钢板成形技术
非合金钢板的超塑性成形技术研究及其应用潜力

非合金钢板的超塑性成形技术研究及其应用潜力超塑性成形是一种通过在高温条件下对材料应力施加的加工方法,可以使非合金钢板也能够实现高度塑性变形。
本文将探讨非合金钢板超塑性成形技术的研究现状以及其在实际应用中的潜力。
首先,我们将介绍非合金钢板超塑性成形技术的研究现状。
非合金钢板由于其较低的碳含量以及少量的合金元素,通常具有较低的塑性,限制了其在成形过程中的应用。
然而,通过对非合金钢板进行超塑性成形的研究,可以改善其塑性特性,使其具备更广阔的应用前景。
目前,非合金钢板超塑性成形技术的研究主要集中在以下几个方面。
首先,研究人员通过调整非合金钢板的化学成分,改变晶体结构,提高材料的塑性。
其次,采用热处理方法,通过控制加热温度和时间,使非合金钢板获得更高的塑性。
此外,研究人员还探索了不同的成形方法,如等温拉伸、等温压缩、等温缩径等,以实现非合金钢板的超塑性变形。
在实际应用中,非合金钢板超塑性成形技术具有广阔的潜力。
首先,超塑性成形可以极大地提高材料的成形能力,使非合金钢板能够制造出更复杂的形状和结构。
这对于一些应用场景,如汽车、航空航天以及能源领域的零部件制造具有重要意义。
其次,超塑性成形技术可以减少材料在成形过程中的应力和变形,降低材料的变形硬化率,从而改善零部件的成形质量和机械性能。
此外,超塑性成形还可以降低材料的成形温度,减少能源消耗,降低生产成本。
然而,在实际应用中,非合金钢板超塑性成形技术还面临一些挑战。
首先,超塑性成形需要非常严格的加工条件和设备配置,包括高温环境、复杂的工艺参数控制等。
这增加了生产成本和困难。
其次,非合金钢板超塑性成形技术的研究还相对较少,需要进一步的实验研究和理论探索。
此外,超塑性成形后的材料往往会出现晶界滑移和晶界扩散现象,可能会影响材料的综合性能和寿命。
为了克服这些挑战,进一步开展非合金钢板超塑性成形技术的研究是非常必要的。
首先,可以通过优化材料的化学成分,改善非合金钢板的塑性特性。
中厚钢板电磁感应加热渐进成形技术研究
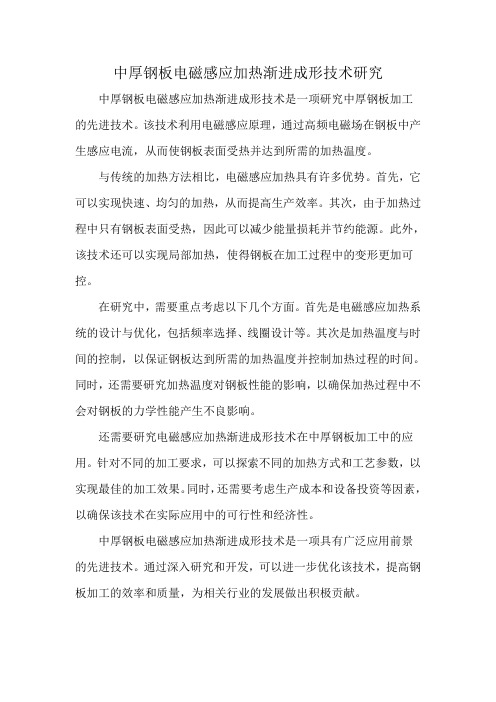
中厚钢板电磁感应加热渐进成形技术研究中厚钢板电磁感应加热渐进成形技术是一项研究中厚钢板加工
的先进技术。
该技术利用电磁感应原理,通过高频电磁场在钢板中产生感应电流,从而使钢板表面受热并达到所需的加热温度。
与传统的加热方法相比,电磁感应加热具有许多优势。
首先,它可以实现快速、均匀的加热,从而提高生产效率。
其次,由于加热过程中只有钢板表面受热,因此可以减少能量损耗并节约能源。
此外,该技术还可以实现局部加热,使得钢板在加工过程中的变形更加可控。
在研究中,需要重点考虑以下几个方面。
首先是电磁感应加热系统的设计与优化,包括频率选择、线圈设计等。
其次是加热温度与时间的控制,以保证钢板达到所需的加热温度并控制加热过程的时间。
同时,还需要研究加热温度对钢板性能的影响,以确保加热过程中不会对钢板的力学性能产生不良影响。
还需要研究电磁感应加热渐进成形技术在中厚钢板加工中的应用。
针对不同的加工要求,可以探索不同的加热方式和工艺参数,以实现最佳的加工效果。
同时,还需要考虑生产成本和设备投资等因素,以确保该技术在实际应用中的可行性和经济性。
中厚钢板电磁感应加热渐进成形技术是一项具有广泛应用前景
的先进技术。
通过深入研究和开发,可以进一步优化该技术,提高钢板加工的效率和质量,为相关行业的发展做出积极贡献。
热成形钢板技术 PPT

• forming of hot blank to final shape
•
to get UHS properties (quenching)
•
板料加热至最终成型以达到UHS属性(冷却)
Sample图示: Tunnel中通道
Direct Hot Forming直接热成型
Advantage优点:
• weight reduction减轻重量 • minimized use of reinforcements
Instrument Panels
Frontbumper
Rocker Panelreinforcement
Side memberreinforcement
A-Pillarreinforcement
Benefit of Hot Stamping 热成形的优势 ➢ highest material strength with high ductility
Hot forming (Press hardening)
direct process
coil
blank
furnace handling
press cooling
INDIRECT HOT FORMING间接热成型工艺
process steps工艺步骤
• pre forming of sheet metal (cold) 板料预成型 • heating up of pre formed press part 加热预成型的冲压件 • hot stamping of pre-formed-press-part to get UHS properties
(quenching)预冲压的钢板进行热成型以达到UHS属性(冷却)
超高强度钢板冲压件热成形工艺

超高强度钢板冲压件热成形工艺摘要:随着国民物质生活水平的提高,大家对汽车安全性的要求也越来越强烈,因此,高强度、超高强度钢板在汽车车身上的应用也越来越广泛。
然而,由于高强度、超高强度钢板在常温下强度较高,变形抗力比较大,导致利用常规冷冲压成形的方式很难成形,因此高强度、超高强度钢板热冲压成形技术就应运而生。
目前,高强度钢板热冲压成形零件已经广泛应用于国内外汽车车身的重要零件上。
关键词:热冲压成形;超高强度钢板;模具设计;冷却系统;数值模拟;一、热冲压成形工艺原理首先把常温下强度为500~600MPa的高强度硼合金钢板加热到880~950℃,使之均匀奥氏体化,然后送入内部带有冷却系统的模具内冲压成形,之后保压快速冷却淬火,使奥氏体转变成马氏体,成形件因而得到强化硬化,强度大幅度提高。
比如经过模具内的冷却淬火,冲压件强度可以达到1500MPa,强度提高了250%以上,因此该项技术又被称为“冲压硬化”技术。
实际生产中,热冲压工艺又分为两种,即直接工艺和间接工艺。
直接工艺,下料后,直接把钢板加热然后冲压成形,主要用于形状比较简单变形程度不大的工件。
对于一些形状复杂的或者拉深深度较大的工件,则需要采用间接工艺,先把下好料的钢板预变形,然后再加热实施热冲压,二、热冲压成形工艺的主要影响因素2.1材料热冲压成形工艺中采用的是一种特殊的具有自硬性的硼合金高强度钢板。
和现在的双相钢、相变诱导塑性钢、复相钢、马氏体钢等汽车高强度钢板不同,这些钢板常温下强度就很高,并且通常都采用冷冲压工艺制造零部件,成形前后零件的微观组织没有变化,强度等指标基本上保持不变。
而热成形工艺中使用的硼合金钢板是一种低碳微合金钢,添加了一定量的B元素,提高了钢板的淬火性能,成形后发生相变,强度等指标成倍提高。
另外,还添加了Ti,Cr,Mo,Cu,Ni等多种合金微量儿素,因而提高了材料的屈服强度以及其他力学性能,材料力学性能也很稳定。
典型的热冲压成形钢板22MnB5的下要成分,这种钢板常温下的强度不很高,抗拉强度仅有500700MPa,塑性、可成形性等性能也很好,而通过热成形工艺的加热、成形、冷却后,成形件被淬火,微观组织转变成马氏体,强度、硬度等指标大幅度提高,屈服强度可以达到1000MPa以上,抗拉强度达到1500MPa,硬度可以达到50HRC。
无模成形技术简介
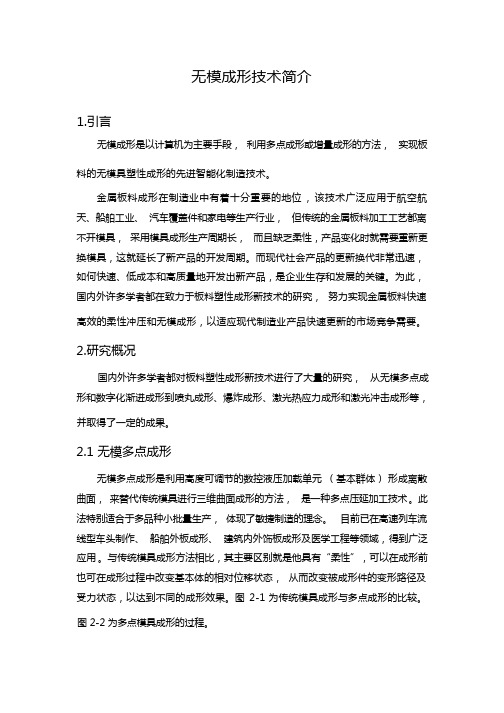
无模成形技术简介1.引言无模成形是以计算机为主要手段,利用多点成形或增量成形的方法,实现板料的无模具塑性成形的先进智能化制造技术。
金属板料成形在制造业中有着十分重要的地位,该技术广泛应用于航空航天、船舶工业、汽车覆盖件和家电等生产行业,但传统的金属板料加工工艺都离不开模具,采用模具成形生产周期长,而且缺乏柔性,产品变化时就需要重新更换模具,这就延长了新产品的开发周期。
而现代社会产品的更新换代非常迅速,如何快速、低成本和高质量地开发出新产品,是企业生存和发展的关键。
为此,国内外许多学者都在致力于板料塑性成形新技术的研究,努力实现金属板料快速高效的柔性冲压和无模成形,以适应现代制造业产品快速更新的市场竞争需要。
2.研究概况国内外许多学者都对板料塑性成形新技术进行了大量的研究,从无模多点成形和数字化渐进成形到喷丸成形、爆炸成形、激光热应力成形和激光冲击成形等,并取得了一定的成果。
2.1 无模多点成形无模多点成形是利用高度可调节的数控液压加载单元(基本群体)形成离散曲面,来替代传统模具进行三维曲面成形的方法,是一种多点压延加工技术。
此法特别适合于多品种小批量生产,体现了敏捷制造的理念。
目前已在高速列车流线型车头制作、船舶外板成形、建筑内外饰板成形及医学工程等领域,得到广泛应用。
与传统模具成形方法相比,其主要区别就是他具有“柔性”,可以在成形前也可在成形过程中改变基本体的相对位移状态,从而改变被成形件的变形路径及受力状态,以达到不同的成形效果。
图2-1 为传统模具成形与多点成形的比较。
图 2-2 为多点模具成形的过程。
图 2-1 模具成形与多点成形的比较图 2-2 多点模具成形过程20 世纪 70 年代,日本造船界开始研究多点成形压力机,并成功应用于船体外板的曲面成形。
此后许多学者为开发多点成形技术进行了大量的探讨与研究,制作了不同的样机,但大多只能进行变形量较小的整体变形。
吉林大学李明哲等人对无模多点成形技术进行了较为系统的研究,已自主设计并制造了具有国际领先水平的无模多点成形设备,2002 年底,李教授组建了产学研实体:长春瑞光科技有限公司。
间接热成型技术
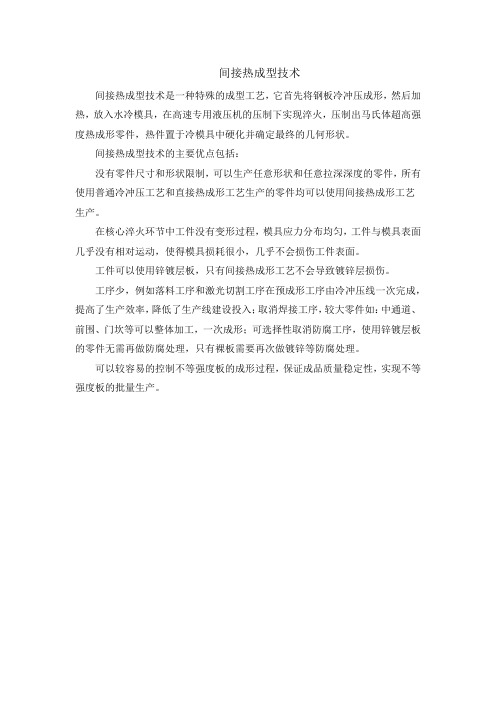
间接热成型技术
间接热成型技术是一种特殊的成型工艺,它首先将钢板冷冲压成形,然后加热,放入水冷模具,在高速专用液压机的压制下实现淬火,压制出马氏体超高强度热成形零件,热件置于冷模具中硬化并确定最终的几何形状。
间接热成型技术的主要优点包括:
没有零件尺寸和形状限制,可以生产任意形状和任意拉深深度的零件,所有使用普通冷冲压工艺和直接热成形工艺生产的零件均可以使用间接热成形工艺生产。
在核心淬火环节中工件没有变形过程,模具应力分布均匀,工件与模具表面几乎没有相对运动,使得模具损耗很小,几乎不会损伤工件表面。
工件可以使用锌镀层板,只有间接热成形工艺不会导致镀锌层损伤。
工序少,例如落料工序和激光切割工序在预成形工序由冷冲压线一次完成,提高了生产效率,降低了生产线建设投入;取消焊接工序,较大零件如:中通道、前围、门坎等可以整体加工,一次成形;可选择性取消防腐工序,使用锌镀层板的零件无需再做防腐处理,只有裸板需要再次做镀锌等防腐处理。
可以较容易的控制不等强度板的成形过程,保证成品质量稳定性,实现不等强度板的批量生产。
高强度钢板的两种热成形技术
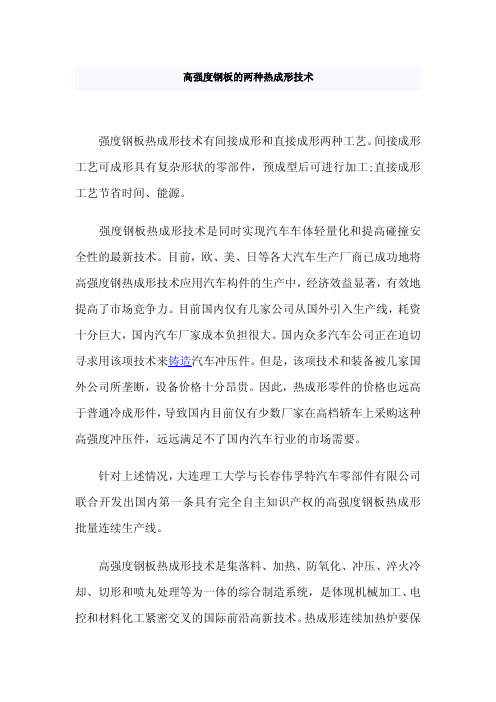
高强度钢板的两种热成形技术强度钢板热成形技术有间接成形和直接成形两种工艺。
间接成形工艺可成形具有复杂形状的零部件,预成型后可进行加工;直接成形工艺节省时间、能源。
强度钢板热成形技术是同时实现汽车车体轻量化和提高碰撞安全性的最新技术。
目前,欧、美、日等各大汽车生产厂商已成功地将高强度钢热成形技术应用汽车构件的生产中,经济效益显著,有效地提高了市场竞争力。
目前国内仅有几家公司从国外引入生产线,耗资十分巨大,国内汽车厂家成本负担很大。
国内众多汽车公司正在迫切寻求用该项技术来铸造汽车冲压件。
但是,该项技术和装备被几家国外公司所垄断,设备价格十分昂贵。
因此,热成形零件的价格也远高于普通冷成形件,导致国内目前仅有少数厂家在高档轿车上采购这种高强度冲压件,远远满足不了国内汽车行业的市场需要。
针对上述情况,大连理工大学与长春伟孚特汽车零部件有限公司联合开发出国内第一条具有完全自主知识产权的高强度钢板热成形批量连续生产线。
高强度钢板热成形技术是集落料、加热、防氧化、冲压、淬火冷却、切形和喷丸处理等为一体的综合制造系统,是体现机械加工、电控和材料化工紧密交叉的国际前沿高新技术。
热成形连续加热炉要保证板料加热到设定的温度充分奥氏体化,同时避免没有防氧化涂层板料的高温氧化脱碳,这决定了热成形连续加热炉与其他加热炉相比应具有独特的核心技术。
成形有间接成形和直接成形两种工艺。
热成形间接成形工艺是指板料先经过冷冲压进行预成形,然后加热到奥氏体化温度,保温一段时间后放到具有冷却系统的模具里进行最终成形及淬火。
热成形间接成形工艺的优点如下:(1)可以成形具有复杂形状的车内零部件,几乎可以获得目前所有的冲压承载件。
(2)板料预成形后,后续热成形工艺不需要过多考虑板料高温成形性能,可以确保板料完全淬火得到所需要的马氏体组织。
(3)板料预成形后可以进行修边、翻边、冲孔等工艺加工,避免板料淬火硬化后加工困难问题。
热成形直接成形工艺是指板料加热到奥氏体化温度保温一段时间后直接放到具有冷却系统的模具里进行成形及淬火。
板材冲压成形的基本知识课件
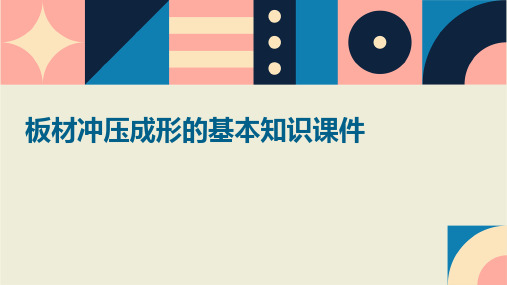
板材冲压成形的应用领域
汽车制造
家用电器
建筑行业
其他领域
汽车车身覆盖件、零部 件等。
外壳、内部结构件等。
金属板材门窗、幕墙等 。
金属包装容器、金属艺 术品等。
板材冲压成形的基本原理
01
02
03
塑性变形
板材在压力作用下发生塑 性变形,从而获得所需形 状和尺寸。
板材的力学性能与厚度
力学性能
指板材在受力时的表现,如强度、硬度、韧性等。这些性能对冲压成形的效果有直接影 响。
厚度
板材的厚度会影响其成形性能和刚性。较厚的板材在冲压时不易发生变形,而较薄的板 材则容易产生较大的变形。
04
板材冲压成形的缺陷与质量控制
起皱与破裂
起皱
在板材冲压过程中,由于材料的流动应 力、切向压应力或切向应变率等因素影 响,板料在弯曲变形区出现多余的金属 材料聚集,形成皱纹的现象。
模具设计
模具是实现板材冲压成形 的重要工具,其设计直接 影响产品的质量和生产效 率。
材料性能
材料的塑性、强度、韧性 等性能对冲压成形效果有 重要影响。
02
板材冲压成形的工艺流程
原材料准备
原材料选择
根据产品要求选择合适的板材,如不锈钢、碳钢板、铝板等 。
板材的剪裁与切割
将大块板材剪裁成适合冲压的小块,并进行必要的切割。
VS
破裂
在板材冲压过程中,由于材料的抗拉强度 不足或变形量过大,导致板料出现裂纹或 断裂的现象。
回弹与畸变
回弹
在板材冲压过程中,板料弯曲变形后,当外 力去除时,由于弹性变形恢复,弯曲角度会 发生变化的现象。
- 1、下载文档前请自行甄别文档内容的完整性,平台不提供额外的编辑、内容补充、找答案等附加服务。
- 2、"仅部分预览"的文档,不可在线预览部分如存在完整性等问题,可反馈申请退款(可完整预览的文档不适用该条件!)。
- 3、如文档侵犯您的权益,请联系客服反馈,我们会尽快为您处理(人工客服工作时间:9:00-18:30)。
7、板后变化趋势
初始板厚1mm
钢板成形技术
目录
1、概述 2、钢板成形技术介绍 3、拉深成形技术介绍 4、拉深成形中对成形质量影响的工艺参数
1、概述
汽车产品
航天产品
航空产品
家用产品
2、钢板成形技术介绍
二. 板材成形极限及影响因素 (1)提高伸长类成形极限的措施
1)提高材料塑性 2)减小变形不均匀程度(提高塑性变形稳定性) 3)消除引起局部应力集中的因素
3、压边力
在成形过程中施加的压边力对材料成形也有巨大影响,材料的压边力过 大会出现材料表面起皱现象,但是如果材料的压边力过大又会导致材料的成 形后出现破裂现象。
4、压边间隙
在成形过程中压边间隙也是影响成形质量的重要因素,压边间隙过小, 材料在成形过程中很难流动,而如果压边间隙过大材料快速进入成形模内, 材料就会在短时间大量堆积,出现表面起皱破裂等现象。
(2)提高压缩类成形极限的措施 1)提高传力区的承载能力,降低变形区的变形抗力及摩擦力 2)阻止毛坯变形区失稳起皱 3)以降低变形区的变形抗力为主要目的的退火
3、拉深成形技术介绍
在凸模作用下,原直径为D0的毛坯, 在凹模和压边圈之间的缝隙中变形, 并被拉进凸,凹模的间隙中形成空间 零件的直壁
拉深的成形方式有很多,如普通拉深,多道次拉深,软模拉深,
拉深成形一般在室温下进行,因此材料硬化 性能对变形有较大影响,材料的成形性已为材料 性能的研究重点,其主要失效形式是破裂和起皱。
在板材成形时,把变形毛坯分成变形区和不变形区。 板料主要出现失稳出现在传力区
A—变形区 B-已变形区,传力区 C-待变形区
4、拉深成形中对成形质量影响的工艺参数
1、材料的r值:
如果材料冲压性能不好容易出现破裂,容易在厚度方向上变形,那么它的r 值基本上小于1;如果材料在成形过程中厚度方向上减薄较少,但在宽度和长度 方向上容易变形,那么它的r值一般会大于1。材料的厚度大幅度的减薄是材料 最终破裂的主要原因,所以r值越大越有利于拉深。 2、材料的n值:
另一个对材料拉深成形影响较大的参数是n,称之为硬化指数。硬化指数 n值较大,这表明该种材料在冷变形时硬化显著,对后续变形工序不利,有时需 要增加中间退火过程以消除硬化,以便后续继续对材料继续进行加工。在双对 数坐标平面上, 硬化指数n值一般是材料真实应变关系曲线的斜率。
颗粒或粉末介质软模成形(granules or powder flexible die forming,GFDF)
工艺是指现今最新的把模具的凸模或凹模用粉末介质或者颗粒物进行替代,这种先 进的冲压成形工艺能够使零件在很复杂的应变和应力条件下完成拉深成形,目前国 际上已能够使用颗粒或粉末软制成的凸模,对板材进行拉深成形。
充液拉深等,需要根据成形材料的特性及所需产品及现有设备的情况 寻找合适的拉深方式。
利用液体( 油或水) 作为介质来传递力的拉深被称之为充液拉深, 目前充液拉深,充液成形正逐步替代传统使用刚性凹模直接作用于毛 坯进行拉深成形的方式
多道次拉深成形相对一次成形更为复杂,前次拉深完成后的产 品成为后次拉深的坯料,称之为半成品,通过多次变形后,材料形状 和性能都发生了很大的变化。所以,多道次拉深成形的变形规律相对 于一次拉深有独特之处,有自己特殊的变形工艺
5、凹模圆角半径
在拉深成形过程中凹模圆角太小 ,毛坯拉入凹模的阻力增大,拉深件容
易产生裂纹和划痕,如果太大,会使毛坯尽早的脱离压边圈,让制件产生褶 皱。
6、润滑状态
在拉深过程中钢板由于塑性变形时会产生很强的抗力,就算模具表面做的非常 光滑,剧烈的摩擦仍然会在模具和制件之间发生。由于钢板与模具材料存在一定的粘 合性,这使制件与模具表面的摩擦更加剧烈。这是制件和模具损伤的主要原因。同时, 制件在成形过程中,它内部金属晶格要发生位错和晶格畸变,会产生大量的热能,由 于没有润滑剂,制件与模具之间的热能无法被带出,无法冷却,这使得制件与模具接 触部位瞬间产生高温,出现冷焊粘接现象,这也是造成制件和模具损伤的重要原因, 所以必须要加润滑剂。