氧化铜矿的氨浸
云南某氧化铜矿氨浸液萃取工艺

和 蒸 馏 水 配 成 含 铜 3 / 含 硫 酸 2 0g L 的 液 体 5g L, 0 /
作 为反萃 水相 , 以模 拟生 产 实 际 中 的电 积贫 液 。萃 取、 洗涤 、 反萃试 验均在 2 0mL分 液漏斗 中进行 。 5
1 2 试 验 过 程 .
图 1 萃 取 一反萃试 验流程
M A iwe Ca— n,Z OU n — u H Qig h a
( c l y o s ur e En i e rn Fa u t fRe o c g n e i g,Ku mi g Unie s t fSce c nd Te h o o y,Ku mi g 6 0 9 n n v r i o in e a c n l g y n n 5 0 3,Chi a n )
到萃取 剂 的供货 条件 , 验选 用 Lx 4工作萃取 剂 。 试 i8 一
针 对 一 段 浸 出液 与 二段 浸 出 液及 洗 涤 液 中 , 含
铜 量 和含 氨量均 不相 同。为此 提 出分流 萃取 的工艺
流程 , 开展 试验 并确 定萃 取过 程 的其 他 工艺参 数 。
电积 ” 艺 来 处 理 。氨 浸 试 验 表 明¨ , 靠 单 段 氨 工 1 仅 ] 浸 , 常温 常压下 强 化 其 工 艺 条 件 不足 以较 大 幅度 在
( 明理 工 大 学 国土 资 源 工 程 学 院 , 明 6 0 9 ) 昆 昆 5 0 3
高碱性氧化铜矿石的氨浸
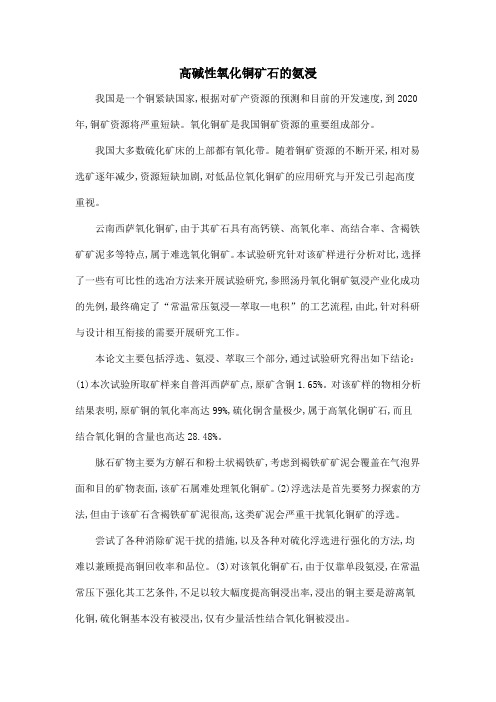
高碱性氧化铜矿石的氨浸我国是一个铜紧缺国家,根据对矿产资源的预测和目前的开发速度,到2020年,铜矿资源将严重短缺。
氧化铜矿是我国铜矿资源的重要组成部分。
我国大多数硫化矿床的上部都有氧化带。
随着铜矿资源的不断开采,相对易选矿逐年减少,资源短缺加剧,对低品位氧化铜矿的应用研究与开发已引起高度重视。
云南西萨氧化铜矿,由于其矿石具有高钙镁、高氧化率、高结合率、含褐铁矿矿泥多等特点,属于难选氧化铜矿。
本试验研究针对该矿样进行分析对比,选择了一些有可比性的选冶方法来开展试验研究,参照汤丹氧化铜矿氨浸产业化成功的先例,最终确定了“常温常压氨浸—萃取—电积”的工艺流程,由此,针对科研与设计相互衔接的需要开展研究工作。
本论文主要包括浮选、氨浸、萃取三个部分,通过试验研究得出如下结论:(1)本次试验所取矿样来自普洱西萨矿点,原矿含铜1.65%。
对该矿样的物相分析结果表明,原矿铜的氧化率高达99%,硫化铜含量极少,属于高氧化铜矿石,而且结合氧化铜的含量也高达28.48%。
脉石矿物主要为方解石和粉土状褐铁矿,考虑到褐铁矿矿泥会覆盖在气泡界面和目的矿物表面,该矿石属难处理氧化铜矿。
(2)浮选法是首先要努力探索的方法,但由于该矿石含褐铁矿矿泥很高,这类矿泥会严重干扰氧化铜矿的浮选。
尝试了各种消除矿泥干扰的措施,以及各种对硫化浮选进行强化的方法,均难以兼顾提高铜回收率和品位。
(3)对该氧化铜矿石,由于仅靠单段氨浸,在常温常压下强化其工艺条件,不足以较大幅度提高铜浸出率,浸出的铜主要是游离氧化铜,硫化铜基本没有被浸出,仅有少量活性结合氧化铜被浸出。
因此采用两段氨浸。
在适宜的工艺条件下,其第二段浸出率可达到6.54%,使总铜浸出率由52.04%升为58.58%。
(4)针对萃取体系中有机相和电积液循环使用的特点,用McCabe—Thiele等温线法,推算了萃取和反萃过程中各产物的含铜浓度变化,得出了二级萃取和一级反萃的流程。
(5)氨浸和过滤作业的氨挥发损失较小,在经济上有利于萃余液在循环使用中少补加氨;反萃前的洗涤作业,可以保证氨被洗下,而铜不被洗脱,这便于外排洗氨水,以缓解体系的水膨胀。
不同氨-铵浸出体系对氧化铜矿铜浸出率影响规律的研究
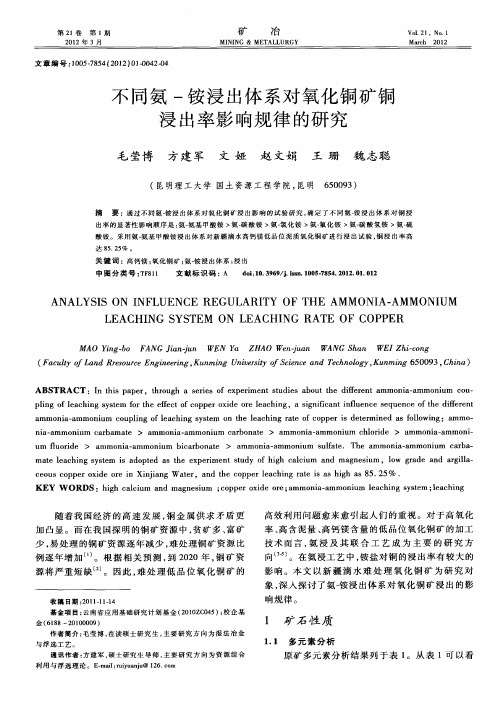
酸铵。采用氨一 氨基 甲酸 铵 浸 出体 系对 新 疆 滴 水 高 钙镁 低 品 位 泥 质 氧 化 铜 矿 进 行 浸 出 试 验 , 浸 出 率 高 铜
达 8.5 。 52%
关 键 词 :高 钙镁 ; 氧化 铜 矿 ; . 浸 出体 系 ; 出 氨铵 浸
中图 分 类 号 : F 1 T8 1
c o sc p e xd r nXij n tr n h o p rla hn aei a ih a 5 2 % . e u o p ro ieo ei ni gWae .a dt ec p e e c ig rt s shg s8 . 5 a
K EY O RD S: h g ac u a d m a n su W ih c l i m n g e i m ; o p ro i e o e; m mo i — mm o um e c i y t m ;e c i g c p e xd r a naa ni la hng s se la h n
MAO Yn -o F NG Ja - n WE Y Z AO We - a W NG S a WE h —o g ig b A inj u N a H nj n u A hh IZ ic n
( aut o a dR e uc n ie ig K n n n e i c ne n eh ooy K n ig6 0 9 , hn ) F cl L n rs r E gne n , u mi U i r t o Si c dTcn l , u m n 5 0 3 C ia yf o e r g v syf e a g
第2 l卷
第 1期
矿
冶
V0 . . N0 1 I21 . Mac 2 2 rh 01
刚果(金)氧化铜矿碳酸铵浸出—负压蒸氨的工艺研究的开题报告
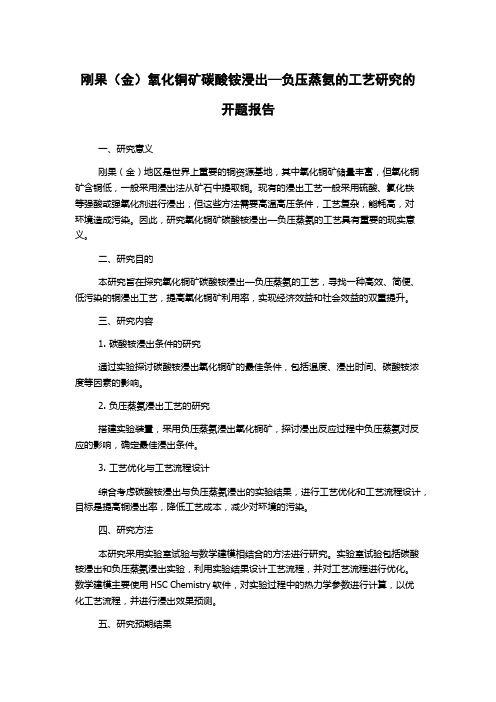
刚果(金)氧化铜矿碳酸铵浸出—负压蒸氨的工艺研究的开题报告一、研究意义刚果(金)地区是世界上重要的铜资源基地,其中氧化铜矿储量丰富,但氧化铜矿含铜低,一般采用浸出法从矿石中提取铜。
现有的浸出工艺一般采用硫酸、氯化铁等强酸或强氧化剂进行浸出,但这些方法需要高温高压条件,工艺复杂,能耗高,对环境造成污染。
因此,研究氧化铜矿碳酸铵浸出—负压蒸氨的工艺具有重要的现实意义。
二、研究目的本研究旨在探究氧化铜矿碳酸铵浸出—负压蒸氨的工艺,寻找一种高效、简便、低污染的铜浸出工艺,提高氧化铜矿利用率,实现经济效益和社会效益的双重提升。
三、研究内容1. 碳酸铵浸出条件的研究通过实验探讨碳酸铵浸出氧化铜矿的最佳条件,包括温度、浸出时间、碳酸铵浓度等因素的影响。
2. 负压蒸氨浸出工艺的研究搭建实验装置,采用负压蒸氨浸出氧化铜矿,探讨浸出反应过程中负压蒸氨对反应的影响,确定最佳浸出条件。
3. 工艺优化与工艺流程设计综合考虑碳酸铵浸出与负压蒸氨浸出的实验结果,进行工艺优化和工艺流程设计,目标是提高铜浸出率,降低工艺成本,减少对环境的污染。
四、研究方法本研究采用实验室试验与数学建模相结合的方法进行研究。
实验室试验包括碳酸铵浸出和负压蒸氨浸出实验,利用实验结果设计工艺流程,并对工艺流程进行优化。
数学建模主要使用HSC Chemistry软件,对实验过程中的热力学参数进行计算,以优化工艺流程,并进行浸出效果预测。
五、研究预期结果通过本研究,预期得出以下结果:1. 探讨出碳酸铵浸出与负压蒸氨浸出的工艺参数,并确定最佳的浸出条件。
2. 设计出工艺流程,以提高铜浸出率,降低工艺成本与环境污染。
3. 完成工艺优化的数学模型,可以进行浸出效果的预测,为实际生产提供指导和参考。
六、研究进度计划1. 第一阶段(1月至3月):文献调研与实验室试验设备准备。
2. 第二阶段(4月至6月):氧化铜矿碳酸铵浸出实验。
3. 第三阶段(7月至9月):氧化铜矿负压蒸氨浸出实验与工艺流程设计。
东川某难选氧化铜矿石氨基甲酸铵浸出试验研究
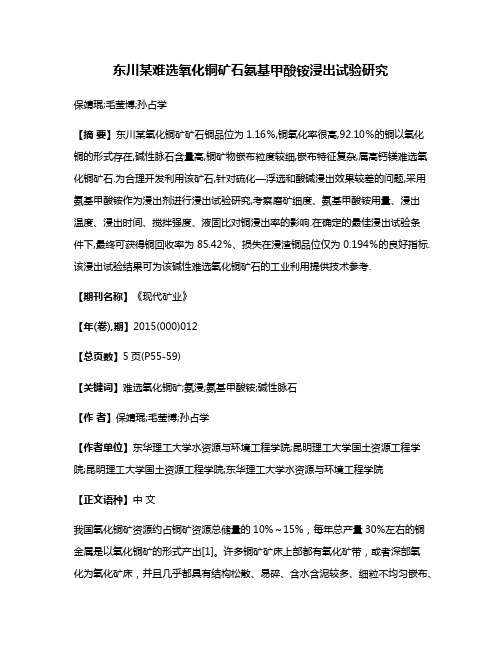
东川某难选氧化铜矿石氨基甲酸铵浸出试验研究保靖琨;毛莹博;孙占学【摘要】东川某氧化铜矿矿石铜品位为1.16%,铜氧化率很高,92.10%的铜以氧化铜的形式存在,碱性脉石含量高,铜矿物嵌布粒度较细,嵌布特征复杂,属高钙镁难选氧化铜矿石.为合理开发利用该矿石,针对硫化—浮选和酸碱浸出效果较差的问题,采用氨基甲酸铵作为浸出剂进行浸出试验研究,考察磨矿细度、氨基甲酸铵用量、浸出温度、浸出时间、搅拌强度、液固比对铜浸出率的影响.在确定的最佳浸出试验条件下,最终可获得铜回收率为85.42%、损失在浸渣铜品位仅为0.194%的良好指标.该浸出试验结果可为该碱性难选氧化铜矿石的工业利用提供技术参考.【期刊名称】《现代矿业》【年(卷),期】2015(000)012【总页数】5页(P55-59)【关键词】难选氧化铜矿;氨浸;氨基甲酸铵;碱性脉石【作者】保靖琨;毛莹博;孙占学【作者单位】东华理工大学水资源与环境工程学院;昆明理工大学国土资源工程学院;昆明理工大学国土资源工程学院;东华理工大学水资源与环境工程学院【正文语种】中文我国氧化铜矿资源约占铜矿资源总储量的10%~15%,每年总产量30%左右的铜金属是以氧化铜矿的形式产出[1]。
许多铜矿矿床上部都有氧化矿带,或者深部氧化为氧化矿床,并且几乎都具有结构松散、易碎、含水含泥较多、细粒不均匀嵌布、氧、硫混杂等特点。
浮选效果差,选矿成本也比硫化矿高[2]。
硫化铜矿容易与脉石分离,浮选回收较为容易。
市场对铜需求量的增加刺激着易选硫化铜矿石的不断开发利用,高品位的硫化铜矿已日益减少[3-5]。
因此,从技术和经济可行性方面考虑,寻求合理的氧化铜矿的处理方法,是当前我国铜选矿的重要研究课题之一。
目前,氧化铜矿的回收方法主要有硫化—浮选法和湿法浸出法,其中浸出主要分为酸浸和氨浸。
酸浸适用于以酸性脉石为主的氧化铜矿[6-7]。
对于碱性脉石含量较高的氧化铜矿进行酸浸,不但会消耗大量的酸,而且还会出现板结现象,浸出效果差[8-9]。
低品位氧化铜矿还原焙烧_氨浸试验研究_李运刚
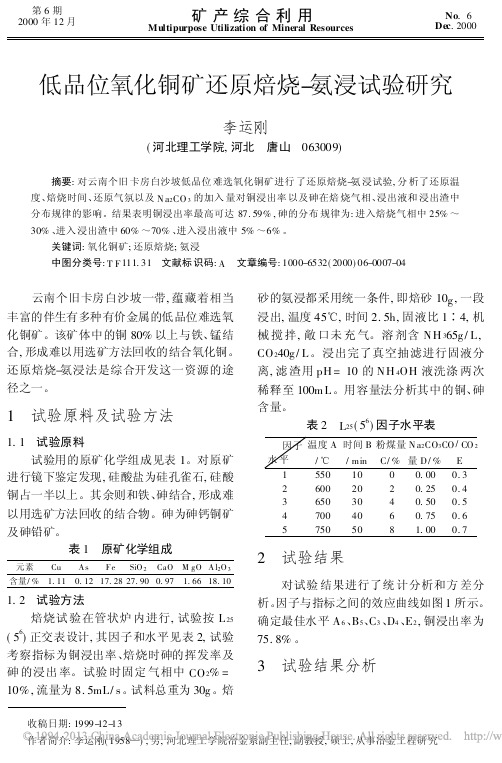
1. 1 试验原料 试验用的原矿化学组成见表 1。对原矿
进行镜下鉴定发现, 硅酸盐为硅孔雀石, 硅酸 铜占一半以上。其余则和铁、砷结合, 形成难 以用选矿方法回收的结合物。砷为砷钙铜矿 及砷铅矿。
表 1 原矿化学组成
元素 Cu A s Fe SiO 2 CaO M gO A l2O 3 含量/ % 1. 11 0. 12 17. 28 27. 90 0. 97 1. 66 18. 10
1. 2 试验方法 焙烧试 验在管状炉 内进行, 试验按 L 25
( 56) 正交表设计, 其因子和水平见表 2, 试验 考察指标为铜浸出率、焙烧时砷的挥发率及 砷 的浸出 率。试验 时固定 气相中 CO 2% = 10% , 流量为 8. 5mL / s。试料总重为 30g 。焙
砂的氨浸都采用统一条件, 即焙砂 10g , 一段 浸出, 温度 45℃, 时间 2. 5h, 固液比 1∶4, 机
矿 产 综 合 利 用 第 6 期
20 00
年
12
月 M ul ti purpos e
Utilization
of
Mineral
Res ources D eNc.o2. 0
6 00
低品位氧化铜矿还原焙烧-氨浸试验研究
李运刚
( 河北理工学院, 河北 唐山 063009)
项目
金属铜
氧化铜 中铜
氧化亚 铜中铜
硫化铜 中铜
氧化物 中铜
焙砂/ % 微 浸 出渣/ %
0. 362 0. 784 0. 074 0. 046 0. 165 0. 120
3. 1. 5 先氧化焙烧后还原焙烧 以上分析表明该矿采用还原焙烧—氨浸
工艺时, 铜的浸出率较低主要是因有硫化铜 存在的缘故, 因此应首先进行脱硫处理, 即氧 化焙烧把硫化铜转化成氧化铜, 然后再进行 还原焙烧, 铜的浸出率肯定提高。我们用 L 16 ( 45 ) 正 交 表 选 定 最 佳 条 件 是 氧 化 时 间 40m in、温度 800℃, 铜的浸出率达 87. 59% 。
aa 某高碱性氧化铜矿常温常压氨浸实验研究sfyj200602005
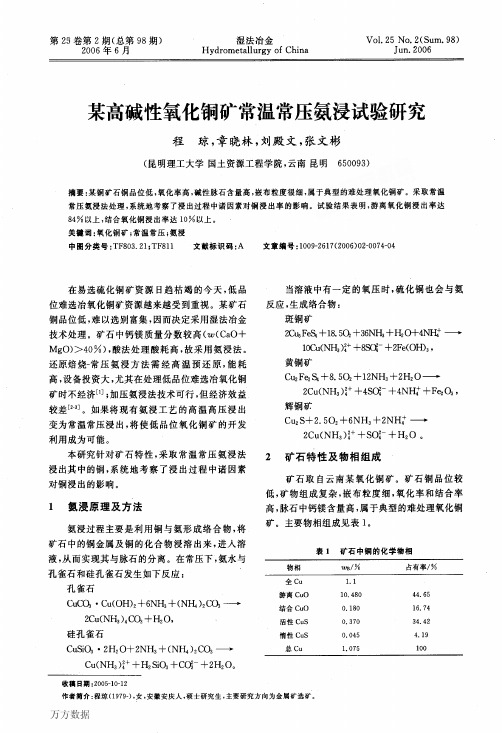
·75·
3试验方法
浸出试验在1 000 mL的烧杯中进行,用JJ一1 增力电动搅拌器进行搅拌。每次试验称取原矿 250 g,经XMQ-67型240×90锥型球磨机磨矿到 所需粒度,按计算量投入所需的浸出剂,浸出后, 对矿浆过滤,滤渣经洗涤、烘干、缩分后送分析。
4 结果与讨论
4.1 主要影响因素对铜浸出率的影响 试验就浸出剂浓度、浸出时间、矿石粒度、液
当溶液中有一定的氧压时,硫化铜也会与氨 反应,生成络合物:
斑铜矿 2Cus FeS4+18.5Q+36NH3+H2 0卜卜4NH产—一
10(、u(NH3)r+8S0《一+2Fe(OH)。, 黄铜矿
CuzFe2&+8.502+12NH3+2H20一
2Cu(NH3):++4S0i一十4NH}+Fez 03, 辉铜矿
第25卷第2期
程琼,等:某高碱性氧化铜矿常温常压氨浸试验研究
·77·
艺,在操作和经济上都有一定困难,而常温常压氨 浸对处理氧化铜矿原矿是可行的,其中游离氧化 铜浸出率达84%以上,虽然结合氧化铜和硫化铜 的浸出率偏低,但加入少量活化剂可提高这部分 铜的浸出率。
参考文献:
[1]北京矿冶研究总院,东川矿物局.东川汤丹氧NNHH4IHHFF22—一2CChu((NNHH33))44FF+2H+2H02。O,
在矿石粒度--200目占80%,室温,浸出时间 l h,NH。与NH。HF。的浓度比为3.5:0.6,液 固体积质量比2 f 1的条件下进行浸出试验,结果 如图5所示。
c(氨水)/(tool·L。1)
粒度一200耳占80%;c(NH3):c(NH4HF2)一3.5:0.6; 液固体积质量比一2:1,室温
图5 活化剂对铜的氨浸率的影响
氧化铜矿常温常压两段氨浸试验研究

铁矿 矿泥 和高岭 土也 会 与 硫 酸发 生 反应 , 消耗 一 定 量 的酸 , 致硫 酸消耗 量太高 , 导 经济 上不宜 采用 。氨
都不高 , 不考虑 回收利 用 。脉 石矿物 以含铁 、 的脉 钙
石矿物 为主 , 岭土 、 酸盐类 脉石矿 物次之 。原矿 高 硅
浸法虽 然工 业生产 卫 生 条件 差 , 萃 余 液 中 的氨 可 但
械搅 拌 浸 出 的 各种 影 响 因素 , 定 按 常温 常压 的 方 式来 浸 出 , 便 产 业化 应 用 。试 验结 果 表 明 采用 两段 浸 出 的 工 艺 比单 段 浸 出 总 拟 以
铜 浸 出率 提 高 r 7 4 % 。 8
关键词 : 氧化铜矿 ; 氨浸 ; 矿泥; 两段浸出
性 试 验 结 果 表 明 , 用 浮 选 法 处 理 该 矿 石 时 , 为 褐 采 因
表 2 铜 物 相 分 析 结 果
Ta l An lssr s t fc p e a e be2 ay i e ulso o p rph s /%
铁矿 矿泥含 量很 高 , 在矿 物表 面产生 矿泥罩 盖 , 响 影 目的矿 物与 浮选药 剂 作用 , 究 认 为许 多 中矿 泥 研 会 在气 液界 面吸 附干 扰 氧化 铜 矿 物 与气 泡 的接 触 , 尤 其 以针 铁矿 矿泥 影 响更 大 , 铁 矿 与针 铁 矿 的性 褐 质 和表 面化学 特性相 似 , 亦会 形成 矿泥 干扰 , 得浮 使
能 耗 的增 加 , 温 后 氨 的挥 发 量 增 加 , 出 液 需 要 冷 加 浸
的增 加 、 度 的 增 加 而 增 加 。 温 ( ) 浸 出 时 间 对 浸 出 率 的 影 响 。 铜 浸 出 率 随 1铜
- 1、下载文档前请自行甄别文档内容的完整性,平台不提供额外的编辑、内容补充、找答案等附加服务。
- 2、"仅部分预览"的文档,不可在线预览部分如存在完整性等问题,可反馈申请退款(可完整预览的文档不适用该条件!)。
- 3、如文档侵犯您的权益,请联系客服反馈,我们会尽快为您处理(人工客服工作时间:9:00-18:30)。
立志当早,存高远
氧化铜矿的氨浸
由于铜离子在氨溶液中形成稳定的配位化合物,Cu (NH3)2+n,n=1~4,因此溶解度很大。
溶液中加人硫酸铵或碳酸氢铵等铵盐,可以缓冲溶液的pH 值,阻止铜的水解反应。
早在1915 年就出现了氨浸法提铜的专利,20 年代开
始工业应用。
孔雀石和蓝铜等碱式碳酸盐矿物中的铜通过生成配合物易于溶
解于氨性溶液:CuC03·Cu(OH)2+6NH40H+(NH4)2C03 ==== 2Cu (NH3)4C03+8H20 可以看出,浸取中要保证足够的氨浓度,以生成稳定的铜氨配合物。
温度虽然可以提高反应速度,但使氨的分压增高,损失增加,因此,以选取适中的温度为宜。
硅孔雀石也能在氨-铵盐溶液中浸出。
早期都用大
桶渗滤的方法浸取这些矿物,回收率能达到80%左右。
使用氨浸处理含碱性
脉石的矿石可减少采用酸浸所额外消耗的酸。
不过,如果矿物中含有蒙脱石等
间层硅酸盐组成的矿物,其中的钠离子能与铜离子交换,吸附铜,造成损失。
我国东川汤丹是大型氧化铜矿床,金属总储量有100 万t。
铜矿物主要是孔雀
石(55%)、斑铜矿(20%)和硅孔雀石(11%),黄铜矿5%,辉铜矿4%。
铜
矿物大部分呈极细颗粒嵌布在脉石之中,因此选矿回收率仅为70%左右。
试验
表明氨浸效果良好,选矿加尾矿氨浸,铜总回收率可接近90%以上。
采用氨和
碳酸铵浓度分别为2mol/L 的溶液进行浸取,温度对浸取的影响最显著,110℃
以上浸取率才能达到90%以上。
空气分压也有较大影响,120℃下浸取3h,分
压从0.3MPa 增高到1.2MPa,浸取率从80%提高到90%。
浸出液蒸氨后,铜生成氧化铜析出,需精炼才能得合格产品。
含氨残液加石灰乳苛化,得含铜硫酸钙。
进行过日处理l00t 矿石原矿氨浸半工业试验,流程见下图的半工业试验,
采用多层空气提升高压釜浸取,效果良好[1]。
参考文献 1.陈家镛等著,湿法
冶金的研究和发展,北京:冶金工业出版社,1998,4~20。