探伤作业指导书
板材无损探伤作业指导书

板材超声波探伤作业指导书编制:审核:批准:二○二二年三月1. 范围本超声波探伤作业指导书规定了板材超声波探伤的技术要求。
2. 规范性引用文件GB 50017 钢结构设计标准GB 50661 钢结构焊接规范GB 50205 钢结构工程施工质量验收规范GB/T 29712焊缝无损检测超声检测验收等级NB/T 47013 承压设备无损检测JB/T 3223 焊接材料质量管理规程Q/GDW 11143 输电线路铁塔焊接材料技术规范3. 一般要求3.1人员资格按本标准实施检测的人员,应按GB/T 9445或合同各方同意的体系进行资格鉴定与认证。
取得超声检测相关工业门类的资格等级证书,并由雇半或其代理对其进行职位专业培训和操作授权。
3.2设备3.2.1仪器性能测试超声检测仪应定期进行性能测试。
仪器性能测试应按JB/T 9712推荐的方法进行。
3.2.2系统性能测试至少在每次检测前,应按JB/T 9214推荐的方法,对超声检测系统工作性能进行测试。
3.2.3探头参数3.2.3.1检测频率检测频率应在2MHz~5MHz范围内,同时应遵照验收等级要求选择合适的频率。
3.2.3.2折射角当检测采用横波且所用技术需要超声从底而反射时,应注意保证声束与底面反射面法线的夹角在35°至70°之间,当使用多个斜探头进行检测时,其中一个探头应符台上述要求,且应保证一个探头的声束尽可能与焊缝熔合面垂直。
3.2.3.3晶片尺寸晶片尺寸选择应与频率和声程有关。
在给定频率下,探头晶片尺寸越小,近场长度和宽度就越小,远场中声束扩散角就越大。
3.2.3.4耦合剂耦含剂应选用适当的液体或糊状物,应具有良好透声性和适宜流动性,不应对检测对象和检测人员有损伤作用,同时应便于检验后清理。
典型的耦合剂为水、机油、甘油和浆糊,耦合剂中可加入适当的“润湿剂”或活性剂以改善耦合性能。
时基范围调节、灵敏度设定和工件检测时应采用相同耦合剂。
超声波探伤作业指导书

作业指导书
姓名:身份证号码:报考级别:
报考门类:
一、适用范围及采用标准
1.适用范围:
本作业指导书适用于母材厚度不小于8mm的铁素体类钢全焊透熔化焊对接焊缝脉冲反射法手工超声波检验。
2.检测标准和检测等级
GB/Tll345-2013《钢焊缝手工超声波探伤方法和探伤结果分级法》,B级检测。
3.验收标准和验收等级
GB/T29712-2013《焊缝无损检测超声检测验收等级》,2级验收。
二、检测人员资质要求
检验人员应经过培训,取得
三、工件参数、探伤面、探伤区及探伤方法(附示意图)
四、探伤系统及性能要求
1.探伤仪型号及性能要求
US-88型数字探伤仪。
探伤仪应符合以下要求:
2.探头规格及性能要求
2.5P13×20
3.试块
CSK-IA试块,RB-1试块
4.耦合剂
应选用适当的液体或模糊状物作耦合剂。
耦合剂应具备有良好透声性和适宜流动性,不应对材料和人体有损伤作用。
同时应便于检验后清理。
典型耦合剂为水、机油、甘油和浆糊。
在试块上调节仪器和产品检验应采用相同的耦合剂。
五、检测准备
1、探伤面准备
2、时基线调节
3、仪器探头主要参数测量及输入
4、灵敏度调节或距离波幅曲线制作
5、工件参数输入(如厚度)
6、传输补偿与衰减系数测量(示意图)
六、检测
1.扫查
2.缺陷定位定量与评级
七、仪器系统复核
八、记录与报告
编制:审核:批准:。
VT探伤作业指导书
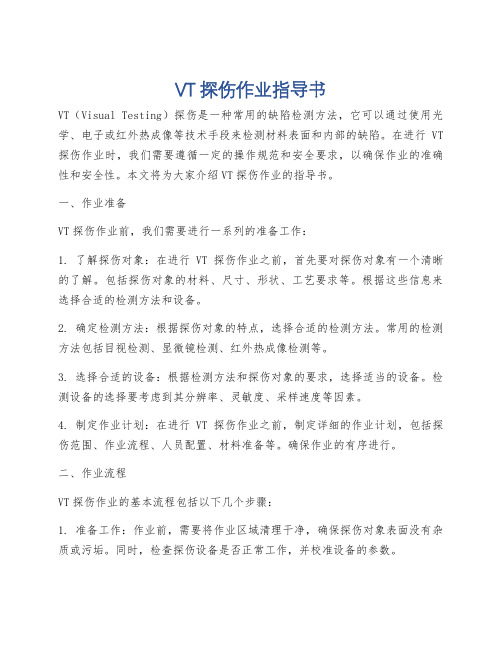
VT探伤作业指导书VT(Visual Testing)探伤是一种常用的缺陷检测方法,它可以通过使用光学、电子或红外热成像等技术手段来检测材料表面和内部的缺陷。
在进行VT 探伤作业时,我们需要遵循一定的操作规范和安全要求,以确保作业的准确性和安全性。
本文将为大家介绍VT探伤作业的指导书。
一、作业准备VT探伤作业前,我们需要进行一系列的准备工作:1. 了解探伤对象:在进行VT探伤作业之前,首先要对探伤对象有一个清晰的了解。
包括探伤对象的材料、尺寸、形状、工艺要求等。
根据这些信息来选择合适的检测方法和设备。
2. 确定检测方法:根据探伤对象的特点,选择合适的检测方法。
常用的检测方法包括目视检测、显微镜检测、红外热成像检测等。
3. 选择合适的设备:根据检测方法和探伤对象的要求,选择适当的设备。
检测设备的选择要考虑到其分辨率、灵敏度、采样速度等因素。
4. 制定作业计划:在进行VT探伤作业之前,制定详细的作业计划,包括探伤范围、作业流程、人员配置、材料准备等。
确保作业的有序进行。
二、作业流程VT探伤作业的基本流程包括以下几个步骤:1. 准备工作:作业前,需要将作业区域清理干净,确保探伤对象表面没有杂质或污垢。
同时,检查探伤设备是否正常工作,并校准设备的参数。
2. 开始探伤作业:按照作业计划和探伤范围,开始进行探伤作业。
根据探伤对象的特点和所选的检测方法,进行探测。
3. 判断缺陷:通过观察探伤结果,判断是否存在缺陷。
缺陷一般分为表面缺陷和内部缺陷两种。
根据缺陷的类型、形状、尺寸等特征,进行判断和记录。
4. 处理缺陷:根据缺陷的性质和要求,对缺陷进行相应的处理。
处理方式可以包括修复、更换、报废等。
5. 作业记录:对探伤作业的过程和结果进行详细的记录,包括探测时间、地点、使用的设备和方法、探测结果等。
三、注意事项在进行VT探伤作业时,需要注意以下几点:1. 安全性:保证作业过程的安全。
例如,使用安全防护设备,注意操作规范,避免因操作不当造成意外伤害。
渗透探伤作业指导书

渗透探伤作业指导书渗透探伤作业指导书(上)一、前言渗透探伤是一种利用特定的方法和设备对材料或构件进行检测的技术。
它可以检测到材料或构件内部的缺陷、疵点和裂纹等问题,为工程质量的保证提供了重要的手段。
本作业指导书旨在为渗透探伤作业提供详细的操作指导,帮助操作人员正确使用设备和工艺,确保探伤作业的准确性和安全性。
二、作业准备1. 设备调试:在开始作业之前,需要对渗透探伤设备进行调试和校准,确保其正常工作状态。
2. 材料准备:根据作业的需要,准备好待检材料和相关辅助设备,确保作业的顺利进行。
3. 环境准备:确保作业现场的环境整洁、安全,并具备良好的照明条件,以便操作人员进行观察和判断。
三、作业步骤1. 准备工作:- 操作人员需要佩戴适当的防护装备,包括手套、护目镜和口罩等,以保证自身安全。
- 对待检材料进行表面清洁处理,确保表面没有灰尘、污渍和残留物,以免对渗透液的渗透和观察造成干扰。
- 根据待检材料的性质和要求,选择合适的渗透液,将其涂布在待检材料的表面上,使其充分渗透。
2. 渗透阶段:- 操作人员需要将渗透液充分涂布在待检材料的表面上,并确保渗透液在表面停留的时间达到要求。
一般情况下,渗透时间为10-30分钟。
- 在渗透过程中,操作人员需要仔细观察渗透液是否发生渗透现象,以及渗透液是否在材料表面形成一定的膜层。
如果发现渗透现象不明显或者膜层形成不完整,需要重新涂布渗透液。
3. 渗透保持阶段:- 渗透保持时间一般为1-2小时,在此期间,操作人员需要保持待检材料表面的渗透膜层湿润,以便更好地观察和检测裂纹和缺陷等问题。
- 在渗透保持期间,操作人员需要定时巡视待检材料的表面,确保渗透膜层无明显干裂或干燥现象。
如果发现渗透膜层出现问题,需要重新涂布渗透液。
4. 渗透显影阶段:- 渗透显影是将渗透液中渗透到材料内部的液体显影剂通过吸附或滴流等方式,使之渗透至膜层中,并形成可见的显影剂聚集效应,从而使缺陷和裂纹等问题显现出来。
支柱瓷瓶探伤试验作业指导书

支柱瓷瓶探伤试验作业指导书一、背景介绍支柱瓷瓶是电力输配电线路中的重要组成部分,用于支撑和固定导线,保证线路的正常运行。
为了确保支柱瓷瓶的质量和安全性能,需要进行探伤试验,以检测瓷瓶内部的缺陷和损伤情况。
本作业指导书旨在提供支柱瓷瓶探伤试验的详细步骤和操作要点,确保试验过程的准确性和可靠性。
二、试验设备和材料准备1. 探伤设备:超声波探伤仪、探头、显示屏等。
2. 试验材料:支柱瓷瓶、超声耦合剂、试验记录表等。
三、试验步骤1. 准备工作a. 检查探伤设备是否正常工作,确保超声波探伤仪处于合适的工作状态。
b. 准备试验材料,包括支柱瓷瓶和超声耦合剂。
c. 对支柱瓷瓶进行外观检查,确保瓷瓶表面无明显损伤和污垢。
2. 超声波探伤a. 选择合适的探头,根据支柱瓷瓶的尺寸和形状进行调整。
b. 将超声耦合剂涂抹在探头和支柱瓷瓶表面,确保良好的声耦合效果。
c. 将探头沿支柱瓷瓶表面逐渐移动,保持一定的探测速度。
d. 观察超声波探伤仪的显示屏,记录探头接收到的超声波信号。
3. 数据分析和判定a. 根据超声波信号的特征,分析支柱瓷瓶内部的缺陷和损伤情况。
b. 判定缺陷的类型、大小和位置,并进行记录。
c. 根据试验标准和要求,对支柱瓷瓶的探伤结果进行评估和判定。
四、注意事项1. 操作人员应具备一定的超声波探伤仪使用经验和相关知识。
2. 操作过程中应注意个人安全,避免超声波探头碰撞到支柱瓷瓶或其他物体。
3. 需要严格按照试验标准和要求进行操作和判定,确保试验结果的准确性和可靠性。
4. 试验结束后,及时清洗和保养探伤设备,确保设备的正常使用寿命。
五、记录和报告1. 在试验过程中,及时记录试验数据和观察结果,包括支柱瓷瓶的缺陷类型、大小和位置等。
2. 根据试验结果,编写试验报告,详细描述支柱瓷瓶的探伤结果和评估结论。
六、附录1. 支柱瓷瓶探伤试验记录表:记录支柱瓷瓶的试验数据和观察结果。
2. 超声波探伤仪操作手册:详细介绍超声波探伤仪的使用方法和操作步骤。
射线探伤工艺作业指导书
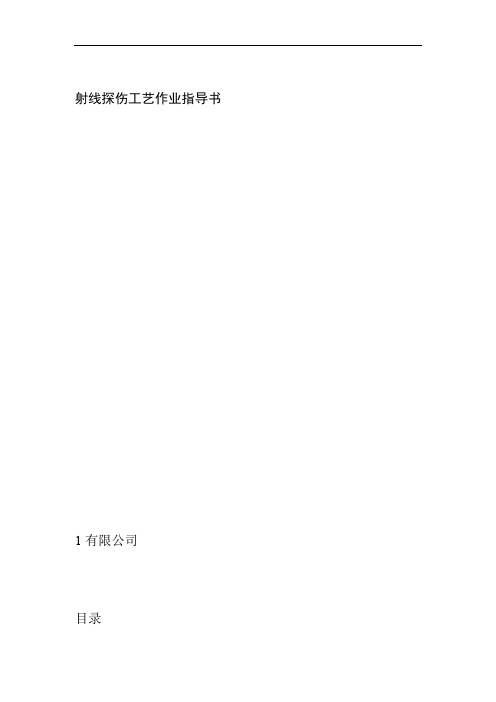
射线探伤工艺作业指导书1有限公司目录1、主题内容2、适用范围3、对探伤人员的要求4、对透照工件表面的要求5、探伤比例的要求及合格级别6、器材的选择7、透照工艺8、胶片的暗室处理9、底片质量10、底片的观察11、记录报告12、安全防护1、主题内容1.1保证工业锅炉对接焊缝射线探伤的准确性,保证锅炉能够正常的运行。
2、适用范围2.1适用于工业锅炉的过热器、省煤器、集箱、压力管道等安装中管-管、管-板对接焊缝射线透照检测。
焊接方式为氩弧焊打底、手工焊盖面。
3、对探伤人员的要求凡从事射线探伤工作人员,都必须经过技术培训,并按3.1.照劳动部文件“锅炉压力容器无损检测人员资格考核规则”进行考核鉴定。
3.2无损检测人员按技术等级分高、中、初级。
取得各技术等级人员,只能从事与该技术等级相应的无损检测工作,并负相应的技术责任。
3.3操作人员应具有RT—I 以上资格证书,评定及审核人员应具有RT—II级以上资格证书。
3.4从射线探伤人员应能辨别距离400mm远的一组高为0.5mm,间距为0.5mm的印刷字母。
4、对透照工件表面的要求4.1焊缝及热影响区的表面质量(包括余高高度)应经外观检查合格。
表面的不规则状态在底片上应不掩盖焊缝中的缺陷或与之相混淆,否则应做适当的修整。
4.2焊缝外观检验合格后,由检验员签发《无损探伤委托书》。
4.3焊缝透照质量达到NB/T47013—2015标准AB级。
5、探伤比例的要求及合格级别5.1探伤比例的要求及合格级别5.2焊缝合格级别达到NB/T47013—2015标准的II级。
6、器材的选择6.1焊缝透照选用理学----300或国产300周向射线探伤机,固定焊缝选用理学-----2505或丹东----2505定向射线探伤机。
胶片选用爱克发型6.2.6.3增感屏选取用厚度为0.03mm的铅箔增感屏,暗盒选用360×80和240×80两种,选用铅质阿拉伯数字英文母。
车轴穿透探伤工位作业指导书
作业指导书车轴穿透探伤目次一、工位介绍 (1)二、本工位作业流程 (2)三、作业程序及标准 (3)1.开工准备 (3)2.日常性能校验 (3)3.季度性能检查。
(13)4.探伤作业 (20)5.完工整理 (22)四、工装设备、检测器具及材料 (24)五、附件 (26)1.作业台帐记录 (26)2.台帐记录填写示例 (28)3.定置示意图 (33)一、工位介绍1. 作业地点:车轮车间轮轴新组装及四级修车轴加工工艺线。
2. 适用范围:适用于铁路货车RD2、RE2B型车轴穿透探伤作业。
3. 上道工序:车轴收入检查工位。
4. 下道工序:车轴冲洗除锈工位。
5. 人员素质要求:应取得总公司无损检测人员技术资格鉴定考核委员会颁发的相关专业探伤技术资格证书。
Ⅱ级及以上的探伤人员应持相关专业证书和上岗证方可独立从事探伤工作。
首次取得Ⅱ级资格证书的探伤人员应经过半年的实践并经铁路局考核合格后方可上岗作业。
Ⅰ级探伤人员应在Ⅱ级及以上人员的指导下从事相关的探伤工作,指导人员须在探伤记录上签章确认。
6. 作业要点:6.1核对轮轴卡片信息,检查轴端探头移动区域无凸台。
6.2在车轴两端面进行探伤作业。
6.3探伤结束涂打探伤标识。
6.4填写探伤记录。
三、作业程序及标准1.开工准备1.1穿戴劳保用品。
每班开工前更换统一发放的工作服,戴好工作帽,着装应整齐、整洁,工作帽帽檐应朝正前方,如图1所示。
1.2接收工作任务。
每班开工前,参加班组点名会,由探伤班组工长组织各工位人员列队点名,传达上级要求,布置当日工作任务,如图2所示。
1.3设备点检。
每班开工前,检查多通道探伤仪定检不过期、打印机良好、转轮器符合要求、设备传输信号良好、探头无磨损、试块良好,备品齐全。
2.日常性能校验2.1每日上、下午开工前,由探伤工、探伤工长、质量检查员、验收员共同参加,对多通道探伤设备进行日常性能校验。
2.2校验前观察温度计,探伤场地环境温度应保持在10℃~30℃范围内,并认真填写《探伤间温度检测记录》,如图3所示。
漏磁探伤作业指导书
检查设备内部是否清 洁,有无杂物、灰尘 等影响设备运行的因
素
检查设备电路是否正 常,有无短路、断路
等情况
检查设备各部件是否 紧固,有无松动、脱
落等情况
检查设备润滑油是否 充足,有无漏油、缺
油等情况
检查设备安全防护装 置是否完好,有无损
坏、失效等情况
对设备进行定期维护 和保养,确保设备正
常运行
管道表面清理
人员培训和技术交底
01
02
03
04
培训内容:漏磁 探伤原理、操作 方法、注意事项 等
培训方式:理论 讲解、实际操作、 考核等
技术交底:明确 作业任务、技术 要求、安全措施 等
培训记录:记录 培训时间、地点、 参加人员等,作 为培训档案保存
设备检查和维护
检查设备外观是否完 好,有无破损、锈蚀
等情况
检测:将被检工件放置在检测装 置上,进行漏磁检测。
复检:对处理后的工件进行复检, 确保质量合格。
准备:检查设备、工具、材料是 否齐全,确保工作环境安全、整
洁。
记录:记录检测结果,包括缺陷 位置、大小、深度等信息。
清理:清理现场,整理设备、工 具、材料,保持工作环境整洁。
磁化:将被检工件放置在磁化装 置上,进行磁化处理。
处理
处理方式:采 用焚烧、填埋、 回收利用等方
式进行处理
排放标准:符 合国家或地方 排放标准,防
止污染环境
监测和报告: 定期监测排放 情况,并向有
关部门报告
环境事故应急处理预案
01
02
03
04
05
感谢您的耐心观看
汇报人:XXX
处理:根据分析结果,对缺陷进 行修复或更换。
射线探伤作业指导书
射线探伤作业指导书一、引言射线探伤是一种常用的无损检测方法,可以用于检测材料内部的缺陷。
本指导书旨在为射线探伤作业提供详细指导,确保安全可靠地进行射线探伤作业。
二、作业前准备1. 工作人员培训:所有参与射线探伤作业的工作人员都必须经过专业培训,熟悉射线设备的操作和安全规范。
2. 工作场所准备:确保作业场所宽敞清洁,并设立明显的警示标志,提示射线探伤作业正在进行。
3. 人员防护装备:工作人员必须佩戴适合的防护装备,包括防护服、防护眼镜、防护手套等,以防止辐射的危害。
三、设备与器材准备1. 射线源准备:选择合适的射线源,并定期进行检测和维护,确保射线源的安全性能。
2. 探测器准备:选择合适的探测器,并进行校准,确保准确可靠地检测缺陷。
3. 辅助工具准备:准备好射线测量仪器、标记笔、尺子等辅助工具,以便于对检测结果进行记录和分析。
四、作业流程1. 环境检查:在进行射线探伤作业前,先对作业环境进行检查,确保周围没有任何人员和无关物品,以防意外伤害。
2. 辐射区域设立:根据射线的辐射半径,设立辐射区域,并进行标识,以禁止无关人员进入。
3. 射线源操作:在辐射区域内,按照操作规程将射线源正确放置,调整角度和距离,保证射线照射的精确性和稳定性。
4. 探测器操作:操作人员应根据实际情况选择合适的探测器,与射线源相配合进行检测操作,确保准确获取数据。
5. 数据分析与记录:对收集到的数据进行分析,判断出现的缺陷类型和位置,并及时记录在报告中。
6. 安全结束:作业完成后,将射线源回收到密封容器中,清理辐射区域,恢复工作现场的正常使用。
五、安全措施1. 人员防护:所有参与作业的人员必须戴上适当的防护设备,减少辐射对人身的伤害。
2. 辐射区域控制:在辐射区域内设立明显的警示标志,并设置屏障限制无关人员进入。
3. 定期检测与维护:定期对射线源和探测器进行检测和维护,确保设备的安全性能。
4. 废弃物处理:将使用过的射线源和工作区所产生的废弃物按照国家相关法规进行正确处置。
超声波探伤作业指导书(二)
超声波探伤作业指导书(二)引言概述:本文档为超声波探伤作业指导书的续篇,旨在为探伤人员提供更详尽的操作指导和技巧。
超声波探伤技术是一种非破坏性检测方法,广泛应用于工业领域,可用于探测材料内部缺陷和结构异常。
在本指导书中,将详细介绍超声波探伤的五个重要方面,包括设备准备、校准、缺陷检测、数据分析和报告撰写。
正文:一、设备准备1.1 确认探伤设备的完好性和性能。
1.2 配置合适的探头或探头组合,考虑材料类型和探测深度等因素。
1.3 检查超声传感器的表面和连接接头,确保无损伤和松动。
1.4 为设备提供稳定的电源,并确保地线连接良好。
二、校准2.1 进行零点校准,即消除探头本身的回波信号。
2.2 进行灵敏度校准,以确保正确反映不同材料的回波幅度。
2.3 进行水平线arity校准,以验证仪器的线性响应。
2.4 进行垂直线arity校准,以验证超声波在探测物体中的深度传播准确性。
2.5 校准的结果应记录在校准证书中,以备查证。
三、缺陷检测3.1 确定缺陷检测区域,并清理表面以保证信号传播的畅通。
3.2 调整超声波探伤仪的参数,如频率、增益和发射角度等。
3.3 沿着检测区域进行扫描,确保探头与材料表面保持垂直,并保持一定的扫描速度。
3.4 注重反射信号的幅度和时间,以判断是否存在缺陷。
3.5 在发现缺陷时,应标记缺陷位置,并记录相关信息。
四、数据分析4.1 基于超声波回波信号,利用幅度图形和时间图形进行数据分析。
4.2 对回波信号进行峰值幅度和时间测量,以判断缺陷的类型和尺寸。
4.3 利用闸门技术提取感兴趣的信号,并进行进一步的分析。
4.4 应用图像处理算法,对回波信号进行图像增强和异常点检测等操作。
4.5 将分析结果记录在报告中,包括缺陷类型、尺寸、位置和评估结果等。
五、报告撰写5.1 报告应明确指出被检测物体的标识信息和探测工艺参数。
5.2 报告应包括设备校准、缺陷检测和数据分析等步骤的记录。
5.3 报告中的数据结果应准确、清晰地呈现,并附带相关图表和图像。
- 1、下载文档前请自行甄别文档内容的完整性,平台不提供额外的编辑、内容补充、找答案等附加服务。
- 2、"仅部分预览"的文档,不可在线预览部分如存在完整性等问题,可反馈申请退款(可完整预览的文档不适用该条件!)。
- 3、如文档侵犯您的权益,请联系客服反馈,我们会尽快为您处理(人工客服工作时间:9:00-18:30)。
无损检测作业指导书(磁粉检测部分)1. 目的与范围1.1目的:使我公司涉及的产品无损检测过程得到有效控制。
1.2范围:对API 4F第4版覆盖的井架、底座、天车及API 7K第5版覆盖的绞车输入轴。
2. 引用文件API 4F第4版钻井和修井井架、底座规范API 7K第5版钻井和修井设备AWS D1.1-2008 美国钢结构焊接规范ASME BPVC V-2010 锅炉及压力容器国际性规范V无损检测ASTM E709-2001 磁粉检验的标准推荐操作方法ASNT SNT-TC-1A-2011 无损检测人员的鉴定与认证ASTM E543-09 无损检测机构资格认可的实施标准3. 人员资格直接为我公司进行磁粉检测工作的人员必须经国家技术监督部门授权的机构培训,并按ASNT-SNT-TC-1A(无损检测人员的鉴定与认证)进行鉴定,并取得国家相关部门颁发的磁粉检测Ⅱ级及以上资质证书,矫正视力不得低于1.0,并且一年检查一次,不得有色盲和色弱,持证上岗。
4. 检测设备4.1 CDX-1型荧光磁粉探伤机。
此设备应每年校准一次。
4.2 30/100试片。
用于检测磁粉检测设备、磁粉和磁悬液的综合性能,了解被检工件表面有效磁场强度和方向、有效检测区以及磁化方向是否正确。
4.3磁粉及磁悬液4.3.1选用荧光磁粉、无味煤油配制的浓度为0.5~3.0g/l(沉淀浓度0.1~0.4ml/100ml)的磁悬液。
每8小时或每班次应对湿粉浓度进行一次检查。
4.3.2湿磁粉的浓度应采用梨形离心管测定它的沉淀体积来决定。
在取样之前,通过循环系统旋转磁悬液至少30分钟,取100ml溶液,并允许它沉淀30分钟,在试管底部的沉淀表示溶液中磁粉深度。
荧光磁粉沉淀体积应是100ml,磁悬液中为0.1~0.4ml。
如果磁粉沉淀物显示处松散的聚集而不是一个固体层,则应重新取样,若仍是松散的聚集物,则磁粉可能被磁化,需要更换磁悬液。
4.4 相关设备的检验周期5. 检测工序及其要求5.1 检测工序:API 4F:在焊缝完成并冷却至环境温度后;API 7K:磁粉检测应当在最终热处理和最终机加工后进行检验。
5.2 检测位置:API 4F:所有关键焊缝及图纸要求焊缝区域;API 7K:所有可接近表面。
5.3 表面准备:被检工件表面应基本上清洁、干燥和无污染物,诸如油、油脂、浮砂、松的氧化皮、棉麻绒、厚油漆、焊剂/渣等可能限制磁粉的运动。
所有被检表面首先应经目检合格,且无影响无损检测的杂物。
表面的清洁可以用洗涤剂、有机溶剂或机械的方法。
6. 检测方法6.1磁粉检测以湿磁粉连续法进行检测。
选用黑磁粉、无味煤油配制的浓度为10~20g/l (沉淀浓度1.2~2.4ml/100ml)的磁悬液。
机加工表面进行湿荧光磁粉连续法进行检测。
选用荧光磁粉、无味煤油配制的浓度为0.5~3.0g/l(沉淀浓度0.1~0.4ml/100ml)的磁悬液。
灵敏度使用A-30% 试片。
交流小磁轭的提升力应不小于45N(4.5千克力)。
6.2应使用交流D型磁轭,进行纵向和横向的磁化检测。
磁化通电时间为2~4秒,磁悬液必须在通电时间内施加完毕,且至少应反复磁化两次。
6.3当焊缝及其热影响区表面难以清理至金属色,影响磁痕观查时,应使用白色反差增强剂以增加色彩对比度。
6.4缺陷磁痕的观察应在磁痕形成后立即进行。
机加工表面湿荧光磁粉探伤时,磁痕观察在暗室进行,检验表面黑光强度不低于1000Uw/cm2;暗室或暗处可见光照度应不大于20lx。
检测人员进入暗区,至少经过3分钟的暗室适应后,才能进行荧光磁粉检测。
观察荧光磁粉检测显示时,检测人员不准戴对检测有影响的眼镜。
当辨认细小磁痕时,应用2~10倍放大镜进行观察。
6.5缺陷磁痕的显示可采用照相、圈涂等方式记录,同时应保持记录。
7.验收准则7.1对于井架、底座、天车:7.1.1任何裂纹都不合格,不论其尺寸或部位。
7.1.2 不得有未熔合。
7.1.3 咬边的验收:厚度小于25 mm的材料上的咬边严禁超1mm,但允许任何300 mm 长度内累计咬边长度为50mm、最大值为2mm的咬边存在。
厚度等于或大于25mm的材料,任何长度的咬边严禁超过2mm。
7.1.4气孔的验收:对于所有坡口焊缝和角焊缝,直径等于或大于1mm的可见管状气孔的总和,在任何25mm长度焊缝范围内严禁超过10 mm。
而在任何300mm长度焊缝范围内严禁超过20mm。
7.2 对于绞车输入轴:7.2.1 无任何主要尺寸等于或大于5mm的相关指示;7.2.2 在任何一个40cm2的面积上,相关指示不超过10个;7.2.3 在任一条直线上,边距小于2mm的相关指示不超过3个;8. 复验当出现下列情况之一时,需要复验:a) 发现检测过程中操作方法有误或技术条件改变时;b) 合同各方有争议或认为必要时。
9.检测报告9.1 探伤结束后应及时开据探伤报告,对有缺陷的产品应进行简明的文字描述,必要时可以图示。
9.2 填写记录和报告字迹应清晰工整,言简意赅,准确描述磁粉检定结论。
9.3 在探伤时若发现缺陷应及时标识并单独存放。
判废的产品应及时处理掉,避免再次混入。
无损检测作业指导书(超声检测部分)1. 目的与范围1.1目的:使我公司涉及的产品无损检测过程得到有效控制。
1.2范围:我公司生产的绞车轴2. 引用文件ASME BPVC V-2010 锅炉及压力容器国际性规范V无损检测ASTM A388-2010 钢锻件超声波检验规程GB/T9445-2008 无损检测人员的鉴定与认证ASTM E543-09 无损检测机构资格认可的实施标准JB/T 4730.3-2005 承压设备无损检测—超声检测部分3. 人员资格直接为我公司进行磁粉检测工作的人员必须经国家技术监督部门授权的机构培训,并按GB/T 9445-2008(无损检测人员的鉴定与认证)进行鉴定,并取得国家相关部门颁发的磁粉检测Ⅱ级及以上资质证书,矫正视力不得低于1.0,并且一年检查一次,不得有色盲和色弱,持证上岗。
4. 绞车轴UT探伤方法概述直探头径向和轴向探测:直探头作径向探测时将探头置于轴的外缘,沿外缘作全面扫查,以发现轴类锻件中常见的纵向缺陷。
直探头做轴向探测时,探头置于轴的端头,并在轴端作全面扫查,以检出与轴线向垂直的横向缺陷。
5.探测条件的选择5.1仪器进行超声波探伤时采用的A型脉冲反射式超声波探伤仪应满足以下要求:工作频率范围为0.5MHZ-10MHZ,仪器至少在荧光屏满刻度的80%范围内呈线性显示。
应具有80dB以上的连续可调衰减器,步进级每档不大于2dB,精度为任意相邻12dB的误差在±1dB以内,最大累计误差在±1dB以内。
水平线性误差不大于1%,垂直线性误差不大于5%,其余指标应符合JB/T10061的规定。
5.2探头的选择锻件超声波探伤时,主要使用纵波直探头,晶片尺寸为Φ14-Φ28mm,常用Φ20mm。
对于较小的锻件,考虑近场区和耦合损耗原因,一般采用小晶片探头。
有时为了探测与探测面成一定倾角的缺陷,也可采用一定K值的斜探头进行探测。
锻件的晶粒一般比较小,因此可选用较高的探伤频率,常用2.5-5.0MHz。
对于少数材质晶粒粗大衰减严重的锻件,为了避免出现“林状回波”,提高信噪比,应选用较低的频率,一般为1.0-2.5MHz。
由于天车轴形状较为简单,直径较大,且经过锻压和热处理后晶粒较细,所以选用Φ20mm、频率为2.5MHz的纵波直探头进行探伤。
5.3耦合选择在锻件探伤时,为了实现较好的声耦合,表面粗糙Ra应不大于12.5μm,表面平整均匀,无划伤、油垢、污物、氧化皮、油漆等。
当在试块上调节探伤灵敏度时,要注意补偿块与工件之间因曲率半径和表面粗糙度不同引起的耦合损失。
锻件探伤时,常用机油、浆糊、甘油等做耦合剂。
当锻件表面较粗糙时,也可选用水玻璃作为耦合剂。
天车轴经过机加工后表面粗糙度可以达到要求,只需将表面的油垢和污物清理干净即可。
探伤时一般选用经济实惠、流动性差且对表面没有腐蚀的机油作为耦合剂。
5.4仪器系统在达到工件的最大检测声程时,其有效灵敏度余量应大于10dB。
仪器和探头的组合频率与公称频率误差不大于±10%。
仪器和直探头的组合的起始脉冲宽度(在基准灵敏度下):频率5 MHZ 的探头,宽度不大于10mm ;频率2.5 MHZ 的探头,宽度不大于15mm 。
直探头的远场分辨力不小于30dB 。
仪器和探头系统性能应按照JB/T9214进行测试。
5.5扫查方法的选择天车轴超探时,应在探测面上从两个相互垂直的方向上进行全面扫查,同时还应辅助以两个端面的扫查。
扫查覆盖面应为探头直径的15%,探头移动速度不大于150mm/s 。
扫查过程中要注意观察缺陷波的情况和底波的变化情况。
5.6材质衰减系统的测定材质的衰减对缺陷定量有一定的影响,特别是材质衰减严重时,影响更明显。
因此,在天车轴探伤时需要测定材质的衰减系数а。
衰减系数可利用下式计算:[][]()mm dB x/26B B 21--=α式中:[][]21B B -——无缺陷处第一、二次波高的分贝差;X ——底波声程(单程)。
测定衰减系数时,应选取表面相对光洁且无缺陷处,一般选取三处进行测试,最后取平均值。
6.探伤灵敏度的调节天车轴探伤灵敏度是由其技术要求或有关标准确定的。
一般不低于Φ2平底孔当量直径。
调节锻件探伤灵敏度的方法有两种,一种是利用锻件底波来调节探伤灵敏度,另一种是利用试块来调节。
当锻件被探部位厚度x≥3N ,且锻件具有平行地面或圆柱面时,常用底波来调节探伤灵敏度。
所以天车轴超声波探伤时选用底波调节法。
底波调节法,首先要计算或查A VG 曲线求得地面回波与某平底孔回波的分贝差,然后再调节。
(1)计算:对于平底或实心圆柱体底面,同距离处底波与平底孔回波的分贝差为:22lg 20lg 20ff B D x p p πλ==∆ 式中 λ——波长;X ——被探部位的厚度;f D ——平底孔直径。
(2)调节:探头对底面,衰减(Δ+5-10)dB ,调节“增益”使底波B 1达基准波高,然后用“衰减器”增益ΔdB ,这时灵敏度就调好了。
为了便于发现缺陷可再增益5-10dB 作为搜索灵敏度,即扫查灵敏度。
进行天车轴探伤时我们增益6dB 作为搜扫查灵敏度。
7.缺陷位置和大小的测定7.1 缺陷位置的测定在天车轴探伤中,主要采用纵波直探头探伤,因此可根据示波屏上缺陷波前沿所对的水平刻度值f τ和扫描速度1:n 来确定缺陷在锻件中的位置。
缺陷至探头的距离X f 为:X f =n f τ7.2缺陷大小的测定在锻件探伤中,对于尺寸小于声束界面的缺陷一般用当量法定量。
若缺陷位于x≥3N区域内时,常用当量计算法和当量A VG 曲线法定量;若缺陷位于x<3N 区域内,常用试块比较法定量。