尿素合成塔主要零部件的制造工艺流程设计-
16MnR钢制尿素合成塔的焊接工艺设计
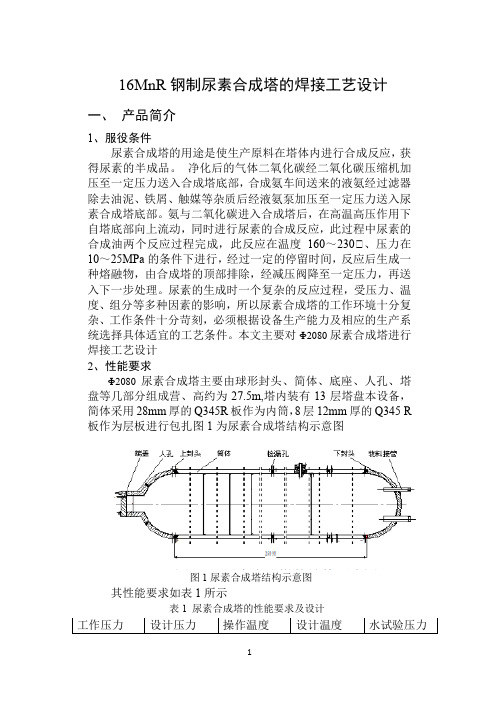
16MnR钢制尿素合成塔的焊接工艺设计一、产品简介1、服役条件尿素合成塔的用途是使生产原料在塔体内进行合成反应,获得尿素的半成品。
净化后的气体二氧化碳经二氧化碳压缩机加压至一定压力送入合成塔底部,合成氨车间送来的液氨经过滤器除去油泥、铁屑、触媒等杂质后经液氨泵加压至一定压力送入尿素合成塔底部。
氨与二氧化碳进入合成塔后,在高温高压作用下自塔底部向上流动,同时进行尿素的合成反应,此过程中尿素的合成油两个反应过程完成,此反应在温度160~230℃、压力在10~25MPa的条件下进行,经过一定的停留时间,反应后生成一种熔融物,由合成塔的顶部排除,经减压阀降至一定压力,再送入下一步处理。
尿素的生成时一个复杂的反应过程,受压力、温度、组分等多种因素的影响,所以尿素合成塔的工作环境十分复杂、工作条件十分苛刻,必须根据设备生产能力及相应的生产系统选择具体适宜的工艺条件。
本文主要对Φ2080尿素合成塔进行焊接工艺设计2、性能要求Φ2080尿素合成塔主要由球形封头、简体、底座、人孔、塔盘等几部分组成营、高约为27.5m,塔内装有13层塔盘本设备,简体采用28mm厚的Q345R板作为内筒,8层12mm厚的Q345 R 板作为层板进行包扎图1为尿素合成塔结构示意图图1尿素合成塔结构示意图其性能要求如表1所示表1 尿素合成塔的性能要求及设计二、制作材料分析1、成分16MnR:16MnR是普通低合金钢,是锅炉压力容器专用钢,锅炉压力容器的常用材料。
它的强度较高、塑性韧性良好。
常见交货状态为热轧或正火。
属低合金高强度钢,含Mn量较低。
性能与20G(412-540)近似,抗拉强度为(450-655)稍强,伸长率为19-21%,比20G的大于24%差。
标准来源GB6654,2010年该钢号逐渐被Q345R所取代。
其化学成分如表2所示表2 16MnR化学成分表增加,屈服点和抗拉强度升高,但塑性和冲击性降低。
由于韧性、焊接和冷成型性能要求高这类钢的含C量不超过0.20%。
尿素生产原理、工艺流程及工艺指标

尿素生产原理、工艺流程及工艺指标1.生产原理尿素是通过液氨和气体二氧化碳的合成来完成的,在合成塔D201中,氨和二氧化碳反应生成氨基甲酸铵,氨基甲酸铵脱水生成尿素和水,这个过程分两步进行。
第一步:2NH3,CO2 NH2COONH4,Q第二步:NH4COONH2 CO(NH2)2,H2O,Q第一步是放热的快速反应,第二步是微吸热反应,反应速度较慢,它是合成尿素过程中的控制反应。
1、2工艺流程:尿素装置工艺主要包括:CO2压缩和脱氢、液氨升压、合成和气提、循环、蒸发、解吸和水解以及大颗粒造粒等工序。
1、2、1 二氧化碳压缩和脱氢从合成氨装置来的CO2气体,经过CO2液滴分离器与来自空压站的工艺空气混合(空气量为二氧化碳体积4%),进入二氧化碳压缩机。
二氧化碳出压缩机三段进脱硫、脱氢反应器,脱氢反应器内装铂系催化剂,操作温度:入口?150?,出口?200?。
脱氢的目的是防止高压洗涤器可燃气体积聚发生爆炸。
在脱氢反应器中H2被氧化为H2O,脱氢后二氧化碳含氢及其它可燃气体小于50ppm,经脱硫、脱氢后,进入压缩机四段、五段压缩,最终压缩到14.7MPa(绝)进入汽提塔。
二氧化碳压缩机设有中间冷凝器和分离器,二氧化碳压缩机压缩气体设有三个回路,以适应尿素生产负荷的变化,多余的二氧化碳由放空管放空。
2 液氨升压 1、2、液氨来自合成氨装置氨库,压力为2.3 MPa(绝),温度为20?,进入液氨过滤器,经过滤后进入高压氨泵的入口,液氨流量在一定的范围内可以自调,并设有副线以备开停车及倒泵用.主管上装有流量计.液氨经高压氨泵加压到18.34 MPa(绝),高压液氨泵是电动往复式柱塞泵,并带变频调速器,可在20—110%的范围内变化,在总控室有流量记录,从这个记录来判断进入系统的氨量,以维持正常生产时的原料N/C(摩尔比)为2.05:1。
高压液氨送到高压喷射器,作为喷射物料,将高压洗涤器来的甲铵带入高压冷凝器,高压液氨泵前后管线均设有安全阀,以保证装置设备安全。
尿素合成塔筒体衬里工艺

尿素合成塔筒体衬里工艺
在尿素制备过程中,尿素合成塔是核心设备,其内部筒体的衬里工艺至关重要。
尿素合成塔筒体衬里的常见材料有不锈钢、双金属、耐腐蚀合金等。
其中不锈钢
耐腐蚀能力强,但耐高温性能不佳;双金属应用广泛,耐复合侵蚀能力强,但价格较高;耐腐蚀合金有优异的耐蚀性,但加工难度大。
尿素合成塔筒体衬里工艺通常分为以下几个步骤:首先,采用砂轮打磨清理筒体的内壁,清除锈蚀和旧的衬里层;其次,选择合适的衬里材料,预加热至适宜的温度;接着,将预加热的衬里材料压入筒体内部,然后使用专用工具进行顶压,使衬里与筒体紧密结合;最后,进行冷却并检查衬里与筒体的结合是否牢固。
需要注意的是,为保证尿素合成塔筒体衬里工艺的质量,衬里材料的选择必须综合考虑尿素合成塔的工作条件,包括温度、压力、尿素浓度等因素。
并且,安装过程中需要严格控制预热温度和顶压力度,以防止衬里层的脱落。
另外,尿素合成塔筒体衬里的使用寿命与合成塔的运行参数、材料的质量、衬里的厚度等有关。
为了延长衬里寿命,应定期对合成塔进行检查,及时发现并处理潜在的问题。
同时,应对衬里材料进行周期性的表面处理,以增强其耐腐蚀能力。
总结来说,尿素合成塔筒体衬里工艺的关键相应环节包括衬里材料的选择、清理、预热、压入、顶压、冷却及检查等。
合理的衬里工艺对于确保合成塔的正常
运行和提高尿素产品的质量具有决定性的影响。
尿素生产简图(彩色工艺流程图)

1
同一段差不多
3.
去常压吸收塔
氨水来自氨水槽
6.氨水解吸
解吸废水
去界区
中压蒸汽来自外管250℃2.4Mpa
流程说明
1、液氨加压
来自界区的液氨在取样分析后由高压泵加压到14Mpa送往高压喷射器
2、反应阶段
液氨作为喷射动力,将来自高压洗涤器的甲铵液一起带入高压甲铵冷凝器,在其中生成甲铵CO2+2NH3 ⇌NH4•COONH2反应放热,回收一部分热量让反应平衡向正反应偏移;反应后的气体跟液体直接通往合成塔底部,在合成塔(14Mpa 183℃)中生成尿素NH4•COONH2 ⇌CO (NH2)2+H2O 反应吸热,而气体CO2+2NH3 ⇌NH4•COONH2反应放热,所以合成塔中自热平衡,且合成塔中设有多层塔板,防止返混;反应生成的尿素-甲铵液体从合成塔底部取样分析后去汽提塔顶部,与下层来的高压CO2逆流接触,在高温以及CO2气体带动下,甲铵液被进一步分解,尿素及甲铵液从汽提塔底部取样分析后去往精馏塔,在精馏塔中循环加热,促进甲铵液进一步分解,出来的尿素溶液浓度大约为68%,取样分析后进入闪蒸罐(常压),闪蒸出CO2/NH3/H20,尿素溶液流进尿素贮罐。
3、尿素造粒
尿素贮罐的尿素溶液取样后打到一段蒸发加热器(0.03Mpa 13 0℃)尿素溶液中的气体水分充分分解、蒸发,出一段加热器的尿素溶液浓度大约为95%,然后流进二段蒸发加热器(0.003MPa 140℃)
. 继续加热浓缩,出来的尿素为熔融状态(99.7%),取样后送到造粒系统直接做成颗粒状,包装存储。
4、其他说明
过程中产生的气体回收利用,或者去排气筒,用过程中产生的溶液吸收后返回氨水槽,不能吸收的气体排大气。
.;。
尿素工艺流程 PPT课件

尿素生产流程有多种,最早实现工业化的方法是不循环法 和部分循环法,后来被水溶液全循环法代替,又出现各种 气提法流程。虽然方法、其实现的工艺流程和工艺条件不 同,但生产原理是相同的。主要介绍尿素生产的工艺流程、 主要设备和操作条件。
一、不循环法和部分循环法
尿素生产工业化早期实现的是不循环和部分循环流程,两 种方法在生产尿素时必定伴有大量副产物生成,此种流 程已不再采用。
5
(二)溶液全循环改良C法
1.工艺流程(见296-297页图)
日本三井东压/东洋工程全循环改良C法,是传统水溶液全 循环法的改进,生产低缩二脲含量尿素产品,也生产常规 尿素产品。
2.主要设备(尿素合成塔)
尿素合成塔操作条件:压力23-25MPa、温度190-200℃, 氨碳比4,水碳比0.37,转化率约72%,外壳应用保温材料 改良C法的尿素合成塔采用高径比为18的空塔,用钛作衬 里,耐高温腐蚀。
❖ 2.P:P降低使甲铵分解,对过量氨蒸出及吸收有利,气 ❖ 提效率提高,但为节省能耗,常选用P气提=P合成。 ❖ 3.液气比:即进入气提塔尿素液与CO2的重量比。它由
合成反应本身的加料组成确定,不可任意改变。生产中为保 证每根管子内的正常流量,防止管子造成严重腐蚀,一 般 气提塔内液气比控制在4左右。 ❖ 4.停留时间:生产上以接近1min为宜。
二、水溶液全循环法
❖(一)传统水溶液全循环法
❖(二)溶液全循环改良C法
1
(一)传统水溶液全循环法
1.工艺流程(见294页图)
2.主要设备(尿素合成塔)
合成塔工艺操作条件:压力20-22MPa、温度190-200℃,氨碳 比4-4.5,水碳比0.6-0.7,转化率约62-64%,应符合高压 容器要求,外壳应用保温材料 大中型尿素工厂采用衬里式合成塔 合成塔外筒为多层卷焊受压容器,内部衬有一层耐腐蚀的 不锈钢板,隔离尿素甲铵腐蚀介质,外壳保温,防止热量 外散。 优点:容积利用率高,耐腐蚀材料用量少,操作方便。 最早采用空塔,不设置内件,塔高径比较大。后采用高径 比小的塔,常设置混合器或筛板等内件,减少返混的影响。
尿素合成塔制造工艺

尿素合成塔制造工艺初稿中国石化集团南化公司化机厂陈建俊《压力容器制造和修理》第六章典型压力容器制造工艺中国石化集团南化公司化机厂陈建俊目录6.6尿素合成塔制造工艺6.6.1概述6.6.2尿素合成塔结构型式6.6.3投产前的技术准备和制造过程中的质量控制6.6.4制造流程图6.6.5材料验收和复验6.6.6主要零部件的制造6.6.7组合、竣工检验6.6.8油漆、包装、运输6.6.9制造记录和出厂技术文件6.6.1概述尿素作为化学肥料,由于其含氮量高(含氮46%),施用后对土壤无副作用,深受农业工作者的欢迎。
尿素除用作化肥外,还广泛用于其他工业和经过深加工作为牙膏、医药、塑料的原料,并可直接掺和在牛羊等反刍动物的饲料中,促进动物长膘。
因此尿素工业自实现工业化后,发展很快,尿素的生产也一直成为工业化国家化肥生产水平的重要标志,我国自二十世纪六十年代开始生产尿素,目前也成为世界尿素生产的大国,生产能力居世界首位,但由于我国人口众多,粮食需求量也是世界首位,尿素总需求量仍然满足不了要求。
由于原料原因,我国的尿素成本比国外高、缺乏竞争力,老装置的改造和新建的尿素生产装置采用高效生产流程和新型设备是今后发展的方向。
尿素合成塔是尿素生产装置中的关键设备之一,它在尿素生产流程中占有重要的地位。
典型的尿素生产流程见图一。
可以说尿素工业的发展与尿素合成塔的设计制造技术的发展是紧密相连的。
根据尿素合成反应式:2NH3+CO2NH4COONH2NH2CONH2+H2O(氨基甲酸铵)(尿素)这些介质的混合物在一定温度和压力下,会生成氰酸和氰氧铵。
CO(NH2)2NH3+HCNO NH4CNO(氰酸)(氰氧铵)氰酸和氰氧铵是一种非氧化性有机酸。
氰氧离子(CNO-)对不锈钢的氧化膜强烈的破坏作用,使一般的不锈钢在尿素介质中失去了耐蚀能力。
据有关资料介绍,1Cr18Ni9Ti这种材料在尿素合成反应条件下,年腐蚀率为3mm,而更可怕的是产生选择性局部腐蚀,不等钢材全面腐蚀变薄就在某一局部甚至某一肉眼无法看到的一点腐蚀穿透导致设备泄漏而失效。
化肥厂尿素装置生产原理及工艺流程
化肥厂尿素装置生产原理及工艺流程一、引言化肥厂尿素装置是化肥生产过程中的重要设备,用于生产尿素肥料。
本文将介绍尿素装置的生产原理和工艺流程。
二、尿素的生产原理尿素是一种氮肥,具有高氮含量、溶解性好等特点,被广泛应用于农业生产中。
尿素的生产原理主要包括合成部分和后处理部分。
2.1 合成部分尿素的合成是通过将氨气和二氧化碳在一定条件下反应得到的。
具体的反应方程式如下:2NH3 + CO2 -> NH2CONH2 + H2O上述反应是在一定压力和温度下进行的。
通常情况下,尿素的合成压力为100至180巴,温度为130至160摄氏度。
2.2 后处理部分尿素合成反应得到的产物中还包含着一些杂质,需要经过后处理步骤进行处理。
后处理主要包括脱水和浓缩两个步骤。
脱水是指将产物中的水分去除,以提高尿素肥料的含氮量和稳定性。
浓缩则是将产物浓缩,以便进行后续的干燥和颗粒化处理。
三、尿素装置的工艺流程尿素装置的工艺流程主要包括原料准备、合成反应、脱水、浓缩、干燥和颗粒化等步骤。
3.1 原料准备尿素的主要原料为氨气和二氧化碳。
氨气一般通过蒸发液氨或氨气合成装置进行提供,而二氧化碳可通过燃煤锅炉烟气或气化炉烟气提供。
3.2 合成反应合成反应是将氨气和二氧化碳在合成反应器中进行反应。
反应器内通常采用催化剂来加速反应速率,保证反应的高效进行。
3.3 脱水合成反应后得到的产物中含有一定的水分,在脱水塔中通过高温条件蒸发除去水分,以提高尿素肥料的纯度。
3.4 浓缩脱水后的产物含有浓度较低的尿素,为了提高尿素的浓度,需要经过浓缩塔进行浓缩处理。
3.5 干燥浓缩后的产物通过干燥器进行干燥,以去除水分和其他杂质。
干燥后的尿素颗粒具有较高的纯度和稳定性。
3.6 颗粒化干燥后的尿素通过颗粒化机进行颗粒化处理,使其形成均匀的粒状,便于储存和施用。
四、总结尿素装置是化肥厂生产尿素肥料的重要设备,其生产原理主要包括合成和后处理两个部分。
工艺流程包括原料准备、合成反应、脱水、浓缩、干燥和颗粒化等步骤。
尿素合成塔主要零部件的制造工艺流程设计_图文(精)
主要零部件的制造㈠筒体的制造如前所述,筒体是整个尿素合成塔的主要部分。
筒体由许多筒节组焊成,就拿φ2.8m×36m尿素合成塔(多层包扎式)为例,筒体共分11节,其中10节长2980mm,1个筒节1800mm,总长度31600mm。
每一个筒节都是由外层层板、盲层和衬里内筒组成,它们的制造工艺过程简要叙述如下:1)内筒内筒的制造工艺过程是:⑴原料检验(包括腐蚀试验和机械性能试验)→⑵按内筒展开周长划线、留有切割量和卷圆带头直边量→⑶标志移植。
将材料牌号、炉批号、板号或其本厂代号,用不含氯离子或金属养料的记号笔(可防水而不褪色)抄写到将要下料的板面上→⑷剪切下料→⑸在卷板机上卷圆,当两头弯曲圆度达到要求后取下。
注意:卷板机应专用,上辊不能有焊渣、焊瘤,最好在上辊套一不锈钢套筒。
避免衬里内筒卷制过程中压出麻点或划伤以及铁离子污染。
→⑹在专用的夹具上切除两端直边余料并刨出纵焊缝坡口→⑺纵向焊缝坡口表面着色探伤。
不得有裂纹或夹层现象。
→⑻重新放在卷板机上进一步卷圆,使纵缝合拢→⑼在卷板机上将纵缝点焊固定。
应采用评定合格的焊条,注意不能将焊渣掉到上辊表面。
→⑽从卷板机上取下,由于筒体直径较大,厚度(一般6~8mm)较薄,刚度不足,容易变形,因此内筒必须用支撑件撑圆固定。
→⑾将筒体放在专用的夹具上进行纵焊缝焊接(带焊接试板)→⑿焊缝铁素体测定。
要求每一根焊条焊接长度上测一点(铁素体≤0.6%)以防止用错了焊条或偏离焊接规范。
→⒀焊缝表面着色探伤,不得有夹渣、裂纹和气孔→⒁纵焊缝X光探伤检查。
由于衬里的内筒主要是起耐腐蚀作用,焊缝是薄弱环节,微小的孔洞将造成严重的危害。
因此X光探伤的验收标准不同于一般受压容器的标准。
除按JB4730的I级片外,还不允许有柱状小气孔出现。
→⒂焊接试板的晶间腐蚀倾向试验和选择性腐蚀检查及金相检查。
其方法按HG/T3172和HG/T3173、HG/T3174验收标准按GB9842或工程标准的规定。
尿素生产工艺设计
第一章 尿素生产概述1.1尿素生产的原理尿素的合成原料是氨和二氧化碳,这两种原料均来自合成氨装置。
尿素合成的条件为:188℃,15.6MPa ,进料氨和二氧化碳的物质的量比是3.6,水和二氧化碳的物质的量比是0.67[2]。
一般认为在合成塔尿素的反应分以下两部进行 第一步,氨基甲酸铵的生成。
反应式为:324212()()()NH l CO g NH COONH l Q ++其次步,氨基甲酸铵脱水。
反应式为:422222()()()()NH COONH l CO NH l H O l Q +-1.2尿素生产的方法由于这两个反应都是可逆反应,因此氨和二氧化碳不行能全部转化为尿素。
在工业生产条件下,二氧化碳转化率仅在50%-70%之间[3]。
为了分别和回收未反应的氨和二氧化碳,可将合成熔融物加热分解,使气体逸出。
但要将逸出的氨和二氧化碳全部或部分返回合成塔重新合成尿素,这就出现了各种不同的流程。
有循环法,半循环法和全循环法。
全循环法又可以分为热气全循环法、矿物油全循环法、气体分别全循环法、水溶液全循环法及汽提全循环法。
气提全循环法又可以分为二氧化碳汽提法、氨汽提法和双汽提法。
其次章 斯那姆氨汽提工艺2.1工艺基本原理汽提是使尿液中的甲铵按下述反应分解为3NH 和2CO 的过程:4232()2()()NH COONH l NH g CO g Q +-这是一个可逆体积增大的反应[4]。
我们只要能够供应热量,降低压力或降低气相中3NH 和2CO 某一组分的分压都可使反应向右方进行,以达到分解甲铵的目的。
汽提法是在保持压力和合成塔相同的条件下,在给热量的同时接受降低气相中3NH 和2CO 某一组分的过程。
当温度为T ℃时,纯态甲铵的离解压力和各组分(3NH 和2CO )的分压的关系按以上化学方程式可作如下表示:设总压力为P s 则从反应式中可以看到氨分压为2/3P s 二氧化碳分压为1/3P s 如反应式在温度为t ℃时的平衡常数为K t ,则:23(2/3)(1/3)4/27t s s s K P P P ==假如氨和二氧化碳之比不是按2:1状态存在,在温度仍为t ℃时,它的总压力为P ,其各组分的分压为:3NH 的分压33NH NH P X =⨯⨯总压氨的分子数=P2CO 的分压232CO NH P X =⨯⨯总压二氧化碳的分子数P3NH X 和2CO X 分别为气体中氨,二氧化碳的分子分数这样反应式在温度为t ℃时平衡常数应为:3232232()()NH CO NH CO Kt P X P X P X X =⋅⋅⋅=⋅⋅ 温度相同,平衡常数应相等,所以当温度为t ℃323334/27NH CO Ps P X X =⋅⋅ ⇒但纯甲胺在某一固定温度下离解力为不变的常数C ,所以从今式可以看出,当趋近于1时,则3NH X 必趋近于0,就趋近于0,则2CO X 趋近于无限大,就是说当甲铵液用二氧化碳气体通入,气相中几乎全为二氧化碳时(2CO X =1)P 趋于无限大,即甲铵的离解压力近于无限大,我们知道假如甲铵在某温度下的离解压力大和操作压力,甲铵就会得到分解,现分解压力为无限大,大于固定操作压力,所以液相中甲铵就进行分解,这就是二氧化碳气提法分解甲铵的理论基础[5]。
尿素合成塔球形封头具体制造工艺流程设计和检测设计
八.尿素合成塔封头制造详细工艺流程(包括检测)●下部半球形封头制造过程:原材料检验→喷砂→UT检测→标准移植→气割下料→刨削拼接坡口→预组合并在大型立车上夹紧→车削外圆边缘坡度→在龙门刨床上精加工拼接焊缝坡口→组对焊接(组对时在特制的装有预热装置的场地上进行)预热温度200℃±30℃→检验,包括焊缝的PT,RT检测以及焊缝及热影响区的硬度试验→加热→冲压→测定成形后球壳各部位实际厚度→焊缝及热影响区内外表面MT→整个球面进行UT→正火+回火(带焊接试板)→试板力学性能试验→精加工环向端面→球壳内壁用砂轮打磨光滑呈金属光泽→清洗内表面→在专用的焊接变位器上夹紧,找正→在球壳外壁安装远红外电加热及保温层→通电预热,使球壳温度≥100℃→进行第一层(过渡层)带极板堆焊和球底中心部位的焊条、电弧堆焊→打磨焊接接头部分→堆焊层表面PT(抽查30﹪面积)→UT检测(也抽查30﹪,以焊带搭接处为主)→消除应力热处理→表面清洗,不得有油污等影响继续堆焊质量的杂物→堆焊第二层(耐蚀层)不锈钢(包括焊条电弧堆焊)→铁素体测定100﹪PT→100﹪UT→测量堆焊层厚度→加工环向焊接坡口→镗制底部和侧面物料接管焊接坡口→所有坡口的碳钢部分进行MT→清洗坡口表面(用酒精擦洗除去油污)→组对接管→球壳接管周围适当预热→焊接→焊接铁素体测定→焊缝表面PT→与筒体组对焊接●上封头球壳的制造工艺过程在球壳冲压成形部分与下封头相同,以后工序如下:上封头球壳冲压成形并经正火+回火处理,力学性能试验合格后→在立车上加工人孔开孔与人孔法兰的焊接坡口→检验坡口合格后→与人孔法兰锻件组对→点焊固定(预热)→预热(≥150℃)焊接→UT、MT→硬度检查→直线加速器RT 检测(有条件厂家)→组对两个吊耳→局部预热≥150℃→焊接吊耳→焊满后表面打磨→MT、UT→消除应力热处理→UT、MT→硬度检查→球壳内壁打磨光滑呈金属光泽→清洗干净→堆焊不锈钢(堆焊程序与下封头相同)→堆焊人孔衬里过渡层→精加工人孔内圆及人孔密封面镶环槽→组对人孔内圆衬里和密封底镶环→焊接→焊接铁素体检查→焊接表面PT→精加工人孔密封面→螺栓孔加工→检验九.封头成形后热处理及其检测热处理奥氏体不锈钢封头在冷压后不需要进行热处理,但在热压后一定要进行热处理。
- 1、下载文档前请自行甄别文档内容的完整性,平台不提供额外的编辑、内容补充、找答案等附加服务。
- 2、"仅部分预览"的文档,不可在线预览部分如存在完整性等问题,可反馈申请退款(可完整预览的文档不适用该条件!)。
- 3、如文档侵犯您的权益,请联系客服反馈,我们会尽快为您处理(人工客服工作时间:9:00-18:30)。
主要零部件的制造㈠筒体的制造如前所述,筒体是整个尿素合成塔的主要部分。
筒体由许多筒节组焊成,就拿φ2.8m×36m尿素合成塔(多层包扎式)为例,筒体共分11节,其中10节长2980mm,1个筒节1800mm,总长度31600mm。
每一个筒节都是由外层层板、盲层和衬里内筒组成,它们的制造工艺过程简要叙述如下:1)内筒内筒的制造工艺过程是:⑴原料检验(包括腐蚀试验和机械性能试验)→⑵按内筒展开周长划线、留有切割量和卷圆带头直边量→⑶标志移植。
将材料牌号、炉批号、板号或其本厂代号,用不含氯离子或金属养料的记号笔(可防水而不褪色)抄写到将要下料的板面上→⑷剪切下料→⑸在卷板机上卷圆,当两头弯曲圆度达到要求后取下。
注意:卷板机应专用,上辊不能有焊渣、焊瘤,最好在上辊套一不锈钢套筒。
避免衬里内筒卷制过程中压出麻点或划伤以及铁离子污染。
→⑹在专用的夹具上切除两端直边余料并刨出纵焊缝坡口→⑺纵向焊缝坡口表面着色探伤。
不得有裂纹或夹层现象。
→⑻重新放在卷板机上进一步卷圆,使纵缝合拢→⑼在卷板机上将纵缝点焊固定。
应采用评定合格的焊条,注意不能将焊渣掉到上辊表面。
→⑽从卷板机上取下,由于筒体直径较大,厚度(一般6~8mm)较薄,刚度不足,容易变形,因此内筒必须用支撑件撑圆固定。
→⑾将筒体放在专用的夹具上进行纵焊缝焊接(带焊接试板)→⑿焊缝铁素体测定。
要求每一根焊条焊接长度上测一点(铁素体≤0.6%)以防止用错了焊条或偏离焊接规范。
→⒀焊缝表面着色探伤,不得有夹渣、裂纹和气孔→⒁纵焊缝X光探伤检查。
由于衬里的内筒主要是起耐腐蚀作用,焊缝是薄弱环节,微小的孔洞将造成严重的危害。
因此X光探伤的验收标准不同于一般受压容器的标准。
除按JB4730的I级片外,还不允许有柱状小气孔出现。
→⒂焊接试板的晶间腐蚀倾向试验和选择性腐蚀检查及金相检查。
其方法按HG/T3172和HG/T3173、HG/T3174验收标准按GB9842或工程标准的规定。
超低碳奥氏体不锈钢的制作,要求有一个清洁的场地和环境,避免铁素体污染和磕碰划伤,否则会影响不锈钢的耐蚀性能。
因此,参加尿素合成塔内筒衬里或其他内件制造的工人要接受这方面工艺守则的教育,并在施工过程中严格遵守;下料场地应打扫干净,消除杂物,可采用橡胶板铺地,并禁止穿带有铁钉子的皮鞋,撬具、吊耳也应采用奥氏体不锈钢制作。
卷制内筒时必须在专用的卷板机上进行。
不能与卷过铁素体钢的卷板机混合使用,除非将卷过碳钢的卷板机辊子表面进行认真的清洗。
当超低碳奥氏体不锈钢冷变形超过20%,应进行提高耐蚀性能的固溶热处理。
热处理炉内的气体应尽量减少硫的含量,防止硫化物对不锈钢的渗透降低耐蚀性能。
当不锈钢表面或焊缝需要打磨时,应采用含有橡胶氧化铝的砂轮打磨,打磨时间不应太长,避免造成回火色。
不能用普通粉笔当作记号笔在不锈钢上乱写乱画。
标记移植用记号笔应采用不含氯离子、硫化物的颜料。
内筒的纵焊缝焊接坡口型式见图九。
焊接程序如下:图九清理坡口→手工焊①和②两道,焊条BM310Mo-Lφ3.5mm,电流90~100A→焊缝表面PT→清理→手工焊③和④道,焊条直径φ4mm,电流120~140A→PT→清理→手工焊⑤道,焊条直径φ4mm→打磨焊道①,磨去焊根及两侧热影响区各2.5mm→手工焊⑥,焊条直径φ3.25mm,电流90~100A→铁素体检查⑤、⑥的表面→PT⑤、⑥焊缝表面→X光探伤。
在焊接前,焊条应烘烤150~200℃2小时,焊接层间温度应控制在<150℃,母材不必预热。
为了尽可能消除焊缝中的气孔、夹渣等小缺陷,进行二次以上的PT是必要的,因为焊一层的厚度一般只有2mm,那么焊一层,PT一次,就可以把缺陷的尺寸限制在小于2mm的范围之内,尤其是可以消除穿透性的小气孔。
但是着色探伤液必须清理干净,否则对焊接不利。
一般来讲,最后一道焊缝表面由于冷却条件好,没有受到再次加热的影响,其耐蚀性能最佳,所以不要轻易打磨。
如果表面成形不好,着色探伤或X光探伤需要打磨或修补,应掌握好打磨和修补工艺,防止焊缝过热。
2)盲层板盲层板主要起保护不锈钢内筒的作用,它只要求可焊性,对机械性能可不予考虑。
一般采用16Mn,它在制造上的特点是在盲层板面向衬里内筒外壁的一面(即盲层板内表面)要加工出纵向和环向槽若干条,槽的深度为2.5mm,宽5~6mm,如图十所示。
盲层板是在平板状态时开槽,要在专用的工装上进行。
纵向槽深度应适当控制,过深了,在盲层板卷制成圆后会有棱角出现,不利于将来的层板包扎。
图十盲层板结构示意图3)外壳层板外壳层板是受压壳体的主要材料,它的制造过程与一般高压容器多层层板的制造过程一样。
对于大型尿素合成塔,为了减轻重量方便运输,要求层板采用低合金高强度钢层板如日本神户制钢的K-TEN62M,美国ASME的SA724A.B,我国的15MnVR、15MnVNR等,其厚度可采用8~12mm。
由于K-TEN62M等材料抗拉强度和屈服强度较高,在压头时需进行模拟试验,根据实际的回弹量来确定压模的半径。
层板的制作过程如下:材料检验→第一层层板进行超声波探伤检查(其它各层可不必进行超声波探伤)→划线→标志移植→气割下料→两头预压弯→卷圆(瓦片状)→切割坡口尺寸→坡口表面磁粉探伤或着色探伤→(第二层层板钻泄气孔)→包扎和焊接。
层板材料是主要的受压元件,也要按DIN50049合格证书3.1C进行验收。
第一层层板相当于多层高压容器的内筒,所以增加了超声波检查。
4)多层筒节包扎图十一多层筒节包扎是在一台专门设计的包扎机上进行的(见图十一照片)该包扎机包扎的容器外径可达φ4000mm。
有两个活塞直径为φ150mm的液压缸,4根φ30mm的拉紧钢丝绳。
总的拉力最大可达78吨。
包扎时将装配好内衬胎的内筒支承在可以转动的主轴上,压力缸和拉紧架均可沿平行于筒体作轴向移动。
先拉紧层板的中间部位,然后拉紧两端,分三次即可完成包扎拉紧工作。
每拉紧一次就将纵缝点焊起来,防止移动后松开,包扎完一层以后,将筒节吊出置于滚轮架上进行纵焊缝的焊接。
小型的多层筒节包扎拉紧架有拉紧架固定式和拉紧架移动式(卡钳式),其中拉紧架移动式(卡钳式)也可以用于层板环缝错开整体包扎用,使整台多层式高压容器在专用支架上包扎完成,消除了深厚的环焊缝,已在其他高压容器上得到应用,可大大提高层板材料利用率,降低多层高压容器的制造成本。
但由于尿素合成塔结构的特殊性,这种方法还未得到应用。
因此本文不再详细叙述。
尿素合成塔筒节的制作过程如下:衬里内筒装配衬胎→装配并包扎盲层板纵缝间断焊→装配包扎第一层层板→纵缝焊接→铣磨焊缝余高→MT、UT、硬度检查→装配包扎第二层、第三层……层板→每包扎一层铣磨焊缝余高→MT、UT、(根据材料强度值)→装配最后一层层板→包扎→焊接→焊缝和热影响区硬度检查→MT、UT→筒节端面坡口加工→钻泄气孔和镗检漏孔坡口→端面堆焊封口→堆焊塞焊检漏孔→交组对。
盲板层的间断焊采用手工焊,焊接长度见图十二。
在靠近筒节的两端部用E5015、J507)焊条,第一道用φ2.5mm,电流50~60A,第二层焊条直径φ3.25mm,电流100~120A。
焊后将焊缝外表面打磨,略显凹陷为宜。
在焊接时要注意,不要在盲层板内壁开有检漏槽的部位进行焊接,以防堵死检漏通道。
图十二盲层板纵缝间断焊示意图层板纵焊缝坡口见图十三。
层板纵焊缝焊接先手工焊①后自动焊②。
对于图十三层板纵焊缝坡口K-TEN62M层板,焊条用LB62,直径φ5mm,电流180~240A,自动埋弧焊焊丝US40+焊剂MF38,焊丝直径φ4.8mm,电流600~650A。
第一层层板和最后一层层板纵焊缝进行硬度检查的目的是考核焊工对焊接工艺是否严格执行。
要求硬度值≤280HB。
筒节端部坡口堆焊的目的是防止在组合后环缝焊接时层板在焊接热的影响下出现张口,使焊渣流进去,影响焊缝的质量。
如图十四所示。
在端部堆焊时应注意内筒与盲层板之间的间隙属于异种钢焊接,应采用奥氏体钢25-22-2LPWN焊丝COOCr25Ni22Mo(M.N.氩弧焊封焊,而其他部分用US40XMF38自动埋弧焊。
图十四筒节端部堆焊示意图]5)筒节与筒节的组对焊接筒节与筒节之间组对以后进行环焊缝焊接,环焊缝结构如图十五所示。
组对是在大型滚轮架上进行的。
组对时必须检查环焊缝对口间隙,控制在2±0.5mm范围内。
同时应特别注意内口的错边量。
因为内筒是耐腐蚀不锈钢,错边量大了就会影响环焊缝的耐蚀层厚度。
一般应控制在3mm以下。
由于筒节外壁上的检漏孔已预先镗制完成,要保证所有筒节上的检漏孔沿筒身在一条直线上,就不允许筒节任意转动,这给组对工作带来一定的困难。
而调节里口错边量达到最小是不容易的。
所以筒节的制作必须预先控制好椭圆度,使椭圆度(大小直径差)达到最小。
采取严格控制内筒的下料尺寸,包扎层板前装配刚度较好的衬胎等措施使所有筒节的最大内径与最小内径之差控制在4mm以内是能做到的。
特别是对多筒节的尿素合成塔壳体,在组对之前,将每个筒节的实际内径进行分类,按最佳组合对象进行组对,可以大大降低里口错边量。
本例的尿素合成塔内口实测错边量见图十六。
图十六筒体组对环缝示意图及内口错边量测定值环焊缝的焊接程序是:(见图十五a,b)清理坡口上的油污和水迹、铁锈等→氩弧焊封底,焊丝TGS-Mφ2.4mm,电流140~160A→目测检查,不能有裂纹→预热100~150℃→手工焊②道至30mm。
焊条LB62,φ4mm,电流140~160A,用风镐敲击焊道消除应力→冷却后进行X光射线探伤→重新预热到100~150℃→手工焊至44 mm→停止预热→内壁手工焊③④道。
焊条BM310Mo-L,φ3.25mm,电流90~110A,φ4mm,电流130~145A→焊满后进行铁素体测定,要求铁素体含量≤0.6%→PT,表面不得有裂纹,特别是收弧处要注意认真检查,弧坑处要进行打磨→X光射线探伤检查。
要求整个焊缝(60mm厚)达到JB4730II级片标准→预热100~150℃→埋弧自动焊⑤道,焊丝US40加焊剂MF38,焊丝直径φ4.8mm,电流550~650A,速度7~9mm/秒→外口焊满后对焊缝表面和热影响区进行MT→硬度测定,要求焊缝及两侧热影响区的硬度≤HB280→直线加速器射线探伤(有条件的厂家)。
㈡半球形封头的制造中、小型尿素合成塔的上下半球形封头均采用厚板在水压机上整体冲压成形,这在国内的多数制造厂均能做到。
而大型尿素合成塔的上下半球形封头(内径φ2800mm左右),整体冲压成形只有少数几个厂家才能做到,其关键条件是必须要有大吨位、大开档、大行程的大型冲压水压机和相应的工装模具、高温加热炉以及合理的冲压工艺。
以直径φ2800mm,厚度为125mm的尿素合成塔半球形封头整体冲压成形为例。