无损检测热处理
铝制品检测标准
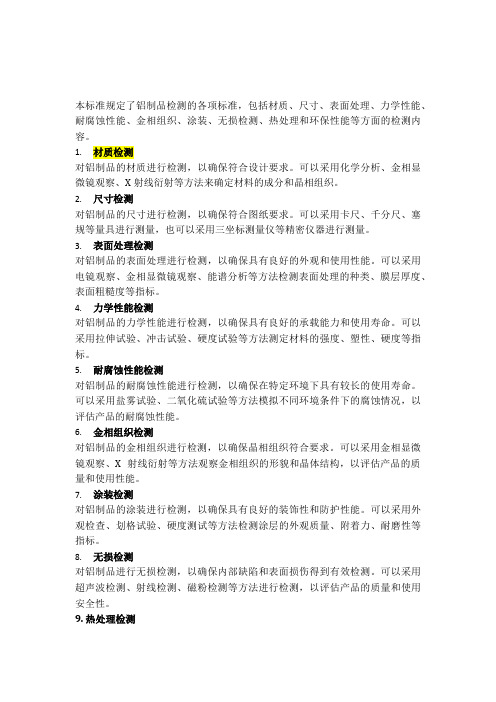
本标准规定了铝制品检测的各项标准,包括材质、尺寸、表面处理、力学性能、耐腐蚀性能、金相组织、涂装、无损检测、热处理和环保性能等方面的检测内容。
1.材质检测对铝制品的材质进行检测,以确保符合设计要求。
可以采用化学分析、金相显微镜观察、X射线衍射等方法来确定材料的成分和晶相组织。
2.尺寸检测对铝制品的尺寸进行检测,以确保符合图纸要求。
可以采用卡尺、千分尺、塞规等量具进行测量,也可以采用三坐标测量仪等精密仪器进行测量。
3.表面处理检测对铝制品的表面处理进行检测,以确保具有良好的外观和使用性能。
可以采用电镜观察、金相显微镜观察、能谱分析等方法检测表面处理的种类、膜层厚度、表面粗糙度等指标。
4.力学性能检测对铝制品的力学性能进行检测,以确保具有良好的承载能力和使用寿命。
可以采用拉伸试验、冲击试验、硬度试验等方法测定材料的强度、塑性、硬度等指标。
5.耐腐蚀性能检测对铝制品的耐腐蚀性能进行检测,以确保在特定环境下具有较长的使用寿命。
可以采用盐雾试验、二氧化硫试验等方法模拟不同环境条件下的腐蚀情况,以评估产品的耐腐蚀性能。
6.金相组织检测对铝制品的金相组织进行检测,以确保晶相组织符合要求。
可以采用金相显微镜观察、X射线衍射等方法观察金相组织的形貌和晶体结构,以评估产品的质量和使用性能。
7.涂装检测对铝制品的涂装进行检测,以确保具有良好的装饰性和防护性能。
可以采用外观检查、划格试验、硬度测试等方法检测涂层的外观质量、附着力、耐磨性等指标。
8.无损检测对铝制品进行无损检测,以确保内部缺陷和表面损伤得到有效检测。
可以采用超声波检测、射线检测、磁粉检测等方法进行检测,以评估产品的质量和使用安全性。
9. 热处理检测对铝制品的热处理过程进行检测,以确保达到预期的热处理效果。
可以采用温度记录仪、硬度测试等方法检测热处理过程中的温度变化、硬度变化等指标,以评估产品的热处理质量和性能稳定性。
10. 环保性能检测对铝制品的环保性能进行检测,以确保在生产过程中符合环保要求。
热处理质量控制和检测

4.2 材料化学成分的检验
4.2.4 微区化学成分分析 电子探针-X射线显微分析
包括: 波谱仪(WDS):一次单个元素,分辨 率高,样品要求高。 能谱仪(EDS):一次多个元素,分析精 度低,可测断口。 点、线、面扫描测定(图)
4.2 材料化学成分的检验
点扫描
4.1 热处理&质量控制
4.1.5 热处理生产过程品质控制 热处理设备管理与质控 1.设备选择:满足技术、品质要求 2.安装调试:达标、验收、记录 3.合理使用:持证上岗、交接规范、维护
良好、 严格操作规程
4.1 热处理&质量控制
4.1.5热处理生产过程品质控制 热处理设备管理与质控 4.检查维修:及时、定期检修 5.计量管理:计量器具保持在规范状态,
群控 质检:自动检测、判定、输出 档案及信息检索:工艺、原始数据存储,
调阅 工序品质分析:用数理工具进行分析、
判断
4.1 热处理&质量控制
4.1.7 热处理品质检验
硬度检验 畸变检验 外观及裂纹 金相检验 化学成分、力学性能检验
4.1 热处理&质量控制
4.1.7 热处理品质检验
4.2 材料化学成分的检验
4.2.2 化学分析法(常规湿法) 重量分析法
用某种方法把待测定组分从样品中分 离出来,根据分离物的质量算出被测组 分的含量
分离方法:沉淀法、气化法或电解法
4.2材料化学成分的检验
4.2.2 化学分析法(常规湿法) 钢材化学分析
①取样:具有代表性(心部),足够数量 (每元素/5g),屑状(湿法、溶解),
4.1热处理&质量控制
4.1.2 产品设计中热处理质量保证
无损检测技术如何判断材料的热处理状态

无损检测技术如何判断材料的热处理状态热处理是一种常用的材料处理方法,通过加热和冷却材料,改善其组织结构和性能。
在工业生产中,热处理广泛应用于各个行业,如航空航天、汽车制造、机械制造等。
为了确保材料的质量和性能,准确判断材料的热处理状态变得至关重要。
而无损检测技术在这个过程中发挥着重要的作用。
无损检测技术是一种非破坏性的材料检测方法,通过对材料内部和表面的信号进行收集、分析,来评估材料的性能和状态。
在判断材料的热处理状态中,无损检测技术主要通过以下几种方法进行:1. 超声检测法超声检测法是一种常用的无损检测方法。
它利用超声波的传播和反射特性来检测材料的内部缺陷和组织变化。
在判断材料的热处理状态时,超声检测法可以通过测量超声波的传播速度和反射信号来评估材料的组织结构和变化情况。
热处理过程中,材料的晶体结构和晶粒尺寸会发生变化,这些变化会对超声波的传播速度和反射信号产生影响,从而可以判断材料的热处理状态。
2. 磁粉检测法磁粉检测法是一种利用磁性颗粒检测材料表面和近表面缺陷的方法。
在判断材料的热处理状态时,磁粉检测法可以通过观察材料表面的磁粉沉积情况来判断材料的组织结构和硬度。
热处理过程中,材料的晶粒尺寸和晶体结构会发生变化,这些变化会影响材料的磁性,从而会导致磁粉在材料表面的沉积情况发生变化。
通过观察磁粉沉积情况的变化,可以准确判断材料的热处理状态。
3. 热红外检测法热红外检测法是一种利用红外辐射测量材料的热分布和温度分布的方法。
在判断材料的热处理状态时,热红外检测法可以通过观察材料表面的红外辐射情况来评估材料的温度分布和热量传导情况。
热处理过程中,材料的温度会发生变化,不同时期的热处理状态会导致不同的红外辐射情况。
通过观察红外辐射情况,可以准确判断材料的热处理状态。
通过以上的无损检测技术,我们可以准确判断材料的热处理状态。
这些无损检测方法都具有高准确性、非破坏性和高效性的特点,可以在生产过程中大大提高效率和准确性。
热处理过程中的无损检测技术探索

热处理过程中的无损检测技术探
索
热处理过程中的无损检测技术探索
热处理是一种常用的工艺,用于改变材料的性质和结构。
在热处理过程中,无损检测技术是一种重要的工具,用于检测材料是否存在缺陷或异常。
首先,热处理过程中最常用的无损检测技术之一是超声波检测。
超声波检测利用声波在材料中传播的原理,通过检测声波的传播速度和衰减情况来判断材料中是否存在缺陷。
在热处理过程中,超声波检测可以用于检测材料的内部结构是否发生变化,例如晶粒尺寸的改变、相变的发生等。
其次,磁粉检测也是热处理过程中常用的无损检测技术之一。
磁粉检测利用磁场的作用,通过在材料表面涂覆磁粉,并施加磁场,以检测材料表面或近表面的缺陷。
在热处理过程中,磁粉检测可以用于检测材料的表面是否存在裂纹、裂纹的深度和长度等。
另外,涡流检测也是一种常用的无损检测技术。
涡流检测利用导体中的涡流效应,通过在材料表面施加交变磁场,检测材料中的缺陷。
在热处理过程中,涡流检测可以用于检测材料中的细小裂纹、气孔等缺陷。
最后,X射线检测也是常用的无损检测技术之一。
X射线检测利用X射线的穿透能力,通过照射材料并
检测透射或散射的X射线来判断材料中的缺陷。
在热处理过程中,X射线检测可以用于检测材料的密度变化、晶体结构的改变等。
综上所述,热处理过程中的无损检测技术是一种非常重要的工具,可以用于检测材料中的缺陷和异常。
超声波检测、磁粉检测、涡流检测和X射线检测是常用的无损检测技术,它们各有优势和适用范围。
在实际应用中,可以根据具体情况选择合适的无损检测技术,以确保热处理过程的质量和安全。
圆钢焊接要求
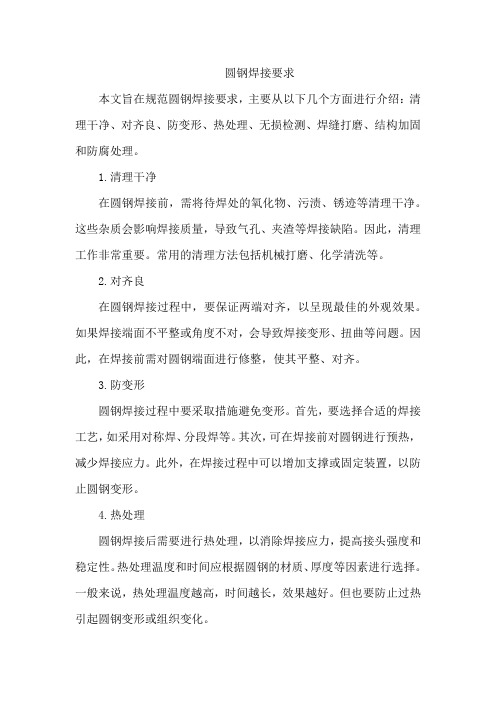
圆钢焊接要求本文旨在规范圆钢焊接要求,主要从以下几个方面进行介绍:清理干净、对齐良、防变形、热处理、无损检测、焊缝打磨、结构加固和防腐处理。
1.清理干净在圆钢焊接前,需将待焊处的氧化物、污渍、锈迹等清理干净。
这些杂质会影响焊接质量,导致气孔、夹渣等焊接缺陷。
因此,清理工作非常重要。
常用的清理方法包括机械打磨、化学清洗等。
2.对齐良在圆钢焊接过程中,要保证两端对齐,以呈现最佳的外观效果。
如果焊接端面不平整或角度不对,会导致焊接变形、扭曲等问题。
因此,在焊接前需对圆钢端面进行修整,使其平整、对齐。
3.防变形圆钢焊接过程中要采取措施避免变形。
首先,要选择合适的焊接工艺,如采用对称焊、分段焊等。
其次,可在焊接前对圆钢进行预热,减少焊接应力。
此外,在焊接过程中可以增加支撑或固定装置,以防止圆钢变形。
4.热处理圆钢焊接后需要进行热处理,以消除焊接应力,提高接头强度和稳定性。
热处理温度和时间应根据圆钢的材质、厚度等因素进行选择。
一般来说,热处理温度越高,时间越长,效果越好。
但也要防止过热引起圆钢变形或组织变化。
5.无损检测在圆钢焊接过程中,需要进行无损检测,以确保焊接质量。
常用的无损检测方法包括超声波检测和射线检测等。
这些检测方法可以检测出焊缝内部的气孔、夹渣、裂纹等缺陷,从而保证焊接接头在使用过程中的安全性。
6.焊缝打磨圆钢焊接完成后,需要对焊缝进行打磨,以呈现平滑的外观。
打磨可以去除焊缝表面的氧化物、熔渣等杂质,使焊缝更加美观,同时也有利于提高焊缝的耐腐蚀性。
7.结构加固在圆钢焊接后,有时需要对结构进行加固,以增加结构的稳定性和强度。
常用的加固方法包括角焊缝和对接焊缝的加强。
角焊缝加固可以在圆钢与支撑结构的连接处增加焊缝,以提高结构的稳定性。
对接焊缝的加强可以通过增加对接长度、减小对接间隙等方式来实现。
8.防腐处理圆钢焊接后需要进行的防腐处理方法包括涂漆和化学处理等。
涂漆是一种常见的防腐措施,可以在圆钢表面形成一层保护膜,防止腐蚀介质侵入。
合金探伤热处理先后

合金探伤热处理先后
合金探伤和热处理是两个独立的工艺过程,一般情况下它们的顺序是先进行合金探伤,再进行热处理。
合金探伤是一种无损检测方法,用于检测材料内部的缺陷、裂纹、气孔等问题。
通过使用探伤仪器,对合金进行超声波、磁性颗粒、涡流等探测技术,可以及时发现和诊断材料的缺陷,并进行修复或更换。
热处理是改变材料的组织结构和性能的方法。
它包括加热材料至一定温度,然后通过冷却或保温的方式,使材料在一定时间内发生相变或晶粒尺寸变化,从而改变其机械性能、物理性能和化学性能。
在合金制品的生产过程中,由于合金常会有各种不完美的缺陷,例如气孔、夹杂物、裂纹等,这些缺陷会对合金构件的性能和使用寿命产生不良影响。
因此,在进行热处理之前,必须先进行合金探伤,及时发现并处理这些缺陷,避免在热处理过程中进一步恶化或扩展。
综上所述,合金探伤和热处理先后是为了保证合金制品的质量和性能,先进行合金探伤,发现并修复缺陷,然后再进行热处理,改善合金材料的性能和结构。
金结中心热处理方式、无损检测要点
产生的原因:焊接电流太小;运条速度太快;焊条角度不当或电弧发生 偏吹;坡口角度或对口间隙太小等因素造成。
焊接缺陷的特征
夹渣:是由焊接冶金反应产生的,焊后残留在焊缝金属中 的非金属夹杂物。
焊接缺陷的特征
2.2、冷裂纹:指焊缝在Ac3以下温度(约300-200℃以下 ),冷却过程中或冷却至室温以后产生的裂纹。
焊接缺陷的特征
未熔合:指熔化焊时,焊道与母材之间或焊道与焊道之间,未能完全熔 化结合的部分称未熔合。多数产生在层间或坡口边缘。
产生的原因:焊接时线能量过小,焊条偏弧(偏于一侧)使母材或前一层 焊缝金属未得到充分熔化,就被填充金属敷盖而造成。另外当母材坡口 或前一层焊缝表面有锈或脏物,焊接时由于温度不够,未能将其熔化而 盖上填充金属,也会造成边缘及层间未熔合。
金属材料相关知识
5、钢件在淬火状态下有三个主要特征 5.1、组织特征:钢件淬火后的组织,主要由马氏体或马
氏体+残余奥氏体组成,还可能存在一些未熔碳化物; 5.2、硬度特性:钢件淬火后,淬火组织硬度、强度高,
塑性、韧性低; 5.3、应力特征:钢件淬火后,钢件表面或心部所处有不
同应力状态,有拉应力或压应力,在工件内部保持平衡, 不及时消除淬火钢件应力,在一定情况下会产生开裂。
目视检测(VT) 涡流检测(ET) 渗透检测(PT) 磁粉检测(MT) 射线检测(RT) 超声检测(UT) 超声衍射时差法检测(TOFD) 声发射检测(AE) 泄漏检测(LT)
无损检测基础知识
无损检测就是一种无破坏性的检测方法,检查材料或工件 表面或内部缺陷存在的情况,保证产品质量和设备的安全 使用
焊接施工、热处理与无损检测控制要点培训试题
焊接施工、热处理与无损检测控制要点培训试题1、下列哪些属于焊接工艺评定内容。
()A、焊接工艺指导书、焊接工艺评定报告B、焊缝无损检测报告、焊接工艺评定施焊记录表、焊缝晶间腐蚀报告C、热处理报告及相应的光谱检测和硬度检测报告D、焊接材料与母材产品质量证明书及合格证等相关文件E、以上都是2、下列关于焊材管理说法错误的是。
()A、进入施工库房的焊接材料,应该包装完好,标记清楚,并提供相应的质保书和自检合格记录,施工承包商向监理报验经确认合格后方可使用B、焊材使用需遵循,“先人先用”的原则,SHrr3501-2021中8.1.3规定库存期不宜超过五年,超过五年的焊条,应检查外观并进行工艺性能试验,符合要求后方可使用C、焊材库房内配备驱湿机和温湿度计,并保证良好的通风条件,库房相对湿度控制在小于等于60%,温度在10・35℃之间为宜,焊材离四周墙面及地面时距离不得小于300mmD、焊工凭,焊工作业证,领用相应的焊材,焊材由专人负责管理、发放、回收。
焊条必须由焊工本人领取使用,也可以他人代领,不得使用别人用剩的焊材,焊条筒内不同种类焊条严禁混放()3、下列有关焊口标识管理说法正确的是。
()A、对于公称直径DN>100mm管段,采用长方格表示方法,具体样式见下图、对公称直径DN≤100mm的管段允许不用长方格标识方法,直接采用字段标识,标识内容可相应简化,但必须包含[管线号H焊缝号H焊工]B、标识距离焊口100mm,需热处理焊缝应距离焊口200mm。
标识填写时机为:管段下料完成后,填写管线号、材质、规格;组对完后,标注焊口号;开始焊接时,标注焊工号,当有多名焊工焊接时,应依次标上各焊工号,在焊接结束并自检合格后,由最后一名焊工在长方格内标注焊接结束日期;焊接完成后,施工单位焊接质检员外观检查合格,由检查人填写检查人姓名、检查日期C、焊缝实体标识必须保持至管道施工任务完成,施工过程中发生遗失、缺损的,必须及时恢复,恢复的标识应与原标识一致,保证不因实体标识未及时恢复影响施工、检测任务的正常开展D、以上都对4、关于铭银不锈钢焊接管理说法错误的是。
(整理)astm c 1279- 退火、热处理和全钢化平玻璃边缘和表面应力的无损光弹性无损测量标准方法 译文
译文名称:ASTM C1279-2009退火、热处理和全钢化平玻璃边缘和表面应力光弹性无损测量标准方法1.总则1.1这个测试方法覆盖了退火、热增强和全钢平板玻璃的边缘和表面应力检测。
1.2这个测试方法是无损的。
1.3这个测试方法是用光线传输,即光线透过玻璃。
1.4这个测试方法不适于化学钢化玻璃。
1.5使用过程描述,表面应力只能在浮法玻璃的锡面上检测。
1.6表面应力的测量仪器设计的表面反射指数是被规范在一定范围内。
1.7值的单位为SI单位。
没有其他的测量单位包括在标准中。
1.8这个标准未明确顾及安全的地方,如果有的话,与此相关联的可以使用。
这个使用人应当建立适当安全和健康行为和决定其先期使用的适用性。
2.涉及文件2.1ASTM标准C162玻璃技术和玻璃生产C770测量玻璃应力的方法-光系数C1048热处理浮法玻璃规范-Kind HS、KindFT镀膜和非镀膜玻璃E691产品和实验室内研究测试方法的测试精度操作2.2其他文件工程标准手册钢化玻璃表面和边缘应力3.术语3.1定义:3.1.1分析仪-一个偏振元件,在被测样品和观察者之间指定位置。
3.1.2起偏器-一个单向平面偏振方向透射光的光源装配。
位置在光源和待测样品之中。
3.1.3光程差补偿片-一个光学设备,一种产生高质量透过光程差的双折射材料:位置在待测样品和分析仪之间。
3.2这种方法的条款定义,涉及C162术语。
4.测试方法概要4.1这个标准里面描述了两种测试方法:4.1.1步骤A-描述一种使用接近平行的光线传播到表面上的表面应力测试方法。
4.1.2步骤B-描述一种使用光线垂直方向传播到玻璃表面上边缘应力测试方法。
4.2两种方法都使用光弹性的基本概念。
因为要产生应力,材料应具有各向异性和双折射性。
当偏振光传播通过各向异性材料,沿着最大和最小主应力方向分解成不同速度和振动方向的光线,这两光线产生相对光程差,相对光程差与测量的应力成正比;而且可以用补偿片精确检测。
热处理质量检验的内容和方法
热处理质量检验的内容和方法热处理是机械制造中的一个重要环节,热处理的质量好坏,直接关系着产品或零件的内在质量及性能。
在生产中影响热处理质量的因素很多,为了确保产品质量达到国家标准或行业标准规定的要求,所有的热处理零件从原材料进厂开始,每一道热处理工序后都必须进行严格的检验。
产品出现质量问题不能直接转入下道工序,这样才能确保产品质量。
另外在热处理生产中一个称职的检验员,只是按照技术要求对热处理后的工件进行质量检验和把关是不够的。
更重要的任务是当好参谋。
在热处理的生产过程中首先要看操作者是不是严格执行工艺规程,工艺参数是否正确。
在质量检验过程中如果发现质量问题要帮助操作者分析产生质量问题的原因,找出解决问题的方法。
把可能影响热处理质量的各种因素都控制起来以保证生产出质量优良、性能可靠、用户满意的合格品。
一、热处理质量检验的内容(一)预先热处理预先热处理的目的是改善原材料的组织、软化,以便于机械加工,消除应力,获得理想的热处理原始组织等。
对有些大件预先热处理也是最终热处理,预先热处理一般采用正火及退火。
1)铸钢件的扩散退火由于在高温长时间加热晶粒易粗大,在退火后还应再进行一次完全退火或正火来细化晶粒。
2)结构钢的完全退火一般用于中低碳钢铸件、焊接件、热轧及热锻件的改善组织、细化晶粒、降低硬度、消除应力等。
3)合金结构钢的等温退火主要用于42CrMo等钢的退火。
4)工具钢的球化退火球化退火的目的是改善切削加工性能及冷变形性能。
5)去应力退火去应力退火的目的是消除铸钢件、焊接件、机加工件的内应力,减少后工序的变形与开裂。
6)再结晶退火再结晶退火的目的是消除工件的冷作硬化。
7)正火正火的目的是改善组织、细化晶粒,可作为预先热处理,也可作为最终热处理。
上述退火与正火获得的组织都是珠光体。
在质量检验中,重点是做工艺参数的检查,即在退火及正火进行过程中,做流动检查工艺参数的执行情况,这是首要的,在过程结束后主要检验硬度,金相组织,脱碳深度,及退火正火目的项,带状,网状碳化物等。
- 1、下载文档前请自行甄别文档内容的完整性,平台不提供额外的编辑、内容补充、找答案等附加服务。
- 2、"仅部分预览"的文档,不可在线预览部分如存在完整性等问题,可反馈申请退款(可完整预览的文档不适用该条件!)。
- 3、如文档侵犯您的权益,请联系客服反馈,我们会尽快为您处理(人工客服工作时间:9:00-18:30)。
第七章无损检测
无损检测是利用、、、、渗透等方法在不损害被检物(材料,零件,构件等)的前提下,掌握其内部状况的现代检测技术。
无损检测包括缺陷检测(无损探戈伤)及材质与热处理质量检测两部分。
目视检测(VT)
目视检测,在国内实施的比较少,但在国际上非常重视的无损检测第一阶段首要方法。
按照国际惯例,目视检测要先做,以确认不会影响后面的检验,再接着做四大常规检验。
例如BINDT的PCN认证,就有专门的VT1、2、3级考核,更有专门的持证要求。
VT常常用于目视检查焊缝,焊缝本身有工艺评定标准,都是可以通过目测和直接测量尺寸来做初步检验,发现咬边等不合格的外观缺陷,就要先打磨或者修整,之后才做其他深入的仪器检测。
例如焊接件表面和铸件表面较多VT做的比较多,而锻件就很少,并且其检查标准是基本相符的。
射线照相法(RT)
是指用或γ射线穿透试件,以胶片作为记录信息的器材的无损检测方法,该方法是最基本的,应用最广泛的一种非破坏性检验方法。
原理:射线能穿透肉眼无法穿透的物质使胶片感光,当X射线或r射线照射胶片时,与普通光线一样,能使胶片乳剂层中的卤化银产生潜影,由于不同密度的物质对射线的吸收系数不同,照射到胶片各处的射线强度也就会产生差异,便可根据暗室处理后的底片各处黑度差来判别缺陷。
总的来说,RT的定性更准确,有可供长期保存的直观图像,总体成本相对较高,而且射线对人体有害,检验速度会较慢。
超声波检测(UT)
原理:通过超声波与试件相互作用,就反射、透射和散射的波进行研
究,对试件进行宏观、几何特性测量、组织结构和力学性能变化的检测和表征,并进而对其特定应用性进行评价的技术。
适用于金属、非金属和复合材料等多种试件的无损检测;可对较大厚度范围内的试件内部缺陷进行检测。
如对,可检测厚度为1~2mm的薄壁管材和板材,也可检测长的钢锻件;而且缺陷定位较准确,对面积型缺陷的检出率较高;灵敏度高,可检测试件内部尺寸很小的缺陷;并且检测成本低、速度快,设备轻便,对人体及环境无害,现场使用较方便。
但其对具有复杂形状或不规则外形的试件进行超声检测有困难;并且缺陷的位置、取向和形状以及材质和晶粒度都对检测结果有一定影响,检测结果也无直接见证记录。
磁粉检测(MT)
原理:铁磁性材料和工件被磁化后,由于不连续性的存在,使工件表面和近表面的磁力线发生局部畸变而产生漏,吸附施加在工件表面的磁粉,形成在合适光照下目视可见的磁痕,从而显示出不连续性的位置、形状和大小。
适用性和局限性:
磁粉探伤适用于检测铁磁性材料表面和近表面尺寸很小、间隙极窄(如可检测出长、宽为微米级的裂纹)目视难以看出的不连续性;也可对原材料、半成品、成品工件和在役的零部件检测,还可对板材、型材、管材、棒材、焊接件、铸钢件及锻钢件进行检测,可发现裂纹、夹杂、发纹、白点、折叠、冷隔和疏松等缺陷。
但磁粉检测不能检测材料和用奥氏体不锈钢焊条焊接的焊缝,也不能检测铜、铝、镁、钛等非磁性材料。
对于表面浅的划伤、埋藏较深的孔洞和与工件表面夹角小于20°的分层和折叠难以发现。
渗透检测(PT)
原理:零件表面被施涂含有荧光染料或着色染料的渗透剂后,在毛细管作用下,经过一段时间,渗透液可以渗透进表面开口缺陷中;经去除零件表面多余的渗透液后,再在零件表面施涂显像剂,同样,在毛细管的作用下,显像剂将吸引缺陷中保留的渗透液,渗透液回渗到显像剂中,在一定的光源下(紫外线光或白光),缺陷处的渗透液痕迹被现实,(黄绿色荧光或鲜艳红色),从而探测出缺陷的形貌及分布状态。
优点及局限性:
渗透检测可检测各种材料,金属、非金属材料;磁性、非磁性材料;焊接、锻造、轧制等加工方式;具有较高的灵敏度(可发现μm宽缺陷),同时显示直观、操作方便、检测费用低。
但它只能检出表面开口的缺陷,不适于检查多孔性疏松材料制成的工件和表面粗糙的工件;只能检出缺陷的表面分布,难以确定缺陷的实际深度,因而很难对缺陷做出定量评价,检出结果受操作者的影响也较大。
涡流检测(ET)
原理:将通有交流电的线圈置于待测的金属板上或套在待测的金属管外。
这时线圈内及其附近将产生交变磁场,使试件中产生呈旋涡状的感应交变电流,称为涡流。
涡流的分布和大小,除与线圈的形状和尺寸、交流电流的大小和频率等有关外,还取决于试件的电导率、磁导率、形状和尺寸、与线圈的距离以及表面有无裂纹缺陷等。
因而,在保持其他因素相对不变的条件下,用一探测线圈测量涡流所引起的磁场变化,可推知试件中涡流的大小和相位变化,进而获得有关电导率、缺陷、材质状况和其他物理量(如形状、尺寸等)的变化或缺陷存在等信息。
但由于涡流是交变电流,具有集肤效应,所检测到的信息仅能反映试件表面或近表面处的情况。
应用:按试件的形状和检测目的的不同,可采用不同形式的线圈,通常有穿过式、探头式和插入式线圈3种。
穿过式线圈用来检测管材、棒材和线材,它的内径略大于被检物件,使用时使被检物体以一定的速度在线圈内通过,可发现裂纹、夹杂、凹坑等缺陷。
探头式线圈适用于对试件进行局部探测。
应用时线圈置于金属板、管或其他零件上,可检查飞机起落撑杆内筒上和涡轮发动机叶片上的疲劳裂纹等。
插入式线圈也称内部探头,放在
管子或零件的孔内用来作内壁检测,可用于检查各种管道内壁的腐蚀程度等。
为了提高检测灵敏度,探头式和插入式线圈大多装有磁芯。
涡流法主要用于生产线上的金属管、棒、线的快速检测以及大批量零件如轴承钢球、汽门等的探伤(这时除涡流仪器外尚须配备自动装卸和传送的机械装置)、材质分选和硬度测量,也可用来测量镀层和涂膜的厚度。
优缺点:涡流检测时线圈不需与被测物直接接触,可进行高速检测,易于实现自动化,但不适用于形状复杂的零件,而且只能检测导电材料的表面和近表面缺陷,检测结果也易于受到材料本身及其他因素的干扰。