2010第六章 挤出成型机
挤出成型—挤出设备(高分子成型课件)

④螺纹升角θ:物料形状:A细粉30º B粒状15º C球状、柱状17º。螺 纹升角θ 一般取17º41′(易加工,对产量影响不大)。 ⑤螺纹宽度:0.08~0.12D,截面通常为梯形,靠近螺槽底部较宽,其根部 应用圆弧过渡。
2 挤出系统——是最主要的系统,它由料筒、螺杆、多孔板和过滤网组成。 (4)过滤装置
多孔板和过滤网设置:机筒和机头连接处,多孔板支撑过滤网(2~3层的 铜丝网或不锈钢丝网)。 作用:物料离开计量段时,避免有杂质未熔冷料进入机头口模,并减少螺 杆带来的旋转作用。 (5)机头与口模 ü机头:口模与料筒之间的过渡部分。其作用为使物料由挤出时旋转运动 →直线运动,并产生成型压力,保证制件密实使物料进一步均匀塑化,均 匀平稳导入口模。 ü口模:具有一定截面形状的通道,使熔体从口模中流出时获得所需形状 ,是用螺栓/其它方法固定在机头上。 ü机头还设有校正和调整装置(定位螺钉),能调整和校正模芯与口模的 同心度、尺寸和外形。
2 按螺杆转速分: 普通(100r/min)、高速(300r/min)超高速(300-1500r/min)三种挤出机
一、挤出机的分类和组成
(一) 挤出机分类
3 按按螺杆数目分: 单螺杆挤出机、双螺杆挤出机和多螺杆挤出机(如三 螺杆、四螺杆、五螺杆、…等) 4 按照可否排气: 非排气型挤出机(目前普遍)和排气型挤出机 5 按装配结构分: 整体式和分开式挤出机
二、挤出机组的辅机设备
1 辅机设备 定形装置、冷却装置、牵引装置、切割装置和卷取装置
2 辅机设备型号的表示
辅机型号:主机和辅机是匹配使用的。 一般在主机型号的第 三项后加“F”,然后在加设备汉字的第一个拼音字母表示, 最后是 辅机型号的主参数。
挤出成型机的主要结构

挤出成型机的主要结构
挤出成型机是一种常见的塑料加工设备,它的主要结构包括以下几个部分:进料系统、螺杆和筒体、加热和冷却系统、模具以及控制系统。
进料系统是挤出成型机的开始部分,它负责将塑料原料输送到螺杆。
进料系统通常包括一个料斗,用于存放和提供塑料颗粒。
通过重力或辅助装置,塑料颗粒从料斗中进入挤出机的喂料区域。
螺杆和筒体是挤出成型机的核心组成部分。
螺杆由一个或多个螺旋线构成,它的作用是将塑料颗粒从进料区域推送到出料区域。
筒体是螺杆的包围壳体,通常由加热和冷却系统控制温度。
当塑料颗粒被螺杆推送时,它们在螺杆和筒体间受到高温和高压的作用,从而熔化和塑形。
加热和冷却系统起着至关重要的作用。
加热系统通过加热螺杆和筒体中的加热器,使塑料颗粒熔化。
冷却系统则通过冷却水循环来控制螺杆和筒体的温度,使塑料在适当的温度下凝固和固化。
模具是挤出成型机的出料部分,它决定了最终制品的形状和尺寸。
模具通常由金属制成,具有一定的孔隙结构。
熔化的塑料通过模具的孔隙流过,并在出料端形成所需的形状。
模具的设计和制造对于生产高质量塑料制品至关重要。
控制系统是挤出成型机的智能化部分,它用于监控和控制整个挤出过程。
通过控制系统,操作人员可以调节螺杆的转速、温度和压力,以实现对制品质量的精确控制。
控制系统还可以自动识别和排除故障,提高生产效率和产品质量。
综上所述,挤出成型机的主要结构包括进料系统、螺杆和筒体、加热和冷却系统、模具以及控制系统。
这些部分的协调工作使得挤出成型机能够高效地将塑料原料加工成各种形状的塑料制品。
挤出成型机概述
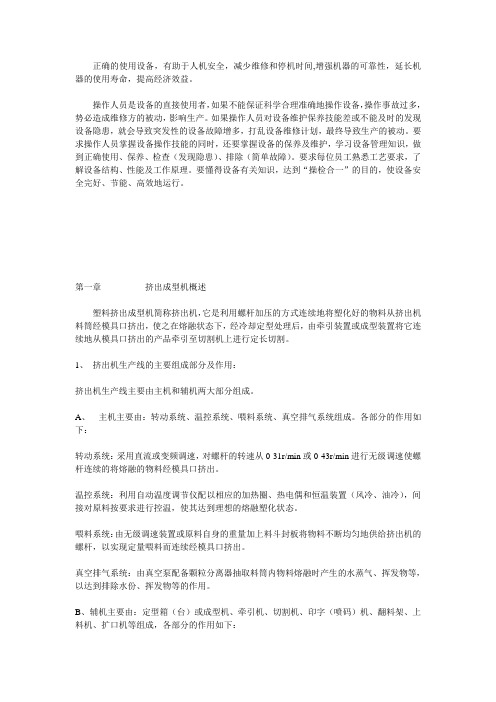
正确的使用设备,有助于人机安全,减少维修和停机时间,增强机器的可靠性,延长机器的使用寿命,提高经济效益。
操作人员是设备的直接使用者,如果不能保证科学合理准确地操作设备,操作事故过多,势必造成维修方的被动,影响生产。
如果操作人员对设备维护保养技能差或不能及时的发现设备隐患,就会导致突发性的设备故障增多,打乱设备维修计划,最终导致生产的被动。
要求操作人员掌握设备操作技能的同时,还要掌握设备的保养及维护,学习设备管理知识,做到正确使用、保养、检查(发现隐患)、排除(简单故障)。
要求每位员工熟悉工艺要求,了解设备结构、性能及工作原理。
要懂得设备有关知识,达到“操检合一”的目的,使设备安全完好、节能、高效地运行。
第一章挤出成型机概述塑料挤出成型机简称挤出机,它是利用螺杆加压的方式连续地将塑化好的物料从挤出机料筒经模具口挤出,使之在熔融状态下,经冷却定型处理后,由牵引装置或成型装置将它连续地从模具口挤出的产品牵引至切割机上进行定长切割。
1、挤出机生产线的主要组成部分及作用:挤出机生产线主要由主机和辅机两大部分组成。
A、主机主要由:转动系统、温控系统、喂料系统、真空排气系统组成。
各部分的作用如下:转动系统:采用直流或变频调速,对螺杆的转速从0-31r/min或0-43r/min进行无级调速使螺杆连续的将熔融的物料经模具口挤出。
温控系统:利用自动温度调节仪配以相应的加热圈、热电偶和恒温装置(风冷、油冷),间接对原料按要求进行控温,使其达到理想的熔融塑化状态。
喂料系统:由无级调速装置或原料自身的重量加上料斗封板将物料不断均匀地供给挤出机的螺杆,以实现定量喂料而连续经模具口挤出。
真空排气系统:由真空泵配备颗粒分离器抽取料筒内物料熔融时产生的水蒸气、挥发物等,以达到排除水份、挥发物等的作用。
B、辅机主要由:定型箱(台)或成型机、牵引机、切割机、印字(喷码)机、翻料架、上料机、扩口机等组成,各部分的作用如下:定型箱(台):由定型套(模)配以喷淋式或侵泡式冷却水,利用真空泵使定型箱(模)内产生负压,使熔融状态的制品定型凝固成理想的合格品。
2010第六章 挤出成型机解析
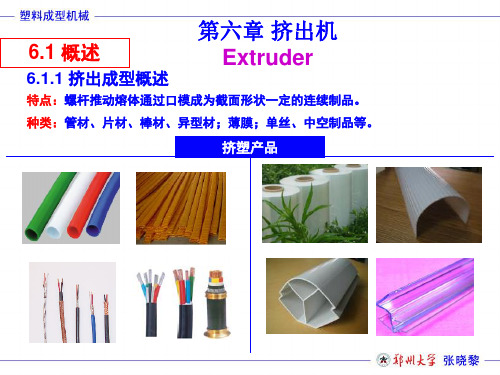
机头的作用:① 改变熔融物料的流动方向,使其由螺旋变为直线运动;② 产生必要的压力
使制品密实;③ 使物料进一步塑化均匀;④ 成型制品。
•
滤网screen:过滤机械杂质、未熔物料;增加料流阻力,提高混合、塑化效 果。由若干片叠在一起的30-120目不锈钢网组成,用多孔板支承。
•
多孔板(筛板、分流板):厚度为螺杆直径的1/3-1/5,上边钻有φ3-6mm的 中间疏、两边密的同心圆孔,距螺杆头部0.1D,即约为计量段一个螺槽容积, 太大易积料分解,太小料流不稳定。
4.筛孔板式:(生产聚烯烃类大管时,可克服自重产生的薄厚不均现象)
无分流梭和芯模,物料经筛孔板进入口模成型段;可保证物料充分熔融、塑化;无熔接痕,强 度高,结构紧凑,占地面积小。
二. 挤板(片)机头
口模由引流道、分配腔和模唇组成。 1.支管式 为将圆柱状流体变为扁平的矩形截面且有相等流速的流体,要设置一个纵向切口为管状的分配腔, 其作用是对熔体稳压、分流,使其均匀地挤出宽幅制品。 优点是结构简单,制造容易;可调幅宽;温度易控制;体积小,重量轻。
作用:输送、压实、塑化、挤出物料
① 加料段(Feeding zone),又称送料段、输送段;
② 压缩段(Compression zone),又称过渡段、熔融段:
③ 计量段(Metering zone):又称均化段、压出段。
不同形式的螺杆和料筒
加料段
作用:自加料斗摄取物料传送给压缩段,物料为固态。
•
分流器(鱼雷头):将圆柱形料流变为薄环状并便于进一步加热塑化。大型 分流器内设加热器,支架用以支承分流器及芯棒,同时使料流分束以加强搅 拌,小型分流器与芯棒做为一体。
一. 挤管机头
1.直向(通)式
第六章-挤出成型2
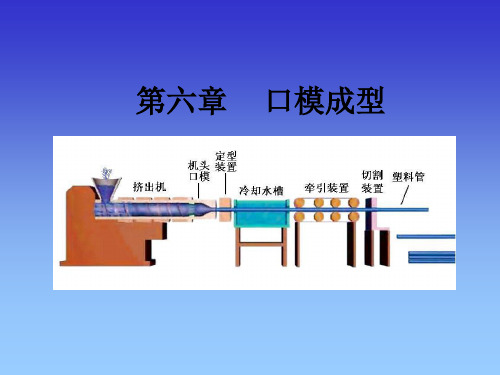
二、挤出成型设备
主机部分
以螺杆挤出机为主
挤出成型设备
辅机部分 控制系统
口模以后的部分
1. 主机、辅机速度 匹配;
2. 控温精度保证
第一节 单螺杆挤出机基本结构及作用
五.料筒
挤出机的主要部件之一。 为一金属圆筒,一般用耐温耐压、强度较
高、坚固耐磨、耐腐的合金钢或内衬合金钢的 复合钢筒制成。 塑料的塑化和加压过程都在其中进行。 外部设有分区加热和冷却装置。 加热:电阻、电感或其它方式。 冷却:风冷或水冷。
六.机头和口模
机头的作用是将处于旋转运动的塑料熔体转变为平 行直线运动,使塑料进一步塑化均匀,并将熔体均匀而 平稳地导入口模,赋予必要的成型压力,使塑料易于成 型和取得制品密实。
2D2 3 tgp 12EL
(1)
简化得:
p
qV An B
A和B只与螺杆的结构尺寸有关。
如果考虑熔体的非牛顿性,若略去漏流项QV,L,得到:
qV
2D2nH sin cos
2
DH m2 sinm1
(m 2)2m1
K
P
m
L
③ 均化段(计量段)
将熔融的物料,定容(定量)定压地送入机头使其 在口模中成型。
螺槽容积恒定不变。
为避免物料因滞留在螺杆头端面死角处引起分解, 螺杆头部常设计成锥形或半圆形。 有些螺杆的均化段是一表面完全平滑的杆体,称为“鱼 雷头”,但也有刻上凹槽或铣刻成花纹的。
鱼雷头具有搅拌和节制物料、消除流动脉冲现象的 作用,并能增大物料的压力,降低料层厚度,改善加热 状况,且能进一步提高螺杆塑化效率。
2010第六章 挤出成型机
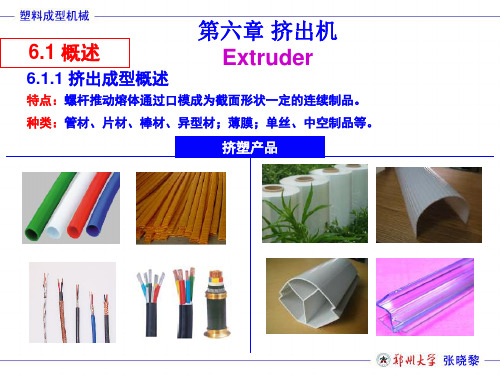
五. 不同形式的排气式挤出机
两级式挤出机:两台单机串联而成,一级的作用是输送和塑炼物料,二级进一步塑 化,均化,挤出成型,可实现稳定的排气挤出成型。
第2-6章 思考题
1.常用的初混和设备有哪些?捏合机的主要结构部件有什么? 2.常用的塑炼设备有什么?密炼机由哪些主要部件组成? 3.对比分析开炼机和密炼机塑炼机理的差别? 4.单螺杆挤出机主机的挤出系统由哪些部分组成? 5.挤出机螺杆的主要作用是什么?常规单螺杆由哪几段组成? 6.几何压缩比的定义是什么?为何要设置压缩比? 7.单螺杆挤出机螺杆工作时主要受哪几方面的作用力? 8.BM分离型螺杆的特点是什么? 9.销钉型分流螺杆上设置销钉的作用是什么? 10.试述排气式挤出机的结构特点,其排气原理是什么? 11.为何排气式挤出机排气孔下压力要为零?聚合物到此处应完全熔融? 12.何为压延成型的“三高两低”现象?由何原因造成,如何改善?
2.十字形(中心进料): 适于加工PP,PE等热稳料 优点:压缩比可大到7-8,无偏心。 缺点:有分流器支架,存在3-4条熔接线(可在支架上方开设缓冲槽改善)。
3.螺旋式:存在渐变的4-8条螺纹形流道,物料逐渐由螺旋变为轴向运动,再自环 形间隙挤出膜管。 优点:无熔接线;芯棒不偏心,成型稳定,厚薄均匀;芯棒粗,不易变形; 缺点:加工复杂。
4.筛孔板式:(生产聚烯烃类大管时,可克服自重产生的薄厚不均现象)
无分流梭和芯模,物料经筛孔板进入口模成型段;可保证物料充分熔融、塑化;无熔接痕,强 度高,结构紧凑,占地面积小。
二. 挤板(片)机头
口模由引流道、分配腔和模唇组成。 1.支管式 为将圆柱状流体变为扁平的矩形截面且有相等流速的流体,要设置一个纵向切口为管状的分配腔, 其作用是对熔体稳压、分流,使其均匀地挤出宽幅制品。 优点是结构简单,制造容易;可调幅宽;温度易控制;体积小,重量轻。
《挤出成型技术》课件
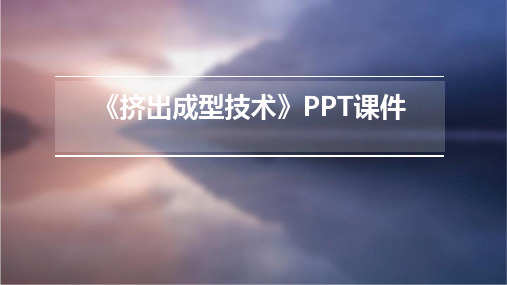
根据制品形状和尺寸进行结构设计,确保制品成型质量、提高生产 效率。
冷却系统
设计合理的冷却系统,控制模具温度,减小制品成型后的收缩率。
挤出成型设备的操作与维护
01
操作规程
制定严格的设备操作规程,确保 操作人员熟悉设备性能和安全操 作要求。
维护保养
02
03
故障排除
定期对设备进行维护保养,检查 各部件磨损情况,及时更换易损 件。
高分子材料在挤出成型技术中的优势在于其可塑性强、加工温度低、成型周期短 等,使得制品具有轻量化、高强度、耐腐蚀等优良性能。同时,高分子材料在挤 出成型过程中易于实现自动化和智能化生产,提高了生产效率和产品质量。
新型挤出成型技术的研发与推广
随着科技的不断发展,新型挤出成型技术不断涌现,如微孔塑料挤出技术、异型截面管材挤出技术、 反应挤出技术等。这些新型技术的研发和应用,极大地丰富了挤出成型制品的种类和性能,满足了不 同领域的需求。
挤出成型技术的应用领域
挤出成型技术广泛应用于塑料加工行业,如管材、型材、薄膜、板材等产品的生产 。
除了塑料加工行业,挤出成型技术还应用于橡胶、陶瓷、玻璃纤维等材料的加工。
随着科技的发展,挤出成型技术的应用领域不断扩大,如3D打印技术的出现,使得 挤出成型技术也可以用于制造个性化的定制产品。
02
挤出成型设备
挤出成型工艺的控制要素
温度控制
温度是挤出成型工艺的重要控制要素之一,包括 机筒温度、模具温度等。温度的控制直接影响着 塑料的塑化和产品质量。
速度控制
速度控制包括挤出速度、注射速度等,它影响着 产品的产量和质量。合理地调整速度参数,可以 提高生产效率和产品质量。
压力控制
压力也是挤出成型工艺的重要控制要素之一,包 括挤出压力、注射压力等。压力的控制对于塑料 的流动性和产品的致密性至关重要。
挤出成型机的主要部件是

挤出成型机的主要部件是
挤出成型机是一种常用于生产塑料制品的机器设备,其主要部件包括进料系统、螺杆和筒体、加热冷却系统、模具和挤出头、变速箱等。
进料系统是挤出成型机的第一个部件,它用于将原料输送至挤出机螺杆中。
通常通过送料机将原料送入到螺杆中,确保原料能够均匀、稳定地供给到后续的挤出过程中。
进料系统的设计和运行稳定性直接影响到挤出成型机整体生产效率。
接下来是挤出机的核心部件——螺杆和筒体。
螺杆是一个具有螺纹结构的旋转元件,负责将原料从进料口推进到挤出头处。
而筒体则是螺杆的外壳,起到容纳原料、加热和压缩的作用。
螺杆和筒体的设计精良与否将直接影响到挤出产品的质量和生产效率。
加热冷却系统也是挤出成型机中至关重要的部件之一。
通过加热系统,可以将原料加热至适宜的挤出温度,以确保原料能够顺利地挤出并形成所需的产品。
而冷却系统则用于快速冷却挤出的塑料制品,使其快速固化并保持形状稳定。
模具和挤出头是挤出成型机中实现产品成型的关键部件。
模具的设计决定了最终产品的外形和尺寸,而挤出头的结构影响到产品的质量和表面光滑度。
精密的模具和挤出头能够生产出高质量的塑料制品,满足客户的需求。
最后是变速箱,它用于控制螺杆的转速,调节挤出速度和产量。
变速箱的运行稳定性对挤出成型机的生产效率起着至关重要的作用,通过合理调节变速箱,可以实现不同产品的生产需求。
综上所述,挤出成型机的主要部件包括进料系统、螺杆和筒体、加热冷却系统、模具和挤出头、变速箱等。
这些部件密切配合,共同完成塑料制品的挤出成型工艺,为各行各业提供高质量、高效率的生产解决方案。
1。
- 1、下载文档前请自行甄别文档内容的完整性,平台不提供额外的编辑、内容补充、找答案等附加服务。
- 2、"仅部分预览"的文档,不可在线预览部分如存在完整性等问题,可反馈申请退款(可完整预览的文档不适用该条件!)。
- 3、如文档侵犯您的权益,请联系客服反馈,我们会尽快为您处理(人工客服工作时间:9:00-18:30)。
4.螺杆分配式机头:在直支管式机头模腔中插入一根旋转的分配螺杆 分配螺杆的作用:将模腔内的熔体进一步塑化并沿宽度方向均匀分布;压力沿横截面各点一致,挤 速均匀;减少机头内积料的可能性。 优点:生产能力高,制品均匀;可发泡成型,易成型宽、厚板材;机头内料温易控;可连续运转; 缺点:加工困难,成本高;分配螺杆旋转,使料流到口模区变为直线运动的距离缩短,易在制品中
压缩段
作用:压实熔融物料,自加料斗排出气体,物料呈固液共存状态。 压缩比:计量段一个螺槽容积和加料段一个螺槽容积之比。 设置压缩比的原因:
(1) 适应物料熔融体积减小的变化而设; (2) 压缩物料,将气体自加料口排出; (3) 建立必要的压力,保证物料到螺杆末端有足够的致密度。 获得压缩比的方法 等深不等距法;等距不等深法;不等深不等距法;采用锥形螺杆。
作用:输送、压实、塑化、挤出物料
① 加料段(Feeding zone),又称送料段、输送段; ② 压缩段(Compression zone),又称过渡段、熔融段: ③ 计量段(Metering zone):又称均化段、压出段。
不同形式的螺杆和料筒
加料段
作用:自加料斗摄取物料传送给压缩段,物料为固态。
熔体在机头中流动方向与螺杆轴向垂直,从料筒流出的熔体绕过芯模再向前流动,会产生一条分 流痕,流动阻力小,料流稳定,出料均匀,但其结构复杂,占地面积大。 适于PP、PE及尺寸要求严格的管材。
3.旁侧式 熔体经过一个近似直角的过渡区才流入机头,阻力大,结构更复杂。
消除或改善熔接线的方法:
适当加大口模平直段(成型段)长;增大分流器支架与出料口的距离;使进口角(扩张角)大于出 口角(收缩角);加大机头进口处截面与出口截面比;采用异型芯棒(目的是增大料流阻力)。
2.十字形(中心进料): 适于加工PP,PE等热稳料 优点:压缩比可大到7-8,无偏心。 缺点:有分流器支架,存在3-4条熔接线(可在支架上方开设缓冲槽改善)。
第六章 挤出机
6.1 概述
6.1.1 挤出成型概述
Extruder
特点:螺杆推动熔体通过口模成为截面形状一定的连续制品。
种类:管材、片材、棒材、异型材;薄膜;单丝、中空制品等。
挤塑产品
6.1.2 挤出机组
主机部分
辅机部分 软管挤出生产线标准设备
硬 管 挤 出 模 拟
6.1.3 挤出机主机
作用:输送、压实、熔融塑化和挤出物料 组成:传动装置、熔融塑化装置、机头和口模
留下波浪形痕迹。
三. 吹膜机头
1. 芯棒式(侧进料): 料流在芯棒处分为两股,再沿芯棒尖的斜刀口处汇合,向模口呈薄管挤出, 芯棒中通压缩空气吹胀。
优点:机头内通道间隙小存料少,物料不宜过热分解,适于加工PVC;只一条熔接线;加工方便。 缺点:芯棒尖处易积料;压力作用到芯棒尖上,易偏中,造成制品不均匀开裂。
传动装置
机头和口模
熔融塑化装置
单螺杆挤出机结构示意图 1—机座 2—电动机 3—传动装置 4—料斗 5—料斗冷却区 6—料筒
7—加热圈 8—热电偶 9—螺杆 10—多孔板和过滤网 11—机头加热圈 12—机头 13—挤出物
单螺杆挤出机(Single screw extruder)
工作状态模拟
6.2 挤出机用三段式Байду номын сангаас通螺杆
4.筛孔板式:(生产聚烯烃类大管时,可克服自重产生的薄厚不均现象)
无分流梭和芯模,物料经筛孔板进入口模成型段;可保证物料充分熔融、塑化;无熔接痕,强 度高,结构紧凑,占地面积小。
二. 挤板(片)机头
口模由引流道、分配腔和模唇组成。 1.支管式 为将圆柱状流体变为扁平的矩形截面且有相等流速的流体,要设置一个纵向切口为管状的分配腔, 其作用是对熔体稳压、分流,使其均匀地挤出宽幅制品。 优点是结构简单,制造容易;可调幅宽;温度易控制;体积小,重量轻。
2. 鱼尾形:熔体从中部进入沿扇形扩展开来 优点: 物料呈流线型流动;物料停留时间短,适用的温度范围广;结构简单。 缺点: 鱼尾形部分扩张角不可过大(避免中心处压力速度太大造成中心出料多两 端少);不能生产宽幅制品。
3. 衣架式:分配腔为两根直管递减的支管并有一个扩张角可大至160-170º的型腔, (吸收了支管式和鱼尾形机头的优点)。 优点: 支管小,缩短了物料在机头内的停留时间;扇形型腔提高了制品的薄厚均匀 性,制品幅宽可达4-5m。
计量段
作用:进一步均化物料并对其进行计量,到达此段时物料已完全熔融。 四种形式的流动:正流、逆流、环流、漏流。 要求:该段螺槽深度应保证其计量能力与压缩段熔融能力匹配
h3=0.02-0.06D Lm=4-7D h3<h2<h1
6.3 常用机头和口模形式 (Dies)
机头的组成和作用
机头:机头和口模常连为一体,通称机头,包括过滤网、多孔板、分流梭(有时与模芯结合 为一个部件)、模芯、口模等。 机头的作用:① 改变熔融物料的流动方向,使其由螺旋变为直线运动;② 产生必要的压力 使制品密实;③ 使物料进一步塑化均匀;④ 成型制品。
• 分流器(鱼雷头):将圆柱形料流变为薄环状并便于进一步加热塑化。大型 分流器内设加热器,支架用以支承分流器及芯棒,同时使料流分束以加强搅 拌,小型分流器与芯棒做为一体。
一. 挤管机头
1.直向(通)式
熔体在机头中流动方向与螺杆轴向一致,结构简单易制造,适于硬、软PVC,PE,PA等。
2.横向(直角)式
• 滤网screen:过滤机械杂质、未熔物料;增加料流阻力,提高混合、塑化效 果。由若干片叠在一起的30-120目不锈钢网组成,用多孔板支承。
• 多孔板(筛板、分流板):厚度为螺杆直径的1/3-1/5,上边钻有φ3-6mm的 中间疏、两边密的同心圆孔,距螺杆头部0.1D,即约为计量段一个螺槽容积, 太大易积料分解,太小料流不稳定。
Qs 2 Db NH f (Db H f )(tan tan b ) /(tan tan b )
Db : 螺杆外径;N:螺杆转速;H f : 加料段槽深;
:移动角;
:
b
料筒表面
处的螺旋角
增大固体物料输送速率的方法:
适当提高N和Db; 加大加料段螺槽深度;逆向冷却螺杆加料段、提高螺 杆表面光洁度;在料筒内壁开设纵向沟槽。