关于单机架冷轧节能降耗技术探讨
关于轧钢生产中节能技术的探讨
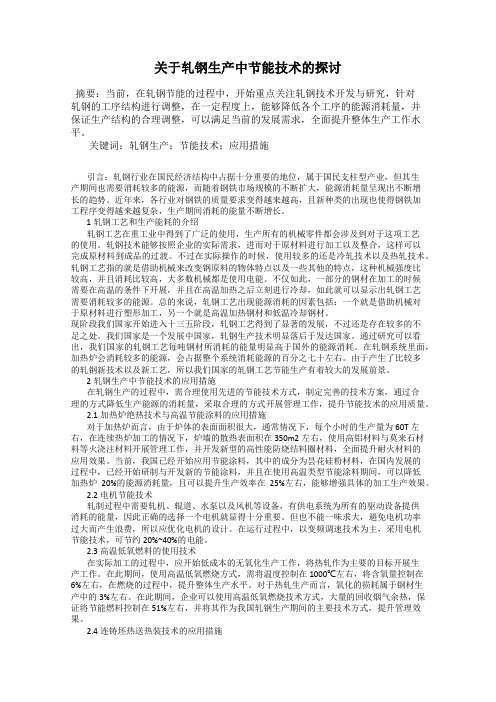
关于轧钢生产中节能技术的探讨摘要:当前,在轧钢节能的过程中,开始重点关注轧钢技术开发与研究,针对轧钢的工序结构进行调整,在一定程度上,能够降低各个工序的能源消耗量,并保证生产结构的合理调整,可以满足当前的发展需求,全面提升整体生产工作水平。
关键词:轧钢生产;节能技术;应用措施引言:轧钢行业在国民经济结构中占据十分重要的地位,属于国民支柱型产业,但其生产期间也需要消耗较多的能源,而随着钢铁市场规模的不断扩大,能源消耗量呈现出不断增长的趋势。
近年来,各行业对钢铁的质量要求变得越来越高,且新种类的出现也使得钢铁加工程序变得越来越复杂,生产期间消耗的能量不断增长。
1轧钢工艺和生产能耗的介绍轧钢工艺在重工业中得到了广泛的使用,生产所有的机械零件都会涉及到对于这项工艺的使用。
轧钢技术能够按照企业的实际需求,进而对于原材料进行加工以及整合,这样可以完成原材料到成品的过渡。
不过在实际操作的时候,使用较多的还是冷轧技术以及热轧技术。
轧钢工艺指的就是借助机械来改变钢原料的物体特点以及一些其他的特点,这种机械强度比较高,并且消耗比较高,大多数机械都是使用电能。
不仅如此,一部分的钢材在加工的时候需要在高温的条件下开展,并且在高温加热之后立刻进行冷却,如此就可以显示出轧钢工艺需要消耗较多的能源。
总的来说,轧钢工艺出现能源消耗的因素包括:一个就是借助机械对于原材料进行塑形加工,另一个就是高温加热钢材和低温冷却钢材。
现阶段我们国家开始进入十三五阶段,轧钢工艺得到了显著的发展,不过还是存在较多的不足之处。
我们国家是一个发展中国家,轧钢生产技术明显落后于发达国家。
通过研究可以看出,我们国家的轧钢工艺每吨钢材所消耗的能量明显高于国外的能源消耗。
在轧钢系统里面,加热炉会消耗较多的能源,会占据整个系统消耗能源的百分之七十左右。
由于产生了比较多的轧钢新技术以及新工艺,所以我们国家的轧钢工艺节能生产有着较大的发展前景。
2轧钢生产中节能技术的应用措施在轧钢生产的过程中,需合理使用先进的节能技术方式,制定完善的技术方案,通过合理的方式降低生产能源的消耗量,采取合理的方式开展管理工作,提升节能技术的应用质量。
轧钢工艺节能技术研究

轧钢工艺节能技术研究轧钢工艺是钢铁生产过程中至关重要的环节之一,节能技术的研究对于提高钢铁工业的能源利用率和降低环境污染具有重要意义。
本文将探讨一些目前常用的轧钢工艺节能技术,并对其进行研究和分析。
首先,采用先进的轧机设备是实现节能目标的首要条件之一、传统的轧机设备普遍存在能源消耗高、工作效率低、设备损耗严重等问题。
而采用先进的轧机设备,如连轧机、宽带轧机、多道次轧制等,能够有效提高轧钢工艺的工作效率,降低能源消耗,并且减少轧机设备的损耗,实现节能效果。
其次,轧钢过程中的热处理技术也是节能的重要手段之一、热处理是钢材性能调控的关键环节,传统的热处理技术存在温度控制不准确、能源浪费、环境污染等问题。
而采用先进的热处理技术,如间歇式热处理、连续式热处理等,能够减少能源消耗,提高热处理的效率,同时还能够降低环境污染,实现节能效果。
再次,合理利用废热也是轧钢工艺节能的重要手段之一、在轧钢过程中,会产生大量的废热,传统的处理方式主要是通过冷却设备冷却后排放,存在能源浪费的问题。
而采用废热回收技术,可以将废热转化为能源,如用于加热和发电等,实现废热资源的合理利用,达到节能的效果。
最后,建立完善的节能管理体系是保证轧钢工艺节能效果的重要保障。
通过建立完善的节能管理体系,包括能源消耗监测、能源效率评估、节能技术应用等方面的管理,可以实现对轧钢过程中能源的全面监控和评估,及时发现问题和改进措施,确保节能效果的实现。
综上所述,轧钢工艺节能技术研究对于提高钢铁工业的能源利用率和降低环境污染具有重要意义。
通过采用先进的轧机设备、热处理技术,合理利用废热,并建立完善的节能管理体系,可以实现轧钢工艺的节能效果,为钢铁工业的可持续发展做出贡献。
轧钢生产工艺节能减排技术研究论文

轧钢生产工艺节能减排技术研究论文轧钢生产工艺节能减排技术研究论文摘要:在国内实施轧钢操作的过程中需要损耗大量的能源,进而从各个环节采用适当的方法来进行节能可以说是非常可行的。
现如今最为盛行的就是发展连铸生产,实施热送热装的形式,利用直扎的技术,尽可能的避免二火成材,在提升工作效率上还是可以有所改进的,尤其是需要加大力度来针对轧钢节能管理工作进行完善和优化,促使轧钢节能技术能够更好的发展。
关键词:轧钢;节能技术;热送热装在最近的几年时间里,伴着国内经济水平的不断提升,带动了各行各业的迅猛发展,进而对钢材的需求量也在不断的增多,但是因为钢铁行业在能源消耗上花费较大,已经达到了全国总能耗的百分之十五左右,轧钢操作的能源消耗在整个钢铁行业中的耗能占比也达到了15%左右,并且还在逐年的增加,因此,做好轧钢节能工作是保证国家健康发展的最首要问题。
1冷轧压缩空气系统节能技术冷轧压缩空气通常都是由企业内部的空压站给予提供的,就其整个运行系统来说问题集中凸显在下面几个层面:首先,系统内压力变化较大,压力供应不稳定,进而不能保证机械的正常用气的需要。
一线机械的压缩空气系统通常都是利用直管式配管的形式,因为所有的用气点所需要的气量都是有所不同的,轧钢机在运行中对气体的需求量较大,压力降低,针对仪表用气短时的冲击十分严重,进而对保证生产的稳定性是十分不利的。
其次,空压机添加和卸载程序次数较多,需要能源较大。
空压机在记载的过程中,系统提供的电流不能满足空压机的需求,压力在短时间内提高到卸载压力,进而迅速完成卸载。
1.1改造方案(1)结合实际情况完善空压站的系统结构,保证生产的稳定进行。
将空压机的气体输出口与储存气体的器皿进行连接,器皿的初期口与除油器、干燥器、过滤器进行连接。
储存气体的器皿在系统运行中能够起到一个缓冲的效果,进而削弱阻力,达到延缓卸载环节时间的目的,节省电能。
(2)在轧钢设备制动结构中采用储气罐和止回阀分压的供气方式。
轧钢生产技术发展与节能降耗研究

轧钢生产技术发展与节能降耗研究摘要:目前我国的轧钢生产技术与工艺依然处在一个相对落后的层面,一些生产工艺与技术还处于探索阶段,落后的制造工艺严重影响我国钢铁质量与产量。
同时随着电价的上涨,能源消耗也在不断上升;因此,节能工作变得尤为迫切。
轧钢厂也相应地采取了诸多措施来降低电能成本,如防止无效运行、切换到节能设施以及加强电力监测。
本研究就轧钢生产工艺与技术展开深入剖析,并就轧钢生产的节能举措从三个方面展开分析,以期为我国轧钢技术的发展提供借鉴。
关键词:轧钢;工艺;技术;钢材生产;节能轧钢生产对于能源的需求量极大,而轧钢工艺的节能与否,不仅关系着企业的生产成本,更会对我国的环境造成直接的影响。
正因如此,现阶段与轧钢有关的各项新型技术、新型机械设备均是围绕节能为根本进行开发。
本文简要分析了我国轧钢工艺的节能方向,并深入研究了实现轧钢工艺的节能途径与措施,希望能为我国的钢铁工业带来一定的参考价值。
1简述轧钢生产工艺轧钢技术是指利用机械设备将钢材原料原有的形态特征彻底改变,然而改变钢材原料原有特征的机械设备通常需要消耗非常高的能量,所需的机械强度也非常高,基本上所有的机械设备都需要使用电能。
除此以外,一些钢材在生产加工的过程中,首先需要在高温环境中操作,当高温加热完成后,就需要马上对其进行冷却,在这样的生产过程中,发现将会消耗掉许多能源,一些能源被白白浪费掉。
总而言之,轧钢生产工艺在生产过程中需要消耗过多能源的原因有两个方面,首先是利用机械设备来加工钢材原材料,塑形过程同样需要较多能量;其次就是钢材的生产过程,在高温加热之后,就需要低温冷却,这两个过程同样会消耗大量的能量。
2轧钢技术的分类2.1热轧带钢轧制技术上世纪70年代以前,我国热轧带钢的轧制技术十分落后,只能引进国外的先进技术,并逐渐吸收和消化,经过几十年的努力,终于形成了VCL轧辊板型控制技术,并不断创新,能够很好地控制热轧和冷却过程中钢材变形的情况。
单机架轧机控轧控冷生产中厚板的节能工艺

单机架轧机控轧控冷生产中厚板的节能工艺摘要:轧机控轧主要的目的就是在热轧的条件下生产出一些比较好的钢材,韧性不仅仅要好,强度也要高。
对轧机控轧的方法主要就是有两种。
轧机控轧的主要作用就是要细化铁素的晶粒,提高钢材的硬度和韧性,对其不良的地方要不断的改善。
若是想要单机架的后板提高就一定要对轧机控轧进行控制,因为轧机控轧会对后板轧机的产量有很大的影响,并且对双机架也有一定的影响。
为了提高轧机控轧的产量,主要就是采用交叉轧制,能够缩短中间的冷却的时间和控制冷却等等措施,另外还有综合加热等等方面控制节能。
由此可见对钢板建设最有用的措施控轧控冷的工艺。
本文主要就针对单机架轧机控轧控冷生产中厚板的节能工艺进行了探讨,以供参考。
关键词:单机架轧机控轧控冷生产节能工艺由于人们对控制轧制和控制冷却的机理认识在不断的深化,并且经济的水平也在不断的提高,现代化的生产水平和检验手段越来越高超,使其控制轧制和控制冷却的技术也被要求不断在完善。
主要就是被应用于钢材的生产中,特别是在中厚板的生产中是最为普遍的。
在日常的生产中就会发现,轧机控轧对轧机的产量影响是比较大的,在目前很多的国家中,在对中厚板的生产过程中都是去开发比较适合自己家生产的轧制方案,在轧制的过程中最好在配合上冷却的装置,更加完美,使得产品能够更加的强韧,并且并没有比较高的成本损耗,又提高竞争的能力。
控轧控冷在不断的被完善和发展,另外在加上一些现代化的技术和手段不仅仅能够生产出低碳的钢,并且还能够生产出含有合金元素的高强度的钢。
并且这些设备配合使用,还能够生产出高碳钢和合金钢。
这些钢能够广泛的应用于板材和带材的生产,还能够用于棒材和型材等等型号材料的生产。
还能够用于生产铁素体珠光体钢,还能够生产低碳贝氏体钢。
1 控轧控冷的相关作用控轧控冷的技术首先就是要在后板的生产中得到广泛的应用,控轧控冷的技术生产的中厚板,也能够用来制造石油、天然气输送关心和采油的平台等等,还有一些桥梁、船舶和具有压力的容器等等一些大型工程的设备。
轧钢生产中节能技术的应用研究
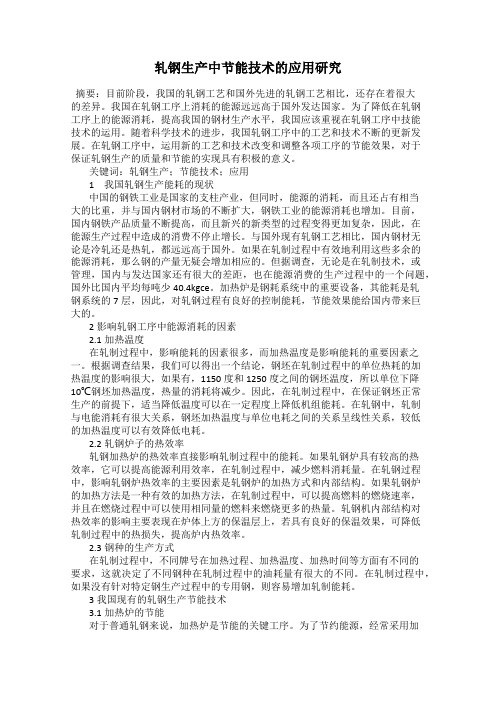
轧钢生产中节能技术的应用研究摘要:目前阶段,我国的轧钢工艺和国外先进的轧钢工艺相比,还存在着很大的差异。
我国在轧钢工序上消耗的能源远远高于国外发达国家。
为了降低在轧钢工序上的能源消耗,提高我国的钢材生产水平,我国应该重视在轧钢工序中技能技术的运用。
随着科学技术的进步,我国轧钢工序中的工艺和技术不断的更新发展。
在轧钢工序中,运用新的工艺和技术改变和调整各项工序的节能效果,对于保证轧钢生产的质量和节能的实现具有积极的意义。
关键词:轧钢生产;节能技术;应用1我国轧钢生产能耗的现状中国的钢铁工业是国家的支柱产业,但同时,能源的消耗,而且还占有相当大的比重,并与国内钢材市场的不断扩大,钢铁工业的能源消耗也增加。
目前,国内钢铁产品质量不断提高,而且新兴的新类型的过程变得更加复杂,因此,在能源生产过程中造成的消费不停止增长。
与国外现有轧钢工艺相比,国内钢材无论是冷轧还是热轧,都远远高于国外。
如果在轧制过程中有效地利用这些多余的能源消耗,那么钢的产量无疑会增加相应的。
但据调查,无论是在轧制技术,或管理,国内与发达国家还有很大的差距,也在能源消费的生产过程中的一个问题,国外比国内平均每吨少40.4kgce。
加热炉是钢耗系统中的重要设备,其能耗是轧钢系统的7层,因此,对轧钢过程有良好的控制能耗,节能效果能给国内带来巨大的。
2影响轧钢工序中能源消耗的因素2.1加热温度在轧制过程中,影响能耗的因素很多,而加热温度是影响能耗的重要因素之一。
根据调查结果,我们可以得出一个结论,钢坯在轧制过程中的单位热耗的加热温度的影响很大,如果有,1150度和1250度之间的钢坯温度,所以单位下降10℃钢坯加热温度,热量的消耗将减少。
因此,在轧制过程中,在保证钢坯正常生产的前提下,适当降低温度可以在一定程度上降低机组能耗。
在轧钢中,轧制与电能消耗有很大关系,钢坯加热温度与单位电耗之间的关系呈线性关系,较低的加热温度可以有效降低电耗。
2.2轧钢炉子的热效率轧钢加热炉的热效率直接影响轧制过程中的能耗。
浅谈轧钢设备能力及生产线产能与节能降耗

浅谈轧钢设备能力及生产线产能与节能降耗摘要:从当下轧钢所具有的生产综合经济性出发,对轧钢生产大型化以及连续化过程当中所存在的问题进行有效的分析,探讨对轧钢设备能力以及生产线产能进行合理选择所具有的可能性。
目前也认为轧钢生产的节能降耗和轧钢设备能力以及生产线的产能之间的联系相对是比较密切的,在钢材市场需求相对旺盛的。
这一时期轧钢的生产大型化及连续化应该属于唯一的一种选择。
尽管从当前的情况来看已经采取了各种节能的措施,但是面对大型化以及连续化轧钢生产线,现在采取的技术仍然是比较落后的,所以对经济型的轧钢设备和轧钢生产线进行有效的发展是一个必然的选择和趋势。
关键词:轧钢设备;轧钢生产;节能降耗;经济性进行规模经济的有效实施,需要从设备生产线以及应用工艺的过程这些角度出发,应用更加先进的工艺手段,同时保证应用的设备大型化以及专业化,这样才能够实行大批量的生产,降低产品的单位投资成本,实现产品的标准化,这样才可以使得产品的质量得到提升,产生良好的经济效果。
在当前我国改革开放以来,国民经济对于钢铁产品的需求是在不断增加的,引进了更多先进的技术,钢铁工业直接进入了一个快速发展的道路。
钢铁生产经济性对于产能有强烈的依赖,高产能带来的收益同样也比较高,所以国内的钢铁产能也是在急剧扩大的,因此在当下需要从另一个角度对轧钢生产模式以及应用的技术手段重新进行分析和审视。
1轧钢设备能力以及节能在当前可以明确的一点是,轧钢设备能力与轧钢的生产节能两者之间本身就有直接并且紧密的联系。
随着当前轧钢设备的大型化发展连续化以及自动化的进步,轧缸设备的能力水平是在不断提升的。
设备能力提高的一个核心,就是在于轧制,轧制速度的不断提高在廉价能源时代是相对具有一定可操作性的。
但是能源价格比较高的这一时期所获得的经济效益也会随之而下降,因为轧制速度的提高会使得在其中所产生的能源消耗不断的上升。
小型的高材连续轧制生产所出现电力方面的消耗要远远高于横列式轧机和半连续式轧机这两种设备,而之所以出现这种现象,主要的原因就是因为连续轧制生产的过程当中采用的都是大规格的坯料以及高速轧制的方式,大规格的坯料和高速轧制可以达成高产能的目标。
我国轧钢工艺的节能方向及途径探究

我国轧钢工艺的节能方向及途径探究【摘要】本文主要研究我国轧钢工艺的节能方向及途径,通过对轧钢工艺的节能潜力进行分析,提出了优化轧钢工艺参数、采用先进设备、推广新技术、智能化管理等节能措施。
通过实施这些措施,可以有效减少能源消耗、降低生产成本,提高生产效率。
未来,我们可以继续探索更多节能方向和途径,进一步提升轧钢工艺的节能水平,为我国钢铁行业的可持续发展做出贡献。
通过这些努力,我们可以实现更加清洁、高效的钢铁生产,助力我国钢铁行业向着智能化、绿色化的方向发展。
【关键词】节能、我国轧钢工艺、优化、先进设备、新型技术、智能化管理、实施效果、建议、展望、未来研究1. 引言1.1 研究背景我国轧钢工艺是钢铁行业的重要环节,在工业生产中所占的比重较大。
由于传统轧钢工艺存在能耗高、资源浪费、环境污染严重等问题,迫切需要实现节能减排,提高生产效率。
目前,我国钢铁产业正处于转型升级的关键期,提高轧钢工艺的节能水平已成为一个重要课题。
在国家提出要建设节约资源型、环境友好型社会的背景下,探索轧钢工艺的节能方向及途径,具有重要的现实意义和挑战。
本文旨在深入研究我国轧钢工艺的节能潜力,探讨优化轧钢工艺参数、采用先进轧制设备、推广新型轧制技术以及加强轧钢工艺的智能化管理等方面的节能措施,以期为我国轧钢工艺的节能提升提供理论参考和实际指导。
1.2 研究意义节能是当前我国工业发展的重要方向和热点问题之一,对于轧钢工艺的节能方向及途径探究具有重要的理论和实践意义。
节能可以有效减少能源消耗和二氧化碳排放,有利于实现经济可持续发展和环境保护。
轧钢工艺在工业生产中消耗大量的能源,通过研究轧钢工艺的节能潜力和优化工艺参数,可以有效降低能源消耗,减少环境污染。
节能还可以提高企业的竞争力和经济效益。
随着全球经济一体化的加深,企业面临着越来越激烈的竞争压力。
实施节能措施可以降低生产成本,提高生产效率,提升产品质量,增强企业的市场竞争力。
研究轧钢工艺的节能方向及途径, 可以为我国轧钢行业的发展提供技术支撑和指导。
- 1、下载文档前请自行甄别文档内容的完整性,平台不提供额外的编辑、内容补充、找答案等附加服务。
- 2、"仅部分预览"的文档,不可在线预览部分如存在完整性等问题,可反馈申请退款(可完整预览的文档不适用该条件!)。
- 3、如文档侵犯您的权益,请联系客服反馈,我们会尽快为您处理(人工客服工作时间:9:00-18:30)。
关于单机架冷轧节能降耗技术探讨
发表时间:2018-10-01T12:38:06.100Z 来源:《基层建设》2018年第24期作者:吴义朝[导读] 摘要:为了提升冷轧企业的经济效益,增加企业的市场竞争力,相关人员对于单机架冷轧机组的节能降耗工作更加关注。
广东省中山市中山中粤马口铁工业有限公司 528437
摘要:为了提升冷轧企业的经济效益,增加企业的市场竞争力,相关人员对于单机架冷轧机组的节能降耗工作更加关注。
基于此,本文分析了单机架冷轧机组的主要消耗指标,阐述了优化单机架冷轧机组的参数、选择合适的电机、优化轧制规程、轧辊结构的优化设计、轧辊的润滑与冷却这些单机架冷轧机组节能降耗的策略。
关键词:单机架冷轧;节能降耗技术;参数优化
引言:目前,我国的钢铁行业处于发展的困境中,产能过剩、效益下降等都是这一阶段中存在的问题,冷轧行业也不例外。
为了摆脱目前的发展困境,实现更好的发展,除了要进行市场的开拓以及创新产品的开发之外,还要降低生产运行的成本,提升产品的利润。
节能降耗就是一种有效降低单机架冷轧机组生产运行成本的措施,受到了相关人员的重点关注。
本文就单机架冷轧机组的主要消耗指标进行了分析,并提出了针对性的节能降耗措施,为相关人员提供参考。
一、单机架冷轧机组的主要消耗指标分析
在冷轧机组实际的生产运行中,主要的成本来源与两个部分:第一,固定生产成本,这其中最主要的项目为冷轧机组的折旧费用,通过确定项目的建设成本以及折旧年限,就能够完成固定生产成本的稳定。
第二,可变生产成本。
这一项成本中主要有人力资源费用和冷轧机组的消耗。
其中,冷轧机组的消耗包含的项目较多,例如电能的消耗、水资源的消耗、轧辊的消耗、轧制油以及空气压缩机的消耗等等。
而在这些费用中,有85%的消耗来自于电能的消耗、轧辊运行的消耗[1]。
所以,对以上项目的消耗指标进行优化和降低,就能够显著的降低单机架冷轧机组的成本费用。
单机架冷轧机组的电能消耗主要受到机组的参数、主电机的参数、轧制规程以及电气配置的影响;轧辊的消耗主要受到辊系设计、轧辊的特性、润滑冷却、轧制规程、操作维护的影响;轧制油的消耗主要受到乳化液系统的设计与应用、乳化液喷射梁的设计以及吹扫装置设计的影响;压缩空气的消耗主要受到吹扫装置的影响;齿轮油的消耗主要受到润滑系统设计的影响。
结合这些主要的能源消耗项目的分析,有针对性的进行使用能源的优化,能够完成对单机架冷轧机组的节能降耗工作。
二、单机架冷轧机组的节能降耗措施探讨
(一)单机架冷轧机组的电耗降低
电能的消耗可以说是单机架冷轧机组运行中耗能最多的项目,在单机架冷轧机组的整体运行费用中占据了60%及以上[2]。
在进行电能消耗的优化中,可以通过对无功补偿装置的合理配置,实现单机架冷轧机组功率因数的提升,使得无功的消耗降低。
依照上文中分析的影响单机架冷轧机组电能消耗的因素,可以提出以下三种优化方式:第一,优化单机架冷轧机组的参数。
例如,单机架冷轧机组在1000m/min以及1200m/min时都实现实际的生产需要,那么就需要进行计算及对比,选择更加合适的运行速度。
笔者经过实际的计算发现,当单机架冷轧机组的运行速度在100m/min时,产能的与功率的增加相对平衡;而当其速度在1200m/min时,功率增加的过高,增加了电能的消耗。
第二,选择合适的电机。
笔者经过调查比较发现,相比于直流传动电机,交流传动的电机功能性对较好,有着维修简单以及传动性能较好的优势,且在实际的运行中能够降低15%的电能消耗。
第三,轧制规程的优化。
笔者在优化实验中,对工作辊线的速度进行了调整,使其保持在413m/min,优化后有两组的轧制的出口厚度由原有的1.2mm、0.73mm转变为1.22mm、0.74mm;压下量由0.80mm、0.47mm转变至0.78mm、0.48mm;压下率由40%、39.2%转变至39%和39.9%;其余三组的出口厚度、压下量、压下率以及速度均没有发生改变。
通过轧制规程的优化,能够实现轧制速度与功率的合理分配,减少了无功损耗、控制了电能的消耗。
(二)单机架冷轧机组中轧辊消耗的降低
在单机架冷轧机组的生产运行中,轧辊的消耗费用可以说的仅次于电能消耗的费用。
通常情况下,轧辊的消耗的费用在单机架冷轧机组的整体消耗费用中占到15%-20%,相关人员必须进行重点的控制。
轧辊的消耗除了与轧辊的设计等这些质量因素有关之外,与轧辊的使用制度也有一定的关系。
结合上文的影响因素分析,能够提出以下两点优化的策略:第一,优化轧辊的结构设计。
利用A表示轧辊的直径,利用L1、L2以及量L3分别表示轧辊辊身的长度距离、直径稍小的中心距离两侧的距离以及两侧的辊劲长。
笔者在实践中发现,在确保轧辊的强度满足轧制力矩的条件下,对直径A进行适当的减小,能够降低轧辊的综合消耗。
一般来说,经过这样的优化设计,能够将轧辊的消耗降低6%。
在确保轧辊能够正常运行的条件下,对L1、L2以及L3进行设计值的适当缩小,同样能够达到降低轧辊总体消耗的作用。
笔者将L1为120mm-150mm的轧辊辊身缩小至100mm-80mm,并进行了能耗的检测,发现这样的方式能够将轧辊的总消耗降低2%。
第二,轧辊的润滑与冷却。
单机架冷轧机组在运行时,乳化液会单侧喷出,这样的方式对轧辊的润滑与冷却效果较差,十分容易造成爆辊、烧辊的情况发生,增加了轧辊运行的能耗。
所以,要对乳化液的喷射系统进行优化,确保其能有效对轧辊进行润滑与冷却。
在轧辊以及乳化液喷射系统的运行中,要对稳定指数ESI、乳化液的浓度、PH值、皂化值等进行监控,确保乳化液的功能的得到最大程度的发挥。
总结:综上所述,对单机架冷轧机组进行节能优化是冷轧行业发展的必经之路。
在单机架冷轧机组的运行中,电能的消耗以及轧辊运行的消耗是最主要的费用以及能源消耗来源。
通过优化单机架冷轧机组的参数、选择合适的电机、优化轧制规程,有效降低了单机架冷轧机组的电能消耗;利用轧辊结构的优化设计、轧辊的润滑与冷却,降低了轧辊运行的能源消耗,使得冷轧企业获得了更大的经济效益,获得了更好的发展。
参考文献:
[1]江东海,尹海元.单机架冷轧节能降耗技术探讨[J].冶金设备,2015(01):47-50.
[2]李阳.单机架可逆冷轧机设定优化研究[D].东北大学,2012.。