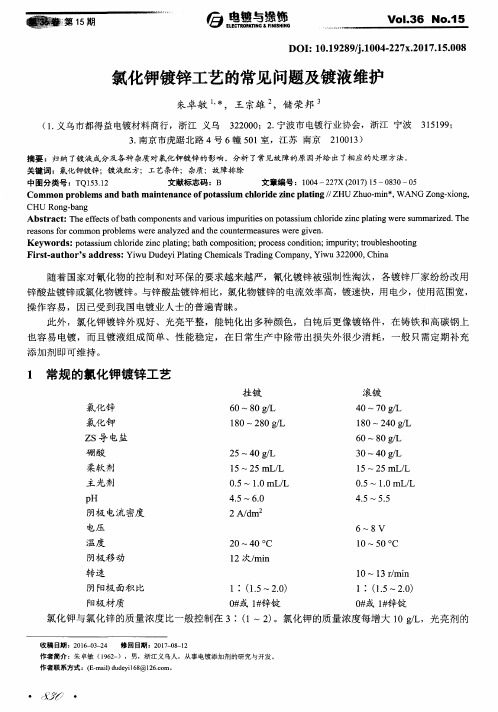
Ke y wo r ds : po t a s s i u m c h l o r i d e z i n c p l a t i n g ; ba t h c o mp os i t i o n ; p r o c e s s c o n d i t i o n; i mp u r i t y; t r o u bl e s ho o t i n g Fi r s t . aut hor’ S a ddr e s s : Yi wu Dud e y i Pl a t i ng Ch e mi c a l s Tr a d i n g Co mp a n y。 Yi wu 3 2 2 0 0 0, Ch i n a
镀液 的配制方法如下 : ( 1 )先用 5 0~6 0。 C的水将计 算量 的氯化钾 溶解 ,用勺子撇去液面浮渣 ,稍作澄清后过滤入镀槽 , 弃去沉渣 。 ( 2 )将 溶解 好 的氯化锌加入镀槽 。
摘 要 :归纳 了镀 液成分及各 种杂质对 氯化钾镀 锌的影 响。分析 了常见故 障的原 因并给 出了相应 的处理 方法 关键 词 :氯化钾镀锌 ;镀 液配方;工艺条件 ;杂质;故障排除 中图分类号 :T Q1 5 3 . 1 2
CH U Ro n g — b a n g
文献标志码 :B
阳极材质
0 ≠ ≠ 或1 群 锌锭
0 ≠ } 或1 ≠ } 锌锭
氯化钾与氯化锌 的质量浓度 比一般 控制在 3:( 1~2 ) 。氯化钾 的质量浓度每增大 1 0 g / L ,光 亮剂 的
氯化物镀锌常见故障处理
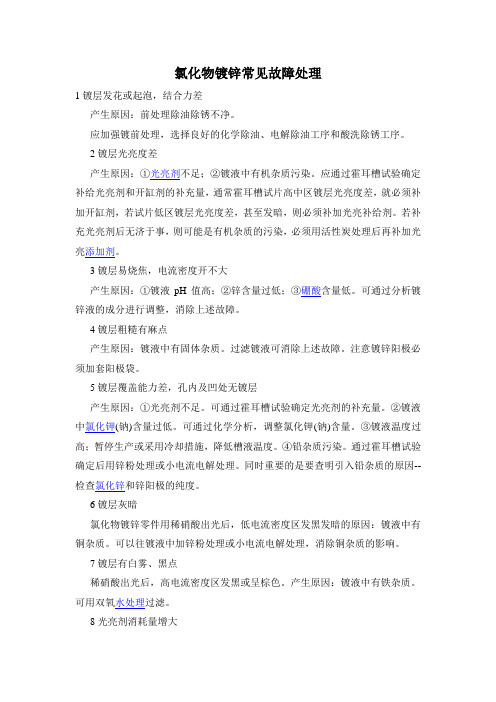
氯化物镀锌常见故障处理1镀层发花或起泡,结合力差产生原因:前处理除油除锈不净。
应加强镀前处理,选择良好的化学除油、电解除油工序和酸洗除锈工序。
2镀层光亮度差产生原因:①光亮剂不足;②镀液中有机杂质污染。
应通过霍耳槽试验确定补给光亮剂和开缸剂的补充量,通常霍耳槽试片高中区镀层光亮度差,就必须补加开缸剂,若试片低区镀层光亮度差,甚至发暗,则必须补加光亮补给剂。
若补充光亮剂后无济于事,则可能是有机杂质的污染,必须用活性炭处理后再补加光亮添加剂。
3镀层易烧焦,电流密度开不大产生原因:①镀液pH值高;②锌含量过低;③硼酸含量低。
可通过分析镀锌液的成分进行调整,消除上述故障。
4镀层粗糙有麻点产生原因:镀液中有固体杂质。
过滤镀液可消除上述故障。
注意镀锌阳极必须加套阳极袋。
5镀层覆盖能力差,孔内及凹处无镀层产生原因:①光亮剂不足。
可通过霍耳槽试验确定光亮剂的补充量。
②镀液中氯化钾(钠)含量过低。
可通过化学分析,调整氯化钾(钠)含量。
③镀液温度过高;暂停生产或采用冷却措施,降低槽液温度。
④铅杂质污染。
通过霍耳槽试验确定后用锌粉处理或小电流电解处理。
同时重要的是要查明引入铅杂质的原因--检查氯化锌和锌阳极的纯度。
6镀层灰暗氯化物镀锌零件用稀硝酸出光后,低电流密度区发黑发暗的原因:镀液中有铜杂质。
可以往镀液中加锌粉处理或小电流电解处理,消除铜杂质的影响。
7镀层有白雾、黑点稀硝酸出光后,高电流密度区发黑或呈棕色。
产生原因:镀液中有铁杂质。
可用双氧水处理过滤。
8光亮剂消耗量增大产生原因:①镀液温度高。
最好采用冷却措施将降低槽液温度或采用间歇生产;②镀液中氯化钾、氯化锌含量过高,使镀液浊点降低,光亮剂析出。
通过分析镀液成分,稀释镀液;③工件除油不净,将大量油污带入镀液中,消耗光亮添加剂中的载体光亮剂。
保证镀锌零件电镀前除油要彻底。
9镀层有条纹产生原因:①光亮剂失调,配槽时添加剂严重不足。
可通过霍耳槽试验,补充添加剂的用量。
氯化钾镀锌常见故障分析

已经应用 于怀集 登 云 汽配 股 份 有 限公 司 的生产 中。 实践 证 明效果 良好 。
参 考文 献
[ ] Q / 6 - 0 , 1 C T4 92 2 汽车发动机气 门技术条件[ ] 0 S. [ ] 文斯雄。钢铁 零件化 学抛 光 [ ] 电镀 与环 保 ,0 5 2 J. 20 ,
a .加强 除油 、 洗 ; 酸 b .调 整光亮 剂含 量 ; C .调整 p 至工艺 范 围 ; H d .补充 硼酸 ; e .降低 阴极 电流密度 。
6 掉入槽 内的镀件 必须及 时捞取 , ) 防止腐蚀
溶解 。
田 永 良
( 中航成 飞热表 处理 厂 )
1 产生原 因 )
对 镀液成 份 、H进行分 析 , 液 温度 、 p 对镀 电流密
度 和 电镀 时 间进 行排 查均未 发现 问题 。怀疑是 光亮
a .镀锌槽 温度 过高 ; b .光亮 剂不 足 ;
C H过高 ; .p
剂 少 了 , 量 添加光 亮 剂 也无 效 。只好 做 赫 尔槽 试 适
2 漏
镀
1 产 生原 因 ) a .镀锌槽 中光亮 剂 比例失调 ; b .镀 锌槽 中有杂 质离子 ; C .镀锌槽 中 C 一 1 含量 低 ; d .局部 前处理 不净 , 有绝缘 物 附着 。 2 处 理方法 ) a .调 整镀锌槽 中光亮剂 比例 ; b .去除镀 锌槽 中杂质 离子 ; c .调 整镀锌槽 中 c 一 量至工 艺 范围 ; 1含 d .加 强除 油 、 酸洗 。
验, 试验也 正 常。在 现场发 现一零件 上有 指纹 , 这下
d .锌离 子含 量过 高 , 钾盐 含量 少 ;
e .硼 酸含 量少 ; f .有重金 属杂 质 。 2 处理 方法 )
氯化钾镀锌镀层起泡、与基体结合力差有哪些原因?如何应对?
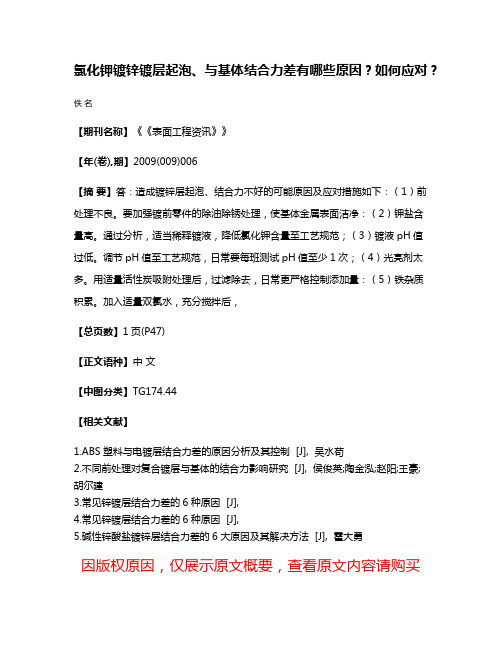
氯化钾镀锌镀层起泡、与基体结合力差有哪些原因?如何应对?佚名
【期刊名称】《《表面工程资讯》》
【年(卷),期】2009(009)006
【摘要】答:造成镀锌层起泡、结合力不好的可能原因及应对措施如下:(1)前处理不良。
要加强镀前零件的除油除锈处理,使基体金属表面洁净:(2)钾盐含
量高。
通过分析,适当稀释镀液,降低氯化钾含量至工艺规范;(3)镀液pH值
过低。
调节pH值至工艺规范,日常要每班测试pH值至少1次;(4)光亮剂太多。
用适量活性炭吸附处理后,过滤除去,日常更严格控制添加量:(5)铁杂质
积累。
加入适量双氯水,充分搅拌后,
【总页数】1页(P47)
【正文语种】中文
【中图分类】TG174.44
【相关文献】
1.ABS塑料与电镀层结合力差的原因分析及其控制 [J], 吴水苟
2.不同前处理对复合镀层与基体的结合力影响研究 [J], 侯俊英;陶金泓;赵阳;王豪;
胡尔建
3.常见锌镀层结合力差的6种原因 [J],
4.常见锌镀层结合力差的6种原因 [J],
5.碱性锌酸盐镀锌层结合力差的6大原因及其解决方法 [J], 霍大勇
因版权原因,仅展示原文概要,查看原文内容请购买。
氯化钾镀锌由原材料引起的故障三例

试片 ,结果显示 :实验 一试片出现的现象和 现在槽 液
赫尔槽试 片现象一致 ,试片发花且低 电流 密度区发灰 不 亮 ,露 底O . 5 c m左 右 。可 以确定 是这 次新 进 的一 批氯化锌有 问题 ,里面含有超标的铅杂质 。
板锌 板 的溶解 度 与镀液 的p H 值 和温 度都相 关 ,通 常 , p H 值低 、槽液 的温度高 ,锌板溶解速度就 比较快 :一般 情 况下 ,要保持足够 的阳极面积 ,以维持 镀液 中锌离子
浓度 ,尽量 少加或不加氯化锌。 在 电镀 原 材 料 中 ,氯化 锌 的质 量还 存 在 较 多 的问 题 ,主要是生产商 没有把铜 、铅杂质 除掉 。所 以,在采
根据 上述故 障 ,对槽液进行处理。往槽 液里加入
2 g / L @ g 锌粉 ,搅拌0 5 h ,沉淀2 h 后过 滤至 清液。最 后 ,阴极挂 瓦楞 铁板 ,按0 . 1 — 0 2 A / d m 小 电流 电解
验 判断 ,应该是 受到铅 杂质 的污染。
电子 因得 不到锌离子而在镀件 上骤集 ,尤其是在 电流密
度较大 的边 角造成 镀层烧 焦。为防止烧焦 ,只好 降低 电
联想 到是加料 之后 出现 的问题 ,于是 问题聚焦 到 原材料 上。由于硼酸还是原 先使 用的,所 以应该不会
出现问题 ,而氯化锌和 氯化钾 是新进 的- - ̄ l : L 。为查 找 问题 出在 哪一种 原料上 ,随即取来 分析纯 的氯化锌和 氯化钾 ,平行做 两组对 比试验 ,分别按 氯化锌5 0 g / L , 氯化 钾2 2 0 g / L ,硼 酸3 0 g / L ,添 加剂 按 正常开 缸 量
低 电流密度 区发黑甚至经硝酸 出光后露 出底层金属 。 根据赫 尔槽 实验 ,取槽液2 5 0 mL ,给 电流0 . 3 A,通 电1 0 mi n ,水 洗 出光 吹干后 观察 试 片 ,试 片发 花且
氯化钾镀锌

氯化钾镀锌氯化钾镀锌2011年07月05日网易博客安全提醒:系统检测到您当前密码的安全性较低,为了您的账号安全,建议您适时修改密码立即修改 | 关闭氯化钾镀锌工艺比较成熟,它的优点是无毒,镀液成分简单,成本低,电流效率高,沉积速度快,可以获得结晶细致、光亮的镀锌层。
缺点是镀液对钢铁设备腐蚀性大,彩色钝化膜易变色,抗盐雾性能不如碱性镀锌。
1 氯化钾镀锌配方及工艺条件氯化钾镀锌配方及工艺条件见下表。
表氯化钾镀锌溶液配方及工艺条件镀液组成及工艺条件挂镀滚镀氯化锌(ZnCl2)(g/L) 60~80 40~50 氯化钾(KCl)(g/L) 180~220 180~220 硼酸(H3BO3)(g/L) 25~35 25~35 柔软剂(ml/L) 20~25 15~20 光亮剂(ml/L) 1~2 0.5~1 pH值 4.8~5.6 4.8~5.6 温度(℃) 10~50 10~50 电流密度(A/dm2) 1~5 0.5~0.8 2 氯化钾镀锌溶液的配制2.1 先在镀槽加入总体积二分之一容积的50~60℃热水,然后将计算量的氯化锌及氯化钾分别加入并搅拌溶解。
2.2 在另一容器用沸水溶解计算量的硼酸,然后加入槽中。
2.3 加水至规定体积,在搅拌下加入1~2ml/L双氧水,继续搅拌约30min,加入锌粉1~2g/L,并剧烈搅拌,静止沉淀2h后过滤。
2.4 测定镀液pH值,如不在工艺范围,可用稀盐酸或稀氢氧化钠溶液调节镀液pH值至5.5左右,加入计算量的添加剂,添加剂需要用水稀释5~10倍后加入。
2.5 用0.1~0.3A/dm2的阴极电流密度通电处理1~2h。
2.6 取镀液用赫尔槽做小样试验,根据试验结果调整镀液后即可生产。
氯化钾应选用精制的电镀级,不要用农用氯化钾,因农用氯化钾杂质太多(配槽时溶液带有赭红色的沉渣沉淀就是农用氯化钾)。
3 各成分及工艺条件的影响3.1 氯化锌氯化锌是主盐,也是一种导电盐,能增加镀液的导电性。
- 1、下载文档前请自行甄别文档内容的完整性,平台不提供额外的编辑、内容补充、找答案等附加服务。
- 2、"仅部分预览"的文档,不可在线预览部分如存在完整性等问题,可反馈申请退款(可完整预览的文档不适用该条件!)。
- 3、如文档侵犯您的权益,请联系客服反馈,我们会尽快为您处理(人工客服工作时间:9:00-18:30)。
常见13种氯化钾镀锌故障分析告诉你答案本篇汇总了氯化钾镀锌的常见故障,包括镀层不光亮、发雾、结合力差、烧焦、黑色条纹、厚度不均、脆性、沉积速度慢、分散能力差、镀液浑浊等。
介绍了这些疵病的产生原因及其处理方法。
提出了应加强工艺管理、认真做好镀液维护、定期进行净化等措施,以期避免或减少故障发生。
氯化钾镀锌是由最早的无氰氯化铵镀液发展而来的一种无铵弱酸性光亮镀锌工艺。
其优点是:(1)镀液导电性好,槽压低,节省电能;(2)镀层结晶细致、光亮、平整;(3)电流效率高,沉积速度快;(4)镀液分散能力好;(5)适用于铸件直接电镀;(6)废水处理简便,解决了环境污染的问题。
因此,氯化钾镀锌在工业上得到了广泛应用。
但是,在日常生产中难免会发生质量故障,主要原因在于镀液维护不力,组分失调或受到有害杂质干扰,以及工件前处理不良。
本篇拟就氯化钾镀锌中常见故障的产生原因及其处理方法进行汇总和介绍。
各种常见故障的产生原因及其处理方法1.镀层不光亮产生原因:(1) 镀液浓度过低(即氯化锌、氯化钾和硼酸的含量均低);(2) 光亮剂不足;(3) pH 过高;(4) 镀液温度过高;(5) 阴极电流密度小;(6) 金属铁杂质多;(7) 有机杂质多。
处理方法:(1) 通过分析,补加氯化锌、氯化钾和硼酸至工艺规范;(2) 适当添加光亮剂;(3) 用稀盐酸溶液调节pH 至工艺规范;(4) 降低镀液温度至工艺规范;(5) 适当提高阴极电流密度;(6) 加入~ 2 mL/L 的双氧水(w = 30%),充分搅拌后,用w = 5% 的氢氧化钠调节pH 至,沉淀、过滤后可除去氢氧化铁;(7) 在镀液温度为45 °C 时加入1 ~ 3 g/L 活性炭,搅拌约30 min 后过滤;或采用高锰酸钾法处理,即先用稀盐酸调低pH 至3 ~ 4,然后在搅拌的情况下将溶有~ 1 g/L 高锰酸钾的热水均匀加入镀液中,再继续搅拌30 min ,然后静置过滤,可除去有机物。
2.发雾、发花:产生原因(1) 镀液温度过高;氯化钾镀锌故障处理(2) pH 过高;(3) 槽镀工件过多或阳极面积不够;(4) 氯化锌含量过低;(5) 金属铜、铅杂质多;(6) 光亮剂不足;(7) 有机杂质多;(8) 工件基体表面的前处理不良。
处理方法(1) 调低镀液温度至工艺规范;(2) 调低pH 至工艺规范;(3) 适当减少工件装载量或增加阳极锌板面积;(4) 通过分析,补加氯化锌至工艺规范;(5) 采用置换法(添加1 ~ 3 g 纯锌粉)或小电流密度电解除去铜、铅杂质(铜、铅含量过多还会使低电流密度区镀层呈黑色雾状);(6) 适当添加光亮剂;(7) 在镀液温度为45 °C 时加入1 ~ 3 g/L 活性炭,搅拌约30 min 后过滤;或采用高锰酸钾法处理,即先用稀盐酸调低pH 至3 ~ 4,然后在搅拌的情况下将溶有~ 1 g/L 高锰酸钾的热水均匀加入镀液中,再继续搅拌30 min ,然后静置过滤,可除去有机物。
3.起泡,结合力差:产生原因(1) 镀液中氯化钾含量过高;(2) pH 过低(3) 阴极电流密度大;(4) 光亮剂过多;(5) 金属铁杂质多;(6) 工件基体含有硅。
处理方法(1) 通过分析,补加氯化钾至工艺规范;(2) 调高pH 至工艺规范;(3) 适当降低阴极电流密度;(4) 用适量的活性炭吸附后过滤;(5) 加入~ 2 mL/L 的双氧水(w = 30%),充分搅拌后,用w = 5% 的氢氧化钠调节pH 至,沉淀、过滤后可除去氢氧化铁;(6) 通过核实,配制含氢氟酸的混合溶液进行酸洗。
可采用300 mL/L 浓盐酸+ 20 mL/L 氢氟酸(wHF = 40%)溶液,其中的氢氟酸能溶解并去除含硅化合物,使工件基体表面完全活化。
4 粗糙,烧焦:产生原因(1) 镀液中氯化锌含量过高(使镀层粗糙)或过低(易烧焦);(2) 氯化钾和硼酸含量过低;(3) pH 过高(使镀层粗糙)或过低(导致烧焦);(4) 光亮剂不足;(5) 金属铁、铜杂质多。
处理方法:(1) 通过分析,调整氯化锌含量至工艺规范;(2) 补加氯化钾和硼酸至工艺规范;(3) 调节pH 至工艺规范;(4) 适当添加光亮剂;(5) 加入~ 2 mL/L 的双氧水(w = 30%),充分搅拌后,用w = 5% 的氢氧化钠调节pH 至,沉淀、过滤后可除去氢氧化铁;(6)采用置换法(添加1 ~ 3 g 纯锌粉)或小电流密度电解除去铜、铅杂质(铜、铅含量过多还会使低电流密度区镀层呈黑色雾状);5 黑色条纹,桔皮状镀层:产生原因(1) 镀液pH 过高;(2) 阴极电流密度大;(3) 镀液温度过低;(4) 有机杂质多。
处理方法(1) 将镀液pH 调低至工艺规范;(2) 适当降低阴极电流密度;(3) 提高镀液温度至工艺规范;(4) 在镀液温度为45 °C 时加入1 ~ 3 g/L 活性炭,搅拌约30 min 后过滤;或采用高锰酸钾法处理,即先用稀盐酸调低pH 至3 ~ 4,然后在搅拌的情况下将溶有~ 1 g/L 高锰酸钾的热水均匀加入镀液中,再继续搅拌30 min ,然后静置过滤,可除去有机物。
6 厚度不均,凹处色暗:产生原因(1) 镀液中氯化锌含量过高;(2) 氯化钾和硼酸含量过低;(3) pH 过高;(4) 光亮剂不足;(5) 镀液温度过高;(6) 金属铜、铅杂质多。
处理方法(1) 稀释部分镀液或相应提高氯化钾含量;(2) 通过分析,补加氯化钾和硼酸至工艺规范;(3) 将镀液pH 调低至工艺规范;(4) 适当添加光亮剂;(5) 降低镀液温度至工艺规范;(6) 采用置换法(添加1 ~ 3 g 纯锌粉)或小电流密度电解除去铜、铅杂质(铜、铅含量过多还会使低电流密度区镀层呈黑色雾状);7 脆性大:产生原因(1) 镀液pH 过高或过低;(2) 光亮剂过多;(3) 镀液温度过低;(4) 金属铁、铜杂质多;(5) 有机杂质多。
处理方法(1) 将镀液pH 调节至工艺规范;(2) 用适量的活性炭吸附处理;(3) 降低镀液温度至工艺规范;(4)加入~ 2 mL/L 的双氧水(w = 30%),充分搅拌后,用w = 5% 的氢氧化钠调节pH 至,沉淀、过滤后可除去氢氧化铁;(5) 在镀液温度为45 °C 时加入1 ~ 3 g/L 活性炭,搅拌约30 min 后过滤;或采用高锰酸钾法处理,即先用稀盐酸调低pH 至3 ~ 4,然后在搅拌的情况下将溶有~ 1 g/L 高锰酸钾的热水均匀加入镀液中,再继续搅拌30 min ,然后静置过滤,可除去有机物。
(6) 采用置换法(添加1 ~ 3 g 纯锌粉)或小电流密度电解除去铜、铅杂质(铜、铅含量过多还会使低电流密度区镀层呈黑色雾状);8 边角锌层疏松、低电流密度区色暗:产生原因(1) 镀液中氯化锌含量过低;(2) pH 过高;(3) 光亮剂不足;(4) 镀液温度过高。
处理方法(1) 通过分析,补加氯化锌至工艺规范;(2) 将镀液pH 调低至工艺规范;(3) 适当添加光亮剂;(4) 降低镀液温度至工艺规范。
9 . 滚镀件有黑眼印:产生原因(1) 镀液pH 过高;(2) 阴极电流密度大;(3) 金属铁杂质多。
处理方法;(1) 将镀液pH 调低至工艺规范;(2) 适当降低阴极电流密度;(3) 加入~ 2 mL/L 的双氧水(w = 30%),充分搅拌后,用w = 5% 的氢氧化钠调节pH 至,沉淀、过滤后可除去氢氧化铁;10 沉积速度慢:产生原因(1) 镀液中氯化锌含量过高或过低;(2) pH 过低;(3) 阴极电流密度小;(4) 光亮剂过多;(5) 镀液温度过低;(6) 有机杂质多。
处理方法( 1) 通过分析,调整氯化锌至工艺规范;( 2) 将镀液pH 调高至工艺规范;( 3) 适当降低阴极电流密度;( 4) 用适量的活性炭吸附处理;( 5) 提高镀液温度至工艺规范;( 6)在镀液温度为45 °C 时加入1 ~ 3 g/L 活性炭,搅拌约30 min 后过滤;或采用高锰酸钾法处理,即先用稀盐酸调低pH 至3 ~ 4,然后在搅拌的情况下将溶有~ 1 g/L 高锰酸钾的热水均匀加入镀液中,再继续搅拌30 min ,然后静置过滤,可除去有机物。
11 分散能力差:产生原因(1) 镀液中氯化锌含量过高;(2) 氯化钾含量过低;(3) 硼酸含量过低;(4) pH 过高;(5) 光亮剂不足;(6) 金属铜、铅杂质多;(7) 有机杂质多。
处理方法:(1) 稀释部分镀液或提高氯化锌含量;(2) 通过分析,补加氯化钾至工艺规范;(3) 补加硼酸至工艺规范;(4) 将镀液pH 调低至工艺规范;(5) 适当添加光亮剂;(6)采用置换法(添加1 ~ 3 g 纯锌粉)或小电流密度电解除去铜、铅杂质(铜、铅含量过多还会使低电流密度区镀层呈黑色雾状);(7) 在镀液温度为45 °C 时加入1 ~ 3 g/L 活性炭,搅拌约30 min 后过滤;或采用高锰酸钾法处理,即先用稀盐酸调低pH 至3 ~ 4,然后在搅拌的情况下将溶有~ 1 g/L 高锰酸钾的热水均匀加入镀液中,再继续搅拌30 min ,然后静置过滤,可除去有机物。
12 镀液浑浊,呈油状:产生原因(1) 镀液中氯化钾含量过低;(2) pH 过低;(3) 光亮剂过多;(4) 镀液温度过高;(5) 有机杂质多。
处理方法:(1) 通过分析,补加氯化钾至工艺规范;(2) 将镀液pH 调高至工艺规范;(3) 用适量的活性炭吸附处理;(4) 降低镀液温度至工艺规范;(5) 在镀液温度为45 °C 时加入1 ~ 3 g/L 活性炭,搅拌约30 min 后过滤;或采用高锰酸钾法处理,即先用稀盐酸调低pH 至3 ~ 4,然后在搅拌的情况下将溶有~ 1 g/L 高锰酸钾的热水均匀加入镀液中,再继续搅拌30 min ,然后静置过滤,可除去有机物。
实践证明,氯化钾镀锌时发生的质量故障,大多是受有害杂质的影响。
除以上所述外,铁杂质还会引起低电流密度区镀层发黄、硝酸出光变灰以及钝化后出现蓝色或黑色污斑等不良现象;铜、铅杂质过多,也会造成镀层钝化后发黑;有机杂质则会导致镀层钝化后出现条纹等疵病。
因此,必须加强工艺管理,认真做好镀液维护,定期进行净化。
只有这样,才能减少故障的发生。