注塑成型作业指导书
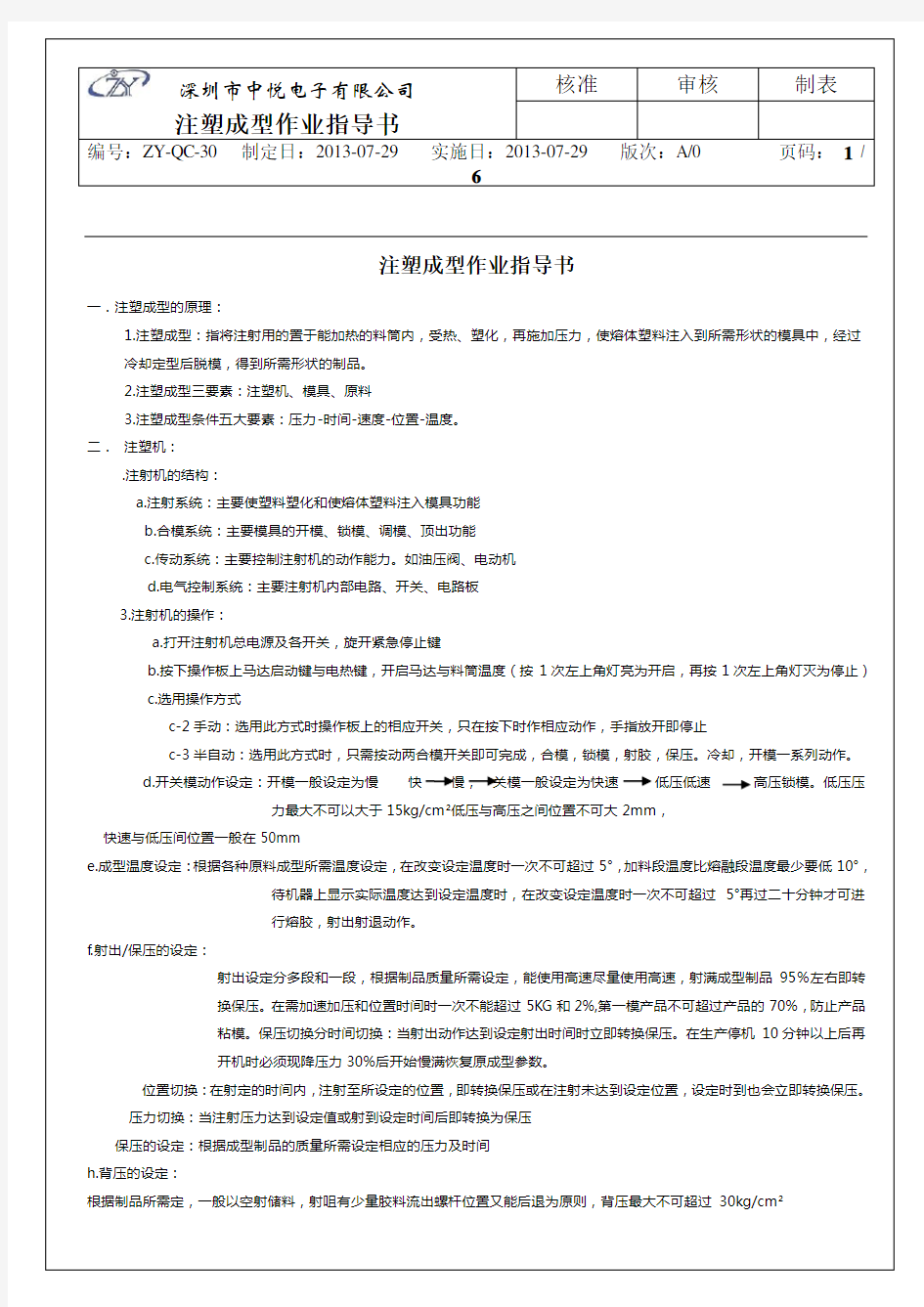

编号:ZY-QC-30 制定日:2013-07-29 实施日:2013-07-29 版次:A/0 页码:1 / 6
注塑成型作业指导书
一.注塑成型的原理:
1.注塑成型:指将注射用的置于能加热的料筒内,受热、塑化,再施加压力,使熔体塑料注入到所需形状的模具中,经过
冷却定型后脱模,得到所需形状的制品。
2.注塑成型三要素:注塑机、模具、原料
3.注塑成型条件五大要素:压力-时间-速度-位置-温度。
二.注塑机:
.注射机的结构:
a.注射系统:主要使塑料塑化和使熔体塑料注入模具功能
b.合模系统:主要模具的开模、锁模、调模、顶出功能
c.传动系统:主要控制注射机的动作能力。如油压阀、电动机
d.电气控制系统:主要注射机内部电路、开关、电路板
3.注射机的操作:
a.打开注射机总电源及各开关,旋开紧急停止键
b.按下操作板上马达启动键与电热键,开启马达与料筒温度(按1次左上角灯亮为开启,再按1次左上角灯灭为停止)
c.选用操作方式
c-2手动:选用此方式时操作板上的相应开关,只在按下时作相应动作,手指放开即停止
c-3半自动:选用此方式时,只需按动两合模开关即可完成,合模,锁模,射胶,保压。冷却,开模一系列动作。
d.开关模动作设定:开模一般设定为慢快慢,关模一般设定为快速低压低速高压锁模。低压压
力最大不可以大于15kg/cm2低压与高压之间位置不可大2mm,
快速与低压间位置一般在50mm
e.成型温度设定:根据各种原料成型所需温度设定,在改变设定温度时一次不可超过5°,加料段温度比熔融段温度最少要低10°,
待机器上显示实际温度达到设定温度时,在改变设定温度时一次不可超过5°再过二十分钟才可进
行熔胶,射出射退动作。
f.射出/保压的设定:
射出设定分多段和一段,根据制品质量所需设定,能使用高速尽量使用高速,射满成型制品95%左右即转
换保压。在需加速加压和位置时间时一次不能超过5KG和2%,第一模产品不可超过产品的70%,防止产品
粘模。保压切换分时间切换:当射出动作达到设定射出时间时立即转换保压。在生产停机10分钟以上后再
开机时必须现降压力30%后开始慢满恢复原成型参数。
位置切换:在射定的时间内,注射至所设定的位置,即转换保压或在注射未达到设定位置,设定时到也会立即转换保压。
压力切换:当注射压力达到设定值或射到设定时间后即转换为保压
保压的设定:根据成型制品的质量所需设定相应的压力及时间
h.背压的设定:
根据制品所需定,一般以空射储料,射咀有少量胶料流出螺杆位置又能后退为原则,背压最大不可超过30kg/cm2
编号:ZY-QC-30 制定日:2013-07-29 实施日:2013-07-29 版次:A/0 页码:2 / 6
四.塑料原料:
1.塑料的分类:热可塑性塑料(可回收再利用),热固性塑料(不可回用)
热塑性塑料成型参数参照表:
序号中文
名称
英文烘料温度(°
C)
烘料时间
(H)
适当模温(°C)可塑化
温度(C)
成型收
缩率(%)
1 聚乙烯PE 70--80
或不烘
1--2 20-50 160--240 0.5—2.5
2 聚丙烯PP 60--80
或不烘
1--2 20--50 170--300 1.3—1.9
3 聚苯乙烯PS 70--80
或不烘
1--2 20--70 180--260 0.3—0.8
4 聚氯乙烯PVC 60--70
或不烘
1--2 50--70 140--180 0.1-0.5
5 丙烯晴+丁二烯
+苯乙烯ABS 80--100 2H以上40--80 180--260 0.4—0.8 6 丙烯酸甲PMMA 80--90 3H以上50--90 180--250 0.2—0.8
7 聚硫胺PA 90--120 4H以上40以上260--300 0.7—2.5
8 聚甲醛POM 70--85 2--4 40--120 170--230 1.6—2.4
9 PBT 100--130 3--4 60--90 230--260 1.3—2.4
10 聚碳酸酯PC 110--140 3--4 80--120 270--310 0.5—0.7
11 聚氧化二PPO 20--100 2--4 60--100 220--300 0.5—0.7
12 聚硫化甲PPS 130--160 1--3 120--160 290--330 1.0—1.4
13 聚醚风PES 180--230 3H以上140--180 340--390 0.5—1.0
14 聚二醚酮PEEK 150--190 3H以上130--170 350--400 1.1—2.0
编号:ZY-QC-30 制定日:2013-07-29 实施日:2013-07-29 版次:A/0 页码:3 / 6
五.制品常见的原因及解决方法
异常
现象
产生原因解决办法
缺料1.料筒及喷嘴温度偏低
2.模具温度偏低
3.加料量不够
4.剩料太多
5.制品超过最大注射量
6.注射压力太低
7.注射速度太慢
8.模孔无适当排气孔
9.流道或浇口太小
10.注射时间太短、柱塞或螺杆退回太早
11.杂物堆塞喷嘴或弹簧喷嘴失灵
提高料筒或喷嘴温度
提高模具温度
适当增加料量
减少剩料量
选用注射量更大的注射机
提高注射压力或熔料温度
提高注射速度
模具开排气孔
适当增加流道或浇口尺寸
增加注射时间及保压时间
清理喷嘴及更换喷嘴零件
毛边1.注射压力太大
2.模具闭合不紧或单向受力
3.模具平面落入异物
4.塑料温度太高
5.制品投影面积超过注射机所允许的成型面积
6.模板变形弯曲
适当减小注射压力
提高合模力,调整合模装置
清理模具
降低料筒及喷嘴温度
改变制品造型或更换大型注射机
检修模板或更换模板
气泡1.原料含水份、溶剂或挥发物
2.熔料温度太高或受热时间太长,已降解或分解
3.注射压力太大
4.注射柱塞退回太早
5.模具温度太低
6.注射速度太快
7.在料筒加料端混入空气
原料进行干燥处理
降低熔料温度,或拆机及更换新料
降低注射压力
延长退回时间或增加预塑时间
提高模温
降低注射速度
适当增加背压,或对空注射
缩水1.流道、浇口太小
2.制品太厚或薄厚悬殊
3.浇口位置不适当
4.注射及保压时间太短
5.加料量不够
6.料筒温度太高
7.注射压力太小
8.注射速度太慢
增加流道、浇口尺寸
改进制品工艺设计,使制品薄厚均匀
浇口开在制品的壁厚处,改进浇口位置
延长及保压时间
增加剩料量
降低料筒温度
提高注射压力
提高注射速度
编号:ZY-QC-30 制定日:2013-07-29 实施日:2013-07-29 版次:A/0 页码:4 / 6
熔接痕1.熔料温度太低
2.浇口太多
3.脱模剂过量
4.注射速度太慢
5.模具温度太低
6.注射压力太小
7.模具排气不良
提高料筒、喷嘴及模具温度
减少浇口或改变浇口位置
采用雾化脱模剂,减少用量
提高注射速度
提高模温
提高注射压力
增加模具排气孔
制品表面波纹1.料筒温度太低
2.注射压力小
3.模具温度低
4.注射速度太慢
5.流道、浇口太小
提高料筒温度
提高注射压力
提高模温
提高注射速度
增大流道、浇口尺寸
黑点及条纹1.塑料已分解
2.塑料碎屑卡入注射柱塞和料筒之间
3.喷嘴与模具主流道吻合不良,产生积料,并在
每次注射时带入模腔
4.模具无排气孔
降低料筒温度或换料
提从高料筒温度
检查喷嘴与模具注口,使之吻合良好
增加模具排气孔
银纹、斑纹1.塑料温度太高
2.原材料含水量太大
3.注射压力太低
4.流道、浇口太小
5.树脂忠有挥发物
降低模温
原材料进行干燥处理
提高注射压力
增加流道、浇口尺寸
原料进行干燥处理
制品变形1.冷却时间不够
2.模具温度太高
3.制品厚薄悬殊
4.制品脱模杆位置不当、受力不均
5.模具前后温度不均
6.浇口部分过分的填充作用
延长冷却时间
降低模温
尽量使制品厚薄均匀
改变制品与脱模杆的位置,使受力均匀
使模具两半的温度一致
减少垫料
裂纹1.模具温度太低
2.制品冷却时间太长
3.制品顶出装置倾斜或不平衡
4.脱模杆截面积太小或数量不够
5.嵌件未预热或温度不够
6.制品斜度不够
提高模温
减少冷却时间
调整顶出装置的位置,使制品受力均匀
增加脱模杆的截面积或数量
提高嵌件预热温度
改进制品工艺设计、增加斜度
制品脱皮1.不同塑料混杂
2.同一塑料不同牌号相混
采用单一品种的塑料
采用同牌号的塑料
编号:ZY-QC-30 制定日:2013-07-29 实施日:2013-07-29 版次:A/0 页码:5 / 6
分层 3.塑化不均
4.混入异物提高成型温度并使之均匀清理原材料,除去杂质
制品强度下降1.塑料降解或分解
2.成型温度太低
3.熔接不良
4.塑料回料用的次数太多
5.塑料潮湿
6.浇口位置不当(如在受弯曲力处)
7.塑料混入杂质
8.制品设计不良,如有锐角、缺口
9.围绕金属嵌件周围的塑料厚度不够
10模具温度太低
适当降低温度或清理料筒
提高成型温度
提高熔接缝的强度
减少回料混入的比例
原料进行干燥
改变浇口位置
原料过筛,以除去杂质
改进制品的工艺设计,避免锐角、缺口
嵌件设计在壁厚处,改变嵌件位置
提高模温
制品
脱模困难1.模具太粗糙
2.模具斜度不够
3.模具镶块处缝隙太大
4.成型周期太短或太长
5.模芯无进气孔
6.模具温度不合适
7.注射压力太高,注射时间太长
8.模具表面划伤或刻痕
9.顶出装置结构不良
降低模具粗糙度
增加模具的脱模斜度
减小模具镶块处缝隙
调整成型周期
缩短模具闭合时间或增加进气孔
降低模温
降低注射压力,缩短注射时间
检修模具型腔
改进顶出装置的结构
主流道粘模1.主流道斜度不够
2.主流道衬套弧度与喷嘴弧度不吻合
3.喷嘴喷孔直径大于主流道直径
4.主流道太粗糙
5.喷嘴温度太低
6.主流道无冷料穴
7.冷却时间太短,主流道尚未凝固
增加主流道的斜度
使喷嘴和主流道的尺寸相同并对准
减小喷嘴直径
降低主流道粗糙度
提高喷嘴温度
增加主流道冷料穴
延长冷却时间
冷块或僵块1.熔料温度太低、塑化不良
2.混入杂质或不同品种塑料混用
3.喷嘴温度太低
4.无主流道或分流道冷料穴
5.制质量量和注射机最大注射量接近,而成型时
间太短
提高熔料温度并使塑化均匀
除去杂质并使用同种同牌号的料
提高喷嘴温度
设置主流道冷料穴
采用大型注射机,或延长成型周期
制品1.注射机液压系统或电气系统不稳定
2.成型周期不一致
检查液压和电气系统的稳定性
使成型周期均匀一致
编号:ZY-QC-30 制定日:2013-07-29 实施日:2013-07-29 版次:A/0 页码:6 / 6
尺寸不稳定3.浇口太小或不均
4.模具定位杆弯曲或磨损
5.加料量不均
6.制品冷却时间太短
7.温度、压力、时间变更
8.塑料颗粒大小不均
9.回料与新料混合比例不合适
加大浇口尺寸
检查模具定位杆
使每个周期的进料和垫料保持不变
延长制品冷却时间
稳定成型工艺条件
采用颗粒均匀的原料
调整回料与新料的比例
真空泡1.模具温度太低
2.制品壁厚薄悬殊
3.注射时间太短
提高模温
改进制品设计工艺,使之厚薄均匀
延长注射时间
修
订
记
录
年月日修订原因修订内容审核核准
注:1本标准除修订栏外手写及修改无效,经厂部审核核准后发行
2本标准加盖受控文件章后发行。并记录分发部门及人员。
注塑成形作业指导书a
注塑作业指导书 编制部门:生产技术部 审核部门:厂部 确认部门: 实施日期: 执行部门:注塑部操作员 检验部门:注塑主管 一、目的:规范注塑机生产操作,确保人员和机器安全。 二、适用范围:注塑车间 三、执行人:操作工、技术员、班组长 四、操作规程: 4.1准备工作; 1.1、认真查阅上一班操作工的交接记录,了解上一班的生产状况和异常状况, 相互之间进行工作交接; 1.2、认真做好“ 5S ”工作;每天上班前10分钟,首先要整理、清扫自己的 工作场所;把无用的东西扔掉,把有用的东西按照标识整齐有序地排放,擦拭工作台、设备等,保持整洁的工作环境,养成良好的工作习惯; 1.3、交接清点好上班期间所要使用的工具、记录表格、产品标识等; 1.4、在工作期间,各操作员要时清洁、整理、擦拭自己工作区域的卫生1.5、使用、借用后的物品归还原处 4.2生产规程; (开机前必须熟悉注塑制品的加工方法、品质标准、包装要求及注意事项)2.1所有注塑机必须在技术员或班长要求开机生产时方可开机,严禁私自开机
生产。 2.2生产步骤如下:开模时打开安全门→取出产品→检查模腔内有无产品残留及浇口残留→关安全门→加工披锋〃浇口→检查产品质量→包装入箱 2.3生产中检查产品是否有以下明显缺陷:注塑不足、明显缩水、混色、黑点、披锋、顶白、断柱及拉伤等。 2.4操作时,较大产品在台面上至少摆放四模以上,冷却后才能加工/包装 2.5 加工产品时,要轻拿轻放,并将产品外观面朝上摆放在工作台上。 2.6 正确对待品检人员提出的品质要求,产品质量以机位样品为准 2.7 根据“生产通知单”上的包装要求,对产品进行包装入箱摆放。 2.8机位浇口、废品要用袋/箱装好,不同原料或不同颜色的浇口要分开装入不同的袋/箱,不可搞混! 2.9注塑生产过程中,机位操作工不得擅自改变注塑工艺参数。 2.10使用工装夹具时,要按顺序摆放产品,不得随意调整工装夹具的使用状态。 2.11在生产过程中,若发现设备有异常情况,如:设定料筒温度与实际温度不符,模具或其它部位螺丝突然断裂或脱落、异味、异声等,立即按下红色按钮,打开安全门并报告技术员或班长处理 2.12生产过程中,若发现产品或水口未脱离模具时,不要关安全门,待处理脱落后方可生产,模具上要放镶件时,机器安全门状态要绝对良好,镶件要放好,不能因振动脱落而导致进入模具损坏模具 2.13若检查模具或处理冷料时一定将机台打成“手动”状态并关掉油泵,方可工作。 2.14在生产过程中,若遇到浇口连续断裂堵塞时,操作员应在技术员的指导下,处理相关问题
注塑成型作业指导书
一、使用目的:指导注塑成型的规范操作,预防因操作不当造成的各种意外事故。 二、适用范围:适用于注塑操作员在成型作业中的操作指导。 三、操作规程: 1、开机步骤(适用机型:震德JN-M3V系列) 合上电源总闸,合上电控箱右侧空气开关,右旋操作面板下方的红色按钮,控制器电源已接通,通过控制面板将胶筒温度设为“开”状态,此时,料筒加热圈开始加热,待显示器所示实际温度与设定温度相当(时间大约半小时左右),按下“油泵”键,待屏幕“马达启动中”字样消失,同时听到“咔嚓”一声,表示油泵马达已完成启动,关上前安全门,将模具完全闭合,把胶筒内过热的胶料连续对空排射几次,熔胶后,将射台前移至限位,按下“半自动”键,机台即入半自动运行状态。 2、关机步骤(适用机型:震德JN-M3V系列) 关上料斗落料口闸刀,直至胶筒内残胶射完为止,将射台退出至限位,模腔及模芯喷上防锈剂,关上安全门,模具闭合至前后模面刚接触但机铰未完全伸直为宜,按下“油泵”键2秒后,油马达即关闭,将温度设定为“关”状态,按下红色“急停掣”,关闭控制器电源,拉下电控箱右侧空气开关,关闭机台总闸,大约10分钟后关闭冷却水阀,关机完毕。注:如遇长时间停机,应卸下模具,将冷却系统中积水排净。 3、注塑作业流程图 4、操作员在操作机台前的准备工作 1)、应先熟悉机台的性能及操作方法,经过严格的岗前培训。 2)、目视机台机械保险杆位置调节是否适当(保险杆离挡板的距离一般规定为2—4CM),前后安全门开关是否失灵(当任一安全门打开时,机台没有锁模为正常)。 3)、拿好修边刀、斜口钳、包装袋、纸箱(胶框)等必需用品。 4)、了解生产的产品名称、型号、材质、颜色、包装、质量等要求及生产过程中易出现的导常情况。 5、生产中应注意的事项: A、严格按照生产工艺标准进行作业。 1)、取拿产品时,应平衡用力取拿,避免因取拿不当造成掰裂、拉断或碰伤等。 2)、产品修边时,应均匀平稳用力,刀口尽量放平,小心谨慎操作,避免深挖,割
新版注塑作业指导书-新版.pdf
版本号:A/0 注塑车间作业指导书页数:第1页,共2页 序号作业项目作业方法/步骤要点工序标准及不合格处置 1 注塑 1.1作业流程: 配料——干燥——装校模具——加料——打空料——首件注塑——作业自检——首件确 认——批量生产——作业自检——过程巡检—收料摆放——移交检验 1.2注塑作业前的准备: a)开机前应检查设备周围是否有异物,如有则清除杂物; b)开机前应准备注塑作业必需的工、用具; c)开机前应设备加油:滑动件加45#机油:轴承座加黄油; d)开机前应检查设备螺母是否松动,如有松动,适当紧固; e)开机前应检查注塑机的水路、油路、电路是否正常 f)开机后应观察设备有无异常现象; 1.3装校模具要点: a)依据订单要求选择合适的模具; b)用合适的螺丝将模具安装在注塑机的适当位置; c)接通模具的冷却水; d)调整注塑机的动模板,将模具打开,观察模具的顶出机构是否正常; e)装模后,检查模具的开、合模动作是否正常; f)检查注塑机的压力表,检查锁模力是否足够; 1.4注塑作业要点: a)领注塑的半成品料时,应检查待注塑的半成品是否符合生产通知单要求;1.1注塑工序检验标准: 1.1.1注塑功能: a)选用注塑料粉必须符合生产通知单 要求; b)注塑后,产品颜色必须与样板或生 产通知单一致; c)注塑后,产品外形及尺寸必须与样 板或生产通知单一致; d)注塑后,产品收缩率必须符合样板 要求; 1.1.2注塑外观: a)产品注塑后,外观应光洁。不可有 明显披锋、毛刺; b)产品注塑后,外观应平整。不可有 水纹、拖花、凹陷; c)产品注塑后,外观应完整,不可有 填充不满或裂纹; d)产品注塑后,外观应密实,不可有 气泡、凸点。 1.1.3注塑数量: a)注塑数量应符合生产通知单要求。不可有不够数或者严重多数。 编制QMS小组审核李振品审批曾纪硕
注塑机维修保养作业指导书
1.目的: 为保障注塑成型机设备正常状态 2.适用范围: 注塑厂成型机 3.权责: 保养维护:注塑成型车间;机修组 4.定义:无 5.作业内容: 5.1日常点检: 5.1.1机台,工作台灰尘,杂物清理 5.1.2检查马达运行状况,是否有异味,异响 5.1.3检查电热是否正常,射咀是否漏胶 5.1.4检查润滑是否正常,润滑油机油位是否正常
5.1.5安全门防护是否正常 5.1.6紧急停止,安全踏板是否正常 5.1.7开关模是否异响 6.1一级保养: 6.1.1检视液油量表,液压油清洁度,油温(37℃~50℃之间) 6.1.2检视润滑油、液压油、动作压力、清洁度. 6.1.3安全部位之功能. 6.1.3.1前后安全门 6.1.3.2安全门动作之开关之功能是否有效 6.1.3.3急停电源开关之功能是否有效 6.1.3.4机械止动棒是否有效 6.1.3.5油压安全阀门 6.1.3.6附加设备安全功能(安全踏板) 6.1.4冷却水之温度、流量、清洁度、水压等 6.1.5料管动作情形 6.1.5.1加温状态 6.1.5.2安全防护,保护罩固定
6.1.5.3高温电线整理,感温线整理, 6.1.6润滑面,挤压摩擦面之目视检查润滑油剂的供应情形: 6.1.6.1曲手(注意润滑油管不可有压断情形堵塞) 6.1.6.2哥林柱是否润滑 6.1.6.3滑道是否干磨 6.2二级保养: 6.2.1打黄油(并注意进油情形) 6.2.2检查松动情形 6.2.2.1射胶油缸,料管组合 6.2.2.2哥林柱,曲手组合 6.2.2.3电箱内电子零件及电线 6.2.3执行每个月大保养之工作记录 6.2.3.1运行时间 6.2.3.2执行人员 6.2.3.3配合设备、工具、保养方式 6.2.3.4工程进度 6.2.3.5改善检讨
注塑拌料作业指导书—范文
注塑拌料作业指导书—范文 一、目的: 规范注塑水口料和色粉的拌料作业,防止所拌材料性能、颜色无法达到生产要求。 二、适用范围: 注塑车间内所有拌料作业 三、责任者: 加料、拌料员 四、作业准备: 4.1 准备好作业工具:酒精(抹机水),干净碎布; 4.2 《注塑生产工令单》,生产所需原料,水口料,色粉。 五、作业内容: 5.1 水口料的拌料 5.1.1依照《注塑生产工令单》准备好生产所需原料,水口料; 5.1.2作业前务必切断搅拌机的主电源; 5.1.3打开搅拌机上盖,把搅拌机里剩余的料清理干净; 5.1.4用干净的碎布粘少许酒精(抹机水)将搅拌机内壁粘附的色粉
等擦拭干净; 5.1.5依照《注塑生产工令单》称好所需原料,按水口料拌料配比称好所需水口料; 5.1.6再次确认所加原料与工令单相符后把原料加进搅拌机里,加料前务必确认放料口开关处于关闭状态,加料时不可将料粒洒在地面上,一次拌料须适当,不可太满或太少; 5.1.7盖好搅拌机上盖,接通搅拌机的主电源,设定好搅拌机运转速度,预定搅拌时间,启动电机使其正常工作; 5.1.8待搅拌定时到后,用干净的料袋放出并做好标识; 5.1.9记录所拌原材料于《注塑拌料记录表》上,搞好工作区域5S。5.2色粉的搅拌 5.2.1依照《注塑生产工令单》准备好生产所需原料,色粉; 5.2.2作业前务必切断搅拌机的主电源; 5.2.3打开搅拌机上盖,把搅拌机里剩余的料清理干净; 5.2.4用干净的碎布粘少许酒精(抹机水)将搅拌机内壁粘附的色粉等擦拭干净; 5.2.5依照《注塑生产工令单》称好所需原料,按色粉配比要求称准所需色粉; 5.2.6再次确认所加原料、色粉与工令单相符后先把原料加进搅拌机里(加料前务必确认放料口开关处于关闭状态),再将称好的色粉均匀的倒在原料上; 5.2.7盖好搅拌机上盖,接通搅拌机的主电源,设定好搅拌机运转速
注塑烘料作业指导书
注塑烘料作业指导书 (ISO9001-2015) 一、目的 指导烘料的规范操作,确保烘料质量,预防烘料作业中带来的各种意外事故。 二、适用范围: 此规定用于烘料人员在烘料作业中的操作指导。 三、烘料程序及注意事项 烘料人员上岗前必须经过严格的岗前培训,熟悉材料类别和各产品使用的颜色、材质及各种材料的干燥温度及干燥周期。熟练掌握换料、换色的操作须知及操作步骤。 A、烘料前的准备工作 1、烘干室内清理 松开后钮,将烘干室与集尘室分解打开,取出孔屏分离器及护屏分离器,分别用高压气枪进行清理,加热筒内不易清理到的粉末,可开动风机将其吹出,气枪清理完毕后,还必须用干净抹布对各部件进行清擦(如遇较难清擦的色渍时,可使用少许白矿油先清擦一遍)。 2、预热料桶 当干燥室各部件清理干净后,将干燥室组装好(组装时请特别注意把上环、下环(密封圈)装好,如漏风将严重影响干燥效果)。 B、填料烘干 1、温度调节
参考“塑料原料干燥温度参考表”结合实际经验,酌情调节电子温控仪,使双金属温度计反应的温度与实际温度相符。 2、风量调节 风量之调节关系干燥效果甚大,一般以全部开放时效果最好,如遇料桶内存料不多时或需较高温度时,可酌情调小风量,减小热量损耗,否则不能达到预期的干燥效果。 3、原料填桶 原料填加时,要确保“满桶”,即桶内原料填量不少于总装料量的70%,以免干燥效果不匀或使干燥时间过长。 4、透明原料的干燥 透明料干燥时,必须在进风口装置空气过滤器“原海棉”等,防止空气中灰尘进入。 四、烘干机的维护与保养 1、进风口过滤器要经常清洗,当过滤器阻塞时,进风量减少,将影响干燥效果。 2、在干燥过程中,粉末物质落入料斗、加热筒,日久淤积,因此需要定期清除(尤其对于长期不换料、不换色的干燥机非常必要)。 3、如遇温度过高,原料在护屏上结块时,原料不能下落,此时严禁用铁棒等硬物铲刮,以防护屏孔分离器受损,应将料桶先分解开,取出妥善处理。 4、在关闭电热后十分钟,再关风机,以确保电热筒充分冷却,延长其使用寿命。 5、在烘干过程中,必须经常巡视干燥机的工作状况,若存在异常应立即停机整修,待故障排除后再开启使用。 五、塑料原料干燥温度参考表
注塑成型机的安全操作规程(2021版)
注塑成型机的安全操作规程 (2021版) The safety operation procedure is a very detailed operation description of the work content in the form of work flow, and each action is described in words. ( 安全管理 ) 单位:______________________ 姓名:______________________ 日期:______________________ 编号:YK-AQ-0062
注塑成型机的安全操作规程(2021版) 1.目的:为了避免技术人员在使用注塑机过程中,因操作不当而发生安全事故. 2.范围:昭和公司的所有注塑机的操作过程. 3.职责: 3.1技术员:按照注塑机安全操作规程点检和使用注塑机. 3.2操作员:在工作中严格遵守注塑机安全操作规程. 3.3技术员有责任协助副领班安全工作的进行. 4.定义:无 5.程序: 5.1岗前培训. 5.1.1成型技术员和操作工必须经过岗前培训,直至合格后方可操作注塑机.
5.1.2未经培训人员,严禁操作注塑机. 5.2开机前应注意事项. 5.2.1进入工作岗位必须把工作服、工作帽、工作鞋手套等劳保用品穿戴整齐,完备. 5.2.2节假日后第一班开机时,要用试电笔检查设备有否漏电, 检查冷却水系统是否堵塞和 滴漏. 5.2.3检查注塑机有无漏油,保持注塑机及其四周环境清洁整齐,无油污、无原料颗粒. 5.2.4检查紧急停机按钮是否失灵,机械式安全杆的位置是否生效. 5.2.5检查前后安全门安全咭掣是否失灵. 5.2.6车间严禁吸烟,火枪严禁在易燃、易爆物旁边使用,以免造成火灾. 5.3安装模具应注意事项. 5.3.1安装模具时,必须要戴安全帽、穿安全鞋.
注塑作业指导书
注塑作业指导书 编制部门:拓进技术与品管部 审核部门: 确认部门: 实施日期: 执行部门:注塑组操作员 检验部门:注塑主管 一、目的:规范注塑机操作,确保人员和机台安全。 二、适用范围:注塑车间 三、责任者:操作工、技术员、班组长 四、准备工作: 4.1、认真查阅上一班操作员的交接记录,了解上一班的生产状况和异常状况,相互之间进行工作交接; 4.2、认真做好“ 5S ”工作;每天上班前10分钟,首先要整理、清扫自己的工作场所;把无用的东西扔掉,把有用的东西按照标识整齐有序地排放,擦拭工作台、设备等,保持整洁的工作环境,养成良好的工作习惯; 4.3、交接清点好上班期间所要使用的工具、表格记录、物品等; 4.4、在工作期间,各操作员随时清洁、整理、擦拭自己工作区域的卫生; 4.5、使用、借用后的物品归还原处; 五、内容:
5.1:机台操作 5.1.1.交接班时,先检查机台、落产品时槽等“5S”项目是否合格,工具、是否齐全、完整。 5.1.2.所有注塑机必须在技术员或班长要求开机生产时方可开机,严禁私自开机生产。 5.1.3.在生产过程中,若发现设备有异常情况,如:设定料筒温度与实际温度不符,模具或其它部位螺丝突然断裂或脱落、异味、异声等,立即按下红色按钮,打开安全门并报 告技术员或班长处理 5.1.4.生产过程中,若发现产品或水口未脱离模具时,不要关安全门,待处理脱落后方可生产,在往模具上扣镶件时,机台要打成手动状态,镶年要扣好,不能因振动脱落而导致进入模具损坏模具 5.1.5. 若检查模具或处理冷料时一定将机台打成“手动”状态并关掉油泵,方可工作。 5.1. 6.在生产过程中,若遇到胶口料连续断裂堵塞时,操作员应在技术员的指导下,处理相关问题 5.1.7.操作员不得私自调机。 5.1.8. 暂时离开机台时,先将模具合成相距3-5mm,关掉油泵后方可离开。 5.2: 检查产品: 5.2.1.严格按HC-600单片目测检验标准要求进行 5.2.2.生产过程中,突然发现产品品质异常,立即停机,报告
注塑成型机安全操作规程
注塑成型机安全操作规定 1. 目的: 为了避免技术人员在使用注塑机过程中,因操作不当而发生安全事故. 2. 范围: 公司的所有注塑机的操作过程. 3. 职责: 3.1 技术员:按照注塑机安全操作规程点检和使用注塑机. 3.2 操作员:在工作中严格遵守注塑机安全操作规程. 3.3 技术员有责任协助副领班安全工作的进行. 4. 定义: 无 5. 程序: 5.1 岗前培训. 5.1.1 成型技术员和操作工必须经过岗前培训,直至合格后方可操作注塑机. 5.1.2 未经培训人员,严禁操作注塑机. 5.2 开机前应注意事项. 5.2.1 进入工作岗位必须把工作服、工作帽、工作鞋手套等劳保用品穿戴整齐,完备. 5.2.2 节假日后第一班开机时,要用试电笔检查设备有否漏电,检查冷却水系统是否堵塞和滴漏. 5.2.3 检查注塑机有无漏油,保持注塑机及其四周环境清洁整齐,无油污、无原
料颗粒. 5.2.4 检查紧急停机按钮是否失灵,机械式安全杆的位置是否生效. 5.2.5 检查前后安全门安全咭掣是否失灵. 5.2.6 车间严禁吸烟,火枪严禁在易燃、易爆物旁边使用,以免造成火灾. 5.3 安装模具应注意事项. 5.3.1 安装模具时,必须要戴安全帽、穿安全鞋. 5.3.2 模具安装前,先检查定位套与定位孔是否配合合适,在吊装模具前要检查纲缆,吊环有无隐患,确认无误后方可使用,做到设备周围无障碍物. 5.3.3 安装模具时严防撞击设备,吊装时,使用天车要有专人负责,相互配合确保安全.人不可站在天车和模具正下方(保持1米距离),入定位孔后,用点动缓慢闭模,调整其它部位直至合适为止.严禁把注塑机一起吊起而损坏吊车和发生危险. 5.3.4 行程的调节要事先量好,行程尺寸要准,同时进行合模力的调整与操作. 5.3.5 在装卸码仔和水咀、水管时,一定要关掉马达,装模温机时,温度超过80℃要用耐高温水管. 5.3.6 平时应对油温机、水温机的水管及高压油管抽蕊模具上的油管进行检查,如有老化及时更换,以免爆裂伤及他人. 5.3.7 新设备、新模具试机试模,要有专人负责,按设备说明书和图纸的规定说明并按事先拟定的方案进行. 5.3.8 在生产前或生产中应对特殊模具的保护装置进行点检,确认看维护装置是否起到保护作用!以避免模具的损坏. 5.3.9 清理料筒时,应把射咀调到最适当和较高的温度,使射咀保持通畅,再使
注塑机作业指导书36830
永康银泰工贸 作 业 指 导 书 工序名称 注塑 文件编号:YT-GY-ZS01-2015 设 备 博创BT 型注塑机 版本:A0 共 2 页 第 1 页 工序示图:表1 注塑时注塑机各加热区段温度:(±15℃) 表2 塑料烘箱参数: 塑料名称 温度℃ 时间h PA66-GF30 110 4~6 区段 射嘴 温区1 温区2 温区3 温区4 温度 320℃ 290℃ 285℃ 280℃ 表3 注塑时注塑机各过程控制:(±5%、±10bar 、±15mm ) 锁 模 开模 射胶 溶胶 冷却计时 部位名称 合模启动 快速合模 低压锁模 高压锁模 高压开模 快速开模 慢速开模 减速开模 注射一段 注射二段 注射三段 保压 塑化 后防涎 10s 速度 % 30 50 25 85 35 35 30 15 75 75 75 15 80 50 压力 bar 50 40 35 120 80 55 40 30 70 85 80 50 80 50 终止位置 mm 250 140 80 5 60 150 180 230 100 40 10 \ 100 120 NO 工步 对象 方式 方法 1 检查 注塑机 点检 按《设备点检卡》的要求操作 目视 检查设备工作参数(如表3,具体参考附件) 模具 目视 检查模腔:无废料、清洁、无异常 注塑料 目视 检查注塑料:无杂质、清洁、干燥 量具 注塑件定型后的尺寸检验 2 加热/升温 温度 设定各区温度,开机加热(如表1) 3 调试 ·合格的模具 ·注塑料 ·注塑机 目视 ·当温度达到所规定温度后,启动螺杆进行溶胶,试射一段,清除残料,观察射出的塑料是否完全塑化 ·启动马达,完成锁模;待塑料塑化完成后,射台前进到位,再进行开模操作; ·试模:将注塑机由手动调成半自动\自动,关好门,启动开始试模,检查注塑机的工作情况,查看成品件的饱满情况,试做2~3模正常后开始进行生产作业
海天注塑机操作规程
1)设有的安全保护装置:有熔断器、热继电器和空气开关等电器元件,为保护电器过载,也就是保护注塑机过载。 急停按钮,当注塑机发生故障或涉及人生安全时,按急停铵钮,注塑机立即停机。报警装置:有报警灯和蜂鸣器,显示屏能显示注塑机当时故障的报警内容。如料温偏差,油温偏差,全程未按时完成,托模进退没有到终位,储料未定时完成,润滑检出失败等等。例显示屏显示射出监控失败,报警灯闪烁,蜂鸣器响,这时必须将半自动转换到手动,报警停止等待排除故障,排除故障后转换到半自动即投入正常生产。射出监控失败,就是注射不到位,造成原因有储料量过多,料温或模温过低,注射压力低或速度慢,喷嘴头堵塞等原因,通过分析即能排除故障。 当开冷车时,在手动工况下如实际料温不在设定的温度范围内,偏高或偏低,此时按预塑和注射触膜键,就无预塑和注射动作,(是有注塑机电脑内已设定保护参数起作用)防止开冷车或喷料。
2) 对人的安全保护和防护装置:有机械保护即锁模安全装置,在移动模板上装锁定螺母来固定保险杆,固定模板上 装档板和保险杆罩。当安全门打开,移动模板后移开模,保险杆从保险杆罩内移出,档板落下,如在安全门打开时其它闭模装置失灵,移动模板闭合时,保险杆随移动模板前进,很快保险杆就撞在档板上,阻止移动模板闭合,保护了操作人员取制品的手等。电器安全装置,急停按纽安装在电脑操作显示面板下面和对面防护罩上,各一只急停按钮。当注塑机发生故障或危及人身安全时,按急停按钮,即关油泵电机,停止所有工作动作,起紧急保护 作用。 行程 开关 装在主辅 操作面固定模板上端各一只。在主 操作 面移 动模板下端机架上装一只行程开关。三只行程开关起连锁保护作用,将主辅操作规程面的二扇安全门关上,三只行程开关动作,移动模板闭合。这要任一扇安全门不关上,即有一只行程开关不动作,闭模电源不接通,注塑机不会合模,达到合模保护作用。液压保护装置在主辅操作面的二扇安全门下装有连动杆,在连动杆处,辅操作面安全门下的机架上装一只二位二通液压伐,当二扇安全门关上,连动杆脱开安全门,液压伐打开,控制压力油接通闭模电液伐,这时才能闭模。当其中任一扇安全门不打开,都不能闭模。 总之:机械、电器和液压三项措施保护闭模,这要其中有一项安全措施不失灵,就能控制不闭模,保护操作 工在开模工况下取制品时不伤及人身。防护罩是防止注塑机移动部位不受外物掉落进去损坏设备和防止操作工不 1、2:锁紧螺母 3:机械保险杆 4:保险挡板 机械安全装置图
注塑成型作业指导书
企业行政培训系列 注塑成型作业指导书 编制:行政部 批准:张三丰 实施:2018-10-31 文件编号:WEL-B10/A1-2018 编号: WEL-B10/A1-2018 XX I 口限责任 限责任公 注塑成型作业指导书xx
1. 初始开机时,应打开水冷系统,再打开电脑,开启电热,然后升温,(升温温度不得超过165C,正常运行时,可根据塑化状态相应提高温度,但不得超过230C),升温时,先打开电热开关、一段165C、二段170C、三段175C、四段180C,炉嘴升温50%,升温1小时,方可开机进行生产。中途停机再开机,保温应在120°C —160°C之间。 2. 启动液压马达,负荷电流不得超过25安培。进行手动操作,正常后,进行全自动运行。运行两 周期正常后,可开机 3. 当运行中出现突发故障时(程序运行),可启用急停开关,在各部位复位后恢复急停开关,可进入 循环作业。 4. 在运行中调节重量或修理模具时,必须停止油泵,方能进行操作。 5. 在运行中出现主机超负荷运行时,必须停止主机和一切设备,排出故障后方能开机。 6. 正常运行时必须保证料斗里不断料;同时不准有带水分物质进入料斗,更不准有铁屑、杂质等掺入。 7. 循环运行中,应以最快速度取出成品,不能影响下一循环作业和延长操作时间。 8. 制品应修削平整,不准有刀子划破现象,提手部位应不刺手。 9. 在机组运行时进行维修,必须有两人在场,并有专业技术人员进行指挥。 10. 停机时应先停止电热,关闭冷却系统,待取出制品后停止油泵电机,最后关闭电源。 11. 停止水泵,作好原始记录,搞好车间卫生。 行政部 2018 年10月31号 第2页共2页
注塑机作业指导书
十堰达峰软轴有限公司 作 业 指 导 书 工序名称 注塑 文件编号:DAFJ02-03.11 设 备 130T 注塑机 版本:A0 共 2 页 第 1 页 工序示图:表1 PA66-GF30料注塑时注塑机各加热区段温度:(±15℃) 表2 塑料烘箱参数: 塑料名称 温度℃ 时间h PA66-GF30 110 4~6 区段 射嘴 温区1 温区2 温区3 温区4 温度 320℃ 290℃ 285℃ 280℃ 表3 PA66-GF30料注塑时注塑机各过程控制:(±5%、±10bar 、±15mm ) 锁 模 开模 射胶 溶胶 冷却计时 部位名称 合模启动 快速合模 低压锁模 高压锁模 高压开模 快速开模 慢速开模 减速开模 注射一段 注射二段 注射三段 保压 塑化 后防涎 10s 速度 % 30 50 25 85 35 35 30 15 75 75 75 15 80 50 压力 bar 50 40 35 120 80 55 40 30 70 85 80 50 80 50 终止位置 mm 250 140 80 5 60 150 180 230 100 40 10 \ 100 120 NO 工步 对象 方式 方法 1 检查 注塑机 点检 按《设备点检卡》的要求操作 目视 检查设备工作参数(如表3,具体参考附件) 模具 目视 检查模腔:无废料、清洁、无异常 注塑料 目视 检查注塑料:无杂质、清洁、干燥 量具 注塑件定型后的尺寸检验 2 加热/升温 温度 设定各区温度,开机加热(如表1) 3 调试 ·合格的模具 ·注塑料 ·注塑机 目视 ·当温度达到所规定温度后,启动螺杆进行溶胶,试射一段,清除残料,观察射出的塑料是否完全塑化 ·启动马达,完成锁模;待塑料塑化完成后,射台前进到位,再进行开模操作; ·试模:将注塑机由手动调成半自动\自动,关好门,启动开始试模,检查注塑机的工作情况,查看成品件的饱满情况,试做2~3模正常后开始进行生产作业
注塑成型作业指导书
编号:ZY-QC-30 制定日:2013-07-29 实施日:2013-07-29 版次:A/0 页码:1 / 6 注塑成型作业指导书 一.注塑成型的原理: 1.注塑成型:指将注射用的置于能加热的料筒内,受热、塑化,再施加压力,使熔体塑料注入到所需形状的模具中,经过 冷却定型后脱模,得到所需形状的制品。 2.注塑成型三要素:注塑机、模具、原料 3.注塑成型条件五大要素:压力-时间-速度-位置-温度。 二.注塑机: .注射机的结构: a.注射系统:主要使塑料塑化和使熔体塑料注入模具功能 b.合模系统:主要模具的开模、锁模、调模、顶出功能 c.传动系统:主要控制注射机的动作能力。如油压阀、电动机 d.电气控制系统:主要注射机内部电路、开关、电路板 3.注射机的操作: a.打开注射机总电源及各开关,旋开紧急停止键 b.按下操作板上马达启动键与电热键,开启马达与料筒温度(按1次左上角灯亮为开启,再按1次左上角灯灭为停止) c.选用操作方式 c-2手动:选用此方式时操作板上的相应开关,只在按下时作相应动作,手指放开即停止 c-3半自动:选用此方式时,只需按动两合模开关即可完成,合模,锁模,射胶,保压。冷却,开模一系列动作。 d.开关模动作设定:开模一般设定为慢快慢,关模一般设定为快速低压低速高压锁模。低压压 力最大不可以大于15kg/cm2低压与高压之间位置不可大2mm, 快速与低压间位置一般在50mm e.成型温度设定:根据各种原料成型所需温度设定,在改变设定温度时一次不可超过5°,加料段温度比熔融段温度最少要低10°, 待机器上显示实际温度达到设定温度时,在改变设定温度时一次不可超过5°再过二十分钟才可进 行熔胶,射出射退动作。 f.射出/保压的设定: 射出设定分多段和一段,根据制品质量所需设定,能使用高速尽量使用高速,射满成型制品95%左右即转 换保压。在需加速加压和位置时间时一次不能超过5KG和2%,第一模产品不可超过产品的70%,防止产品 粘模。保压切换分时间切换:当射出动作达到设定射出时间时立即转换保压。在生产停机10分钟以上后再 开机时必须现降压力30%后开始慢满恢复原成型参数。 位置切换:在射定的时间内,注射至所设定的位置,即转换保压或在注射未达到设定位置,设定时到也会立即转换保压。 压力切换:当注射压力达到设定值或射到设定时间后即转换为保压 保压的设定:根据成型制品的质量所需设定相应的压力及时间 h.背压的设定: 根据制品所需定,一般以空射储料,射咀有少量胶料流出螺杆位置又能后退为原则,背压最大不可超过30kg/cm2
注塑机操作作业指导书
文件编号 页次1/1 文件名称 注塑机操作作业指导书制定部门注塑课作业指导书制定日期2010-11-27 1.目的: 安全使用注塑机 2.范围: 注塑机器。 3内容: 3.1 操作步骤:打开电源,打开电热开关设定参数; 安装模具,驳接水; 清洁模腔,调校开/锁模; 清洁料斗及炮 筒,后上料及胶料干燥; 注射参数的设定及产品自检. 模具执行工艺员装模工工艺员上料工工艺员确认——装模组长—工艺员——普通模具应以碎布擦干净模腔,型芯和顶针上的油污,必要时可使用清洗剂以及风枪等工具. 清洁模具镜面部分应以脱脂棉加洗模水清洗,不可用碎布擦拭镜面部分. 模厚调节:根据模具的厚度设定模厚数据进行自动或手动调节. 3.2 锁模力调节: —根据产品的投影面积(含浇口)及材料的种类设定锁模力进行自动或手动调节.根据模具 结构要求,部分须调校回针保护. 出芯位置:分开模前,开模途中,开模终止三种. 入芯位置:分锁模前,锁模途中,锁模终止三种. 抽芯分时间及行程控制两种抽芯,具体根据产品生产安全情况选择使用. 料筒温度: 料筒温度根据不同胶料的熔融指数要求设定,以保证胶料塑化良好能顺利充模. 3.3 胶料干燥温度:时间根据不同种类的胶料及其吸水性而设定. 3.4 模温:模具温度的设定应考虑聚合物性质,制品大小形状,模具结构,浇道系统及环境温度等而设定. 3.5 压力:根据制件的形状厚薄不同,选用的注射压力也相应不同,制件不缩水为宜. 3.6保压:保压时间长短与料温有直接关系,熔料温度高,浇口封闭时间长,保压时间长.反之,保压时间短. 保压时间又因产品投影面积及壁厚而不同,在背压参与的情况下,胶料塑化效果好 3.7背压:背压压力越大, 排除塑料中各种气体的力量越大, 有利减少银纹和气泡等. 但过大的背压又使 模塑周期加长, 不利于提高生产效率, 同时也会产生较高的内热. 螺杆转速可影响胶料在螺槽中输送和塑化的热压程度及剪切效应,因此它是影响塑化能力,塑化质量和成型周期等因素的重要参数. 3.8 螺杆:螺杆转速越高塑化能力越强,但增加熔料温度的不均匀,熔体温度升高,物料转速产生分解,炭化等, 胶料排气有影响; 3.9冷却冷却时间根据成形品厚度,融化树脂温度,金属模具温度以及热传导率等的树脂固有值时间来决 定. 计量完位置由决定射出充填量的成形品重量决定 4.参数管理 4.1.试产利用试验设计优选参数. 试产完成后,将参数填写于工艺卡.工艺卡经工艺工程师和注塑主管确认 后,由工艺工程师存档保存 核准审查拟案版本修订内容修订日期符号 版本号 1 A 2 修改号 3 0 4
注塑换模作业指导书
注塑换模作业指导书 (ISO9001-2015) 一、目的 指导注塑换模的规范操作及设备的合理使用、维护,预防操作过程中的各种意外事故。 二、适用范围: 本规定用于注塑领班在换模中的操作指导。 三、换模程序及注意事项: A、领班接主管签发的《换模指令单》后的准备工作。 1、将待产模从模具存放区调出进行全面检查,检查项目包括:型腔、分型面有无生锈或粘有残料,导柱、导柱套是否磨损、变形、配合是否紧密,弹簧是否疲劳、断裂,顶针是否折断或缺少,滑块是否灵活,冷却水道是否畅通,水咀是否安装配套。 B、开始换模 1、关上料桶闸刀,当胶筒余料用完后退出座台,如需要更换材料或颜色应将料桶余料放出,并对料桶、胶筒进行清理,待清理干净后再加入新料。 2、卸模:用抹布将模具分型面拭擦干净,前后模喷上防锈剂,闭合模具,装上吊环,用行车吊钩可靠套牢,松开模具夹板,将机台设定为调试状态,慢速打开机台动模板,同时,注意模具状态,将模具吊高到适当位置(便于拆除水管),关闭冷却水阀,用螺丝刀松开水管锁箍,拔脱水管,再将模具吊起移至无人安全区放下。
3、装模:用量具测量待装模厚度,输入电脑,启动自动调模功能进行粗调模,同时将待产模装上吊环,用葫芦钩套牢,拉动葫芦链条上升模具,上升至适当高度平移至机台装模区上方,对准中心慢速下降,操作中应谨慎小心,避免撞伤机台哥林柱,当下降到适当位置,将模具衬套套上定位铁圈,对准机台前板中心孔,移动行车,使模具紧贴机台前板,闭合机台动模板,关闭机台马达,开始安装夹板,前后模两边各不得少于四块夹板,螺母锁定确认可靠夹紧模具后,取掉行车吊钩,将前后模冷却水接好(注意水管一进一出为一组,接好后打开水阀观察是否有漏水现象,启动马达,打开模具用抹布清擦分型面(清擦时注意不要将模腔光面弄花)。 4、调试 1)对模具厚度进行精调整,根据模具制品投影面积适当调整锁模力,一般电脑参数设定选择50—85范围之间为宜,锁模力设定不宜过大,正常情况下以保证产品不溢边为基准。 2)如指令要求使用的原料与现用材料不同,清洗料筒后应根据新材料工艺重新设定胶筒温度。 3)调整开模终止位置,以便于取拿产品为宜,各段闭、合模压力、速度视情况而设定,应考虑开、闭模动作运行中机台的平稳度。闭模时模具导柱对套导、回位针对前模分型面,滑块导柱对滑块导孔等之间的撞击、摩擦,尤其是滑块部分,闭模过快,易导致滑块导柱变形或严重磨损,开模过快,由于受导柱拉力惯性作用,当完全脱离导柱后,滑块继续滑动而脱离定位钢珠,极易导致下一模滑块压坏。
注塑烘料作业指导书
光华电子工贸有限公司 一、使用目的:指导烘料的规范操作,确保烘料质量,预防烘料作业中带来的各种意外事故。 二、适用范围:此规定用于烘料人员在烘料作业中的操作指导。 三、烘料程序及注意事项 烘料人员上岗前必须经过严格的岗前培训,熟悉材料类别和各产品使用的颜色、材质及各种材料的干燥温度及干燥周期。熟练掌握换料、换色的操作须知及操作步骤。 A、烘料前的准备工作 1、烘干室内清理 松开后钮,将烘干室与集尘室分解打开,取出孔屏分离器及护屏分离器,分别用高压气枪进行清理,加热筒内不易清理到的粉末,可开动风机将其吹出,气枪清理完毕后,还必须用干净抹布对各部件进行清擦(如遇较难清擦的色渍时,可使用少许白矿油先清擦一遍)。 2、预热料桶 当干燥室各部件清理干净后,将干燥室组装好(组装时请特别注意把上环、下环(密封圈)装好,如漏风将严重影响干燥效果)。 B、填料烘干 1、温度调节 参考“塑料原料干燥温度参考表”结合实际经验,酌情调节电子温控仪,使双金属温度计反应的温度与实际温度相符。 2、风量调节 风量之调节关系干燥效果甚大,一般以全部开放时效果最好,如遇料桶内存料不多时或需较高温度时,可酌情调小风量,减小热量损耗,否则不能达到预期的干燥效果。 3、原料填桶 原料填加时,要确保“满桶”,即桶内原料填量不少于总装料量的70%,以免干燥效果不匀或使干燥时间过长。 4、透明原料的干燥 透明料干燥时,必须在进风口装置空气过滤器“原海棉”等,防止空气中灰尘进入。 四、烘干机的维护与保养 1、进风口过滤器要经常清洗,当过滤器阻塞时,进风量减少,将影响干燥效果。 2、在干燥过程中,粉末物质落入料斗、加热筒,日久淤积,因此需要定期清除(尤其对于长期 不换料、不换色的干燥机非常必要)。 3、如遇温度过高,原料在护屏上结块时,原料不能下落,此时严禁用铁棒等硬物铲刮,以防护 屏孔分离器受损,应将料桶先分解开,取出妥善处理。 4、在关闭电热后十分钟,再关风机,以确保电热筒充分冷却,延长其使用寿命。 5、在烘干过程中,必须经常巡视干燥机的工作状况,若存在异常应立即停机整修,待故障排除 后再开启使用。 编制: 审核: 批准:
注塑工序作业指导书
一、注塑机操作工职责 ①认真学习设备使用说明书,应了解注塑的结构组成及各部位主要零部件的功能作用。 ②经过培训后,操作工应牢记注塑机生产操作规定和操作程序,经实际操作考核后,合格者才可以独立进行生产操作。 ③注塑机生产操作工应能及时发现生产中的设备故障和注塑制品的质量问题,并能找出设备故障原因和影响制品质量的原因,及时排除解决。 ④知道怎样对设备进行维护保养。 ⑤生产操作工作中,如发生较重大故障和设备事故时,要及时向车间有关人员报告,并能说明设备故障现象及发生的可能原因。 ⑥不经车间领导批准,任何人不允许随意操作使用归操作者负责的设备,设备操作者有权制止。经车间领导同意的其他人对设备进行操作时,该设备操作工应在一旁监护其操作。 ⑦设备上的生产工具及附属零部件应由设备操作工保管,不允许随意乱堆。若发生丢失或损坏现象,操作工应负保管失职责任。 ⑧不允许以任何理由或借口,做出容易造成人身伤害或损坏设备的操作方式。 二、注塑机生产操作注意事项 ①上岗生产前要穿好车间规定的安全防护服装。 ②清理设备周围工作环境,不许存放任何与生产无关的物品。 ③清理设备工作台,注射座滑动导轨和加料斗上方处不许放任何物品;注意检查料斗台,注射座滑动导轨和加料斗上方处不许存放任何物品;注意检查料斗内,不许有任何异物落人料斗内。
④检查注塑机上的安全防护设施装置,应无损坏,并试验其工作可靠性。 ⑤检查各部位坚固螺母有无松动。 ⑥开车前各润滑部位要注满润滑油,在开车生产过程中,要2-3h 检查一次各部位润滑情况,随时补充加足润滑油(脂)。 ⑦发现设备上零部件工作出现导常或有损坏现象不能再开车生产时,应及时向车间有关人员报告,不能自行处理,并做好记录。 ⑧设备上的安全防护装置不准随便移动,更不允许改装或故意使其失去作用。 ⑨对已发现有问题的设备,未经维修排除故障之前,不允许开车生产使用。 ⑩经常检查液压油的质量和油量,保持液压油的油量在油箱中的油标显示范围内,液压油面接近油标低位时,要适当补加油量。液压油工作1年时应按油质状况考虑更换新油。 ⑾经常检测液压传动系统工作时液压油温度的变化,当液压油开始出现温度升高时要加大液压油冷却水的流量。 ⑿试模生产、对空注射熔料时,喷嘴前方不许站人。 ⒁操作者因故需要暂时离开机台时,应切断电源。 ⒂如遇有突然停电或意外事故停机时,若机筒内塑化注射原料是聚氯乙烯料,应立即拆卸喷嘴、螺杆,把机筒喷嘴内余料除净;若是聚乙烯、聚丙烯等聚烯烃类原料,可不必清除,待故障排除或恢复供电时,机筒、喷嘴重新加热升温,等机筒内料温达到注射要求时再开始启动螺杆工作。 ⒃对于合模部位的安全防护装置,接班生产前应试验检查其工作的可靠性。
注塑成型作业指导书
注塑成型作业指导书 一.注塑成型的原理: 1.注塑成型:指將注射用的置於能加熱的料筒內,受熱、塑化,再施加壓力,使熔體塑料注入到所需形 狀的模具中,經過冷卻定型後脫模,得到所需形狀的制品。 2.注塑成型三要素:注塑機、模具、原料 3.注塑成型条件五大要素:压力-时间-速度-位置-温度。 二.注塑機: 1.注塑機的種類: a.按塑化方式分柱塞式和螺桿式 b.按傳動方式分液壓式、機械式、液壓機械式 c.按外型分臥式、立式、角式 目前我們公司使用的注射機為臥式、螺桿塑化、液壓傳動式注射機。 2.注射機的結構: a.注射系統:主要使塑料塑化和使熔體塑料注入模具功能 b.合模系統:主要模具的開模、鎖模、調模、頂出功能 c.傳動系統:主要控制注射機的動作能力。如油壓閥、電動機 d.電氣控制系統:主要注射機內部電路、開關、電路板 3.注射機的操作: a.打開注射機總電源及各開關,旋開緊急停止鍵 b.按下操作板上馬達啟動鍵與電熱鍵,開啟馬達與料筒溫度(按1次左上角燈亮為開啟,再按1次左 上角燈滅為停止) c.選用操作方式 c-1點動:上下模時使用,又稱調模使用 c-2手動:選用此方式時操作板上的相應開關,隻在按下時作相應動作,手指放開即停止 c-3半自動:選用此方式時,隻需開關安全門一次,機器即做關模射出儲料(冷卻)開模頂出頂退,循環動作,再開安全門一次,再做一次循環 c-4.全自動:選用此方式操作,關上安全門後,機器重復關模頂出頂退(制品取出確認)關模至打開安全門或選用其它方式操作,生产有斜顶/滑块模具禁止使用。 d.開關模動作設定:開模一般設定為慢快慢,關模一般設定為快速低壓低速高 壓鎖模。低壓壓力最大不可以大於15kg/cm2低壓與高壓之間位置不可大2mm,快速與低壓間位置一般在50mm e.成型溫度設定:根據各種原料成型所需溫度設定,在改变设定温度时一次不可超过5°,加料段温度比熔融 段温度最少要低10°,待機器上顯示實際溫度達到設定溫度時,在改变设定温 度时一次不可超过5°再過二十分鐘才可進行熔胶,射出射退動作。 f.射出/保壓的設定: 射出設定分多段和一段,根據制品品質所需設定,能使用高速盡量使用高速,射滿成型制品 95%左右即轉換保壓。在需加速加压和位置时间时一次不能超过5KG和2%,第一模产品不可 超过产品的70%,防止产品粘模。保壓切換分時間切換:當射出動作達到設定射出時間時立 即轉換保壓。在生产停机10分钟以上后再开机时必须现降压力30%后开始慢满恢复原成型参 数。 位置切換:在射定的時間內,注射至所設定的位置,即轉換保壓或在注射未達到設定位置,設定時到也會立即轉換保壓。
注塑件包装作业指导书
注塑件包装作业指导书 1.目的:规范注塑件包装作业的详细要求,确保注塑件的包装质量,降低不 良率。 2.范围:适用于注塑件包装作业的全过程。 3.权责: 3.1作业员:严格按照本作业指导书的要求进行包装作业。 3.2检验员、工艺技术员、领班、物料员:监督本规范的作业执行情况,纠正、 改善相关作业的规范性,奖罚相关作 业人员。 4.作业指导: 4.1.装箱前须自检产品符合品质检验要求。 4.2.装箱之前须将产品上残留的料屑、削除的飞边毛丝等杂物吹除,保持产品清 洁干净。 4.3.交接班时上一班作业员要主动将装箱数量、包装方式方法等内容交接给下一 班。同样,下一班作业员接班时要主动向上一班询问以上相关信息。 4.4.对外观件、直接与水接触的产品以及所有对灰尘有控制要求的产品须套塑料 袋包装,且要确认包装袋和包装箱是否清洁干净。 4.5.对外观有要求的产品装箱后不可发生相互擦伤的现象,对结构有要求的产品 装箱后不可发生相互挤压变形、断裂的现象。 4.6.产品在包装箱内放置方式方法要以平稳、可靠为原则,选择竖放、平放、交 错放置、背对背放置等等,要视具体产品而定。包装后要保证在正常搬运过程中产品在箱内不发生翻倒、严重倾斜的现象。 4.7.产品装箱后不可超出箱面,封箱后箱面不可凸起。即保证多箱产品堆积后箱 内产品不受力,而由包装箱承受上面包装箱的重力。 4.8.同一种型号的产品装在同一种规格的包装箱里,每箱数量须一致,白班和晚 班的装箱数量须一致。 4.9.每一批次的产品装箱后只允许存在一个尾数箱,即每一批次的装箱数量只允 许一个零头数(机器模具故障、计划更改等情况除外)。 4.10.关于物料标示卡的相关详细要求: 4.10.1.填写内容如下:日期、班次、姓名(全名)、品名、规格(型号)、数 量、箱序号或袋序号(当班包装箱或包装袋的顺序号)。填写内容须与实际情况一致。 4.10.2.同一包装箱上只允许有一张物料标示卡,不允许有两张或两张以上物料 标示卡。即要求在贴上新的物料标示卡之前把旧的物料标示卡撕掉。 4.10.3.标示卡须统一贴在包装箱中间的上方,且不可倒贴。 4.10.4.包装箱放在指定的仓板上后物料标示卡须朝外,即仓板四周可视方位。