拉伸模设计实例
纯实战宽凸缘圆筒形拉伸件级进模具设计实例
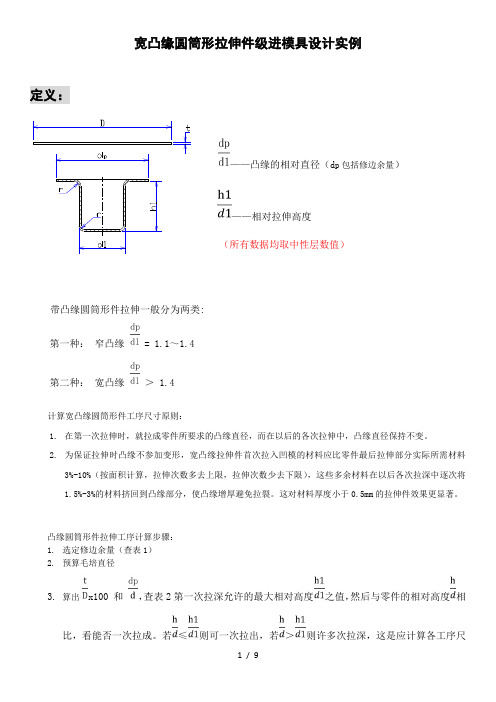
宽凸缘圆筒形拉伸件级进模具设计实例定义:——凸缘的相对直径(d p包括修边余量)——相对拉伸高度(所有数据均取中性层数值)带凸缘圆筒形件拉伸一般分为两类:第一种:窄凸缘 = 1.1~1.4第二种:宽凸缘> 1.4计算宽凸缘圆筒形件工序尺寸原则:1.在第一次拉伸时,就拉成零件所要求的凸缘直径,而在以后的各次拉伸中,凸缘直径保持不变。
2.为保证拉伸时凸缘不参加变形,宽凸缘拉伸件首次拉入凹模的材料应比零件最后拉伸部分实际所需材料3%-10%(按面积计算,拉伸次数多去上限,拉伸次数少去下限),这些多余材料在以后各次拉深中逐次将1.5%-3%的材料挤回到凸缘部分,使凸缘增厚避免拉裂。
这对材料厚度小于0.5mm的拉伸件效果更显著。
凸缘圆筒形件拉伸工序计算步骤:1.选定修边余量(查表1)2.预算毛培直径3.算出x100 和,查表2第一次拉深允许的最大相对高度之值,然后与零件的相对高度相比,看能否一次拉成。
若≤则可一次拉出,若>则许多次拉深,这是应计算各工序尺寸。
4.查表3第一次拉深系数m1,查表4以后各工序拉深系数m2、m3、m4……,并预算各工序拉深直径,得出拉深次数。
5.调整各工序拉深系数。
计算实例1.产品件简化凸缘直径:d p=74.9 拉伸直径:d=43.15 拉伸高度:H=19.5 材料厚度:t=1 2.修边余量表1 带凸缘拉深件修边余量凸缘尺寸dp相对凸缘尺寸 dp/d≤1.5 >1.5~2 >2~2.5 >2.5~325 1.6 1.4 1.2 1 50 2.5 2 1.8 1.6 100 3.5 3 2.5 2.2 150 4.3 3.6 3 2.5 200 5 4.2 3.5 2.7 250 5.5 4.6 3.8 2.8 300 6 5 4 3相对凸缘尺寸:=74/43.15=1.71 ;根据上面的表格(表1) 1.5<=1.71<2 ;50<dp=74 <100则,带凸缘的拉伸件修边余量:2~3,取值 3 则,带凸缘的拉伸件修边余量:Δd=3 mm3. 展开根据成型前后中性层的面积不变原理使用UG 测量出拉深件中性层面积7379.0492 mm ² (不推荐使用公式计算,个人感觉一般计算得数偏大,故本文省略公式) 则,展开尺寸D== 96.95≈97 mm凸缘直径:d 凸=80.9拉伸直径:d=43.15拉伸高度:H=19.5材料厚度:t=1修边余量:Δd=3展开直径:D=974. 拉深系数确定表2 带凸缘拉深件的首次拉深系数凸缘相对直径dp/d1 材料相对厚度x100≤0.2>0.2~0.5 >0.5~0.1 >1~1.5 >1.5≤1.1 0.64 0.62 0.6 0.58 0.55 >1.1~1.3 0.60 0.59 0.58 0.56 0.53 >1.3~1.5 0.57 0.56 0.55 0.53 0.51 >1.5~1.8 0.53 0.52 0.51 0.50 0.49 >1.8~2 0.470.46 0.45 0.440.43凸缘相对直径dp/d1 材料相对厚度x100≤0.2 >0.2~0.5 >0.5~0.1 >1~1.5 >1.5 ≤1.1 0.45 0.50 0.57 0.65 0.75 >1.1~1.3 0.40 0.45 0.50 0.56 0.65 >1.3~1.50.350.40 0.45 0.500.58>1.5~1.8 0.29 0.34 0.37 0.42 0.48>1.8~2 0.25 0.29 0.32 0.36 0.42表4 带凸缘拉深件的以后各次拉深系数凸缘相对直材料相对厚度x100径dp/d1≤0.2 >0.2~0.5 >0.5~0.1 >1~1.5 >1.5 m2 0.80 0.79 0.78 0.76 0.75m3 0.82 0.81 0.80 0.79 0.78m4 0.85 0.83 0.82 0.81 0.80m5 0.87 0.86 0.85 0.84 0.82(1)验证可否一次完成拉伸材料相对厚度:t/D=1/97×100=1.03≈1凸缘相对直径:dp/d=80.9/43.15=1.87总的拉伸系数:M=d/D=43.15/97=0.45根据上表(附表2):0.5< t/D ≤1;1.8< dp/d <2则有工艺切口的首次最小拉伸系数 M1=M根据上表(附表3)有工艺切口的首次拉伸最大相对高度:h/d=19.5/43.15=0.45>0.32所以,根据 M1=M 和 h/d=0.45>0.32 ,判定一次拉伸不能成功,需要多步拉伸。
第二章第5节 冲压模具设计——拉伸模
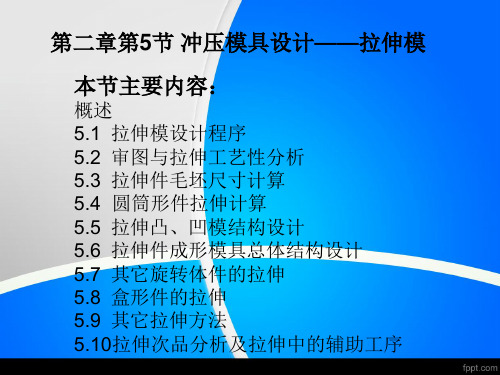
5.4.4 圆筒形件拉伸的拉伸力与压料力 1. 拉伸力的计算 (1)采用压边圈 首次拉伸 以后各次拉伸 (2)不采用压边圈 首次拉伸 以后各次拉伸
2. 压料力
Q=Ap 式中 A——压料圈下坯料的投影面积; p——单位面积压料力。
圆筒形件首次拉伸
FY
圆筒形件以后各次拉伸
(i=2、3、…、n)
FY
4)拉伸件口部尺寸公差应适当。
5)一般拉伸件允许壁厚变化范围0.6t1.2t,若 不允许存在壁厚不均现象,应注明;
6)需多次拉伸成形的工件,应允许其内、外壁 及凸缘表面上存在压痕;
5.2.2 拉伸件圆角半径的要求 1.凸缘圆角半径rdΦ 凸缘圆角半径rdΦ :指壁与凸缘的转角半径。 要求: 1)rdΦ >2t 一般取:rdΦ =(48)t 2)当rdΦ <0.5mm时,应增加整形工序。
拉伸件
拉伸模
5.1 拉伸模设计程序
审图
拉伸工艺性分析 拉伸工艺方案制定 毛坯尺寸计算 拉伸次数确定
冲压力及压力中心计算 冲压设备选择
凸、凹模结构设计 总体结构设计 冲压模装配图绘制 非标零件图绘制
5.2 审图与拉伸工艺性分析
学习目标: 掌握拉伸件的结构工艺性要求,了解拉伸件在 公差、材料上的要求,掌握拉伸件工序安排的一般 原则。 教学要求: 根据弯曲件的结构工艺性要求改善拉伸件的结 构设计;能够根据拉伸件的工艺条件,确定拉伸件 圆角半径,确定带孔拉伸件的孔的位置。
2)工序件底部圆角半径 合理选配各次拉伸工序件的底部圆角半径
3)高度
无凸缘圆筒形件拉伸工序计算流程
5.4.3 有凸缘圆筒形的拉伸计算 1.判断能否一次拉伸成形 (1)利用极限相对高度进行判断(查表) 如果工件的相对高度h/d小于或等于 表中对应的极限相对高度[h1/d1]值时, 则可以一次拉伸成形;否则需多次拉伸。 (2)利用极限拉伸系数进行判断(查表) 如果工件的相拉伸系数mF1大于或等 于表中对应的极限拉伸系数[mF1]值时, 则可以一次拉伸成形;否则需多次拉伸。
第二章第5节冲压模具设计——拉伸模方案
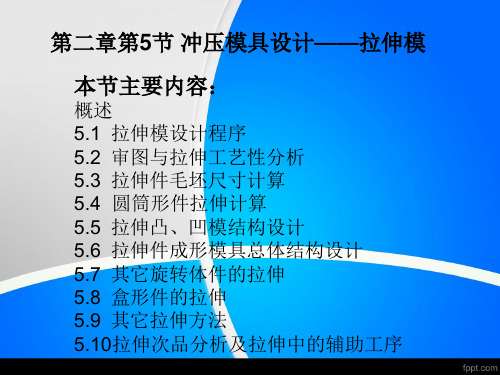
5.3.2 复杂旋转体拉伸件坯料尺寸的确定
相似原则
1.解析法 若拉伸件可由若干个简单几何形状组成,
则先分别求出各部分的表面积F,再相加得出 拉伸件的总面积∑F,最后按下式计算毛坯直 径。
D 4 F 1.13 F
5.3.2 复杂旋转体拉伸件坯料尺寸的确定
5.2.2 拉伸件圆角半径的要求
1.凸缘圆角半径rdΦ 凸缘圆角半径rdΦ :指壁与凸缘的转角半径。
要求:
12))r当dΦr>dΦ 2<t0.5m一m时般,取应:增rd加Φ =整(形4工8序)。t
pg
pg
py
ห้องสมุดไป่ตู้ 2.底部圆角半径rpg 底部圆角半径rpg:指壁与底面的转角半径。
要求:
1)rpg≥t,一般取:rpg≥(35)t 2)rpg<t,增加整形工序,每整形一次,rpg
m总——需多次拉伸成形制件的总拉伸系数。
注意:拉伸系数系愈小,表示拉伸变形程度愈大。
极限拉伸系数:指当拉伸系数减小至使拉伸件起 皱、断裂或严重变薄超差时的临界拉伸系数。
5.4.2 圆筒形拉伸件拉伸次数及工序尺寸计算
1.拉伸次数
当md=d/D>m极限时,可以一次拉伸,否则需多 次拉伸。
1)推算法:根据极限拉伸系数和毛坯直径,从第 一道拉伸工序开始逐步向后推算各工序的直径,
教学要求: 能够利用等面积法,计算圆筒形
拉伸件的毛坯尺寸;能够查表确定 常见的旋转体拉伸件的毛坯尺寸。
5.3.1 简单旋转体拉伸件坯料尺寸的确定
计算原则:按等面积(即拉伸前后材料面积 不变)原则进行计算,再加上修边余量。
数学计算法: 1)将制件分成若干简单几何形状(包括修边余
接线盒拉伸模设计及仿真模拟

目录摘要 (1)Abstract (2)0文献综述 (3)0.1 汽车工业的现状 (3)0.2 汽车覆盖件现状 (3)0.2.1 汽车拉伸模的设计必要性 (3)0.2.2 设计水平 (4)0.2.3 理论研究水平 (4)0.2.4 制造水平 (4)0.3 今后的发展方向 (5)0.3.1 标准化发展 (5)0.3.2 智能化方向发展 (5)0.3.3 联盟化发展 (6)0.4 结语 (6)1 引言 (7)2 零件分析 (7)2.1 零件的生产纲领 (7)2.2 接线盒产品的工艺分析 (7)3 冲压工艺方案的分析与确定 (7)3.1接线盒拉伸工艺的计算 (8)3.1.1 选取修边余量⊿h。
(8)3.1.2 假象毛坯直径(r r底) (8)3.1.3 毛坯长度L (8)3.1.4 毛坯宽度K (8)3.1.5 毛坯半径 (8)3.1.6 毛坯的形状如图1所示 (8)3.1.7 拉伸次数的确定n (9)3.1.8 确定工序件形状和尺寸 (9)3.2.确定冲压工艺方案 (10)4.模具结构形式的选择 (11)4.1 工序一的模具结构形式 (11)4.1.1 定位装置 (11)4.1.2卸料及顶件装置 (11)4.2工序二的模具结构设计 (11)4.2.1 结构形式 (11)4.2.2推件装置 (12)4.2.3 导向装置 (12)4.3工序三的模具结构形式 (12)4.3.1结构形式 (12)4.3.2 推件装置 (12)4.3.3 导向装置 (13)4.4工序四的模具结构设计 (13)4.4.1 结构形式 (13)4.4.2 定位装置 (13)4.4.3卸料与顶件装置 (13)5 计算各工序冲压力、选择压力机 (13)5.1工序一:[落料与冲底孔复合] (14)5.1.1 冲裁力的计算 (14)5.1.2 压力机的选择 (14)5.2 工序二:[一次拉伸] (15)5.2.1 拉伸力的计算 (15)5.2.2 压力机的选择 (15)5.3 工序三:[二次拉伸] (15)5.3.1 拉伸力的计算 (15)5.3.2 压力机的选择 (16)5.4 工序四:[冲边缘孔] (17)5.4.1 冲裁力的计算 (17)5.4.2 压力机的选择 (17)5.5 工序五:[切边] (18)5.5.1 冲裁力的计算 (18)5.5.2 压力机的选择 (18)6 设计冲模及其主要零部件 (19)6.1 工序一[落料与冲底孔复合] (19)6.1.1 模具工作部分尺寸的计算 (19)6.2 工序二[一次拉伸] (21)6.2.1 首次拉伸模的圆角半径 (21)6.2.2 首次拉伸单边间隙 (21)6.2.3 首次拉伸凹模工作尺寸 (22)6.3工序三 [二次拉伸] (22)6.3.1 二次拉伸直边区单边间隙 (22)6.3.2 二次拉伸圆角区单边半径 (22)6.3.3 二次拉伸模圆角半径 (22)6.3.4 凸、凹模工作部分的尺寸和公差。
拉伸模设计实例
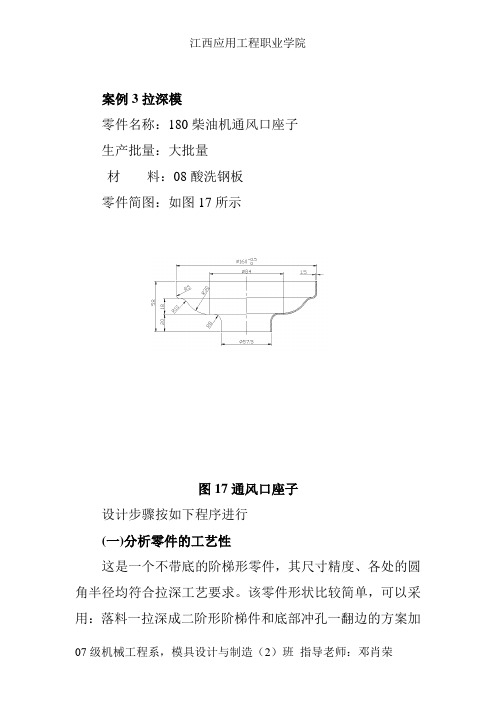
案例3拉深模零件名称:180柴油机通风口座子生产批量:大批量材料:08酸洗钢板零件简图:如图17所示图17通风口座子设计步骤按如下程序进行(一)分析零件的工艺性这是一个不带底的阶梯形零件,其尺寸精度、各处的圆角半径均符合拉深工艺要求。
该零件形状比较简单,可以采用:落料一拉深成二阶形阶梯件和底部冲孔一翻边的方案加工。
但是能否一次翻边达到零件所要求的高度,需要进行计算。
1. 翻边工序计算一次翻边所能达到的高度:按相关表取极限翻边系数K最小=0.68由相应公式计算得:H最大=D/2(1-K最小)+0.43r+0.72δ=56/2(1-0.68)+0.43*8+0.72*1.5=13.48(mm)而零件的第三阶高度H=21.5>H最大=13.48。
由此可知一次翻边不能达到零件高度要求,需要采用拉深成三阶形阶梯件并冲底孔,然后再翻边。
第三阶高度应该为多少,需要几次拉深,还需继续分析计算。
计算冲底孔后的翻边高度h(见图18):取极限翻边系数K最小=0.68拉深凸模圆角半径取r凸=2σ=3mm由相关公式得翻边所能达到的最大高度:图18拉深后翻边h最大=D/2(1-K最小)+0.57r凸=56/2(1-0.68)+0.57*3=10.67(mm)取翻边高度 h=10(mm)计算冲底孔直径d:d=D+1.14r凸-2h=56+1.14×3-2×10=39.42(mm)实际采用Ф39mm。
计算需用拉深拉出的第三阶高度h´h´=H-h+r凸+δ=21.5-10+3+1.5=16(mm)根据上述分析计算可以画出翻边前需拉深成的半成品图,如图19所示。
2.拉深工序计算图19所示的阶梯形半成品需要几次拉深,各次拉深后的半成品尺寸如何,需进行如下拉深工艺计算。
计算毛坯直径及相对厚度:先作出计算毛坯分析图,如图20所示。
为了计算方便,先按分析图中所示尺寸,根据弯曲毛坯展开长度计算方法求出中性层母线的各段长度并将计算数据列于表6中。
拉伸模具设计

凸缘拉伸膜设计(1) 原始数据:零件名:凸缘件 生产数量:4万件 材料:08F 料厚度t=1 零件简图如下:(1)零件分析:这是一个有凸缘零件,材料08F 具有较好的拉深性能,各处韵圆角半径及尺寸精度均符合拉伸工艺的要求。
该零件形状比较简单,可以采用落料—拉深拉深(2)拉深工艺计算:(1)零件毛坯直径的计算:根据分析有,D=h d d 1422+ d 1=28 d 2=40 h=25 所以D=66,33 (2)拉深系数和拉深的次数计算:该工件是有凸缘件,查表可得,该工件的第一次拉伸系数为:m 1=0.51 拉深次数“ 1d =1m D=0.55×109=59.95mm → 调整为62mm 2d =2m D0.76×59.95=45.56mm → 调整为47mm 3d =3m D0.79×45.56=35.99mm <39mm → 调整为39mm 计算共需3次拉深1各次拉深工件圆角半径及拉伸高度的确定: 工件的内角半径一般取r=(3-5)tr 1=3.5,r 2=2.5,r 3=1.5,所以每次拉深后筒形件的高度为h 1=0.25×(112d d D -)+0.43×11132.0(1r d d r +)=35.5 同理h 2=52.772,落料拉深复合模工艺计算(1)落料凹凸模刃口尺寸计算A 凹=(109-0.5×0.87)0175.2..0- =108.570.22.0-A 凸=A 凹-0.14=108.4322.00+(2)拉深凸凹模刃口尺寸计算Δ=0.62,X=0.75,δ凹=4Δ=0.155,A 凹=(A-X Δ)=(40-0.75×0.62)=39.535005.0- A 凸(A 凹- X Δ-Z min )=37.0708.00+ (3)第一套拉深模必要的计算拉伸力为:F L =πd 1t бb k 1=3.14×109×1×600×0.8=164285N 压力边为Q =4п[D 2-(d 1+2r A )2]p =26974N总拉深力为:P 总=164285+26975=191×103N所以应该选压力机设备为J23-25. 拉深磨具装配图:。
拉伸模设计课程设计

无凸缘筒形件拉深模设计样例 (5)(一)零件工艺性分析 (5)1.材料分析 (5)2.结构分析 (5)3.精度分析 (5)(二)工艺方案的确定 (5)(三)零件工艺计算 (5)1.拉深工艺计算 (5)2.落料拉深复合模工艺计算 (8)3.第二次拉深模工艺计算 (10)4.第三次拉深模工艺计算 (11)5.第四次拉深模工艺计算 (11)(四)冲压设备的选用 (11)1.落料拉深复合模设备的选用 (11)2.第二次拉深模设备的选用 (12)(五)模具零部件结构的确定 (12)1.落料拉深复合模零部件设计 (12)2.第二次拉深模零部件设计 (13)(六)落料拉深复合模装配图 (13)摘要简短介绍了我国模具行业发展状况,以及在当下模具行业情况,并且对国内外模具行业发展现状加以分析,从而对我国模具行业与国外模具行业进行了综合比较提出差距所在。
同时介绍了模具的类型和主要功能。
综合阐述对镶套落料拉深模具进行设计,首先对工件进行工艺分析,对拉深特点拉深变形过程进行技术分析。
在设计之前先确定修边余量和毛坯尺寸是否需要使用压边圈。
其次对拉深模具进行总体设计,了解拉深模具结构、分类,选择压边装置。
然后确定工作部分结构参数,确定拉深系数及工序尺寸。
计算凸模圆角半径、凹模圆角半径、间隙、凸、凹模尺寸公差、压边力、压边圈尺寸、拉深力、卸料力、拍样计算,并计算压力中心对压力机进行选择。
最后选择模具主要零部件及结构,对模具材料、模架进行选择,计算凸模长度、凹模高度和壁厚、凸模固定板尺寸以及校核凸、凹模强度。
同时设计选择其他零部件,确定模具闭合高度,对拉深模具进行安装调试。
关键词:模具冲压凸模圆角半径尺寸公差间隙拉深力凸、凹模绪论一、概述1、模具工业的概况模具工业是国民经济的基础工业,受到政府和企业界的高度重视,发达国家有“模具工业是进入富裕社会的源动力”之说,可见其重视的程度。
当今,“模具就是经济效益”的观念,已被越来越多的人所接受。
拉伸模具设计

凸缘制件的落料拉伸模
返回
在单动压力机的一个工作行程内,落料拉伸模可完成落料、 拉伸两道(甚至更多道)工序,工作效率高,但结构较复杂, 设计时要特别注意模具中所复合的各冲压工序的工作次序。
球形制件落料拉伸模
返回
矩形制件落料拉伸模
返回
落料拉伸压形模
返回
落料拉伸冲孔模
返回
单动压力机落料、正反拉 伸、冲孔、翻边复合模
返回
无压边圈带有顶出装置的拉伸模
适用于底部平整、拉 伸变形程度不大、相对 厚度(t/D)较大和拉伸 高度较小的零件。
返回
无压边圈落件拉伸模
采用锥形凹模,为拉伸变形提供有利条件, 坯料不易起皱,适用于薄料拉伸。
返回
带固定压边圈的拉伸模Fra bibliotek返回有弹性压边装置的正装式拉伸模
返回
有弹性压边装置的倒装式拉伸模
无压边圈的后次拉伸模
返回
适用于侧壁厚一致、直 径变化量不大、稍加整 形即可达到尺寸精度要 求的深筒形拉伸件。
无压边圈的反向后次拉伸模
多用于较薄材料的后次拉伸和锥形、 半球形及抛物线形等旋转体形状零 件的后次拉伸。
反拉伸的极限拉伸系数可比一般拉 伸降低10%~15%;
但凹模的壁厚尺寸受拉伸系数的限 制,而不能根据强度需要确定。
要求:如图所示零件, 材料为08钢,厚度为 1mm,大批量生产。 试确定拉伸工艺,设 计拉伸模。
拉伸模设计实例(二)下一页
步骤: (1)零件的工艺性分析; (2) 工艺方案确定:包括计算坯料直径、确定拉伸
次数、确定首次拉伸工序件尺寸、计算以后各次拉伸 的工序件尺寸、绘制冲压工序图、制定工艺方案; (3)落料与首次拉伸复合工序力的计算:包括计算 落料力、拉伸力与压料力、初选压力机标称压力等;
- 1、下载文档前请自行甄别文档内容的完整性,平台不提供额外的编辑、内容补充、找答案等附加服务。
- 2、"仅部分预览"的文档,不可在线预览部分如存在完整性等问题,可反馈申请退款(可完整预览的文档不适用该条件!)。
- 3、如文档侵犯您的权益,请联系客服反馈,我们会尽快为您处理(人工客服工作时间:9:00-18:30)。
案例3拉深模
零件名称:180柴油机通风口座子
生产批量:大批量
材料:08酸洗钢板
零件简图:如图17所示
图17通风口座子
设计步骤按如下程序进行
(一)分析零件的工艺性
这是一个不带底的阶梯形零件,其尺寸精度、各处的圆角半径均符合拉深工艺要求。
该零件形状比较简单,可以采用:落料一拉深成二阶形阶梯件和底部冲孔一翻边的方案加
工。
但是能否一次翻边达到零件所要求的高度,需要进行计算。
1. 翻边工序计算
一次翻边所能达到的高度:
按相关表取极限翻边系数K最小=0.68
由相应公式计算得:
H最大=D/2(1-K最小)+0.43r+0.72δ
=56/2(1-0.68)+0.43*8+0.72*1.5
=13.48(mm)
而零件的第三阶高度H=21.5>H最大=13.48。
由此可知一次翻边不能达到零件高度要求,需要采用拉深成三阶形阶梯件并冲底孔,然后再翻边。
第三阶高度应该为多少,需要几次拉深,还需继续分析计算。
计算冲底孔后的翻边高度h(见图18):
取极限翻边系数K最小=0.68
拉深凸模圆角半径取r凸=2σ=3mm
由相关公式得翻边所能达到的最大高度:
图
18拉深后翻边
h最大=D/2(1-K最小)+0.57r凸
=56/2(1-0.68)+0.57*3
=10.67(mm)
取翻边高度 h=10(mm)
计算冲底孔直径d:
d=D+1.14r凸-2h
=56+1.14×3-2×10
=39.42(mm)
实际采用Ф39mm。
计算需用拉深拉出的第三阶高度h´
h´=H-h+r凸+δ
=21.5-10+3+1.5
=16(mm)
根据上述分析计算可以画出翻边前需拉深成的半成品图,如图19所示。
2.拉深工序计算
图19所示的阶梯形半成品需要几次拉深,各次拉深后的半成品尺寸如何,需进行如下拉深工艺计算。
计算毛坯直径及相对厚度:
先作出计算毛坯分析图,如图20所示。
为了计算方便,先按分析图中所示尺寸,根据弯曲毛坯展开长度计算方法求出中性层母线的各段长度并将计算数据列于表6中。
图
19
翻
边
前
半
成
品
形
状
图20 计算毛坯分析图
表6毛料计算附表(mm )
序
号 l
r
lr
序 号 l
r
lr
1
17
79.25
1374.25
6
13.75
31.17
428.59
2 6.67 77.7
1 518.3
3
7 2 28 56
3 10.4
28 70.1
84
731.8
8
8 5.89 26.6
4
156.
67
4 28.3
7 55.1
04
1563.
3
9 24.2
5
12.1
3
293.
43
5 5.25 39.3
75 206.7
2
∑lr=5302.17
根据公式计算得毛坯直径:
计算相对厚度:δ/D*100=1.5/206*100=0.72
确定拉深次数:
根据h/d n=54.5/57.5=0.95
δ/D*100=0.72
查相关表得拉深次数为2,故一次不能拉成。
计算第一次拉深工序尺寸:
为了计算第一次拉深工序尺寸,需利用等面积法,即第二次拉深后的面积和拉深前参与变形的面积相等,求出第一次拉深工序的直径和深度。
由于参与第二次拉深变形的区域是从图2-30中的L5开始,因此以L5开始计算面积,并求出相应的直径。
δ/D*100=0.72
查相应表和第二次拉深系数m2=0.76
因此,第一次应拉成的第二阶直径
d=56/0.76=73.6(mm)
为了确保第二次拉深质量,充分发挥板料在第一次拉深变形中的塑性潜力,实际定为:d=72mm
按照公式(4-7c)求得:
h=0.25/72(96.62-842)+0.86*4.75
=11(mm)
这样就可以画出第一次拉深工序图,如图21所示。
上述计算是否正确,即第一次能否由Ф206的平板毛坯拉深成图21所示的半成品,需进行核算。
阶梯形零件,能否一次拉成,可以用下述近似方法判断,即求出零件的高度与最小直径之比h/dn,再按圆筒形零件拉深许可相对高度表(相应表)查得其拉深次数,如拉深次数为1,则可一次拉成。
根据图2-31所示:h=51, dn=72, h/dn=0.70, δ/D×100=72,查相关表提拉深次数为1,说明图2-31所示半成品可以由平板毛坯一次拉成。
(二)确定工艺方案
通过上述分析计算可以得出该零件的正确工艺方案是:落料;第一次拉深,压成如图2-31所示的形状;第二次拉深、冲孔,压成如图2-29所示的形状;第四道工序为翻边,达到零件形状和尺寸要求,如图2-27所示。
共计四道工序。
现在以第一次拉深模为例继续介绍设计过程。
(三)进行必要的计算
1.计算总拉深力
根据相对厚度δ/D×100=0.27,按照公式判断要使用压边圈
按照公式计算得到拉深力为:
P=πd1δσbK1=3.14×158.5×1.5×450×0.91
=300000(N)
压边力为:Q=π/4[D2-(d1-2r凹)2]q
=π/4[2052-(160+2*8)2]2.5
=22000(N)
式中 q的值按相应表选取为2.5N/mm²
总拉深力P总=P+Q=300000+22000
=322000(N)
图21 第一次拉深工序图图22模具结构草图
2.工作部分尺寸计算
该工件要求外形尺寸,因此以凹模为基准间隙取在凸模
单边间隙Z=1.1δ=2.55(mm)
凹模尺寸按公式(4-33a)得:
D凹=(D-0.75△)+δ凹=(160-0.75×0.5)
+0.10
=159.6+0.10(mm)
式中δ凹见表
凸模尺寸按公式得:
D凹=(D-0.75△–2Z)_δ凸
=(160-0。
75×0.5-2×2.55)_0.07
=156.3 _0.07(mm)
式中δ凸见表
圆角处的尺寸,经分析,若该处是以凸模成形,则以凸模为基准,间隙取在凹模上;若是以凹模成形,则以凹模为基准,间隙取在凸模上。
(四) 模具总体设计
勾画的模具草图,如图22所示。
初算模具闭合高度:
H模=272.5(mm)
外轮廓尺寸估算为Ф420(mm)
(五)模具主要零部件设计
该模具的零件比较简单,可以在绘制总图时,边绘边设
(六)选定设备
本工件的拉深力较小,仅有322000N,但要求压力机行程应满足:S≥2.5h工件=145(mm),同时考虑到压边要使用气垫,所以实际生产中选用有气垫的3150000N闭式单点压力机。
其主要技术规格为:
公称压力 3150000N
滑块行程 400mm
连杆调节量 250mm
最大装模高度 500mm
工作台尺寸 1120×1120 mm
(七) 绘制模具总图
模具总图,如图23所示
图23 座子拉深模(第一次)
1-上模座 2-内六角螺钉3-内六角螺钉4-顶杆5-模柄6-圆柱销7-凹模与推件板
8-凹模9-凸模10-卸料板11-顶杆12-下模座
表7 零件明细表
序号名称数
量
材料热处理
1 上模座 1 HT200
2 内六角螺钉M12
×70
10 45 HRC40~45
3 内六角螺钉M12
×25
6 45 HRC40~45
4 顶杆 1 4
5 HRC40~45
5 模柄 1 Q235(A5)
6 圆柱销12n6×
100
2 45 HRC40~45
7 凹模与推件板 1 T8A HRC56~60
8 凹模 1 T8A HRC56~60
9 凸模 1 T8A HRC56~60
10 卸料板 1 Q235(A3)
江西应用工程职业学院
11 顶杆 4 45 HRC40~45
12 下模座 1 HT200
07级机械工程系,模具设计与制造(2)班指导老师:邓肖荣。