评价岩石脆性指标对滚刀破岩效率的影响
滚刀滚动切削岩石的数值及试验研究

滚刀滚动切削岩石的数值及试验研究谭青;杨秧;夏毅敏;易念恩;张旭辉【摘要】为了研究滚刀滚动切削岩石的性能,合理简化盘形滚刀滚压破岩过程,采用颗粒离散元法分别建立了考虑摩擦力的滚刀滚动切削有、无节理岩体模型,分析了滚动切削模拟过程中切削力、裂纹发育、岩石破碎形态的变化规律.利用滚刀回转切削试验台进行了破岩试验,得到切削力随工况变化的规律,验证了仿真模型的准确性.研究结果表明:对无节理岩体,提高贯入度会增加主干裂纹深度和破碎面积,提高切削速度会增加法向力,而对滚动力影响不大;对含节理岩体,岩体节理强度越强则主干裂纹越深,比能耗越高;岩体的节理倾向会对破岩比能耗产生一定的影响,正向倾角切削效率高于逆向倾角约12%;节理倾角越小,正、逆向节理倾角破岩比能耗差值越大;合理安排刀盘正反转可提高破岩效率.【期刊名称】《湖南大学学报(自然科学版)》【年(卷),期】2018(045)008【总页数】10页(P69-78)【关键词】盘形滚刀;岩石力学;裂纹;节理;比能耗【作者】谭青;杨秧;夏毅敏;易念恩;张旭辉【作者单位】中南大学高性能复杂制造国家重点实验室,湖南长沙410083;中南大学机电工程学院,湖南长沙410083;中南大学高性能复杂制造国家重点实验室,湖南长沙410083;中南大学机电工程学院,湖南长沙410083;中南大学高性能复杂制造国家重点实验室,湖南长沙410083;中南大学机电工程学院,湖南长沙410083;中南大学高性能复杂制造国家重点实验室,湖南长沙410083;中南大学机电工程学院,湖南长沙410083;中南大学高性能复杂制造国家重点实验室,湖南长沙410083;中南大学机电工程学院,湖南长沙410083【正文语种】中文【中图分类】TP391.9;U455.39随着我国隧道工程建设的展开,全断面岩石掘进机(Full face rock tunnel boring machine,TBM)以其施工效率高、掘进安全、噪声小等诸多优点,在隧道施工中使用日益广泛.岩石的破坏和剥落通过刀盘上的盘形滚刀滚动切削来实现,然而在实际切削过程中,地质情况是复杂多变的,如岩石种类、节理等[1-2].国内外学者针对TBM不同工况下破岩效率进行了相应的滚刀切削试验.刘红岩等人[3]通过物理实验研究了节理对岩石的破坏模式、单轴抗压强度、弹性模量的影响.Howarth[4]通过线性切割试验研究了刀间距对破岩效果的影响.龚秋明等人[5]研究了岩石节理间距对破岩效果的作用,发现节理面对破岩过程中滚刀的力有很大影响.以上研究探讨了不同地质条件下掘进参数对滚刀滚动破岩效果的作用.近年来也有学者通过数值仿真研究滚刀切削岩石的工况并取得了一些成果.Bejari 等人[6-7]采用UDEC研究了节理对刀具破岩的影响,研究表明节理间距增大会减小刀具的切入率.Sun等人[8]采用有限元法对盘形滚刀的最优刀间距进行分析,并解决了平面刀盘的布置问题.Labra等人[9]采用混合离散元/有限元法建立滚刀切削岩石模型并分析掘进参数下滚刀破岩过程.马洪素等人[10]通过两组试验对不同节理倾向下裂纹走向进行研究,并通过FLAC分析了裂纹走向与应力场分布的关系.孔晓璇等人[11]及孙金山等人[12]通过PFC2D研究双滚刀侵入不同节理间距及节理倾角的岩体时裂纹的走向,得到了节理特征对裂纹扩展的影响.张桂菊等人[13]采用二维颗粒离散元研究岩石温度对破岩的影响.Liu等人[14-16]采用PFC2D研究单、多滚刀垂直侵入岩石的效率与岩石裂纹扩展形态.Choi等[17]采用PFC2D研究节理间距与节理倾角对滚刀受力的影响.谭青等[18]采用PFC2D研究滚刀侵入不同围压与节理条件岩石时破碎模式与破岩比能耗的规律.上述模拟研究多将滚刀滚动切削过程简化为滚刀垂直贯入岩体的过程,忽略滚刀水平滚动以及岩石摩擦因素.易于观察到滚刀垂直贯入岩石过程中裂纹发育规律,难以得到滚刀滚动破岩过程中岩石裂纹发育规律.此外,以上建立的岩石节理模型仅关注节理倾角或者节理间距,尚未考虑含节理岩体强度和节理倾向对破岩的影响.本文采用离散元数值方法建立了无节理滚动切削与含节理滚动切削模型,通过改变滚刀工作参数及岩石参数,对贯入度、切削速度、节理倾向、含节理岩体强度等参数进行模拟.通过观察仿真结果,得到破岩时滚刀受力、岩石裂纹数量变化、岩石裂纹生长过程,最后以回转试验对仿真得到的切削力进行验证.本文的创新之处在于:建立了考虑摩擦力的滚刀滚动切削数值模型,该模型与实际工程应用中滚刀破岩过程拟合度更高;分析不同工况下滚刀受力与岩石破碎模式的关联规律;建立了不同节理倾向、倾角与节理面强度的岩石模型,其结论适用地质范围更广.1 数值模型的建立1.1 简化滚刀模型TBM在掘进时,滚刀布置在刀盘上并伴随刀盘的运动而做垂直贯入和水平滚动(视掌子面为水平面),滚刀与岩石相互作用时产生指向掌子面的法向力FN、与掌子面平行而指向滚刀平移方向的滚动力FR和受到回转切削影响生成的侧向力FL三种滚刀切削力,如图1所示.法向力主要由刀盘推力提供,滚动力主要由刀盘扭矩提供,侧向力主要由回转运行中滚刀对岩石的挤压力产生.考虑本文主要研究滚刀水平滚动破岩,忽视侧向力影响,因此将三维的滚刀运动简化为二维滚动过程.文献[14-18]研究证明,将滚刀三维破岩简化为二维破岩是可行的.本文以工程实践中的常用滚刀进行1∶2缩尺所得的小滚刀作为研究对象,其参数见表1.基于表1中参数,简化滚刀模型为二维模型.1.2 模型宏、细观参数的标定由于试验条件限制,假定切削对象为泥岩、砂岩等软岩,由于天然岩石内部初始损伤缺陷难以统计,为了增加试验的可重复性,降低试样物理力学性能分布的随机性,本文采用混凝土代替岩石进行研究.混凝土的制作和养护参照GB/T 50081-2002《普通混凝土力学性能试验方法标准》[19].在力学测试中心测得混凝土试样的物理力学性能参数如表2所示,由表2可知,混凝土强度等级为C20,其抗压强度等物理力学特性近似自然界的泥岩、砂岩等软岩[20].为建立颗粒流模型细观参数与材料宏观物理力学参数之间的联系,需要确定颗粒的基本尺寸等参数(表3).以单轴压缩、巴西劈裂和直剪试验对模型进行标定(图2):单轴压缩试验见图2(a);巴西劈裂试验见图2(b);剪切试验见图2(c).通常采用试凑法按照一定规律反复调整细观参数,直到仿真输出曲线接近物理标定的曲线即可.标定得到的颗粒流模型细观力学参数见表4.图1 滚刀切削力示意图Fig.1 Cutter forces of the disc cutter表1 滚刀基本参数Tab.1 The basic parameters of the disc cutter直径/cm刀刃宽度/mm过渡圆弧半径/mm刀刃角/(°)2110420表2 软岩材料宏观参数Tab.2 Macro-parameters of soft rock material参数名单位数值密度kg/m32 360弹性模量GPa1.82抗压强度MPa21.88抗拉强度MPa1.47内聚力MPa4.12内摩擦角(°)35表3 颗粒流模型基本参数Tab.3 Basic parameters of PFC2DmodelRmin/mmRmax/Rminkn/ks0.31.22.5图2 颗粒流模型细观参数的确定Fig.2 Meso-parameters determination in PFC2D表4 细观力学参数Tab.4 Meso-mechanical parameters参数名单位数值颗粒密度kg/m32 950法向强度MPa15切向强度MPa15法向刚度N/m9.5×108切向刚度N/m3.8×108摩擦因数0.31.3 建立滚刀滚动切削数值模型为了研究滚动切削对破岩的影响,根据标定得到的细观力学参数分别建立无节理、含节理两种滚刀侵入岩体的切削模型.试样被安置在一个三面墙皆被固定的方槽中,模型尺寸为400 mm×200 mm.节理模型中节理特征通过JSET命令设置,由于滚刀的刚度远远大于软岩的刚度,所以将滚刀简化为刚体并赋予属性wall类型.滚刀在破岩过程中因摩擦力而被动转动,滚刀与岩石的接触摩擦因数取0.3.通过FISH语句可以提取滚刀受力等信息.仿真中材料的破坏过程可视为颗粒间连接键在载荷作用下断裂的过程.键连接有两种形式:接触键和平行键.通过设定键与颗粒的大小、强度,对不同的本构进行表述,当载荷超过预设键的强度时,便会使颗粒脱离接触而产生破坏,通过观察、统计仿真所得的微观裂纹可以了解岩体内部破碎情况.2 滚刀切削无节理岩石模型分析2.1 滚刀切削过程分析图3为滚刀滚动切削破岩过程,根据工程实践应用,设定滚刀贯入度为8 mm,切削速度为0.6 m/s.随着滚刀向前推进,岩体上层的岩石不断被破碎,滚刀前方产生较大的破碎块(图3(a)),同时岩体内部产生大量微裂纹,部分微裂纹汇聚成主干裂纹并向岩体深处扩展.图3 滚刀滚动切削岩石动态过程Fig.3 Dynamic process of rock cutting图4为滚刀切削力及滚刀角速度动态变化图.由图4可知,滚刀破岩过程中滚刀力曲线波动较大,且法向力的波动远大于滚动力.这说明岩石内部裂纹扩展主要由法向力主导,滚刀与岩石接触而转动,角速度均值约为5 rad/s,这说明滚刀的旋转瞬心在刀刃下方附近.图5为FISH函数记录的裂纹数目变化.随着切削行程的增加裂纹数目线性增加,张拉裂纹数目始终大于剪切裂纹数目,说明滚刀破岩过程中岩石的破碎以张拉破坏为主.切削行程/mm图4 滚刀力与角速度变化图Fig.4 Variation diagram of cutting force and angular velocity2.2 贯入度对滚刀切削的影响贯入度及切削速度的变化会改变滚刀与岩石的接触情况,同时受力、岩石破碎形态以及裂纹发育都会受到影响.图6反映了滚刀切削行程为300 mm,切削速度为0.6 m/s时不同贯入度下的切削状态.从图6可知,岩石破碎面积与主干裂纹深度均随贯入度的增加而增大.切削行程/mm图5 微裂纹个数随切削行程变化图Fig.5 Variation diagram of crack number with cutting length图6 不同贯入度下滚刀滚动破岩状态Fig.6 Rock breaking state under different cutting depths如图7所示,贯入度的增加使得主干裂纹平均深度大幅度增长.然而,随着贯入度的增加,主干裂纹平均长度与贯入度的比值在下降,说明随着贯入度增加,主干裂纹平均长度增速下降,单纯增加贯入度并不能有效增加主干裂纹长度.主干裂纹的扩张虽然消耗了大量能量,但并未直接将岩体剥落下来.较深的主干裂纹说明滚刀做功主要引起裂纹纵深发展,而用于表面破岩的做功较少,所以主干裂纹越长则破岩效率越低.此外,统计仿真结果可知,随着贯入度的增加,微裂纹数量线性增长.当贯入度较小时,剪切微裂纹占多数,在较大贯入度下,张拉微裂纹则占多数.这说明增加贯入度有利于张拉微裂纹的发育.通常岩石破碎效率以破碎比功[13]来衡量.本文为了简化模型,不考虑破碎块度大小,以掘进机常用的比能耗SE来衡量破岩效率.由于本文开展二维数值模拟,故将其定义为刀具切削单位面积岩石所需消耗的能量,表示为:(1)式中:SE为破岩比能耗(MJ/m2);WN为滚刀法向力做功;WR为滚刀滚动力做功;FN为法向力(N);FR为滚动力(N);p为贯入度(mm);J为滚刀的切削行程(mm);S为岩石破碎的面积(mm2).一般情况下法向力做功为滚动力做功的5%[18],故实际计算中只考虑滚动力做功.贯入度/mm图7 贯入度与裂纹深度关联规律Fig.7 Variation of cutting depth with crack depth随着贯入度的增加,滚刀滚动力和法向力都呈递增趋势(表5).其中,滚刀滚动力增长率远大于法向力的增长率,这说明滚动力对贯入度更加敏感.在工程中,一般控制滚刀的贯入度不超过10 mm以避免贯入度过大而增加滚刀的受力负荷,造成滚刀过早失效.由表5可知,随着滚刀贯入度的增加,破碎面积的增长速率下降,而比能耗迅速上升,最大增加量约为96%.说明增大贯入度虽然提高破岩速度,但是切削效率下降,且加剧了滚刀磨损,缩短了轴承寿命,导致提早换刀.因此,在施工中,不可盲目增加贯入度以提高掘进效率.表5 不同贯入度下滚刀滚动破岩参数统计表Tab.5 Simulation results with different cutting depth贯入度/mm滚动力/kN法向力/kN破碎面积/cm2比能耗/(J·cm-2)41.439.88110.503.8862.1912.23141.174.6584.0214.44176.926.82104.5815. 69180.177.632.3 速度对滚刀切削的影响图8为滚刀切削行程为300 mm,贯入度为6 mm时的破岩状态图.由图8可知,在不同切削速度下,岩体破坏状况相近,裂纹扩展情况及破碎块的形成亦相似.这说明切削速度对岩石破坏以及裂纹扩展的影响不大.此外,统计仿真结果可知,裂纹总数随切削速度变化波动较小,这说明切削速度不是影响微裂纹数目的主要参数.剪裂纹数目所占总裂纹数目的比例随切削速度的增加而上升.图8 不同切削速度下滚刀滚动破岩状态图Fig.8 Rock breaking state diagram with different cutting speed表6为不同切削速度下滚刀破岩的参数统计表.可知加大切削速度对滚动力、破碎面积和比能耗的影响并不大.滚刀法向力对切削速度较为敏感,随着切削速度的提升,法向力显著增加,当切削速度从0.4 m/s提高到1 m/s时,滚刀法向力增加约50%.因此,施工中在确保滚刀承受的法向冲击力不超过刀圈承载额的前提下,可提高切削速度增加破岩速度.表6 不同切削速度下滚刀滚动破岩参数统计表Tab.6 Simulation results with different cutting speed速度/(m·s-1)滚动力/kN法向力/kN破碎面积/cm2比能耗/(J·cm-2)0.42.128.9132.254.810.62.5210.6134.675.610.82.6111.6139.005.631.02.71 12.23131.176.203 滚刀切削含节理岩石模型分析3.1 滚刀切削过程分析已有研究表明[6,7,11],节理特性对滚刀切削岩石有较大的影响.自然界中岩石的节理分布一般都比较复杂,同时滚刀与节理的相对位置也不断变化,因此,本文对此进行必要的简化.假定数值模型中只存在一组等间距节理(设节理间距恒为10 mm),综合考虑节理倾向、倾角和含节理岩体强度对滚刀破岩的影响,规定节理倾向与滚刀掘进方向一致为正向,相反为逆向.图9和图10分别为水平0°和垂直90°,正、逆向倾角分别为20°、40°、60°和80°的节理岩体.含节理的岩体强度由节理面的颗粒细观参数(摩擦因数、法向强度、切向强度)间接决定.通过改变节理面的颗粒细观参数,可以得到不同强度的节理岩体(也有文献简称为节理强度),即节理岩体具有不同的内聚力和内摩擦角.不同强度节理岩体的物理数值可通过直剪试验得到(图2(c)).研究发现,当摩擦因数一定时(本文设置摩擦因数为0.3),法向强度与切向强度越大,得到含节理的岩体强度也会较大.本文用2种节理面颗粒连接强度(法向与切向强度分别取8 kPa和200 kPa)来描述低强度和高强度含节理岩体.图9和图10是切削距离为250 mm,贯入度为8 mm,削速度为0.6 m/s时的破岩状态图.其中,图9对应的节理面粘接强度为8 kPa,摩擦因数为0.3,节理强度较低.从图9可知,主干裂纹很少向纵深扩展,这是由于低强度节理面很容易起裂和断裂,阻碍了滚刀力向岩体深处传递,所以岩体深处很少有主干裂纹.此外,还可以观察到有大量碎块从岩体表面崩落,起裂方向大多垂直于节理面.图10对应的节理面粘接强度为200 kPa,摩擦因数为0.3,节理强度高.当节理倾向为正,倾角分别为60°与80°时可以观察到主干裂纹扩展方向有垂直于节理面的倾向,有的主干裂纹可以跨越几组节理面到达岩体深处.这说明较高的节理强度对于裂纹扩张的阻碍效应小于低节理强度.当节理倾向为逆向时,倾角分别为60°和80°时,主干裂纹扩展方向有平行于节理面的倾向,与无节理破岩比较(图6(c)),二者裂纹扩展形态非常近似,节理的存在对于主干裂纹扩展深度影响很小.图9 低强度含节理岩体(连接强度为8 kPa)Fig.9 Low strength for jointed rock masses(joint bond strength 8 kPa)图10 高强度含节理岩体(连接强度为200 kPa)Fig.10 High strength for jointed rock masses(joint bond strength 200 kPa)3.2 节理特征对微裂纹数量的影响微裂纹与节理关联规律如图11所示.由图11可知,高强度节理岩体含张拉裂纹数量多于低强度岩体,低强度节理岩体含剪切裂纹数量多于高强度岩体.考虑到岩石抗压不抗拉的特性,滚刀入侵高强度节理岩体时主要发生了张拉破坏.对低强度节理岩体而言,节理间连接强度较低,节理层容易断裂,因而剪切裂纹较高强度节理岩体多.岩体节理强度高时,正向节理倾角下含有更多的微裂纹数量.此外,节理倾角分别为20°、60°时,裂纹发育受到阻碍.节理角度/(°)(a)拉张裂纹数节理角度/(°)(b)剪切裂纹数图11 微裂纹与节理特征关系图Fig.11 Relation diagram of micro-crack numbers with joint characteristics3.3 节理特征对裂纹深度的影响节理倾角与节理强度对主干裂纹的扩展深度有着明显的控制作用:应力场不均分布导致低强度节理面容易产生张拉微裂纹起裂[10],节理面对主干裂纹扩展起阻隔作用[5],而且节理倾角能影响主干裂纹扩展方向.因此,在相同的主干裂纹长度下,裂纹深度会由于扩展方向的改变而改变.主干裂纹深度整体趋势规律如图12所示. 相较低强度节理面,高强度节理面中主干裂纹更容易扩展到岩体深处,这是由于低强度节理面对裂纹继续扩展起到阻隔作用.基于上文讨论,主干裂纹深度过大对于提高破岩效率并无直接益处,所以低节理强度更有利于提高破岩效率.由图12可看出,水平和垂直节理倾角下主干裂纹相对较长.在高强度节理面中,倾角分别为20°、60°时,主干裂纹较浅,且逆向节理倾角产生的裂纹较正向倾角更深,这反映了正向节理倾角下破岩更加高效.在低强度节理面中,正、逆向倾角则对裂纹深度无明显影响.节理角度/(°)图12 主干裂纹深度与节理特征关系图Fig.12 Relation diagram main crack depth with joint characteristics3.4 节理特征对破岩面积的影响在相同贯入度下,更大的破碎面积意味着更快的掘进速度.通过测量,可以得到破岩面积受节理特征影响的规律,如图13所示.正向倾角破岩面积更大,高强度节理面下该现象更显著.高强度节理倾角分别为80°与0°时,破碎面积相比其他倾角更大,该结论与谭青等[18]的结论一致.低强度节理倾角分别为20°、60°和90°时,破碎面积相对较小.节理角度/(°)图13 破岩面积与节理特征关系图Fig.13 Variation of breakingarea with joint characteristics3.5 节理特征对比能耗的影响通过仿真计算,得出滚刀力、破碎面积及比能耗等参数如表7所示.由于仿真条件限制,破碎块无法排出(图9(d)),导致在后续滚刀切削中已经崩落的岩石会进一步被滚刀破碎,造成滚动力增加.为了贴近实际施工状态,对仿真所得滚动力乘以系数φ(φ取值为0~1).根据表7中数据可以得到比能耗趋势如图14所示.表7 比能耗统计表Tab.7 Specific energy statistics table连接强度/kPa节理倾向节理倾角/(°)滚动力/kN破碎面积/cm2比能耗/(J·cm-2)8逆正03.48114.17.63203.81105.29.05404.13126.38.17604.31124.18.68804.42125.78.79904.10117.68.72203.31107.47.70403.54120.37.36603.74117.87.94804. 26126.98.39200逆正05.37137.79.74204.78126.59.45405.38133.710.06604.66124.09.40804.96133 .29.31904.70130.59.00204.27131.18.14404.79135.58.84604.27125.98.48804. 58133.88.56由图14可知,在相同掘进参数下,正向节理倾角比能耗均低于逆向倾角比能耗.这是由于在逆向倾角下,滚刀运动方向与节理夹角大多呈钝角,主干裂纹将沿节理面向深处扩展.在正向倾角下,夹角多为锐角,滚刀挤压节理面产生破碎块,因而阻断主干裂纹的扩展.该结论与文献[17]中结论一致.在垂直90°倾角时,滚刀力一部分与节理面相互作用使岩石破碎,一部分沿节理面向岩石内部传递.90°节理倾角比能耗介于正向和逆向倾角比能耗之间.由表7中切削比能耗计算可知,正向倾角下节理岩体切削效率高于逆向倾角约12%.对低强度节理岩体,当节理倾角分别为20°、40°、60°和80°时,比能耗减少比例分别为18%、11%、9%和5%;对高强度节理岩体,减少比例分别为16%、14%、11%和9%,这是由岩体的连接强度所决定的.在低节理强度下,岩体连接强度小,使岩体容易破碎,所以低强度节理岩体受节理倾角影响较大;反之,高强度节理岩体强度受倾角影响较小.低节理强度岩体比能耗普遍低于高节理强度岩体,这说明低强度节理面阻隔了主干裂纹向岩体深处扩展,减少了滚刀做功的无效耗散,提高了破岩效率.相反,高强度节理面不易阻隔主干裂纹向岩体深处扩展,破岩效率不如低强度节理岩体高.整体上,正向倾角为20°对提高滚动切削高强度节理岩体的效率有利,正向倾角为40°时对提高滚动切削低强度节理岩体效率有利.节理角度/(°)(a)低强度节理岩体倾向对比节理角度/(°)(b)高强度节理岩体倾向对比节理角度/(°)(c)逆向倾角高、低强度岩体对比节理角度/(°)(d)正向倾角高、低强度岩体对比图14 比能耗与节理特征关系图Fig.14 Variation of specific energy with joint characteristics4 试验验证4.1 试验系统组成试验在盘形滚刀回转破岩试验台上进行.如图15(a)和图15(b)所示,试验台由回转机械主机、液压系统、控制系统和测试系统构成.测试系统由三向力传感器、低通滤波器、USB采集卡、工控机、高速摄像系统、LabVIEW系统组成.高速摄像系统可以捕捉到岩体表面起撬直到崩落的全过程(图15(c)和图15(d)).切削对象为混凝土(仿软岩),混凝土的物理力学指标见表2,滚刀参数见表1.图15 TBM滚刀物理切削试验Fig.15 Experiment of rock breaking by TBM disc cutter4.2 滚刀受力分析试验试验通过改变切削速度及贯入度来观察滚刀的受力状况,进行2组试验分别记录滚刀滚压过程中所受的三向力和滚刀行程.第1组试验为恒定速度:贯入度分别采用4 mm和10 mm,切削速度为0.6 m/s.第2组试验为恒定贯入度:切削速度分别采用0.4 m/s和1.0 m/s,贯入度为6 mm.不同贯入度与切削速度下切削力变化情况如图16所示.4.3 切削力误差分析PFC2D基本结构是一个三维的圆柱体(圆柱体有厚度,但是不能在Z轴上移动,只能在X和Y轴移动、转动),厚度定义为滚刀刀刃宽,仿真得到的滚刀力与物理试验测试的滚刀力之差别在于是否考虑滚刀两侧摩擦力.本文研究滚刀在较小贯入度下的切削,此时摩擦力影响较小.根据仿真与试验滚刀力的数据做出误差分析,如表8所示.可见贯入度较大时,因摩擦力引入的误差会增大,平均误差为16.44%.这说明仿真得到的滚动力较为贴近工程实际情况.同时证明数值模型与试验试样的宏观物理参数一致性较高.图16 不同贯入度与切削速度下切削力变化曲线Fig.16 Cutting force with different cutting depth and speeds表8 不同掘进参数下的误差分析Tab.8 Error analysis under different cutting parameters贯入度/mm速度/(m·s-1)滚动力/kN仿真值试验值误差/%法向力/kN仿真值试验值误差/%40.61.431.5910.06 9.889.940.60 100.64.583.4632.3715.6913.8213.53 60.42.521.7444.83 10.68.5823.54 61.02.712.813.5612.2312.613.015 结论1)无节理切削组中,贯入度从4 mm 提高到10 mm会增加主干裂纹深度和破碎面积,但裂纹深度和破碎面积的增长速率会逐渐降低,且比能耗相应增加96%.相对法向力,滚刀的滚动力对贯入度更加敏感.施工中不能盲目增加贯入度,以免损坏刀架.2)无节理切削组中,当切削速度从0.4 m/s 提高到1.0 m/s时,滚刀法向力增加。
盾构刀具大解析

某刀盘实物照片
北京铁城建设监理有限责任公司
3
某 刀 盘 主 驱 动
刀 盘 驱 动 系 统 示 意 图
主 轴 承
刀 盘 搅 拌 结 构
搅拌棒
北京铁城建设监理有限责任公司
4
关于盾构机的刀盘、驱动机构等将在后边介 绍,因此这里主要介绍盾构机掘削地层的刀 具。
刀具布置和刀具形状在盾构机设计中是非常
北京铁城建设监理有限责任公司
ห้องสมุดไป่ตู้
海瑞克周边刀的刃口主要承受高应力 的磨粒磨损,周边刀迎土面钎焊有球齿, 球齿材料为硬质合金,主要用于承受砂 砾、卵石的磨粒磨损与冲击。
超 硬 钢 的 种 类 及 特 性 特性值 种 类 硬度 抗弯强度 (HRA) (MPa) E1 E2 E3 E4 E5 >90 >89 >88 >87 >86 >1200 >1400 >1600 >1700 >2000 化学成份(%) W C0 C 用途
北京铁城建设监理有限责任公司
25
(6) 滚刀
根据广州及深圳地铁建设经验,随着城市轨道路网 的延伸及建设力度的加大,盾构区间不仅需穿越常见的 软弱地层,同时还需在部分硬岩地段中通过。因此在刀 具选择上既要考虑在软岩中开挖的需要,也要考虑在硬 岩中的要求。一般认为刮刀适用于土层及部分软岩,盘 形滚刀适用于硬岩,其中单刃滚刀能用在强度很高的岩 石中,国外曾有在抗压强度超过200 MPa岩石中应用的工 程记录。
19
(2) 超前刀(也称先行刀)
顾名思义,超前刀即为先行切削土体的刀具。超前刀在设计中主 要考虑与切削刀组合协同工作。刀具切削土体时,超前刀在切削刀 切削土体之前先行切削土体,将土体切割分块,为切削刀创造良好 的切削条件。据其作用与目的,超前刀断面一般比切削刀断面小。 采用超前刀,一般可显著增加切削土体的流动性,大大降低切削刀 的扭矩,提高刀具切削效率,减少切削刀的磨耗。在松散体地层, 尤其是砂卵石地层使用效果十分明显。
岩石温度对盘形滚刀掘进参数破岩特性的影响
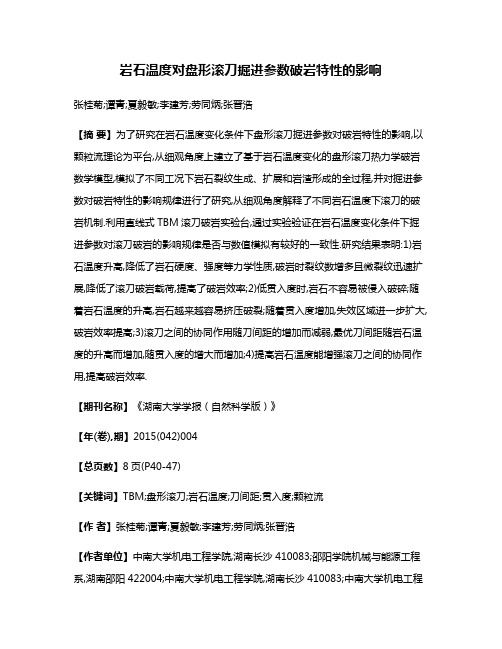
岩石温度对盘形滚刀掘进参数破岩特性的影响张桂菊;谭青;夏毅敏;李建芳;劳同炳;张晋浩【摘要】为了研究在岩石温度变化条件下盘形滚刀掘进参数对破岩特性的影响,以颗粒流理论为平台,从细观角度上建立了基于岩石温度变化的盘形滚刀热力学破岩数学模型,模拟了不同工况下岩石裂纹生成、扩展和岩渣形成的全过程,并对掘进参数对破岩特性的影响规律进行了研究,从细观角度解释了不同岩石温度下滚刀的破岩机制.利用直线式TBM滚刀破岩实验台,通过实验验证在岩石温度变化条件下掘进参数对滚刀破岩的影响规律是否与数值模拟有较好的一致性.研究结果表明:1)岩石温度升高,降低了岩石硬度、强度等力学性质,破岩时裂纹数增多且微裂纹迅速扩展,降低了滚刀破岩载荷,提高了破岩效率;2)低贯入度时,岩石不容易被侵入破碎;随着岩石温度的升高,岩石越来越容易挤压破裂;随着贯入度增加,失效区域进一步扩大,破岩效率提高;3)滚刀之间的协同作用随刀间距的增加而减弱,最优刀间距随岩石温度的升高而增加,随贯入度的增大而增加;4)提高岩石温度能增强滚刀之间的协同作用,提高破岩效率.【期刊名称】《湖南大学学报(自然科学版)》【年(卷),期】2015(042)004【总页数】8页(P40-47)【关键词】TBM;盘形滚刀;岩石温度;刀间距;贯入度;颗粒流【作者】张桂菊;谭青;夏毅敏;李建芳;劳同炳;张晋浩【作者单位】中南大学机电工程学院,湖南长沙410083;邵阳学院机械与能源工程系,湖南邵阳422004;中南大学机电工程学院,湖南长沙410083;中南大学机电工程学院,湖南长沙410083;高性能复杂制造国家重点实验室,湖南长沙 410083;中南大学机电工程学院,湖南长沙410083;中南大学机电工程学院,湖南长沙410083;中南大学机电工程学院,湖南长沙410083【正文语种】中文【中图分类】TP391.9;U455.39全断面岩石隧道掘进机(full face hard rock tunnel boring machine, 简称TBM)集大型化、自动化、高速化、流程化、精密化等特性于一体,广泛应用于铁路建设、南水北调、西气东输等隧道工程中.[1]盘形滚刀是TBM破碎岩石的主要刀具,其破岩效率直接影响隧道工程的开挖进度.在大埋深、长距离硬岩掘进环境中,TBM通常会受到复杂地质条件如高温、节理、岩溶、高地应力、掘进地层的自重应力、温度引起的热应力等因素的影响,使岩石表现出与浅部截然不同的物理力学特性,进而造成滚刀的损耗量大、破岩效率低、稳定性差等施工问题.[2]因此,在考虑这些掘进中的地质因素耦合作用下,提高滚刀的破岩效率,延长滚刀的使用寿命已经成为国内外专家学者研究的重要课题.针对不同温度条件下岩石的力学性能变化,国内外许多专家学者做了大量的研究工作:Vander Molen[3]就1980年以前的温度对岩石特性影响的主要研究成果做了系统的总结;Alm[4]等研究了花岗岩在不同温度条件下的力学性能及其微破裂性能;Chen等 [5]研究了在单轴压缩和疲劳载荷条件下温度对花岗岩力学性能的影响;Smithies等[6]探讨了不同温度下花岗岩岩石和岩浆的力学性质,如泊松比、弹性模量、断裂韧性、抗压强度以及岩石微破裂,获得了岩石力学性能随温度和时间的破坏机理;张志镇等[7]通过高温冷却加载以及实时高温加载下的单轴压缩试验,得到了两种加载方式下弹性模量、单轴抗压强度、剪切滑移应变及纵波波速等随温度的变化规律;左建平等[8]研究了不同温度对岩石的破坏规律以及变形的影响,建立了岩石在静载荷下温压耦合的破坏准则.盘形滚刀掘进参数(贯入度和刀间距)的合理设计是提高TBM破岩效率的关键因素,设计掘进参数时需综合考虑地质条件的影响.由于在不同的温度条件下,岩石表现出不同的力学特性以及破裂方式,因而针对岩石温度变化设计滚刀掘进参数具有一定的现实意义.研究掘进过程中刀具与岩石之间相互作用的工作状况与动态行为,揭示破岩机理及破碎特征,可为延长刀具的使用寿命、改善切削效果、提高破岩效率提供理论基础.为此,本文尝试在岩石温度及掘进参数变化的条件下,从岩体细观尺度出发,基于颗粒流离散元方法对盘形滚刀的破岩特性进行分析,研究不同岩石温度下滚刀掘进参数对破岩特性的影响,并进行数值模拟及实验验证,为TBM盘形滚刀的破岩机理研究提供一定的理论依据,同时对提高滚刀的破岩效率、增强滚刀的地质适应性和使用寿命,实现高效率、低能耗、低损耗的隧道掘进具有一定的理论价值和工程意义.1.1 岩石颗粒流方法颗粒流方法是一种离散单元法,其从细观角度的离散单元之间的相互作用,解释岩石的宏观变形等力学性质,对分析大位移、大变形以及非线性等相关的岩石问题具有显著的优势.颗粒离散元法可以解决研究对象在特定条件下的宏观变形与裂纹问题.其将离散单元分为颗粒以及块体两部分,根据单元之间的相互作用以及循环迭代求解整个颗粒集合体的行为.当两颗粒接触时,会产生位移重叠;根据力-位移定律和本构关系可以得到颗粒受到的力,进而获得颗粒的加速度、速度以及新的位移量,如此反复循环[9].式中:mi和Ji分别为颗粒单元的质量和转动惯量;和分别为颗粒单元的中心位置和角矢量;为颗粒单元i的相邻颗粒单元j对它的作用力;为到颗粒单元i的力臂;和分别为颗粒单元i的外力和外力矩;Ni为颗粒单元i的邻居单元数目;N为模型中颗粒单元的总数目.1.2 颗粒流热力学耦合计算模型在颗粒流方法中,采用与颗粒有关的热存储器以及与接触键有关的热管的细观模型来模拟宏观的温度场,热量在激活管道中通过激活的热存储器进行传递.当岩石样本模型中两颗粒的接触有重叠或存在接触键时,热存储器之间的热管被激活;当岩石样本模型在加载过程中不存在接触键或接触键断裂时,将影响活动热管的数量,进而改变材料的宏观热学特性[10].岩石、混凝土等材料的破坏可以看作颗粒之间接触键的断裂过程.1)颗粒流热力学基本方程.对于连续介质,假设物体的应变变化不会引起温度的改变,则热传导方程为:其中:qi为热流通量;qv为单位热功率密度;ρ为材料的密度;Cv为岩石材料的比热容;T为材料温度.依据傅里叶变换,连续介质的热流通量和温度梯度之间的关系为:其中:kij为材料的热传导率张量.对式(3)进行离散化,假设离散后的颗粒总体积为V,单位体积内的热流通量用qi的散度表示,则在颗粒体积V的热存储器上平均散度qi为:假设离散后材料的热量只在N个热管中流动,从而式(4)可以转换为:其中:下标p为与热管p相关的变量;为流经热管p的功率,此处可得离散化后的热传导方程:其中:Qv=Vqv,为离散化后的热源强度;m为离散化后的质量.在颗粒离散元中,假设单个热管的热阻为η,颗粒体中包含N个热管,总体积为V,由于热量只在热管内流通,则材料的平均热流通量为:其中:A(p)为热管的有效横截面积;l(p)为热管的长度.热管的热流通量为:其中ΔT为热管两端的温度差,与温度梯度的关系为:可得颗粒离散元中热传导率的张量kij表达式为:从式(10)可以看出,只要给定单位法向矢量、单个热管的长度、热阻及总热管数目等相关参数就可计算出颗粒离散元材料的热传导率.2)颗粒流热力学耦合方程.颗粒流程序中,主要通过颗粒元素之间接触键的热膨胀来描述颗粒材料的热应变,则宏观温度的变化引起的材料热应变可通过对颗粒半径的改变来实现.当宏观温度改变ΔT,可计算出颗粒半径的改变量ΔR=αRΔT.其中:α是指颗粒的热线性膨胀系数.假设两颗粒元素之间存在接触键且热管已经激活,则接触键的长度随着宏观温度的改变会产生相应的变化,从而影响颗粒的受力情况.当温度变化为ΔT时,随着接触键长度的改变,颗粒受到的法向力为其中为接触键的法向刚度;A为接触键的横截面面积;为颗粒材料的热膨胀系数.在实际数值模拟中,可通过对岩石材料加载不同的温度,来模拟岩石材料宏观热力学特性.1.3 盘形滚刀破岩效率盘形滚刀的破岩效率主要通过比能耗大小来体现,比能耗指滚刀切割单位体积岩石所做的功[11].式中:Es为破岩比能耗;Fv为滚刀所受平均垂直力;Fr为滚刀所受平均滚动力;d为贯入度;S为破碎块面积;l为滚刀的切削轨迹,只考虑滚刀侵入过程时l=0;V为岩屑体积,V=St,t为单位厚度.1.4 盘形滚刀侵入岩体模型本课题研究的岩石材料是从广州某地采购的花岗岩,为了使颗粒流样本能够反映真实岩石材料的宏观力学特性,需匹配岩石材料的细观参数与宏观力学特性,对材料的宏、细观参数进行标定.依据真实试验测得的数据,通过数值试验反复进行调节细观参数,直到试验表现出来的宏观特性与真实材料的宏观特性参数相一致,标定过程才算完成,标定过程参见文献[12-13]. 图1所示为双刀破岩的颗粒流模型,其中参数D为刀间距,d为贯入度.在数值模拟过程中,将盘形滚刀刀圈定义为刚体,刀圈轮廓用刚性墙(wall)模拟,文中采用的是应用较为广泛的近似常截面盘形滚刀,适应软到中硬岩地层,主要几何参数:刀刃顶部宽度10 mm,过渡圆弧半径4 mm,刀刃角20°.岩石试件尺寸为200 mm×400 mm,包含颗粒数目38 662个.利用软件自带fish语言,编制控制滚刀运动的伺服控制程序,通过改变岩石的温度参数及掘进参数,监测盘形滚刀破岩规律的变化.2.1 数值模拟2.1.1 破岩体积分析岩石温度对破岩体积的数值模拟结果进行统计分析,结果如图2所示.可以看出:在同一温度和刀间距条件下,随着贯入度的增加,岩石的破碎体积过度增大,因此破碎体积增加的幅度逐渐减少;在同一温度和贯入度条件下,破岩体积随刀间距的增加而增大,说明刀间距的增大增加了滚刀之间能够破碎的岩石体积,当滚刀之间的岩石裂纹贯通,相应的破岩体积增大,但当刀间距增加到一定程度时,裂纹会互不贯通,出现各自破岩现象;在同一刀间距和贯入度条件下,随着岩石温度的增加,岩石从无法交汇贯通逐渐过渡到贯通、过度破碎,说明岩石温度是影响滚刀破岩体积的一个因素,温度的增加造成了滚刀破岩载荷减少,同时促进岩石裂纹的扩展,相应的破岩体积也随着增大,其增加的幅度逐渐增大,说明温度的增加,引起岩石内部应力的减少,减少的幅度逐渐增大,岩石更加容易破碎,且破岩体积相应增大.2.1.2 破岩载荷分析根据数值结果对滚刀破岩平均载荷进行分析,结果如图3所示.可知,在相同岩石温度、贯入度条件下,滚刀的破岩载荷随着刀间距的增加逐渐增加,这是由于刀间距较小时,滚刀之间存在协同效应,滚刀受到的破岩载荷相对较小;刀间距逐渐增大,协同作用逐渐减弱,滚刀呈现各自破碎的状况,对应的破岩平均载荷也相应增大.在相同贯入度、刀间距条件下,随着温度的逐渐升高,滚刀的破岩平均载荷逐渐降低.这是由于温度的升高,增加了岩石内部的热应力,降低了岩石的断裂韧度以及强度,使得岩石更加容易破裂,并且增大了滚刀之间的协同效应,滚刀平均载荷也逐渐降低.2.1.3 破岩比能耗分析对数值模拟的破碎体积和破岩平均载荷进行统计,计算各工况条件下的破岩比能耗,结果如图4所示.可以看出:在相同贯入度和岩石温度条件下,滚刀破岩比能耗随刀间距的增加呈现先减小后增大的趋势,说明在该工况下存在一个最优刀间距,使得滚刀的破岩比能耗最小.在常温和贯入度d=4 mm时,岩石的破碎模式从裂纹贯通过渡到没有贯通,刀间距的增加,使得破岩体积和破岩载荷增大,但增大的幅度不一样,开始破岩载荷增大的幅度比破岩体积增大的幅度小,滚刀破岩比能耗随刀间距的增大而逐渐减小.随着刀间距进一步增大,岩石裂纹从贯通过渡到不贯通,滚刀之间的协同作用减弱,滚刀的破岩比能耗随之增大,并且破岩体积由于裂纹没有贯通而变得很小,滚刀的破岩比能耗随刀间距的增大而逐渐增大.在同一贯入度以及刀间距下,随着岩石温度的升高,使得岩石更加容易侵入,岩石更加容易破碎,滚刀的破岩比能耗逐渐减小,对应的最小比能耗即最优刀间距则增大到150 ℃时的80 mm,如图4(a)所示.贯入度为8 mm时,由于滚刀贯入度的增大,滚刀之间的协同效应相对增大,破岩比能耗逐步增加,裂纹从不贯通过渡到刚好贯通最终为过度破碎状态,滚刀的破碎体积逐渐增大,同时滚刀的破岩比能耗也增大,增大的幅度比破岩体积大,因此,滚刀的破岩比能耗增大, 如图4(b)所示.2.2 实验验证2.2.1 实验装置采用实验方法可以准确获得特定参数对盘形滚刀破岩特性的影响,更直观地再现不同岩石温度下滚刀掘进参数变化对破岩特性的影响.因此,通过模拟实验对不同岩石温度条件下滚刀破岩过程进行研究,分析相应的破岩特性,与数值模拟结果进行对比以验证其合理性,有助于全面研究盘形滚刀在不同岩石温度下掘进参数变化的破岩特性.为了使实验模拟接近实际施工条件,课题组自主设计了直线式TBM滚刀破岩实验台,如图5所示.实验台主要由油缸、导向机构、导轨、横梁、岩石料仓、液压站、操作台等部分组成.2.2.2 实验方法实验通过直线式TBM滚刀破岩实验台对不同岩石温度下改变掘进参数对破岩过程进行研究,了解滚刀破岩的动态特性.岩石加热装置如图6所示,加热时将其放置于岩石上,使加热板与岩土直接接触,通电后加热棒产生热量通过加热板传递给岩石;铁制上板和铝制下板对加热板的位置固定进行夹紧,阻止热量往铁板传递.依次进行25,50,75,100,125和150 ℃下滚刀的破岩实验;采用三向力传感器记录不同工况条件下滚刀的破岩载荷,转换成电压信号后通过数据采集卡采集数据;实验过程中,观察滚刀破岩现象,记录滚刀破岩载荷、破岩体积、岩石的裂纹扩展规律以及岩渣破碎块度,计算破岩比能耗;最后通过Lab View进行数据分析,分析刀间距及贯入度变化对滚刀破岩特性的影响.2.2.3 实验结果分析1)破岩载荷分析图7所示为当D=4 mm,d=80 mm时,不同岩石温度下滚刀破岩载荷的仿真值与实验值对比曲线.可以看出:随着岩石温度的升高,滚刀的破岩载荷逐渐下降,并呈现一定的阶跃性,这与数值仿真得出的变化规律基本一致.这表明岩石温度是影响盘形滚刀破岩效率的一个关键因素,岩石温度的升高会使岩石内部产生新的微裂纹或使原有微裂纹进一步扩展,改变了岩石的强度及硬度,从而导致破岩载荷的改变.通过图7可以看出仿真值与实验值之间存在一定的误差,这主要是由于数值仿真实验中只对岩石局部进行加热,没有整体加热,且岩石加热后到切削有一定的时间差,使得岩石有一定的热量散失.2)破岩现象分析图8所示为双滚刀共同破岩时,不同工况下岩石破碎情况.可以看出:刀间距为60 mm时,滚刀之间的协同作用较强,滚刀之间的岩石被完全破碎,形成许多小块的岩渣,岩石过度破碎,岩石温度越高,破碎块度越小,如图8(a)和(b)所示;刀间距为80 mm时,滚刀之间的协同作用减弱,刀间岩石裂纹基本贯通,产生大块的岩渣,岩石温度越高,破碎效率越好,如图8(c)和(d)所示;刀间距为100 mm 时,滚刀之间的协同作用较差,温度较低时,滚刀下方出现两条互不交汇的压痕,呈现各自破碎状态,岩石温度越高,压痕越明显,产生大量粉末状岩渣,出现过度破碎现象,能量耗损过大,破岩效率反而降低,如图8(e)和(f)所示.总之岩石温度的升高能增强滚刀之间的协同作用,提高滚刀的破岩效率.根据实验破碎模式的统计结果,可以看出其变化规律与数值模拟所得出的岩石破碎规律基本一致,从而验证了数值仿真的可靠性以及可行性.3)破岩效率分析采用精密电子秤对各工况下滚刀的破岩量进行称量,并进行记录和统计,再根据岩石材料的质量,可以获得滚刀的破岩体积,利用公式(13)计算出各工况下的破岩比能耗.表1所示为各工况下的破岩比能耗实验值与仿真值.可以看出:1)在同一岩石温度下,随着滚刀之间岩石裂纹从没有贯通到刚好贯通,比能耗逐渐减小;随着岩石裂纹从刚好贯通到过渡破碎,比能耗增加,即存在一个最优刀间距破岩比能耗最小,其数值大概在80 mm左右;在相同刀间距和岩石温度下,贯入度越大,破岩效率越高.2)在同一刀间距下,随着温度的升高,岩石裂纹从无贯通到交汇贯通,再到过度破碎,比能耗先减小后上升,说明岩石温度是影响比能耗的一个因素,随着温度的升高,最优刀间距逐渐升高.由于仿真过程中所用的离散元颗粒模型是二维的,被设置为刚体的滚刀不可破坏和磨损,滚刀切削条件是在理想工况条件下进行的,没有受到来自外部无关条件的干扰,而在破岩实验过程中,滚刀会存在磨损,且实验条件如滚刀的加载、岩石的加热以及测试条件等受外界条件干扰的影响,因此仿真值与实验值存在一定的误差,但在允许范围内.1)滚刀的破岩载荷随贯入度的增加呈跃进破碎特性;随着岩石温度的升高,破岩载荷逐渐降低,岩石破碎体积增加.2)滚刀间距的增加,抑制了滚刀之间的协同作用,岩石裂纹不易交汇贯通,滚刀破岩呈现各自破碎模式;随着贯入度的增加,岩石裂纹从不交汇到刚好交汇贯通,最后到形成过度破碎的破碎模式,使得滚刀下方应力之间出现相互作用,减弱了滚刀之间岩石的强度,致使侧向裂纹扩展速度向两侧自由面增加.3)随着岩石温度的升高,岩石的强度以及破裂方式发生改变,岩石更加容易破碎,相同刀间距、贯入度条件下,相对于温度较低时岩石裂纹没有出现贯通,温度较高时已经出现贯通甚至过度贯通状态,滚刀的最优刀间距随岩石温度的升高而升高,随贯入度的增大而变大.总的来说,岩石温度的升高能增强滚刀之间的协同作用,使滚刀的破岩效率增高.这表明岩石温度是影响滚刀破岩特性的重要因素之一,基于岩石温度的滚刀掘进参数对破岩特性影响的研究具有一定工程实践价值.†通讯联系人,E-mail:**********************【相关文献】[1] 王梦恕. 中国铁路、隧道与地下空间发展概况[J]. 隧道建设, 2010, 30(4):351-364.WANG Meng-shu. An overview of development of railways, tunnels and underground works in China[J]. Tunnel Construction, 2010, 30(4):351-364. (In Chinese)[2] WANG L, KANG Y, CAI Z, et al. The energy method to predict disc cutter wear extent for hard rock TBMs [J]. Tunneling and Underground Space Technology, 2012, 28(4): 183-191.[3] VANDER MOLEN I. The shift of the α-β transition of associ ation with the thermal expression granite at high pressure [J]. Tectonophsics, 1981,73: 323-342.[4] ALM O, JAKTLUND L L. The influence of micro crack density on the elastic and fracture mechanical properties of Stripa granite [J]. Physics of the Earth and Planetary Interiors, 1985, 40:17-61.[5] CHEN Y L, NI J, SHAO W, et al. Experimental study on the influence of temperature on the mechanical properties of granite under uni-axial compression and fatigue loading [J].International Journal of Rock Mechanics and Mining Sciences, 2012, 56 (2): 62-69. [6] SMITHIES R H, HOWARD P M, KIRKLAND C L, et al. High-temperature granite magmatism [J]. Journal of Petrology, 2011,52(5):931-958.[7] 张志镇, 高峰, 徐小丽. 花岗岩力学特性的温度效应试验研究[J]. 岩土力学, 2011, 32(8):2346-2352.ZHANG Zhi-zhen, GAO Feng, XU Xiao-li. Experimental study of temperature effect of mechanical properties of granite[J]. Rock and Soil Mechanics, 2011, 32(8): 2346-2352. (In Chinese)[8] 左建平, 谢和平, 刘瑜杰, 等. 不同温度热处理后砂岩三点弯曲的断裂特性[J]. 固体力学学报, 2010,31(2):119-126.ZUO Jian-ping, XIE He-ping, LIU Yu-jie, et al. Investigation on fracture characteristics of sandstone after thermal effects through three bending point experiments[J]. Chinese Journal of Solid Mechanics, 2010,31(2):119-126. (In Chinese)[9] CHO N, MARTIN C D, SEGO D C. A clumped particle model for rock[J]. International Journal of Rock Mechanics and Mining Sciences, 2007, 44(7): 997-1010.[10]李建芳. 岩石温度对盘形滚刀破岩特性影响的研究[D]. 长沙:中南大学机电工程学院, 2014.LI Jian-fang. The research on influence of rock breaking mechanism by disc cutters under the temperature of rock[D]. Changsha: College of Mechanical and Electrical Engineering, Central South University, 2014. (In Chinese)[11]LIU H Y, KOU S Q, LINDQVIST P A. Numerical studies on bit-rock fragmentation mechanisms[J]. International Journal of Geomechanics, 2008, 8(1): 45-67.[12]徐孜军. 盾构刀具破岩特性的数值模拟及实验研究[D]. 长沙:中南大学, 2012: 43-46.XU Zi-jun. Numerical simulation and experimental study of rock breaking mechanism by shield machine cutters[D]. Changsha: Central South University, 2012: 43-46. (In Chinese) [13]赵衡, 曹文贵, 李翔. 考虑应变率影响的单轴受压岩石动态变形过程模拟[J]. 湖南大学学报:自然科学版, 2008, 35(8):14-18.ZHAO Heng, CAO Wen-gui, LI Xiang. Study on the simulation of the dynamic deformation process of uniaxial compressed rock with consideration of strain rate [J]. Journal of Hunan University: Natural Sciences, 2008, 35(8):14-18. (In Chinese)。
硬岩地质下镶齿滚刀齿形对破岩性能影响研究

硬岩地质下镶齿滚刀齿形对破岩性能影响研究
刘毅;曹殿彬;崔建波;彭宇星
【期刊名称】《中国测试》
【年(卷),期】2024(50)3
【摘要】为了降低镶齿滚刀的破岩比能耗和刀齿接触面应力,提高镶齿滚刀在硬岩地质下的破岩效率和使用寿命,采用LS-DYNA建立显示动力学仿真模型,并通过实验验证模型的可靠性。
仿真分析镶齿滚刀的破岩机理及不同齿形的破岩效率,确定较优的齿形。
通过正交试验法,分析齿宽、齿高、齿顶半径和齿数对破岩效率以及接触面应力值的影响,确定齿形参数对破岩性能影响权重。
研究结果表明:在118 MPa硬岩地质下,镐齿滚刀的破岩效率最高,齿顶半径为破岩效率的最主要影响因素,权重达到50%,齿数与齿顶高为接触面应力值的主要影响因素,权重分别占31%、36%。
齿形最优参数组合是齿宽为11 mm、齿顶高为1 mm、齿顶半径为10 mm、齿数为36个。
该研究对于镶齿滚刀的齿形选择及参数优化具有参考价值。
【总页数】8页(P62-68)
【作者】刘毅;曹殿彬;崔建波;彭宇星
【作者单位】济南轨道交通集团有限公司;中南大学轻合金研究院
【正文语种】中文
【中图分类】TU63;TB9
【相关文献】
1.反井钻井镐形镶齿滚刀破岩试验研究
2.排齿间距对镶齿滚刀破岩效果影响试验研究
3.球型镶齿滚刀参数对破岩比能影响性研究
4.镶齿滚刀破岩机理及效率的旋转破岩试验
5.硬岩大直径钻机用球齿滚刀破岩分析
因版权原因,仅展示原文概要,查看原文内容请购买。
隧道掘进机滚刀对岩石破碎的影响研究

隧道掘进机滚刀对岩石破碎的影响研究
郁歆鸿;高金铭;王旭
【期刊名称】《技术与市场》
【年(卷),期】2024(31)6
【摘要】随着隧道掘进技术的逐步发展,盾构法已经逐步取代爆破法成为隧道掘进作业的主流技术。
首先分析了岩石表面破碎的4个过程。
然后,通过多功能振动接触试验机建立滚刀破岩石的试验环境,研究了滚刀刃角、刃宽和刃形的变化对破岩效果方面的影响。
综合不同滚刀在粗糙度指数和比能耗方面的试验结果认为:在刃角方面,0°刃角的滚刀更适合于硬岩掘进;在刃宽方面,刃宽越大,破岩效果相对越好;在刃形方面,平头刀有着较好的破岩效果,但弧形刀的能耗更低。
【总页数】3页(P101-103)
【作者】郁歆鸿;高金铭;王旭
【作者单位】黑龙江工商学院
【正文语种】中文
【中图分类】U45
【相关文献】
1.隧道掘进机滚刀在刀盘上的固定方式研究
2.全断面岩石隧道掘进机滚刀磨损影响因素分析
3.全断面岩石掘进机平面刀盘上盘形滚刀磨损研究
4.极硬岩隧道工程中双护盾隧道掘进机刀盘设计与滚刀磨损分析
5.全断面隧道掘进机锥面刀盘滚刀破岩机制研究
因版权原因,仅展示原文概要,查看原文内容请购买。
岩石脆性研究现状
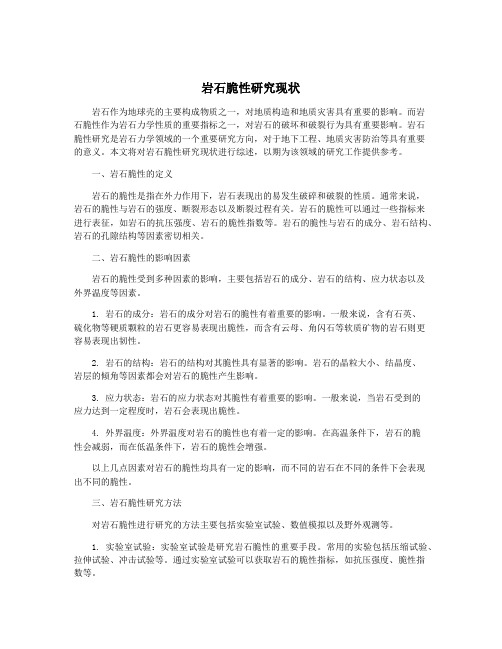
岩石脆性研究现状岩石作为地球壳的主要构成物质之一,对地质构造和地质灾害具有重要的影响。
而岩石脆性作为岩石力学性质的重要指标之一,对岩石的破坏和破裂行为具有重要影响。
岩石脆性研究是岩石力学领域的一个重要研究方向,对于地下工程、地质灾害防治等具有重要的意义。
本文将对岩石脆性研究现状进行综述,以期为该领域的研究工作提供参考。
一、岩石脆性的定义岩石的脆性是指在外力作用下,岩石表现出的易发生破碎和破裂的性质。
通常来说,岩石的脆性与岩石的强度、断裂形态以及断裂过程有关。
岩石的脆性可以通过一些指标来进行表征,如岩石的抗压强度、岩石的脆性指数等。
岩石的脆性与岩石的成分、岩石结构、岩石的孔隙结构等因素密切相关。
二、岩石脆性的影响因素岩石的脆性受到多种因素的影响,主要包括岩石的成分、岩石的结构、应力状态以及外界温度等因素。
1. 岩石的成分:岩石的成分对岩石的脆性有着重要的影响。
一般来说,含有石英、硫化物等硬质颗粒的岩石更容易表现出脆性,而含有云母、角闪石等软质矿物的岩石则更容易表现出韧性。
2. 岩石的结构:岩石的结构对其脆性具有显著的影响。
岩石的晶粒大小、结晶度、岩层的倾角等因素都会对岩石的脆性产生影响。
3. 应力状态:岩石的应力状态对其脆性有着重要的影响。
一般来说,当岩石受到的应力达到一定程度时,岩石会表现出脆性。
4. 外界温度:外界温度对岩石的脆性也有着一定的影响。
在高温条件下,岩石的脆性会减弱,而在低温条件下,岩石的脆性会增强。
以上几点因素对岩石的脆性均具有一定的影响,而不同的岩石在不同的条件下会表现出不同的脆性。
三、岩石脆性研究方法对岩石脆性进行研究的方法主要包括实验室试验、数值模拟以及野外观测等。
1. 实验室试验:实验室试验是研究岩石脆性的重要手段。
常用的实验包括压缩试验、拉伸试验、冲击试验等。
通过实验室试验可以获取岩石的脆性指标,如抗压强度、脆性指数等。
2. 数值模拟:数值模拟是利用计算机对岩石脆性进行研究的手段。
TBM岩渣几何特征与滚刀破岩效率相关性分析

TBM岩渣几何特征与滚刀破岩效率相关性分析
张春瑜
【期刊名称】《施工技术(中英文)》
【年(卷),期】2024(53)7
【摘要】在运用TBM进行隧道挖掘施工中,TBM破岩效率会受到围岩状况以及机械参数的影响。
因此岩体不同节理间距、倾角以及滚刀间距对破岩工作效率的影响值得关注。
首先,利用室内滚刀试验,在固定岩体节理倾角、间距或滚刀间距其中一个参数的条件下,对另外两个参数变化生成岩渣的粗糙度指数的变化规律进行模拟,分析和总结岩渣的形状与破岩效率之间的关系以及不同条件下TBM掘进产生的岩渣特征。
再依托广州北江输水隧洞工程,现场量测该隧洞开挖施工过程中产生的岩渣,并对其进行筛分试验,然后分析统计数据,得出了不同围岩性质下TBM刀盘的磨损规律与岩渣粗糙度指数及颗粒级配系数之间的相关性。
最后,把岩渣的粗糙度指数、扁平度与比能分别进行拟合,进一步说明节理倾角与间距对滚刀破岩效率的影响。
【总页数】7页(P85-91)
【作者】张春瑜
【作者单位】中铁十八局集团隧道工程有限公司
【正文语种】中文
【中图分类】U459
【相关文献】
1.不同贯入度下铁路隧道TBM盘形滚刀的破岩效率分析
2.不同围压下节理岩体中TBM滚刀破岩效率研究
3.不同结构参数TBM盘形滚刀的破岩效率分析
4.高压水刀辅助TBM滚刀破岩效率室内模型试验
5.盘形滚刀对TBM破岩效率的影响参数分析及优化设计
因版权原因,仅展示原文概要,查看原文内容请购买。
盾构机滚刀
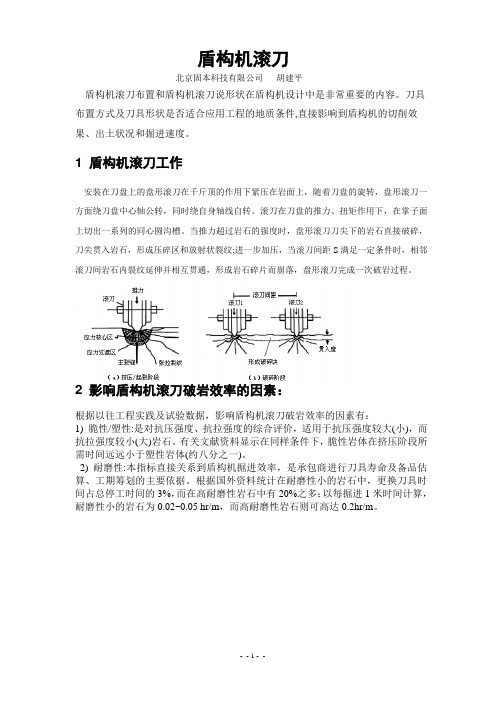
盾构机滚刀北京固本科技有限公司胡建平盾构机滚刀布置和盾构机滚刀说形状在盾构机设计中是非常重要的内容。
刀具布置方式及刀具形状是否适合应用工程的地质条件,直接影响到盾构机的切削效果、出土状况和掘进速度。
1 盾构机滚刀工作安装在刀盘上的盘形滚刀在千斤顶的作用下紧压在岩面上,随着刀盘的旋转,盘形滚刀一方面绕刀盘中心轴公转,同时绕自身轴线自转。
滚刀在刀盘的推力、扭矩作用下,在掌子面上切出一系列的同心圆沟槽。
当推力超过岩石的强度时,盘形滚刀刀尖下的岩石直接破碎,刀尖贯入岩石,形成压碎区和放射状裂纹;进一步加压,当滚刀间距S满足一定条件时,相邻滚刀间岩石内裂纹延伸并相互贯通,形成岩石碎片而崩落,盘形滚刀完成一次破岩过程。
2 影响盾构机滚刀破岩效率的因素:根据以往工程实践及试验数据,影响盾构机滚刀破岩效率的因素有:1) 脆性/塑性:是对抗压强度、抗拉强度的综合评价,适用于抗压强度较大(小),而抗拉强度较小(大)岩石。
有关文献资料显示在同样条件下,脆性岩体在挤压阶段所需时间远远小于塑性岩体(约八分之一)。
2) 耐磨性:本指标直接关系到盾构机掘进效率,是承包商进行刀具寿命及备品估算、工期筹划的主要依据。
根据国外资料统计在耐磨性小的岩石中,更换刀具时间占总停工时间的3%,而在高耐磨性岩石中有20%之多;以每掘进1米时间计算,耐磨性小的岩石为0.02~0.05 hr/m,而高耐磨性岩石则可高达0.2hr/m。
3.双刃盾构机滚刀刀具的磨损及原因:(1)正常磨损刀具的正常磨损是指刀圈的磨损量超过了规定值,磨损量可用专用的量具进行测量。
2)刀圈偏磨如果滚刀在掘进工作面不转动,由于刀圈和掘进工作面的相对运动就会形成刀圈的偏磨。
由于中心区滚刀线速度较小,承受载荷较大,中心区滚刀容易出现此现象。
3)刀圈挡圈磨损或脱落挡圈是由两个半圆的钢环安装在滚刀轴的卡槽里焊接成一个完整的圆环,其作用是防止刀圈从滚刀轴上脱落,一旦刀圈挡圈脱落或焊接处磨损严重,就应该更换刀具。
- 1、下载文档前请自行甄别文档内容的完整性,平台不提供额外的编辑、内容补充、找答案等附加服务。
- 2、"仅部分预览"的文档,不可在线预览部分如存在完整性等问题,可反馈申请退款(可完整预览的文档不适用该条件!)。
- 3、如文档侵犯您的权益,请联系客服反馈,我们会尽快为您处理(人工客服工作时间:9:00-18:30)。
第35卷第3期岩石力学与工程学报V ol.35 No.3 2016年3月Chinese Journal of Rock Mechanics and Engineering March,2016评价岩石脆性指标对滚刀破岩效率的影响刘泉声1,2,刘建平1,时凯3,潘玉丛1,黄兴1,刘学伟1,魏莱1(1. 中国科学院武汉岩土力学研究所岩土力学与工程国家重点实验室,湖北武汉 430071;2. 武汉大学土木建筑工程学院岩土与结构工程安全湖北省重点实验室,湖北武汉 430072;3. 碧桂园控股有限公司营销中心,广东广州 528000)摘要:脆性是岩石重要的力学性质之一。
岩石脆性与滚刀破岩效率密切相关,但目前还没有统一的用于评价滚刀破岩效率的岩石脆性指标。
总结现有的35种脆性指标,将其分为基于强度、应变、应变能、硬度、莫尔包络线、特殊试验和其他等7种类型。
为研究岩石脆性与滚刀破岩效率之间的关系,通过滚刀贯入试验,引入归一化比能概念,提出表征岩石脆性的新指标,重点研究基于强度和贯入试验的脆性指标与归一化比能之间的关系。
试验结果表明:(1) 滚刀更难贯入高强度岩石;(2) 脆性指标B2和B4与归一化比能之间呈强烈的指数函数关系,随着脆性的增高,归一化比能降低,滚刀破岩效率增高,应优先选用脆性指标B2来评价滚刀破岩效率,其次是脆性指标B4;(3) 将单轴抗压强度约20 MPa定义为单轴抗压强度过渡值,滚刀不适宜切削单轴抗压强度小于20 MPa的软岩。
试验结果对评价滚刀破岩效率时岩石脆性指标的选取具有一定的指导意义。
关键词:岩石力学;脆性指标;盘形滚刀;贯入试验;破岩效率中图分类号:TU 45 文献标识码:A 文章编号:1000–6915(2016)03–0498–13Evaluation of rock brittleness indexes on rock fragmentationefficiency by disc cutterLIU Quansheng1,2,LIU Jianping1,SHI Kai3,PAN Yucong1,HUANG Xing1,LIU Xuewei1,WEI Lai1 (1. State Key Laboratory of Geomechanics and Geotechnical Engineering,Institute of Rock and Soil Mechanics,Chinese Academy of Sciences,Wuhan,Hubei 430071,China;2.Key Laboratory of Safety for Geotechnical and Structural Engineering of Hubei Province,School of Civil Engineering,Wuhan University,Wuhan,Hubei 430072,China;3. Marketing Center of Country Garden Holdings Company Limited,Guangzhou,Guangdong 528000,China)Abstract:Brittleness is one of the most important mechanical properties of rock. The fragmentation efficiency of rock is closely related to the rock brittleness. No unified brittleness index of rock is confirmed in evaluating rock fragmentation efficiency by disc cutter. The existing 35 different brittleness indices were summarized and classified into seven categories with respect to strength,strain,strain energy,hardness,Mohr envelope,special tests,etc. In order to study the relations between the rock brittleness and the rock fragmentation efficiency by disc cutter,the normalized specific energy concept was introduced after carrying out the indentation tests with disc cutter,and a new index of rock brittleness was proposed. In addition,the relations between the normalized specific energy and brittleness indexes based on strength and indentation test were mainly studied. The results show that it收稿日期:2015–05–04;修回日期:2015–07–22基金项目:国家重点基础研究发展计划(973)项目(2014CB046903,2015CB058102);湖北省自然科学基金重点项目(2011CDA119)Supported by the National Key Basic Research and Development Program of China(973 Program)(Grants No. 2014CB046903 and 2015CB058102) and Key Program of Natural Science Foundation of Hubei Province(Grant No. 2011CDA119)作者简介:刘泉声(1962–),男,博士,1983年毕业于山东矿业学院矿井建设专业,现任研究员、博士生导师,主要从事岩土与地下工程方面的教学与研究工作。
E-mail:liuqs@DOI:10.13722/ki.jrme.2015.0569第35卷 第3期 刘泉声等:评价岩石脆性指标对滚刀破岩效率的影响 • 499 •is more difficult to penetrate into the rock of high strength for disc cutter. The relationships between the normalized specific energy and brittleness indexes B 2 and B 4 were found to be exponential. With the increasing of brittleness indexes B 2 and B 4,the normalized specific energy decreased but the rock fragmentation efficiency increased. Therefore ,the brittleness index B 2 can be firstly used for evaluating the rock fragmentation efficiency ,followed with the brittleness index B 4. The uniaxial compressive strength of about 20 MPa can be defined as the transitional uniaxial compressive strength ,and disc cutter may be not suitable for cutting the soft rock with uniaxial compressive strength less than 20 MPa.Key words :rock mechanics ;brittleness index ;disc cutter ;indentation test ;rock fragmentation efficiency1 引 言国民经济快速可持续发展迫切需要建设一大批重大生命线工程,如高速铁路、跨流域调水工程和深部矿产开采等,而深埋长大隧道是这些生命线工程的关键控制性工程。
隧道掘进机(TBM)因其开挖快、优质、安全、经济、环保和劳动强度低等优点[1],广泛应用于岩石隧道开挖。
目前TBM 工法已基本成为深埋长大隧道的标准施工方法。
工程实践中准确预测特定地质条件下的TBM 施工性能对于隧道施工方法选择、施工进度安排和成本估计至关重要。
然而,影响TBM 施工性能的因素众多,可以分为两大类:一是机器参数,包括单刀推力、刀盘转速、刀具直径、刀间距、刀尖宽度和滚刀岩石接触角等;二是岩体参数,包括岩石脆性、岩石单轴抗压强度、不连续面(弱面)间距以及不连续面(弱面)和隧道轴向之间的夹角等。
其中,机器参数为可控参数,而岩体参数为不可控参数。
对TBM 施工中出现的不同岩体参数进行准确地评估和表征,选择合理的机器参数以实现安全高效掘进破岩一直是TBM 研究领域的热点和前沿话题。
岩石脆性显著影响岩石的可切削性、可钻性和可掘性。
可切削性主要用于评价割煤机的切削性能,可钻性主要用于评价钻机钻进的难易程度,可掘性则主要用于评价TBM 的施工效率。
I. Evans 和C. D. Pomeroy [2]研究发现,刀具冲击能与岩石脆性成反比。
S. P. Singh [3-4]指出,煤岩的可切削性和普氏强度指数与其脆性密切相关,且煤岩切削比能与其脆性成正比。
R. M. Goktan [5]研究发现,相比低脆性岩石,高脆性岩石破坏时比能更低。
基于不同研究人员的原始试验数据,R. Altindag [6-7]运用回归分析方法,研究3种不同脆性指标(2B ,3B 和4B )与岩石可钻性指数DI 和比能SE 之间的关系,发现可钻性指数DI 与脆性指标2B 之间无相关性,比能SE 与脆性指标2B ,3B 之间无相关性,但可钻性指数DI 和比能SE 与脆性指标4B 之间显著相关,因此可选用脆性指标4B 来分析岩石切削效率。
S. Kahraman 和R. Altindag [8]基于收集的原始数据,研究断裂韧性IC K 与脆性指标3B ,3B 之间的关系,发现脆性指标3B 可用于评估断裂韧性。